Bolt Tensioning Pump
Electrical Pump
Product Information
General Information
Safety Signal Words
The safety signal words Danger, Warning, Caution, and Notice have the following meanings:
DANGER | DANGER indicates a hazardous situation which, if not avoided, will result in death or serious injury. |
WARNING | WARNING indicates a hazardous situation which, if not avoided, could result in death or serious injury. |
CAUTION | CAUTION, used with the safety alert symbol, indicates a hazardous situation which, if not avoided, could result in minor or moderate injury. |
NOTICE | NOTICE is used to address practices not related to personal injury. |
Warranty
Product warranty will expire 12+1 months after dispatch from Atlas Copco's Distribution Center.
Normal wear and tear on parts is not included within the warranty.
Normal wear and tear is that which requires a part change or other adjustment/overhaul during standard tools maintenance typical for that period (expressed in time, operation hours or otherwise).
The product warranty relies on the correct use, maintenance, and repair of the tool and its component parts.
Damage to parts that occurs as a result of inadequate maintenance or performed by parties other than Atlas Copco or their Certified Service Partners during the warranty period is not covered by the warranty.
To avoid damage or destruction of tool parts, service the tool according to the recommended maintenance schedules and follow the correct instructions.
Warranty repairs are only performed in Atlas Copco workshops or by Certified Service Partners.
Atlas Copco offers extended warranty and state of the art preventive maintenance through its ToolCover contracts. For further information contact your local Service representative.
For electrical motors:
Warranty will only apply when the electric motor has not been opened.
Website
Information concerning our Products, Accessories, Spare Parts and Published Matters can be found on the Atlas Copco website.
Please visit: www.atlascopco.com.
ServAid
ServAid is a portal that is continuously updated and contains Technical Information, such as:
Regulatory and Safety Information
Technical Data
Installation, Operation and Service Instructions
Spare Parts Lists
Accessories
Dimensional Drawings
Please visit: https://servaid.atlascopco.com.
For further Technical Information, please contact your local Atlas Copco representative.
Safety Data Sheets MSDS/SDS
The Safety Data Sheets describe the chemical products sold by Atlas Copco.
Please consult the Atlas Copco website for more information www.atlascopco.com/sds.
Country of Origin
For the Country of Origin, please refer to the information on the product label.
Dimensional Drawings
Dimensional Drawings can be found either in the Dimensional Drawings Archive, or on ServAid.
Please visit: http://webbox.atlascopco.com/webbox/dimdrw or https://servaid.atlascopco.com.
Overview
Unpacking and Storage
Open the package carefully to avoid damaging fixed accessories, for example, the gauge and the hydraulic connection. Check the contents of the package for obvious damage upon receiving. Check the contents against the delivery note. During transport, the oil filling tube will be plugged with a black cap. After unpacking and setting up the pump for use, replace the black cap with the orange cap.
Storage for less than two months:
Preferably in its original packaging and protected from the elements. If the original package is not available, store it covered with a plastic cover.
Storage for longer than two months:
Preferably in its original packaging, protected from the elements, with a heat sealed plastic cover.

Before storage, if there is any hydraulic oil in the tank, either empty the tank or add a label on the pump showing that it contains oil.
Product Description
The SP1500 is a portable and automatic hydraulic pump which has been designed for tightening bolts by tensioning process in an industrial environment. It can quickly reach high pressures, significantly saving time in assembly operations. The SP1500 must only be used for the purpose for which it is intended and not for any other purposes not listed in this manual.
One of the features of the SP1500 hydraulic pump is that it can be totally remote-operated using the remote control.. The processes of switching on-off, raising pressure, circuit relief and maintaining the work pressure are always carried out using the remote control. This means that the same operator who inspects the tightening operation can also operate on the pump according to the needs of the tightening process being carried out.
The SP1500 pump is designed to work "continuously" so that once the operator selects the pressure of work and this pressure is achieved by the pump, the machine compensates the possible pressure drops in the circuit due to dilatations or small leaks, therefore maintaining the initially selected pressure.
The SP1500 portable hydraulic pump is a tool designed to work in adverse environmental conditions. To ensure its durability, the tool has an IP-54 degree of protection.
In addition, it is equipped with an oil gauge, temperature control, and light signals in the control box of the hydraulic pump to guarantee a correct and safe use.
The hydraulic pressure pump is a compact electro-mechanical kit, developed to facilitate its use in different sites. It consists of the following parts:
Submerged electrical motor
Gear pump
Directional solenoid valve
Manifold and secondary solenoid valve
Pressure gauge
Remote control handgrip
Control box
Protective steel frame
Hydraulic oil tank
Pressure regulating manual valve
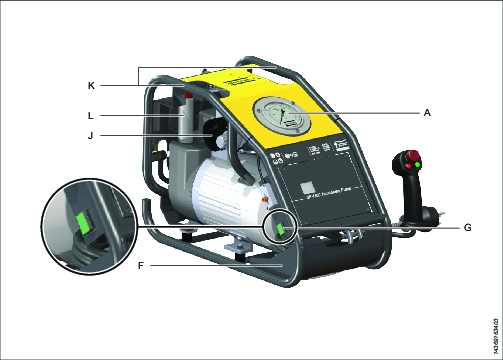
A: Pressure gauge | G: Main supply switch |
F: Cable rack | J: Filter |
K: Carrying handle | L: Filling tube |
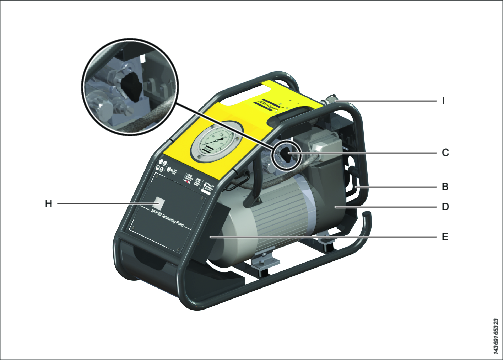
I: Hose connectors | C: Regulating pressure valve |
B: Lifting handle | D: Oil tank |
H: Display | E: control box |
A logic module manages the control of the whole system. It is installed inside the control box.
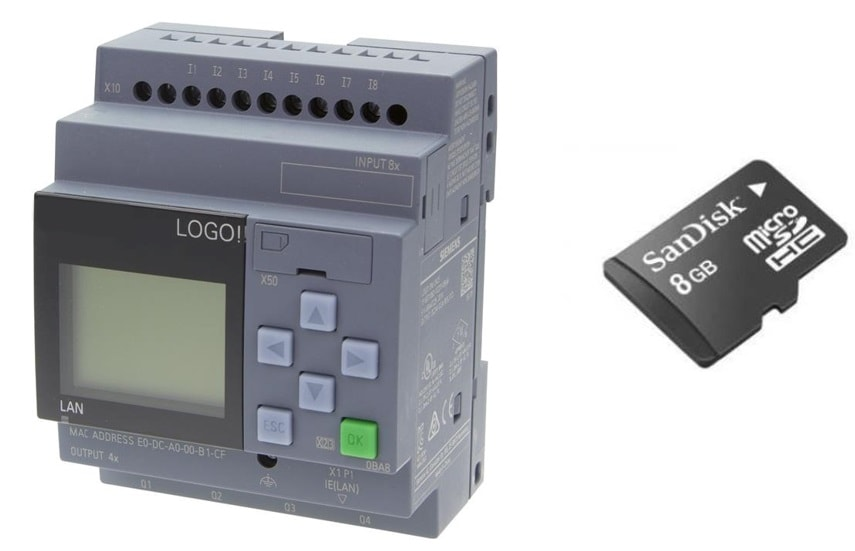

A: Emergency stop switch | B: Stop and pressure release button |
C: Start and pressure rise button |
Operating Conditions
Reading the present manual is highly recommended to carry out correctly the transport, installation, commissioning, use, regulation, assembly, disassembly and maintenance of the hydraulic pump.
This manual is an integral part of the supplied product; the buyer is responsible for enforcing its careful reading to all the personnel involved with the equipment and those, for any reason, who have to use it or intervene on it. The hydraulic pressure pump is a piece of equipment suitable for its industrial use, in association with bolt tensioners. The hydraulic pressure pumps described in this manual are not suitable for domestic use or similar use; therefore they must not be within reach of children or, in general, of people without expertise in installation, operation and maintenance.
The contents of this manual correspond to the “Commercial Type” pump application. Other similar pumps supplied by order can have variations with regards to the instructions contained on this manual. The manufacturer does not assume any responsibility for possible injuries to people, animals or damages to goods, caused by not strictly following all the recommendations contained in this manual. For safety reasons and to ensure the conditions of the warranty, it is absolutely prohibited to use it in case of a breakdown or variations in the performance of the pressure pump. To obtain subsequent information, contact Atlas Copco local service or sales representative.
The standard pressure pump has NOT been manufactured to be used in explosive environments or to be installed in areas classified as with explosion risk. To work in classified areas, the manufacturer or the dealer must be contacted and there must be equipment available with flame proof characteristics, codified in the pressure pump plate that satisfy the classification demands of the installation zone.
Product data
Description | SP-1500-115 |
---|---|
Current supply | 110 V (Monophase) |
Frequency | 60 Hz |
Power | 1.8 kW |
Rated current | 18 A |
Starting power | 4.5 x 18A |
cos φ | 0,94 |
Flow 1st pressure* | 2,73 (l.p.m) |
Flow 2nd pressure** | 0,27 (l.p.m) |
Turning speed | 3420 rpm |
Oil Tank capacity | 4,7 litres |
Available volume | 1,7 litres |
Empty weight | 39.5 kg |
Max Pressure | 1.500 bar |
Noise level | 85 dB |
IP rating | IP54 |
Use temperature range | -200- 550 (See note) |

*Oil flow below 1/10 of the set pressure.
**Oil flow above 1/10 of the set pressure.
Height | 400 mm |
Width | 280 mm |
Length | 570 mm |
Very low TRA Ambient (<-15˚C) | - |
Low TRA Ambient (-15˚C<T<0˚C) | Maximizer 15 |
Normal TRA Ambient (0˚C<T<25˚C) | Maximizer 32 |
High TRA Ambient (25˚C<T<50˚C) | Maximizer 68 |

The hydraulic pump has a submerged electrical motor, so the hydraulic oil achieves the optimal operating temperature about 10 to 15 minutes after the motor starts working. It is always recommended to start the hydraulic pump and leave it working without pressure for 10 to 15 minutes to improve its performance.
It is necessary to use special hydraulic oil to facilitate cold start. See also Hydraulic fluids, when working at temperatures lower than -20ºC (down to -30ºC).
The display of the logic module is not able to show any text when it is working at very low temperatures, but both the logic module and the hydraulic pump continue operating as usual. The movement of the pressure gauge needle can be slower due to the higher viscosity of fluid.
Technical Product Data
Technical Product Data can be found on either ServAid, or the Atlas Copco website.
Please visit: https://servaid.atlascopco.com or www.atlascopco.com.
Service Overview
Hydraulic Fluid
The behaviour “In-service” of hydraulic equipment heavily depends on the quality and characteristics of the hydraulic fluid selected. The choice of the specification and viscosity of the hydraulic fluid should be based on the conditions of use, taking into account several factors as follows:
The range of environmental temperature.
The range of oil viscosity defined for the equipment.
The application (range of pressures, sources of contamination of the hydraulic fluid, the type of pump…)
The ease of getting a proper replacement or equivalent hydraulic fluid.
In general, hydraulic fluids recommended for this kind of portable hydraulic equipment should be manufactured under these specifications:
AFNOR NF E 48-603 HV
ISO 6743/4 HV
DIN 51524/ P3 HVLP
It is always recommended to use fluids with a high viscosity index fluid (V.I. > 140) to ensure a good stability under a wide range of temperatures. The user could cover a wide range of temperatures using the high V.I. TOTAL Equivis ZS or, Maximizer fluids. Refer below given chart for the hydraulic oil selection
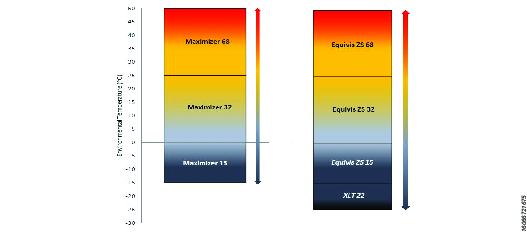

For Artic Climates, we recommend a fluid such as the TOTAL XLT 22, which allows for a good start-up below -20ºC. For applications with critical conditions of service, environmental restrictions, or similar, please contact Atlas Copco to select the appropriate hydraulic fluid for each service.
Installation
Main Supply Requirements
The SP1500 hydraulic pump has a single phase motor with a power of 1.8 kW. It generally requires the use of autonomous generators because the applications of this machine are usually in the field, with no connection to the mains supply.
Because of the peak in power consumption that occurs during the starting up process, a minimum power of 16 kVA is required; 20-30 kVA generators, that provide a more stable service, are usually used for this kind of applications.
Bear in mind that the length of cable used to connect the pump is a determining factor in applications for the wind power sector, as it normally exceeds 80 meters from the power supply to the pump. The voltage drop must be limited, as it can cause malfunction of the pump. Check the following table for advice on the section of power cable recommended for keeping the voltage drop below 5%:
Cable length (m) | Standard Section(mm2) |
---|---|
15 | 4 |
25 | 6 |
50 | 10 |
75 | 16 |
100 | 25 |
125 | 25 |
150 | 25 |
Electrical Installation
Before connecting the equipment:
Check the cables for damage. Cables must be free from erosions or scrapings.
All the connections must be carried out with elements standardized for this purpose, marked with their electrical characteristics which must agree with the characteristics of the power supply and the pressure equipment.
Check that the voltage indicated on the pump ID plate matches the power lead voltage.
If it is necessary to replace the power cable, make sure to assemble correctly and carefully.
Before assembling, replace its insulating sheath.
Adjust the relevant screws, equally if the plug is replaced.
Check that the union is perfectly insulated and protected from humidity.
Any improper or unauthorized handling of the control box and its internal components can lead to the loss of the warranty and the manufacturer’s responsibility. For this reason, it is recommended to send the equipment to the distributer or contact Atlas Copco Service centers.
Hydraulic Installation
Make sure that the pump is disconnected from the main supply.
Connect one end of the hose to the pump.
Hydraulic connector Lay the hoses down in a way that they cannot be forced or damaged and out of the passing vehicles area. Always respect the minimum curve radius of 175 mm of the hose.
Use the hoses and connection elements of the recommended characteristics and without any wear and tear (worn exterior coat, bents, deformed, worn out or rusty connectors, etc.).
The pump is supplied ready for use with the exception of the hydraulic oil.
Before every use, make sure that the pump tank is filled with the adequate amount of oil. If necessary, fill the tank only with oil with the recommended characteristics always respecting the minimum and maximum level. See also sections Hydraulic Fluid and Maintenance and Conservation Program.

Wear protective gloves, eliminate any spillage immediately and clean the surfaces with degreaser.
Operation
Ergonomic Guidelines
Consider your workstation as you read through this list of general ergonomic guidelines to identify areas for improvement in posture, component placement, or work environment.
Take frequent breaks and change work positions frequently.
Adapt the workstation area to your needs and the work task.
Adjust for a convenient reach range by determining where parts and tools need to be located to avoid static load.
Use workstation equipment such as tables and chairs appropriate for the work task.
Avoid work positions above shoulder level or with static holding during assembly operations.
When working above shoulder level, reduce the load on the static muscles by lowering the weight of the tool, using for example torque arms, hose reels or weight balancers. You can also reduce the load on the static muscles by holding the tool close to the body.
Take frequent breaks.
Avoid extreme arm or wrist postures, particularly during operations requiring a degree of force.
Adjust for a convenient field of vision that requires minimal eye and head movements.
Use appropriate lighting for the work task.
Select the appropriate tool for the work task.
In noisy environments, use ear protection equipment.
Use high-quality inserted tools and consumables to minimize exposure to excessive levels of vibration.
Operating Instructions
Operating Instructions
The SP1500 pump is designed to work with hydraulic tensioners. Before operating the pump, verify the maximum pressure of the tensioner and the hose, as well as compatibility between the connectors.
ALWAYS check the general state of the equipment before connecting it to the main supply, to detect possible damages, both in the pump and in the hydraulic circuit.
Verify that the hydraulic circuit is properly closed and that the tightening devices are correctly placed on the bolts to be tightened.
Check that the personnel involved in the tightening process is on alert and wear adequate personal protective equipment.
Connect the pump to the main supply. Note that when using an autonomous generator unit, it must provide a minimum of 16 KVA. Refer to the section Main Supply Requirements for details.
Make sure that the emergency stop switch is released.
Turn the regulating pressure valve counterclockwise to make sure that at the start up moment the pressure does not rise to an undesirable value.
Turn on the hydraulic pump: Turn the motor on by pressing the GREEN Button. The pump will be running on idle, ready to build the pressure.
Set the working the pressure: To regulate the target pressure, press and hold the GREEN Button of the pendant and turn the pressure regulating valve progressively clockwise. Raise the pressure until the required value is reached.
Once the working pressure has been adjusted, the pump can be operated in two ways:
CONTINUOUS MODE: The pump remains on and automatically compensate the pressure drop on the circuit due to expansion or small leaks. This operational mode can be used by a CONSTANT pressure of the GREEN button.
STATIC MODE: When the pump has reached the working pressure, press the GREEN button every so often for the intensifier to compensate the pressure.
To relieve the pressure of the circuit:
While the pump is turned on, press the RED button of the pendant to activate the relief valve, which lets the oil return to the tank. The valve remains open for 2 seconds in this mode to let the oil return. After that, the valve stops being activated and the motor remains running on idle.
The pressure is also relieved during the time the RED button is kept pressed. This is useful when the 2 seconds pre-set are not enough for the tensioners to retract the whole stroke.
Press the emergency stop switch at any time. While in this state, the alarm of the control box will be activated, the blinking screen of the logic module in red color. The pump remains in this mode for 6 seconds, relieving the pressure and after that time the motor will turn off.
To turn off the hydraulic pump:
Turn the pump off by pressing the RED button a second time after pressure relieve.
Upon pressing the emergency stop switch, the hydraulic pump will turn off after it is relieve of pressure during 6 seconds.
Service
Maintenance Instructions
General concept
Before any intervention, unplug the pump from the main and make sure that the equipment cannot be switched on accidentally. Depressurize the whole hydraulic system prior to any disassembly.
Oil change intervals
Portable hydraulic equipment are susceptible to contamination due to the extreme conditions in which they work. Although selected fluids are designed to suffer less degradation than another product, we recommend an oil change and filter at least every 750 hours of use, or once a year, whichever occurs first.
It is recommended to periodically check the color of the oil and level seeking extreme contamination or loss of oil level that will require to refill the tank.
For oil changes or refilling, it is always recommended to use the same oil in the pump.
In case of an emergency and having to refill the tank and mix different types of fluids, it is preferred to use fluids with no additives as the HL or HLP fluids. After that, and always before a period of 2-4 working days, replace the oil with recommended oils.
Maintenance and Conservation Program
The checking and operations maintenance program depends on the equipment working conditions. The frequencies indicated here are only an orientation and it is for the user to adapt them to the conditions of use.
Frequency | Verification / Task to be carried out |
---|---|
Prior to each use | Check that the oil level in the tank is between maximum and minimum indicators. Set zero pressure and 100% pressure and check for noise (absence of friction, tapping, etc.) Check for leaks when the pressure is 150 bar. |
Monthly | Check that the pump reaches the maximum pressure. Check condition of power cable, free of erosion, joints, etc. Check hydraulic hoses and couplings. Replace if there is any damage. |
After 200 hours of use | It is recommended to perform a complete maintenance check. Consult your local Atlas Copco sales representative directly. |
Total hours of use since the last pump maintenance can be checked as follows:
Remove the lid of the control box to gain access inside by using a 2.5 mm allen key to remove 4 screws. Be aware of the earth cable attachment behind the lid.
To continue in the menu, press and hold the “ESC” and “down” arrows again. If the breaker is up, the display will show a message: “Disarm breaker to enter service menu”.
Screen of the logic module SP1500 hydraulic pump. Disarm system Once the breaker is disarmed, the screen shows information about the firmware. Press and hold “ESC” + ”down” arrow + “RED button” in the handgrip. Now, total hours and cycles is showed.
Logic module If you continue pressing “ESC”+”down” arrow, you can see maintenance counter since last maintenance, oil filter counter and oil counter.
To go back to the main screen, press “ESC”+ “UP” arrow several times. A re-arm warning screen will appear before the main screen is reached. Re-arm the breaker and the main screen is shown.
SP1500 hydraulic pump. Re-arm system

When re-placing the control box lid, be careful not to trap the earth wire.
Service Recommendations
Preventive maintenance is recommended at regular intervals. See the detailed information on preventive maintenance. If the product is not working properly, take it out of service and inspect it.
If no detailed information about preventive maintenance is included, follow these general guidelines:
Clean appropriate parts accurately
Replace any defective or worn parts
Troubleshooting
Hydraulic Pump does not raise the pressure
Check that the pump is properly connected to the main supply.
Check that there is no sign of alarm in the control box.
Check for leaks in the circuit.
Check if right oil is used as per ambient temperature.
If the pump does not raise the pressure, contact local Atlas Copco sales representative.
Changing the Oil Filter
It is recommended to replace the oil filter at every oil change or at 1 year intervals along with the oil. If the oil is contaminated, change both oil and filter immediately.
Unscrew the oil filter (A) by turning it counterclockwise.
Grease the joint of the new filter.
Screw the new filter clockwise back onto the pump.
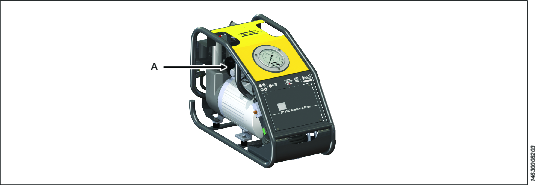
Changing the Hydraulic Oil
It is recommended to change the hydraulic oil after 750 operation hours or after one year depending on what occurs first.
Remove the oil cap from the top of the oil filling tube.
Loosen the plug at the bottom of the tank by using the allen key.
Put back the plug after draining the oil.

If the oil has a dark color, any traces of foam or particles, change both the oil and the filter immediately. Otherwise, the pump could be damaged.
Pay attention to the characteristics of the oil. In case of doubt, contact local Atlas Copco sales representative to avoid using the wrong oil.
Oil Level Alarm Turns On
Check that the hydraulic liquid level is in between the minimum and the maximum oil marking level.
Minimum level | Maximum level |
---|---|
![]() | ![]() |
Update the Firmware with a Memory Card
Updating the firmware of the logic module is quite easy. Only a specific memory card and the firmware file are needed.
Remove the lid of the control box to gain access inside by using a 2.5mm allen key to remove 4 screws. Be aware of the earth cable attachment behind the lid.
Insert card in according with version of the logic module. Ensure the micro SD is inserted in the correct orientation, otherwise the firmware will not update.
Logic module Logic module Insert microSD and close the Switch off the pump in the switch at the side of the control box or unplug the pump from the mains supply.
Switch ON the pump with the main supply switch, after plugging the pump back into the mains supply. The update is done in this moment, you can remove the card.
Temperature Alarm Turns On
After a very intensive use, the pump may suffer an excessive increase in the hydraulic fluid temperature, accentuated if the drop of voltage in the current supply is above 5%. In that case (oil temperature > 85° C) turn off the pump and let it cool. Once the temperature of the pump falls, start working again as usual.
Alarms
The SP-1500 pump is equipped with a display which shows following alert messages and the machine status:
At the start
At the start-up of the pump, the main screen shows the following information:
Pump model
Atlas Copco web address
Working
When the pump is running, the screen could show different alarms described below:
Temperature
Screen on the logic module
The pump will automatically shut off and allow for the pump temperature to cool. The pump does not automatically restart, the message will carry on blinking in the screen until cool. At this point the pump can be restarted manually.
Oil Level
Screen alarm oil level
Check the oil level and refill it if necessary. See the section Oil Level Alarm Turns On. The screen will return to normal once the adequate oil level required is reached.
Oil and temperature Level
Screen on the logic module
If the alarm is showed in the display, check the harting connection (A), because it could be disconnected. If this connection is correct and the message does not disappear, you must contact your local Atlas Copco Sales representative.
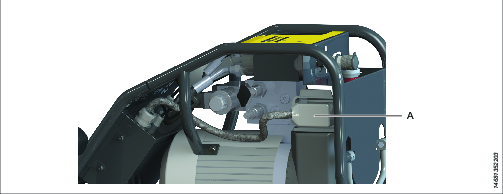
Current supply fault
Screen on the Logic Module
There is a safety switch which protects the control box and the motor. If there is a severe current supply fault, the switch turns off. In this case, you have to re-arm the breaker. If the cover of the control box is still removed, this can be done by flipping up the safety switch OFF, or by sliding the lever downwards on the side of the control without opening the control box.
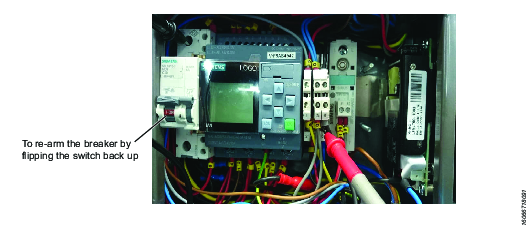
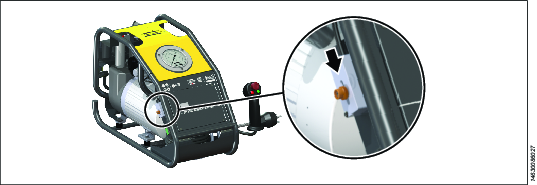
If there are 5 current supply fault alarms in less than 5 minutes, the display shows the message during 5 minutes (see the picture below). Verify power of the generator and section cable recommended (see section Main Supply Requirements) and check voltage between terminal 6 (B) and input pin (A) of the circuit breaker before working. This voltage should be 230V or 110V according to the configuration of the pump. Otherwise, contact Atlas Copco Distributer or Sales representative.

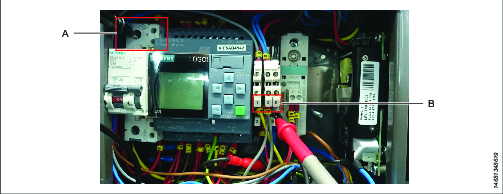
Emergency button
Screen on the logic module
The emergency stop switch of the handgrip is pressed. Investigate the cause of the stop and take relevant actions. Release the emergency stop switch before operation.
Oil Service
Every 750 operation hours from maintenance, a message in the blinking red screen appears when the pump is connected to main supply: "Oil Service". Change the oil and filter of the pump.
Recycling
Environmental Regulations
When a product has served its purpose it has to be recycled properly. Dismantle the product and recycle the components in accordance with local legislation.
Batteries shall be taken care of by your national battery recovery organization.