D500 HP Hydraulic Air Pump
Pneumatic Pump
Product Information
General Information
Safety Signal Words
The safety signal words Danger, Warning, Caution, and Notice have the following meanings:
DANGER | DANGER indicates a hazardous situation which, if not avoided, will result in death or serious injury. |
WARNING | WARNING indicates a hazardous situation which, if not avoided, could result in death or serious injury. |
CAUTION | CAUTION, used with the safety alert symbol, indicates a hazardous situation which, if not avoided, could result in minor or moderate injury. |
NOTICE | NOTICE is used to address practices not related to personal injury. |
Warranty
Product warranty will expire 12+1 months after dispatch from Atlas Copco's Distribution Center.
Normal wear and tear on parts is not included within the warranty.
Normal wear and tear is that which requires a part change or other adjustment/overhaul during standard tools maintenance typical for that period (expressed in time, operation hours or otherwise).
The product warranty relies on the correct use, maintenance, and repair of the tool and its component parts.
Damage to parts that occurs as a result of inadequate maintenance or performed by parties other than Atlas Copco or their Certified Service Partners during the warranty period is not covered by the warranty.
To avoid damage or destruction of tool parts, service the tool according to the recommended maintenance schedules and follow the correct instructions.
Warranty repairs are only performed in Atlas Copco workshops or by Certified Service Partners.
Atlas Copco offers extended warranty and state of the art preventive maintenance through its ToolCover contracts. For further information contact your local Service representative.
For electrical motors:
Warranty will only apply when the electric motor has not been opened.
Website
Information concerning our Products, Accessories, Spare Parts and Published Matters can be found on the Atlas Copco website.
Please visit: www.atlascopco.com.
ServAid
ServAid is a portal that is continuously updated and contains Technical Information, such as:
Regulatory and Safety Information
Technical Data
Installation, Operation and Service Instructions
Spare Parts Lists
Accessories
Dimensional Drawings
Please visit: https://servaid.atlascopco.com.
For further Technical Information, please contact your local Atlas Copco representative.
Safety Data Sheets MSDS/SDS
The Safety Data Sheets describe the chemical products sold by Atlas Copco.
Please consult the Atlas Copco website for more information www.atlascopco.com/sds.
Country of Origin
For the Country of Origin, please refer to the information on the product label.
Dimensional Drawings
Dimensional Drawings can be found either in the Dimensional Drawings Archive, or on ServAid.
Please visit: http://webbox.atlascopco.com/webbox/dimdrw or https://servaid.atlascopco.com.
Overview
Atlas Copco Air Driven Pump Unit
Atlas Copco air driven pump units operate on the simple but efficient principle of power magnification through the use of differential areas. A relatively large air-operated piston drives the smaller piston, which provides fluid flow at high pressures. All Atlas Copco air driven pump units are fitted into an easily transportable, tubular steel frame.
The pump units are available, fitted with a large choice of pressure gauges and are supplied complete with an air pressure regulator which can be set to stall the pump unit when it reaches the pressure required for each particular tensioning application.
Introduction
The operating and maintenance procedures listed within this manual should be adhered to and will enable the operator to obtain maximum efficiency and reliability from the equipment.
Precautions
Prior to connecting the hydraulic pump to any equipment, the user is to ensure that :
The working pressure of the hydraulic pump and the equipment to be operated are compatible. i.e. maximum working pressure of the hydraulic tensioning tools, hydraulic connections & hydraulic hoses.
The reservoir pump capacity is adequate to operate the equipment throughout its range.
The hydraulic oil specification used within the pump and the equipment are compatible.
Technical Product Data
Technical Product Data can be found on either ServAid, or the Atlas Copco website.
Please visit: https://servaid.atlascopco.com or www.atlascopco.com.
Installation
Installation Requirements
Safety ON/OFF Valve
The pump unit is fitted with a safety ON/OFF valve. The spring loaded valve defaults to OFF when the valve handle is untouched. Holding the valve handle in the down position turns the pump ON. Releasing the handle turns the pump OFF.
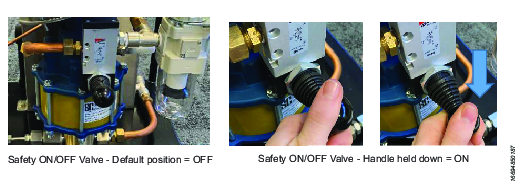
Pre-Pressurization Checks
It is strongly recommended that the pump is checked for any leaks prior to any tensioning operations.
Check for any loose connections on the hydraulic pump unit. A visual inspection should indicate any issues.
Make sure the operator has performed the before and after connecting air supply see also Before and After Connecting Air Supply, before proceeding to step 3.
On the pressure filter regulator (See also Hydraulic Pump Assembly for part 7), pull up the adjustment cap . Rotate the cap in a clockwise direction, until an air pressure of 1 – 2 bar is shown on the gauge.
Make sure the pressure release valve (See also Hydraulic Pump Assembly for part 12) is in the open position. This is achieved by rotating the clutch mechanism (designed to protect the nipple in the pressure release valve) in a anti-clockwise direction. When the valve is open, the clutch mechanism will slip, preventing excessive torque on the pressure release valve.
Make sure oil is present in the tank (oil reservoir), prior to hydraulic pump activation. A minimum level of 5 litres is standard.
To activate the hydraulic pump, pull the dead-mans handle down. The hydraulic pump will begin to operate, forcing hydraulic oil around the pump unit and back to the tank (oil reservoir). This process will remove any air bubbles in the system. Continue to hold the dead-mans handle for 30 seconds. After this period, release and hydraulic pump will stop pumping.
To perform a pressurisation test, rotate the pressure release valve in a clockwise direction. The clutch mechanism will slip, when the correct closing torque on the nipple has been reached.
Hold down the dead-mans handle, the pump will activate, building up a hydraulic pressure. Increase until the oil gauge reading is 750 bar, release the dead-mans handle and monitor if the pressure drops. If no pressure drop is indicated (i.e. the pressure gauge remains at 750 bar), the hydraulic pump is ready for tensioning set-up.
To release the pressure, rotate the pressure release valve in an anti-clockwise direction. The pressure in the system will reduced to zero.
Setting Hydraulic Pump Stall Pressure
The pressure relief valve (See also Hydraulic Pump Assembly for part 3) is factory set by Atlas Copco not to exceed 1650 bar. If the air pressure is increased by the operator by accident, the pressure relief valve will blow or vent preventing excessive hydraulic pressure from being created.
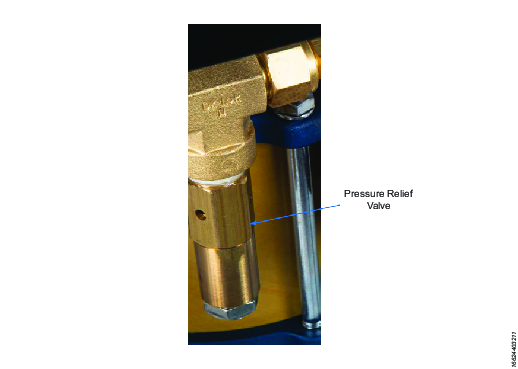
The hydraulic pump in this unit has a hydraulic to pneumatic ratio of 330:1, hence for a maximum working pressure of 1500 bar, the required pneumatic air pressure is (1500 / 330) = 4.545 bar.
Setting Pneumatic / Air Pressure to Create Hydraulic Pressure
Atlas Copco have supplied a pump unit with a pressure filter regulator set to stall the hydraulic pump at 1650 bar. This has been achieved by setting the pressure relief valve, to blow / vent at 5 bar air input.
Connect the main air supply to the hydraulic pump, see also Before and After Connecting Air Supply. Check the air pressure gauge on the filter regulator is set to zero or minimum air pressure. This is performed by lifting up the adjustment cap on the air filter regulator valve and rotating clockwise to stop.
Close the pressure release valve via the clutch mechanism i.e. rotate in a clockwise direction.
De-press the dead-mans handle to activate the hydraulic pump. The hydraulic pump will stall, due to the lack of air pressure.
With the dead-mans handle de-pressed, slowly increase the air pressure to the required level, by rotating the adjustment cap on the air filter regulator valve anti-clockwise. As the air pressure increases, the hydraulic pressure will increase also. Continue until the desired hydraulic pressure is obtained.
Release dead-mans handle, push down the adjustment cap on the filter regulator. Double check the hydraulic pressure, if suitable release the On/OFF valve.
Pump Preparation
Ensure the pressure release valve is in the open position (rotate anticlockwise to stop). The pressure relief valve is fitted with a torque limiter to prevent over tightening it. Limiter will ‘click out’ as a preventative measure.
Ensure the On/OFF valve is in the OFFposition.
Connect the air hose to the air inlet connector. Give the hose a sharp tug afterwards, to ensure a solid connection.
Connect the hydraulic link hose to the female quick connector. (Refer to the operation manual supplied with your tensioners for correct hydraulic link hose configuration).
Ensure an adequate volume of oil is contained in the Oil Tank.
Before and After Connecting Air Supply
It is strongly recommended that the pump is regulated in order to stall at the required tensioning pressure. This process is achieved by the adjustment of the air regulator valve, See also Hydraulic Pump Assembly for component 7.
Before connecting an air supply, it is important to check the following.
The pressure release valve is fully open (rotate Anti-Clockwise).
The Dead-mans handle (See also Hydraulic Pump Assembly; part 12 ) is in the normally closed position i.e. in the highest position. To activate the valve, the dead-mans handles is de-pressed down, opening the air circuit.
The oil reservoir has sufficient oil (Grade ISO 10, 32, 68).
Check that the cap seal plug has been removed.

The oil tank on this pump unit is fitted with a cap seal plug to prevent oil spillage during transit. Remove the M6 cap screw and seal from tank cap prior to use.
Air Line Connection Process
Connect the air hose to the air inlet connector. Give the hose a sharp tug afterwards to ensure a solid connection.
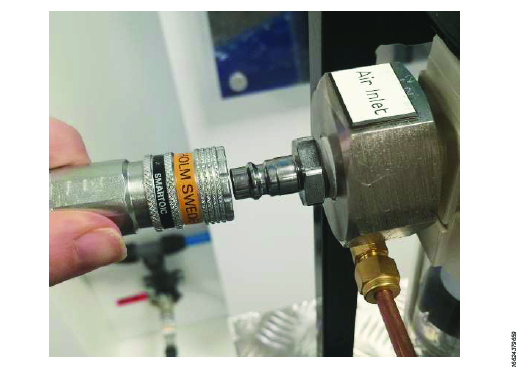
Operation
Ergonomic Guidelines
Consider your workstation as you read through this list of general ergonomic guidelines to identify areas for improvement in posture, component placement, or work environment.
Take frequent breaks and change work positions frequently.
Adapt the workstation area to your needs and the work task.
Adjust for a convenient reach range by determining where parts and tools need to be located to avoid static load.
Use workstation equipment such as tables and chairs appropriate for the work task.
Avoid work positions above shoulder level or with static holding during assembly operations.
When working above shoulder level, reduce the load on the static muscles by lowering the weight of the tool, using for example torque arms, hose reels or weight balancers. You can also reduce the load on the static muscles by holding the tool close to the body.
Take frequent breaks.
Avoid extreme arm or wrist postures, particularly during operations requiring a degree of force.
Adjust for a convenient field of vision that requires minimal eye and head movements.
Use appropriate lighting for the work task.
Select the appropriate tool for the work task.
In noisy environments, use ear protection equipment.
Use high-quality inserted tools and consumables to minimize exposure to excessive levels of vibration.
Operating Instructions
Shut down procedure
Disconnect the main air supply.
Open the oil pressure release valve.
Open the On/OFF valve (air will vent through the exhaust).
Close the On/OFF valve.
Drain water from the air filter.
Top-up the oil tank.
Store in pump box supplied.
Adjustment of Pressure Relief Valve
The pressure relief valve is factory set to vent air if a too high air pressure is set, thus preventing the pump from generating more hydraulic pressure. Adjustment is not necessary.

Do not adjust the pressure relief valve. A plastic cover has been placed over the valve to prevent any adjustment.
If the pressure relief valve has been triggered by excessive compressed pneumatic air pressure, reduce the air pressure by rotating the adjustment cap on the filter regulator in an anticlockwise direction. This will allow the spring and ball bearing assembly in the pressure relief valve to reset. When reset, increase air pressure to 5 bar. Any questions, please contact Atlas Copco.
Pump Operation
Close the pressure relief valve (clockwise).
Hold down the On/OFF valve. The pressure gauge will slowly indicate pressure.
Once the desired pressure is reached, release the On/OFF valve. The valve will spring back to the OFF position. Check the pressure reading on the oil pressure gauge. (Ensure the pressure is holding steady before approaching any pressurized bolt tensioning equipment).
To release the hydraulic pressure, slowly open the pressure release valve (anticlockwise), and the pressure will slowly drop.
Service
Maintenance Instructions
Service Recommendations
Preventive maintenance is recommended at regular intervals. See the detailed information on preventive maintenance. If the product is not working properly, take it out of service and inspect it.
If no detailed information about preventive maintenance is included, follow these general guidelines:
Clean appropriate parts accurately
Replace any defective or worn parts
Lubrication Instructions
Hydraulic Fluid
The performance of hydraulic equipment is heavily dependent on the quality and characteristics of the hydraulic fluid selected for use. The choice of the specification and viscosity of the hydraulic fluid should be based of the conditions of use, taking into account several factors as follows:
The range of environmental temperature.
The range of oil viscosity defined for the equipment.
The application (range of pressures, sources of contamination of the hydraulic fluid, the type of pump, etc.)
The ease of getting a proper replacement or equivalent hydraulic fluid.
Example: ISO Grade 15, 32 and 68.
For changing or refilling the oil, it is recommended to use the same oil as supplied with the pump.
Hydraulic Oil Selection Chart
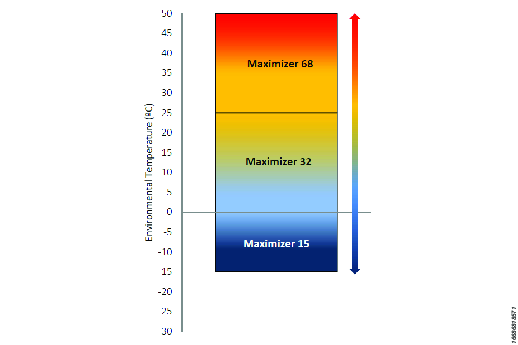
Please use the link below to find our safe data sheets for Maximizer.
https://www.atlascopco.com/en-uk/sys/safetydatasheets
Troubleshooting
Troubleshooting
If for any reason the pump does not run properly, look for one of the following causes:
If the pump appears to be short stroking and running too fast without pumping properly, it usually indicates that the pilot valve assembly is not working as it should. Refer to instructions for the he hydraulic piston and repairing of the pilot valve assembly.
Loss of pressure may be caused by one of two reasons; the hydraulic check valve have developed a leak or the hydraulic fluid is bleeding past the packing in the hydraulic cylinder. Replace the packing in the hydraulic cylinder or repair/replace the hydraulic check valve.
Should the pump run erratically and in a jerky manner after a period of time, it is usually an indication of seizing in the hydraulic piston and cylinder assembly. Refer to instructions on how to disassemble the air motor and to replace the packing in the hydraulic cylinder. If the hydraulic piston and cylinder have not been damaged, a thorough cleaning will normally put the pump back into operation mode again.
To ensure hydraulic fluid flow is optimized, ensure sufficient air volume is supplied to the pump. Hooking the pump up to a smaller pipe size than the “AIR IN” port on the pump will not allow it to run at its full rated capacity. Long runs of relatively small pipe supplying air to the pump will have the same effect.
If an excessive amount of oil or water is pouring through the pump air exhaust, check for and correct;
Lubricating unit in the air supply is delivering too much oil. Adjust to about one drop of oil for every 20 strokes of the pump.
The hydraulic fluid being pumped (oil or water) may be leaking past the packing in the hydraulic cylinder into the air motor. Replace the packing in the hydraulic cylinder.
Recycling
Environmental Regulations
When a product has served its purpose it has to be recycled properly. Dismantle the product and recycle the components in accordance with local legislation.