S8050
Electric screwdriver
Product Information
General Information
Safety Signal Words
The safety signal words Danger, Warning, Caution, and Notice have the following meanings:
DANGER | DANGER indicates a hazardous situation which, if not avoided, will result in death or serious injury. |
WARNING | WARNING indicates a hazardous situation which, if not avoided, could result in death or serious injury. |
CAUTION | CAUTION, used with the safety alert symbol, indicates a hazardous situation which, if not avoided, could result in minor or moderate injury. |
NOTICE | NOTICE is used to address practices not related to personal injury. |
Warranty
Product warranty will expire 12 months after the product is first taken into use, but will in any case expire at the latest 13 months after delivery.
Normal wear and tear on parts is not included within the warranty.
Normal wear and tear is that which requires a part change or other adjustment/overhaul during standard tools maintenance typical for that period (expressed in time, operation hours or otherwise).
The product warranty relies on the correct use, maintenance, and repair of the tool and its component parts.
Damage to parts that occurs as a result of inadequate maintenance or performed by parties other than Atlas Copco or their Certified Service Partners during the warranty period is not covered by the warranty.
To avoid damage or destruction of tool parts, service the tool according to the recommended maintenance schedules and follow the correct instructions.
Warranty repairs are only performed in Atlas Copco workshops or by Certified Service Partners.
Atlas Copco offers extended warranty and state of the art preventive maintenance through its ToolCover contracts. For further information contact your local Service representative.
For electrical motors:
Warranty will only apply when the electric motor has not been opened.
Website
Information concerning our Products, Accessories, Spare Parts and Published Matters can be found on the Atlas Copco website.
Please visit: www.atlascopco.com.
ServAid
ServAid is a portal that is continuously updated and contains Technical Information, such as:
Regulatory and Safety Information
Technical Data
Installation, Operation and Service Instructions
Spare Parts Lists
Accessories
Dimensional Drawings
Please visit: https://servaid.atlascopco.com.
For further Technical Information, please contact your local Atlas Copco representative.
Safety Data Sheets MSDS/SDS
The Safety Data Sheets describe the chemical products sold by Atlas Copco.
Please consult the Atlas Copco website for more information www.atlascopco.com/sds.
Country of Origin
For the Country of Origin, please refer to the information on the product label.
Dimensional Drawings
Dimensional Drawings can be found either in the Dimensional Drawings Archive, or on ServAid.
Please visit: http://webbox.atlascopco.com/webbox/dimdrw or https://servaid.atlascopco.com.
Overview
Technical Product Data
Technical Product Data can be found on either ServAid, or the Atlas Copco website.
Please visit: https://servaid.atlascopco.com or www.atlascopco.com.
Bit Grounding Test
Bit grounding is measured by the ground circuit stability and resistance with the tool running at no load with a rotation speed of 1000 rpm.
The resistance is measured between the bit and the outside of the tool connector.
The measurement of the resistance is between 1~ 20Ω.

Accessories
EBS D Power Adapter
Use this universal power source only with applicable screwdrivers (S8020, S8020-WS, S8050, S8120, S8120-2000, S8160, S8200 and S8250).
Installation
Position the power adapter on a stable surface and keep its surroundings clear to allow heat dissipation.
Connect the power adapter to the tool using the supplied cable. Make sure that the guide notch is aligned with the convex point in the socket, then twist it to fix it in the drive.
Power Setting
The input voltage of the power adapter is ranged from 100 to 240 VAC and from 50 to 60 Hz. Make sure to use the correct voltage to avoid any damage to the power adapter.
Connect one side of the cable to the AC power socket and the other side to the AC input socket (C13 specification).
Change the position of the two-stage switch on the power adapter to ON mode.
Change the position of the two-stage switch on the power adapter to OFF mode.
Disconnect the cable from the AC power socket and from the AC input socket (C13 specification).
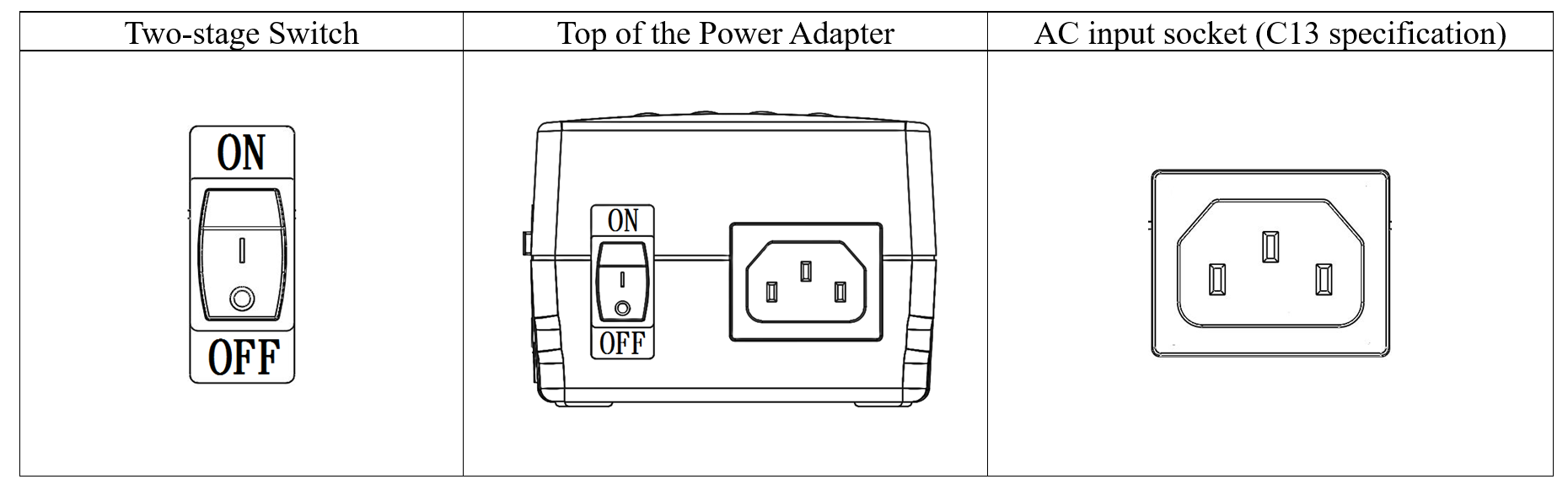
Output Plug (DC)
The output plug provides power to the screwdriver.
The plug specifications are the following ones:
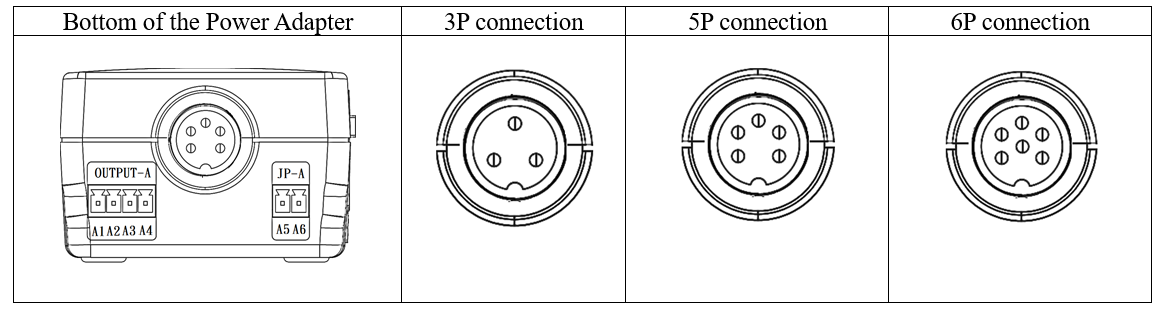
There are two terminals at the bottom of the power adapter:
Output A: Output signal terminal:
Outputs A3 and A4: Switch on signal outputs. A3 and A4 will not export any voltage conduct signal when the tool is switched on.
Outputs A1 and A2: Switch off signal outputs. When the tool has reached its set torque and stopped, no voltage conduct signal will be exported.
No voltage conduct signal will be exported at a high voltage specification (DC 24 V/400 mA).
JP-A: External controller use terminal:
Outputs A5 and A6: Start signals for automation only.
For forward direction, use the external controller to check the conduction between the power adapter and the screwdriver.
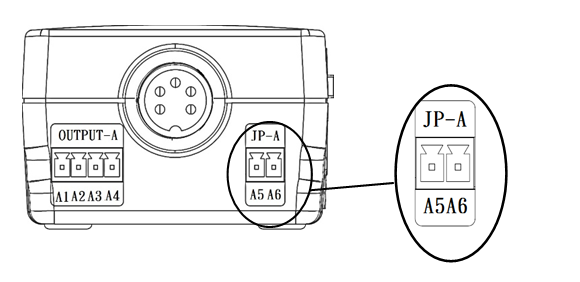
Speed Setting
To modify the speed, turn the speed setting screw on the side of the power adapter with a screwdriver:
To increase the speed, turn the speed setting screw clockwise (0 - 10) on the scale.
To decrease the speed, turn the speed setting screw counterclockwise (10 - 0) on the scale.
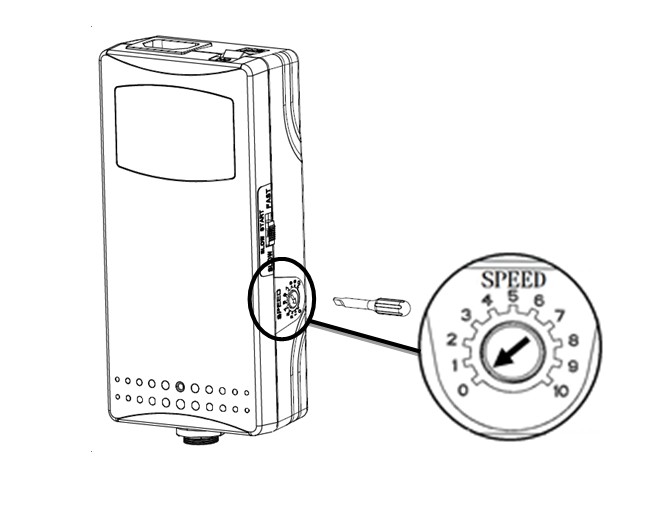
Indicator Light
The power adapter has an indicator light providing different kinds of information.
Green light | Activation (preceded by three orange flashes). |
Tightening OK. | |
No light | No DC voltage output. |
Flashing green light | Short circuit protection. |
Overpower protection. | |
Red light | Tightening NOT OK. |
Flashing red light | Heating protection (temperature set at 75-85 °C). |
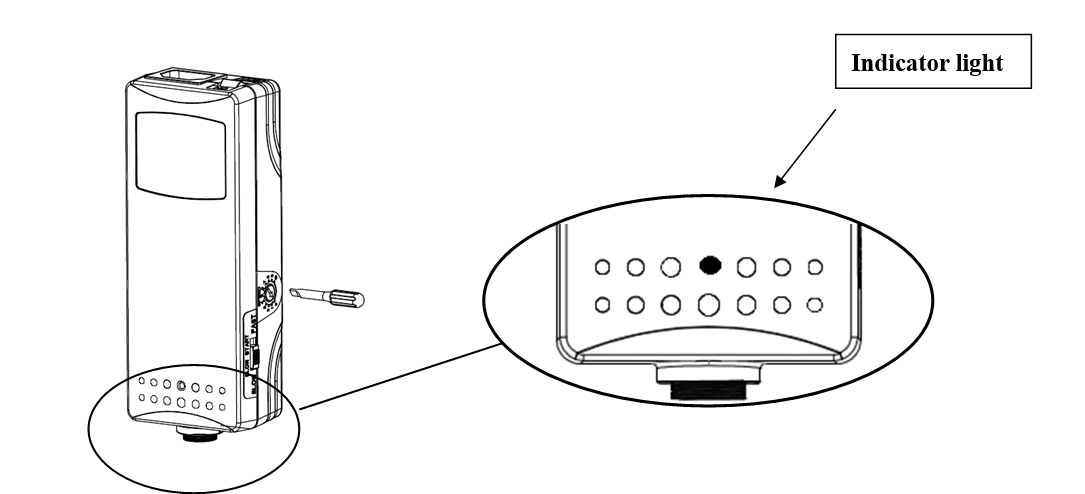
Assembly to a Balancer
There are screw holes at the bottom of the power adapter to assemble it to a balancer. See illustration below.
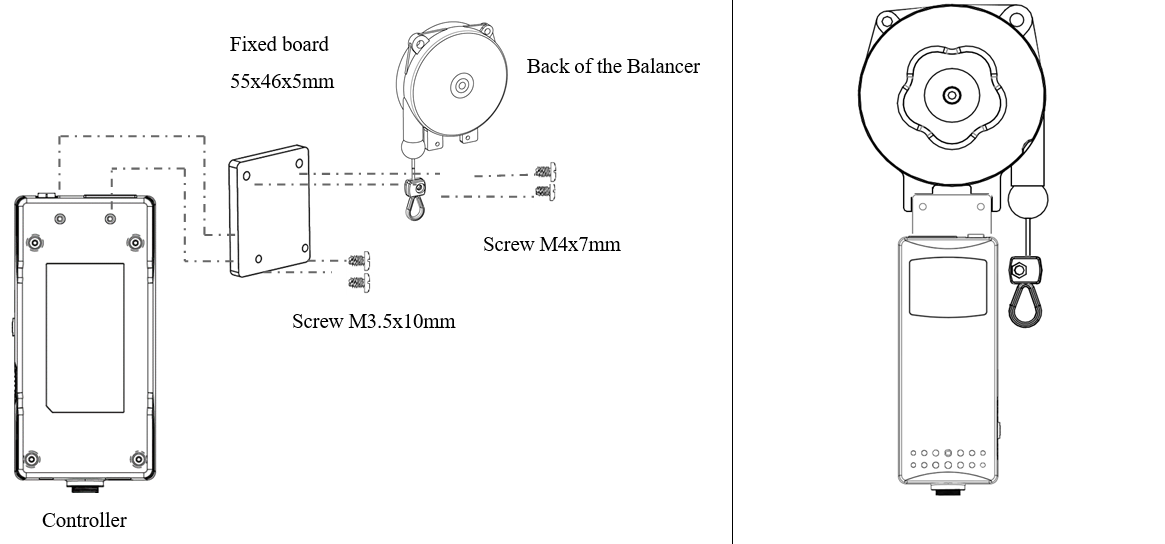
Service Overview
Service Recommendations
Preventive maintenance is recommended at regular intervals. See the detailed information on preventive maintenance. If the product is not working properly, take it out of service and inspect it.
If no detailed information about preventive maintenance is included, follow these general guidelines:
Clean appropriate parts accurately
Replace any defective or worn parts
Installation
Installation Instructions
Installing the Tool
Connect the tool to the power adapter using the supplied cable. Make sure that the guide notch is aligned with the convex point in the socket, then twist it to fix it in the drive.
If required, hang the tool securely, for example from a balancer.
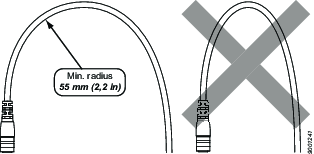
Operation
Ergonomic Guidelines
Consider your workstation as you read through this list of general ergonomic guidelines to identify areas for improvement in posture, component placement, or work environment.
Take frequent breaks and change work positions frequently.
Adapt the workstation area to your needs and the work task.
Adjust for a convenient reach range by determining where parts and tools need to be located to avoid static load.
Use workstation equipment such as tables and chairs appropriate for the work task.
Avoid work positions above shoulder level or with static holding during assembly operations.
When working above shoulder level, reduce the load on the static muscles by lowering the weight of the tool, using for example torque arms, hose reels or weight balancers. You can also reduce the load on the static muscles by holding the tool close to the body.
Take frequent breaks.
Avoid extreme arm or wrist postures, particularly during operations requiring a degree of force.
Adjust for a convenient field of vision that requires minimal eye and head movements.
Use appropriate lighting for the work task.
Select the appropriate tool for the work task.
In noisy environments, use ear protection equipment.
Use high-quality inserted tools and consumables to minimize exposure to excessive levels of vibration.
Minimize exposure to reaction forces.
When cutting:
A cut-off wheel can get stuck if the cut-off wheel is bent or not guided properly. Use the correct flange for the cut-off wheel and avoid bending the cut-off wheel during operation.
When drilling:
The drill might stall when the drill bit breaks through. Use support handles if the stall torque is high. The safety standard ISO11148 part 3 recommends using a device to absorb a reaction torque above 10 Nm for pistol grip tools and 4 Nm for straight tools.
When using direct-driven screwdrivers or nutrunners:
Reaction forces depend on the tool settings and joint characteristics. Strength and posture determine the amount of reaction force that an operator can tolerate. Adapt the torque setting to the operator's strength and posture and use a torque arm or reaction bar if the torque is too high.
In dusty environments, use a dust extraction system or wear a mouth protection mask.
Configuration Instructions
Bit Insertion

Press the slide sleeve into the tool.
Insert the bit.
Release the slide sleeve to engage the bit.

Do not hammer the bit or pull it out by force.
Torque Settings
Select the desired torque setting before operating the screwdriver.
To modify the torque setting, do the following:
To increase the torque, turn the regulating handle clockwise.
To decrease the torque, turn the regulating handle counterclockwise.
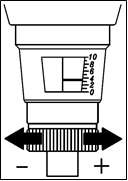
When the selected torque is reached, the internal clutch disengages and a click is heard. This indicates that the power to the motor is cut off.
Use a torque meter to check that the tool is set to the desired torque. The engraved marks on the ring are just for reference.
Secure the regulating handle with a torque cover to prevent torque changes.

Do not use the screwdriver over the 80% of the rated maximum torque to avoid inaccurate clutch escape.
Operating Instructions
Tighten Joint
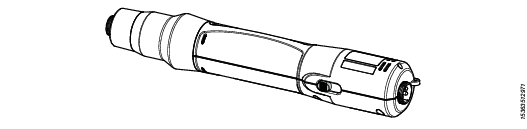
Slide down the button on the handle of the screwdriver to set the tool in forward mode.
Place the tip of the screwdriver on the screw.
Press the trigger and push the bit towards the screw and work piece. The trigger must be pressed during the whole tightening process.
The power adapter gives information about the tightening process:
If the tightening process is performed correctly, the power adapter will show a green light.
If the tightening process is performed incorrectly, the power adapter will show a red light.

Do not change the running direction of the screwdriver while in operation, wait until the tool has stopped.
Unscrew Joint
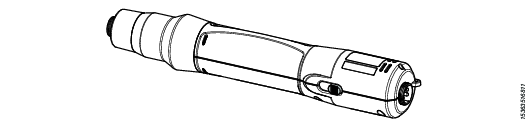
Slide up the button on the handle of the screwdriver to set the tool in reverse mode.
Place the tip of the screwdriver on the screw.
Press the trigger and hold it firmly until the joint is completely loosen. The trigger must be pressed during the whole unscrewing process.

Do not change the running direction of the screwdriver while in operation, wait until the tool has stopped.
Service
Preventing ESD Problems
The components inside the product and controller are sensitive to electrostatic discharge. To avoid future malfunction, make sure that service and maintenance is carried out in an ESD approved work environment. The figure below shows an example of an appropriate service work station.
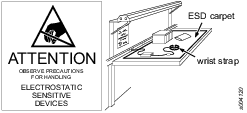
Maintenance Instructions
Service Recommendations
Preventive maintenance is recommended at regular intervals. See the detailed information on preventive maintenance. If the product is not working properly, take it out of service and inspect it.
If no detailed information about preventive maintenance is included, follow these general guidelines:
Clean appropriate parts accurately
Replace any defective or worn parts
Storage
Store the screwdriver, the power adapter and its components at a dry place protected from dust and direct sunlight. Store the bit in grease.
Disconnect the power adapter and remove the bit.
Open the carbon brush cover and blow out any accumulated carbon brush dust with compressed air.
Wipe clean the exterior components.
Troubleshooting
Troubleshooting
The table below shows the most common troubleshooting procedures. Note that some actions must only be done by authorized workshops or qualified service technicians.
Problem | Reason | Action |
---|---|---|
The screwdriver does not run. | The power adapter is not outputting power. | Turn on the relay inside the screwdriver to measure the output voltage. Make sure that the DC voltage is:
|
The connection wire plug 3P-3P, 5P-5P or 6P-6P is broken. | Replace the connection wire plug with a new connection wire or with a new plug. | |
The forward/reverse button is not working properly and no click is heard when the trigger is pressed. | Replace the trigger. | |
Possible damage on the electric braking system of the power adapter. | Contact our authorized workshops or qualified service technicians to perform the repair. | |
The screwdriver is not rotating normally or the motor runs intermittently during forward operation. | The power adapter has a protective circuit and power is only supplied normally from 3 to 5 seconds after the current flow begins. | Operate the tool in reverse mode or rotate the anvil 90 degrees until a click is heard, then operate the tool in forward mode. |
The bit falls out easily. | The bit does not match the specifications. | Change the bit to one matching the specifications. |
The bit is not inserted correctly. | Remove the bit and reinsert it tightly. | |
The bit wobbles. | The bit is not inserted correctly. | Remove the bit, rotate it 60 or 180 degrees and reinsert it tightly. |
The screwdriver does not stop when the selected torque is reached. | An excessive torque setting can strip the screw threads, as a result, the clutch does not activate. | Lower the torque to a level that does not cause stripping. |
Differences in size between the bit and the screw slot lengths can cause slopping. | Change the bit to a suitable one. | |
Possible damage on the electric braking system or on the sensor switch of the power adapter. | Contact our authorized workshops or qualified service technicians to perform the repair. | |
The screwdriver is overloaded. | The handle is overheated or the revolutions plunge rapidly while fastening. | Change the torque of the screwdriver to a higher level or reduce the fastening frequency to prolong the life span of the screwdriver. |
Recycling
Environmental Regulations
When a product has served its purpose it has to be recycled properly. Dismantle the product and recycle the components in accordance with local legislation.
Batteries shall be taken care of by your national battery recovery organization.
Recycling Information
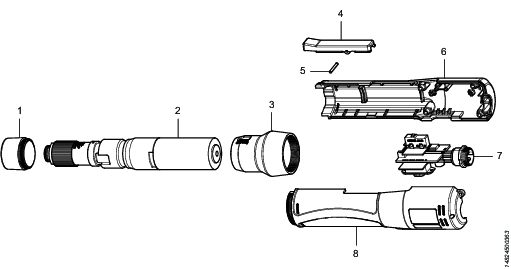
Pos. | Part | Recycle as |
---|---|---|
1 | Front part | Plastic |
2 | Drive unit | Electronics |
3 | Gear housing | Plastic |
4 | Trigger | Plastic |
5 | Pin | Metal, Steel |
6 | Handle complete | Plastic |
7 | Motor complete | Electronics |
8 | Handle complete | Plastic |