R1006
Air Hydraulic Riveter
Product Information
General Information
Safety Signal Words
The safety signal words Danger, Warning, Caution, and Notice have the following meanings:
DANGER | DANGER indicates a hazardous situation which, if not avoided, will result in death or serious injury. |
WARNING | WARNING indicates a hazardous situation which, if not avoided, could result in death or serious injury. |
CAUTION | CAUTION, used with the safety alert symbol, indicates a hazardous situation which, if not avoided, could result in minor or moderate injury. |
NOTICE | NOTICE is used to address practices not related to personal injury. |
Website
Information concerning our Products, Accessories, Spare Parts and Published Matters can be found on the Atlas Copco website.
Please visit: www.atlascopco.com.
ServAid
ServAid is a portal that is continuously updated and contains Technical Information, such as:
Regulatory and Safety Information
Technical Data
Installation, Operation and Service Instructions
Spare Parts Lists
Accessories
Dimensional Drawings
Please visit: https://servaid.atlascopco.com.
For further Technical Information, please contact your local Atlas Copco representative.
Safety Data Sheets MSDS/SDS
The Safety Data Sheets describe the chemical products sold by Atlas Copco.
Please consult the Atlas Copco website for more information www.atlascopco.com/sds.
Country of Origin
For the Country of Origin, please refer to the information on the product label.
Dimensional Drawings
Dimensional Drawings can be found either in the Dimensional Drawings Archive, or on ServAid.
Please visit: http://webbox.atlascopco.com/webbox/dimdrw or https://servaid.atlascopco.com.
Overview
Applications
This tool is designed for the purpose of setting blind rivets. Professional use only. No other use permitted.
Nose Piece Assignment
Rivet Ø (mm) | Rivet Material | Nose Piece | Part No. |
---|---|---|---|
2.4 | Al/steel, Al/stainless steel | 17/18 |
|
3.2 | CAP® Al, CAP® Cu | 17/18 | |
3.0 | Al/Cu | 17/20 | |
3.0 | Al, Cu, steel, stainless steel, Stinox, Al/al | 17/22 | |
3.0 and 3.2 | Al/cu, steel, stainless steel, Stinox, PG-al, PGsteel, PG-stainless steel | 17/24 | |
4 | Al/cu, CAP® Al, CAP® Cu | 17/24 | |
4 | Steel, Al, PG Al | 17/27 | |
4 | Stinox, stainless steel, PG steel, PG stainless steel | 17/29 | |
4.8 and 5 | Al, CAP® Al, CAP® Cu, PG Al | 17/29 | |
4.8 and 5 | Steel, Al/Al | 17/32 | |
4.8 and 5 | Stainless steel, Stinox, PG steel, PG stainless steel, G-Bulb | 17/36 | |
6 | Al | 17/36 | |
6 | Steel | 17/40 | |
6.4 | Al | 17/40 | |
6.4 | Steel, Al, stainless steel, G-Bulb, PG stainless steel | 17/45 |
The extended version of nose piece and other special versions are available on request.
Main Components
1 | Nose piece |
2 | Steel head sleeve (Internal components: O-ring, chuck housing and jaws) |
3 | Oil filter plug and seal |
4 | Stem collector |
5 | Trigger |
6 | Slide |
7 | Internal component: Control slide valve |
Equipment and Consumables
Tool Type | R1005 | R1006 |
---|---|---|
Nose piece in working position | 17/32 | 17/45 |
Nose piece in tool base | 17/24 | 17/40 |
1 wrench WAF 12/14 (144 6044) | Yes | Yes |
1 wrench WAF 14/17 (144 6043) | Yes | Yes |
1 bottle of hydraulic oil 100 ml (144 5294) | Yes | Yes |
1 oil refill can (162 5612) | Yes | Yes |
Working Range
Tool Type | R1005 | R1006 |
---|---|---|
Standard blind rivet Ø (mm) | Up to 5 | Up to 6.4 |
All materials | ||
Up to 6 Al/steel | - | |
Max. stem Ø (mm) | 3.2 | 4.5 |
Bulb-Tite® Ø (mm) | - | Up to 7.7 |
All materials |
Technical Product Data
Technical Product Data can be found on either ServAid, or the Atlas Copco website.
Please visit: https://servaid.atlascopco.com or www.atlascopco.com.
Accessories
AC Part NO. | Item Name | Item Description |
---|---|---|
3520060010 | Jaws | (3 parts) P1006 tool |
3520060216 | Mandrel container | Transperant. |
3520060052 | Nosepiece 17/45 | (3 mm, 3.2 mm) Alu, Steel - (4 mm) Alu. |
3520060053 | Nosepiece 17/27 | (4 mm) Steel. |
3520060054 | Nosepiece 17/29 | (4.8 mm, 5 mm) Alu. |
3520060055 | Nosepiece 17/32 | (4.8 mm, 5 mm) Steel. |
3520060067 | Nosepiece 17/36 | (6 mm) Alu. |
3520060068 | Nosepiece 17/40 | (6 mm) Steel, (6.4 mm) Alu. |
3520060066 | Nosepiece 17/45 | (6.4 mm) Alu, Steel |
Part No. | Name | Long Rivet Range | Drill bit | Suitable Nosepiece | Rivet in a box | Material |
---|---|---|---|---|---|---|
3520061000 | LR-AS 3,2X 8,0 | 0.5 - 5.0 mm | 3.3 | 17/24 | 1000 pcs | Alu/steel |
3520061001 | LR-AS 3,2X 9,5 | 1.5 - 6.5 mm | 3.3 | 17/24 | 1000 pcs | Alu/steel |
3520061002 | LR-AS 3,2X11,0 | 3.0 - 8.0 mm | 3.3 | 17/24 | 1000 pcs | Alu/steel |
3520061003 | LR-AS 4,0X10,0 | 0.5 - 6.5 mm | 4.1 | 17/24 | 500 pcs | Alu/steel |
3520061004 | LR-AS 4,0X13,0 | 3.5 - 9.5 mm | 4.1 | 17/24 | 500 pcs | Alu/steel |
3520061005 | LR-AS 4,0X17,0 | 7.0 - 13.0 mm | 4.1 | 17/24 | 500 pcs | Alu/steel |
3520061006 | LR-AS 4,8X10,0 | 0.5 - 6.5 mm | 4.9 | 17/29 | 500 pcs | Alu/steel |
3520061007 | LR-AS 4,8X15,0 | 4.5 - 11.0 mm | 4.9 | 17/29 | 500 pcs | Alu/steel |
3520061008 | LR-AS 4,8X17,0 | 6.5 - 13.0 mm | 4.9 | 17/29 | 500 pcs | Alu/steel |
3520061009 | LR-AS 4,8X25,0 | 11 - 19.5 mm | 4.9 | 17/29 | 250 pcs | Alu/steel |
3520061010 | LR-AS 6,4X15,0 | 1.5 - 9.0 mm | 6.5 | 17/40 | 250 pcs | Alu/steel |
3520061011 | LR-AS 6,4X20,0 | 6.0 - 14 mm | 6.5 | 17/40 | 250 pcs | Alu/steel |
Installation
Installation Instructions
General Installation Safety
Have technical personnel to connect the compressed air supply to the tool.
Only hydraulic fluid recommended by the manufacturer shall be used.
Initial Set-Up
Before starting the tool, read the product instructions and the safety information documents and keep them in a safe place.
Have technical personnel connect the compressed air supply to the tool.
Operation
Operating Instructions
General Operation Safety
Operation guidelines
This tool is designed to be used solely for the purpose of setting blind rivets. Never use the tool as a hammer.
Never use without the stem collector fitted.
Never overload the tool. Work within the specified working capacity.
Do not exceed the permitted working pressure.
Do not use the tool without a workpiece.
Do not rivet outside of the riveting holes.
Never turn the tool towards yourself or towards other people.
Be aware of that the blind rivet could be flung from the tool.
Always wear protective goggles when working with the tool. Personal protective equipment such as protective clothing, gloves, safety helmet, non-slip footwear, ear protection and fall arresting device is recommended.
The stem collector must remain mounted on the tool during operation.
When putting down the tool, make sure that it is placed on a stable position on a stable surface from which it cannot fall.
Hydraulic handling
Avoid excessive contact with hydraulic oil. If irritation of the skin occurs, wash the affected skin parts thoroughly with water.
Disconnect the power supply and depressurize the hydraulic system before disconnecting or connecting hoses, fittings, or accessories.
Never grab, touch, or in any way come in contact with a hydraulic pressure leak. Escaping oil can penetrate the skin and cause severe injury.
All hydraulic connections must be securely connected. Loose or improper threaded fittings can be potentially dangerous if pressurized. Severe over tightening can cause premature thread failure. Fittings need to be only securely tightened and leak free.
Ensure quick-disconnect couplings are clean and fully engaged.
Threaded connections such as fittings, gauges etc. must be clean, securely tightened and leak-free.
Do not use kinked hoses. Inspect and replace if damaged.
Protect hoses and connectors from hazards such as sharp edges, heat or impacts. Inspect daily and replace if cracked, worn, damaged or leaking.
Selecting and Changing the Nose piece

Always fit the nosepiece corresponding to the size of the blind rivet. See Nose Piece Assignment.
Disconnect the tool from the compressed air supply.
Loosen the nose piece from the steel head sleeve.
Fasten the selected nose piece and tighten it.
Attaching the Stem Collector
Fully screw on the stem collector by turning it clockwise.
Setting a Blind Rivet
Connect the tool to the compressed air supply.
Insert the blind rivet in the nose piece and use the tool fit as far as it can go in the hole in the material to be joined.
Press the trigger until the stem breaks off.
Release the trigger.
The stem is automatically conveyed into the stem collector. See Emptying the Stem Collector.
Sucking in and Holding a Blind Rivet
This function is used to hold the blind rivet in the nose piece for riveting vertically downward.
Using a pin (e.g. rivet stem), push the slide valve in the tool head as far as it will go to the left or to the right.
After the tool has grabbed the rivet, push up the slide so that it locks in. To switch off the suction, push down the slide.
The complete suction function of the tool is deactivated by pushing back the slide valve.
Service
Maintenance Instructions
General Service and Maintenance Safety
Always disconnect the tool from the compressed air supply when carrying out maintenance work and when the tool is not in use.
Store the tool in a dry place protected from frost.
Regularly maintain the complete grip mechanism.
Regularly empty the stem collector. Overfilling will cause the tool to malfunction.
Regularly check the compressed air lines to ensure that they are fitted correctly and airtightly.
Repairs must be carried out only by skilled personnel. In case of doubt, always send in the complete tool (not disassembled) to the supplier or to Atlas Copco.
Replace worn nose pieces if necessary.
Regular maintenance will extend the service life of your high-quality tool. Service the tool at least every 2 years by an authorised workshop or by Atlas Copco Service. Service the tool ahead of schedule is it is subject to intensive use.
Repairs under warranty are carried out by the manufacturer. Repairs outside the warranty period should only be carried out by skilled technical personnel. Failure to observe the assembly and setting procedures and operation by non-skilled personnel may result in serious damage to the tool. In case of doubt, always send the tool back to the supplier or to Atlas Copco.
Refill or replace the hydraulic oil after prolonged use.
Dispose of the used hydraulic oil in accordance with valid environmental protection regulations.
Maintenance
Maintain the complete grip mechanism regularly.
If necessary, replace worn nose pieces. See Nose Piece Assignment.
Regular maintenance will extend the service life of your high-quality tool. Service the tool at least every 2 years by an authorised workshop or by Atlas Copco Service. Service the tool ahead of schedule if it is subject to intensive use.
Dispose of the used hydraulic oil in accordance with valid environmental protection regulations.
Storage
Store the tool in a dry place protected from frost.
Emptying the Stem Collector
Empty the stem collector regularly. Overfilling will cause the tool to malfunction.
Unscrew the stem collector by turning it counterclockwise. Collect the stems in a suitable container and recycle them as metal.
Fasten the stem collector.
Changing the Jaws
Disconnect the tool from the compressed air supply
Loosen the steel head sleeve.
Loosen the jaw housing.
Remove the jaws.
Clean the jaw housing and the grease sliding surfaces.
Fit new jaws from the front (they are held by grease).
Re-assemble in reverse order, ensuring that all parts are tightly fixed.
Lubrication Instructions
Refilling the Hydraulic Oil

Refill the hydraulic oil after prolonged use if needed.
Follow the correct sequence.
Wear safety goggles and gloves when refilling the hydraulic oil.
Dispose of the used hydraulic oil in accordance with valid environmental protection regulations.
Connect the tool to the compressed air supply. The tool will move to the start position.
Disconnect the tool from the compressed air supply.
Loosen the steel head sleeve.
Loosen the oil filler plug and the gasket with a TORX® screwdriver T20.
Fasten the oil top-up tank with the cover supplied and fill to approximately 50% with hydraulic oil.
Carefully move the piston unit by hand back and forth several times up to the stop until the hydraulic oil comes out bubble-free.
Push the piston unit completely back and leave it at rear position. The hydraulic oil level in the oil top-up tank will drop.
Make sure that no air is drawn in.
Loosen the oil top-up tank from the tool.
Fasten the oil filler plug with gasket with a TORX® screwdriver T20.
Connect the tool to the compressed air supply via a pressure regulator and reset the pressure regulator to 0 bar.
Do not release the trigger.
Loosen the oil filler plug and the gasket with a TORX® screwdriver T20.
Fasten the oil top-up tank provided with the cover.
Gradually increase the air pressure to the mains pressure at the regulator; any excess hydraulic oil will be squeezed out.
Loosen the oil top-up tank from the riveting tool and wipe up any leaked hydraulic oil with a cloth.
Fasten the oil filler plug with gasket with a TORX® screwdriver T20.
Carefully loosen the oil filler plug by approximately 2 turns. The piston unit will slowly move into the forward end position. Wipe up any leaking oil with a cloth.
Fasten the steel head sleeve.
Replacing the Hydraulic Oil

Refill the hydraulic oil after prolonged use if needed.
Follow the correct sequence.
Wear safety goggles and gloves when replacing the hydraulic oil.
Dispose of the used hydraulic oil in accordance with valid environmental protection regulations.
Disconnect the tool from the compressed air supply.
Loosen the steel head sleeve.
Loosen the oil filler plug and the gasket with a TORX® screwdriver T20
Fasten the oil top-up tank provided with the cover.
Connect the tool to the compressed air supply and press the trigger.
The old hydraulic oil will be squeezed out. Keep the cover tightly closed.
Disconnect the tool from the compressed air supply.
Pour out the old hydraulic oil and fill the oil refill container with fresh hydraulic oil up to the upper mark.
Carefully move the piston unit by hand back and forth several times up to the stop until the hydraulic oil comes out bubble-free.
Push the piston unit completely back and leave it at rear position. The hydraulic oil level in the oil top-up tank will drop.
Make sure that no air is drawn in.
Loosen the oil top-up tank from the tool.
Fasten the oil filler plug with gasket with a TORX® screwdriver T20.
Connect the tool to the compressed air supply via a pressure regulator and reset the pressure regulator to 0 bar.
Do not release the trigger.
Loosen the oil filler plug and gasket with a TORX® screwdriver T20.
Fasten the oil top-up tank provided with the cover.
Gradually increase the air pressure to the mains pressure at the regulator, any excess hydraulic oil will be squeezed out.
Loosen the oil top-up tank from the riveting tool and wipe up any leaked hydraulic oil with a cloth.
Fasten the oil filler plug with gasket with a TORX® screwdriver T20.
Carefully loosen the oil filler plug by approximately 2 turns. The piston unit will slowly move into the forward end position. Wipe up any leaking oil with a cloth.
Fasten the steel head sleeve.
Oiling the Jaws
Disconnect the tool from the compressed air supply.
Loosen the steel head sleeve.
Dip the complete jaw mechanism up to the O-ring into an oil batch or wet the jaws with oil and allow to drip off.
Re-assemble in reverse order.
Repair Instructions
Repairs
Repairs under warranty are carried out by the manufacturer.
Repairs outside the warranty period should only be carried out by skilled technical personnel. Failure to observe the assembly and setting procedures and operation by non-skilled personnel may result in serious damage to the tool. In case of doubt, always send the tool back to the supplier or to Atlas Copco for service.
Troubleshooting
Troubleshooting
Problem | Reason | Action |
---|---|---|
The blind rivet is not set | Jaws dirty | Clean and oil sliding surfaces . See Oiling the Jaws |
Jaws worn out | Replace the jaws. See Changing the Jaws | |
Insufficient working pressure | Check the working pressure. See Technical Data | |
Tool stroke too low | Refill with hydraulic oil. See Refilling the Hydraulic Oil | |
The stem is not evacuated | The stem collector is full | Empty the stem collector. See Emptying the Stem Collector |
Wrong nosepiece used | Replace the nose piece. See Nose Piece Assignment | |
Nosepiece worn out | Replace the nose piece. See Selecting and Changing the Nose piece | |
Stem jammed in jaws | Clean the jaws and the jaw housing and oil sliding surfaces; replace if worn. See Changing the Jaws |
Recycling
Environmental Regulations
When a product has served its purpose it has to be recycled properly. Dismantle the product and recycle the components in accordance with local legislation.
Batteries shall be taken care of by your national battery recovery organization.
Recycling Information
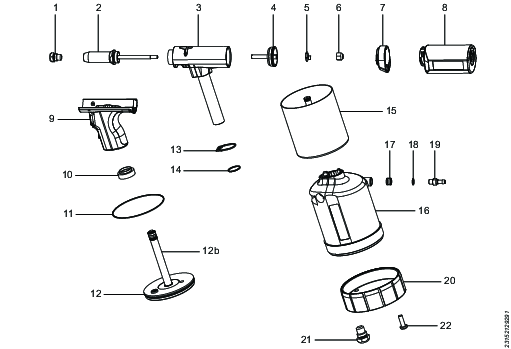
Part No. | Part | Recycle as |
---|---|---|
1 | Nose piece | Metal, Steel |
2 | Head sleeve | Metal, Steel |
3 | Tool head, compl. | Metal, Aluminium |
4 | End cap, compl. | Metal, Steel |
5 | Lock washer | Metal, Steel |
6 | Screw connection | Metal, Steel |
7 | Adapter | Plastic, Other, PA |
8 | Spent mandrel container | Plastic, Other, PA |
9 | Grip, compl. | Plastic, Other, PA |
10 | Al nut | Metal, Aluminium |
11 | O-ring | Rubber |
12 | Air piston | Plastic, Other, PA |
12b | Air piston | Metal, Steel |
13 | Gasket | Rubber |
14 | O-ring | Rubber |
15 | Cylinder, compl. | Metal, Aluminium |
16 | Air cylinder | Plastic, Other, PA |
17 | Spacer | Metal, Steel |
18 | Seal | Rubber |
19 | Connecting Nipple | Metal, Steel |
20 | Bottom | Plastic, Other, PA |
21 | Mouth Piece | Metal, Steel |
22 | Screw | Metal, Steel |