Multistep Monitors and Restrictions
Step Monitors
The step monitors are used to verify that the tightening was achieved according to the specification, for example, angle limits or torque. Each step has mandatory step monitors and optional step monitors. The mandatory monitors are included when dragging a new step to the multistep program. The optional monitors are flexible and can be placed as needed in the multistep program. Every step can have up to eight monitors each.
The following monitors are automatically added to every step that is added to the multistep tightening program.
Step Monitor | Applicable steps |
---|---|
Angle | All |
Peak Torque | All |
PT – Peak Torque
This step monitor measures the maximum torque reached during the monitor, including any over-shoot, and checks that it is between High Limit and Low Limit.
SOT – Shut Off Torque
The shut off point is the point where the step reaches its target. When using the step monitor Shut off Torque, the torque is measured at the shut off point and checked to be between High Limit and Low Limit.
SOC – Shut Off Current
The shut off point is the point where the step reaches its target. When using the step monitor Shut off Current, the current is measured at the shut off point and checked to be between High Limit and Low Limit.
TRD – Torque Rate and Deviation
This step monitor measures and checks the torque rate, that is the ratio of torque versus angle. The calculated torque rate is then checked to see that it is within the torque rate limits defined by High Limit and Low Limit.
Parameter | Description | In illustration |
---|---|---|
TorqueStart | Torque from where AngleStart starts | Tstart |
TorqueStop | Torque where the measuring of the torque is stopped. | Tstop |
AngleStart | When AngleStart has been measured from TorqueStart the torque starts to be measured. | Astart |
AngleStop | Angle point where the measuring of the torque is stopped. | Astop |
Low Limit | Defined lowest torque. | TRL |
High Limit | Defined highest torque. | TRH |
Parameter | Description | In illustration |
---|---|---|
TorqueStart | Torque from where AngleStart starts | Tstart |
TorqueStop | Torque where the measuring of the torque is stopped. | Tstop |
AngleStart | When AngleStart has been measured from TorqueStart the torque starts to be measured. | Astart |
AngleStop | Angle point where the measuring of the torque is stopped. | Astop |
Low Limit | Defined lowest torque. | TRL |
High Limit | Defined highest torque. | TRH |
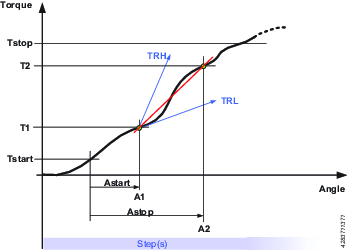
A – Angle
This step monitor measures the peak angle, angle at peak torque, shut-off angle or angle at end, which is achieved during the monitoring sequence and checks that it is between High Limit and Low Limit. The angle measurement starts at the start or end of the monitoring sequence or, if specified, at the point where the torque passes Trigger Torque for the first time.
PTCA – Post Thread Cut Angle
Measures the angle achieved during the monitoring and checks that it is between the specified angle limits. The Trigger Torque level is ignored until the end of the Thread cut angle window is reached. After that, the angle measuring starts as soon as the measured torque is above Trigger Torque. The parameter Stop Condition specifies where the angle measurement should end.
PTCPT – Post Thread Cut Peak Torque
Measures the maximum torque achieved during the monitoring, including any over-shoot, and checks that it is between the Torque limits. All torque values are ignored until the end of the Thread cut angle window has been reached.
TAW – Torque in Angle Window
The monitor checks that all torque values in the Angle Window Length are between the Torque limits. The Angle Window starts at the Start Angle from the point where the torque first passes the Trigger Torque. If Trigger Torque is not set, the Start Angle begins at the start of the monitor step. Since all torque values must be between the Torque limits, it can happen that both limits are exceeded. In this case, the error Torque In Angle Window High has priority and is the one that will be presented in the result. If the end of Angle Window is not reached, the status of the monitor is NOK.
PVTH – Post View average Torque High
All torque values in the Angle Window Length should be below the Torque Limit High. The Angle Window starts at the angle degrees set in Start Angle in reverse direction from the shut-off point. This then spans for the angle degrees set in Angle Window Length in reverse direction. If Start Angle is left blank the Angle Window starts at the shut-off point. The torque values used in the monitor are based on the mean torque value, calculated over Number of Samples. If the total angle of the step is less than Start Angle plus Angle Window Length the monitor will report NOK.
PVTL – Post View average Torque Low
Same as monitor Post View average Torque High but this monitor checks that all torque values in the Angle Window Length are above Torque Limit Low instead.
YA – Angle from Yield
The angle is monitored after finding the yield point. The Yield point is found by monitoring the torque gradient, calculated based on Torque and Angle distance measurements. The Angle distance parameter is set according to the specified hardness of the joint.
SSD - Stick Slip Detection
This step monitor detects and reports stick slip effects during a step. The detection is done by counting the number of times the torque falls below the Trigger Level. If the number of times is larger than Maximum Number of Oscillations then the stick slip error is reported. The monitor operates in two different modes, Dynamic or Fixed. The difference between the modes is the way that the Trigger level is calculated.
Dynamic Torque: Trigger Level is dynamically calculated as Peak Torque Percentage of the current max torque, which has been achieved so far during the monitoring. The monitoring is started as soon as the torque passes the Trigger Torque.
Fixed Torque: Trigger Level is the fixed Trigger Torque specified by the user. In this mode the percentage is not needed.
If the torque never reaches the Trigger Torque then the monitoring is not started, this will result in status NOK.
PrT - Prevailing Torque
The monitor calculates the prevailing torque value in the Window Length and checks that it is between the Torque limits. The Angle Window starts at the angle degrees set in Start Angle in reverse direction from the shut-off point. This then spans for the angle degrees set in Angle Window Length in reverse direction. If Start Angle is left blank the angle window starts at the shut-off point. The calculated prevailing torque value is the mean or peak torque value (depending on the parameter set by the user) during the Window Length. The calculated value is saved as result data Prevailing Torque Measured. If Torque compensation is set to On, the Prevailing Torque Measured will be subtracted from all torque result values in consecutive steps. Any previously calculated prevailing torque compensation values will no longer be subtracted from torque result values. If Torque compensation is set to No, no subtraction will be made in consecutive steps.
If the total angle of the step is less than the Start Angle plus Angle Window Length, then the monitor will report NOK.
Prevailing torque can be measured as an average of measured values, or at peak torque. To choose between these two modes, set the Use Value parameter to either Mean torque (for average values), or Peak torque (for peak value).
Ti – Time
Measures the elapsed time during the monitor and checks that it is between the time limits. The time measurement starts at the start of the monitor and, if the Trigger Torque is specified, at the point where the torque passes Trigger Torque for the first time during the monitor.
Cl – Click
Monitor to enable click torque and click angle results. This monitor has no settings, and can only be used in conjunction with the MWR step.
Restrictions
To make sure the tightening stops if something unexpected happens, it is possible to add restrictions to the multistep tightening program. These restrictions could, for example, test that a maximum torque is not reached or that a part of the multistep tightening does not take too long to run. Each step has its own set of mandatory step restrictions and optional step restrictions. The mandatory restrictions are included when dragging a new step to the multistep program. All steps can have up to four restrictions each.
The following restrictions are automatically added to every step that is added to the multistep tightening program.
Step Restriction | Applicable steps |
---|---|
Step Restriction Maximum Time | All |
Step Restriction Maximum Torque |
|
Step Restriction Maximum Angle |
|
Ti – Maximum Time
This restriction checks the time. If Maximum Limit is reached, the tool is stopped immediately.
A – Maximum Angle
This restriction measures the angle. If the measured angle reaches the Maximum Limit the tool is stopped immediately. The angle is measured from the start of the restriction or, if specified, from the point where the torque passes Torque Trigger for the first time during this step.
Parameter | Description |
---|---|
Trigger Torque | If specified, this is the torque from where the angle is measured. |
Maximum Limit | If this limit is reached the tool is stopped immediately. |
T - Maximum Torque
This restriction checks the torque and if the measured torque exceeds the Maximum Limit, the tool is stopped immediately.
CTh – Cross Thread
This restriction checks the angle from the point where torque passes Start Torque (T1) to the point where the torque passes End Torque (T2). If the angle measured from Start Torque (T1) is higher than Maximum Angle Limit (Amax), the tool is stopped immediately.
When the torque passes End Torque (T2), the measured angle is checked against the limit Minimum Angle Limit (Amin). If the angle is lower than this limit, the tool is stopped immediately.
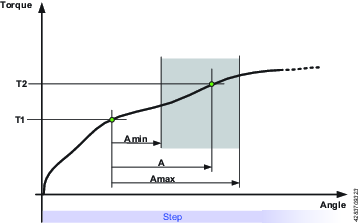
RT - Rescinding Torque
This restriction checks the torque, and if the measured torque is lower than the Rescinding Torque Limit the tool is stopped immediately and the program jumps to the end. For the restriction to be active, the torque must first exceed 110 % of the Rescinding Torque Limit.
Cable tools have the option of choosing Rescinding Torque for Angle. This restriction is controlled by two parameters: Percentage and Time Below Limit. Percentage sets the downward deviation from the last peak torque, and Time Below Limit sets the duration (between 5 and 500 ms) of that deviation. Only when both conditions (equal to or lower than the indicated percentage for the set duration) are met, will the program be interrupted and jump to the end.
TG - Torque Gradient
This restriction checks the gradient and if it is outside the Gradient limits, the tool is stopped immediately and the program jumps to the end. The first gradient is calculated Angle Window after Trigger Torque has been reached, and then a new gradient is calculated every time a new torque and angle sample is available.
If the end of the step is reached before passing Trigger Torque this restriction is considered OK and no tightening errors are reported.
TCD - Torque vs Current Deviation
This restriction verifies that all current measurements converted to the corresponding torque are, at most, the Maximum deviation away from the actual torque measured with the torque transducer. The restriction starts when the torque reaches Trigger Torque for the first time during the step and is active until the step reaches its target.
If Trigger Torque is never reached, the monitor will report OK.
TAW - Torque in Angle Window
This restriction checks that the measured torque in the Angle Window Length is between the Torque limits. If the measured torque is outside the limits the tool is stopped immediately and the program jumps to the end. The Angle Window Length starts at the Start Angle from the point that the torque first passed the Trigger Torque. If Trigger Torque is not set, then the Start Angle begins at the start of the restriction.
If the end of the Angle Window Length is not reached, the status of the restriction is NOK.