Vacuum Adapter
User guide
Vacuum adapter
This document describes how to use the vacuum adapter.
- Attaching adapter and connecting vacuum on tools with external vacuum
- Disconnecting vacuum hose on tools with external vacuum
- Removing vacuum adapter
- Modifying stroke (±1.5mm)
- Changing nozzle
- Changing metal nozzle
- Holding adapter
- Machining a nozzle with press fit
- Improving vacuum pickup process
- Choosing bits
- FAQs
Attaching adapter and connecting vacuum on tools with external vacuum
Required tools: Assembly tool 4080 1457 03 (for I06) or 4080 1457 02 (for HM4).
To attach the adapter and connect to the vacuum system, perform the following steps:
Unscrew the front protection.
Pull the telescope downwards to disconnect the telescope.
Attach the vacuum adapter holder. Use the assembly tool.
Adjust the placement of the vacuum adapter holder.
Insert the vacuum hose.
Attach the telescope to the vacuum adapter holder.


Disconnecting vacuum hose on tools with external vacuum
Push the connection that holds the vacuum hose. This will release the mechanism that holds the vacuum hose.
Pull the vacuum hose upwards.
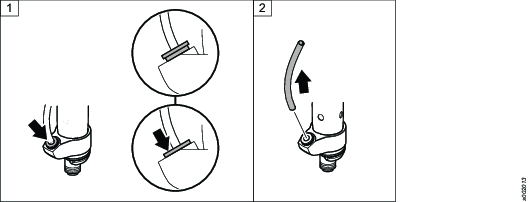
Removing vacuum adapter
Required tools: Assembly tool 4080 1457 03 (for I06) or 4080 1457 02 (for HM4).
Remove vacuum adapter telescope.
Remove vacuum adapter holder.

Modifying stroke (±1.5mm)
Unlock outer sleeve with lock nut.
Adjust outer sleeve.
Lock outer sleeve.
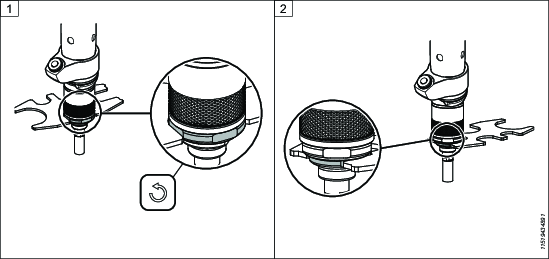
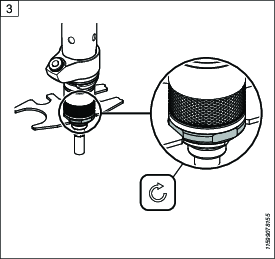
Changing nozzle
Remove nozzle.
Lock inner sleeve and mount nozzle.
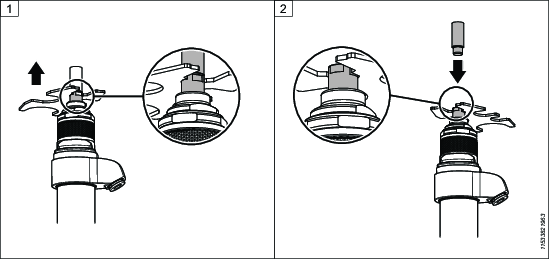
Changing metal nozzle
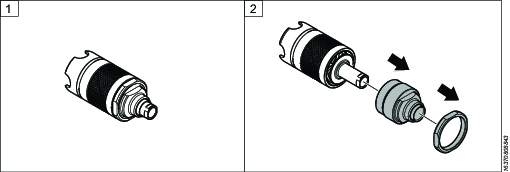
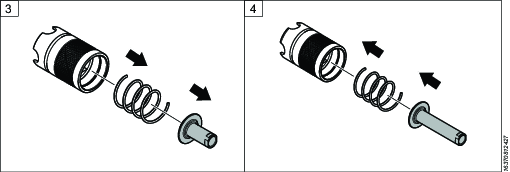
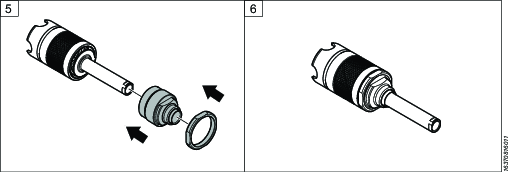
Holding adapter
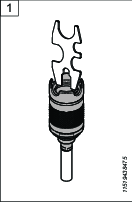
Machining a nozzle with press fit
Definitions
B = Distance from the telescope to bit end.
d = Thickness of the screw head.
L>S,
L = Clearance between bit and nozzle
S = Screw length.

Procedure
Perform the following steps to machine the nozzle:
Make sure that the nozzle have the correct dimension:
3,8 mm long.
Ø4,5 p8 HM4 Ø8,5 P9 I06
Shorten the nozzle to the correct length (Z).
The length (Z) depends on the bit (B) and position of the screw inside the nozzle (d). Z=B+d .
Enlarge the inner diameter of the nozzle.
The inner diameter of the nozzle must be larger than the outer diameter of the bit (ØA).
Make a hole with a center drill.
Before drilling the inner hole you must drill a hole with a center drill. This hole will guide the drill and maintain concentricity.
Drill the hole for the bit. Minimum diameter is bit diameter +0,2. Bigger gap between bit and nozzle results in a bigger vacuum force.
The inner diameter of the inner hole must be 0.2 mm larger than the outer diameter of the bit (ØB).
Drill the hole for the screw head.
The depth of the hole (d) depends on the application.
The diameter of the hole (D) must be 0.02 mm larger than the outer diameter of the screw head.
Note! If you don’t have a screw drawing, measure the thickest screw and add 0,05 mm instead of 0,02 mm.
If necessary, widen the hole to fit the pole of the bit.
The inner diameter of the nozzle must be larger than the outer diameter of the bit (ØC).
Machine the outline of the nozzle.
The nozzle height must be larger than the depth of the hole (H).
The outer diameter of the nozzle must be less than the diameter of the hole (W).
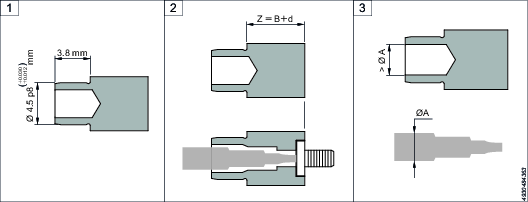
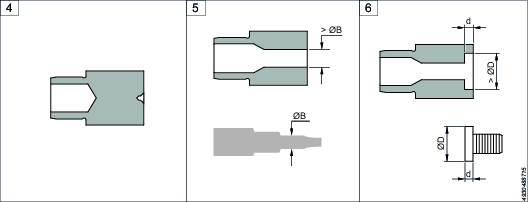

Improving vacuum pickup process
This user guide provides a general guidance for machining the nozzle. However, each application is unique. The following recommendations can improve the vacuum pickup process:
The vacuum nozzle can be machined to follow the same shape as the head of the screws in order to decrease leakage and increase the force from the vacuum holding the screw.
Low profile bits improve the vacuum pressure. Therefore, use the lowest profile bits if possible.
Choosing bits
Pros | Cons | |
---|---|---|
¼” Hex bits |
|
|
HM 4mm bits |
|
|
FAQs
Question | Answer |
---|---|
How to detect misaligned screws? | Use Atlas Copco Smart Vacuum Pump with the integrated sensor to measure the amount for vacuum provided during the pickup process and while the screw is being transported. |
What to do if the customer is not using an AC Smart Vacuum Pump and the screw is falling from the tip of the nozzle? |
|
Which type of nozzle is better, metallic or plastic? | This depends on both the application and customer. A plastic nozzle can avoid cosmetic issues for parts with fragile surfaces. Metallic nozzles are easier to machine and more durable. |