Diz ao usuário se é possível configurar o evento por meio da página “Configurar Evento”.
Power Focus HC (3.9)
Software
Introdução
Nesta seção, é possível achar informações básicas sobre o produto e também convenções de formatação usadas nos tópicos.
Descrição Geral
O Smart Tensioning System (Sistema de Tensionamento Inteligente) é uma solução rastreável e guiada de tensionadores de parafusos que é constituída de três componentes principais. O tensionador inteligente (STT) vem com dispositivos eletrônicos e sensores integrados, que proporcionam feedback instantâneo aos operadores. O Controlador Manual (PFHC) é o trem do sistema, que controla o processo incluindo: a leitura de código de barras integrada, a operação do gerador e a coleta de dados. O sistema como um todo funciona em um circuito fechado, com todos os comandos dados pelo controlador manual. O Gerador vem com um motor para serviços pesados e dispositivos eletrônicos de alto desempenho.
Recursos
Coleta de dados
Sensores de pressão, torque e ângulo
LED na ferramenta
Dispositivos eletrônicos integrados
Identificação da ferramenta e da bateria
Contador de ciclo digital
IHM intuitiva
Benefícios
Total rastreabilidade do processo
Redução do tempo de processamento
Feedback instantâneo a cada etapa
Número mínimo de periféricos
Precisão do processo
Convenções
Para melhorar o entendimento do usuário, certas convenções de formatação são usadas neste documento. As convenções de formatação usadas estão listadas na tabela abaixo.
Elemento | Notação | Descrição | Saída |
---|---|---|---|
Ênfase geral | No espaço de trabalho Programa | Para destacar ou realçar certos elementos de texto. | Texto em Negrito |
Itens da Interface Gráfica do Usuário (GUI) | Selecione o botão Função . | Qualquer referência aos itens encontrados na tela da interface GUI (por exemplo, botões de comando, nomes de ícones e nomes de campos). | Texto em Negrito |
Caminho da Interface Gráfica do Usuário (GUI) > | Em geral, na parte superior da GUI. | Recurso de navegação que mantém registro da localização na GUI. | Por exemplo: Controlador > Programa > Editar |
Entrada do usuário | Insira uma Descrição do programa. | Qualquer texto digitado pelo usuário. | Texto em Negrito |
Nomes de arquivo | Insira um Nome de Arquivo para a exportação. | Arquivos exportados ou importados para o sistema. | Texto em Negrito e Itálico |
Nomes de variáveis e de parâmetros | Insira um Nome para a exportação. | Nomes de variáveis e de parâmetros (sem os valores). | Texto em Itálico |
Valores de variáveis e de parâmetros | Insira um VALOR para a exportação. | Valores de variáveis e de parâmetros. | Texto em MAIÚSCULAS EM NEGRITO |
Saída do sistema | Client.Domain.Models.ExportImportConfiguration | Qualquer saída de texto do sistema. | Texto em Espaçamento uniforme |
Links externos | Links para sites externos que contêm informações relacionadas ao conteúdo ou assunto, que podem incluir:
| Texto selecionável para sites externos | |
Links de documentações internas |
Se disponíveis, esses links serão apresentados embaixo do texto. | Texto selecionável para conteúdo interno |
Regulamento Geral de Proteção de Dados (RGPD)
Este produto permite processar informações pessoais identificáveis, tais como o nome de usuário do sistema, a função e o endereço de IP. A finalidade deste recurso de processamento é melhorar o controle de qualidade através da rastreabilidade e do gerenciamento adequado de acessos.
Caso você decida processar dados pessoais, é necessário estar ciente e cumprir as regras relevantes de proteção de dados, incluindo o RGPD da UE, bem como quaisquer outras leis, diretivas e regulamentos aplicáveis. A Atlas Copco não pode de forma alguma, ser responsabilizada por qualquer utilização do produto feita por você.
Responsabilidades e Advertências
Responsabilidade
Muitas situações no ambiente operacional poderão afetar o processo de aperto e podem exigir uma validação de resultados. Em conformidade com as normas e/ou regulamentos aplicáveis, solicitamos que se inspecione o torque instalado e a direção rotacional depois de qualquer situação que possa influenciar o resultado do aperto. Exemplos de tais situações incluem, porém não se limitam a:
instalação inicial do sistema de ferramentas
alteração do lote de peças, parafuso, lote de parafusos, ferramenta, software, configuração ou ambiente
Alteração nas conexões de ar ou elétricas
alteração na ergonomia da linha, processo, procedimentos ou práticas de qualidade
alteração do operador
qualquer outra alteração que influencie o resultado do processo de aperto
A inspeção deve:
Garantir que as condições da junta não tenham sido alteradas por situações de influência.
Ser realizada após a instalação inicial, manutenção ou reparo do equipamento.
Ocorrer no mínimo uma vez por turno ou em outra frequência adequada.
Avisos
Sobre o Guia do Usuário
O Guia do Usuário descreve como instalar e configurar o PFHC.
Destina-se a todos que operam e dão manutenção no PFHC.
Histórico das revisões
Número da Versão | Data da Revisão | Descrição da Revisão |
---|---|---|
item | item | none |
3.9 | 01/2023 | NOVO conteúdo: ATUALIZAÇÃO do conteúdo: Parâmetros de serviço do parafuso Informações exportadas e formato do arquivo Trabalhar com a Aba Settings (Definições) |
3.8 | 09/2022 | Primeira versão oficial do Guia do Usuário do Power Focus HC. |
Pré-requisitos
Qualquer pessoa interessada em aprender mais sobre o PFHC pode se beneficiar com a leitura desse Guia do Usuário.
Para uma plena compreensão dos aspectos técnicos descritos no Guia do Usuário, recomendamos o seguinte:
Conhecimento sobre técnicas de aperto
Experiência de trabalhar com as versões anteriores do Power Focus
System Overview (Visão Geral do Sistema)
Estrutura do Software
Visão Geral do Menu
O GUI da Web, acessado no computador externo, possui vários menus disponíveis para realizar o seguinte:
Configurar tensionamento e acessórios do hardware
Realizar a manutenção da ferramenta
Gerenciar o software
Visualizar relatórios
GUI do controlador, exibido no display do controlador manual, é uma interface de usuário para operação e monitoramento do sistema.
GUI da Web
Aba de tensionamento
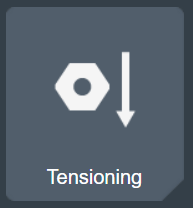
A aba Tensioning (Tensionamento) lista os programas de tensionamento armazenados no controlador manual que se encontram disponíveis para um tensionamento individual.
As configurações de tensionamento estão descritas na aba Tensioning (Tensionamento).
Aba Configuration (Configuração)
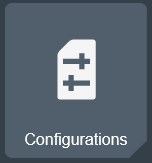
Uma lista de configurações é fornecida na aba Configurations (Configurações). Configurações comuns dependem do tipo de tensionador e bomba hidráulica conectados.
Aba Tensioner Controller (Controlador do Tensionador)
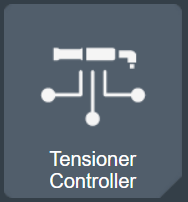
A aba Controlador lista componentes de hardware e software.
As versões de software armazenadas e usadas no controlador manual estão listadas e podem ser atualizadas.
Também é possível importar ou exportar definições para o controlador manual e a partir dele.
Aba Reports (Relatórios)
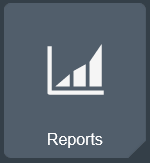
A aba Reports (Relatórios) lista os resultados e eventos de tensionamento.
Aba Settings (Definições)
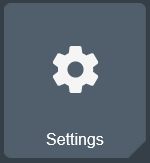
A aba Settings (Definições) é utilizada para configurar as definições específicas do controlador,como data e hora, código PIN, eventos e rede sem fio.
Aba Help (Ajuda)
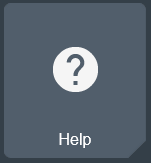
A aba Help (Ajuda) contém seções de ajuda úteis sobre o controlador manual.
GUI do controlador
Aba Tarefas
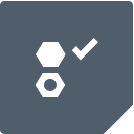
A aba Tarefas lista os programas de tensionamento armazenados no controlador manual que se encontram disponíveis para um tensionamento individual. As configurações de tensionamento estão descritas na aba Tensionamento na GUI da Web.
Aba Reports (Relatórios)
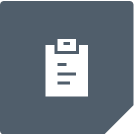
Na aba Reports (Relatórios), os resultados do tensionamento estão listados e o relatório pode ser gerado e salvo em um unidade flash USB.
Aba Controller Information (Informações do Controlador)
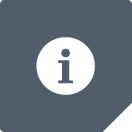
A aba Controller Information (Informações do Controlador) lista os dados da unidade do controlador manual, como número de série, endereço IP e versão do software.
Aba Settings (Definições)
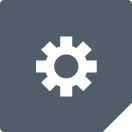
A aba Settings (Definições) permite definir data e hora e limpar resultados.
Aba Connected Devices (Dispositivos Conectados)
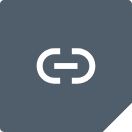
A aba Connected Devices (Dispositivos Conectados) mostra o status da conexão do tensionador e bomba conectados ao controlador manual.
Ela lista os dados da unidade do tensionador e bomba conectados, como número de série e versão do software. Também mostra a contagem da barra extratora do tensionador.
Operação e Manuseio
GUI da Web
GUI Buttons and Icons (Botões e Ícones da GUI)
Botão | Nome | Descrição |
---|---|---|
![]() | Adicionar | Acrescente um item adicional. |
![]() | Remover | Remova um item. |
Ellipsis (Elipse) | Edite um item. | |
![]() | Voltar | Volte para a exibição anterior. |
![]() ![]() | Scroll up (Rolar para cima) Scroll down (Rolar para baixo) | Mova em uma lista que é longa demais para a tela. |
![]() ![]() | Maximize Minimize | Maximize ou minimize uma seção com parâmetros. |
![]() ![]() | Back (Voltar (ao início) (em uma lista)) Back (Voltar (em uma lista)) | Mova para trás em páginas de uma lista. |
![]() ![]() | Forward (Avançar (para o fim) (em uma lista)) Forward (Avançar (em uma lista)) | Mover para frente em páginas de uma lista. |
![]() | Fechar | Toque para fechar a janela. |
![]() | Notice (Aviso) | Sinalização mostrando que um parâmetro está erradamente configurado). |
![]() | AVISO | Sinalização indicando que a há uma aviso sobre o risco de lesões. |
![]() | Validate program (Validar programa) | Toque para verificar se um programa é válido. |
![]() | Download manual | Toque para baixar um manual. |
![]() | Go home (Ir para a página Inicial) | Acessar a tela inicial. |
![]() | Go result (Ir para o resultado) | Acesse a tela de resultados em tempo real. |
GUI do controlador
GUI Buttons and Icons (Botões e Ícones da GUI)
Os botões no teclado do controlador manual são sensíveis ao contexto. Os botões ativos são representados por ícones na GUI do controlador. Esses ícones mostram a funcionalidade atual dos botões do teclado. Por exemplo, na visualização Inicial, os botões ativos são representados pelos seguintes ícones (veja a figura abaixo):
Voltar (para a esquerda)
Avançar (para a direita)
Para cima
Para baixo
Enter
Para navegar, utilize os botões para a esquerda, para a direita, para cima e para baixo no teclado. Para inserir um menu ou confirmar uma escolha, utilize o botão Enter na parte central.
Para informações sobre todos os ícones na GUI do controlador, consulte a tabela abaixo.
1 | Voltar |
2 | Avançar |
3 | Para cima |
4 | Para baixo |
5 | Enter (selecionar) |
6 | Status da conexão do Wi-Fi e do ToolsNet |
Botão | Nome | Descrição |
---|---|---|
![]() | Voltar | Volta para a visualização anterior |
![]() | Avançar | Continuar. |
![]() | Para cima Para baixo | Move para cima ou para baixo em uma lista |
![]() | Enter | Confirma a opção selecionada |
![]() ![]() | Mais | Outras informações ou ações |
![]() | Avançar | Vai para a próxima visualização. |
![]() | Voltar | Vai para a visualização anterior. |
![]() | Status da conexão Wi-Fi | Conectado ao Wi-Fi |
![]() | Status da conexão Wi-Fi | Não conectado a Wi-Fi |
![]() | Status da conexão do ToolsNet | Conectado ao ToolsNet |
![]() | Status da conexão do ToolsNet | Não conectado ao ToolsNet |
Luz de sinalização de Status de LED
A matriz do LED no tensionador é imitada na GUI do controlador manual durante o processo de tensionamento. Para mais informações sobre a Luz de sinalização de Status de LED, veja as Instruções do Produto Tensionador STT.
Guia de Início Rápido
Para criar uma melhor visão geral do sistema, esta seção apresenta um guia rápido abrangendo as etapas básicas para iniciar no Sistema de Tensionamento Inteligente e Software Power Focus.

Esta seção não explica todos os recursos do sistema, mas concentra-se nos recursos mais básicos.
Para iniciar o sistema, a bomba e o tensionador devem estar conectados ao controlador manual antes de ligar a alimentação na bomba hidráulica com a botão liga/desliga.
Executar o rundown do tensionador diretamente na parte superior do parafuso. Certifique-se de que o soquete dentro do tensionador está encaixado na porca movendo o torquímetro de estalo. Ouça o som do clique. Observe se o tensionador gira à medida que o torquímetro aplica força à porca.
Quando o ícone Tasks (Tarefas) no controlador manual estiver ativo, execute o Manual mode (Modo Manual) usando os botões do teclado no controlador manual.
Defina a pressão-alvo para uma pressão baixa, por exemplo, 500 bares, e em seguida pressiona o botão Pressurizar.
Se o motor estiver funcionando, mas não houver aumento de pressão, o problema mais comum é o motor estar funcionando para trás. Desligue o sistema e inverta as fases do conector de alimentação; em seguida, tente novamente.
Quando o sistema estive pressurizado, mova o torquímetro de estalo para visualizar as atualizações de leitura de Ângulo e Torque.
Para informações mais detalhadas sobre a partida do sistema do Sistema de Tensionamento Inteligente, consulte o Guia de Trabalho do Sistema de Tensionamento Inteligente.
Instalação e atualização
Nesta seção, é possível encontrar informações para ajudar com a instalação inicial do produto ou atualizar de uma versão para outra.
Requisitos de navegador da web
Para um desempenho ideal, use um navegador da web que possua um bom desempenho do JavaScript, e habilite o cache do navegador.
É possível executar o software por meio dos seguintes navegadores web:
Google Chrome 70 ou posterior
Microsoft Edge 79 ou posterior.
Firefox 63 ou posterior
Configuração
Nesta seção, é possível encontrar detalhes sobre como criar, modificar e verificar as configurações do produto.
Conectando à GUI de Configuração do PFHC
Para um desempenho ideal, use um navegador da web que possua um bom desempenho do JavaScript, e habilite o cache do navegador.
Abra a tampa da porta de conexão de USB do controlador manual.
Conecte um PC ao conector USB-C no controlador manual. Para garantir que o PC forneça alimentação suficiente ao controlador manual, use portas USB-3.0.
Para inserir a GUI de configuração, insira o endereço a seguir em seu navegador: http://169.254.1.1/config.html.
Consulte mais informações na seção Requisitos de navegador da web.
GUI da Web
Resultados ao vivo
Abra a visualização de resultados ao vivo clicando no ícone de resultados no canto inferior esquerdo, quando ele estiver visível.
São exibidos o status, o torque e o ângulo.
Clique no ícone de conexão no canto superior direito na visualização de resultados ao vivo para abrir a visualização do status do protocolo.
Trabalhando com a Aba Tensioning (Definições)
Esta seção descreve a estratégia de tensionamento de múltiplas etapas, e como criar um programa de tensionamento.
Na visualização da Página Inicial, acesse a aba Tensioning (Tensionamento), e depois selecione Multistep Program Library (Biblioteca do programa de múltiplas etapas).
Interface de usuário de Configurações Múltiplas
A Interface do Usuário para a configuração de um programa de Múltiplas Etapas consiste nas principais áreas a seguir:
No painel esquerdo, na aba Properties (Propriedades), há as General Settings (Definições gerais) do programa de tensionamento de múltiplas etapas, contendo o Program name (Nome do programa)..
No painel esquerdo, a aba Program (Programa) tem um menu suspenso contendo Steps (Etapas).
Para o programas de Múltiplas Etapas, clique em Steps (Etapas), arraste o ícone de etapa adequado - Tensioning (Tensionamento) ou Tensioning Service (Serviço de Tensionamento) da lista até a área de tensionamento. Solte o ícone da etapa selecionada entre o início e o final do programa.
O programa Tensioning Manual (Manual de Tensionamento) é criado automaticamente pelo controlador manual e pode ser editado conforme necessário.
A principal área da interface é composta pela tensioning area (área de tensionamento). Essa é a área que engloba todas as etapas no programa de tensionamento.
Programa Manual Padrão
Em Multistep Program Library (Biblioteca do programa de múltiplas etapas), selecione Default Manual Program (Programa de Múltiplas Etapas Padrão) O Default Manual Program (Programa Manual Padrão) é automaticamente criado. O programa manual pode ser executado com todos os tamanhos e tipos de ferramentas tensionadoras.
O programa manual contém três configurações para controle do comportamento do modo manual. O nome do programa manual pode ser editado em General Settings > Properties (Definições gerais > Propriedades).
Configurações Gerais
General Settings (Definições Gerais) consiste do Nome do campo.
Selecione um programa, acesse a aba Properties (Propriedades) para editar General Settings (Definições Gerais) inserindo o nome no campo cadeia de texto livre.
O nome do programa escolhido é exibido na GUI do controlador nos programas listados em diferentes tipos de trabalho na aba Tasks (Tarefas).
Parâmetros do Modo Manual
No Programa Manual Padrão, clique no ícone Manual de Tensionamento na área de tensionamento para editar os seguintes parâmetros:
Nome
Pressão hidráulica manual padrão (bar)
Pressão hidráulica máx. do sistema (bar)
Parâmetro | Padrão | Descrição | Comentários |
---|---|---|---|
Nome | Etapa Modo Manual | Nome da cadeia de caracteres da etapa | Não utilizada, uma vez que o modo manual não gera resultados. |
Pressão hidráulica manual padrão (bar) | 1000 | Utilizado para preencher a janela Definir pressão do modo Manual quando o modo Manual é executado pela primeira vez após a inicialização do sistema. | A pressão manual padrão confirma se o operador não apenas reutiliza uma pressão anterior de uma execução anterior do modo Manual. Defina a pressão-padrão com um valor adequado a sua aplicação. Após utilizar o modo Manual, o sistema supõe que essa é a pressão adequada à operação atual. A última pressão utilizada é usada como a pressão do modo Manual até que o sistema seja desligado. È sempre possível alterar a pressão-alvo na GUI do controlador. |
Pressão hidráulica máx. do sistema | 1980 | O alvo mais alto de pressão permitido ao utilizar essa configuração. | O sistema está utilizando a pressão máx.mais baixa de suas unidades conectadas. Caso qualquer das unidades conectadas apresente uma pressão máx. inferior, a pressurização para neste nível de pressão. |
Programa de Tensionamento
Na exibição da Página inicial, selecione a aba Tensioning (Tensionamento). Multistep Program Library (Biblioteca do programa de múltiplas etapas) é selecionada automaticamente.
Para acrescentar um programa de tensionamento, clique no ícone, clique no ícone Plus (Mais) acima da lista do programa para abrir a aba Program (Programa), e depois clique em Steps (Etapas).
Se algum programa de tensionamento já estiver disponível, selecione o programa para editá-lo.
Arraste e solte as etapas de tensionamento na área

As etapas só podem ser colocadas entre o ponto inicial e final do programa.
Os botões Delete Tightening Program (Excluir programa de aperto) e Copy Tightening Program (Copiar programa de aperto) estão disponíveis no canto inferior direito para excluir e copiar o programa.

Um sistema de tensionamento só usa uma etapa por configuração.
As alterações feitas em programas de aperto em qualquer seção precisam ser ativamente aplicadas clicando-se no botão Apply (Aplicar) no canto inferior direito da GUI. Ou as alterações podem ser realizadas clicando-se no botão Undo (Desfazer) no mesmo local.
Ao navegar para fora da seção onde as alterações foram feitas (usando o botão Back (Voltar), Home (Página Inicial) ou Result (Resultado)), será apresentado um pop-up de aviso onde as alterações podem também ser aplicadas ou desfeitas. O usuário não pode prosseguir sem aplicar ou desfazer as alterações.
Função | Descrição | |
---|---|---|
Start and end points (Pontos de início e fim) | ![]() | Pontos de início e fim do programa de múltiplas etapas. Todas as etapas devem ser colocadas entre esses dois pontos. |
Mostrando propriedades de uma etapa | ![]() | Clique na etapa para revelar as propriedades. |
Fechando propriedades de uma etapa | ![]() | Clique em qualquer lugar na área de aperto para fechar o menu properties (Propriedades). |
Excluindo uma etapa | ![]() | Clique na nas Propriedades da etapa e clique em Delete (Excluir) na parte inferior do menu |
Erro de etapa | ![]() | Quando ocorre um erro de validação em uma etapa, essa etapa será marcada. Observe que quando step properties (Propriedades da etapa) é aberto, os parâmetros que geram o erro também serão marcados. Clique na marcação em vermelho para obter mais informações sobre o erro. |
Colocação proibida | ![]() | Quando uma colocação em particular de uma etapa não é permitida, o ícone de espaço reservado não será mostrado. |
Parâmetros de tensionamento
Under Program tab, click on the Tensioning item to open it and edit the parameters. As convenções de formatação usadas estão listadas na tabela abaixo. See also Diagram of the tensioning process in the section Tensioning process.
Parâmetro | Valor padrão | Unidade | Descrição | Comentários | |
---|---|---|---|---|---|
a All default values are tailored for an M36 bolt running with min angle 40 degrees and no max angle. b The rotation detection parameters define an expected play in the wrench-socket-gear box chain. The experience is that this can vary a lot depending on, mainly bolt geometry – even when the tool is attached to the same bolt but the socket aligns to different sides of the nut. c The rotation detection parameters define an expected play in the wrench-socket-gear box chain. The experience is that this can vary a lot depending on, mainly bolt geometry – even when the tool is attached to the same bolt but the socket aligns to different sides of the nut. | |||||
Nome |
| User name of the step configuration, written in the xml report file and reported in the step Results. | |||
Tamanho do parafuso | M36 a | mm | The size of the bolt for the intended configuration. The bolt size is compared to the connected tool and if it does not match, an invalid configuration event is emitted. | The controller GUI filters out the configurations that fit the connected tools. Configurations made for other tool sizes are not displayed in the list under Tasks > Assembly or Tasks > Batch Assembly. | |
Tensioner type | Flange bolt | Tensioner type must match the connected tensioner. The string is compared to the string that identifies the type of tensioner which is programmed in the tensioner during its production. The string is case sensitive when compared to the string in the tensioner. | The controller GUI filters out the configurations that fit the connected tools. Configurations made for other tensioner types are not displayed in the list under Tasks > Assembly or Tasks > Batch Assembly. | ||
Min nut rotation angle | 40 | Graus | The minimum nut rotation angle for an OK tensioning. | The field can be left empty if the tensioning process does not depend on minimum tightening angle. | |
Max nut rotation angle | Graus | The maximum nut rotation angle for an OK tensioning. | The field can be left empty if the tensioning process does not depend on the maximum tightening angle. | ||
Angle approval | Approve last angle | Controls the behavior of the angle measurement when re-tensioning after NOK result. Choices are:
| For configurations that require max angle, it is recommended to use only the last angle. For configurations that require min angle, use angle summarization in order to consider the sum of all attempts for OK/NOK results. For configurations that define an angle range, consider which behavior applies for the job the that the configuration is tailored for. | ||
Use clamping force estimation | Ativo | Controls which clamping force estimation is used for the result. On -> Clamping force estimation is used: tensioning force – Estimated Initial mean settlement Off -> clamping force is calculated according to Load Transfer Factor equation: tensioning force / (1.01 + (bolt diameter / clamping length)) | The Atlas Copco (AC) Load Transfer Factor (LTF) equation utilized in the STS is for use on ‘Flange’ connected joints only. Do NOT use on foundation style joints. | ||
Clamping length | mm | The height of the flange, i.e. the distance between the nuts on each side of the flange. Active when: Use clamping force estimation is ’Off’. | Visible if Use clamping force estimation is ’Off’. | ||
Estimated initial mean settlement | 99 | kN | An estimation of the average force loss when releasing the pressure. Active when: Use clamping force estimation is ’On’. | Visible if Use clamping force estimation is ’On’. It is used in the xml report generation. The value depends on the tensioner size and the type of the flange. | |
Estimated initial max settlement | 155 | kN | An estimation of the maximum force loss when releasing the pressure. Active when: Use clamping force estimation is ’On’. | Visible if Use clamping force estimation is ’On’. It is used in the xml report generation. The value depends on the tensioner size and the type of the flange. | |
Min required average clamping force | 510 | kN | The minimum average clamping force for all bolts on the flange used in flange summary section in the xml report. Active when: Use clamping force estimation is ’On’. | Visible if Use clamping force estimation is ’On’. It is used in the xml report generation. The value depends on the tensioner size and the type of the flange. | |
Batch job report type | Geral | Controls the flange summary generation in the xml reports:
| Taylored for Vestas xml report requirements: First round, Second round, User General for Service jobs. | ||
Angle sensor reset force | 100 | kN | The force at which the angle measurement reference for 0 degrees is set. | The expected angles are calculated depending on the force increase from the angle sensor reset force to Min bolt tensioning pressure. This evaluates to different pressures depending on the tensioner size, see the table in the section Pressures for Different Tensioner Sizes. The larger the tensioner is, the higher the angle reset force must be set, due to issues with control of low pressures in installation check step. This is necessary in order to avoid overshooting of Installation check hydraulic pressure higher than pressure equivalent of angle sensor reset force. | |
Min bolt tensioning pressure | 1900 | Bar | The min pressure for an OK tensioning result. | The pressure control in the system will set a target value higher than the Min bolt tensioning pressure to avoid pressure drop ending in a NOK result. See the picture in the section Hydraulic Pressure Target Window. | |
Max system hydraulic pressure | 1980 | Bar | The highest pressure the pressure control in the hand controller allows for this configuration. | The actual max pressure is the lowest of the max pressures in the pump and tensioner and the Max system hydraulic pressure of the configuration. | |
Min bolt tensioning force | 698 | kN | Force equivalent of the Min bolt tensioning pressure parameter. | Value manually calculated from bolt pressure. This value is written in the xml report files, but it is not used by the hand controller's software. | |
Lista de verificação da instalação | 20 | Nm | The required torque for an acknowledged installation check. | ||
Installation check torque duration | 1,0 | S | The required time the Installation check torque must be applied for an acknowledged installation check. | ||
Torque-alvo final | 100 | Nm | The required torque for an acknowledged tightening of the nut. | ||
Resultado de torque de aperto | 1,0 | S | The required time the Tightening target torque must be applied for an acknowledged tightening of the nut. | ||
Tightening unexpected clockwise rotation detection angle | 5 | Graus | The maximum allowed change of the nut rotation angle in clockwise direction when the process is waiting for pressure release. | To avoid the risk of nut rotation while the system waits for pressure release, activate automatic pressure release (see section Tool Configuration). b | |
Tightening unexpected counter clockwise rotation detection angle | 5 | Graus | The maximum allowed change of the nut rotation angle in counter clockwise direction when the process is waiting for pressure release. | To avoid the risk of nut rotation while the system waits for pressure release, activate automatic pressure release (see section Tool Configuration). c | |
Installation check hydraulic pressure | 20 | Bar | The pressure set point for installation check. | The installation check pressure fixes the tensioner to the flange during the installation check. The installation check pressure, including overshoot, must not exceed the pressure equivalent of Angle reset force. | |
Hydraulic pressure set point factor | 1,025 | The actual set point for the pressure regulation is calculated as follows: Min bolt tensioning pressure times Hydraulic pressure set point factor. See the picture in the section Hydraulic Pressure Target Window. | When pressing and holding the pressurization button, the system is pressurized, the pressure will be held inside a pressure window above Min bolt tensioning pressure. |
Processo de tensionamento
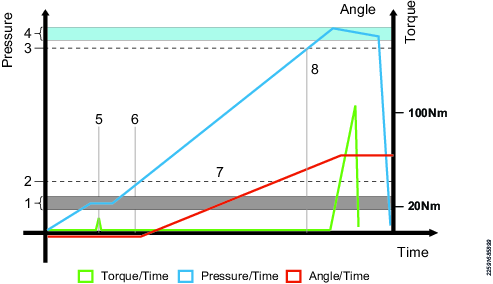
1 | Pressão hidráulica de verificação de instalação |
2 | Força de redefinição do ângulo |
3 | Pressão mínima de tensionamento do parafuso |
4 | Janela-alvo de pressão. Com o botão pressurizar mantido apertado, o sistema manterá a pressão dentro da janela. |
5 | Verificação de instalação. Define a mecânica em uma posição conhecida. A porca não gira. A folga na catraca e caixa de engrenagem é fixada no sentido do aperto. |
6 | Obtém-se amostra do ponto de referência do ângulo. A medição do ângulo de aperto começa neste ponto. |
7 | Pressão aumenta, rotação da porca OK, mas não é necessário aplicar qualquer torque alto. Deixe o sistema hidráulico fazer o trabalho. |
8 | Pressão mínima do parafuso alcançada. Fixação final da porca. |

Se a pressão de verificação de instalação terminar mais alta do que a pressão que corresponde à força de redefinição do ângulo, o processo de tensionamento não define seu ponto de referência de ângulo (6).
Portanto, a força de redefinição do ângulo do parâmetro pode ter que ser ajustada, dependendo do tamanho do tensionador, para incluir alguma margem para sobreapertos de pressão de verificação de instalação. A pressão de verificação de instalação real depende, por exemplo,do tipo de óleo ou temperatura do óleo. Consulte a tabela na seção Pressões para Diferentes Tamanhos de Tensionador.
Pressões para Diferentes Tamanhos de Tensionador
Força de redefinição do ângulo 100 kN com pressões equivalentes calculadas para diferentes tamanhos do tensionador são exibidas na Tabela 1.
Tensionador | Força de redefinição do ângulo (kN) | Pressão de redefinição do ângulo (em bar) |
---|---|---|
M36 | 100 | 272 |
M42 | 100 | 198 |
M48 | 100 | 151 |
M56 | 100 | 109 |
M64 | 100 | 83 |
M72 | 100 | 64 |
As definições da força de redefinição de diferentes tensionadores com margem para pressão de verificação de instalação são mostradas na Tabela 2.
Tensionador | Força de redefinição do ângulo (kN) | Pressão de redefinição do ângulo (em bar) |
---|---|---|
M36 | 100 | 272 |
M42 | 100 | 198 |
M48 | 150 | 226 |
M56 | 200 | 219 |
M64 | 200 | 166 |
M72 | 250 | 161 |
Janela-alvo de pressão hidráulica
A figura abaixo ilustra como o sistema mantém a pressão dentro da janela-alvo de pressão ao se manter pressionado o botão de pressurização.
Veja também o Diagram of the tensioning process (Diagrama do processo de tensionamento) na seção Processo de tensionamento.
1 | Pressão mínima de tensionamento do parafuso (y) |
2 | Alvo de pressão hidráulica (x) |
3 | Nível de histerese da pressão hidráulica (x-y)/3 |
Cálculo
Alvo de pressão hidráulica (x) = Pressão minima de tensionamento do parafuso (y) × Fator-alvo de pressão hidráulica (k)
Nível de histerese de pressão hidráulica = 1/3 da distância entre o alvo de pressão hidráulica (x) e a pressão mínima de tensionamento do parafuso (y).
A pressurização tem início nesse nível para mantê-la acima do nível mínimo.
Parâmetros de serviço do parafuso
Parâmetro | Valor padrão | Unidade | Descrição | Comentários | |
---|---|---|---|---|---|
a All default values are tailored for an M36 bolt running with min angle 40 degrees and no max angle. b The rotation detection parameters define an expected play in the wrench-socket-gear box chain. The experience is that this can vary a lot depending on, mainly bolt geometry – even when the tool is attached to the same bolt but the socket aligns to different sides of the nut. c The rotation detection parameters define an expected play in the wrench-socket-gear box chain. The experience is that this can vary a lot depending on, mainly bolt geometry – even when the tool is attached to the same bolt but the socket aligns to different sides of the nut. | |||||
Nome | User name of the step configuration, written in the xml report file and reported in the step Results. | ||||
Tamanho do parafuso | M36 a | mm | The size of the bolt for the configuration intended for it. The bolt size is compared to the connected tool and if it does not match, an invalid configuration event is emitted. | The controller GUI filters out the configurations that fit the connected tools. Configurations made for other tool sizes are not displayed in the list under Tasks > Bolt Service or Tasks > Batch Bolt Service. | |
Tensioner type | Flange bolt | Tensioner type must match the connected tensioner. The string is compared to the string that identifies the type of tensioner which is programmed in the tensioner during its production. The string is case sensitive when compared to the string in the tensioner. | The controller GUI filters out the configurations that fit the connected tools. Configurations made for other tensioner types are not displayed in the list under Tasks > Bolt Service or Tasks > Batch Bolt Service. | ||
Max delta nut rotation | 13 | Graus | The max total allowed rotation of the nut for the bolt service process, i.e. the maximum nut rotation in tightening direction compared to the starting point. | See also section Bolt Service Process. | |
Min delta nut rotation | 0 | Graus | The minimum actual nut rotation that is allowed for the bolt service process. | Min delta nut rotation and max delta nut rotation create a range of accepted result of the bolt process, e.g. 0.13 - the nut needs to return to its original position (Min delta nut rotation = 0) but must not rotate more than 13 degrees in the tightening direction Max delta nut rotation = 13). A value < 0 for Min delta nut rotation allows that the nut does not return completely to the original position. | |
Use clamping force estimation | Ativo | Controls which clamping force estimation is used for the result. On -> Clamping force estimation is used: tensioning force – Estimated Initial mean settlement Off -> clamping force is calculated according to Load Transfer Factor equation: tensioning force / (1.01 + (bolt diameter / clamping length)) | The Atlas Copco (AC) Load Transfer Factor (LTF) equation utilized in the STS is for use on ‘Flange’ connected joints only. Do NOT use on foundation style joints. | ||
Clamping length | mm | The height of the flange, i.e. the distance between the nuts on each side of the flange. | |||
Estimated initial mean settlement | 99 | kN | An estimation of the mean force loss when releasing the pressure. Active when: Use clamping force estimation is ’On’. | Visible if Use clamping force estimation is ’On’. It is used in the xml report generation. The value depends on the tensioner size and the type of the flange. | |
Estimated initial max settlement | 155 | kN | An estimation of the maximum force loss when releasing the pressure. Active when: Use clamping force estimation is ’On’. | Visible if Use clamping force estimation is ’On’. It is used in the xml report generation. The value depends on the tensioner size and the type of the flange. | |
Min required average clamping force | 510 | kN | The minimum average clamping force for all bolts on the flange used in flange summary section in the xml report. | It is used in the xml report generation. The value depends on the tensioner size and the type of the flange. | |
Batch job report type | Geral | Controls the flange summary generation in the xml reports:
| |||
Nut loosening attempt count torque | 75 | Nm | The torque limit for a loosening attempt. If the number of attempts passes Nut loosening number of attempts, the bolt service process prompts the user to tighten the bolt again because it was not possible to loosen it. | ||
Nut loosening number of attempts | 3 | The number of attempts with torque higher than Nut loosening attempt count torque before prompting the user to tighten the nut again since it was not possible to loosen it. | |||
Nut loosening min loosening angle | 10 | Graus | The required loosening angle for an acknowledged bolt service operation. | ||
Angle sensor reset force | 100 | kN | The force at which the angle measurement reference for 0 degrees is set. | The expected angles are calculated depending on the force increase from the angle sensor reset force to Min bolt tensioning pressure. This evaluates to different pressures depending on the tensioner size, see the table in the section Pressures for Different Tensioner Sizes. The larger the tensioner is, the higher the angle reset force must be set, due to issues with control of low pressures in installation check step. This is necessary in order to avoid overshooting of Installation check hydraulic pressure higher than pressure equivalent of angle sensor reset force. | |
Min bolt tensioning pressure | 1900 | Bar | The min pressure for an OK tensioning result. | The pressure control in the system will set a target higher than the Min bolt tensioning pressure to avoid pressure drop ending in a NOK result. See picture in the chapter Hydraulic Pressure Target Window. | |
Max system hydraulic pressure | 1980 | Bar | The highest pressure the pressure control in the hand controller allows for this configuration. | The actual max pressure is the lowest of the max pressures in the pump and tensioner and the Max system hydraulic pressure of the configuration. | |
Min bolt tensioning force | 698 | kN | Force equivalent of the Min bolt tensioning pressure parameter. | Value manually calculated from bolt pressure. This value is written in the xml report files, but it is not used by the hand controller's software. | |
Lista de verificação da instalação | 20 | Nm | The required torque for an acknowledged installation check. | ||
Installation check torque duration | 1,0 | S | The required time the Installation check torque that must be applied for an acknowledged installation check. | ||
Torque-alvo final | 100 | Nm | The required torque for an acknowledged tightening of the nut. | ||
Resultado de torque de aperto | 1,0 | S | The required torque for an acknowledged tightening of the nut. | ||
Tightening unexpected clockwise rotation detection angle | 5 | Graus | The maximum allowed change of the nut rotation angle in clockwise direction when the process is waiting for pressure release. | To avoid the risk of nut rotation while the system waits for pressure release, activate automatic pressure release (see section Tool Configuration). b | |
Tightening unexpected counter clockwise rotation detection angle | 5 | Graus | The maximum allowed change of the nut rotation angle in counter clockwise direction when the process is waiting for pressure release. | To avoid the risk of nut rotation while the system waits for pressure release, activate automatic pressure release (see section Tool Configuration). c | |
Installation check hydraulic pressure | 20 | Bar | The pressure set point for installation check. | The installation check pressure fixes the tensioner to the flange during the installation check. The installation check pressure, including overshoot, must not exceed the pressure equivalent of Angle sensor reset force. | |
Hydraulic pressure set point factor | 1,025 | 1,025 | The actual set point for the pressure regulation is calculated as follows: Min bolt tensioning pressure timesHydraulic pressure set point factor. See the picture in the section Hydraulic Pressure Target Window. | When pressing and holding the pressurization button, the system is pressurized, the pressure will be held inside a pressure window above Min bolt tensioning pressure. |
Processo de serviço do parafuso
Para garantir os resultados do ângulo de desaperto e de aperto, siga o processo de serviço do parafuso:
Posicione a ferramenta no parafuso.
Pressurize até a Pressão hidráulica de verificação da instalação.
Faça uma verificação da instalação para o serviço do parafuso:
Aplique um torque > 20 Nm no sentido do aperto. O controlador manual assume o ponto de referência do ângulo no sentido do aperto.
Aplique um torque > 20 Nm no sentido do desaperto. O controlador manual assume o ponto de referência do ângulo no sentido do desaperto.
O controlador manual armazena o ângulo do jogo mecânico.
Enquanto mantém a chave e a caixa redutora na posição de desaperto, pressione e mantenha pressionado o botão de pressurização até que a pressão atinja a Pressão mínima de tensionamento do parafuso em bar.
Desaperte a porca até um ângulo maior ou igual ao parâmetro de serviço do parafuso Ângulo mínimo de desaperto do desaperto da porca..
A UI do controlador mostra o ângulo de desaperto como uma medição negativa a partir do ponto de referência do ângulo de desaperto.
Aperte o parafuso conforme o parâmetro Torque-alvo do aperto. O ângulo de aperto é registrado.
Os ângulos de desaperto e de aperto referem-se à rotação real da porca. O controlador manual compensa o jogo mecânico. A GUI do controlador inicializa atualizando o ângulo quando a porca começar a girar, ou seja, desprezando o jogo mecânico. Por isso, o ângulo exibido reflete o movimento da porca, e quando a medição do ângulo for 0, a porca está de volta à posição original.
A rotação delta da porca no sentido do aperto não deve ser maior do que a do parâmetro Rotação máxima delta da porca com um padrão de 13 graus. Na prática, isso significa que a porca não deve girar até um ângulo mais do que 13 graus maior do que o da posição original.
Libere a pressão e armazene o resultado. As seguintes condições devem ser verdadeiras para se obter resultados OK:
O ângulo de desaperto registrado é maior e ou igual ao Ângulo mínimo de desaperto do desaperto da porca.
O ângulo delta registrado após o aperto deve estar no intervalo entre Rotação mínima delta da porca e Rotação máxima delta da porca.
A Rotação mínima delta da porca é igual a D na figura do processo de serviço do parafuso.
1 | Transporte da chave até o alinhamento do aperto |
2 | A rotação da porca começa aqui |
3 | Apertada até a posição original |
A | Ângulo de desaperto |
B | Desaperto de ponto fixo |
C | Folga |
D | Aperto de ponto fixo |
E | Intervalo de aperto permitido após o desaperto estar entre os parâmetros de rotação mínima e máxima delta da porca |
F | Rotação máx. da porca |
Trabalhando com a Aba Configurações
As configurações das ferramentas é feita no menu Configurations (Configurações).
Configuração da ferramenta
Na visualização da Página Inicial, acesse a aba Configurations (Configurações) > Tool Configuration (Configurações da Ferramenta) para configurar as funções disponíveis no sistema.
Insira um nome no campo Name (Nome).
Edite uma configuração clicando no botão Edit (Editar). Veja a tabela abaixo.
Parar criar outra configuração com definições diferentes, clique no ícone Plus (mais) na parte superior da página.
Por exemplo, crie uma configuração com Automatic pressure release (Liberação automática de pressão) = ON (Ativada), ou Pump motor timeout (Tempo limite do motor da bomba) com tempo diferente.Para escolher uma configuração para uso, acessa a Visualização da Página Inicial,, Tensioner Controller (Controlador do Tensionador) > Tool (Ferramenta).
Parâmetro | Valor padrão | Unidade | Descrição | Comentários |
---|---|---|---|---|
Tempo limite do motor da bomba | 30 | s | Temporizador para arrefecimento do motor da bomba, também controlando a válvula de retorno do óleo hidráulico. O motor da bomba para quando o temporizador termina e a válvula de retorno hidráulica fecha. Quando a pressão é liberada, a válvula de retorno do óleo hidráulico é aberta e o motor opera por 6 segundos. O tempo limite do motor da bomba começa e, quando termina, a válvula é fechada e o motor para. | Quando o sistema é usado em condições quentes, o óleo hidráulico pode superaquecer se o motor parar. No caso de tensionadores maiores, o transporte de óleo hidráulico de volta para o recipiente de óleo hidráulico pode precisar de mais do que o tempo mínimo de 6 segundos. |
Liberação automática de pressão | DESLIGADO | Quando a liberação automática de pressão está ON (Ligada), a pressão é automaticamente liberada quando a porca é apertada de acordo com as configurações - o tensionamento fica concluído. | A pressão é liberada quando o torque é relaxado após ser aplicado no torque necessário e pelo tempo necessário. Veja o Diagram of the tensioning process (Diagrama do processo de tensionamento na seção Processo de tensionamento. A configuração recomendada para esse parâmetro é ON (Ligada) pelas razões a seguir:
|
Trabalhando com a aba Controlador do Tensionador
Virtual Station (Estação virtual)
Uma estação virtual é uma abstração do software de um controlador manual. O controlador manual possui um controlador integrado com uma estação virtual conectada. Várias configurações podem ser designadas à estação virtual, conforme a necessidade.
Ferramenta
As informações da ferramenta mostram os dados do tensionador.
Modelo: tamanho do soquete e tipo do tensionador. Uma configuração compatível deve ter os campos Tamanho do parafuso e Tipo de tensionador idênticos à cadeia de caracteres (diferencia maiúsculas e minúsculas) no modelo para ser compatível com o tensionador conectado. Se uma configuração não for exibida em uma HCGUI -> Tarefas -> Serviço de parafuso de montagem, o motivo é provavelmente identificado nessas duas propriedades.
Relação de engrenagem: a relação da caixa redutora no tensionador
Número de série: o número de série do tensionador.
Torque máx.: o torque mais alto que não danifica o sensor de torque.
Versão do software.
Número do produto : o número de artigo do tensionador.
Módulo de Aplicação Inteligente
O Intelligent Application Module (IAM) (Módulo de Aplicação Inteligente (IAM)) é um armazenamento não volátil localizado no controlador manual. O módulo de armazenamento contém todos os programas, configurações e resultados da ferramenta.
Acesse a aba Tensioner Controller (Controlador do Tensionador) no menu da página principal e selecione IAM.
Atribua um Name (Nome) de campo de sequência ao controlador manual.
O Name (Nome) será usado na GUI da Web e na GUI do controlador manual.
Versões do Software
Duas versões do software podem ser instaladas na ferramenta simultaneamente. Instalar a segunda versão do software pode ser útil como preparação quando ao atualizar diversos controladores manuais para ativação sincronizada.

Alterar as versões do software não transfere as configurações da ferramenta ou os programa de tensionamento.
Ativação do Software
O controlador manual pode armazenar duas versões de software instaladas. Usando-se a Ativação de software, é possível escolher qual versão de software utilizar.
Acesse Tensioner Controller (Controlador do Tensionador) no menu da página inicial e selecione Software no painel esquerdo.
Selecione Current (Atual) ou Stored (Armazenado) na janela Software Activation (Ativação de Software).

O controlador manual é reiniciado automaticamente para que a ativação seja efetivada.
Versão Atualizada do Software

Se o pacote de software a ser instalado não for compatível com o hardware do controlador manual, a atualizações do software será cancelada. Será exibida uma mensagem de alerta, indicando quais partes do hardware causaram o cancelamento.
Para informações sobre o atual hardware de ferramenta, acesse Tensioner Controller > Hardware (Controlador do tensionador > Hardware).
Acesse o menu Tens(Controlador do tensionador) e selecione Software no painel esquerdo.
Acesse o campo Software Update (Atualização de software) e selecione BROWSE (NAVEGAR).
Navegue e escolha o arquivo compactado contendo o respectivo software e siga as instruções para finalizar a instalação.
Hardware
A aba Hardware contém informações do Controlador, como designação do modelo e número de série.
É possível realizar uma reinicialização a quente do controlador manual na janela Restart Controller (Reiniciar o controlador). Clique no botão RESTART (REINICIALIZAÇÃO).
Exportação e Importação Configurações
As funções exportar e importar são usadas para exportar eventos e resultados de tensionamento para análise em programas externos, bem como permitir a transferência dos programa de Tensionamento e configurações da ferramenta entre ferramentas.
A função Exportar é usada para:
Exportar resultados e eventos de tensionamento para processamento posterior.
Exportar arquivos de log para auxílio na depuração por parte de um engenheiro de assistência técnica da Atlas Copco.
Exportar configurações da ferramenta que podem ser utilizadas para copiar definições para outra ferramenta.
Acesse Tensioner Controller (Controlador do Tensionador) no menu da página principal. Selecione Export/Import (Exportar/Importar) no painel esquerdo.
Selecione o que exportar da ferramenta.
Todas as informações
Ajustes e configurações
Logs do sistema e informações
Resultados
Ao exportar parâmetros a serem importados em outros controladores, escolha Settings and configurations (Definições e Configurações).
Ao escolher Settings and configurations (Definições e Configurações), nenhum arquivo com resultados ou eventos será exportado para o arquivo. Com esse ajuste, a exportação leva menos tempo para ser realizado.
Selecione EXPORT (EXPORTAR). É exibido uma lembrete para selecionar onde salvar ou recuperar o arquivo exportado.
Acessar Tensioner Controller (Controlador do Tensionador) no menu da página principal. Selecione Export/Import (Exportar/Importar) no painel esquerdo.
Selecione IMPORT (IMPORTAR). Quando usar a função Importar, todos os ajustes para programas e configurações de tensionamento são substituídos pelos ajustes do arquivo de importação. No entanto, os ajustes da rede, PIN, resultados e eventos não são importados.
Selecione CONTINUE (CONTINUAR) na caixa de diálogo para iniciar a importação.
Informações exportadas e formato do arquivo
O arquivo exportado é um arquivamento de arquivo comprimido contendo os seguintes arquivos:
Todas as informações
PFExport_<datetime>_Results.csv
PFExport_<datetime>_Events.csv
ExportInfo.txt
settings/settings.zip
atlas_tool_i.zip
atlas_sys_i.zip
atlas_subsystems_info.zip
atlas_plc.zip
jsonConfigurations.zip:
Ajustes e configurações
ExportInfo.txt
settings/settings.zip
jsonConfigurations.zip:
Arquivo | Descrição |
---|---|
PFExport__<Tool name>_<Time stamp>_Events.csv | Um arquivo separado por ponto e vírgula contendo as seguintes informações:
|
PFExport__<Tool name>_<Time stamp>_Results.csv | Um arquivo separado por ponto e vírgula contendo as seguintes informações:
|
ExportInfo.txt | Informações sobre a instalação da ferramenta e o software da ferramenta. |
settings/settings.zip | Um arquivo binário contendo todos os programas de aperto e definições de lote, as configurações de acessórios e as definições da ferramenta, como: Idioma, Unidades de torque, Data e hora e Aparência do resultado. |
atlas_tool_i.zip | Logs da ferramenta (para depuração) |
atlas_sys_i.zip | Arquivos de log do aplicativo IT. |
atlas_subsystems_info.zip | Informações sobre software de subsistema |
atlas_plc.zip | Configuração do PLC |
jsonConfigurations.zip: | Programas de Aperto e Desaperto de Múltiplas Etapas |
Exportando “Logs do sistema e informações”
Com essa exportação, um técnico de manutenção pode compartilhar os logs de sistema e suas informações com os técnicos da Atlas Copco para facilitar a resolução de problemas.

A exportação de logs de sistema e informações não incluem logs de ferramentas conectadas.
Todos os dados constantes da exportação de log do sistema e informações são armazenados em um arquivo PFExport_<IAM name>_<datetime>.tar.gz, que inclui os seguintes e diretórios:
atlas_sys_i.zip - Arquivos de log do aplicativo de TI
atlas_protocol_log.zip – Arquivos de logo dos adaptadores de protocolos externos
ExportInfo.txt - Documento de texto contendo informações sobre IAM e controlador
licenseInformation.zip – Informações da licença e recursos do sistema
atlas_systeminformation.zip – Informações de P&D da Atlas Copco para a integridade e definição do sistema atual
Exportando “Logs do sistema e informações”
Acesse Tensioner Controller Controlador do tensionador) no menu da página inicial e selecione Export/Import (Exportar/importar) no painel esquerdo.
Na janela Export (Exportar), abra o menu suspenso e selecione System logs and information (Logs do sistema e informações).
Na janela Export (Exportar), selecione EXPORT (EXPORTAR).
Ao final do processo de exportação, uma janela pop-up de exportação confirma que a exportação foi concluída.
Um arquivo PFExport_<IAM name>_<datetime>.tar.gz é automaticamente baixado.
Trabalhando com a Aba Relatórios
Visualizando Resultados
Esta seção descreve como acessar resultados de tensionamentos a partir do controlador manual, e como ler as informações apresentadas em diferentes visualizações de resultados.
Quando o tensionamento é realizado, o resultado é armazenado no controlador manual. Os resultados também podem ser enviados a um sistema externo, como o ToolsNet, ou exportados para análises usando-se a função exportar. Para obter mais informações sobre análises estatísticas, filtragem de resultados e análises de tensionamentos usando o ToolsNet, consulte o Guia do Usuário do ToolsNet 8.
Resultados Armazenados
Cada tarefa é exibida como um único resultado. Um único tensionamento pode exibir resultados em uma tabela com parâmetros importantes.
Visualização de Resultados Armazenados
O controlador manual armazena o resultado de cada aperto ou desaperto realizado.
Vá para Relatórios no menu inicial e selecione Resultados no painel da esquerda.
Selecione Visualizar todos os resultados. A lista de resultados mostrará informações sobre o seguinte:
Data: data e hora do tensionamento realizado.
Programa de Aperto: A coluna Programa de Aperto mostra o nome do Programa de Tensionamento de Múltiplas Etapas.
Força: força medida durante o tensionamento.
Pressão: pressão medida durante o tensionamento.
Resultado: Resultado de Torque/Ângulo
Limites: Intervalo de torque, intervalo de ângulo e intervalo de pressão para um resultado OK. Em resultados NOK o limite de intervalo violado é destacado em um texto em vermelho.
Resultados marcados com uma barra vermelha têm o status de NOK.
Visualizando Eventos
Eventos são utilizados para notificar o suário sobre determinadas alterações ou ocorrências no sistema. Eles são divididos em três tipos; Informação, Advertências e Erros e exigem diferentes tipos de ação.
Os eventos apresentam definições padrões: se devem ser confirmados (ACK.), registrados em log (LOG.) ou exibidos (DISP.). Essas definições podem ser configuradas no menu Settings (Definições) em Events (Eventos).
Acesse Reports (Relatórios) no menu da página principal e selecione Events (Eventos) no painel da esquerda.
Selecione View all events(Visualizar todos os resultados).
Selecione um evento na lista para abrir a caixa de diálogos do evento.
A caixa de diálogo de eventos
A caixa de diálogo de eventos contém informações sobre o evento ocorrido descrevendo o que ocorreu, quando e onde.

Posição | Descrição |
---|---|
1 | Heading (Cabeçalho) - Descreve a que parte do sistema se refere o evento. |
2 | Event name (Nome do evento) - Uma breve texto descritivo do evento. |
3 | Code (Código) - Um número único de quatro dígitos que identifica o evento. |
4 | Module (Módulo) - Descreve a que parte do sistema se refere o evento. |
5 | Type (Tipo) - Information (Informação), Warning (Advertência )ou Error (Erro). |
6 | Time (Data/hora) - Data e hora quando ocorreu o evento. |
Códigos de Evento
Diferentes tipos de eventos são utilizados para notificar o usuário sobre determinadas alterações ou ocorrências no sistema. Cada evento requer uma ação diferente.

Alguns dos procedimentos descritos só podem ser realizados pelo pessoal da Assistência Técnica da Atlas Copco.
Para mais informações sobre um código de evento específico, use os filtros a seguir ou insira os critérios de pesquisa do código de evento na caixa de pesquisa.
Log / Display / Confirmar / Conf. | |||||||
---|---|---|---|---|---|---|---|
none | item | none | none | none | column | list | list |
1000 | Informações | Controlador Iniciado | O controlador é inicializado. | Flex IxB Power Focus 6000 Power Focus 8 StepSync Power Focus XC PFHC | Controlador e Ferramenta | ||
1001 | Alerta | Número de Série do Controlador Atualizado | Gerado na inicialização se o número de série da caixa da placa de TI (número de série do controlador) diferir do número de série da caixa da placa AUX. A placa AUX é considerada não substituível no campo. O controlador reinicializará ao ser atualizado o número de série. | Substituir a placa de TI ou a caixa. | Log Conf. | Power Focus 6000 Power Focus 8 StepSync Power Focus XC | Controlador e Ferramenta |
1010 | Informações | Ferramenta conectada | A ferramenta está conectada. | Registrar Display Conf. | Flex Power Focus 6000 Power Focus 8 StepSync Power Focus XC PFHC | Controlador e Ferramenta | |
1011 | Informações | Ferramenta Desconectada | A ferramenta está desconectada. | Log Display Conf. | Flex Power Focus 6000 Power Focus 8 StepSync Power Focus XC PFHC | Controlador e Ferramenta | |
1012 | Informações | A Ferramenta Rejeitou a Conexão do Controlador | Esse evento pode ocorrer se a ferramenta estiver na zona de salto (“skip-zone”), | Verifique se outro controlador está conectado à ferramenta. As configurações da ferramenta devem estar corretamente configuradas. | Log Display Conf. | Power Focus 6000 Power Focus 8 Power Focus XC | Controlador e Ferramenta |
2000 | Alerta | Bateria fraca | Substituir a bateria. | Log Display Conf. | IxB Power Focus 6000 Power Focus 8 Power Focus XC | Ferramenta | |
2001 | Alerta | Bateria totalmente descarregada | Substituir a bateria. | Log Display Conf. | IxB Power Focus 6000 Power Focus 8 Power Focus XC | Ferramenta | |
2002 | Alerta | Bateria da Ferramenta com Integridade Baixa | Foi detectado problema de integridade da bateria da ferramenta. | Substituir a bateria. | Log Display Conf. | IxB Power Focus 6000 Power Focus 8 Power Focus XC | Ferramenta |
2004 | Alerta | A ferramenta não é do tipo preferido | A ferramenta foi substituída por uma ferramenta com um Torque Máximo de Ferramenta diferente. | Troque a ferramenta. | Conf. | IxB Power Focus 6000 Power Focus 8 Power Focus XC | Ferramenta |
2006 | Alerta | Bateria-reserva da Ferramenta com Integridade Baixa | A bateria-reserva na ferramenta apresenta desempenho fraco demais. | A bateria-reserva deve ser trocada. | Log Display Confirm. Conf. | IxB Power Focus 6000 Power Focus 8 Power Focus XC | Ferramenta |
2007 | Alerta | Falta Bateria-reserva da Ferramenta | Falta uma bateria-reserva da ferramenta. | Inserir uma bateria | Log Display Conf. | IxB Power Focus 6000 Power Focus 8 Power Focus XC | Ferramenta |
2008 | Alerta | Erro na Bateria-reserva da Ferramenta | Detectado um erro na bateria reserva da ferramenta. | Substituir a bateria. | Log Display Conf. | IxB Power Focus 6000 Power Focus 8 Power Focus XC | Ferramenta |
2009 | Alerta | Tensão Baixa na Bateria-reserva | A bateria-reserva do controlador está quase sem carga. | Substituir a bateria. | Log Display Conf. | IxB Power Focus 6000 Power Focus 8 Power Focus XC | Ferramenta |
2010 | Erro | Incompatibilidade da Versão do Software da Ferramenta | As versões de software da ferramenta e do controlador não são compatíveis. | Dar assistência técnica à ferramenta - atualizar software da ferramenta. | Log Display Confirm. Conf. | Flex IxB Power Focus 6000 Power Focus 8 StepSync Power Focus XC | Ferramenta |
2012 | Alerta | Problemas na Comunicação da Ferramenta | Interrupção da comunicação entre a ferramenta e o controlador. | Realocar o posicionamento da antena. | Conf. | Flex Power Focus 6000 Power Focus 8 StepSync Power Focus XC PFHC | Ferramenta |
2013 | Alerta | Posição Ilegal do Anel | Chave de direção de ferramenta na posição incorreta. | Se acontecer com frequência, dê assistência técnica à ferramenta. | Log Display Conf. | Flex Power Focus 6000 Power Focus 8 Power Focus XC | Ferramenta |
2014 | Alerta | Ferramenta superaquecida | Ferramenta superaquecida. | Deixar a ferramenta esfriar. | Log Display Conf. | Flex IxB Power Focus 6000 Power Focus 8 StepSync Power Focus XC | Ferramenta |
2015 | Erro | Erro no Sensor de Temperatura da Ferramenta | Somente para ferramentas SRB, TBP e IxB. | Dê assistência técnica à ferramenta. | Log Display Conf. | Flex IxB Power Focus 6000 Power Focus 8 StepSync Power Focus XC | Ferramenta |
2016 | Alerta | Superaquecimento da Unidade de Pulsos da Ferramenta | Unidade de pulso superaquecida. A ferramenta não está bloqueada, mas o aviso é exibido sempre que a ferramenta for iniciada, desde que a temperatura da unidade de pulso esteja acima do limite. | Deixar a ferramenta esfriar. | Log Display Conf. | Power Focus 6000 Power Focus 8 Power Focus XC | Ferramenta |
2019 | Alerta | Ferramenta não pôde ligar motor | Falha do motor da ferramenta. | Log Display Conf. | IxB Power Focus 6000 Power Focus 8 Power Focus XC | Ferramenta | |
2020 | Alerta | Ferramenta Requer Ajuste do Motor | A ferramenta requer ajuste do motor. | Ajuste o motor. | Log Display Conf. | Flex IxB Power Focus 6000 Power Focus 8 StepSync Power Focus XC | Ferramenta |
2021 | Alerta | Falha de Ajuste do Motor | Falha de ajuste do motor. | Concluir o ajuste do motor ou dê assistência técnica à ferramenta. | Log | Flex IxB Power Focus 6000 Power Focus 8 StepSync Power Focus XC | Ferramenta |
2022 | Informações | Ajuste do Motor Concluído | Ajuste do motor concluído. | Log Conf. | Flex IxB Power Focus 6000 Power Focus 8 StepSync Power Focus XC | Ferramenta | |
2023 | Alerta | A Ferramenta Requer Ajuste da Extremidade Aberta | A ferramenta requer ajuste da extremidade aberta. | Realize o ajuste da extremidade aberta. | Log Display Conf. | IxB Power Focus 6000 Power Focus 8 Power Focus XC | Ferramenta |
2024 | Alerta | Falha de Ajuste da Extremidade Aberta | Falha de ajuste da extremidade aberta. | Tente realizar o ajuste da extremidade aberta mais uma vez. Se falhar de novo, dê assistência técnica à ferramenta. | Log Conf. | IxB Power Focus 6000 Power Focus 8 Power Focus XC | Ferramenta |
2025 | Informações | Ajuste da Extremidade Aberta Bem-sucedido | Ajuste da extremidade aberta bem-sucedido. | Log Conf. | IxB Power Focus 6000 Power Focus 8 Power Focus XC | Ferramenta | |
2026 | Alerta | Falha de Posicionamento da Extremidade Aberta | Falha de posicionamento da extremidade aberta. | Pressione novamente o acionador da ferramenta e aguarde pela finalização do posicionamento. Se falhar de novo, dê assistência técnica à ferramenta. | Log Display Conf. | IxB Power Focus 6000 Power Focus 8 Power Focus XC | Ferramenta |
2027 | Alerta | Uso Limitado por Alta Temperatura da Ferramenta | O limite de temperatura foi atingido. O aperto foi inibido para reduzir o risco da ferramenta parar por causa do superaquecimento. | Espere até a temperatura da ferramenta baixar. | Log Display Conf. | Flex IxB Power Focus 6000 Power Focus 8 StepSync Power Focus XC | Ferramenta |
2030 | Erro | Falha na Memória da Ferramenta: Troque a Ferramenta | Memória da ferramenta corrompida. | Dê assistência técnica à ferramenta. | Log Display Confirm. Conf. | Flex IxB Power Focus 6000 Power Focus 8 StepSync Power Focus XC | Ferramenta |
2031 | Erro | Memória do Acessório da Ferramenta Corrompida | Memória do acessório da ferramenta corrompida. | Dê assistência técnica ao acessório da ferramenta. | Log Display Confirm. Conf. | Flex IxB Power Focus 6000 Power Focus 8 StepSync Power Focus XC | Ferramenta |
2040 | Erro | Falha na Verificação do Sistema | Log Display Confirm. Conf. | Flex IxB Power Focus 6000 Power Focus 8 StepSync Power Focus XC | Ferramenta | ||
2041 | Erro | Erro do Transdutor de Torque | Será gerado, seja por erro de calibração ou se a ferramenta relatar erro do transdutor. | Dê assistência técnica à ferramenta. | Log Display Conf. | Flex IxB Power Focus 6000 Power Focus 8 StepSync Power Focus XC | Ferramenta |
2042 | Erro | Erro do Transdutor de Ângulo | Dê assistência técnica à ferramenta. | Log Display Confirm. Conf. | Flex IxB Power Focus 6000 Power Focus 8 StepSync Power Focus XC | Ferramenta | |
2043 | Erro | Erro de Falta à Terra da Ferramenta | Dê assistência técnica à ferramenta. | Log Display Confirm. Conf. | Flex IxB Power Focus 6000 Power Focus 8 StepSync Power Focus XC | Ferramenta | |
2044 | Informações | Intervalo de Assistência Técnica da Ferramenta Expirou | Indica que a manutenção da ferramenta precisa ser realizada. Acionado quando o número de apertos definido for excedido. | Dê assistência técnica à ferramenta. | Log Display Conf. | Flex IxB Power Focus 6000 Power Focus 8 StepSync Power Focus XC | Ferramenta |
2045 | Alerta | Dados de Calibração da Ferramenta Inválidos | Caso a validação dos dados de calibragem falhe. | Dê assistência técnica à ferramenta. | Log Display Conf. | Flex IxB Power Focus 6000 Power Focus 8 StepSync Power Focus XC | Ferramenta |
2046 | Informações | Ferramenta: Próxima Data de Calibração Passou | Indica que a calibragem da ferramenta precisa ser feita. Acionada quando o alarme de calibragem é habilitado nas configurações e o tempo atual é maior do que a próxima data de calibração. | Dê assistência técnica à ferramenta. | Log Display Conf. | Flex IxB Power Focus 6000 Power Focus 8 StepSync Power Focus XC | Ferramenta |
2048 | Informações | Valor de calibração da ferramenta atualizado pelo dispositivo de GQ | A calibração da ferramenta foi atualizada quando foi realizada uma calibração com um dispositivo de GQ. | Log Display Conf. | IxB Power Focus 6000 Power Focus 8 Power Focus XC | Ferramenta | |
2050 | Erro | Arquivo de Parâmetros da Ferramenta Incompatível | Os parâmetros necessários da ferramenta estão ausentes. | Atualizar os parâmetros da ferramenta. | Log Display Conf. | Flex IxB Power Focus 6000 Power Focus 8 StepSync Power Focus XC | Ferramenta |
2060 | Informações | Comportamento Inesperado do Acionador | Usado para prevenir o início automático da ferramenta se um acessório estiver conectado. | Log Display Conf. | IxB Power Focus 6000 Power Focus 8 StepSync Power Focus XC | Ferramenta | |
2071 | Erro | Memória da Ferramenta Corrompida | O descritor da ferramenta está corrompido. | Dê assistência técnica à ferramenta. | Log Display Conf. | Flex Power Focus 6000 Power Focus 8 StepSync Power Focus XC | Ferramenta |
2072 | Informações | Dispositivo Desconhecido Conectado | Log Display Conf. | Flex IxB Power Focus 6000 Power Focus 8 StepSync Power Focus XC | Ferramenta | ||
2073 | Alerta | Falha da Supervisão do Acionador da Ferramenta | Falha do canal do HW. Incompatibilidade entre o hardware e o software do acionador da ferramenta. | Log Display Conf. | IxB Power Focus 6000 Power Focus 8 Power Focus XC | Ferramenta | |
2074 | Alerta | Falha da Placa de Luzes de Sinalização da Ferramenta | Falha da placa de luses de sinalização da ferramenta. | Dê assistência técnica à ferramenta. | Log Display Conf. | Flex IxB Power Focus 6000 Power Focus 8 StepSync Power Focus XC | Ferramenta |
2075 | Alerta | Falha de Tensão do Ventilador da Ferramenta | Falha de tensão do ventilador da ferramenta. | Dê assistência técnica à ferramenta. | Log Display Conf. | Power Focus 6000 Power Focus 8 StepSync Power Focus XC | Ferramenta |
2076 | Alerta | Falha de Tensão do Barramento Auxiliar da Ferramenta | Falha de tensão do barramento auxiliar da ferramenta. | Dê assistência técnica à ferramenta. | Log Display Conf. | Flex IxB Power Focus 6000 Power Focus 8 StepSync Power Focus XC | Ferramenta |
2077 | Alerta | Erro do Sensor do Acionador da Ferramenta | Erro do sensor do acionador da ferramenta. | Dê assistência técnica à ferramenta. | Log Display Conf. | IxB Power Focus 6000 Power Focus 8 StepSync Power Focus XC | Ferramenta |
2078 | Informações | Atualização do Programa de Aperto da Ferramenta | Ferramenta bloqueada devido à atualização do programa de aperto. | Log Display Conf. | IxB Power Focus 6000 Power Focus 8 Power Focus XC | Ferramenta | |
2079 | Erro | Cabo da Ferramenta Incompatível | O cabo da ferramenta está corrompido. O chip no cabo não responde ou está danificado. | Troque o cabo. | Log Display Conf. | Flex Power Focus 6000 Power Focus 8 StepSync Power Focus XC | Ferramenta |
2080 | Erro | Falha na Bateria da Ferramenta | Tensão CC alta demais ou baixa demais. Falha da bateria. | Entre em contato com o representante de assistência técnica da Atlas Copco e envie a bateria de volta à Atlas Copco (não a reutilize). | Log Display Conf. | IxB Power Focus 6000 Power Focus 8 Power Focus XC | Ferramenta |
2081 | Erro | Limite de Corrente da Ferramenta Atingido | O limite de corrente foi atingido e a unidade é desativada. | Dê assistência técnica à ferramenta. | Log Display Conf. | IxB Power Focus 6000 Power Focus 8 Power Focus XC | Ferramenta |
2082 | Erro | Erro na Medição da Corrente da Ferramenta | Erro de medição de corrente. A medição da corrente não fornece um resultado confiável. | Dê assistência técnica à ferramenta. | Log Display Conf. | IxB Power Focus 6000 Power Focus 8 Power Focus XC | Ferramenta |
2083 | Erro | Erro Interno da Ferramenta | Vários erros internos de hardware. | Dê assistência técnica à ferramenta. | Log Display Conf. | IxB Power Focus 6000 Power Focus 8 Power Focus XC | Ferramenta |
2084 | Erro | Erro Interno de Software da Ferramenta | Erro interno de software da ferramenta. | Dê assistência técnica à ferramenta. | Log Display Conf. | IxB Power Focus 6000 Power Focus 8 Power Focus XC | Ferramenta |
2085 | Erro | Erro da RBU da Ferramenta | Um erro RBU foi detectado pelo software da ferramenta. | Confirme se a RBU está corretamente instalada. Se o erro ainda persistir, dê assistência técnica à ferramenta. | Log Display Conf. | IxB Power Focus 6000 Power Focus 8 Power Focus XC | Ferramenta |
2086 | Erro | Bloqueio de Ferramenta | O motor da ferramenta está travado. | Dê assistência técnica à ferramenta. | Log Display Conf. | IxB Power Focus 6000 Power Focus 8 Power Focus XC | Ferramenta |
2087 | Alerta | Corrente Alta no Motor da Ferramenta | O valor-limite da corrente do motor da ferramenta foi excedido e a ferramenta está bloqueada. A ferramenta entrará no modo À prova de falhas. | Log Display Conf. | IxB Power Focus 6000 Power Focus 8 Power Focus XC | Ferramenta | |
2088 | Alerta | Corrente Alta na Bateria da Ferramenta | A corrente da bateria da ferramenta está alta demais. | Log Display Conf. | IxB Power Focus 6000 Power Focus 8 Power Focus XC | Ferramenta | |
2089 | Alerta | Tensão Baixa no Acionamento da Ferramenta | A tensão no acionamento da ferramenta está abaixo do limite inferior de tensão monitorado. | Log Display Conf. | IxB Power Focus 6000 Power Focus 8 Power Focus XC | Ferramenta | |
2090 | Alerta | Tensão Alta no Acionamento da Ferramenta | A tensão no acionamento da ferramenta está acima do limite superior de tensão monitorado. | Log Display Conf. | IxB Power Focus 6000 Power Focus 8 Power Focus XC | Ferramenta | |
2091 | Alerta | Erro na Placa-mãe da Ferramenta | Erro na placa-mãe da ferramenta. | Log Display Conf. | IxB Power Focus 6000 Power Focus 8 Power Focus XC | Ferramenta | |
2092 | Alerta | Erro no Módulo de Alimentação da Ferramenta | Erro no módulo de alimentação da ferramenta. | Log Display Conf. | IxB Power Focus 6000 Power Focus 8 Power Focus XC | Ferramenta | |
2093 | Alerta | Nível de Óleo Baixo da Unidade de Pulso | O nível de óleo da ferramenta de pulso conectada está baixo. | Dê assistência técnica à ferramenta. | Log Display Conf. | Power Focus 6000 Power Focus 8 Power Focus XC | Ferramenta |
2094 | Alerta | Nível de Óleo da Unidade de Pulso Vazio | O nível de óleo da ferramenta de pulso conectada está abaixo do nível operacional necessário. | Dê assistência técnica à ferramenta. | Log Display Confirm. Conf. | Power Focus 6000 Power Focus 8 Power Focus XC | Ferramenta |
2095 | Alerta | Perda de Comunicação da Bateria da Ferramenta | A ferramenta perdeu a comunicação com a bateria. | Confirme se a bateria está corretamente encaixada. Ou troque a bateria. | Log Display Conf. | IxB Power Focus 6000 Power Focus 8 Power Focus XC | Ferramenta |
2096 | Erro | Versão do Software da Bateria da Ferramenta Incompatível | O software da bateria da ferramenta é incompatível com o software da ferramenta. | Atualizar o software. | Log Display Conf. | IxB Power Focus 6000 Power Focus 8 Power Focus XC | Ferramenta |
2100 | Informações | smartHead da STwrench Removida | A smartHead da STwrench foi removida. | Reconecte a smartHead e reinicie a chave. | Log Display Conf. | IxB Power Focus 6000 Power Focus 8 Power Focus XC | Ferramenta |
2101 | Alerta | Aperto da Chave Quando Bloqueada | Foi realizado um aperto de torquímetro quando o status da ferramenta era de bloqueada no controlador. | Espere até o status da ferramenta no controlador indicar desbloqueada | Log Display Conf. | Power Focus 6000 Power Focus 8 | Ferramenta |
2120 | Alerta | Não Foi Possível Iniciar: Ferramenta Sem Transdutor de Torque Ativo | Log Display | Flex | Ferramenta | ||
2121 | Alerta | Transdutores Desativados para a Ferramenta Conectada | Log Display | Flex | Ferramenta | ||
2122 | Alerta | Não Foi Possível Iniciar: Ferramenta Sem o Transdutor de Torque Necessário | Log Display | Flex IxB | Ferramenta | ||
2123 | Alerta | Não Foi Possível Iniciar: Ferramenta Sem o Transdutor de Ângulo Necessário | Log Display | Flex | Ferramenta | ||
2124 | Erro | Erro de Transdutor de Torque no Transdutor Principal | Indica que há um erro no Transdutor de torque principal de uma Ferramenta com transdutores de elemento duplo. | Log Display | Flex | Ferramenta | |
2125 | Erro | Erro de Transdutor de Torque no Transdutor Secundário | Indica que há um erro no Transdutor de torque secundário de uma Ferramenta com transdutores de elemento duplo. | Log Display | Flex | Ferramenta | |
2126 | Erro | Transdutor de Torque da Ferramenta - Erro de Calibração no Transdutor Principal | Log Display | Flex | Ferramenta | ||
2127 | Erro | Transdutor de Torque da Ferramenta - Erro de Calibração | Log Display | Flex StepSync | Ferramenta | ||
2128 | Erro | Transdutor de Torque da Ferramenta: Falha no Teste da Resistência de Derivação do Transdutor Principal | Log Display | Flex | Ferramenta | ||
2129 | Erro | Transdutor de Torque da Ferramenta: Falha no Teste da Resistência de Derivação | Log Display | Flex StepSync | Ferramenta | ||
2130 | Erro | Transdutor de Torque da Ferramenta: Falha na Compensação de Zero no Transdutor Principal | Log Display | Flex | Ferramenta | ||
2131 | Erro | Transdutor de Torque da Ferramenta: Falha na Compensação de Zero | Log Display | Flex StepSync | Ferramenta | ||
2132 | Erro | Hardware do Transdutor de Torque da Ferramenta - Erro no Transdutor Principal | Log Display | Flex | Ferramenta | ||
2133 | Erro | Transdutor de Torque da Ferramenta - Erro de Hardware | Log Display | Flex StepSync | Ferramenta | ||
2134 | Erro | Erro no Transdutor de Torque da Ferramenta: Estouro no Conversor A/D no Transdutor Principal | Log Display | Flex | Ferramenta | ||
2135 | Erro | Erro no Transdutor de Torque da Ferramenta: Estouro no Conversor A/D | Log Display | Flex StepSync | Ferramenta | ||
2136 | Erro | Transdutor de Torque da Ferramenta - Erro de Calibração no Transdutor Secundário | Log Display | Flex | Ferramenta | ||
2137 | Erro | Erro no Transdutor de Torque da Ferramenta: Falha no Teste da Resistência de Derivação no Transdutor Secundário | Log Display | Flex | Ferramenta | ||
2138 | Erro | Erro no Transdutor de Torque da Ferramenta: Falha na Compensação de Zero no Transdutor Secundário | Log Display | Flex | Ferramenta | ||
2139 | Erro | Transdutor de Torque da Ferramenta - Erro de Hardware no Transdutor Secundário | Log Display | Flex | Ferramenta | ||
2140 | Erro | Erro no Transdutor de Torque da Ferramenta: Estouro no Conversor A/D no Transdutor Secundário | Log Display | Flex | Ferramenta | ||
2202 | Erro | Ocorreu sobrecorrente na IHM da ferramenta | Sobrecorrente na IHM da ferramenta detectada. | Dê assistência técnica à ferramenta. Substituir a IHM da ferramenta. | Log Display Confirm. Conf. | IxB | Ferramenta |
2203 | Erro | Ocorreu sobrecorrente na luz frontal da ferramenta | Sobrecorrente na luz frontal da ferramenta detectada | Dê assistência técnica à ferramenta. Substituir a luz frontal da ferramenta. | Log Display Confirm. Conf. | IxB | Ferramenta |
2204 | Erro | Ocorreu sobrecorrente no barramento do acessório | Sobrecorrente no barramento do acessório detectada. | Dê assistência técnica à ferramenta. Substituir barramento do acessório. | Log Display Confirm. Conf. | IxB | Ferramenta |
2207 | Erro | Ocorreu sobrecorrente no vibrador | Sobrecorrente no vibrador detectada. | Dê assistência técnica à ferramenta. Substituir o vibrador. | Log Display Confirm. Conf. | IxB | Ferramenta |
2208 | Alerta | Temperatura alta na CPU do sistema | Temperatura alta na CPU do sistema. | Espere até a temperatura da ferramenta baixar. | Log Display Conf. | IxB | Ferramenta |
2209 | Erro | Temperatura crítica na CPU do sistema | Temperatura crítica na CPU do sistema. | Espere até a temperatura da ferramenta baixar. | Log Display Conf. | IxB | Ferramenta |
2210 | Erro | Fonte de alimentação incompatível: aperto não permitido | Bateria com tensão baixa demais acoplada à ferramenta. | Acoplar bateria com tensão mais alta à ferramenta. | Log Display Confirm. Conf. | IxB | Ferramenta |
2500 | Erro | Número máx. da barra extratora do tensionador | A barra extratora do tensionador deve ser trocada. Sistema bloqueado para utilização. A pressão só pode ser liberada. | Envie o tensionador à organização de assistência técnica para a troca da barra extratora. | Log Display Confirm. | PFHC | Ferramenta |
2501 | Erro | Alarme da proteção do motor da bomba | A proteção do motor da bomba parou o motor. O sistema deve parar. Se o sistema estiver sob pressão, é necessário ações manuais para liberar a pressão. | Desligue o sistema. Se estiver sob pressão, libere mecanicamente a pressão e envie a bomba para a assistência técnica. | Log Display Confirm. | PFHC | Ferramenta |
2502 | Erro | Alarme de nível de óleo baixo no motor da bomba | O nível do óleo do motor da bomba está baixo, por isso o motor parou. Se o sistema estiver sob pressão, é necessário ações manuais para liberar a pressão. | Desligue o sistema. Se estiver sob pressão, libere mecanicamente a pressão e complete o óleo. | Log Display Confirm. | PFHC | Ferramenta |
2503 | Erro | Alarme de temperatura alta do óleo do motor da bomba | A temperatura do óleo do motor da bomba está alta. | Desligue o sistema e espere o óleo esfriar. | Log Display Confirm. | PFHC | Ferramenta |
2504 | Erro | Alarme do sensor de pressão do tensionador | Falha no dispositivo eletrônico do sensor de pressão do tensionador. Nenhuma pressão pode ser lida nem relatada ao sistema; | Desligue o sistema. Se estiver sob pressão, libere mecanicamente a pressão e envie o tensionador para a assistência técnica. | Log Display Confirm. | PFHC | Ferramenta |
2505 | Erro | Alarme do sensor de pressão da bomba | Falha no dispositivo eletrônico do sensor de pressão da bomba. Nenhuma pressão pode ser lida nem relatada ao sistema; | Desligue o sistema. Se estiver sob pressão, libere mecanicamente a pressão e envie a bomba para a assistência técnica. | Log Display Confirm. | PFHC | Ferramenta |
2506 | Erro | Rotação inesperada no sentido horário detectada | Rotação da porca no sentido horário ao aguardar pela liberação de pressão após concluído o tensionamento. O resultado é invalidado. | Libere a pressão e a tensione a porca novamente. | Log Display Conf. | PFHC | Ferramenta |
2507 | Erro | Rotação inesperada no sentido anti-horário detectada | Rotação da porca no sentido anti-horário ao aguardar pela liberação de pressão após concluído o tensionamento. O resultado é invalidado. | Libere a pressão e a tensione a porca novamente. | Log Display Conf. | PFHC | Ferramenta |
2508 | Erro | Falha no sensor de pressão da bomba ou do tensionador | Diferença de pressão grande demais entre as leituras do sensor de pressão na bomba e no tensionador. A pressurização é parada. | Problema no sistema hidráulico ou na calibração dos sensores de pressão. Reinicie o sistema e tente novamente. Se o problema se repetir, entre em contato com o seu representante local da Atlas Copco. | Log Display Confirm. | PFHC | Ferramenta |
2509 | Erro | Falha no sensor de pressão do tensionador ou falha na mangueira hidráulica. | O sensor de pressão do tensionador indica que não há pressão, mas o sensor da bomba mostra um aumento de pressão. A pressurização é parada. | Problema no sistema hidráulico ou na calibração dos sensores de pressão. Reinicie o sistema e tente novamente. Se o problema se repetir, entre em contato com o seu representante local da Atlas Copco. | Log Display Confirm. | PFHC | Ferramenta |
2510 | Erro | Falha em Definir ID personalizada | Falha na definição da ID personalizada. | Reinicie o sistema e verifique os dispositivos conectados. Se a ID Personalizada da unidade estiver errada, refaça a definição. | Log Display Confirm. | PFHC | Ferramenta |
2511 | Informações | A ID personalizada está definida. | Definição da ID personalizada bem-sucedida. | Log Display Confirm. | PFHC | Ferramenta | |
2512 | Alerta | Cadeia de caracteres do Código de barras malformada, ignorado | A cadeia de caracteres não pôde ser analisada como um código de barras de dados da torre. | Leia um código QR de dados da torre adequado ou leia a ID da seção da torre. | Log Display Confirm. | PFHC | Ferramenta |
2513 | Erro | Nenhuma pressão detectada na bomba | O sistema está tentando pressurizar, mas não é registrado aumento de pressão na bomba. A possível causa é a ordem incorreta da fase no conector trifásico. | Desligue o sistema e inverta as fases do conector de alimentação. | Log Display Confirm. | PFHC | Ferramenta |
2514 | Alerta | Alarme de sobretorque do tensionador | É aplicado um torque alto demais no torquímetro de estalo. Isso causa danos ao sensor de torque. | Relaxe o torque. | Log | PFHC | Ferramenta |
2515 | Alerta | Alarme de sobretorque do tensionador | A pressão no tensionador está alta demais. | Deixe a pressão cair ou libere a pressão. Verifique os parâmetros da pressão hidráulica. | Log | PFHC | Ferramenta |
2516 | Alerta | Firmware inesperado da Bomba ou do Tensionador | Versão do firmware inesperada da Bomba ou do Tensionador detectada. Se o problema persistir, pode ser possível executar o sistema, mas observe com atenção qualquer comportamento inesperado. | Sistema do ciclo de alimentação | Log Display Confirm. | PFHC | Ferramenta |
2517 | Erro | Versão do firmware incompatível da Bomba ou do Tensionador, reinicie o sistema.. Não é possível executar o sistema. | Versão do firmware incompatível da Bomba ou do Tensionador, reinicie o sistema. Não é possível executar o sistema. | Reinicie o sistema. Se isso não ajudar, troque a unidade que falhou. Verifique os dispositivos conectados para identificar qual deles não se conectou. | Log Display Confirm. | PFHC | Ferramenta |
3000 | Erro | Erro Interno no Software do Controlador | Erro de software no controlador. | Entre em contato com a assistência técnica. | Log Display Confirm. Conf. | IxB Power Focus 6000 Power Focus 8 Power Focus XC | Controlador, Unidade e StepSync |
3001 | Erro | Relógio do Controlador - Bateria Totalmente Descarregada | A bateria interna está se aproximando do final da vida útil. | Substituir a bateria. | Log Display Confirm. Conf. | Flex Power Focus 6000 Power Focus 8 StepSync Power Focus XC | Controlador, Unidade e StepSync |
3010 | Alerta | Superaquecimento do Sistema | O controlador está superaquecido. | Esfriar. | Log Display Conf. | Power Focus 6000 Power Focus 8 Power Focus XC | Controlador, Unidade e StepSync |
3011 | Alerta | Unidade Superaquecida - Hardware do Controlador | Esfriar. | Log Display Conf. | Flex | Controlador, Unidade e StepSync | |
3013 | Alerta | Uso Limitado por Alta Temperatura do Controlador | O limite de temperatura foi atingido. O aperto foi inibido para reduzir o risco do controlador parar por causa do superaquecimento. | Espere até a temperatura do controlador baixar. | Log Display Conf. | Power Focus 6000 Power Focus 8 StepSync Power Focus XC | Controlador, Unidade e StepSync |
3020 | Alerta | Falha no Hardware do Controlador | Log Display Conf. | Flex IxB Power Focus 6000 Power Focus 8 StepSync Power Focus XC | Controlador, Unidade e StepSync | ||
3021 | Alerta | Problema na Tensão do Sistema | Tensão CC alta demais ou baixa demais. | Log Display Conf. | Flex IxB Power Focus 6000 Power Focus 8 StepSync Power Focus XC | Controlador, Unidade e StepSync | |
3022 | Alerta | Problema na Tensão do Controlador: Tensão da Entrada CA Alta Demais | Tensão CC alta demais ou baixa demais. | Corrija a tensão de entrada. | Log Display | Power Focus 6000 Power Focus 8 StepSync Power Focus XC | Controlador, Unidade e StepSync |
3023 | Alerta | Problema na Tensão do Controlador: Tensão da Entrada CA Baixa Demais | Tensão CC alta demais ou baixa demais. | Corrija a tensão de entrada. | Log Display | Power Focus 6000 Power Focus 8 StepSync Power Focus XC | Controlador, Unidade e StepSync |
3024 | Alerta | Problema na Tensão da Unidade: Tensão da Entrada CA Alta Demais | Tensão CC alta demais ou baixa demais. | Corrija a tensão de entrada. | Log Display | Flex | Controlador, Unidade e StepSync |
3025 | Alerta | Problema na Tensão da Unidade: Tensão da Entrada CA Baixa Demais | Tensão CC alta demais ou baixa demais. | Corrija a tensão de entrada. | Log Display | Flex | Controlador, Unidade e StepSync |
3030 | Erro | Endereço IP em Conflito com outro Nó na Rede | O endereço IP definido está em uso por outro dispositivo na mesma rede. | Altere o endereço IP em um dos dispositivos. | Log Display Conf. | Flex Power Focus 6000 Power Focus 8 StepSync Power Focus XC PFHC | Controlador, Unidade e StepSync |
3031 | Informações | Cabo de Rede Desconectado | O sinal portador da porta de fábrica foi perdido (cabo desconectado). | Confira a conexão do cabo. | Log Display Conf. | Flex Power Focus 6000 Power Focus 8 StepSync Power Focus XC | Controlador, Unidade e StepSync |
3032 | Informações | Emparelhamento Iniciado | Iniciado o emparelhamento da ferramenta. | Log Display Conf. | Power Focus 6000 Power Focus 8 Power Focus XC | Controlador, Unidade e StepSync | |
3033 | Informações | Emparelhamento Bem-sucedido | O emparelhamento da ferramenta foi bem-sucedido. | Log Display Conf. | Power Focus 6000 Power Focus 8 Power Focus XC | Controlador, Unidade e StepSync | |
3034 | Informações | Emparelhamento Malsucedido: Nenhuma Ferramenta Encontrada | O controlador não encontrou uma ferramenta para emparelhar no escaneamento por pares de rádio. | Defina a ferramenta em modo de emparelhamento e tente de novo. | Log Display Conf. | Power Focus 6000 Power Focus 8 Power Focus XC | Controlador, Unidade e StepSync |
3035 | Erro | Emparelhamento Malsucedido: Mais de uma Ferramenta Encontrada | O controlador encontrou mais de uma ferramenta no escaneamento por pares de rádio. | Confira se somente uma única ferramenta está no modo de emparelhamento ao iniciar o modo de emparelhamento no controlador. | Log Display Conf. | Power Focus 6000 Power Focus 8 Power Focus XC | Controlador, Unidade e StepSync |
3036 | Erro | Emparelhamento Malsucedido: Erro de Comunicação | O controlador apresentou uma perda de comunicação, uma resposta inesperada ou tempo esgotado durante o processo de emparelhamento. | Tente realizar o emparelhamento mais uma vez. Se falhar de novo, dê assistência técnica à ferramenta. | Log Display Conf. | Power Focus 6000 Power Focus 8 Power Focus XC | Controlador, Unidade e StepSync |
3037 | Informações | Emparelhamento Malsucedido: Abertura da Ferramenta Completa | Libere uma das aberturas da ferramenta. | Log Display Conf. | Power Focus 6000 Power Focus 8 Power Focus XC | Controlador, Unidade e StepSync | |
3040 | Alerta | Parada de Emergência | Unidade desativada em decorrência da parada de emergência. | Reinicializar a parada de emergência. | Log Display Conf. | Flex Power Focus 6000 Power Focus 8 StepSync Power Focus XC | Controlador, Unidade e StepSync |
3050 | Informações | Relógio do Sistema Atualizado | O relógio do sistema foi atualizado. | Log Conf. | Flex IxB Power Focus 6000 Power Focus 8 StepSync Power Focus XC PFHC | Controlador, Unidade e StepSync | |
3051 | Erro | Erro de Relógio do Sistema | Leitura errada do horário no hardware do Relógio em Tempo Real (RTC) | Troque a bateria do RTC. | Log Display Confirm. Conf. | Flex IxB Power Focus 6000 Power Focus 8 StepSync Power Focus XC PFHC | Controlador, Unidade e StepSync |
3052 | Alerta | Erro de Configuração da Inicialização Remota | Incompatibilidade entre a configuração de inicialização remota do hardware e do software. | Confira se a chave DIP do hardware é compatível com a fonte da inicialização selecionada. | Log Display Conf. | Power Focus 6000 Power Focus 8 StepSync Power Focus XC | Controlador, Unidade e StepSync |
3053 | Informações | Unidade Conectada | A unidade StepSync foi conectada. | Log Display | Flex Power Focus 6000 Power Focus 8 StepSync Power Focus XC | Controlador, Unidade e StepSync | |
3054 | Informações | Unidade Desconectada | Unidade do StepSync desconectada. | Log Display | Flex Power Focus 6000 Power Focus 8 StepSync Power Focus XC | Controlador, Unidade e StepSync | |
3055 | Alerta | Erro na Configuração do Modo | Gerado quando o modo selecionado é configurado da maneira errada. Por exemplo, configurar dois parafusos com o mesmo número de parafuso ou o mesmo canal, ou uma configuração de modo incompleta. | Confira se há erro de configuração de modo no ToolsTalk 2. | Log Display | Flex StepSync | Controlador, Unidade e StepSync |
3056 | Alerta | Não Foi Possível Iniciar: Não Há Ferramenta ou Unidade | Gerado quando um canal utilizado não dispõe de uma unidade ou ferramenta. | Verifique o Menu Canal na IHM. Conecte a unidade ou ferramenta que falta. | Log Display | Flex StepSync | Controlador, Unidade e StepSync |
3057 | Informações | Não Foi Possível Iniciar: Canal já em Uso | Gerado quando um canal necessário for alocado a outra estação virtual. | Log Display | Flex | Controlador, Unidade e StepSync | |
3058 | Informações | Nenhum Modo Selecionado | Selecionar o modo. | Log Display | Flex StepSync | Controlador, Unidade e StepSync | |
3059 | Alerta | Falha na Conexão com o Gerenciador de Licenças da Atlas Copco | Indica que o controlador falhou em conectar-se com o gerenciador de licenças local para obter licenças. | Verifique a Rede Local. Se falhar de novo, envie o controlador para a assistência técnica. | Log Display Conf. | IxB Power Focus 6000 Power Focus 8 StepSync Power Focus XC | Controlador, Unidade e StepSync |
3061 | Alerta | Não Foi Possível Iniciar: Habilitar Sinal Está Baixo | Log Display | Flex StepSync | Controlador, Unidade e StepSync | ||
3062 | Alerta | Não Foi Possível Iniciar: Sinal de Parada Alto | Log Display | Flex StepSync | Controlador, Unidade e StepSync | ||
3063 | Alerta | Não Foi Possível Iniciar: Todos os Canais Inibidos | Todos os canais foram definidos como inibidos, assim, nenhum aperto pode ser iniciado. | Defina pelo menos um único canal como não inibido. | Log Display | Flex StepSync | Controlador, Unidade e StepSync |
3064 | Alerta | Defeito no Número do Carrier | A chave hexadecimal do FlexCarrier está definida em zero. | Gire a chave para um valor diferente de zero. | Log Display | Flex | Controlador, Unidade e StepSync |
3065 | Alerta | Plugue de Configuração da Parada de Emergência (E-stop) do Carrier do Tipo Errado ou Inexistente | Um Carrier sem o seu plugue de configuração da parada de emergência (E-stop), ou o tipo do plugue está errado. | Insira um plugue do tipo correto. | Log Display | Flex | Controlador, Unidade e StepSync |
3066 | Alerta | Entrada de Tensão do Carrier: Sem CA Trifásica | Log Display | Flex | Controlador, Unidade e StepSync | ||
3067 | Alerta | Entrada de Tensão do Carrier: Sem uma das Fases CA | Log Display | Flex | Controlador, Unidade e StepSync | ||
3068 | Alerta | Carrier: Unidade de Fonte de Alimentação Interna de 24 VCC Quebrada | Log Display | Flex | Controlador, Unidade e StepSync | ||
3069 | Alerta | Porta OUT de 24 V do Carrier Desativada por Sobrecorrente | Restaurar o sistema. | Log Display | Flex | Controlador, Unidade e StepSync | |
3070 | Alerta | Carrier; Erro de Hardware na Saída do Cabo FlexControl do PF6 | Restaurar o sistema. | Log Display | Flex | Controlador, Unidade e StepSync | |
3071 | Alerta | Carrier; Erro de Hardware na Entrada do Cabo FlexControl do PF6) | Restaurar o sistema. | Log Display | Flex | Controlador, Unidade e StepSync | |
3072 | Alerta | Falta de Energia de 24 VCC na Parada de Emergência por Curto-circuito | Log Display | Flex | Controlador, Unidade e StepSync | ||
3073 | Alerta | Não Foi Possível Iniciar: Sistema Parado pela Parada de Emergência | Ao alocar diversos eixos, este evento foi invocado por “preStartCheckFailed” devido à parada de emergência. | Restaurar a parada de emergência. | Log Display | Flex StepSync | Controlador, Unidade e StepSync |
3074 | Alerta | Carrier Superaquecido | Log Display | Flex | Controlador, Unidade e StepSync | ||
3075 | Alerta | Temperatura do Carrier OK | Log Display | Flex | Controlador, Unidade e StepSync | ||
3076 | Alerta | Carrier: Sobrecarga na Fonte de Alimentação Interna de 24 VCC) | Saída de corrente da PSU interna está alta demais. | Desconecte outros Carriers alimentados pela PSU. Desconecte qualquer equipamento externo usando 24 VCC. | Log Display | Flex | Controlador, Unidade e StepSync |
3077 | Alerta | Carrier: Sobretensão na Fonte de Alimentação Interna de 24 VCC | Saída de tensão da PSU interna está alta demais. | Trocar o Carrier. | Log Display | Flex | Controlador, Unidade e StepSync |
3078 | Alerta | Carrier: Subtensão na Fonte de Alimentação Interna de 24 VCC | Saída de tensão da PSU interna está baixa demais. | Trocar o Carrier. | Log Display | Flex | Controlador, Unidade e StepSync |
3079 | Alerta | Alimentação Externa ao Carrier: Sobretensão de 24 VCC | A tensão de entrada auxiliar é maior do que 27 VCC. | Ajustar a tensão de entrada auxiliar. | Log Display | Flex | Controlador, Unidade e StepSync |
3080 | Alerta | Alimentação Externa ao Carrier: Subtensão de 24 VCC | A tensão de entrada auxiliar é menor do que 19 VCC. | Ajustar a tensão de entrada auxiliar. | Log Display | Flex | Controlador, Unidade e StepSync |
3081 | Alerta | Entrada de Tensão do Carrier: Sobretensão da CA Trifásica | A tensão de entrada está alta demais. | Tensão de entrada mais baixa: deve ser de 400 VCA ou 480 VCA. | Log Display | Flex | Controlador, Unidade e StepSync |
3082 | Alerta | Entrada de Tensão do Carrier: Subtensão da CA Trifásica | A tensão de entrada está baixa demais. | Tensão de entrada mais alta: deve ser de 400 VCA ou 480 VCA. | Log Display | Flex | Controlador, Unidade e StepSync |
3083 | Erro | Firmware do Módulo Anybus/Profisafe Incorreto | Log Display | Flex Power Focus 6000 Power Focus 8 StepSync | Controlador, Unidade e StepSync | ||
3084 | Erro | Erro de Tempo de Execução do Soft PLC | eCLR encerrado de maneira descontrolada. | Log Display Conf. | Flex Power Focus 6000 Power Focus 8 StepSync | Controlador, Unidade e StepSync | |
3085 | Alerta | Carrier: Módulo do Ventilador Avariado | Log Display | Flex | Controlador, Unidade e StepSync | ||
3086 | Alerta | Carrier: Módulo do Ventilador Parcialmente Avariado | Log Display | Flex | Controlador, Unidade e StepSync | ||
3087 | Alerta | Carrier: Módulo do Ventilador Esquerdo Avariado | Log Display | Flex | Controlador, Unidade e StepSync | ||
3088 | Alerta | Carrier: Módulo do Ventilador Esquerdo Parcialmente Avariado | Log Display | Flex | Controlador, Unidade e StepSync | ||
3089 | Alerta | Carrier: Módulo do Ventilador Direito Avariado | Log Display | Flex | Controlador, Unidade e StepSync | ||
3090 | Alerta | Carrier: Módulo do Ventilador Direito Parcialmente Avariado | Log Display | Flex | Controlador, Unidade e StepSync | ||
3096 | Alerta | Força de sinal de celular baixa | O valor do RSSI da conexão de celular está abaixo do valor-limite definido de -98 dBm. | Aproxime mais a ferramenta das antenas de celular para obter uma conexão mais forte e evitar a perda de dados. | Conf. | IxB | Controlador, Unidade e StepSync |
3097 | Alerta | Conexão de celular perdida. | O sistema perdeu a conexão com a rede de celular. |
| Log Display Conf. | IxB | Controlador, Unidade e StepSync |
3100 | Alerta | Configuração do Modo Não Existe | Log Display | Flex StepSync | Controlador, Unidade e StepSync | ||
3150 | Erro | Incompatibilidade do Software do IAM | O IAM é incompatível com o software instalado no controlador. | Substitua o IAM. | Log Display Confirm. | Flex IxB Power Focus 6000 Power Focus 8 StepSync Power Focus XC | Controlador, Unidade e StepSync |
3160 | Erro | Falha na ativação do software recém-instalado | Algo deu errado durante a ativação. Quando o software recém instalado é iniciado, ocorre um fallback no software anteriormente em funcionamento. Esse erro ocorre quando um novo software falha três vezes na inicialização e somente durante a instalação do software. | Exporte-o e entre em contato com a Atlas Copco para obter assistência adicional. Anote a versão do software que você está tentando instalar bem como a versão do software com a qual está trabalhando. | Log Display Confirm. | Flex IxB Power Focus 6000 Power Focus 8 StepSync Power Focus XC | Controlador, Unidade e StepSync |
3161 | Erro | Iniciou em uma Partição Inesperada do Software | O controlador iniciou em um lado inativo do software e não no lado esperado do software. | Anote as informações do software (na tela Inicial do controlador, selecione Controlador > Software). Tente reinicializar o controlador e assegure-se de que este está executando o software correto ao ser novamente reinicializado. Se o erro persistir, exporte-o e entre em contato com a Atlas Copco. | Log Display Confirm. | Flex IxB Power Focus 6000 Power Focus 8 StepSync Power Focus XC | Controlador, Unidade e StepSync |
3500 | Erro | Erro Genérico do Gerenciador de Licenças | Detectada inconsistência no sistema de gerenciamento de recursos utilizado. | Entre em contato com um representante da Atlas Copco. | Log Display Confirm. | IxB Power Focus 6000 Power Focus 8 StepSync Power Focus XC | Controlador, Unidade e StepSync |
3501 | Erro | Erro de sincronização do Gerenciador de licenças | Log Display Confirm. | IxB Power Focus 6000 Power Focus 8 StepSync Power Focus XC | Controlador, Unidade e StepSync | ||
3502 | Informações | Sincronização do Gerenciador de licenças concluída | IxB Power Focus 6000 Power Focus 8 StepSync Power Focus XC | Controlador, Unidade e StepSync | |||
3503 | Alerta | Gerenciador de Licenças: Outra Fonte em Uso | Licença utilizada por outra fonte. | Verifique a atribuição da licença. | Log Display | IxB Power Focus 6000 Power Focus 8 StepSync Power Focus XC | Controlador, Unidade e StepSync |
3504 | Alerta | Necessário Reinicializar Gerenciador de Licenças | Reinicializar o Gerenciador de Licenças | Log Display | IxB Power Focus 6000 Power Focus 8 StepSync Power Focus XC | Controlador, Unidade e StepSync | |
3505 | Informações | Sincronização de Licença do USB Iniciada | Log | Power Focus 6000 Power Focus 8 Power Focus XC | Controlador, Unidade e StepSync | ||
3506 | Erro | Erro na Sincronização de Licença do USB | Log | Power Focus 6000 Power Focus 8 Power Focus XC | Controlador, Unidade e StepSync | ||
3507 | Informações | Sincronização da Licença do USB Concluída | Log | Power Focus 6000 Power Focus 8 | Controlador, Unidade e StepSync | ||
3508 | Informações | Uma ou mais de suas licenças estão quase para expirar. Confira se há um servidor de licenças configurado | Atualizar licenças. | Log Display Conf. | IxB Power Focus 6000 Power Focus 8 StepSync Power Focus XC | Controlador, Unidade e StepSync | |
3511 | Alerta | Um de suas licenças apresenta uma definição de licença diferente | Detectada inconsistência em uma licença a ser usada. | Entre em contato com um representante da Atlas Copco. | Log Display Conf. | IxB Power Focus 6000 Power Focus 8 StepSync Power Focus XC | Controlador, Unidade e StepSync |
3550 | Alerta | Licença Inexistente | Instale a licença correta. | Log Display Conf. | IxB Power Focus 6000 Power Focus 8 StepSync Power Focus XC | Controlador, Unidade e StepSync | |
3551 | Alerta | Comunicação Sem Fio Desabilitada Pelo Licenciamento | Cancelar Atribuição da Licença Autônoma na Estação Virtual. | Log Display Conf. | IxB Power Focus 6000 Power Focus 8 StepSync Power Focus XC | Controlador, Unidade e StepSync | |
4010 | Informações | Ferramenta Travada por Entrada Digital | A ferramenta está bloqueada por um sinal de entrada digital. | Log Display Conf. | Flex IxB Power Focus 6000 Power Focus 8 StepSync Power Focus XC | Processo de Aperto | |
4011 | Informações | Ferramenta Travada por Open Protocol | A ferramenta está travada por Open Protocol. | Log Display Conf. | Flex IxB Power Focus 6000 Power Focus 8 StepSync Power Focus XC | Processo de Aperto | |
4012 | Informações | Ferramenta Travada por Fieldbus | A ferramenta é travada por Fieldbus. | Log Display Conf. | Flex Power Focus 6000 Power Focus 8 StepSync Power Focus XC | Processo de Aperto | |
4013 | Informações | Ferramenta Bloqueada por Seletor de Soquetes | A ferramenta está bloqueada quando o seletor de soquetes está desconectado da Estação Virtual. | Desbloquear com o Desbloqueio-mestre. | Log Display Conf. | IxB Power Focus 6000 Power Focus 8 Power Focus XC | Processo de Aperto |
4014 | Informações | Ferramenta Bloqueada por Soft PLC | O sinal do Soft PLC bloqueou a ferramenta. | Desbloquear com o Desbloqueio-mestre. | Log Display Conf. | Flex Power Focus 6000 Power Focus 8 StepSync Power Focus XC | Processo de Aperto |
4015 | Informações | Desaperto Desativado | O desaperto é desativado no programa de aperto. | Log Display Conf. | Flex IxB Power Focus 6000 Power Focus 8 StepSync Power Focus XC | Processo de Aperto | |
4016 | Informações | Aperto Desativado | Log Display Conf. | Flex IxB Power Focus 6000 Power Focus 8 StepSync Power Focus XC | Processo de Aperto | ||
4017 | Informações | Desaperto Não Configurado | O desaperto não está configurado no programa de aperto selecionado | Selecionar um programa de aperto diferente. | Log Display Conf. | Flex IxB Power Focus 6000 Power Focus 8 StepSync Power Focus XC | Processo de Aperto |
4020 | Informações | Número Excessivo de Apertos NOK | O número máximo de apertos NOK consecutivos é excedido no lote | Log Display Conf. | Flex IxB Power Focus 6000 Power Focus 8 StepSync Power Focus XC | Processo de Aperto | |
4025 | Informações | Nenhum Programa de Aperto Selecionado | Nenhum programa de aperto foi selecionado. | Selecionar um programa de aperto ou sequência de lotes. | Display Conf. | IxB Power Focus 6000 Power Focus 8 Power Focus XC | Processo de Aperto |
4030 | Informações | Sequência de Lotes Cancelada | A sequência de lotes foi cancelada. | Log Conf. | Flex IxB Power Focus 6000 Power Focus 8 StepSync Power Focus XC PFHC | Processo de Aperto | |
4031 | Informações | Tempo Máx. para Conclusão da Sequência de Lotes Atingido | Log Display Conf. | Flex IxB Power Focus 6000 Power Focus 8 StepSync Power Focus XC | Processo de Aperto | ||
4032 | Informações | Tempo Máx. para Conclusão do Primeiro Aperto Atingido | Log Display Conf. | Flex IxB Power Focus 6000 Power Focus 8 StepSync Power Focus XC | Processo de Aperto | ||
4035 | Informações | Bloqueado por Controle de Linha | Log Display Conf. | IxB Power Focus 6000 Power Focus 8 Power Focus XC | Processo de Aperto | ||
4040 | Informações | Bloqueada por Identificador Alternativo | A ferramenta está bloqueada por um identificador alternativo. | Log Display Conf. | IxB Power Focus 6000 Power Focus 8 Power Focus XC | Processo de Aperto | |
4050 | Configuração de Soquete Inválida | Programa de aperto atribuído a diversos soquetes. | Programa de aperto atribuído a diversos soquetes. | Log Display Conf. | IxB Power Focus 6000 Power Focus 8 Power Focus XC | Processo de Aperto | |
4060 | Informações | Ferramenta Bloqueada na Conclusão do Lote | Ao executar um lote com o sinalizador Ferramenta bloqueada na sequência de lotes concluída, esse evento é gerado quando o usuário pressiona o acionador. | Desbloqueie com o sinal Desbloquear ferramenta ao concluir. | Log Display Conf. | Flex IxB Power Focus 6000 Power Focus 8 StepSync Power Focus XC | Processo de Aperto |
4070 | Informações | Processo Entra em Modo Manual | Indica que o modo Manual foi ativado para uma estação virtual | Conf. | IxB Power Focus 6000 Power Focus 8 Power Focus XC | Processo de Aperto | |
4071 | Informações | Processo Entra em Modo Automático | Indica que o modo Automático foi inserido para uma estação virtual. | Conf. | IxB Power Focus 6000 Power Focus 8 Power Focus XC | Processo de Aperto | |
4072 | Informações | Testar Parafuso | Conf. | Flex StepSync | Processo de Aperto | ||
4073 | Informações | Posição zero da ferramenta atualizada | Indica que a posição zero da ferramenta é definida utilizando sinais. | Conf. | Flex IxB Power Focus 6000 Power Focus 8 StepSync Power Focus XC | Processo de Aperto | |
4100 | Alerta | Identificador Não Aceito Comprimento da Cadeia de Caracteres Inválido | Display Conf. | Flex IxB Power Focus 6000 Power Focus 8 StepSync Power Focus XC | Processo de Aperto | ||
4101 | Alerta | Seleção da Cadeia de Caracteres Mal-sucedida: Inúmeras Correspondências | Display Conf. | Flex IxB Power Focus 6000 Power Focus 8 StepSync Power Focus XC | Processo de Aperto | ||
4102 | Alerta | Seleção da Cadeia de Caracteres Malsucedida: Nenhuma Correspondência Encontrada | Display Conf. | Flex IxB Power Focus 6000 Power Focus 8 StepSync Power Focus XC | Processo de Aperto | ||
4103 | Alerta | Identificador Não Aceito Cadeia de Caracteres Idêntica Já Recebida | Display Conf. | Flex IxB Power Focus 6000 Power Focus 8 StepSync Power Focus XC | Processo de Aperto | ||
4104 | Alerta | Identificador Não Aceito Nenhuma Correspondência Encontrada | Display Conf. | Flex IxB Power Focus 6000 Power Focus 8 StepSync Power Focus XC | Processo de Aperto | ||
4500 | Informações | Resultado: Erro de unidade | Erro interno do driver ou foi detectada a perda do driver. | Conf. | Power Focus 6000 Power Focus 8 Power Focus XC | Processo de Aperto | |
4501 | Informações | Resultado: Reaperto | Tentativa de apertar um parafuso já apertado quando a detecção de Reaperto está ativada. | Conf. | IxB Power Focus 6000 Power Focus 8 Power Focus XC | Processo de Aperto | |
4502 | Informações | Resultado: Torque com Soft Start (Partida Suave) Baixo | O torque de partida suave está abaixo do nível mínimo. | Conf. | IxB Power Focus 6000 Power Focus 8 Power Focus XC | Processo de Aperto | |
4503 | Informações | Resultado: Torque com Soft Start (Partida Suave) Alto | O torque de partida suave excedeu do nível máximo. | Conf. | IxB Power Focus 6000 Power Focus 8 Power Focus XC | Processo de Aperto | |
4504 | Informações | Resultado: Torque Autoatarraxante Alto | O torque autoatarraxante excedeu o nível máximo. | Conf. | IxB Power Focus 6000 Power Focus 8 Power Focus XC | Processo de Aperto | |
4505 | Informações | Resultado: Torque Autoatarraxante Baixo | O torque autoatarraxante está abaixo do limite mínimo. | Conf. | IxB Power Focus 6000 Power Focus 8 Power Focus XC | Processo de Aperto | |
4506 | Informações | Resultado: Torque de Segurança Baixo | O valor de torque automaticamente calculado para garantir que o sensor de torque seja corretamente instalado. | Conf. | IxB Power Focus 6000 Power Focus 8 Power Focus XC | Processo de Aperto | |
4507 | Informações | Resultado: Torque alto de Rundown | O torque de Rundown excedeu o nível máximo. | Conf. | IxB Power Focus 6000 Power Focus 8 Power Focus XC | Processo de Aperto | |
4508 | Informações | Resultado: Ângulo alto de Rundown | O ângulo de Rundown excedeu o nível máximo. | Conf. | IxB Power Focus 6000 Power Focus 8 Power Focus XC | Processo de Aperto | |
4509 | Informações | Resultado: Duração longa de Rundown | A duração do Rundown excedeu o limite máximo. | Conf. | IxB Power Focus 6000 Power Focus 8 Power Focus XC | Processo de Aperto | |
4510 | Informações | Resultado: Duração curta de Rundown | A duração do Rundown ficou abaixo do limite mínimo. | Conf. | IxB Power Focus 6000 Power Focus 8 Power Focus XC | Processo de Aperto | |
4511 | Informações | Resultado: Torque baixo de Rundown | O torque de Rundown ficou abaixo do nível mínimo. | Conf. | IxB Power Focus 6000 Power Focus 8 Power Focus XC | Processo de Aperto | |
4512 | Informações | Resultado: Ângulo baixo de Rundown | O ângulo de Rundown ficou abaixo do nível mínimo. | Conf. | IxB Power Focus 6000 Power Focus 8 Power Focus XC | Processo de Aperto | |
4513 | Informações | Resultado: Torque final alto | O torque final da etapa excedeu do nível máximo. | Conf. | IxB Power Focus 6000 Power Focus 8 Power Focus XC | Processo de Aperto | |
4514 | Informações | Resultado: Ângulo final alto | O ângulo final da etapa excedeu do nível máximo. | Conf. | IxB Power Focus 6000 Power Focus 8 Power Focus XC | Processo de Aperto | |
4515 | Informações | Resultado: Torque final baixo | O torque final da etapa ficou abaixo do nível mínimo. | Conf. | IxB Power Focus 6000 Power Focus 8 Power Focus XC | Processo de Aperto | |
4516 | Informações | Resultado: Ângulo final baixo | O ângulo da etapa final ficou abaixo do nível mínimo. | Conf. | IxB Power Focus 6000 Power Focus 8 Power Focus XC | Processo de Aperto | |
4517 | Informações | Resultado: Tempo-limite de aperto | O limite de tempo de aperto foi excedido Para Estratégias Gerais de Aperto a duração máxima do aperto é de 30 segundos. Para Múltiplas Etapas, a duração máx. do aperto depende da restrição Limite máximo de duração. O código do erro depende da fase do aperto. | Executar novamente o aperto. | Conf. | IxB Power Focus 6000 Power Focus 8 Power Focus XC | Processo de Aperto |
4518 | Informações | Resultado: Perda de acionador | O acionador da ferramenta foi liberado antes do alvo ser atingido. Para Estratégias Gerais de Aperto, não é permitida a liberação do acionador antes da fase de aperto ser finalizada. Para Múltiplas Etapas, o erro é exibido quando o acionador é perdido antes do alvo ser atingido em uma etapa específica. | Conf. | IxB Power Focus 6000 Power Focus 8 Power Focus XC | Processo de Aperto | |
4519 | Informações | Perda Prematura do Torque | O soquete escapou da porca. | Conf. | IxB Power Focus 6000 Power Focus 8 Power Focus XC | Processo de Aperto | |
4520 | Informações | Resultado: Alvo atingido antes da etapa final | O torque-alvo foi atingido antes da etapa final no programa de aperto | Conf. | IxB Power Focus 6000 Power Focus 8 Power Focus XC | Processo de Aperto | |
4521 | Informações | Resultado: Torque pós-visualização baixo | O torque pós-visualização abaixo do nível mínimo. | Conf. | IxB Power Focus 6000 Power Focus 8 Power Focus XC | Processo de Aperto | |
4522 | Informações | Resultado: Torque alto pós-visualização | O torque pós-visualização excedeu o nível máximo. | Conf. | IxB Power Focus 6000 Power Focus 8 Power Focus XC | Processo de Aperto | |
4523 | Informações | Resultado: Intervalo de torque pós-visualização não atingido | O intervalo do torque pós-visualização não foi atingido. | Conf. | IxB Power Focus 6000 Power Focus 8 Power Focus XC | Processo de Aperto | |
4524 | Informações | Resultado: Intervalo de compensação de torque não atingido | O ângulo do intervalo de compensação do torque antes do final do Rundown não foi atingido. | Conf. | IxB Power Focus 6000 Power Focus 8 Power Focus XC | Processo de Aperto | |
4525 | Informações | Resultado: Movimentação da Ferramenta Excedida | A partir do status detalhado de um aperto NOK. | Conf. | IxB Power Focus 6000 Power Focus 8 Power Focus XC | Processo de Aperto | |
4526 | Informações | Resultado: Sensor de Monitoramento de corrente de segurança incompatível | Erro de monitoramento de corrente. | IxB Power Focus 6000 Power Focus 8 Power Focus XC | Processo de Aperto | ||
4527 | Informações | Resultado: Movimentação da Ferramenta Excedida | IxB Power Focus 6000 Power Focus 8 Power Focus XC | Processo de Aperto | |||
4538 | Informações | Resultado: Torque final de supervisão baixo | O torque final de supervisão não foi atingido. | Conf. | IxB Power Focus 6000 Power Focus 8 Power Focus XC | Processo de Aperto | |
4543 | Informações | Resultado: Monitor de encosto alto | Somente para chaves. O monitor detectou que o valor no encosto foi excedido. | Conf. | IxB Power Focus 6000 Power Focus 8 Power Focus XC | Processo de Aperto | |
4545 | Informações | Resultado: Sem torque residual | Somente para chaves. O torque residual ficou abaixo do limite. | Conf. | IxB Power Focus 6000 Power Focus 8 Power Focus XC | Processo de Aperto | |
4546 | Informações | Resultado: Sobrevelocidade | Somente para chaves. O giroscópio da chave falhou em medir o ângulo por causa da alta velocidade. | Conf. | IxB Power Focus 6000 Power Focus 8 Power Focus XC | Processo de Aperto | |
4547 | Informações | Resultado: Desaperto eficaz | Somente para chaves. A chave detectou um desaperto inesperado. | Conf. | IxB Power Focus 6000 Power Focus 8 Power Focus XC | Processo de Aperto | |
4548 | Informações | Resultado: Final menor do que alvo | O torque final ficou abaixo do torque-alvo definido no programa de aperto. | Conf. | IxB Power Focus 6000 Power Focus 8 Power Focus XC | Processo de Aperto | |
4549 | Informações | Tempo de limite do TurboTight Excedido | Conf. | IxB Power Focus 6000 Power Focus 8 Power Focus XC | Processo de Aperto | ||
4550 | Informações | Resultado: Pulsos de Rundown elevados | O número máximo de pulsos de Rundown foi excedido. | Conf. | IxB Power Focus 6000 Power Focus 8 Power Focus XC | Processo de Aperto | |
4551 | Informações | Resultado: Pulsos de Rundown baixos | O Rundown é concluído antes que o número mínimo de pulsos de Rundown seja atingido. | Conf. | IxB Power Focus 6000 Power Focus 8 Power Focus XC | Processo de Aperto | |
4552 | Informações | Resultado: Pulsos finais elevados | O número máximo de pulsos foi excedido. | Conf. | IxB Power Focus 6000 Power Focus 8 Power Focus XC | Processo de Aperto | |
4553 | Informações | Resultado: Pulsos finais baixos | O aperto é concluído antes que o número mínimo de pulsos de Rundown seja atingido. | Conf. | IxB Power Focus 6000 Power Focus 8 Power Focus XC | Processo de Aperto | |
4554 | Informações | Corrente Alta no Desligamento | A corrente no desligamento excedeu o Limite Alto de Corrente. | Conf. | IxB Power Focus 6000 Power Focus 8 Power Focus XC | Processo de Aperto | |
4555 | Informações | Corrente Baixa no Desligamento | A corrente de desligamento medida ficou abaixo do Limite Baixo de Corrente. | Conf. | IxB Power Focus 6000 Power Focus 8 Power Focus XC | Processo de Aperto | |
4556 | Informações | Erro de Múltiplas Etapas não Categorizado | Um erro na configuração de múltiplas etapas, frequentemente, com validação da ferramenta. | Conf. | IxB Power Focus 6000 Power Focus 8 Power Focus XC | Processo de Aperto | |
4557 | Informações | Resultado: Sobrecarga | Conf. | IxB Power Focus 6000 Power Focus 8 Power Focus XC | Processo de Aperto | ||
4600 | Alerta | Data Drop ou Data Hold utilizados em combinação com Aperto em Lotes. Os sinais não têm efeito | Data Drop e Data Hold são compatíveis somente para tarefas, sem controle de lote. Selecione outra tarefa se os sinais tiverem que ser usados. | Flex StepSync | Processo de Aperto | ||
4601 | Informações | Data Hold Ativo: resultado do aperto enviado depois que o sinal está baixo | Flex StepSync | Processo de Aperto | |||
4602 | Informações | Data Drop ativo: resultado do aperto descartado | Flex StepSync | Processo de Aperto | |||
5010 | Alerta | Valor do Parâmetro do Programa de Aperto Inválido | O parâmetro no programa de aperto selecionado é inválido. | Verifique a configuração do programa de aperto selecionado para encontrar e alterar o valor do parâmetro. | Log Display Conf. | Flex IxB Power Focus 6000 Power Focus 8 StepSync Power Focus XC PFHC | Configuração do Programa |
5011 | Alerta | Não foi possível preparar o armazenamento do programa na ferramenta | Não é possível ler a dimensão do armazenamento do programa atual na ferramenta STB, ou preparar o armazenamento do programa para baixar o programa de aperto atualizado, ou o selecionado por último, na ferramenta STB. |
| Log Display Conf. | Power Focus 6000 Power Focus 8 Power Focus XC | Configuração do Programa |
5020 | Informações | Acionador Principal não é a Fonte de Partida Ativa | Gerado quando configurado somente para partida "No tranco" e o usuário pressiona o acionador principal. Será gerado até o usuário pressionar a partida "No tranco". | Pressione partida "No tranco" para iniciar a ferramenta. | Log Display Conf. | IxB Power Focus 6000 Power Focus 8 Power Focus XC | Configuração do Programa |
5030 | Informações | Complexidade do Programa de Aperto Excede a Capacidade da Ferramenta | O programa de aperto selecionado é complexo demais para a ferramenta STB utilizada. A ferramenta será bloqueada. | Reduza a complexidade do programa de aperto ou escolha um programa diferente. | Log Display Conf. | Power Focus 6000 Power Focus 8 Power Focus XC | Configuração do Programa |
6010 | Informações | Acessório Conectado | O acessório está conectado ao controlador. | Log Display Confirm. Conf. | Flex IxB Power Focus 6000 Power Focus 8 StepSync Power Focus XC | Acessório | |
6020 | Informações | Acessório Desconectado | O acessório está desconectado do controlador. | Log Display Confirm. Conf. | Flex IxB Power Focus 6000 Power Focus 8 StepSync Power Focus XC | Acessório | |
6021 | Alerta | Barramento de campo off-line | Não há comunicação com o Fieldbus. | Log Display Confirm. Conf. | Flex Power Focus 6000 Power Focus 8 StepSync Power Focus XC | Acessório | |
6030 | Alerta | Colisão de Endereços do Acessório | Dois ou mais acessórios com o mesmo endereço estão conectados. | Altere o endereço no acessório. | Log Display Confirm. Conf. | Flex IxB Power Focus 6000 Power Focus 8 StepSync Power Focus XC | Acessório |
6040 | Alerta | Erro de Comunicação do Acessório | Erro de comunicação intermitente com o acessório. | Verifique os cabos e os conectores. | Log Display Conf. | Flex IxB Power Focus 6000 Power Focus 8 StepSync Power Focus XC | Acessório |
6041 | Alerta | Erro de Fieldbus | Erro de comunicação com o Fieldbus. |
| Log Display Confirm. Conf. | Flex Power Focus 6000 Power Focus 8 StepSync | Acessório |
6042 | Alerta | Incompatibilidade do Módulo de Fieldbus | O módulo do Fieldbus instalado não é compatível com o módulo configurado. | Altere a configuração para corresponder ao módulo instalado, ou substitua o módulo instalado pelo módulo correto. | Log Display Confirm. Conf. | Flex Power Focus 6000 Power Focus 8 StepSync | Acessório |
6043 | Alerta | Estouro de Buffer da Saída do Fieldbus | A saída de buffer usada na comunicação do Fieldbus está esgotada e ocorreu um estouro do buffer. Uma ou mais atualizações de sinal foram descartadas. | Pare a comunicação do Fieldbus e o diagnóstico do Fieldbus (se usado) para recuperar o buffer. Caso esse evento ocorra com frequência, verifique a configuração de comunicação de seu Fieldbus, inclusive o programa do PLC: atualizações frequentes demais comparadas a seu intervalo de atualização pode levar a esse cenário. | Log Display Confirm. Conf. | Flex Power Focus 6000 Power Focus 8 StepSync | Acessório |
6044 | Alerta | Incompatibilidade da ID do Provedor do Fieldbus | O módulo do Fieldbus instalado não é compatível. | Conecte um módulo de Fieldbus Atlas Copco compatível. | Log Display Confirm. | Power Focus 8 | Acessório |
6050 | Informações | Seleção de Soquete Incorreta | Gerado quando nenhum soquete ou o soquete incorreto é selecionado. | Log Display Conf. | IxB Power Focus 6000 Power Focus 8 Power Focus XC | Acessório | |
6090 | Alerta | Scanner de Código de Barras não pôde ser identificado | Quando nenhum número de série exclusivo é encontrado. | Configure o dispositivo leitor de código de barras. | Log Display Confirm. Conf. | Flex Power Focus 6000 Power Focus 8 StepSync Power Focus XC PFHC | Acessório |
7010 | Informações | Texto da Mensagem a Exibir | Evento em geral para exibição de mensagens. | Display Confirm. Conf. | Flex IxB Power Focus 6000 Power Focus 8 StepSync Power Focus XC PFHC | Mensagem | |
8200 | Informações | Falha em Abrir Porta Serial | A Porta serial a ser usada não pôde ser aberta. | Verifique as conexões da porta serial. | Display Conf. | IxB Power Focus 6000 Power Focus 8 Power Focus XC | Diversos |
8300 | Alerta | Tempo-limite da comunicação com o Open Protocol cliente expirou | Comunicação com o Open Protocol cliente atingiu o tempo limite Nenhuma mensagem ou comando keep alive enviado dentro do tempo esperado. |
| Log Display Conf. | Flex IxB Power Focus 6000 Power Focus 8 StepSync Power Focus XC | Diversos |
8214 | Erro | Incompatibilidade da Versão do Software da EHMI | A versão de software da EHMI não é compatível com o controlador. | Atualizar a versão do software da EHMI. | Log Display Confirm. Conf. | IxB Power Focus 6000 Power Focus 8 Power Focus XC | Diversos |
Lista de produtos para os quias o código de evento está disponível.
Grupo ao qual os códigos de eventos pertencem.
Uma breve descrição do evento e por que este ocorre.
Se for aplicável, o procedimento contém uma instrução sobre como apagar o evento.
Diz ao usuário se o evento deve ser salvo ou não em um log de eventos. O valor nessa lista é o valor-padrão.
Diz ao usuário se o evento deve ser ou não exibido na tela. O valor nessa lista é o valor-padrão.
Diz ao usuário se o evento deve ser confirmado ou não antes que se possa prosseguir. O valor nessa lista é o valor-padrão.
O número exclusivo do evento.
Tipo de evento: Informações, Avisos e Erros
Um nome que descreve o evento.
Trabalhando com a Aba Settings (Definições)
Configurações de rede
A ferramenta pode ser configurada para ser acessada sem fio a partir de um navegador de rede em uma rede local (LAN) usando um protocolo IPv4.
Há uma opção de usar a ferramenta como um cliente ou um ponto de acesso para outros serviços.
Abra a tampa da porta de conexão de USB do controlador manual.
Conecte um PC ao conector USB-C no controlador manual. Para garantir que o PC forneça alimentação suficiente ao controlador manual, use as portas USB-3.0.
Para inserir a GUI de configuração, insira o endereço a seguir em seu navegador: 164.254.1.1/config.html.
Consulte mais informações na seção Requisitos de navegador da web.
Configuração de canais
Acesse Settings (Definições) no menu da página inicial e selecione Network (rede) no painel da esquerda.
No campo Channels (Canais), escolha a frequência (2,4 GHz ou 5 GHz) e selecione Edit (Editar).
Escolha ativar ou desativar os canais.
Configurando um Cliente Sem Fio
Acesse Settings (Definições) no menu da página inicial e selecione Network (rede) no painel da esquerda.
Na janela Wireless Client (Cliente Sem Fio), selecione Edit (Editar).
Defina Enabled (Ativado) como On (Ativo).
Defina DHCP como On (Ativo) ou Off (Desativado), dependendo da configuração. Caso esteja definido como Off (Desativado), preencha com as informações necessárias fornecidas pelo administrador local do sistema.
Endereço IP
Máscara de sub-rede
Gateway
Insira um Network name (SSID) (Nome de rede (SSID)).
No campo Security (Segurança), selecione Mode (Modo) e escolha o modo security (Segurança) na lista. Caso seja escolhido WPA2 Personal, escolha Security key (Chave de segurança).
Insira parâmetros de segurança e importe arquivos de certificado e chaves, conforme aplicável.
Edite the Optional Settings (Definições Opcionais), conforme aplicável.
Selecione Apply (Aplicar).
A ferramenta estabelecerá uma conexão sem fio para a rede, indicada com o indicador azul de LED de conexão emitindo uma luz permanente.
Para acessar sem fio a interface do usuário, digite o endereço IP no navegador da Web.
Configurando a Ferramenta como um Ponto de Acesso Sem Fio

Se múltiplos canais foram configurados anteriormente em Wireless Client mode (Modo Cliente Sem Fio), ativar Wireless AP mode (Modo de Ponto de Acesso Sem Fio) atualizará a lista de canais para que ela contenha somente o canal atual/padrão para o Wireless AP mode (Modo Ponto de Acesso Sem Fio).
Acesse Settings (Definições) no menu da página inicial e selecione Network (rede) no painel da esquerda.
No campo Wireless AP (Ponto de Acesso Sem Fio), selecione Edit (Editar).
Defina Enabled (Ativado) como On (Ativo).
Insira as informações necessárias fornecidas pelo administrador local do sistema:
Endereço IP
Máscara de sub-rede
Gateway
Para distribuir endereços IP, defina DHCP Server (Servidor DHCP) como On (Ativo) e insira IP range start (Início do intervalo IP) e IP range stop (Fim do intervalo IP).
Insira um Network name (SSID) (Nome de rede (SSID)).
No campo Security (Segurança), selecione Mode (Modo) e escolha o modo security (Segurança) na lista. Caso seja escolhido WPA2 Personal, escolha Security key (Chave de segurança).
Selecione Apply (Aplicar).
Conexões do Server
O controlador manual pode ser configurado para comunicação com os servidores executando o seguinte software daAtlas Copco:
ToolsNet − utilizado para administrar relatórios de resultados.
Configuração da Conexão do ToolsNet
Acesse Settings (Definições) no menu da página inicial e selecione Server Connections (Conexões do Servidor) no painel da esquerda.
No campo ToolsNet, defina os seguintes parâmetros:
Campo
Descrição
Ativo/Desativado
Ativa/Desativa a comunicação com o servidor do ToolsNet
Porta do servidor
Porta do servidor do ToolsNet.
Host do servidor
Endereço IP do servidor do ToolsNet.
Selecione Apply (Aplicar).

Para visualizar o status da conexão do ToolsNet, acesse Reports > Results (Relatórios > Resultados) e selecione o botão . Na caixa de diálogo que aparece, selecione a aba Server connections (Conexões do servidor).
Para informações sobre como configurar o ToolsNet, consulte o ToolsNet 8 User Guide(Guia do Usuário do ToolsNet 8).
Configurando a Conexão de Registro em Log Remoto
Para conectar um controlador a um servidor de registro em log remoto, configure e ative as definições do registro em log remoto no controlador.
Na exibição inicial, vá para a aba Settings (Definições) e selecione Server connections (Conexões do Servidor) no painel esquerdo.
Na seção Remote Logging (Registro em Log Remoto), configure os seguintes parâmetros:
Campo | Descrição |
---|---|
Ativo/Desativado | Ativa/Desativa a comunicação com o servidor de registro em log remoto |
TCP/UDP | Seleciona o protocolo TCP ou UDP |
Host do servidor | Endereço IP do servidor do registro em log remoto |
Porta do servidor | Porta do servidor do registro em log remoto |
Configurar Níveis de Log
Configure os logs que estão armazenados no servidor:
Na exibição inicial, vá para a aba Settings (Definições) e selecione Server connections (Conexões do Servidor) no painel esquerdo.
Na janela Remote Logging (Registro em log remoto), selecione Configure (Configurar).
Na janela Configure Facilities Configurar Instalações), selecione as caixas de seleção aplicáveis.
Categoria
Classificação do SysLog
Erro
Alerta, Crítico, Emergência, Erro
Alerta
Alerta
Informações
Informativo, Aviso
Para restaurar a seleção a uma configuração anterior, selecione UNDO (DESFAZER).
Selecione Apply (Aplicar).
Preferências
Data e Hora
Data e hora devem ser definidas para que eventos e resultados tenham o carimbo com a data e hora corretas de quando ocorreram. A hora é recuperada de uma das três fontes disponíveis:
Manual − a data, a hora e o fuso horário são definidos manualmente.
NTP − a data e a hora são recuperados de um servidor NTP (Network Time Protocol) definido na interface do usuário.
ToolsNet − a data e a hora são recuperados de um servidor ToolsNet.
É necessária uma conexão de rede funcional para as fontes de data/hora do NTP e do ToolsNet.
Acesse Definições no menu inicial e selecione Preferências no painel da esquerda.
No campo Data e Hora, defina os seguintes parâmetros:
Parâmetro
Descrição
Fonte
Fonte de onde recuperar a hora.
Servidor NTP 1
Endereço IP.de um servidor NTP que fornece data e hora para a ferramenta.
Status do servidor 1
Status OK/Nenhum
Servidor NTP 2
Endereço IP.de um servidor NTP que fornece data e hora para a ferramenta.
Status do servidor 2
Status OK/Nenhum
Data
Data inserida manualmente, caso a fonte seja definida como manual.
Hora
Hora inserida manualmente, caso a fonte seja definida como manual.
Fuso horário
O fuso horário; seja a localização ou o horário padrão, como UTC.
Selecione APLICAR
Definindo o Idioma
A interface do usuário está disponível nos doze idiomas seguintes:
Inglês
Tcheco
Alemão
Espanhol
Francês
Coreano
Italiano
Japonês
Português
Russo
Sueco
Chinês
Acesse Definições no menu inicial e selecione Preferências no painel da esquerda.
No campo Idioma, selecione o idioma geralmente utilizado e escolha um idioma na lista.
A alteração do idioma é imediatamente efetivada.
Definindo a Unidade de Torque
Os resultados do torque são exibidos na unidade escolhida, tanto após o aperto ser realizado como quando armazenados na lista de resultados.
Unidade | Descrição |
---|---|
cNm | centinewton metro |
dNm | decinewton metro |
Nm | newton metro |
kNm | quilonewton metro |
in·lbf | libra-força polegada |
ft·lbf | libra-força pé |
in·ozf | onça-força polegada |
ft·ozf | onça-força pé |
gf·cm | grama-força centímetro |
kgf·cm | quilograma-força centímetro |
kgf·m | quilograma-força metro |
Unidades de Pressão
Acesse Definições no menu inicial e selecione Preferências no painel da esquerda.
No campo Unidades de Pressão, selecione a unidade Bar ou Pa na lista.
Configurando as Definições do PIN
O código PIN evita a utilização não autorizada da GUI da web ou alterações acidentais.
Se ativado, o código PIN é necessário ao configurar mudanças a partir da GUI da Web.
Configurando o PIN
É possível ter uma ou diversas configurações de PIN na GUI da web. Os usuários podem decidir se desejam ou não ativar uma ou diversas configurações de PIN ao mesmo tempo.
Cada configuração do PIN possui um código PIN, um nome de usuário, uma chave para habilitar ou desabilitar o usuário/PIN, e uma lista de configurações disponíveis que o usuário pode acessar.
Quando o PIN está habilitado e a tela está bloqueada, um ícone de cadeado fechado é mostrado no canto superior direito do GUI. ]O usuário pode acessar e efetuar as alterações somente nas configurações selecionadas, sem inserir qualquer código PIN, e procurar as configurações não selecionadas com acesso apenas para leitura. As configurações não selecionadas estão em cinza ou desabilitadas.
O bloqueio da tela liga automaticamente após determinado período de inatividade, o que pode ser configurado pelo usuário.
O valor mínimo de tempo de inatividade é de 20 s e o valor máximo é de 600 s. O tempo de inatividade é configurável e se aplica a todas as configuração do PIN.
Depois de uma inicialização do sistema, o controlador é bloqueado se o PIN estiver ativado, independente do tempo de inatividade atual.

Os usuários e os PINs configurados aplicam-se também à Porta de Serviço (169.254.1.1).
Para ativar a proteção do PIN na Porta de Serviço, na janela PIN, defina Use PIN for Service Port (Usar PIN na Porta de Serviço) como On (Ativo).
Cada controlador pode configurar até 10 usuários.
O PIN de cada configuração deve ser único. É obrigatório ter no mínimo uma configuração para ativar a funcionalidade PIN no controlador.
O PIN pode ser configurado a partir da GUI da web.
Criando Novos Usuários
Na visualização Home (Página Inicial), selecione a aba Settings (Definições). Em seguida, à esquerda, selecione PIN.
Na janela PIN, selecione Configure (Configurar).
Selecione o ícone Plus (sinal de mais), no canto superior direito da GUI.
A janela PIN-Users (Usuários do PIN) mostra o novo. Caso não haja usuários armazenados na GUI da Web, o novo usuário é o primeiro e o único na lista; caso existam usuários armazenados na GUI da Web, o novo usuário é o último da lista.Selecione um novo usuário.
A janela User (Usuário) aparece.
Insira o Nome e o PIN do novo usuário, e em seguida confirme o PIN.O Nome do Usuário deve ser único.
A caixa de texto Name (Nome) pode conter de 1 a 32 caracteres.O código PIN deve ter 4 dígitos (número 1 a 9).
A caixa Enter PIN (Insira o PIN) e a caixa Confirm PIN (Confirme o PIN) precisa corresponder às alterações a serem aplicadas. Por padrão, são indicados pontos em ambas as caixas de texto, mas esses são apenas espaços reservados e necessitam ser substituídos por códigos PIN reais.Selecione Permissions (Permissões). Uma lista de configurações disponíveis aparece.
Selecione a caixa de seleção à esquerda das configurações necessárias que o usuário pode acessar e nelas fazer alterações.
Após selecionar as configurações necessárias, selecione OK (Ativo).
A janela User (Usuário) aparece.Select all (Selecionar todas) seleciona todas as configurações disponíveis ao mesmo tempo.
Selecione Deselect all (Desmarcar todas) para limpar as caixas de seleção e desfazer a seleção.O usuário pode acessar e efetuar as alterações somente nas configurações selecionadas na janela Permissions (Permissões), e navegar pelas configurações não selecionadas com acesso apenas para leitura. Para configurações não selecionadas, não são permitidas alterações.
Na janela User (Usuário), selecione Apply (Aplicar).
Ativando Usuários
Na visualização Home (Página Inicial), selecione a aba Settings (Definições). Em seguida, à esquerda, selecione PIN.
Na janela PIN, selecione Configure (Configurar).
Na janela de PIN-Users (PIN-Usuários), selecione a caixa de seleção à esquerda do nome do usuário a ser ativado.
O PIN pode também ser ativado clicando-se no nome do usuário e definindo - na janela User (Usuário) - a chave seletora Enabled (Ativado) como On (Ativo).
Ativando a configuração do PIN
Na visualização Home (Página Inicial), selecione a aba Settings (Definições). Em seguida, à esquerda, selecione PIN.
Na janela PIN, selecione Configure (Configurar).
Na janela PIN-activating (Ativação do PIN, defina a chave seletora PIN Code (Código PIN) como On (Ativo).
O PIN pode ser ativado quando pelo menos um usuário/PIN está ativado. Caso nenhum usuário/PIN esteja ativado, uma janela pop-up de Warning (Advertência) aparece.
Insira Inactivity Timeout (Tempo-limite de Inatividade) (em segundos) que define o intervalo de tempo após o qual a tela é automaticamente bloqueada.
O valor padrão do Tempo -limite de Inatividade é de 120 segundos: isso é uma definição global, e não pode ser definido pelo usuário.
Desbloqueando a GUI da Web
Na exibição Home (Página inicial), selecione o ícone Padlock (Cadeado) no canto superior direito da GUI. Uma janela pop-up com um teclado numérico aparece.
Insira o código PIN configurado e selecione OK.
Quando o PIN está ativado e a tela está bloqueada, um ícone Open Padlock (Abrir Cadeado) aparece no canto superior direito do GUI. A GUI da Web pode ser novamente bloqueada manualmente, selecionando-se o ícone Open Padlock (Abrir Cadeado).
Desativando Usuários
Na visualização Home (Página Inicial), selecione a aba Settings (Definições). Em seguida, à esquerda, selecione PIN.
Na janela PIN, selecione Configure (Configurar).
Na janela PIN-Users (PIN-Usuários), desmarque a caixa de seleção à esquerda do nome do usuário a ser desativado.
O PIN pode também ser desativado clicando-se no nome do usuário e definindo - na janela User (Usuário) - a chave seletora Enabled (Ativado) como Off (Desativado).
Excluindo Usuários
Na visualização Home (Página Inicial), selecione a aba Settings (Definições). Em seguida, à esquerda, selecione PIN.
Na janela PIN, selecione Configure (Configurar).
Na lista de PIN-Users (PIN-Usuários), selecione o ícone Delete (Excluir) à direita do nome do usuário a ser excluído.
Caso o User (Usuário) seja removido, o PIN também é excluído. Não é possível acessar configurações com o PIN excluído.
Configurações das Definições de Eventos
É possível configurar os eventos disponíveis no controlador tanto como um quanto vários dos itens a seguir:
Reconhecimento
Registrado em log
Exibido
Configuração de Registro em Log Estendido
O PFHC cria automaticamente logs e os armazena. Esses registros em log podem ser configurados para incluir registros em log estendidos utilizando grupos de registro em log.
Configurando Grupos de Log
A configuração padrão para um grupo de registro em log é “desativado”. Para alterar a definição de um grupo de log para on (ativo):
Na exibição inicial, vá para a aba Settings (Definições) e selecione Extended Logging (Registro em Log Estendido) no painel esquerdo.
Na janela Log Groups (Grupos de Log), defina o grupo como ON (Ativo).
Restaurar Grupos de Registro em Log
É possível restaurar todos os grupos de registro em log às suas configurações padrões.
Na exibição inicial, vá para a aba Settings (Definições) e selecione Extended Logging (Registro em Log Estendido) no painel esquerdo.
Na janela Reset Log Groups (Restaurar Grupos de Registro em Log), selecione Reset (Restaurar).
Uma janela pop-up aparece perguntando se você deseja restaurar todos os grupos de log. Selecione YES (DEFINIR).
Grupos de Registro em Log Persistentes
Os grupos de registro em log são restaurados à sua configuração padrão a cada reinicialização. Para impedir a restauração, utilize grupos de registro em persistentes.
Na exibição inicial, vá para a aba Settings (Definições) e selecione Extended Logging (Registro em Log Estendido) no painel esquerdo.
Na janela Keep Selection after Restart (Manter Seleção após reinício) , defina Persistent (Persistente) como ON (LIGADO).
Restabelecer
Controlador de Restauração da Fábrica
É possível restaurar o controlador às definições originais de fábrica.

Todas as definições, configurações de dados históricos serão excluídos quando o controlador for restaurado. Faça uma restauração de fábrica somente quando você estiver totalmente seguro de que isso é necessário.
Realizando uma Restauração de Fábrica do Controlador
Na visualização Home (Página Inicial), selecione a aba Settings (Definições). Em seguida, à esquerda, selecione Reset (Reinicializar).
Na janela Factory Reset Controller (Controlador de Redefinição da Fábrica), selecione Reset (Redefinir).
Uma janela pop-up aparece alertando que todos os dados serão excluídos. Em seguida, selecione Yes (Sim).
O controlador reinicializa para ativar as novas definições.
Apagar resultados
É possível excluir resultados e eventos armazenados no controlador.
Excluindo Resultados e Eventos
Na visualização Home (Página Inicial), selecione a aba Settings (Definições). Em seguida, à esquerda, selecione Reset (Reinicializar).
Na janela Clear Results (Apagar Resultados), selecione Clear (Apagar).
Uma janela pop-up aparece alertando que todos os resultados e eventos serão excluídos. Em seguida, selecione Yes (Sim).
Desligue o sistema e aguarde 30 segundos para depois ligar o sistema novamente.
Trabalhando com a Aba Help (Ajuda)
Esta seção fornece ajuda ao trabalhar na GUI da Web. O Manual do Usuário do Power Focus HC está integrado nesta aba. Os capítulos estão no painel da esquerda.
Operação
Nesta seção, é possível encontrar informações progressivas sobre como operar o produto.
GUI do controlador
Inicialização do sistema
O menu Tarefas no controlador manual está na cor cinza durante a inicialização, o que significa que ele não está acessível até que a inicialização do sistema seja finalizada..
Durante a inicialização do sistema, ocorre o seguinte:
A bomba e o tensionador partem e estabelecem comunicação com o controlador manual.
Se a versão do firmware da bomba ou do tensionador não for compatível com a versão do software do controlador manual, a versão do software será atualizada para uma versão compatível. Esse processo pode ser observado no LED do tensionador, que está em azul durante a verificação da compatibilidade do firmware e do possível processo de atualização. Quando o LED de status do tensionador parar de piscar e estiver na cor branca constante, significa que o tensionador estabeleceu conexão com o controlador manual.
Se o firmware da bomba ou do tensionador não for o que o controlador manual está esperando, é acionado o evento 2516 "Versão inesperada do firmware da bomba ou do tensionador detectada, reinicie o sistema. Se o problema persistir, pode ser possível executar o sistema, mas observe com atenção qualquer comportamento inesperado”. Caso um firmware relatado esteja na lista de versões de firmware incompatíveis do controlador manual, o controlador manual emite um evento 2617 “Versão incompatível de firmware da bomba ou do tensionador, reinicie o sistema. O sistema não pode ser executado”. No caso de um firmware incompatível, o controlador manual não ativará Início->Tarefas. Em ambos os casos, reinicie o sistema e deixe a unidade que falhou na atualização fazer outra tentativa.
O Nome do controlador manual pode ser substituído no IAM. Consulte a seção Módulo de Aplicação Inteligente.
Status da conexão
Os ícones de status da conexão sem fio e de status da conexão ToolsNet mostram uma atualização ao vivo do estado da conexão. O controlador manual se conectará ao Wi-Fi, caso ele esteja configurado para fazê-lo em Definições -> Rede.
Quando o sem fio está conectado e o HC tem uma conexão ativa com a rede de Wi-Fi, o ícone da conexão Wi-Fi aparece sem a linha diagonal.
Quando o controlador manual está configurado para a conexão com o ToolsNet, o estado do ícone reflete o estado da conexão. A linha diagonal significa que não há conexão aberta para o ToolsNet.
Tela inicial
Quando todos os três componentes finalizarem o processo upstart e a comunicação do sistema é iniciada, o menu Tarefas estará disponível.
Avisos e lembretes
Quando o sistema tem um aviso ou uma mensagem de informação relacionada ao status da bomba ou do tensionador, o ícone dos dispositivos conectados é destacado com uma moldura azul e o número de mensagens é exibido. Ao entrar na aba Dispositivos conectados, o ícone de informações ou de aviso mostra ao usuário onde as informações adicionais estão disponíveis. Alguns status também aparecem como faixas de aviso na tela inicial.
Lembretes de trocas de óleo
É exibido um lembrete de troca de óleo quando o tempo da próxima troca de óleo for menor do que quatro semanas, ou o tempo de funcionamento do motor já atingiu as últimas 50 horas.

Os últimos 28 dias antes da data da próxima troca de óleo e as últimas 50 horas de funcionamento do motor, e o ícone de informações são exibidos.
O ícone de informações se torna um aviso quando a data da troca de óleo já passou, ou o motor já atingiu o limite de tempo.
Trabalhando com a aba Tarefas
O menu Tasks (Tarefas) está disponível quando tanto a bomba quanto o tensionador estão conectados ao controlador manual.
Somente tarefas com configurações válidas são exibidas na GUI dos controladores manuais.
Por exemplo, se não houver configurações para Assembly (Conjunto), então, nem o Assembly (Conjunto) e nem o Batch Assembly (Conjunto de lotes) estão disponíveis.
O Manual Mode (Modo manual) está sempre presente.
Assembly (Conjunto) e Bolt Service (Serviço do Parafuso) permitem uma execução para um parafuso, por exemplo, para fins de treinamento e testes.
As tarefas a seguir estão disponíveis no controlador manual:
Assembly (Conjunto): uma execução única de uma configuração de tensionamento da Etapa.
Batch Assembly (Conjunto de lotes): executa um serviço de lote de uma configuração de tensionamento da Etapa. O operador deve inserir as informações adicionais antes de iniciar o trabalho.
Manual mode (Modo manual): permite o controle manual do processo de tensionamento. Esse processo pode ser executado por qualquer tensionador.
Bolt Service (Serviço de parafuso): uma execução única de uma configuração de serviço do parafuso.
Batch Bolt Service (Serviço de parafuso de lote): executar um serviço de lote de uma configuração de serviço de tensionamento. O operador deve inserir as informações adicionais antes de iniciar o trabalho.
Use o Manual mode (Modo manual) para remover o tensionamento ou desapertar parafusos. Recomenda-se usar uma estratégias de desaperto aplicável. Para mais informações sobre a remoção do tensionamento, consulte a seção Remoção do tensionamento da Porca.
GUI simplificada de operações de tensionamento
Há duas telas de GUI do controlador manual para operações de tensionamento, uma GUI completa e uma GUI simplificada.
A GUI completa mostra os valores medidos da pressão, torque, ângulo e a força aplicada no flange.
A GUI simplificada é uma GUI do Operador mais limpa, semelhante aos LEDs no tensionador, assim, os LEDs no controlador manual mostram o mesmo status que os LEDs no tensionador.
É possível alternar entre essas duas telas de GUI usando os botões para cima e para baixo no controlador manual.
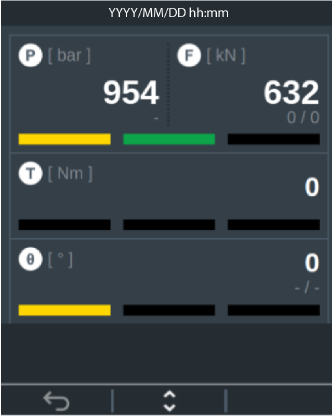
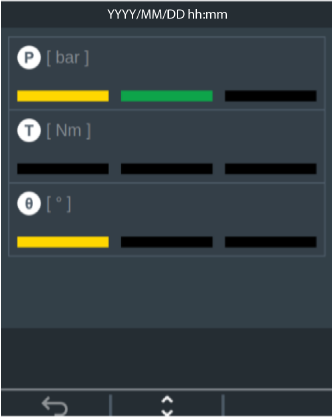
Conjunto
Na aba Assembly (Conjunto), há uma lista de programas de tensionamento pré-configurados compatíveis com o tensionador conectado. Se nenhum programa compatível estiver disponível, a mensagem a seguir aparece na parte inferior da tela: No compatible program (Nenhum programa compatível.
Na visualização da página inicial, Tasks > Assembly (Tarefas > Conjunto).
Selecione um programa para executar usando os botões para cima e para baixo para navegar pela lista e depois pressione o botão Enter no meio para confirmar a escolha.
O nome apresentado na lista é tomado do campo Name (Nome) na aba General Settings > Properties (Definições Gerais > Propriedades).
Quando a mensagem Position tool on bolt (Posicionar a ferramenta no parafuso) aparecer na tela, execute o tensionador diretamente na parte superior do parafuso.
Verifique se o soquete está alinhado com a porca.
Pressione o botão Forward (Avançar) no teclado para iniciar a operação de tensionamento.
Operação de tensionamento
A operação de tensionamento consiste das seguintes etapas:
Verificação de instalação
Etapa de pressurização
Aperto da porca
A anulação pode ser realizada a qualquer momento durante a operação de tensionamento.
Enquanto o sistema aguarda que o usuário tome alguma ação, aparece um texto de ajuda após alguns segundos; este desaparece assim que a ação esperada seja detectada.
Verificação de instalação
O objetivo da verificação de instalação.é criar um ponto de referência para a medição do ângulo.
Pressione o botão Pressurizar para evitar que o tensionador gire durante a verificação de instalação.
A pressão pode ser insuficiente, especialmente nas primeira execuções após um longo intervalo. Nesse caso, pressione novamente o botão Pressurizar.
A pressão pode ultrapassar - o sistema avisa o usuário para que libere pressão e tente novamente.
Essa ultrapassagem pode ocorrer devido ao parâmetro Angle reset force (Força de redefinição do ângulo); ver seção Tensioning Parameters (Parâmetros de tensionamento).
Gire a porca no sentido horário para atingir o nível de torque definido no parâmetro Installation check torque (Torque de verificação da instalação) (valor padrão 20 Nm). Mantenha o torque pode no mínimo Installation check torque duration (a duração do torque de verificação da instalação) (valor padrão 1 segundo).
Todos os 3 LEDs ficam verdes.
Libere a força no torquímetro de estalo.
Etapa de pressurização
Pressione e mantenha pressionado botão Pressurizar.
Quando um LED na fileira de ângulos do tensionador e seu equivalente no controlador manual fica aceso, execute a porca seguindo a extensão do parafuso.
Não aplique torque à porca antes da pressão-alvo ser atingida. A pressão fará o trabalho.
Aperto da porca
Mantenha o botão Pressurizar pressionado para que o sistema mantenha a pressão acima do parâmetro Pressão mínima de tensionamento do parafuso.
A pressão cairá vagarosamente, o sistema irá pressurizar antes de cair abaixo da pressão mínima.
Aperte a porca conforme o Torque-alvo de aperto e mantenha o torque pelos segundos da duração do torque de aperto.
Todos os LEDs ficam acesos quando essa condição é atendida.
Relaxe o torque.
Se o parâmetro Liberação automática de pressão estiver ON (Ligado), o sistema liberará a pressão quando o torque for relaxada para menos de 10 Nm.
Se o parâmetro Liberação automática de pressão estiver OFF (Desligado), libere a pressão usando o botão Pressurizar.
Quando a pressão for liberada, o resultado OK ou NOK será exibido no controlador manual. Em ambos os casos, a visualização detalhada mostrará o ângulo/força registrada e as leituras de torque.
Anulação

É sempre possível anular uma tarefa em andamento, mas a pressão do sistema deve ser liberada antes disso.
Pressione o botão Despressurizar para liberar a pressão.
Pressione o botão Back (Voltar) no teclado para iniciar a operação de tensionamento.
Ao abortar a operação de tensionamento durante um serviço de lote, o usuário terá duas opções:
Cancelar o parafuso: se o número do parafuso estiver incorreto. A GUI do controlador manual retorna à tela Position tool on bolt (Posicionar ferramenta no parafuso).
Abort Batch (Anular parafuso): quando o serviço de tensionamento precisa ser pausado e interrompido.
Ao executar o serviço de Conjunto, a GUI do controlador manual retorna ao menu Tasks (Tarefas).
Conjunto de Lote
Um lote é configurado para executar um número específico de tensionamentos consecutivos usando as mesmas configurações de tensionamento.
Na visualização da página inicial, acesse Tasks > Assembly (Tarefas > Conjunto de Lote).
Selecione um programa para executar usando os botões para cima e para baixo para navegar pela lista e o botão Enter no meio para confirmar a escolha.
O nome apresentado na lista é tomado do campo Name (Nome) na aba General Settings > Properties (Definições Gerais > Propriedades).
Selecione uma das duas opções conforme aplicável: Tower Section ID (ID da Torre) ou Tower Data (Dados da Torre).
Escaneie o identificador do flange.
Escaneie ou insira manualmente a ID da seção da torre que é a referência para o flange específico. O identificador é necessário para gerar o relatório do resultado, uma vez que é usado para agrupar os resultados que pertencem ao um flange específico. Para mais informações sobre como usar os botões do teclado no controlador manual, consulte a seção GUI Buttons and Icons (Botões e Ícones da GUI).
Escaneie ou insira manualmente o QR code Tower Data (Dados Torre) se estes estiverem disponíveis. Essa sequência é uma lista separada por ponto e vírgula contendo a ID da seção da torre e alguns dados adicionais acrescentados aos resultados. Controlador manual verifica o formato dessa sequência e gera uma mensagem de erro se o formato não for aprovado.
Escaneie os metadados opcionais do serviço incluídos nos resultados:
Escanear os dados do operador
Escanear a empresa do operador
Dados do parafuso
Localização do parafuso
ID do Operador
Dados do operador
Empresa do operador
Pressione o botão Forward ((Avançar) para continuar.
Insira o número total de parafusos no flange mesmo se a intenção não seja fazer um subconjunto de parafusos.
Insira um dígito usando os botões para cima e para baixo e pressionando o botão Enter para confirmar. Pressione o botão Next (Avançar) para inserir o próximo dígito usando os botões para cima e para baixo e Enter para confirmar a escolha.
Para mais informações sobre como usar os botões do teclado no controlador manual, consulte a seção GUI Buttons and Icons (Botões e Ícones da GUI).
Quando o número total de parafusos no flange for inserido corretamente, pressione o botão Forward (Avançar) para inserir a tela-resumo.
A tela-resumo mostra o nome do programa a ser executado e o número de parafusos.
Pressione o botão Forward (Avançar) para iniciar o primeiro tensionamento.
Ao reiniciar um serviço de lote iniciado anteriormente, os resultados de cada tensionamento aparecem em verde (OK) ou vermelho (NOK) na tela Position tool on bolt (Posicionar a ferramenta no parafuso).
Se o número do parafuso não estiver correto, edite-o usando o botão More (Mais).
O usuário é responsável por garantir que o número do parafuso esteja correto.
Pressione o botão Forward (Avançar) para começar a operação de tensionamento;consulte a seção Operação de tensionamento.
Modo manual
No Manual mode (Modo manual), nenhum processo é monitorado pelo sistema, exceto para controle da pressão-alvo, e nenhum resultado é registrado.
Para poder monitorar manualmente o processo, a GUI do controlador mostra as informações sobre a pressão, torque e ângulo.
A primeira vez que o Modo Manual é executado após a partida do sistema, o operador precisa Definir a pressão-alvo inserindo a pressão-alvo a usar. O modo manual subsequente executado lembrará a última pressão-alvo utilizada desde que o sistema esteja ligado.
A tela Set Target Pressure (Definir pressão-alvo) é preenchida com o parâmetro de configuração do modo manual Pressão hidráulica manual padrão.
A pressão-alvo é limitada pelo valor mais baixo do seguinte:
Pressão Máx. da bomba
Pressão Máx. do tensionador
Pressão hidráulica máx. do sistema - o parâmetro de configuração do modo manual
Operação no Modo Manual
Na visualização da página inicial, acesse Tasks > Manual Mode (Tarefas > Modo Manual).
Defina a pressão-alvo.
Quando surgir Posicionar a ferramenta no parafuso, é possível alterar a pressão-alvo pressionando o botão More (Mais).
Pressione o botão Forward (Avançar) para iniciar o Modo Manual.
Pressurize pressionando o botão Pressurizar.
A pressurização para na pressão-alvo ou quando o botão é liberado.
O torque aplicado no torquímetro é visualizado tanto como uma barra branca quanto como dígitos.
O ângulo registrado é apresentado com dígitos.
Quando o torque começa a diminuir, o pico do torque é visualizado em preto, e o atual torque em uma barra branca. O pico da medição é apresentado com dígitos.
Use o botão More (Mais) para fazer o seguinte:
Definir a nova pressão-alvo - selecione Set Target Pressure (Definir pressão-alvo) na janela pop-up.
Apague o pico de torque e registrado e o ângulo.
Ao mover o torquímetro no sentido anti-horário, registra-se um torque e ângulo negativos.
Para sair do modo manual, use o botão Back (Voltar).
Só é possível sair do modo manual quando a pressão for liberada do sistema.
A GUI do controlador volta ao menu Tasks (Tarefas).
Desapertar a porca
Gire para trás o tensionador em 3 mm a partir da superfície de contato do flange.
Selecione Manual mode (Modo manual) no controlador manual, e, em seguida, defina pressão na qual o parafuso foi tensionado originalmente, e comece a aumentar a pressão enquanto segura o torquímetro de estalo: com força positiva no sentido anti-horário.
Quando a carga aplicada atingir o ponto de abertura de ruptura, o torquímetro de estalo se move livremente abrindo a porca. Gire o torquímetro de estalo de 6 a 7 vezes seu ciclo de janela limitado.
Libere a pressão e verifique se o parafuso está desapertado.

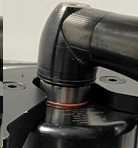

A luz de sinalização de curso máximo na barra extratora não deve ficar visível quando se pressuriza o tensionador. Se estiver visível, pare e ajuste a posição da barra extratora no parafuso, de modo que a posição máxima não seja atingida até que a pressão requerida seja obtida. Do contrário, caso isso seja feito repetidas vezes, poderá danificar fisicamente os componentes internos do tensionador.
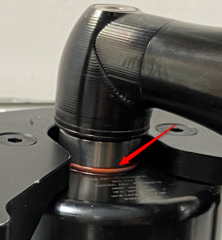
Serviço do parafuso
O processo de serviço do parafuso verifica se as porcas e os parafusos estão em boas condições. A porca é desapertada conforme o Ângulo de desaperto mínimo de desaperto da porca (valor padrão 10 graus), e depois apertada novamente.
O ângulo e torque no sentido de aperto serão exibidos como valores positivos, enquanto o ângulo e o torque no sentido de desaperto, como valores negativos.
Na visualização da página inicial, acesse Tasks > Bolt Service (Tarefas > Serviço do parafuso).
Selecione um programa para executar usando os botões para cima e para baixo para navegar pela lista e depois o botão Enter no meio para confirmar a escolha.
O nome apresentado na lista é tomado do campo Name (Nome) na aba General Settings > Properties (Definições Gerais > Propriedades).
Quando a mensagem Position tool on bolt (Posicionar a ferramenta no parafuso) aparecer na tela, execute o tensionador diretamente na parte superior do parafuso.
Verifique se o soquete está alinhado com a porca.
Pressione o botão Forward (Avançar) no teclado para iniciar a operação de serviço do parafuso.
Operação de serviço do parafuso
As operações de serviço de parafuso compreendem as seguintes fases:
Verificação da instalação
Fase de pressurização
Desaperto da porca
Aperto da porca
O cancelamento pode ser feito a qualquer momento durante operação de serviço do parafuso.
Quando o sistema aguarda a atuação do usuário, aparece um texto de ajuda após alguns segundos e ele desaparece logo que a ação esperada é detectada.

A rotação delta da porca é definida como a soma da rotação das porcas: rotação de desaperto + rotação de aperto. Por exemplo, se a rotação de desaperto for −13 graus, e a rotação de aperto for de 15 graus, a total a rotação total da porca é igual a 2. (−13 +15 = 2)
Verificação da Instalação
O objetivo da verificação da instalação é criar um ponto de referência para a medição do ângulo.
Pressione o botão de pressurização para evitar que o tensionador gire durante a verificação da instalação.
A pressão pode ser insuficiente, especialmente nas primeiras execuções após uma longa parada. Nesse caso, pressione o botão de pressurização novamente.
A pressão pode ser excessiva - o sistema avisa ao usuário para liberar a pressão e tentar novamente.
O excesso pode ocorrer devido ao parâmetro Força de restauração do ângulo, consulte a seção Parâmetros de Tensionamento.
Gire a porca no sentido horário para atingir o nível de torque definido no parâmetro Torque de verificação da instalação (valor-padrão 20 Nm). Mantenha o torque no mínimo pela Duração do torque de verificação da instalação (valor-padrão 1 segundo).
Todos os três LEDs se tornam verdes.
Libere a força no torquímetro de estalo.
Gire a porca no sentido anti-horário para atingir o nível de torque definido no parâmetro Torque de verificação da instalação(valor-padrão 20 Nm). Mantenha o torque no mínimo pela Duração do torque de verificação da instalação (valor-padrão 1 segundo).
Todos os três LEDs se tornam verdes.
Libere a força no torquímetro de estalo.
Fase de pressurização
Pressione e mantenha pressionado o botão de pressurização.
Não tente girar a porca antes da pressão-alvo ser atingida, pois a porca está fixa ao flange com uma força elevada.
Desaperto da Porca
Mantenha o botão de pressurização pressionado para permitir que o sistema mantenha a pressão acima do parâmetro Pressão mínima de tensionamento do parafuso.
A pressão cai vagarosamente; o sistema pressuriza até antes que ela caia abaixo da pressão mínima.
Desapertar a porca conforme o Ângulo mínimo de desaperto do desaperto da porca.
Se a porca ficar presa por algum motivo, como corrosão, o sistema permite um Número de tentativas de desaperto da porca (valor-padrão 3); depois ele avisa ao usuário para apertar a porca novamente. Este será um resultado NOK .
Uma tentativa é definida como a aplicação de um torque mais alto do que o Torque de contagem de tentativas de desaperto da porca.
Todos os três LEDs na fileira do ângulo estão acesos quando esta condição é atendida.
Se o ângulo de desaperto for maior do que o Ângulo de desaperto mínimo do desaperto da porca e o movimento total da porca estiver dentro do intervalo entre a Rotação mínima delta da porca e a Rotação máxima delta da porca, o resultado é OK.
Aperto da Porca
Aperte a porca conforme o Torque-alvo de aperto e mantenha o torque pelos segundos da Duração do torque de aperto.
Todos os três LEDs estão acesos quando essa condição é atendida.
Libere a força no torquímetro de estalo.
Se o parâmetro Liberação automática da pressão estiver Ativo, o sistema libera pressão quando o torque estiver relaxado até menos do que 10 Nm.
Se o parâmetro Liberação automática da pressão estiver Desativado, libere a pressão pressionando o botão despressurizar.
Quando a pressão estiver liberada, o resultado OK ou NOK é exibido no controlador manual. Em ambos os casos a visualização detalhada mostra as leituras registradas de pressão/ângulo da força e torque.
Se o ângulo de desaperto for maior do que o Ângulo de desaperto mínimo do desaperto da porca e o movimento total da porca estiver dentro do intervalo entre a Rotação mínima delta da porca e a Rotação máxima delta da porca, o resultado é OK.
Cancelamento

É sempre possível cancelar uma tarefa em andamento, mas a pressão do sistema deve ser liberada antes disso.
Pressione o botão Despressurizar para liberar a pressão.
Pressione o botão Voltar para sair da operação de serviço do parafuso.
Ao cancelar a operação de serviço do parafuso durante para um trabalho de lote, o usuário terá duas opções:
Cancelar o Parafuso: se o número do parafuso não estiver correto. A GUI do controlador manual retorna para a tela Posicionar ferramenta no parafuso.
Cancelar Lote: quando o trabalho de tensionamento precisa ser pausado ou parado.
Ao executar um trabalho de Serviço de Parafuso, a GUI do controlador manual retorna para o menu Tarefas.
Serviço do parafuso de lote
Na visualização da página inicial, acesse Tasks > Batch Bolt Service (Tarefas > Serviço de Parafuso de lote).
Selecione um programa para executar usando os botões para cima e para baixo para navegar pela lista e o botão Enter no meio para confirmar a escolha.
O nome apresentado na lista é tomado do campo Name (Nome) na aba General Settings > Properties (Definições Gerais > Propriedades).
Selecione uma das duas opções conforme aplicável: Tower Section ID (ID da Torre) ou Tower Data (Dados da Torre).
Escaneie o identificador do flange.
Escaneie ou insira manualmente a ID da seção da torre que é a referência para o flange específico. O identificador é necessário para gerar o relatório do resultado, uma vez que é usado para agrupar os resultados que pertencem ao um flange específico.
Para mais informações sobre como usar os botões do teclado no controlador manual, consulte a seção GUI Buttons and Icons (Botões e Ícones da GUI).
Escaneie ou insira manualmente o QR code Tower Data (Dados Torre) se estes estiverem disponíveis. Essa sequência é uma lista separada por ponto e vírgula contendo a ID da seção da torre e alguns dados adicionais acrescentados aos resultados. Controlador manual verifica o formato dessa sequência e gera uma mensagem de erro se o formato não for aprovado.
Escaneie os metadados opcionais do serviço incluídos nos resultados:
Escanear os dados do operador
Escanear a empresa do operador
Dados do parafuso
Localização do parafuso
ID do Operador
Dados do operador
Empresa do operador
Pressione o botão Forward ((Avançar) para continuar.
Insira o número total de parafusos no flange mesmo se a intenção não for fazer um subconjunto de parafusos.
Para mais informações sobre como usar os botões do teclado no controlador manual, consulte a seção GUI Buttons and Icons (Botões e Ícones da GUI).
Pressione o botão Forward (Avançar) para inserir a tela de resumo.
A tela-resumo mostra o nome do programa a ser executado e o número de parafusos.
Pressione o botão Forward (Avançar) para iniciar a operação de serviço do parafuso.
Ao reiniciar um serviço de lote iniciado anteriormente, os resultados de cada serviço de parafuso aparecem em verde (OK) ou vermelho (NOK) na tela Position tool on bolt (Posicionar a ferramenta no parafuso).
Se o número do parafuso não estiver correto, edite-o usando o botão More (Mais).
O usuário é responsável por garantir que o número do parafuso esteja correto.
Pressione o botão Forward (Avançar) para iniciar a operação de serviço do parafuso; consulte a seção Operação de serviço do parafuso em Serviço do parafuso.
Trabalhando com a Aba Relatórios
Gerar Relatórios
Os relatórios são gerados para uma unidade flash USB conectada ao conector USB-A no controlador manual.
Na visualização da Página inicial, selecione a aba Reports (Relatórios), e, depois, Generate Reports (Gerar relatórios) pressionando o botão Enter.
Para definir o intervalo de datas para gerar o relatório, edite Data de início e a Data final usando os botões do teclado no controlador manual. Se esses campos forem deixados vazios, o relatório incluirá todos os resultados do controlador manual.
Pressione o botão Forward (Avançar) e, depois, selecione Start Generation (Começar a gerar) pressionando o botão Enter ou anule pressionando o botão Back (Voltar).
Um texto de alerta Make sure that a USB flash drive is connected before report generation starts (Verifique se uma unidade flash USB está conectada antes do relatório ser gerado) aparece aparece.
Quando aparece a mensagem Report Generated (Relatório gerado) na tela, pressione o botão Next (Próximo).
Remova a unidade flash USB.
Resultados
Os resultados dos trabalhos de serviço de lote podem ser visualizados na aba Relatórios. Os resultados armazenados podem ser visualizados por ID de Seção de Torre para todos os trabalhos de lote.
O resultado completo do flange é visualizado como um círculo.
Segmentos na cor verde para resultados OK.
Segmentos na cor vermelha para resultados NOK.
Segmentos ativos estão na cor branca.
Resultados faltantes estão na cor cinza.
Na aba Relatórios, selecione Resultados.
Para definir o intervalo da data para os Resultados, edite e a Data de Início e a Data Final utilizando os botões do teclado no controlador manual. Se esses campos forem deixados vazios, todos os resultados no controlador manual podem ser visualizados.
Navegue pelos resultados pressionando os botões para cima e para baixo no teclado
Selecione o Resultado a ser visualizado pressionando o botão Enter.
A aparece a visualização de um círculo com o Resultado selecionado. Cada segmento representa um único parafuso no trabalho de lote.
Navegue pelos resultados do parafuso utilizando os botões para cima e para baixo no teclado para avançar ou para voltar ao resultado anterior.
É possível navegar até um número de parafuso específico utilizando o botão Mais, depois insira o número do parafuso, e pressione o botão Avançar.
Clique no botão Avançar para visualizar detalhes do parafuso escolhido.
Trabalhando com a Aba Informações do Controlador
O menu Controller information (Informações do controlador) mostra as seguintes informações:
Dados da unidades do controlador manual - número de série.
Número de artigo
Endereço Ethernet
Versão do Software
Dados do desenvolvimento do software
Trabalhar com a Aba Settings (Definições)
Na visualização Inicial, selecione a abas Definições para fazer o seguinte:
Definir Hora
Definir Data
Limpar Resultados
Idioma
Definir Hora
Definir a hora no formato 24 horas utilizando os botões para cima e para baixo, depois pressione o botão Avançar.
Para mais informações sobre como utilizar botões do teclado no controlador manual, consulte a seção Botões e Ícones da GUI.
Confirme a hora com o botão Avançar quando o campo dos minutos estiver ativo.
Para cancelá-lo, pressione o botão Voltar quando o campo da hora estiver ativo.
Definir Data
Defina a data no formato dd/mm/aaaa utilizando os botões para cima para baixo, depois pressione o botão Avançar.
Para mais informações sobre como utilizar botões do teclado no controlador manual, consulte a seção Botões e Ícones da GUI.
Confirme a data com o botão Avançar quando o campo do dia estiver ativo.
Para cancelá lo, pressione o botão Voltar quando o campo do ano estiver ativo.
Limpar Resultados
Para limpar todos os resultados armazenados no controlador:
Acesse a aba Definições, depois selecione Limpar Resultados.
Pressione o botão Enterpara confirmar, depois selecione Sim na janela pop-up ou Não para cancelar.
Para evitar problemas, recomenda-se limpar os resultados regularmente após concluídos os trabalhos e exportações de lote. O espaço de disco no controlador manual não é ilimitado.
Idioma
Para alterar a definição de idioma:
Acesse a aba Definições, depois selecione Idioma. Pressione o botão Enter para confirmar.
O menu Idioma está sempre por último na lista Inicial -> Definições para permitir também a navegação para o idioma quando o controlador manual está utilizando um idioma desconhecido para o operador.
Escolha o idioma desejado na lista. Pressione o botão Enter para confirmar.
Trabalhando com Dispositivos conectados
Na visualização Inicial, selecione a aba Dispositivos Conectados para ver os dados das unidades conectadas.
A tela principal mostra também informações sobre os seguintes itens:
Versões do firmware
Tamanho do tensionador
Contagem da barra extratora
Número máximo de pressurizações da barra extratora
Bomba
Na exibição Inicial, vá para a aba Dispositivos Conectados.
Selecione a Bomba, depois pressione o botão Enter para ver os seguintes itens:
Detalhes da bomba
Identificador Personalizado da Bomba
Troca de óleo - Tempo de funcionamento restante
Para ver mais detalhes pressione o botão Enter.
Detalhes da bomba
Selecione Detalhes da bomba para ver informações sobre essa unidade conectada, por exemplo, número de artigo, número de série, versão do hardware e os seguintes itens:
Motor da bomba no tempo conta o número de segundos em que o motor esteve em funcionamento.
Intensificador da bomba no tempo conta o número de segundos em que em que o intensificador esteve em funcionamento.
Contagem da pressurização do óleo da bomba conta o número de pressurizações > 75% do máximo (=>1400 bares) que já ocorreram desde a última troca de óleo registrada.
Identificador Personalizado da Bomba
Identificador Personalizado da Bomba é um campo que pode ser utilizado pelo cliente para identificar a unidade com a ajuda de uma ID arbitrária. A ID personalizada é armazenada na bomba e é lida pelo controlador manual na partida do sistema.
Para editar a ID personalizada, selecione a tela Identificador Personalizado da Bomba pressionando o botão Enter.
Pressione o botão Mais para ler ou inserir manualmente a nova ID personalizada.
Selecione Ler ou Inserir Manualmente na janela pop-up para inserir a nova ID personalizada.
Para Inserir Manualmente:
Selecione Salvar e Sair na janela pop-up ou Restaurar e Sair para cancelar esta etapa.
É emitido um evento mostrando sucesso (aparece ID Personalizada está definida).

Os caracteres no identificador personalizado devem ser caracteres ASCII e com valores < 128; consulte uma tabela de ASCII.

A nova ID personalizada será válida na próxima inicialização do sistema.
Troca de óleo - Tempo de funcionamento restante
Ao final da troca do óleo e do filtro, confirme a troca selecionando Bomba -> Troca de óleo - Tempo de funcionamento restante -> Óleo e filtro trocados -> Sim.
A próxima data de troca do óleo será definida como uma vez ao ano no futuro e o motor da bomba no tempo é limpo exibindo 0.
A nova data é transferida para a bomba e armazenada; a próxima data de troca de óleo e do filtro segue a bomba e será exibida no controlador manual conectado a ela.
Tensionador
Na exibição Inicial, vá para a aba Dispositivos Conectados.
Selecione a Tensionador, depois pressione o botão Enter para ver os seguintes itens:
Tensionador
Barra Extratora
Célula de Carga
Pistão
Identificador Personalizado do Tensionador
Para ver mais detalhes pressione o botão Enter.
Quando a lista for maior do que a tela, utilize os botões para cima e para baixo para ver a lista completa.
Tensionador
Tamanho do Soquete
Pressão Máx.
Número de artigo
Nome - esse campo é definido na produção
Revisão
Número de Série
GUID
Barra extratora
A barra extratora é uma peça de desgaste interna que precisa ser trocada regularmente.
Contagem Real da Barra Extratora mostra o número de vezes em que a barra extratora foi pressurizada, que é > 70% da pressão máxima (1.400 bares).
Contagem Máxima da Barra Extratora mostra a pressurização máxima permitida, que é > 70% da pressão máxima (1.400 bares).
Contagem Restante da Barra Extratora
Número de Artigo
Número de Série
Data da Montagem
Data de Fabricação
Célula de Carga
Pressão Máx.
Contagem Real da Célula de Carga mostra o número de pressurizações > 75% da máxima (=> 1400 bares).
Número de Artigo
Número de Série
Data da Montagem
Data de Fabricação
Pistão
Área do Pistão
Número de Artigo
Número de Série
Data da Montagem
Data de Fabricação
Identificador Personalizado do Tensionador
Identificador Personalizado do Tensionador é um campo que pode ser utilizado pelo cliente para identificar a unidade com a ajuda de uma ID arbitrária. A ID personalizada é armazenada no tensionador e é lida pelo controlador manual na partida do sistema.
Para editar a ID personalizada, selecione a tela Identificador Personalizado do Tensionador pressionando o botão Enter.
Pressione o botão Mais para ler ou inserir manualmente a nova ID personalizada.
Selecione Ler ou Inserir Manualmente na janela pop-up para inserir a nova ID personalizada.
Para Inserir Manualmente:
Selecione Salvar e Sair na janela pop-up ou Restaurar e Sair para cancelar esta etapa.
É emitido um evento mostrando sucesso (aparece ID Personalizada está definida ou falha).

Os caracteres no identificador personalizado devem ser caracteres ASCII e com valores < 128; consulte uma tabela de ASCII.

A nova ID personalizada será válida na próxima inicialização do sistema.
Alerta máx. da barra extratora
Quando o contador da barra extratora se aproxima do máximo da barra extratora, uma mensagem de aviso Contagem restante da barra extratora, que também aparece ao se iniciar o trabalho de tensionamento, aparece na aba Dispositivos Conectados.
Quando o número de trabalhos de tensionamento restantes é igual a 500, aparece uma mensagem de aviso Contagem restante da barra extratora: 500. As mensagens de aviso continuam a aparecer mais frequentemente quando esse número chega mais próximo de 0. Quando o número de trabalhos de tensionamento restantes é igual a zero, não é permitido mais nenhum tensionamento. Troque o tensionador para continuar o trabalho.
Na GUI do controlador, selecione Dispositivos Conectados, depois selecione Tensionador e clique em Barra Extratora para ver as seguintes informações:
Contagem Real da Barra Extratora
Contagem Máxima da Barra Extratora
Contagem Restante da Barra Extratora
Número de artigo
Número de série
Solução de problemas e assistência técnica
Esta seção fornece auxílio na solução de problemas, caso este surjam, e contém informações que o ajudam a manter e dar manutenção ao produto.
Resolução de problemas e alarmes
As tabelas abaixo descrevem diferentes situações, problemas e alarmes com as possíveis causas e soluções correspondentes. Os alarmes mostraram um alerta com um código no controlador manual para a execução de ações corretivas.
Alarme | Possível causa | Solução |
---|---|---|
Alarme de temperatura alta do óleo do motor da bomba | A temperatura do óleo no interior da bomba está acima da temperatura permitida devido a diferentes motivos: Trabalho continuo | Deixe a bomba funcionar em vazio para deixá-la resfriar por alguns minutos. |
Qualidade do óleo | Verificar se há contaminação Trocar o óleo. | |
Temperatura externa | Trocar o óleo por um de qualidade adequada. | |
Alarme de nível de óleo baixo no motor da bomba | Quando o nível de óleo da bomba está abaixo do nível mínimo, o sistema para. | Complete o óleo na bomba para reiniciar o trabalho. |
Vazamento no sistema | Verificar vazamentos no sistema; depois, reparar ou trocar. | |
Alarme da proteção do motor da bomba | Corrente forte ou alimentação anormal no interior do motor. Esse alarme é acionado para a segurança dos dispositivos eletrônicos e componentes elétricos conectados ao motor. | Abra a pequena janela frontal na bomba. Reposicionar o botão preto na posição I reinicia a alimentação elétrica do motor. Se o erro se repetir, verifique a rede elétrica. |
Problemas na comunicação da ferramenta | Sobrecorrente fluindo durante um Intervalo de tempo longo demais é o mais comum. Esse alarme é acionado para a segurança dos dispositivos eletrônicos e dos componentes elétricos dentro dos invólucros elétricos. | Abra a pequena janela frontal na bomba. Rearme o disjuntor para reiniciar o trabalho. Se o disjuntor continuar desarmando dentro de segundos de retrabalho, pare o trabalho e execute ações corretivas.
|
Um curto circuito elétrico. | ||
Uma falha elétrica no terra. | ||
Nenhuma pressão detectada na bomba | Falha do motor Ordem incorreta da fase no conector trifásico. | Desligue o sistema e inverta as fases do conector de alimentação. |
Alerta | Possível causa | Solução |
---|---|---|
Troca do óleo | É necessária uma troca de óleo. Uma mensagem de informação é exibida:
Uma mensagem de aviso é exibida:
| Trocar o óleo. Confirme se o óleo já foi trocado; consulte Troca de óleo - Tempo de funcionamento restante, Bomba (Bomba). |
Sobretorque | Força de aperto alta demais. | Relaxar a força no torquímetro. |
Sobrepressão | Pressão alta demais podendo causar danos à máquina. | Reduza a pressão. |
Problema | Possível causa | Solução |
---|---|---|
Tensionador preso ao parafuso após o tensionamento | Nível baixo de carga da apertadeira a bateria. | Troque a bateria da apertadeira por uma bateria carregada. |
Sem afastamento entre a parede e o tensionador. | Verifique o afastamento da parede na parte posterior do tensionador. Se não houver espaço, destensione o parafuso utilizando o modo manual. | |
Alinhamento dos orifícios, lubrificação e roscas dos parafusos. | Verifique também o alinhamento dos orifícios, a lubrificação e as roscas dos parafusos. Se tiver com dúvida, troque o parafuso e tente novamente. | |
O tensionador não executa o Rundown no parafuso | As roscas do parafuso estão danificadas. | Troque o parafuso. |
As roscas do parafuso não estão lubrificadas. | Lubrifique as roscas do parafuso. | |
Detritos nas roscas do tensionador. | Remova os detritos das roscas com uma escova de aço. | |
A protrusão do parafuso excede o limite máximo. | Ajuste a protrusão desapertando o parafuso, de modo que ele não exceda o limite máximo. | |
A pressão não aumenta acima de 200 bares na bomba | Vazamento na bomba. | Verifique se há vazamentos na bomba ou na linha hidráulica do sistema. Verificar o nível do óleo. Complete o óleo se ele estiver baixo demais. Envie a bomba para manutenção ou reparo, se o problema persistir. |
Óleo de qualidade errada. | Confirme se está utilizando o óleo da qualidade correta. | |
Dificuldade em desconectar da bomba o engate da linha hidráulica | O niple da mangueira está desgastado. | Troque os niples da mangueira e do tensionador, assim que ficarem agarrando ou com maior dificuldade de desconexão. |
Referências
Nesta seção, pode-se encontrar diversas informações úteis.
Termos e Definições
Termo | Sinônimo | Definição | Observação |
---|---|---|---|
batch (lote) | Tensionamento múltiplo utilizando o mesmo programa de tensionamento e soquete | ||
controller GUI (GUI do controlador) | Interface Gráfica do Usuário | Interface de usuário do controlador manual usado para operar o sistema | |
event (evento) | Sinais de status do controlador manual ou dispositivos conectados | ||
final angle (ângulo final) | valor real do ângulo medido no final do ciclo do processo de tensionamento | ||
final torque (torque final) | valor real do torque medido no final do ciclo do processo de tensionamento | ||
Pressão final | valor real da tensão medida no final do ciclo do processo de tensionamento. | ||
GUI | Interface Gráfica do Usuário | interface gráfica do usuário formada por elementos gráficos interativos, como janelas, ícones e símbolos em um display | |
IAM | Módulo de Aplicação Inteligente | Módulo do controlador manual contendo dados de produção | |
Programa de Tensionamento | Parameter set (Conjunto de parâmetros) | configuração de parâmetros e valores para controlar e monitorar uma única ação de tensionamento e armazenar o resultado do tensionamento | O alvo expresso em pressão, torque ou ângulo. |
target (alvo) | resultado desejado de um tensionamento | O alvo expresso em torque ou ângulo. | |
target angle (ângulo-alvo) | valor de ângulo desejado ao final do ciclo do processo de tensionamento a partir de um ponto de referência | ||
target torque (torque-alvo) | valor de torque desejado ao final do processo de tensionamento | ||
web GUI (GUI da Web) | interface do usuário para o controlador por meio da janela Navegador da Web a partir de um computador remoto | ||
virtual station (estação virtual) | virtual controller (controlador virtual) | Abstração do software de um controlador físico | Um controlador pode fazer parte de somente um sistema de tensionamento. |
Third Party Licenses (Licenças de Terceiros)
Lista de licenças de Terceiros
Os controladores Power Focus incorporam componentes de terceiros cujas licenças exigem que publiquemos cópias do idioma de licença e/ou avisos de direitos autorais. Em conformidade com esses requisitos, seguem algumas cópias de licenças. Clique em qualquer licença abaixo para exibir uma cópia do texto da licença.
Software | Version | Licenses |
---|---|---|
acl | 2.2.52 | |
alsa-lib | 1.1.2 | |
alsa-state | 0.2.0 | |
alsa-tools | 1.1.0 | |
alsa-utils | 1.1.2 | |
anybus | 1.1 |
|
atftp | 0.7.1 + gitAUTOINC + be3291a18c | |
attr | 2.4.47 | |
barebox | 2018.06.0 | |
base-files | 3.0.14 | |
base-files-px2-base | 1.0 | |
base-passwd | 3.5.29 | |
bash | 4.3.30 | |
bash-completion | 2.4 | |
bluez5 | 5.41 | |
boost | 1.61.0 | |
busybox-px2base | 1.24.1 | |
bzip2 | 1.0.6 | |
ca-certificates | 20160104 | |
cppunit | 1.13.1 | |
cryptodev-linux | 1.8 | |
curl | 7.50.1 | |
db | 3.0.35 | |
dbus | 1.10.10 | |
dhcp | 4.3.4 | |
dosfstools | 4.0 | |
dt-utils | 2017.03.0 | |
e2fsprogs | 1.43 | |
ecryptfs-tools | 1.0 | |
elfutils | 0.166 | |
eudev | 3.2.2 | |
expat | 2.2.0 | |
fbset | 2.1 | |
fb-test | 1.1.0 | |
fcgi | 2.4.0 | |
finit | 3.1 | |
firmware-imx | 5.4 |
|
flac | 1.3.1 | |
flatbuffers | 1.9.0 | |
fruit | 3.4.0 + gitAUTOINC + ece0f7218c | |
fuse | 2.9.4 | |
gcc-runtime | 6.2.0 | |
gdb | 8.0.1 | |
gdbm | 1.12 | |
glib-2.0 | 2.48.2 | |
glibc | 2.24 | |
gmp | 6.1.1 | |
gnutls | 3.5.3 | |
grep | 2.25 | |
gstreamer1.0 | 1.8.3 | |
gstreamer1.0-plugins-base | 1.8.3 | |
hostpad | 2.6 | |
htop | 1.0.3 | |
icu | 57.1 | |
init-ifupdown | 1.0 | |
initscripts | 1.0 | |
iproute2 | 4.7.0 | |
iptables | 1.6.0 | |
ipwatchd | 1.2 | |
iw | 4.7 | |
json-spirit | 4.08 | |
keyutils | 1.5.9 | |
kmod | 23 + gitAUTOINC + 65a885df5f | |
kmsfbwrap-px2base | 12.0 | |
libarchive | 3.2.2 | |
libbsd | 0.8.3 |
|
libcap | 2.25 | |
libdrm | 2.4.70 | |
libestr | 0.1.10 | |
libevent | 2.0.22 | |
libfastjson | 0.99.4 | |
libffi | 3.2.1 | |
libgcc | 6.2.0 | |
libgcrypt | 1.7.3 | |
libgpg-error | 1.24 | |
libidn | 1.33 | |
libite | 2.0.2 | |
libjpeg-turbo | 1.5.0 | |
liblogging | 1.0.5 | |
libnet | 1.2-rc3 | |
libnfsidmap | 0.25 | |
libnl | 3.2.28 | |
libogg | 1.3.2 | |
libpcap | 1.8.1 | |
libpcre | 8.39 | |
libpng | 1.6.24 | |
librcf | 2.2.0.0 | |
libsamplerate0 | 0.1.8 | |
libsndfile1 | 1.0.27 | |
libtinyxml | 2.6.2 | |
libtirpc | 1.0.1 | |
libuev | 2.2.0 | |
libusb1 | 1.0.20 | |
libvorbis | 1.3.5 | |
libxml2 | 2.9.4 | |
libxslt | 1.1.29 | |
lighttpd | 1.4.51 | |
linux-atlas | 4.14 | |
linux-libc-headers | 4.14.13 | |
logrotate | 3.9.1 | |
lua | 5.1.5 | |
luabind | git | |
lzo | 2.09 | |
lzop | 1.03 | |
memlog | 2.0 | |
mesa | 12.0.1 | |
mg | 20161005 |
|
minizip | 1.2.8 | |
mmc-utils | 0.1 | |
mtd-utils | 1.5.2 | |
nano | 2.2.5 | |
ncurses | 6.0 + 20160625 | |
netbase | 5.3 | |
netcat-openbsd | 1.105 | |
nettle | 3.2 | |
nfs-utils | 2.1.1 | |
ntp | 4.2.8p8 | |
openssh | 7.6p1 | |
openssl | 1.0.2n | |
opkg | 0.3.3 | |
opkg-arch-config | 1.0 | |
opkg-utils | 0.3.2 + gitAUTOINC + 3ffece9bf1 | |
orc | 0.4.25 | |
os-release | 1.0 | |
packagegroup-atlas-qt5 | 1.0 | |
packagegroup-atlas-sxb | 1.0 | |
packagegroup-base | 1.0 | |
packagegroup-core-boot | 1.0 | |
packagegroup-core-eclipse-debug | 1.0 | |
packagegroup-core-nfs | 1.0 | |
packagegroup-core-ssh-openssh | 1.0 | |
packagegroup-px2it | 1.0 | |
parted | 3.2 | |
perl | 5.22.1 | |
pm-utils | 1.4.1 | |
poco | 1.9.0 | |
pointercal | 0.0 | |
popt | 1.16 | |
procps | 3.3.12 | |
protobuf | 2.6.1 + gitAUTOINC + bba83652e1 | |
python | 2.7.12 | |
qtbase | 5.7.1 + gitAUTOINC + a55f36211e | |
qtdeclarative | 5.7.1 + gitAUTOINC + 2a992040e2 | |
qtlocation | 5.7.1 + gitAUTOINC + de5be121d8 | |
qtsensors | 5.7.1 + gitAUTOINC + 5a57beaaa5 | |
qtwebkit | 5.7.1 + gitAUTOINC + 76e2732f01 | |
qtwebsockets | 5.7.1 + gitAUTOINC + 60cede232a | |
qtxmlpatterns | 5.7.1 + gitAUTOINC + 89dbcc4f80 | |
rauc | 0.4 | |
readline | 6.3 | |
rpcbind | 0.2.3 | |
rsync | 3.1.2 | |
rsyslog | 8.22.0 | |
run-postinsts | 1.0 | |
shadow | 4.2.1 | |
shadow-security | 4.2.1 | |
sqlite3 | 3.14.1 |
|
squashfs-tools | 5.7.1 + gitrAUTOINC + 9c1db6d13a |
|
st-load | 1.0 |
|
stm32flash | git | |
strace | 4.13 | |
sysfsutils | 2.1.0 | |
sysvinit-bootlogd | 2.88dsf | |
tcf-agent | 1.4.0 + gitAUTOINC + 2dddd5f440 | |
tcpdump | 4.7.4 | |
tcp-wrappers | 7.6 | |
tslib | 1.1 | |
tzdata | 2016i |
|
u-boot-atlas | 2017.09 | |
u-boot-fw-utils | 2017.09 | |
unzip | 6.0 | |
usbutils | 008 | |
util-linux | 2.28.1 | |
wireless-tools | 30.pre9 | |
wpa-supplicant | 2.5 | |
xerces-c | 2.7.0 | |
xz | 5.2.2 |
|
yaml-cpp | 0.6.2 | |
zip | 3.0 | |
zlib | 1.2.8 |