Parameters for Four Step Tightening - Start Stage
The time, torque and angle are monitored during the start step. This step has an angle as target.

The graphical representation is used in the documentation to describe the configuration setting and the interpretation of the parameter values. The graphs are not used in any GUI.
The step is defined from trigger pressed until the specified target angle is reached.
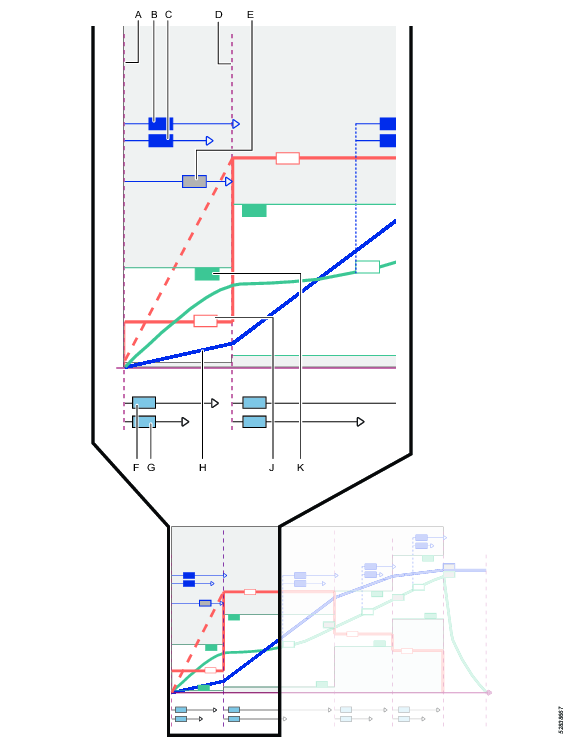
A | Trigger pressed |
B | Angle max (monitor) |
C | Angle min (monitor) |
D | End of start step |
E | Target angle for start step |
F | Time min (monitor) |
G | Time max (monitor) |
H | Angle curve |
J | Speed curve |
K | Torque max value (monitor) |

The tables list all available parameters. Some parameters are only available and visible for certain functions.
Parameter | Description | Default value |
---|---|---|
Direction | Rotation direction for the tightening. CW: Clockwise CCW: Counter clockwise | CW |
Current monitoring | Off: Current monitoring is disabled and the tool torque is measured by the torque sensor. On: the current is measured at final torque target and converted to a torque value. The calculated torque is compared to the measured torque. If the difference is within 10%, the tightening is considered OK | |
True angle compensation | Switch with On or Off position. | Off |
Negative | Only visible if True angle compensation = On. Defines the maximum negative rotation of the tool. If the value is exceeded the tightening is terminated and an error is reported. This is expressed in a numeric angle value. | 30 |
Positive | Only visible if True angle compensation = On. Defines the maximum positive rotation of the tool. If the value is exceeded the tightening is terminated and an error is reported. This is expressed in a numeric angle value. | 30 |
Attachment tuning enabled | Yes No | No |
Parameter | Description | Default value |
---|---|---|
Soft start | On: The soft start allows a smooth start at slow speed. It is used to engage the thread. Off: The tool speed ramps up to the rundown speed as quickly as possible. | On |
Speed | Defines the speed during Soft start. | 34 |
Angle | Target angle for the step. End of step is defined at this point, when the target has been reached. | 90 |
Angle min | Monitors the angle value and checks that the result is within the limit. | 70 |
Angle max | Monitors the angle value and checks that the result is within the limit. | 110 |
Torque min | Defines the lower torque limit during Soft start. If Torque min falls below the limit, the tightening is aborted and an error message is issued. The tightening will be considered NOK. | 0.00 |
Torque max | Defines the upper torque limit during Soft start. If Torque max is exceeded, the tightening is aborted and an error message is issued. The tightening will be considered NOK. | 1.25 |
Time min | Minimum time for the step. measured from trigger pressed. Expressed in a numeric millisecond value. | 100.00 |
Time max | Maximum time for the step. measured from trigger pressed. Expressed in a numeric millisecond value. | 500.00 |
Use attachment tuning | Yes No | No |
Gear ratio | Only visible if Use attachment tuning is set to Yes. Min/Max values: 0.5/4.0 Gear ratio is needed to compensate the angle and torque. The Gear ratio will affect the max speed and max torque of the tool. ![]() When switching between the parameter Use attachment tuning Yes/No, the values of the Gear ratio are not reset to default values. | 1.00 |
Efficiency tuning | Only visible if Use attachment tuning is set to Yes. Min/Max values: 0.5/1.0 Sets the efficiency loss for the attachment. Gear ratio combined with Efficiency tuning is needed to compensate the torque. ![]() When switching between the parameter Use attachment tuning Yes/No, the values of the Efficiency tuning are not reset to default values. | 1.00 |