Produktinformation
Allgemeine Informationen
NICHT WEGWERFEN - AN BENUTZER WEITERLEITEN
Bestimmungsgemäße Verwendung
Nur zum Gebrauch durch ausgebildete Fachkräfte.
Dieses Produkt und sein Zubehör dürfen in keinem Fall modifiziert werden.
Benutzen Sie dieses Produkt nicht, wenn es beschädigt ist.
Wenn die Produktdatenschilder oder Gefahrenwarnschilder unleserlich werden oder sich ablösen, sind diese sofort zu ersetzen.
Das Produkt darf nur von ausgebildeten Fachkräften bedient und gewartet werden.
Sicherheitsbezogene Signalwörter
Die sicherheitsbezogenen Signalworte Gefahr, Warnung, Vorsicht und Hinweis haben folgende Bedeutung:
GEFAHR | GEFAHR weist auf eine gefährliche Situation hin, die bei Nichtvermeidung zu schweren Verletzungen mit möglicher Todesfolge führen wird. |
WARNUNG | WARNUNG weist auf eine gefährliche Situation hin, die bei Nichtvermeidung zu schweren Verletzungen mit möglicher Todesfolge führen könnte. |
VORSICHT | VORSICHT weist bei Verwendung mit dem Sicherheitswarnsymbol auf eine gefährliche Situation hin, die bei Nichtvermeidung zu leichten oder mittelschweren Verletzungen führen könnte. |
HINWEIS | Ein HINWEIS wird für Situationen verwendet, die sich nicht auf eine mögliche Verletzungsgefahr beziehen. |
Garantie
Die Produktgarantie läuft 12 Monate nach dem ersten Einsatz des Produkts ab, aber in jedem Fall spätestens 13 Monate nach Auslieferung.
Normaler Verschleiß von Teilen wird nicht von der Garantie abgedeckt.
Unter normalem Verschleiß versteht man, dass während der für diesen Zeitraum typischen Standardwerkzeugwartung Teile ausgetauscht oder Einstellungen / Verbresserungsarbeiten durchgeführt werden müssen (ausgedrückt in Zeit, Betriebsstunden, oder anderweitig).
Die Produktgarantie stützt sich auf einen korrekten Einsatz, Wartung und Reparatur des Werkzeugs und seiner Bestandteile.
Schäden an Teilen, die als Folge einer unzureichenden Wartung oder eines falschen Einsatzes durch andere Parteien als Atlas Copco oder deren zertifizierten Service-Partner während der Garantiezeit verursacht werden, sind nicht durch die Garantie gedeckt.
Um eine Beschädigung oder Zerstörung von Werkzeugteilen zu vermeiden, warten Sie das Werkzeug entsprechend der empfohlenen Wartungspläne und befolgen Sie die richtigen Anweisungen.
Garantiereparaturen werden nur in Atlas Copco-Werkstätten oder von einem zertifizierten Service-Partner ausgeführt.
Atlas Copco bietet eine erweiterte Garantie und eine vorbeugende Wartung nach dem neuesten Stand der Technik durch seine ToolCover-Verträge. Weitere Informationen erhalten Sie von Ihrem lokalen Servicerepräsentanten.
Für Elektromotoren:
Die Garantie gilt nur dann, wenn der Elektromotor nicht geöffnet wurde.
ServAid
ServAid ist ein Portal, das ständig aktualisiert wird und technische Informationen bietet, wie z.B.:
Behörden- und Sicherheitsinformationen
Technische Daten
Installations-, Betriebs- und Wartungsanweisungen
Ersatzteillisten
Zubehör
Maßzeichnungen
Besuchen Sie: https://servaid.atlascopco.com.
Weitere technische Informationen erhalten Sie bei Ihrem Atlas Copco-Vertreter vor Ort.
Sicherheitsdatenblätter MSDS/SDS
In den Sicherheitsdatenblättern werden die von Atlas Copco vertriebenen chemischen Produkte beschrieben.
Weitere Informationen finden Sie auf der Internetseite von Atlas Copco unter www.atlascopco.com/sds.
Herkunftsland
Informationen zum Herkunftsland sind auf dem Produktetikett angegeben.
Maßzeichnungen
Maßzeichnungen finden Sie entweder im Maßzeichnungsarchiv oder auf ServAid.
Besuchen Sie: http://webbox.atlascopco.com/webbox/dimdrw oder https://servaid.atlascopco.com.
Übersicht
Technische Produktdaten
Technische Produktdaten finden Sie entweder auf ServAid oder auf der Internetseite von Atlas Copco.
Besuchen Sie: https://servaid.atlascopco.com oder www.atlascopco.com.
Service-Übersicht
Wartungsempfehlungen
Es wird empfohlen, eine vorbeugende Wartung regelmäßig durchzuführen. Beachten Sie die ausführlichen Informationen über die vorbeugende Wartung. Wenn das Produkt nicht ordnungsgemäß funktioniert, bringen Sie es außer Betrieb und prüfen Sie es.
Wenn keine detaillierten Informationen über eine vorbeugende Wartung enthalten sind, befolgen Sie die folgenden allgemeinen Richtlinien:
Entsprechende Teile gründlich reinigen
Defekte und verschlissene Teile ersetzen
Bedienung
Ergonomie-Richtlinien
Betrachten Sie Ihren Arbeitsplatz, während Sie diese Liste mit allgemeinen Ergonomie-Richtlinien lesen, und versuchen Sie, Bereiche zu identifizieren, in denen Verbesserungen in Bezug auf Körperhaltung, Positionierung der Komponenten oder Arbeitsumgebung möglich sind.
Legen Sie regelmäßige Pausen ein und wechseln Sie regelmäßig die Arbeitshaltung.
Passen Sie den Bereich um Ihre Arbeitsstation Ihren Anforderungen und den auszuführenden Arbeiten an.
Positionieren Sie Teile und Werkzeuge so, dass statische Belastungen möglichst vermieden werden und sich sämtliche Arbeitsmittel bequem erreichen lassen.
Verwenden Sie an Ihrer Arbeitsstation für die Aufgabe geeignete Tische, Stühle oder andere Gegenstände.
Vermeiden Sie während der Ausführung von Montagearbeiten Körperhaltungen über Schulterhöhe oder mit statischer Halteposition.
Wenn Sie über Schulterhöhe arbeiten müssen, verringern Sie die auf die statischen Muskeln wirkende Belastung durch Verringerung des Werkzeuggewichts. Setzen Sie hierzu beispielsweise Drehmomentarme, Schlauchaufroller oder Gewichtsausgleicher ein. Sie können die auf die statischen Muskeln ausgeübte Belastung auch reduzieren, indem Sie das Werkzeug nah am Körper halten.
Legen Sie häufig Pausen ein.
Vermeiden Sie extreme Arm- oder Handgelenkhaltungen, insbesondere während Arbeiten, bei denen ein gewisser Kraftaufwand erforderlich ist.
Richten Sie Ihren Arbeitsplatz so in Ihrem Sichtfeld ein, dass nur minimale Augen- und Kopfbewegungen erforderlich sind.
Verwenden Sie zur Ausführung Ihrer Arbeit eine angemessene Beleuchtungen.
Wählen Sie ein zur Ausführung Ihrer Arbeit angemessenes Werkzeug aus.
Tragen Sie in lauten Umgebungen einen entsprechenden Gehörschutz.
Verwenden Sie hochwertige Einsätze und Kleinteile, um eine übermäßige Vibrationsbelastung möglichst zu vermeiden.
Betriebsanleitung
Elektrische Anschlüsse
Stellen Sie sich sicher, dass die richtige Stromzufuhr verfügbar ist, um Motorschäden oder gefährliche elektrische Überlastungen zu vermeiden. Stellen Sie die auf dem Typenschild des Motors empfohlene Stromstärke bereit. Verwenden Sie die elektrischen Pumpe nicht, wenn der Stecker nicht geerdet ist.
Halten Sie Verlängerungskabel so kurz wie möglich und achten Sie darauf, dass sie einen entsprechenden Leitungsquerschnitt haben und geerdet sind.
Das Verlängerungskabel muss ein 10-AWG-Kabel sein.
Allgemeine Konfiguration
Alle unsere hydraulischen Drehmomentschlüssel werden komplett montiert und einsatzbereit geliefert. Mit dem hydraulischen Drehmomentschlüssel von Atlas Copco sollte ein Hydraulikaggregat von Atlas Copco verwendet werden, das für die Geschwindigkeit, den Druck und die Mobilität und dadurch für die optimale Effizienz und Präzision des Atlas-Copco-Systems sorgt.
Die Genauigkeit des hydraulischen Drehmomentschlüssels von Atlas Copco beträgt +/-3 % basierend auf unseren Herstellerangaben. Diese Genauigkeit ist durch Kalibrierprüfungen durch Atlas Copco oder durch eine andere qualifizierte Kalibrierstelle, deren Programm auf das National Institute of Standards and Technology (N.I.S.T) rückführbar ist, zertifiziert. Wir empfehlen dringend die Verwendung von durch Atlas Copco zertifizierten Messgeräten (mit Genauigkeitsklasse 1), um die Genauigkeit Ihres Verschraubungssystems zu verbessern.
Hydraulikanschlüsse
Unsere Hydraulikpumpen sind mit einem Null-Druckentlastungsventil ausgestattet. Allerdings könnte nach Abschalten der Pumpe die Einfahrseite weiterhin unter Druck stehen. Dieser eingeschlossene Druck verhindert, dass der Benutzer die Anschlussstücke an der Einfahrseite von Hand lösen kann. Um den Druck abzulassen, drücken Sie einfach den schwarzen Schalter auf dem Magnetventil. Alle Anschlussstücke sind frei und können von Hand angezogen werden.
Trennen oder verbinden Sie niemals Hydraulikschläuche und Hydraulikanschlüsse, ohne zuerst den Schlüssel und die Pumpe drucklos zu machen. Wenn das System über ein Manometer verfügt, vergewissern Sie sich mittels des Manometers, dass der Druck abgelassen wurde. Wenn Sie Anschlüsse mit Schnellkupplungen herstellen, vergewissern Sie sich, dass die Kupplungen vollständig einrasten. Gewindeanschlüsse, wie beispielsweise Anschlussstücke, Messgeräte usw., müssen sauber sein und sicher und leckagefrei angezogen werden.
Luftanschlüsse
Gewährleisten Sie für den Betrieb der Pneumatikpumpe einen ausreichenden Luftdurchsatz (58 bis 100 psi / 4 bis 7 bar). Ziehen Sie im Zweifelsfall den vom Pumpenhersteller empfohlenen Luftdurchsatz heran, bevor Sie die Pumpe unter Druck setzen. Durch einen falschen Luftdurchsatz kann der Pumpenmotor beschädigt werden.
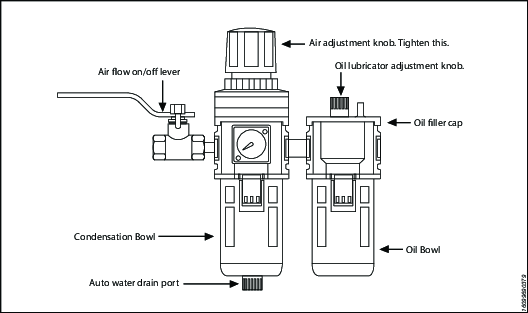
Beste Ergebnisse erzielen Sie mit Luftschläuchen mit einem Innendurchmesser von mindestens 3/4 Zoll.
Die Verwendung eines FRLs (Luftaufbereiters) wird dringend empfohlen. Mit Öl befüllen und den Luftzutritt mit dem Einstellknopf anpassen.
Betriebsdruck
Der maximale Betriebsdruck des Werkzeugs beträgt 10.000 psi (700 bar). Stellen Sie sicher, dass die gesamte mit diesem Werkzeug verwendete Hydraulikausrüstung (Pumpen, Schläuche, Kupplungen) auf einen Betriebsdruck von 10.000 psi (700 bar) ausgelegt ist. Schlagen Sie in der Dokumentation für die Hydraulikpumpe nach und vergewissern Sie sich, dass der Druck nicht 10.000 psi übersteigt.
Systemanschluss
Der hydraulische Drehmomentschlüssel und das Hydraulikaggregat von Atlas Copco werden durch eine Doppel-Schlauchanordnung mit einem Betriebsdruck von 10.000 psi (700 bar) verbunden. Der Sicherheitsfaktor des Hydraulikschlauchs von Atlas Copco beträgt 4/1. Bei jedem Doppel-Hydraulikschlauch muss eine Leitung aus Stecker-Stecker und die andere Leitung aus Buchse-Buchse bestehen, um eine ordnungsgemäße Interaktion zwischen Pumpe und Maschine zu gewährleisten. Schließen Sie den Doppel-Schlauch wie dargestellt an der Schwenktülle an:
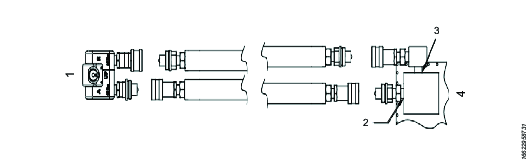
Referenz | Beschreibung |
---|---|
1 | Schraubenschlüssel |
2 | Port „A“ |
3 | Port „R“ |
4 | Pumpe |
Prüfen Sie alle Kupplungsverbindungen. Wenn das System unter Druck steht, können Sie die Kupplungen nicht mehr von Hand anziehen, und der Gebrauch von Werkzeugen führt zu Schäden an den Kupplungen.
Stellen Sie sicher, dass sämtliche Kupplungen korrekt und ohne Lücke zwischen der Manschette und dem Anschlussstück verbunden sind. Verwenden Sie keine Spanner oder andere Werkzeuge, um Kupplungen festzuziehen oder zu lösen.
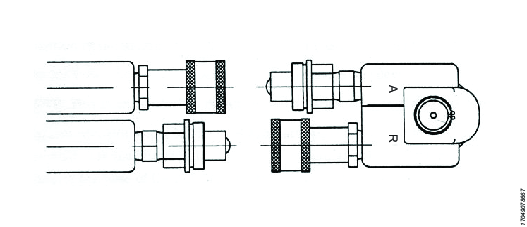

Stellen Sie sicher, dass die Kupplungen vollständig eingerastet und fest miteinander verschraubt sind.
Verwenden Sie niemals zwei Doppel-Hydraulikschläuche zwischen Pumpe und Maschine. In diesem Fall würde der hohe Druck an der Einfahrseite vorliegen und die Maschine nicht ordnungsgemäß funktionieren. Um eine Fehlfunktion des Werkzeugs zu vermeiden, die Kupplung nicht vertauschen. Versuchen Sie keinesfalls die Schwenktüllenbaugruppe zu lösen.
Verwenden der Hydraulikpumpe
Einstellen des Betriebsdrucks der Pumpe
Der Pumpendruck wird wie folgt eingestellt:
Lösen Sie den gerändelten Sicherungsring unter dem T-Griff am externen Druckregler der Pumpe. Drehen Sie dann den T-Griff gegen den Uhrzeigersinn, bis er sich frei und leicht drehen lässt.
Schalten Sie die Pumpe ein. Drücken Sie an der Fernsteuerung der Pumpe die „Vorwärts“-Taste (oder die Taste an der Luftpumpe) und halten Sie diese gedrückt.
Drehen Sie mit der Pumpe im „Vorwärts“-Modus langsam den T-Griff im Uhrzeigersinn. Der Druck am Manometer steigt an.
Stellen Sie den Regler immer so ein, dass dabei Druck aufgebaut wird und niemals umgekehrt. Stellen Sie niemals den Regler mit dem Werkzeug am Werkstück ein.
Wenn das Manometer 4.000 psi erreicht, drehen Sie den T-Griff nicht weiter und lassen Sie das Manometer einpendeln.
Wenn der Druck weiter ansteigt (über 4.000 psi), dann lassen Sie die „Vorwärts“-Taste los und senken Sie den Druck ab, indem Sie den T-Griff leicht gegen den Uhrzeigersinn drehen. Drücken Sie dann erneut die „Vorwärts“-Taste an der Fernsteuerung und bringen Sie den Druck langsam wieder auf 4.000 psi.
Wenn der Druck richtig eingestellt ist, dann schalten Sie die Pumpe aus und ziehen Sie den gerändelten Sicherungsring unter dem T-Griff an. Dadurch wird der Pumpendruck eingestellt, der das Ausgangsdrehmoment des Werkzeugs bestimmt.
Referenz
Beschreibung
A
Verschlussring
B
T-Griff
Wenn der Solldruck eingestellt und arretiert ist, lassen Sie die Pumpe nochmals laufen, um sicherzustellen, dass sich die Druckeinstellung beim Anziehen des gerändelten Sicherungsrings nicht verändert hat.
Verwenden des Drehmomentschlüssels
Wenn Sie den Solldruck eingestellt haben, lassen Sie das Werkzeug drei oder vier Mal auf vollem Druck laufen. Dadurch wird sichergestellt, dass das System ordnungsgemäß funktioniert und gegebenenfalls eingeschlossene Luft entfernt wird.
Vergewissern Sie sich, dass verwendete Steckschlüsseleinsätze auf das volle Ausgangsdrehmoment des jeweiligen Werkzeugs ausgelegt sind. Stellen Sie sicher, dass die Größe des Steckschlüsseleinsatzes der Schlüsselweite der Mutter entspricht und dass der am Vierkantantrieb aufgesteckte Steckschlüsseleinsatz mit einem Sicherungsstift und Ring fixiert ist.
Setzen Sie das Werkzeug und den Steckschlüsseleinsatz an der Mutter an und stellen Sie dabei sicher, dass der Steckschlüsseleinsatz die Mutter völlig umschließt. Vergewissern Sie sich, dass die Antriebsaufnahme eingerastet ist.
Stellen Sie sicher, dass der Reaktionsarm fest an einem feststehenden Objekt anliegt (z. B. eine angrenzende Mutter, ein Flansch, Gerätegehäuse usw.). Sorgen Sie bei der Positionierung des Schlüssels dafür, dass die Schlauchanschlüsse frei von Hindernissen sind und sich alle Körperteile sicher außerhalb des Gefahrenbereichs befinden. Lassen Sie dann einen momentanen Druck auf das System wirken, um eine ordnungsgemäße Werkzeugplatzierung zu gewährleisten. Wenn etwas nicht richtig wirkt oder nicht richtig reagiert, stoppen Sie das System und stellen Sie den Reaktionsarm neu ein.

Lesen Sie die mit dem Drehmomentschlüssel gelieferten Sicherheitsanweisungen für weitere Hinweise zur Werkzeugverwendung.
Durch Drücken der „Vorwärts“-Taste an der Fernsteuerung wird die Rückseite des Werkzeugs nach hinten geschoben, bis dessen Reaktionsarm seinen Reaktionspunkt berührt.
Halten Sie die Taste gedrückt, während sich der Steckschlüsseleinsatz dreht, bis ein Klicken zu hören ist. Dies bedeutet, dass der Hydraulikzylinder im Werkzeug vollständig ausgefahren ist und die Stecknuss sich nicht weiter vorwärts drehen kann.
Wenn die Taste an der Fernsteuerung weiter gedrückt gehalten wird, führt dies zu einem schnellen Druckaufbau bis zu dem Punkt, an dem das Manometer den Wert anzeigt, der vor der Anwendung des Drehmomentschlüssels voreingestellt wurde.

Die Anzeige des vollen voreingestellten Drucks nach dem Ausfahren des Zylinders BEDEUTET NICHT, dass dieser Druck (Drehmoment) an der Schraube anliegt. Es bedeutet nur, dass der Zylinder vollständig ausgefahren ist und die Stecknuss oder das Ratschengelenk sich nicht weiter drehen kann, bis sich das Werkzeug automatisch zurücksetzt.
Wenn die Taste an der Fernsteuerung losgelassen wird, wird der Zylinder eingefahren. Das Werkzeug setzt sich automatisch zurück und der Bediener hört ein Klicken. Dies bedeutet, dass er die Taste an der Fernsteuerung erneut drücken kann und sich die Stecknuss drehen wird. Jedes Aus- und Einfahren des Zylinders wird als Zyklus bezeichnet. Es werden aufeinanderfolgende Zyklen ausgeführt, bis das Werkzeug beim voreingestellten Drehmoment-/psi-Wert mit einer Genauigkeit von +/-3 % „stehen bleibt“. Die Wiederholgenauigkeit liegt bei +/- 1 %.

Führen Sie immer einen abschließenden Zyklus aus, um sicherzustellen, dass der „Stillstandspunkt“ erreicht wurde.
Sollte sich das Werkzeug nach dem abschließenden Zyklus verkanten, drücken Sie die Taste an der Fernsteuerung erneut (um Druck aufzubauen); halten Sie diesen Druck und ziehen Sie an dem externen Ausrückhebel (RT) oder an der Reaktionsklinke (RTX). Indem die Taste losgelassen und gleichzeitig der Ausrückhebel/die Reaktionsklinke weiterhin nach hinten gezogen wird, kann das Werkzeug auf einfache Weise entfernt werden.
Löseverfahren
Stellen Sie die Pumpe zuerst auf 9.000 psi ein (und nicht direkt auf 10.000 psi). Bringen Sie den Antrieb und den Reaktionsarm in den Lösemodus (Links = Lösen). Dabei muss der Reaktionsarm gerade an einem festen Reaktionspunkt anliegen. Drücken und halten Sie die Taste an der Fernsteuerung. Der Druck nimmt ab, wenn sich die Stecknuss zu drehen beginnt. Wenn der Zylinder vollständig ausgefahren ist, ist ein Klicken zu hören. Lassen Sie die Taste an der Fernsteuerung los; der Zylinder wird dann automatisch eingefahren; dabei ist erneut ein Klicken zu hören. Wiederholen Sie diesen Vorgang, bis die Schraube von Hand gelöst werden kann.

Wenn sich die Schraube mit dem obigen Verfahren nicht löst, weist dies darauf hin, dass dazu ein größeres Werkzeug erforderlich ist.
Einstellen des Drehmoments
Alle Aggregate von Atlas Copco arbeiten in einem Druckbereich von 500 bis 10.000 psi und sind vollständig einstellbar. Sie sind auf Mobilität und einen hohen Durchsatz für eine höhere Drehzahl ausgelegt. Prüfen Sie folgende Punkte, bevor Sie Ihr Atlas-Copco-Aggregat verwenden.
Ist der Tank mit Öl befüllt?
Wo ist die nächste Steckdose am Arbeitsplatz?
Ist am Arbeitsplatz ausreichend Luftdruck (60 bis 100 psi) und Luftstrom vorhanden? (Nur Lufteinheiten)
Ist das Manometer installiert und auf 10.000 psi/700 bar ausgelegt?
Betriebsdruck
Der maximale Betriebsdruck der Pumpe beträgt 10.000 psi / 700 bar. Stellen Sie sicher, dass die gesamte Hydraulikausrüstung und alles Zubehör auf einen Betriebsdruck von 10.000 psi / 700 bar ausgelegt sind. Es sind Hydraulikpumpen mit höherer Druckleistung erhältlich. Wenn Sie kein Atlas-Copco-Aggregat verwenden, prüfen Sie den maximalen Betriebsdruck der verwendeten Einheit und stellen Sie sicher, dass der maximale Betriebsdruck des Systems (10.000 psi / 700 bar) nicht überschritten wird.
Hydraulikanschlüsse
Trennen oder verbinden Sie niemals Hydraulikschläuche und Hydraulikanschlüsse, ohne zuerst den Schlüssel drucklos zu machen. Trennen Sie das Stromkabel der Pumpe und öffnen Sie mehrmals alle Hydraulikregelungen, um sicherzustellen, dass das System drucklos ist. Wenn das System über ein Manometer verfügt, vergewissern Sie sich mittels des Manometers, dass der Druck abgelassen wurde. Wenn Sie Anschlüsse mit Schnellkupplungen herstellen, vergewissern Sie sich, dass die Kupplungen vollständig einrasten. Gewindeanschlüsse, wie beispielsweise Anschlussstücke, Messgeräte usw., müssen sauber sein und sicher und leckagefrei angezogen werden.

Lose oder unsachgemäß angebrachte Kupplungen können unter Druck eine Gefahr darstellen. Allerdings kann ein übermäßig starkes Anziehen zu einem vorzeitigen Gewindeversagen führen. Anschlussstücke müssen lediglich fest und leckagefrei angezogen werden. Fassen Sie Lecks im Hydrauliksystem niemals an und berühren Sie diese in keinerlei Weise. Austretendes Öl kann in die Haut eindringen und Verletzungen verursachen. Schützen Sie den Schlauch vor möglichen Gefahrenquellen wie scharfen Kanten, extremer Hitze oder starken Stößen. Der Schlauch darf sich nicht knicken oder verdrehen. Prüfen Sie vor der Verwendung den Schlauch auf Verschleiß.
Elektrischer Strom
Überprüfen Sie vor dem Anschließen die ordnungsgemäße Stromversorgung.
Dieser Motor kann Funken bilden. Betreiben Sie diesen nicht in explosiven Umgebungen oder in der Nähe von leitenden Flüssigkeiten.
Verwenden Sie keine Strom- oder Verlängerungskabel, die Beschädigungen oder freiliegende Drähte aufweisen.
Alle Einphasenmotoren verfügen über einen 3-Zinken-Stecker mit Erdung passend für die entsprechende geerdete Steckdose. Verwenden Sie kein ungeerdetes 2-Zinken-Verlängerungskabel, da der Pumpenmotor geerdet sein muss.
Vergleichen Sie die Angaben auf dem Motortypenschild mit der verfügbaren Stromzufuhr, um einen Heißlauf des Motors oder gefährliche elektrische Überlastungen zu vermeiden.
Vor der Verwendung
Prüfen Sie den Hydraulikölstand (verwenden Sie Maximizer-Öl Sorte 46 von Atlas Copco), um einen möglichen Pumpenheißlauf zu verhindern. Öffnen Sie die Einfüllschraube an der Tankplatte. Prüfen Sie den Ölstand anhand des Ölschauglases. Der Ölstand sollte bei abgeschaltetem Motor etwa 5 cm unterhalb des oberen Rands der Tankplatte liegen. Fügen Sie bei Bedarf Öl hinzu. Vermischen Sie keine unterschiedlichen Ölsorten. Vergewissern Sie sich vor dem Betrieb, dass alle erforderlichen Manometer-, Ventil-, Schlauch- und Schnellkupplungsanschlüsse fest und sicher sitzen. Für den normalen Pumpenbetrieb ist ein Manometer erforderlich. Das am Verteiler installierte Manometer ermöglicht eine Überwachung der Last am Schlüssel. Für die meisten Anwendungen sind mit Klasse 1 zertifizierte Manometer erhältlich.
Verwendung des Vierkantantriebs
Wechsel der Antriebsrichtung
Entfernen des Vierkantantriebs: Drücken Sie den runden Knopf an der Antriebsaufnahme und ziehen Sie den Vierkantantrieb am rechteckigen Ende vorsichtig heraus (bei RT20, 25 u. 50: auf die Antriebsaufnahme drücken und diese gleichzeitig gegen den Uhrzeigersinn drehen). Einsetzen des Antriebs in das Werkzeug: Setzen Sie den Antrieb in gewünschter Richtung ein, lassen Sie den Antrieb und die Buchsenverzahnung einrasten, drehen Sie dann den Antrieb und die Buchse, bis die Ratschenverzahnung einrasten kann. Schieben Sie den Antrieb durch die Ratsche.
Drücken Sie den Knopf an der Antriebsaufnahme, lassen Sie den Antrieb in die Aufnahme einrasten und lassen Sie den Knopf los, um den Vierkantantrieb zu fixieren.
Reaktionsarm
Alle hydraulischen Drehmomentschlüssel von Atlas Copco sind mit einem Universalreaktionsarm ausgestattet. Diese Reaktionsarme absorbieren Kräfte, die während des Betriebs der Einheit entstehen, und wirken diesen entgegen. Der Reaktionsarm sollte in die gleiche Richtung wie der Vierkantantrieb weisen; jedoch können entsprechend der jeweiligen Anwendung geringfügige Anpassungen vorgenommen werden. Der RT-Reaktionsarm besteht aus einer speziellen Legierung in Flugzeugqualität und kann um 360° verstellt werden.
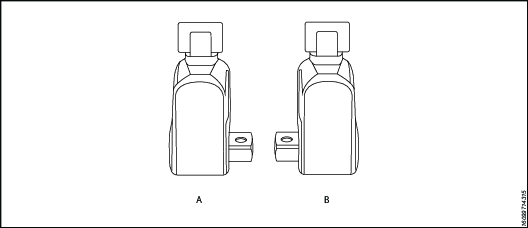
Referenz | Beschreibung |
---|---|
A | Rechts = Anziehen |
B | Links = Lösen |

Der Standard-RT-Reaktionsarm kann nicht geschweißt werden und darf nicht modifiziert werden.
Der Reaktionsarm bei allen RT-Monoblock-Gehäusen weist eine Verzahnung auf, die auf den hinteren Teil des Werkzeugs (Zylinder) geschoben wird. Während des Betriebs muss der Reaktionsarm vollständig eingerastet und fixiert sein; dazu muss der federbelastete Reaktionsarmhebel an der Basis des Gehäuses (Abschlussstück) eingesetzt werden. Vor dem Betrieb sicherstellen, dass der Gegenhalter komplett eingerastet ist.
Einstellen des Drehmoments
Wenn das System vollständig angeschlossen ist und ordnungsgemäß mit Strom versorgt wird, kann der Bediener nun den Pumpendruck auf das für die Anwendung benötigte Niveau einstellen.
Ziehen Sie beim Verschrauben die Angaben des Herstellers heran, um den erforderlichen Drehmomentwert zu bestimmen.
Die Schraubsequenz kann je nach Dichtungsmaterial usw. von Werk zu Werk und sogar innerhalb eines Werks variieren. Beachten Sie immer die lokalen Verfahren.
Siehe Druck-Drehmoment-Umwandlungstabelle für das zu verwendende Werkzeug. Die Drehmomenttabellen sind in ServAid verfügbar.
Vierkant-/Sechskantantrieb - Arbeitsdrehmoment
Antriebsgröße: Die maximale Leistung des Vierkant- oder Sechskantantriebs ist durch dessen Material und Aufnahmebereich begrenzt. Da Atlas Copco für die Antriebselemente eine speziell geeignete Stahllegierung verwendet, kann die folgende maximale Drehmomentleistung ohne Antriebsfehler erreicht werden, insofern das Reaktionselement nahe derselben Ebene wie die zu schraubende Mutter anliegt.
Wenn der Reaktionsarm nicht an derselben Ebene wie die zu schraubende Mutter anliegen kann, muss ein geringeres Drehmoment angewendet werden, da die zusätzliche Seitenlast berücksichtigt werden muss. Wenn die Drehmomentanforderungen nahe oder knapp über den oben angegebenen Werten liegen, verwenden Sie den RT's/-9/-Sechskantantrieb mit austauschbaren Sechskantstecknüssen.
Die RT-Serie ist mit Vierkantantrieb (Standard) oder optionalem Sechskantantrieb erhältlich. Die folgende Tabelle zeigt den optimalen Arbeitsbereich für die entsprechenden Antriebe.
Antriebsgröße Zoll oder mm | Antriebstyp | Maximaler Betriebsdruck | Möglicher Fehler | ||
ft lbs | Nm | ft lbs | Nm | ||
1/2" | Sechskant | 353 | 478 | 392 | 531 |
1/2" | Vierkant | 367 | 497 | 408 | 553 |
5/8" | Sechskant | 689 | 934 | 766 | 1038 |
3/4" | Sechskant | 1191 | 1614 | 1324 | 1794 |
3/4" | Vierkant | 1239 | 1679 | 1377 | 1865 |
7/8" | Sechskant | 1892 | 2565 | 2102 | 2848 |
1" | Sechskant | 2824 | 3827 | 3138 | 4252 |
1" | Vierkant | 2937 | 3980 | 3263 | 4422 |
1-1/8" | Sechskant | 4021 | 5448 | 4468 | 6054 |
1-1/4" | Sechskant | 5516 | 7474 | 6129 | 8304 |
1-3/8" | Sechskant | 7341 | 9948 | 8157 | 11053 |
1-1/2" | Sechskant | 9531 | 12915 | 10590 | 14350 |
1-1/2" | Vierkant | 9912 | 13432 | 11014 | 14924 |
1-5/8" | Sechskant | 12118 | 16420 | 13465 | 18245 |
1-3/4" | Sechskant | 15135 | 20508 | 16817 | 22787 |
1-7/8" | Sechskant | 18616 | 25224 | 20684 | 28027 |
2" | Sechskant | 22593 | 30613 | 25103 | 34015 |
2-1/4" | Sechskant | 32168 | 43588 | 35742 | 48431 |
2-1/2" | Sechskant | 44126 | 59791 | 49029 | 66435 |
2-1/2" | Vierkant | 45891 | 62183 | 50990 | 69092 |
12mm | Sechskant | 298 | 404 | 331 | 449 |
17mm | Sechskant | 847 | 1147 | 941 | 1275 |
19mm | Sechskant | 1182 | 1602 | 1313 | 1780 |
22mm | Sechskant | 1835 | 2486 | 2039 | 2763 |
24mm | Sechskant | 2382 | 3228 | 2647 | 3587 |
27mm | Sechskant | 3392 | 4596 | 3769 | 5107 |
32mm | Sechskant | 5647 | 7652 | 6275 | 8502 |
36mm | Sechskant | 8040 | 10895 | 8934 | 12105 |
41mm | Sechskant | 11878 | 16094 | 13197 | 17882 |
46mm | Sechskant | 16774 | 22730 | 18638 | 25255 |
50mm | Sechskant | 21542 | 29190 | 23935 | 32433 |
Wartung
Wartungsanweisungen
Wartungsempfehlungen
Es wird empfohlen, eine vorbeugende Wartung regelmäßig durchzuführen. Beachten Sie die ausführlichen Informationen über die vorbeugende Wartung. Wenn das Produkt nicht ordnungsgemäß funktioniert, bringen Sie es außer Betrieb und prüfen Sie es.
Wenn keine detaillierten Informationen über eine vorbeugende Wartung enthalten sind, befolgen Sie die folgenden allgemeinen Richtlinien:
Entsprechende Teile gründlich reinigen
Defekte und verschlissene Teile ersetzen
Schmierung: Alle beweglichen Teile müssen regelmäßig mit hochwertigem Schmiermittel versehen werden, wie Molykote P37 mit Graphit oder Dow Corning 1000. Unter rauen Umgebungsbedingungen müssen Reinigung und Schmierung häufiger erfolgen.
Hydraulikschläuche: Schläuche müssen nach jedem Arbeitseinsatz auf Risse und Undichtigkeiten geprüft werden. Hydraulikanschlüsse können mit Schmutz verstopft werden und müssen regelmäßig gespült werden. Hydraulikschläuche müssen eine gültige Kontrollzertifizierung aufweisen.
Schnellkupplungen: Anschlüsse müssen sauber gehalten und dürfen nicht am Boden entlang gezogen werden, da sogar kleine Schmutzpartikel zu einer Fehlfunktion der internen Ventile führen können.
Zylinderdichtungen: Wenn der Zylinder demontiert werden muss, sollten gleichzeitig die Zylinderdichtungen ausgetauscht werden. Dichtungssätze sind jederzeit erhältlich.
Bauteile: Alle Bauteile des Werkzeugs sollten einmal jährlich auf Risse, Späne und Verformungen geprüft werden. Bei einem derartigen Befund ist ein sofortiger Austausch erforderlich.
Störungshilfe
Fehlerbehebung - Hydraulischer Drehmomentschlüssel
Werkzeugdefekte können vorkommen, wenn auch selten. Meist liegen solche Fehler an den Hydraulikkupplungen oder Hydraulikschläuchen. Diese Komponenten können unmittelbar repariert oder ausgetauscht werden, da diese überall verfügbar sind. Defekte von Bauteilen des Werkzeugs sind sehr selten, dennoch sind Ersatzteile ab Lager erhältlich. Alle Reparaturen an Atlas-Copco-Werkzeugen können von ausreichend erfahrenen Personen entsprechend der vorgenannten Anweisungen durchgeführt werden. Ansonsten wenden Sie sich bitte an Atlas Copco, um eine schnelle Reparatur des Werkzeugs zu vereinbaren.
Empfohlene Wartungsintervalle:
Bei starker Beanspruchung oder korrosiven/rauen Umgebungen – alle 3 Monate. Bei starker Beanspruchung müssen interne Antriebskomponenten möglicherweise häufig geprüft und geschmiert werden, z. B. wöchentlich.
Normale Beanspruchung – alle 6 Monate.
Leichte oder sporadische Beanspruchung – alle 12 Monate.
Fehlerbehebung - Aggregate
Atlas-Copco-Hydraulikaggregate sind Präzisionseinheiten und erfordern daher ein gewisses Maß an Pflege und Wartung.
Hydrauliköl muss nach 300 Betriebsstunden oder mindestens zweimal im Jahr vollständig gewechselt werden. Sorgen Sie stets dafür, dass der Tank mit Flüssigkeit gefüllt ist. Verwenden Sie für eine optimale Leistung immer die Maximizer-Öle von Atlas Copco.
Kupplungen und Anschlüsse müssen regelmäßig auf Lecks geprüft werden. Schmutz und Fremdkörper müssen von Anschlüssen ferngehalten werden. Reinigen Sie diese vor der Verwendung.
Hydraulikanzeige: Einige Anzeigen sind mit Flüssigkeit gefüllt. Falls der Flüssigkeitspegel sinkt, deutet dies auf eine undichte Stelle nach außen hin und macht einen Austausch erforderlich. Füllt sich die Anzeige mit Hydrauliköl, ist von einem Defekt im Inneren auszugehen und das Anzeigegerät muss ausgewechselt werden.
Filter an Pumpe: Der Filter muss bei normaler Beanspruchung zweimal im Jahr ausgetauscht werden und häufiger, wenn die Pumpe täglich oder in einer schmutzigen, rauen Umgebung eingesetzt wird.
Fernsteuerung: (Lufteinheit) Die Luftleitung zur Fernsteuerung muss regelmäßig auf Obstruktionen und Knicke in der Leitung geprüft werden. Wenn die Leitung einen Knick oder Riss aufweist, muss diese ausgetauscht werden. Die Druckknöpfe am Fernsteuerungsgriff müssen bei Bedienschwierigkeiten geprüft werden. (Elektrische Einheit) Die Schaltknöpfe müssen regelmäßig auf Problemanzeichen geprüft werden.
Luftventil: Dieses Ventil muss zweimal im Jahr geprüft werden.
Armatur: (Elektrische Einheit) Jährlich prüfen.
Pumpeneinheit: Die Pumpe sollte alle 2 Jahre überholt werden. Dies kann durch Atlas Copco oder einen anderen Fachbetrieb für die Wartung von Hydraulikteilen erfolgen.
Fehlerbehebung - Prozeduren
Test 1
Bringen Sie die Schläuche auf normale Weise an der Pumpe und dem Werkzeug an.
Drücken Sie die „Vorwärts“-Taste und halten Sie diese gedrückt.
Wenn sich Pumpendruck aufbaut und sich die Schläuche „biegen“, aber das Werkzeug dennoch nicht läuft, dann liegt das Problem wahrscheinlich an einer losen oder fehlerhaften Kupplungsverbindung. Um die fehlerhafte Kupplung aufzufinden, trennen Sie die Schläuche vom Werkzeug, verbinden Sie die losen Enden miteinander und lassen Sie die Pumpe laufen. Wenn das Manometer einen Druck von höchstens 500 psi anzeigt, dann befindet sich der fehlerhafte Anschluss am Werkzeug. Ein wesentlich größerer Druck weist darauf hin, dass das Problem entweder an der Pumpe oder einem Schlauchanschluss liegt.
Test 2
Entfernen Sie die Schrauben zwischen Pumpenmotor und Tank. Schieben Sie den Pumpenmotor nach hinten und belassen Sie dabei den Kolben im Öl.
Schalten Sie die Pumpe ein. Wenn kein Öl aus dem Magnetventilrohr austritt, dann tauschen Sie das Magnetventil aus.
Schließen Sie das Regelventil bis zum Maximum. Drücken Sie die „Vorwärts“-Taste und halten Sie diese gedrückt. Prüfen Sie währenddessen, ob Öl aus dem Regelventilrohr austritt. Wenn Öl austritt, dann tauschen Sie das Regelventil aus.
Test 3
Trennen Sie das Werkzeug von den Schläuchen.
Lassen Sie die Pumpe laufen.
Wenn die Pumpe keinen Druck aufbaut, dann liegt das Problem an der Pumpe. Wenn sie Druck aufbaut, dann liegt das Problem am hydraulischen Blowby im Werkzeug.
Test 4
Dieser Test sollte vor jeder Verwendung eines Atlas-Copco-Werkzeugs durchgeführt werden.
Verbinden Sie Werkzeug, Pumpe und Schläuche auf normale Weise.
Lassen Sie die Pumpe mehrmals laufen.
Lassen Sie das System nochmals laufen und beobachten Sie die Vorgangssequenz.
Wenn Sie die „Vorwärts“-Taste drücken, sollte sich der Werkzeugantrieb um etwa 24 Grad drehen und es sollte ein Klicken zu hören sein. Ebenso sollten die Ausrückhebel zur Rückseite des Werkzeugs fahren und nach vorne springen.
Lassen Sie an diesem Punkt die „Vorwärts“-Taste los. Es sollte keine weitere Bewegung erkennbar sein, zudem sollte nach kurzer Zeit ein weiteres Klicken zu hören sein. Auf diese Weise soll das Werkzeug arbeiten.
Wenn eine abweichende Vorgangssequenz erkennbar ist, dann arbeitet das System fehlerhaft und kann höchstens 10 % seiner Auslegungskapazität erbringen.
Ergreifen Sie sofort eine Korrekturmaßnahme. Zu Referenzzwecken: Werkzeuge und Pumpen sind werksseitig folgendermaßen angeschlossen. Dies verhindert, dass das Werkzeug, die Pumpe und EIN Schlauch nicht falsch angeschlossen werden können.
Test 5
Werkzeug | Schlauch | Pumpe |
---|---|---|
Ausfahrseite-Stecker | Ausfahrseite-Buchse auf Buchse | Ausfahrseite-Stecker |
Einfahrseite-Stecker | Einfahrseite-Stecker auf Stecker | Einfahrseite-Buchse |

Hinweis: Durch das Verbinden von zwei (oder einer anderen geraden Anzahl von) Schläuchen miteinander entsteht „ein“ Schlauch, der rückwärts angeschlossen ist! Stecker auf Buchse und Buchse auf Stecker. Dadurch läuft das System rückwärts gemäß obigem Test Nr. 5. Wenn Ihr Schlauch nicht lang genug ist, dann verbinden Sie 3 Schläuche miteinander oder verstellen Sie Ihre Pumpe oder wenden Sie sich an Atlas Copco für eine längere Schlauchanordnung.
Fehlersuche - Symptome und erforderliche Maßnahmen
Symptom | Mögliche Ursache | Erforderliche Maßnahme |
---|---|---|
Das Manometer zeigt einen Druckaufbau, aber das Werkzeug läuft nicht. | Lose oder fehlerhafte Kupplungen. Magnetventil funktioniert nicht. | Kupplungen anziehen und/oder austauschen. Mit Test Nr. 1 das Problem lokalisieren. Test Nr. 2 heranziehen. Falls es nicht funktioniert, Magnetventil austauschen. |
Zylinder fährt nicht ein | 1. Siehe oben. | 1. Siehe oben. |
2. Spannung zur elektrischen Pumpe ist zu niedrig, Spannungsabfall oder falsche Stromstärke. | 2. Ein kürzeres Verlängerungskabel oder ein 12-AWG-Kabel mit Mindestamperezahl von 25 verwenden. | |
3. Bindeglied zwischen Kolbenstange und Antriebsklinke ist beschädigt. | 3. Teile nach Bedarf austauschen. | |
Zylinder baut keinen Druck auf | 1. Öl-Blowby in Werkzeug (Leck in Kolbendichtung, beschädigter O-Ring, beschädigter Kolben). | 1. Fehlerhafte Teile austauschen. Wenden Sie sich an den Atlas Copco-Service |
2. Pumpenproblem. | 2. Entfernen Sie die Schrauben zwischen Pumpenmotor und Tank. Schieben Sie den Pumpenmotor nach hinten und belassen Sie dabei den Kolben im Öl. Schalten Sie die Pumpe ein. Wenn kein Öl aus dem Magnetventilrohr austritt, dann tauschen Sie das Magnetventil aus. 2A. Wenn sich die Pumpe wie viele Kiesel in einer Blechdose anhört, dann kann das Problem an einer verschlissenen Motorkupplung liegen. Den Motor von der Grundplatte entfernen. Mit einer Spitzzange die Motorkupplung entfernen. Bei Verschleiß austauschen. Wenden Sie sich an den Atlas Copco-Service. 2B. Wenn sich die Pumpe wie viele Kiesel in einer Blechdose anhört, dann kann das Problem an einer verschlissenen Motorkupplung liegen. Den Motor von der Grundplatte entfernen. Mit einer Spitzzange die Motorkupplung entfernen. Bei Verschleiß austauschen. Wenden Sie sich an den Atlas Copco-Service. 2C. LUFTPUMPE - Fehler FRL aufgrund übermäßiger Feuchtigkeit und/oder Schmutz in der Luftzufuhr. Demontieren und austauschen. Wenden Sie sich an den Atlas Copco-Service. 2D. Luftpumpe - Fehlerhafte Patrone des Fernsteuerventils austauschen. | |
Zylinder/Werkzeug leckt | 1. Sicherheitsventil an der Schwenktülle hat sich gehoben. | 1A. Alle Schläuche und Kupplungen anziehen. Wenn das Leck bestehen bleibt, die Sicherheitskonfiguration anpassen – Test Nr. 4. 1B. Prüfen Sie mithilfe des Tests Nr. 5, ob das System ordnungsgemäß angeschlossen ist (durch einen hohen Druck an der Einfahrseite hebt sich das Sicherheitsventil). |
2. Beschädigter O-Ring im Zylinder. | 2. O-Ring durch entsprechenden Hochdruck-O-Ring austauschen. Wenden Sie sich an den Atlas Copco-Service. | |
3. Fehlerhafte Stopfbuchsendichtung. | 3. Stopfbuchsendichtung austauschen. Wenden Sie sich an den Atlas Copco-Service. | |
Werkzeug läuft rückwärts | 1. Kupplungen verkehrt herum. | 1. Test Nr. 5 durchführen. System nach Bedarf neu anschließen. |
2. Mehrere Schläuche in gerader Anzahl. | 2. Gemäß der Anschlusskonfiguration dürfen Atlas-Copco-Schläuche NUR in ungerader Anzahl miteinander verbunden werden. Wenn 2, 4, 6 Schläuche erforderlich sind, einen Adapter aus Ersatz-Hochdruckkupplungen und Ersatz-Hochdruckstutzen fertigen. | |
Ratsche fährt mit Rückhub zurück | Beschädigte oder anderweitig nicht funktionsfähige Reaktionsklinke. | |
Ratsche führt keine aufeinanderfolgenden Hübe aus. | 1. Beschädigte oder anderweitig nicht funktionsfähige Antriebsklinke oder Feder. | 1. Antriebsklinke und/oder Feder austauschen. Wenden Sie sich an den Atlas Copco-Service. |
2. Zylinder wird nicht vollständig eingefahren. Ratsche führt keine aufeinanderfolgenden Hübe aus. | 2. Das Werkzeug von der Schraube lösen und für mehrere Hübe frei laufen lassen. Wenn das Problem bestehen bleibt, die Klinken prüfen. 2A. Der Bediener lässt nicht ausreichend Zeit für ein vollständiges Einfahren des Zylinders verstreichen. | |
3. Bindeglied zwischen Kolbenstange und Antriebsplatten ist beschädigt. | 3. Teile nach Bedarf austauschen - Wenden Sie sich an den Atlas Copco-Service. | |
Werkzeug verkantet sich auf Schraube. | 1. Reaktionsklinke ist belastet, wenn das Drehmoment des Werkzeugs ausgereizt ist. | 1. Auf der Fernsteuerung die „Vorwärts“-Taste drücken und Druck aufbauen. Die Taste gedrückt halten und einen der Ausrückhebel zurückziehen. Die Taste lösen und gleichzeitig weiter die Hebel nach hinten ziehen. |
2. Werkzeug läuft rückwärts. | 2. Die „Vorwärts“-Taste drücken. Das Werkzeug sollte sofort frei kommen. Test Nr. 5 durchführen. | |
3. Werkzeug ist unter einem festen Objekt eingekeilt. | 3. Kragen um die Ratsche entfernen. Mit irgendeinem Werkzeug die Antriebsklinke aus der Ratsche hebeln und gleichzeitig die Ausrückhebel zurückziehen. Das Werkzeug sollte frei kommen oder den Aufsatz oder das Hindernis wegdrehen. | |
Manometer zeigt keinen Druck | 1. Manometeranschluss ist lose. | 1. Kupplung anziehen. |
2. Fehlerhaftes Manometer. | 2. Manometer austauschen. | |
3. Pumpe baut keinen Druck auf. | 3. Siehe oben Zylinder baut keinen Druck auf. Siehe oben Zylinder baut keinen Druck auf. | |
4. Werkzeugdichtungen sind beschädigt. | 4. Fehlerhafte Dichtungen austauschen. Wenden Sie sich an den Atlas Copco-Service. |
Fehlersuche - Symptome und erforderliche Maßnahmen
Symptom | Mögliche Ursache | Erforderliche Maßnahme |
---|---|---|
Pumpe baut keinen Druck auf. | 1. Luft- oder Stromzufuhr ist gering. | 1. Luftdruck oder Spannung prüfen. |
2. Fehlerhaftes Entlastungs- oder Regelventil. | 2. Ventil austauschen. Wenden Sie sich an den Atlas Copco-Service. | |
3. Niedriger Ölstand oder verstopfter Filter. | 3. Tank füllen und Filter reinigen. | |
4. Internes Leck in Ölleitung von externem Entlastungsventil zu Pumpenkörper. | 4. Tank öffnen, Ölleitung prüfen und gleichzeitig versuchen, Druck aufzubauen. Bei einem Leck die Anschlüsse anziehen oder austauschen. | |
5. Fehlerhaftes Magnet- oder Regelventil | 5. Siehe oben „Zylinder baut keinen Druck auf - Nr. 2“. | |
Motor läuft schleppend und leistungsschwach, hört sich „schlecht“ an, baut nur langsam Druck auf. | 1. Luft- oder Stromzufuhr ist gering. | 1. Siehe Nr. 1 in vorherigem Abschnitt |
2. Verstopfter Filter. | 2. Filter reinigen oder austauschen | |
Pumpe heizt sich auf. | 1. Unsachgemäße Verwendung. | 1. Der Bediener drückt beim Ausfahrhub das Werkzeug weiter an, nachdem der Zylinder das Hubende erreicht hat. Dadurch läuft viel Öl durch ein sehr kleines Loch im Entlastungsventil. Dies führt zu Wärmeentwicklung. Der Bediener muss das Werkzeug lösen, nachdem die Ausrückhebel nach vorne springen. |
2. Die Fernbedienung ist immer noch eingeschaltet, auch wenn die Pumpe nicht aktiv verwendet wird. | 2. Pumpe ausschalten, wenn sie nicht tatsächlich verwendet wird. Pumpe NICHT laufen lassen, wenn das Werkzeug nicht verwendet wird. | |
Pumpe erreicht keine 10.000 psi, nur 9.000 psi | Regelventil austauschen | 1A. 3 Schrauben vom 4-Wege-Verteilerblock entfernen IB. Regelventil entfernen IC. Neues Regelventil anbringen ID. Metallring nicht vergessen IE. O-Ringe am Verteilerblock prüfen IF. Verteilerblock austauschen IG. Jede Schraube mit 1 Tropfen Loctite versehen IH. Schrauben fest anziehen. Genau nachprüfen, dass die Schrauben fest angezogen sind. |
Druck erreicht keine 4.000 psi | Absperrventil(e) austauschen | IA. Pumpe vom Tank entfernen IB. Absperrventile austauschen, 3.250 psi /70 bar, 90 % Wahrscheinlichkeit, dass Pumpe funktioniert IB. Absperrventile austauschen, 3.250 psi /70 bar, 90 % Wahrscheinlichkeit, dass Pumpe funktioniert IC. Wenn Pumpe keine 10.000 psi erreicht, Absperrventil austauschen, 1.250 psi / 350 bar |
Druck nicht stabil (große Schwankungen) | Magnetventil austauschen (115 V), (220 V) | IA. Oberes Magnetventil entfernen IB. Neues oberes Magnetventil anbringen IC. O-Ringe prüfen |
Druck nicht stabil (geringe Schwankungen) | Rückschlagventile austauschen, Teile-Nr. 20374. Spezialwerkzeuge erforderlich. | IA. Pumpe vom Tank entfernen IB. Rückschlagventil austauschen IC. Nicht zu fest anziehen |
Kein Druck | Rohrleitungen prüfen | IA. Pumpe vom Tank entfernen. Rohrleitungskupplungen prüfen IB. T-Kupplung innerhalb der Pumpe prüfen |
Unkontrollierter Druck | 1. Kupplung prüfen, Teile-Nr. 10190 | IA. Pumpe vom Tank entfernen IB. Rohrleitung entfernen IC. Blockpumpe entfernen (Schrauben Nr. 20444) ID. Kupplung sorgfältig prüfen IE. Nicht vergessen, die Schlüssel auszutauschen (Teile-Nr. 10184) |
2. Pumpen prüfen, Teile-Nr. 10168-10169-10170 | 2A. Pumpe vom Tank entfernen 2B. Schrauben der Pumpe lösen 2C. Dichtungen prüfen 2D. Ersetzen 2E. Fest anziehen |
Fehlersuche - Symptome und erforderliche Maßnahmen
Symptom | Mögliche Ursache | Erforderliche Maßnahme |
---|---|---|
Motor läuft nicht | 1. Sicherung 16 a prüfen, Teile-Nr. 10064 | 1. Sicherung 16 a austauschen (weiß - oben) |
2. Schaltkasten prüfen | 2. Auf getrennte Anschlüsse prüfen | |
3. 115-V-Kabel prüfen | 3. Leitung auf Risse oder Unterbrechungen prüfen | |
4. Stecker prüfen | 4. Leitung auf getrennte Anschlüsse prüfen | |
5. Fernsteuerung prüfen | 5. Leitung auf getrennte Anschlüsse prüfen | |
Startschwierigkeiten beim Motor | 1. Lager, Teile-Nr. 10198 u. 10178 | IA. Pumpe vom Tank entfernen IB. Blockpumpe entfernen IC. Blockpumpe demontieren ID. Lager austauschen |
2. Handschalter der Fernsteuerung, kleine weiße Kunststoffauflage | 2A. Handschalter 2B öffnen. Kleine Kunststoffteile austauschen | |
Durchgebrannte Sicherungen beim Start | Prüfen, ob Sicherung 16 a durchgebrannt ist, Teile-Nr. 10064 | Um dieses Problem zu vermeiden, lassen Sie den Motor nicht laufen, wenn der Hydraulikschlauch nicht angeschlossen ist. |
Schlauch oder Werkzeuganschluss ist beschädigt oder leckt. | 1. Die äußere Kunststoffabdeckung ist beschädigt oder geschmolzen. | 1. Wenn der darunter liegende Kunststoff unversehrt ist, den Betrieb fortsetzen. Regelmäßig prüfen. Wenn der darunter liegende Kunststoff unversehrt ist, den Betrieb fortsetzen. Regelmäßig prüfen. |
2. Zerfaserte Kunststoffstränge. | 2. Schlauch durchschneiden und entsorgen Schlauch austauschen. | |
3. Öl leckt durch Fasern. | 3. Schlauch durchschneiden und entsorgen Schlauch austauschen. | |
4. Beschädigte Anschlüsse. | 4. Alten Anschluss entfernen und nur durch Hochdruckanschlüsse aus STAHL austauschen. Nach dem Austausch von Anschlüssen immer mittels Test Nr. 5 einen ordnungsgemäßen Anschluss verifizieren. | |
Elektrische Pumpe läuft nicht | 1. Lose elektrische Anschlüsse in Steuerbox. | 1. Steuerbox öffnen und per Sichtprüfung auf lose Gewinde- oder Steckanschlüsse prüfen. |
2. Motor durchgebrannt. | 2. Motorkomponenten nach Bedarf austauschen. Wenden Sie sich an den Atlas Copco-Service. | |
Sicherung | 3. Defekte Sicherung austauschen |
Recycling
Umweltschutzbestimmungen
Nachdem ein Produkt seinen Zweck erfüllt hat, muss es ordnungsgemäß recycelt werden. Zerlegen Sie das Produkt und recyceln Sie die Komponenten gemäß örtlicher Vorschriften.