Torque Compensation

The graphical representation is used in the documentation to describe the configuration setting and the interpretation of the parameter values. The graphs are not used in the GUI of the controller or ToolsTalk 2.
By using torque compensation, the actual clamping force applied to the joint can be better determined and the scatter in the applied clamping force can be reduced.
The torque compensation point is set by referring back to a specified angle from Rundown complete and calculating a value for the torque used during rundown. This is then compensated for when creating the preload in the bolt by adding the torque value calculated in the torque compensation point to the Target torque.
Parameter | Description |
---|---|
Torque compensation | Enables adjustment of the Target torque used in the rundown stage. Off: No compensation is made. On: Manually sets the Torque compensation point. |
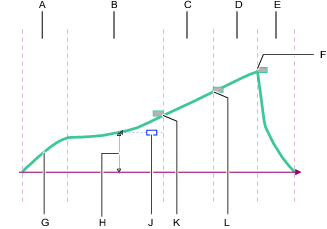
A | Start stage |
B | Rundown stage |
C | First step of the Tightening stage |
D | Final step of the Tightening stage |
E | Stop stage |
F | Final tightening target torque |
G | Torque over time curve |
H | Torque compensation value (torque) |
J | Torque compensation reference point (angle) |
K | Rundown complete target torque |
L | First tightening target torque |
The optional torque compensation parameter is found in the first tightening step in the tightening stage, but the measurement is done in the rundown stage. If enabled, the following happens:
A torque value is measured at a defined angle before rundown complete.
The measured value is defined as the torque compensation value.
The tightening continues into the first tightening step.
All the following torque values, like for example a target torque or an angle monitoring torque, are compensated with the addition of the torque compensation value.