Step Restrictions
To make sure the tightening stops if something unexpected happens, it is possible to add step restrictions to the multistep tightening program. These restrictions could, for example, test that a maximum torque is not reached or that a part of the multistep tightening does not take too long to run. Each step has its own set of mandatory step restrictions and optional step restrictions. The mandatory restrictions are included when dragging a new step to the multistep program. All steps can have up to four restrictions each.

In Power Focus 6000 StepSync and Power Focus 8 StepSync controllers, it is possible to use synchronization points in the tightening program. When any condition that is set for a restriction is met, the tool will be stopped immediately and the program jumps to the next synchronization point (only valid for the Power Focus 6000 StepSync, Power Focus 8 StepSync and Flex), or the end of the program. In controllers without StepSync the tool is stopped immediately and the program jumps to the end of the program.

For Flex only:
For each restriction, select Repairable = Yes to allow retry when tightening stops.
The following restrictions are automatically added to every step that is added to the multistep tightening program.
Step Restriction | Applicable steps |
---|---|
Maximum Time | All except External Result and MWR |
Maximum Torque |
|
Maximum Angle |
|
CTh – Cross Thread
This restriction checks the angle from the point where torque passes Start torque (T1) to the point where the torque passes End torque (T2). If the angle measured from Start torque (T1) is higher than Maximum limit (Amax), the tool is stopped immediately.
When the torque passes End torque (T2), the measured angle is checked against the limit Minimum limit (Amin). If the angle is lower than this limit, the tool is stopped immediately.
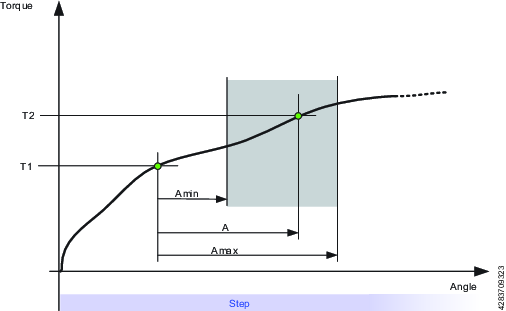
Parameter | Description | In illustration |
---|---|---|
Start Torque | Must be <=0. | T1 |
End Torque | Must be <=0. | T2 |
Minimum Limit | The low angle limit. | Amin |
Maximum Limit | The high angle limit. | Amax |
C – Current

This step restriction is not supported for Power Focus XC.
This restriction checks the actual current where torque passes Torque Trigger. If the actual current exceeds the limits, the tool will be stopped immediately and the tightening program will jump to the next synchronization point or the end of the program. The result will be the first peak or low value, that made the monitor NOK. In case of OK, the result will be the last measured current value. If the torque trigger is never reached during the restriction it will end with status OK.
Parameter | Description |
---|---|
Torque Trigger | Must be >= 0 and < Tool Max Torque. |
Low limit | Lowest acceptable current. |
High limit | Highest acceptable current. |
A – Maximum Angle
This restriction measures the angle. If the measured angle reaches the Maximum Limit, the tool is stopped immediately. The angle is measured from the start of the restriction or, if specified, from the point where the torque passes Trigger Torque for the first time during the restriction.
Parameter | Description |
---|---|
Trigger Torque | If specified, this is the torque from where the angle is measured. |
Maximum Limit | If this limit is reached the tool is stopped immediately. |
T – Maximum Torque
This restriction checks the torque. If the measured torque exceeds the Maximum limit, the tool is stopped immediately.
Parameter | Description |
---|---|
Maximum Limit | If the torque reaches this specified limit the tool is stopped immediately. |
Ti – Maximum Time
This restriction checks the time. If Maximum Limit is reached, the tool is stopped immediately.
Parameter | Description |
---|---|
Maximum Limit | If this time is elapsed, the tool is stopped immediately. |
RH – Rehit
This restriction checks the torque. If the measured torque exceeds the Detection Torque, the tool is stopped immediately and the program jumps to the next synchronization point (for Power Focus 6000 StepSync and Power Focus 8 StepSync), or the end of the program.
It is only possible to add step Rehit restriction to the first step of the multistep tightening program. Once the Rehit restriction has been added to the first step it shall not be possible to move the step to any other position within the tightening program. The Rehit restriction has to be deleted from the first step in order to move it to other position in the tightening program.
Parameter | Description |
---|---|
Detection Torque | If the measured torque exceeds the Detection Torque, the tool is stopped immediately and the program jumps to the next synchronization point (for Power Focus 6000 StepSync and Power Focus 8 StepSync), or the end of the program. Must be greater than zero. |
Angle Window | The angle window is measured from the start of the step. If no Angle Window is set, the restriction is active during the whole step. |
RT – Rescinding Torque
This restriction checks the torque. If the measured torque drops below the condition of the restriction the tool is stopped immediately and the program jumps to the next synchronization point (for Power Focus 6000 StepSync and Power Focus 8 StepSync), or the end of the program.
Torque control processes
The restriction condition is the measured torque. For the restriction to be active the torque must first exceed 110 % of the Rescinding Torque Limit.Angle control processes
This restriction checks the maximum torque reached during the restriction. For the restriction to be active the torque must first exceed the Trigger Torque.
Parameter | Description |
---|---|
Rescinding torque limit | Default: 10 Nm. Must be > 0. |
Parameter | Description |
---|---|
Trigger Torque | Must be > 0. |
Peak torque percentage | Default: 95. Must be >= 50. |
Rescinding torque time | Default: 20. Must be >= 5 and <= 500. |
Rescinding Torque Angle | Must be > 0. |

Cable tools have the option to select Rescinding Torque for Angle. This restriction is controlled by two parameters: Peak Torque Percentage and Rescending Torque Time. Percentage sets the downward deviation from the last peak torque, and Rescending Torque Time sets the duration (between 5 and 500 ms) of that deviation. Only when both conditions (equal to or lower than the indicated percentage for the set duration) are met, will the program be interrupted and jump to the end.
TG – Torque Gradient
This restriction checks the gradient and if it is outside the limits the tool is stopped immediately and the program jumps to the end of the program.
Parameter | Description |
---|---|
Gradient Angle Window | Specifies Angle Window:
|
Angle Window | Available when Gradient Angle Window is set to Manual. Must be > 0 and <= 100. |
Trigger Torque | Must be > 0 and < Tool MaxTorque. |
Damping | Frequency in which the gradient is being calculated. Must be > 0 and < 100 and < Angle window. |
Minimum Limit | Must be >= -100. |
Maximum Limit | Must be > -100 and > Low limit. |
Torque Filter Type | The type of the filter:
|
Cut-off Frequency | Needs to be specified when Torque Filter Type is set to Low pass:
|
Number of Samples | Needs to be specified when Torque Filter Type is set to Sliding Average:
|
TAW – Torque in Angle Window
This restriction checks that the measured torque in the Angle Window Length is between the Torque limits. If the measured torque is outside the limits the tool is stopped immediately and the program jumps to the end. The Angle Window Length starts at the Start Angle from the point that the torque first passed the Trigger Torque. If Trigger Torque is not set, then the Start Angle begins at the start of the restriction.
If the end of the Angle Window Length is not reached, the status of the restriction is NOK.
Parameter | Description |
---|---|
Trigger Torque | Must be >= 0 |
Start Angle | Must be >= 0 |
Window Length | Must be >0 |
Minimum Limit | Must be >= 0 |
Maximum Limit | Must be <= Minimum limit |
TCD - Torque vs Current Deviation
This restriction verifies that all current measurements converted to the corresponding torque are, at most, the Maximum deviation away from the actual torque measured with the torque transducer. The restriction starts when the torque reaches Trigger Torque for the first time during the step and is active until the step reaches its target.
If Trigger Torque is never reached, the monitor will report OK.
Parameter | Description |
---|---|
Trigger Torque | Must be >= 0 |
Maximum Deviation | Default: 1, Must be > 0 |
PCH - Pulse Count High

This restriction is only available for the following tools:
ETV-STR61-100-13
ETV-STR61-70-13
ETV-STR61-50-10
Before using the Pulse Count restriction, the Low Reaction Strategies license must be installed on the controller.
This restriction gives a limit to the number of pulses, and makes sure that those are below the specified pulse count high limit.
If the measured number of pulses is higher than the pulse count high limit, the tool is stopped immediately and the program goes to the next synchronization point or the end of the program.
If the torque trigger level is set, the check starts as soon as the measured torque is above the torque trigger level.
If running a tightening step with Pulse Count High step restriction, use the necessary PulseDrive socket/adapter.
If the tightening step runs without the PulseDrive socket/adapter, all the tightenings are NOK. The step error “PulseDrive socket/adapter not detected” shows for no PulseDrive socket/adapter.
Parameter | Description |
---|---|
Pulse Count High Limit - n+ | Pulse count high limit must range from 1 through 9999999. |
Torque Trigger - Tt | Torque Trigger must range from 0 through the maximum torque of the tool. |