C8-05
Tensioner
Produktinformation
Allgemeine Informationen
Sicherheitsbezogene Signalwörter
Die sicherheitsbezogenen Signalworte Gefahr, Warnung, Vorsicht und Hinweis haben folgende Bedeutung:
GEFAHR | GEFAHR weist auf eine gefährliche Situation hin, die bei Nichtvermeidung zu schweren Verletzungen mit möglicher Todesfolge führen wird. |
WARNUNG | WARNUNG weist auf eine gefährliche Situation hin, die bei Nichtvermeidung zu schweren Verletzungen mit möglicher Todesfolge führen könnte. |
ACHTUNG | VORSICHT weist bei Verwendung mit dem Sicherheitswarnsymbol auf eine gefährliche Situation hin, die bei Nichtvermeidung zu leichten oder mittelschweren Verletzungen führen könnte. |
HINWEIS | Ein HINWEIS wird für Situationen verwendet, die sich nicht auf eine mögliche Verletzungsgefahr beziehen. |
Garantie
Die Produktgarantie verfällt 12+1 Monate nach dem Versand aus dem Distributionszentrum von Atlas Copco.
Normaler Verschleiß von Teilen wird nicht von der Garantie abgedeckt.
Unter normalem Verschleiß versteht man, dass während der für diesen Zeitraum typischen Standardwerkzeugwartung Teile ausgetauscht oder Einstellungen / Verbesserungsarbeiten durchgeführt werden müssen (ausgedrückt in Zeit, Betriebsstunden, oder anderweitig).
Die Produktgarantie stützt sich auf einen korrekten Einsatz, Wartung und Reparatur des Werkzeugs und seiner Bestandteile.
Schäden an Teilen, die als Folge einer unzureichenden Wartung oder eines falschen Einsatzes durch andere Parteien als Atlas Copco oder deren zertifizierten Service-Partner während der Garantiezeit verursacht werden, sind nicht durch die Garantie gedeckt.
Um eine Beschädigung oder Zerstörung von Werkzeugteilen zu vermeiden, warten Sie das Werkzeug entsprechend der empfohlenen Wartungspläne und befolgen Sie die richtigen Anweisungen.
Garantiereparaturen werden nur in Atlas Copco-Werkstätten oder von einem zertifizierten Service-Partner ausgeführt.
Atlas Copco bietet eine erweiterte Garantie und eine vorbeugende Wartung nach dem neuesten Stand der Technik durch seine ToolCover-Verträge. Weitere Informationen erhalten Sie von Ihrem lokalen Servicerepräsentanten.
Für Elektromotoren:
Die Garantie gilt nur dann, wenn der Elektromotor nicht geöffnet wurde.
Website
Informationen zu unseren Produkten, Zubehör, Ersatzteilen und Veröffentlichungen finden Sie auf der Internetseite von Atlas Copco.
Besuchen Sie: www.atlascopco.com.
ServAid
ServAid ist ein Portal, das ständig aktualisiert wird und technische Informationen bietet, wie z.B.:
Behörden- und Sicherheitsinformationen
Technische Daten
Installations-, Betriebs- und Wartungsanweisungen
Ersatzteillisten
Zubehör
Maßzeichnungen
Besuchen Sie: https://servaid.atlascopco.com.
Weitere technische Informationen erhalten Sie bei Ihrem Atlas Copco-Vertreter vor Ort.
Sicherheitsdatenblätter MSDS/SDS
In den Sicherheitsdatenblättern werden die von Atlas Copco vertriebenen chemischen Produkte beschrieben.
Weitere Informationen finden Sie auf der Internetseite von Atlas Copco unter www.atlascopco.com/sds.
Herkunftsland
Informationen zum Herkunftsland sind auf dem Produktetikett angegeben.
Maßzeichnungen
Maßzeichnungen finden Sie entweder im Maßzeichnungsarchiv oder auf ServAid.
Besuchen Sie: http://webbox.atlascopco.com/webbox/dimdrw oder https://servaid.atlascopco.com.
Übersicht
Produktüberblick
Hauptkomponenten

Teilkennung | Beschreibung |
---|---|
A | Geteilte Kontermutter zur Schnellmontage |
B | Kolben |
C | Spanner-Gehäuse |
D | Hebegurt |
E | Hydraulik-Anschlussbuchse (Konfiguration kann variieren) |
F | Hydraulik-Anschlussstecker (Konfiguration kann variieren) |
Separate geteilte Kontermutter
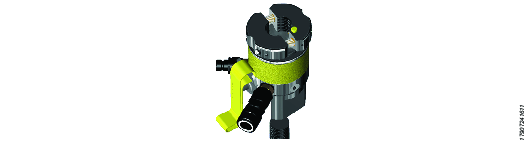
Die geteilte Kontermutter ist eine vollständig separate Komponente und wird an der Schraube montiert, nachdem der Spanner angebracht wurde.
Technische Produktdaten
Technische Produktdaten finden Sie entweder auf ServAid oder auf der Internetseite von Atlas Copco.
Besuchen Sie: https://servaid.atlascopco.com oder www.atlascopco.com.
Zubehör
Anwendungsbereich der Schlitzmutter
Spanner-Gewindegröße | Produktnr. der Schlitzmutter | Gewindegröße der Schlitzmutter |
---|---|---|
C8-05 | 8434220037 | 2-1/4" |
8434220038 | 2-1/2" | |
8434220039 | M56 x 5.5 | |
8434220040 | M60 x 5.5 | |
8434220041 | M64 x 6 |
Installation
Installationsanleitung
Installationsvorbereitungen
Bevor die Hydraulikpumpe an ein Schraubenspanngerät angeschlossen wird, stellen Sie sicher, dass:
Der Betriebsdruck der Hydraulikpumpe mit dem des betriebenen Geräts kompatibel ist.
Die Kapazität des Pumpspeichers ausreichend ist, um das Gerät im gesamten Anwendungsbereich zu betreiben.
Die Hydrauliköl-Spezifikationen, die für die Pumpe und das Gerät verwendet werden, kompatibel sind.
Die technischen Spezifikationen des Spanngeräts bekannt sind.
Stellen Sie sicher, dass eine ausreichende Länge des Bolzens oberhalb der Sechskant- oder Rundmutter herausragt.
Anschluss des Hydraulikschlauchs
Verbinden Sie sämtliche Spanner auf einer Seite des Flanschs mit Verbindungsschläuchen. Schließen Sie die Druckluft-Ableitung an eine frei Steckerverbindung an. Stellen Sie sicher, dass nach der Schlauchmontage eine freie Anschlussbuchse verfügbar ist.
A
Ableitungsschlauch zur Oberfläche und der druckluftbetriebenen Pumpe
B
Typischer Hydraulik-Verbindungsschlauch
Verbinden Sie sämtliche Spanner auf der anderen Seite des Flanschs. Stellen Sie sicher, dass eine freie Steckerverbindung und eine freie Anschlussbuchse verfügbar sind.
Verbinden Sie die beiden Seiten des Flanschs mit dem mitgelieferten Cross-Over-Verbindungsschlauch, der identisch zu den Verbindungsschläuchen ist, nur länger. Verbinden Sie mit dem Cross-Over-Verbindungsschlauch die Anschlussbuchse an der ersten Flanschseite mit dem freien Steckeranschluss auf der zweiten Flanschseite.
A
Flanschseite 1
B
Flanschseite 2
C
Cross-Over-Verbindungsschlauch

Ist das Hydraulikschlauchsystem korrekt angeschlossen, bleibt eine ANSCHLUSSBUCHSE an der Flanschseite 2 frei. Dies ist korrekt und sicher. Eine freie Anschlussbuchse kann SICHER druckbeaufschlagt werden. Ein freier Anschlussstecker dagegen ist NICHT SICHER. Falls ein freier Anschlussstecker zurückbleibt, überprüfen Sie die Montage der Hydraulik-Verbindungsschläuche und korrigieren Sie den Fehler.
Verwendung der geteilten Kontermutter
Die geteilte Kontermutter ist eine vollständig separate Komponente und wird an der Schraube montiert, nachdem der Spanner angebracht wurde.
Positionieren Sie die geteilte Kontermutter über der Schraube.
Drücken Sie den Entriegelungsknopf der Mutter, sodass die Kontermutter in die „offene“ Position schnappt. Die beiden Hälften der geteilten Kontermutter springen auseinander.
Positionieren Sie die geteilte Kontermutter über dem Schraubenüberstand.
Drücken Sie die beiden Hälften der Kontermutter zusammen, nachdem diese auf der Oberfläche des Spannwerkzeugs positioniert wurden. Es ist ein „Klick“ zu hören, wenn die beiden Hälfte in ihrer geschlossenen Position einrasten.
Drehen Sie die Kontermutter mithilfe einer Knebelstange, die in den Schlitz an der Kontermutter eingeführt wird, nach unten, bis sie vollständig am Sitzkonus des Spanners anliegt.
Stellen Sie vor dem Beginn des Spannvorgangs sicher, dass mindestens drei Gewinde oberhalb der geteilten Kontermutter hervorstehen, wenn die geteilte Kontermutter vollständig im Sitzkonus an der Oberseite des Spannwerkzeugs anliegt.
A: Es sollten mindestens drei Gewinde aus der Oberseite der geteilten Kontermutter herausragen.

Belasten Sie niemals eine geteilte Kontermutter, die nicht mit einem „Klick“ in ihre vollständig geschlossene Position eingerastet ist.
Belasten Sie niemals eine geteilte Kontermutter, die nicht über die gesamte Länge vollständig am Gewinde anliegt.

Befolgen Sie den Montagevorgang zur Demontage in umgekehrter Reihenfolge.
Schrauben-Einrichtung
Um eine gleichmäßig verteilte Last auf eine Untersee-Schraubverbindung anzuwenden, wird im Allgemeinen ein Verhältnis zwischen Spanner und Schraube von 100 % vorausgesetzt. Das bedeutet, dass wenn 8 Schrauben am Flansch gespannt werden müssen, 8 Spanner benötigt werden. Alle Schrauben werden gleichzeitig gespannt.
Die korrekte Schrauben-Einrichtung für einen Flansch mit 8 Schrauben.
Beispiele:
Ein Flansch mit 6 Schrauben erfordert 6 Schraubenspanner.
Ein Flansch mit 8 Schrauben erfordert 8 Schraubenspanner.

Achten Sie darauf, wie jede Schraube abwechselnd mit einem weit hervorstehenden Bolzen eingerichtet ist. Die Seite mit dem lang herausstehenden Bolzen ist die Seite, an welcher der Schraubenspanner angesetzt wird.
In diesem Fall werden bei den 4 abwechselnden roten Schrauben Spanner auf der linken Seite des Flansches angesetzt und bei den 4 abwechselnden grünen Schrauben auf der rechten Seite des Flansches.
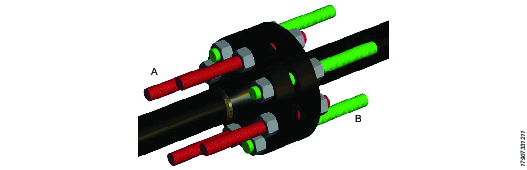
A | Es werden 4 Spannwerkzeuge auf der linken Seite des Flanschs angesetzt. | B | Es werden 4 Spannwerkzeuge auf der rechten Seite des Flanschs angesetzt. |
Technische Daten
Die technischen Spezifikationen Ihrer jeweiligen Schraubenspannwerkzeuge sind in das Spanner-Gehäuse eingestanzt.
Verfahren zur Schrauben-Einrichtung
Stellen Sie sicher, dass die Flansche vollständig eingerastet und die Schrauben und Muttern angezogen sind. Montieren Sie 50 % der Schraubenspannwerkzeuge über den „langen“ Schraubenverlängerungen auf einer Seite des Flanschs.
Stellen Sie sicher, dass nach der Einpassung mindestens drei Gewinde aus der Oberfläche der Kontermutter herausragen.
A
Es sollten mindestens drei komplette Gewinde nach der Einpassung aus der Kontermutter herausragen
Stellen Sie sicher, dass die Flansche vollständig zusammengezogen und die Schrauben und Muttern angezogen sind. Montieren Sie die verbleibenden 50 % der Schraubenspannwerkzeuge über den „langen“ Schraubenverlängerungen auf der anderen Seite des Flanschs.
Stellen Sie sicher, dass nach der Einpassung mindestens drei Gewinde aus der Oberfläche der Kontermutter herausragen.
A
Es sollten mindestens drei komplette Gewinde nach der Einpassung aus der Kontermutter herausragen
Überprüfen Sie den Umfang der Spannerbasis, um sicherzustellen, dass diese vollständig plan auf der Spannoberfläche aufliegt.
Bedienung
Betriebsanleitung
Schrauben-Spannvorgang
Bevor das System druckbeaufschlagt wird
Lesen und beachten Sie die dem Produkt beiliegenden Sicherheitshinweise.
Machen Sie sich mit dem korrekte Betrieb der hydraulischen Pumpeneinheit vertraut.
Machen Sie sich mit dem maximalen Betriebsdruck des Spanners vertraut.
Machen Sie sich mit der maximalen Kolbenbewegung des Spanners vertraut (auf den Wägezellen des Spanners eingestanzt).
Machen Sie sich mit dem erforderlichen Betriebsdruck vertraut, der am Spanner anliegen muss.
Hebeösen und Gurte an Werkzeugen sollten vor der Verwendung überprüft werden. Achten Sie auf Risse und andere sichtbare Schäden. Beschädigte Hebegurte oder Ringschrauben sollten nicht verwendet werden.
Bereit für den Spannvorgang
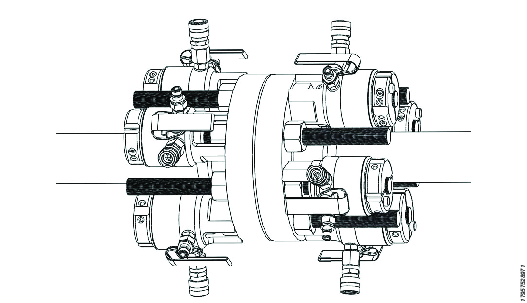

In den folgenden Abbildungen wurden die Hydraulik-Verbindungsschläuche für eine klarere Darstellung entfernt.
Schließen Sie das Absperrventil an der Pumpeneinheit und beaufschlagen Sie das System mit dem benötigten Druck. Überwachen Sie den Druck kontinuierlich während des gesamten Vorgangs. Sobald der Solldruck erreicht ist, halten Sie die Pumpe an (Druck halten). In dieser Phase wird die Schraube zunächst mit der durch den Spanner gehaltenen Last belastet. Der Kolben des Spanners wird ausgefahren und die Flanschmutter hebt sich von der Flanschoberfläche ab.
Überschreiten Sie den maximalen Kolbenhub des Spanners nicht (bei Annäherung an den maximalen Kolbenhub wird ein rotes Band sichtbar).
Achten Sie auf das Manometer der Pumpe, um sicherzustellen, dass der Druck konstant bleibt. Wenn der Druck stabil ist, nähern Sie den Spanner an und drehen Sie die Mutter mithilfe der Knebelstange (durch die Zugangsöffnung des Spanners) zurück herunter zur Verbindungsfläche. Ziehen Sie die Mutter mithilfe eines Hammers und der Knebelstange sicher an der Verbindung fest. Wird die Mutter nicht fest genug angezogen, wird deutlich mehr Zeit zum Abschluss des Spannvorgangs benötigt. Die Reihenfolge, in welcher die Muttern angezogen werden, ist nicht ausschlaggebend, damit jedoch keine vergessen wird, wird empfohlen, sie in der entsprechenden Reihenfolge anzuziehen.
Wiederholen Sie nun den Spannvorgang aus Schritt 1. Die erste Druckbeaufschlagung dient zum Setzen der Flanschschrauben und Muttern. Dies ist hilfreich, um die aufrechterhaltene Schraubenlast zu maximieren. Wiederholen Sie Schritt 1 ein drittes Mal.
Lassen Sie den Druck an der Hydraulikpumpe ab und trennen Sie sämtliche hydraulischen Verbindungsschläuche, Cross-Over-Verbindungsschläuche und die Ableitung, sobald das Öl zurückgeflossen ist. Lösen Sie die geteilte Kontermutter und entfernen Sie alle Schraubenspannwerkzeuge.
Sobald die Spannwerkzeuge an der Oberseite positioniert sind, schließen Sie alle Kolbenstößel, um diese für die nächste Verwendung vorzubereiten.
Entspannungsvorgang
Beim Entspannen stehen normalerweise keine spezifischen Werkzeugdrücke zur Verfügung, da es nicht immer möglich ist, den Druck zu berechnen, bei dem die Flanschmutter sich löst. Als Faustregel gilt: Wenn die ursprünglichen Drücke zur Verschraubung der Flanschmutter zur Verfügung stehen, ist der Entspannungsdruck üblicherweise geringfügig höher als der ursprüngliche Spanndruck (jedoch nicht immer).

Der Maximaldruck, der angelegt werden kann, wurde berechnet, um sicherzustellen, dass entweder 95 % der Materialstreckgrenze der Schraube oder der maximale Werkzeugdruck nicht überschritten werden, wobei jeweils der niedrigere Wert gilt. Die Pumpe muss hierzu entsprechend voreingestellt werden.
Bringen Sie die Spannwerkzeuge an den Schrauben an. Wenn die Kontermutter komplett eingeschraubt ist und am Kolben anliegt, lösen Sie die Kontermutter um eineinhalb Drehungen. So wird vermieden, dass die Kontermutter sich am Kolben festsetzt, wenn die Schraubenspannung gelöst wird.
Führen Sie die Knebelstange durch die Zugangsöffnung des Spanners und in die Öffnung an der Sechskantmutter des Flanschs ein. Beaufschlagen Sie das System mit Hydraulikdruck, bis sich die Flanschmutter drehen lässt, und stellen Sie gleichzeitig sicher, dass der Kolben den maximalen Hub oder der Systemdruck nicht den maximal zulässigen Druck überschreitet.
Drehen Sie jede Flanschmutter um eine vollständige Drehung zurück.
Lassen Sie den Druck aus dem System ab und überprüfen Sie, ob die Flanschmuttern sich weiterhin leicht drehen lassen.
Entfernen Sie die Schraubenspanner.
Wartung
Austausch der Dichtung Typ S2/K2
Achten Sie auf die richtige Ausrichtung des dreieckigen Stützrings.
Setzen Sie den äußeren Stützring auf die äußere Dichtungsrille des Kolbens auf.
Positionieren und dehnen Sie die äußere Dichtung in die äußere Dichtungsrille des Kolbens. Die Dichtung passt über den Stützring.
Drücken Sie die Dichtung mit einem abgerundeten, glatten Schraubendreher in die Dichtungsrille, bis die Dichtung in der Rille einrastet. Achten Sie darauf, dass Dichtung und Stützring vollständig am Umfang anliegen.
Drücken Sie die innere Dichtung in die innere Dichtungsrille.
Drücken Sie die innere Dichtung mit einem glatten, abgerundeten Schraubendreher in ihre Position.
Positionieren Sie den inneren Stützring unter die innere Dichtung.
Biegen Sie den Stützring vorsichtig, damit er einrasten kann. Achten Sie darauf, dass Dichtung und Stützring vollständig am Umfang anliegen.
Wartungsanweisungen
Wartungsempfehlungen
Es wird empfohlen, eine vorbeugende Wartung regelmäßig durchzuführen. Beachten Sie die ausführlichen Informationen über die vorbeugende Wartung. Wenn das Produkt nicht ordnungsgemäß funktioniert, bringen Sie es außer Betrieb und prüfen Sie es.
Wenn keine detaillierten Informationen über eine vorbeugende Wartung enthalten sind, befolgen Sie die folgenden allgemeinen Richtlinien:
Entsprechende Teile gründlich reinigen
Defekte und verschlissene Teile ersetzen
Aufbewahrung und Lagerung
Unterwasser-Vorspannwerkzeuge werden aus Edelstahl mit einer zusätzlichen Elektrolyse-Nickel-Beschichtung gefertigt. Sie sind korrosions- und verschleißfest und rosten unter geeigneten Bedingungen nicht.
Werkzeuge, die Salzwasser ausgesetzt wurden, sollten vor der Lagerung mit Süßwasser abgespült und getrocknet werden.
Werkzeuge, die während der Verwendung Wasser ausgesetzt wurden (aufgrund von Regen oder ähnlichem), sollten vor der Lagerung gründlich abgetrocknet werden. Nach dem Verpacken sollten alle zugänglichen Oberflächen der Werkzeuge mit einem geeigneten, nicht-trocknenden Rostschutzöl eingesprüht werden (zum Beispiel Shell Ensis Fluid oder Castrol Rustillo DW300X). So wird sichergestellt, dass die Werkzeuge über ihre gesamte Lebensdauer hinweg rostfrei bleiben.
Es wird empfohlen, während der Lagerung an sämtlichen Hydraulikanschlüssen die mit ihnen verbundenen Staubkappen korrekt anzubringen, um das Eindringen von Fremdkörpern in die Anschlüsse und damit ihre Verunreinigung zu vermeiden.
Die standardmäßig mitgelieferten Verpackungskisten sind nicht wasserfest und sollten abgedeckt werden (zum Beispiel mit einer wasserdichten Plane oder Plastikfolie), wenn sie für eine längerfristige Lagerung verwendet werden. Die Verpackungskisten schützen gegen gelegentliche Wasserspritzer, sind jedoch nicht für ständig feuchte Bedingungen geeignet.
Verpacken Sie die Werkzeuge in der Kiste mit geeignetem Verpackungsmaterial, damit diese sich nicht bewegen.
Wartung der Spanner

Tragen Sie stets schlagfeste Schutzbrillen und Gesichtsschutz, wenn Sie mit dem Werkzeug arbeiten, es warten oder reparieren, Zubehör austauschen oder sich in der Nähe der Arbeiten am oder mit dem Werkzeug aufhalten.

Vor dem Anschließen oder Abnehmen von Schläuchen, Fittings oder Zubehör oder dem Einstellen oder Abnehmen des Werkzeugs ist die Stromzufuhr abzuschalten.
Während der Montage und der Wartung der Spannwerkzeuge sollten Gewindekomponenten geschmiert und mit einer dünnen Schicht Anti-Seize-Verbindung, wie etwa Copaslip oder Molyslip, geschützt werden, um Rostbildung an den Schraubengewinden sowie ein Verklemmen von Gewindekomponenten während der Verwendung zu vermeiden.
Vor der Installation sollten die Vorderkanten der Dichtungen, der Lagerbänder und der Abstreifdichtungen mit einem geeigneten, leichten Schmiermittel, wie etwa Rocol Aqua-Sil, geschmiert werden. Dies erleichtert die Montage.
Das Werkzeug sollte einmal alle 12 Monate runderneuert werden.
Überprüfen Sie es auf Anzeichen von Korrosion. Werkzeuge, die Anzeichen von Korrosion aufweisen, sollten zum Kundenzentrum zurückgesendet werden.
Nach jeder Verwendung: Überprüfen Sie, ob Öl aus dem Anschluss oder den Adapterstücken austritt. Leckende Adapter oder Anschlüsse sollten mit 25 Nm angezogen werden. Adapter oder Anschlüsse, die auch nach dem Anziehen weiterhin lecken, sollten ausgetauscht werden.
Hebeösen und Gurte an Werkzeugen sollten vor der Verwendung überprüft werden. Achten Sie auf Risse und andere sichtbare Schäden. Beschädigte Hebegurte oder Ringschrauben sollten nicht verwendet werden.
Das Werkzeug sollte nicht fallengelassen oder gegen andere Objekte geschlagen werden, da dies zu Beschädigung der Dichtungsflächen des Werkzeugs und somit zu einem Werkzeugausfall während der Verwendung führen kann.
Die Werkzeugbeschichtung sollte regelmäßig inspiziert und auf Anzeichen von Sprüngen oder Abblätterungen überprüft werden. Es wird empfohlen, Werkzeuge, die Anzeichen von Sprüngen oder Abblätterungen aufweisen, zum Kundenzentrum zurückzusenden.
Falls Sie Zweifel an der Eignung für den Betrieb haben, kontaktieren Sie bitte das Kundenzentrum von Atlas Copco.
Recycling
Umweltschutzbestimmungen
Nachdem ein Produkt seinen Zweck erfüllt hat, muss es ordnungsgemäß recycelt werden. Zerlegen Sie das Produkt und recyceln Sie die Komponenten gemäß örtlicher Vorschriften.