Two Step
The Two step strategy is very similar to the Quick step strategy except that it adds a small time delay between the first step and the final step, to further counteract short-term relaxation effects in the joint.
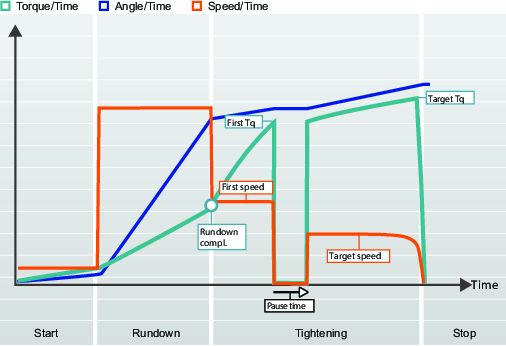
When the First target is reached, the tool makes an immediate stop for a specified time before it continues with the final step. The First torque value and the Pause time should be chosen to improve ergonomics for hand-held tools.
The table below lists all the parameters for the Two step tightening strategy. Some parameters are mandatory, some are optional and some are conditional.
The conditional parameters are not shown in the configuration menu if the condition is not valid, this is also the case when certain functions are disabled.
Parameters for a torque value as the final target.
Parameter name | Condition | Description | Default value |
---|---|---|---|
Target |
| Torque or Angle can be selected from a shortcut menu |
|
First torque | Target = torque |
|
|
First speed |
| Selected by radio buttons. First speed can be Automatically or Manually selected |
|
First speed | First speed = manual | Specifies the tools speed during the first step |
|
Target speed |
| Selected by radio buttons. Target speed can be Automatically or Manually selected |
|
Target speed | Target speed = manual | Specifies the tools speed during the final step |
|
Pause time | Strategy = Two step | Time between first and final step | 50 ms |
Target Torque |
| Defines the target torque of the final step of the tightening |
|
Torque limits |
| Selected by radio buttons. Torque values for max and min can be Automatically or Manually selected |
|
Torque min | Torque limits = Manual | Torque value for the lower limit | 95% of target torque |
Torque max | Torque limits = Manual | Torque value for the upper limit | 120% of target torque |
Angle limits |
| Angle limits is activated through a shortcut menu. Off: No angle limit monitoring. From rundown complete: The monitoring window is set from when the Rundown complete torque is reached. From first torque: The monitoring window is set from when the First torque is reached. From torque: The monitoring window is set from when the specific torque value is reached. |
|
Final angle monitoring torque | Angle limits = from torque | Torque value from when the angle limits are monitored |
|
Angle min | Angle limits = on | Angle value lower limit | 324° |
Angle max | Angle limits = on | Angle value upper limit | 396° |
Time min | Angle limits = on | Minimum time for the stage Range 0 - 99999 ms | 0 ms |
Time max | Angle limits = on | Maximum time for the stage Range 1 - 99999 ms | 1000 ms |
Measure torque at |
| Selected from a shortcut menu: Max torque value: Measures the highest torque value during the tightening. Value at peak angle: Measures the torque value at the highest angle value. Shutoff: Measures the torque value before starting the stop stage. |
|
Torque compensation |
| Selected from a shortcut menu: On: Compensating the final torque value with the measured torque during rundown at the torque compensation point. Off: No torque compensation value is applied. | Off |
Torque compensation point | Torque compensation = On | The torque compensation point is set by referring back to a specified angle from Rundown complete.
| 45° |
Measure angle to | Angle limits = on | Selected from a shortcut menu: Value at peak torque: Measures the angle value at the maximum torque during the tightening. Max angle value: Measures the maximum angle value during the tightening. Shutoff:Measures the angle value before starting the stop stage.
| |
Premature torque loss detection time | 200 ms | ||
Current monitoring | Selected from a shortcut menu: On: The current monitoring is enabled. Off: The current monitoring is disabled. The current monitor is used as a redundancy check for the measured torque to give reasonable confidence that torque readings are accurate. | ||
Shutoff current high limit. | Current monitor = On | The current value must be above 0 and below tool maximum current. | |
Shutoff current low limit. | Current monitor = On | The current value must be above 0 and below the current high limit. |
The table below lists all the parameters for the Two step tightening strategy. Some parameters are mandatory, some are optional and some are conditional.
The conditional parameters are not shown in the configuration menu if the condition is not valid, this is also the case when certain functions are disabled.
Parameters for an angle value as the final target.
Parameter name | Condition | Description | Default value |
---|---|---|---|
Target |
| Torque or Angle can be selected from a shortcut menu |
|
First torque | Target = angle |
|
|
First speed |
| Selected by radio buttons. First speed can be Automatically or Manually selected |
|
First speed | First speed = manual | Specifies the tools speed during the first step |
|
Target speed |
| Selected by radio buttons. Target speed can be Automatically or Manually selected |
|
Target speed | Target speed = manual | Specifies the tools speed during the final step |
|
Pause time | Strategy = Two step | Time between first and final step | 50 ms |
Torque min | Torque value for the lower limit | 95% of target torque | |
Torque max | Torque value for the upper limit | 120% of target torque | |
Target angle |
| Target value for the final step |
|
Angle limits |
| Angle limits is activated a through shortcut menu. Auto: Set automatically by the algorithm. Manual: The limits are set manually. |
|
Angle min | Angle limits = Manual | Angle value lower limit | 324° |
Angle max | Angle limits = Manual | Angle value upper limit | 396° |
Time min | Angle limits = Manual | Minimum time for the stage Range 0 - 99999 ms | 0 ms |
Time max | Angle limits = Manual | Maximum time for the stage Range 1 - 99999 ms | 1000 ms |
Measure torque at |
| Selected from a shortcut menu: Max torque value: Measures the highest torque value during the tightening. Value at peak angle: Measures the torque value at the highest angle value. Shutoff: Measures the torque value before starting the stop stage. |
|
Torque compensation |
| Selected from a shortcut menu: On: Compensating the final torque value with the measured torque during rundown at the torque compensation point. Off: No torque compensation value is applied. | Off |
Torque compensation point | Torque compensation = On | The torque compensation point is set by referring back to a specified angle from Rundown complete.
| 45° |
Premature torque loss detection time | 200 ms | ||
Current monitoring | Selected from a shortcut menu: On: The current monitoring is enabled. Off: The current monitoring is disabled. The current monitor is used as a redundancy check for the measured torque to give reasonable confidence that torque readings are accurate. | ||
Shutoff current high limit. | Current monitor = On | The current value must be above 0 and below tool maximum current. | |
Shutoff current low limit. | Current monitor = On | The current value must be above 0 and below the current high limit. |