Teilt dem Benutzer mit, ob das Ereignis über die Seite „Ereigniskonfiguration“ konfiguriert werden kann.
Power Focus HC (3.9)
Software
Einleitung
In diesem Abschnitt finden Sie grundlegende Informationen zum Produkt sowie die in den Themen angewandten Formatierungskonventionen.
Allgemeine Beschreibung
Das Smart Tensioning System ist eine rückverfolgbare und geführte Schraubenspannlösung, die aus drei Hauptkomponenten besteht. Der Smart Tensioner (STT) verfügt über integrierte Elektronik und Sensoren, welche dem Benutzer unmittelbares Feedback liefern. Die Handsteuerung (PFHC) ist das Gehirn des Systems und steuert den Prozess, wie beispielsweise: das Scannen mit dem integrierten Barcode-Lesegerät, der Betrieb des Antriebsaggregats und die Erfassung von Daten. Das gesamte System funktioniert als geschlossener Regelkreis, in dem alle Befehle von der Handsteuerung ausgehen. Das Antriebsaggregat ist mit unserem Hochleistungsmotor und und -elektronik ausgestattet.
Eigenschaften
Datenerfassung
Druck-, Drehmoment- und Winkelsensoren
LEDs am Werkzeug
Integrierte Elektronik
Werkzeug- und Antriebsaggregats-Erkennung
Digitaler Zykluszähler
Intuitive MMS
Vorteile
Vollständige Rückverfolgbarkeit des Prozesses
Verkürzte Prozesszeiten
Unmittelbares Feedback bei jedem Schritt
Minimaler Bedarf von Peripheriegeräten
Prozessgenauigkeit
Konventionen
Zur Verbesserung des Benutzerverständnisses werden in diesem Dokument bestimmte Formatierungen verwendet. Die verwendeten Formatierungen sind nachfolgend aufgeführt.
Element | Schreibweise | Beschreibung | Ausgabe |
---|---|---|---|
Allgemeine Hervorhebung | Im Arbeitsbereich Programm. | Zur Hervorhebung oder Markierung von bestimmten Textelementen | Text in Fettschrift |
Elemente der grafischen Benutzeroberfläche (GUI) | Wählen Sie die Schaltfläche Funktion aus. | Alle Verweise zu Elementen auf dem GUI-Bildschirm (z.B. Befehlsschaltflächen, Symbolnamen und Feldnamen). | Text in Fettschrift |
Grafische Benutzeroberfläche (GUI) Pfad > | Im Allgemeinen oben auf der GUI. | Navigationshilfe, mit der Sie den Überblick über Ihre Position innerhalb der GUI behalten können. | Zum Beispiel: Steuerung > Programm > Bearbeiten |
Benutzereingabe | Geben Sie eine Beschreibung für das Programm ein. | Beliebige Texteingabe durch den Benutzer. | Text in Fettschrift |
Dateinamen | Geben Sie einen Dateinamen für den Export ein. | Dateien, die entweder aus dem System exportiert oder in das System importiert werden. | Text in Fettschrift Kursiv |
Namen von Variablen und Parametern | Geben Sie einen Namen für den Export ein. | Namen von Variablen und Parametern (keine Werte). | Text in Kursivschrift |
Werte von Variablen und Parametern | Geben Sie einen WERT für den Export ein. | Werte von Variablen und Parametern. | Text in GROSSBUCHSTABEN |
Systemausgabe | Client.Domain.Models.ExportImportConfiguration | Jede Textausgabe durch das System. | Text in Monospace |
Externe Links | Links zu externen Seiten, die mit dem Dokument oder dem Themeninhalt verbundene Informationen enthalten. Dies können sein:
| Auswählbarer Text in externen Seiten | |
Interne Dokumentenverknüpfungen |
Diese Links werden, wenn sie verfügbar sind, unter dem Text angezeigt. | Auswählbarer Text in internen Inhalten |
Datenschutz-Grundverordnung (DSGVO)
Dieses Produkt bietet die Möglichkeit, personenbezogene Informationen wie den Systembenutzernamen, die Rolle und die IP-Adresse zu verarbeiten. Der Zweck dieser Verarbeitungsfähigkeit könnte darin bestehen, die Qualitätskontrolle durch Rückverfolgbarkeit und geeignetes Zugriffsmanagement zu verbessern.
Wenn Sie sich dazu entschließen, personenbezogene Daten zu verarbeiten, müssen Sie die einschlägigen Datenschutzbestimmungen kennen und einhalten, einschließlich der DSGVO sowie anderer in der EU anwendbarer Gesetze, Richtlinien und Vorschriften. Atlas Copo kann in keiner Weise für die Verwendung des Produkts durch Sie haftbar gemacht werden.
Verpflichtungen und Warnungen
Haftung
Viele Ereignisse in der Arbeitsumgebung können sich auf die Verschraubung auswirken und bedürfen einer Validierung der Ergebnisse. In Übereinstimmung mit den geltenden Standards und/oder Vorschriften sind das installierte Drehmoment und die Drehrichtung nach einem Ereignis zu überprüfen, das sich auf die Verschraubung auswirken kann. Zu solchen Ereignissen zählen unter anderem:
Erstinstallation des Werkzeugsystems
Änderung von Chargen, Bolzen, Schrauben, Werkzeugen, Software, Konfiguration oder Umgebung
Änderung von Druckluft- oder Elektroanschlüssen
Änderung von Linienergonomie, Prozessen, Qualitätsverfahren und -praktiken
Bedienerwechsel
Andere Änderungen, die sich auf das Ergebnis der Verschraubung auswirken
Die Prüfung muss:
Sicherstellen, dass die gemeinsamen Bedingungen sich nicht aufgrund von Ereignissen geändert haben.
Nach der Erstinstallation, Wartung oder Reparatur der Anlage erfolgen.
Mindestens einmal pro Schicht oder in einem anderen geeigneten Intervall erfolgen.
Warnungen
Über das Benutzerhandbuch
In diesem Benutzerhandbuch wird die Einrichtung und Konfiguration der PFHC beschrieben.
Es richtet sich an alle, die die PFHC bedienen oder warten.
Revisionsverlauf
Versionsnummer | Revisionsdatum | Revisionsbeschreibung |
---|---|---|
item | item | none |
3,9 | 01/2023 | NEUER Inhalt: AKTUALISIERTER Inhalt: Exportierte Informationen und Dateiformat Arbeiten mit der Registerkarte Einstellungen |
3,8 | 09/2022 | Erste offizielle Version des Benutzerhandbuchs für die Power Focus HC. |
Voraussetzungen
Jeder, der mehr über PFHC erfahren möchte, kann von diesem Benutzerhandbuch Nutzen ziehen.
Um ein vollständiges Verständnis sämtlicher in diesem Benutzerhandbuch beschriebenen technischen Aspekte sicherzustellen, empfehlen wir Folgendes:
Kenntnisse über Verschraubungsverfahren
Erfahrung im Umgang mit vorherigen Power Focus Versionen
Systemüberblick
Softwarestruktur
Menü-Übersicht
Auf die Web-Benutzeroberfläche wird über den externen Computer zugegriffen; sie bietet mehrere Menüs für die folgenden Aktionen:
Konfiguration von Spann- und Hardwarezubehör
Durchführung der Werkzeugwartung
Verwaltung der Software
Anzeige von Berichten
Die Steuerungs-Benutzeroberfläche, die auf dem Bildschirm der Handsteuerung angezeigt wird, dient zum Betrieb und zur Überwachung des Systems.
Web-GUI
Registerkarte Spannen
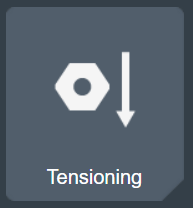
In der Registerkarte Spannen sind die in der Handsteuerung gespeicherten Spannprogramme aufgelistet, die für die einzelnen Spannvorgänge verfügbar sind.
Spannkonfigurationen werden in der Registerkarte Spannen beschrieben.
Registerkarte Konfiguration
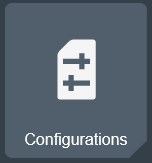
In der Registerkarte Konfigurationen wird eine Liste mit Konfigurationen angezeigt. Allgemeine Konfigurationen sind unabhängig von der Art des verbundenen Spanners und der hydraulischen Pumpe.
Registerkarte Spanner-Steuerung
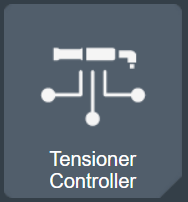
In der Registerkarte Steuerung werden Hardware- und Softwarekomponenten aufgelistet.
Die in der Handsteuerung gespeicherten und verwendeten Softwareversionen werden aufgelistet und können aktualisiert werden.
Sie können die Einstellungen auch in die Handsteuerung importieren bzw. aus dieser exportieren.
Registerkarte Berichte
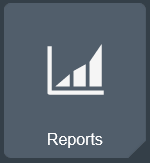
In der Registerkarte Berichte werden die Spannergebnisse und Ereignisse aufgeführt.
Registerkarte Einstellungen
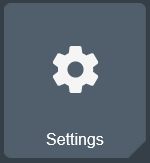
In der Registerkarte Einstellungen können die spezifischen Einstellungen der Handsteuerung, wie zum Beispiel Uhrzeit und Datum, Pin-Code, Ereignisse oder Drahtlosnetzwerk, festgelegt werden.
Registerkarte Hilfe
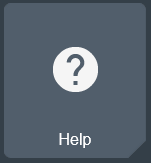
In der Registerkarte Hilfe finden Sie nützliche Angaben zur Handsteuerung.
Steuerungsoberfläche
Registerkarte Aufgaben
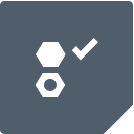
Auf der Registerkarte Aufgaben sind die in der Handsteuerung gespeicherten Spannprogramme aufgelistet, die für einzelne Spannvorgänge zur Verfügung stehen. Spannkonfigurationen werden auf der Registerkarte Spannen in der Web-GUI beschrieben.
Registerkarte Berichte
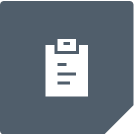
Auf der Registerkarte Berichte werden die Spannergebnisse aufgeführt; zusätzlich kann der Bericht generiert und auf einem USB-Stick gespeichert werden.
Registerkarte Steuerungsinformationen
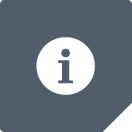
In der Registerkarte Steuerungsinformationen werden die Gerätedaten der Handsteuerung aufgeführt, wie etwa Seriennummer, IP-Adresse und Softwareversion.
Registerkarte Einstellungen
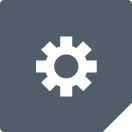
Auf der Registerkarte Einstellungen können das Datum und die Uhrzeit festgelegt und Ergebnisse gelöscht werden.
Registerkarte Angeschlossene Geräte
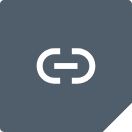
Die Registerkarte Angeschlossene Geräte zeigt den Verbindungsstatus des Spanners und der Pumpe an, die mit der Handsteuerung verbunden sind.
Hier werden Daten zum verbundenen Spanner und der Pumpe angezeigt, wie etwa Seriennummer und Softwareversion. Zudem finden Sie hier den aktuellen Stand des Zugstangenzählers des Spanners.
Betrieb und Umgang
Web-GUI
Schaltflächen und Symbole auf der GUI
Schaltfläche | Bezeichnung | Beschreibung |
---|---|---|
![]() | Hinzufügen | Hinzufügung eines weiteren Elements. |
![]() | Entfernen | Entfernen eines Elements. |
Auslassen | Bearbeiten eines Elements. | |
![]() | Zurück | Zurück zur vorherigen Ansicht. |
![]() ![]() | Scrollen auf Scrollen ab | Den Inhalt einer Liste, die über die Bildschirmlänge hinaus geht, verschieben |
![]() ![]() | Maximieren Minimieren | Einen Abschnitt mit Parametern maximieren bzw. minimieren |
![]() ![]() | Zurück (zum Start) (in einer Liste) Zurück (in einer Liste) | Zurück zwischen den Seiten einer Liste. |
![]() ![]() | Vorwärts (zum Ende) (in einer Liste) Vorwärts (in einer Liste) | Vorwärts zwischen den Seiten einer Liste. |
![]() | Schließen | Zum Schließen des Fensters drücken |
![]() | Hinweis | Symbol, das darauf hinweist, dass ein Parameter falsch konfiguriert wurde. |
![]() | WARNUNG | Warnzeichen zum Hinweis auf Verletzungsgefahr. |
![]() | Programm validieren | Drücken, um zu prüfen, ob ein Programm gültig ist. |
![]() | Handbuch herunterladen | Drücken, um ein Handbuch herunterzuladen. |
![]() | Startbildschirm | Gehen Sie zur Startseite. |
![]() | Zu Ergebnis | Gehen Sie zur Ansicht „Live-Ergebnisse“. |
Steuerungsoberfläche
Schaltflächen und Symbole auf der GUI
Die Tasten auf der Tastatur der Handsteuerung sind kontextsensitiv. Aktive Tasten werden durch die Symbole auf der GUI der Steuerung dargestellt. Diese Symbole zeigen die aktuelle Funktionalität der Tastaturtasten an. Auf der Startseite werden die aktiven Tasten beispielsweise durch die folgenden Symbole repräsentiert, siehe folgende Abbildung:
Vorherige (links)
Weiter (rechts)
Nach oben
Nach unten
Eingabe-Taste
Verwenden Sie zum Navigieren die Tasten Links, Rechts, Oben und Unten auf der Tastatur. Verwenden Sie die Eingabetaste in der Mitte, um ein Menü aufzurufen oder eine Auswahl zu bestätigen.
Informationen zu allen Symbolen auf der Steuerung-GUI finden Sie in der folgenden Tabelle.
1 | Vorherige |
2 | Weiter |
3 | Nach oben |
4 | Nach unten |
5 | Eingabe (Auswahl) |
6 | WLAN- und ToolsNet-Verbindungsstatus |
Schaltfläche | Bezeichnung | Beschreibung |
---|---|---|
![]() | Zurück | Zur vorherigen Ansicht zurückkehren |
![]() | Vorwärts | Fortfahren. |
![]() | Nach oben Nach unten | In einer Liste nach oben oder unten bewegen. |
![]() | Eingabe-Taste | Bestätigt die Auswahl. |
![]() ![]() | Mehr | Zusätzliche Informationen oder Aktionen. |
![]() | Weiter | Zur nächsten Ansicht wechseln. |
![]() | Vorherige | Zur vorherigen Ansicht wechseln. |
![]() | WLAN-Verbindungsstatus | Mit WLAN verbunden |
![]() | WLAN-Verbindungsstatus | Nicht mit WLAN verbunden |
![]() | ToolsNet-Verbindungsstatus | Mit ToolsNet verbunden |
![]() | ToolsNet-Verbindungsstatus | Nicht mit ToolsNet verbunden |
LED-Statusanzeige
Die LED-Matrix an den Spannern wird während des Spannvorgangs auf der GUI der Handsteuerung nachgeahmt. Weitere Informationen zur LED-Statusanzeige finden Sie in der Produktanleitung des STT-Spanners.
Schnellstartanleitung
Um einen besseren Überblick über das System zu bieten, enthält dieser Abschnitt eine Schnellanleitung zu den ersten grundlegenden Schritten für die Arbeit mit dem Smart Tensioning System und der Power Focus Software.

Der Abschnitt erklärt nicht jede einzelne Funktion des Systems, sondern konzentriert sich lediglich auf die wichtigsten.
Für den Systemstart müssen die Pumpe und der Spanner mit der Handsteuerung verbunden werden, bevor die Hydraulikpumpe mithilfe des Netzschalters eingeschaltet wird.
Fahren Sie den Spanner direkt auf die Oberseite der Schraube herunter. Stellen Sie sicher, dass der Aufsatz innerhalb des Spanners korrekt auf der Mutter aufsitzt, indem Sie den Knickschlüssel bewegen. Achten Sie auf das Klickgeräusch. Überprüfen Sie, ob der Spanner sich dreht, wenn der Schlüssel Kraft auf die Mutter aufwendet.
Wenn das Symbol Aufgaben auf der Handsteuerung aktiv ist, führen Sie den Manuellen Modus mithilfe der Tastatur auf der Handsteuerung aus.
Legen Sie den Solldruck auf einen niedrigen Wert fest, zum Beispiel 500 bar, und drücken Sie anschließend die Taste zur Druckbeaufschlagung.
Wenn der Motor läuft, jedoch kein Druckanstieg erfolgt, ist eines der am häufigsten auftretenden Probleme, dass der Motor rückwärts läuft. Schalten Sie das System ab, kehren Sie die Phase des Stromanschlusses um und versuchen Sie es erneut.
Wenn das System druckbeaufschlagt wurde, bewegen Sie den Knickschlüssel, damit die Messwerte für Winkel und Drehmoment aktualisiert werden.
Nähere Informationen zum Start des Smart Tensioning Systems finden Sie in der Smart Tensioning System Betriebsanleitung.
Installation und Upgrade
In diesem Abschnitt finden Sie Informationen zur Unterstützung der Erstinstallation des Produkts sowie zu Versionsaktualisierungen.
Webbrowser-Anforderungen
Verwenden Sie für eine optimale Performance einen Webbrowser, der für die Ausführung von JavaScript geeignet ist, und aktivieren Sie Browser-Caching.
Die Software kann in den folgenden Webbrowsern ausgeführt werden:
Google Chrome 70 oder höher
Microsoft Edge 79 oder höher
Firefox 63 oder höher
Konfiguration
In diesem Abschnitt finden Sie ausführliche Informationen zum Erstellen, Ändern und Überprüfen von Produkteinstellungen.
Verbindung zur Benutzeroberfläche für die PFHC-Konfiguration
Verwenden Sie für eine optimale Performance einen Webbrowser, der für die Ausführung von JavaScript geeignet ist, und aktivieren Sie Browser-Caching.
Öffnen Sie die Abdeckung am USB-Anschluss der Handsteuerung.
Verbinden Sie einen PC mit dem USB-C-Anschluss an der Handsteuerung. Um sicherzustellen, dass der PC genügend Leistung zum Betrieb der Handsteuerung abgibt, verwenden Sie USB-3.0-Anschlüsse.
Um auf die Konfigurations-GUI zuzugreifen, geben Sie die folgende Adresse in Ihren Browser ein: http://169.254.1.1/config.html.
Weitere Informationen finden Sie im Abschnitt Webbrowser-Anforderungen.
Web-GUI
Live-Ergebnisse
Öffnen Sie die Live-Ergebnisansicht, indem Sie in der unteren linken Ecke auf das Symbol Ergebnisse klicken, wenn dieses angezeigt wird.
Es werden Status, Drehmoment und Winkel angezeigt.
Klicken Sie auf das Verbindungssymbol in der oberen rechten Ecke der Live-Ergebnisansicht, um die Ansicht Protokollstatus zu öffnen.
Arbeiten mit der Registerkarte Spannen
Dieser Abschnitt beschreibt die mehrstufige Spannstrategie sowie die Erstellung eines Spannprogramms.
Öffnen Sie auf dem Startbildschirm die Registerkarte Spannen und wählen Sie anschließend Multistep-Programmbibliothek aus.
Benutzeroberfläche für mehrstufige Konfiguration
Die Benutzeroberfläche für die Konfiguration eines mehrstufigen Programms besteht aus den folgenden Hauptbereichen:
Im linken Fenster, unterhalb der Registerkarte Eigenschaften, befinden sich die Allgemeinen Einstellungen des mehrstufigen Spannprogramms, welche den Programmnamen beinhalten.
Im linken Fenster enthält die Registerkarte Programm ein Dropdown-Menü, das Stufen enthält.
Klicken Sie zur Erstellung eines Multistep-Programms auf Stufen und ziehen Sie anschließend das entsprechende Stufensymbol – Spannen oder Spann-Dienst – aus der Liste in den Spannbereich. Legen Sie das ausgewählte Stufensymbol zwischen dem Anfang und dem Ende des Programms ab.
Das Programm für Manuelles Spannen wird automatisch durch die Handsteuerung erstellt und kann nach Wunsch bearbeitet werden.
Den Hauptbereich der Benutzeroberfläche nimmt der Spannbereich ein. Dies ist der Bereich, der alle Stufen des Spannprogramms beinhaltet.
Manuelles Standardprogramm
Wählen Sie in der Multistep-Programmbibliothek Manuelles Standardprogramm aus. Das Manuelle Standardprogramm wird automatisch erstellt. Das manuelle Programm kann mit allen Größen und Arten von Spannwerkzeugen ausgeführt werden.
Das manuelle Programm enthält drei Einstellungen zur Steuerung des Verhaltens des manuellen Modus. Der Name des manuellen Programms kann unter Allgemeine Einstellungen > Eigenschaften bearbeitet werden.
Allgemeine Einstellungen
Die Allgemeinen Einstellungen beinhalten das Feld Name.
Wählen Sie ein Programm aus und öffnen Sie die Registerkarte Eigenschaften, um die Allgemeinen Einstellungen durch Eingabe des Namens in das Freitext-Eingabefeld zu bearbeiten.
Der gewählte Programmname wird auf der GUI der Steuerung in den unter den verschiedenen Aufgabentypen in der Registerkarte Aufgaben aufgeführten Programmen angezeigt.
Parameter des manuellen Modus
Klicken Sie im Manuellen Standardprogramm im Bereich Spannen auf das Symbol Manuelles Spannen, um die folgenden Parameter zu bearbeiten:
Bezeichnung
Standardmäßiger manueller Hydraulikdruck (bar)
Max. System-Hydraulikdruck (bar)
Parameter | Vorgegeben | Beschreibung | Kommentar |
---|---|---|---|
Bezeichnung | Stufe des manuellen Modus | Stringname der Stufe | Nicht verwendet, da im manuellen Modus keine Ergebnisse generiert werden. |
Standardmäßiger manueller Hydraulikdruck (bar) | 1000 | Wird zum Befüllen des eingestellten Druckfensters im manuellen Modus verwendet, wenn der manuelle Modus erstmals nach einem Systemstart ausgeführt wird. | Der standardmäßige manuelle Druck stellt sicher, dass der Bediener keine vorherige Druckeinstellung aus einer früheren Nutzung des manuellen Modus erneut verwendet. Legen Sie den Standardruck auf einen für Ihre Anwendung geeigneten Wert fest. Sobald der manuelle Modus verwendet wurde, nimmt das System an, dass dieser Druck für den laufenden Betrieb geeignet ist. Der letzte verwendete Druck wird als Druck für den manuellen Modus verwendet, bis das System abgeschaltet wird. Der Solldruckwert kann jederzeit über die Steuerungs-GUI geändert werden. |
Max. System-Hydraulikdruck | 1980 | Der höchste Solldruckwert, der bei der Verwendung dieser Konfiguration zulässig ist. | Das System verwendet den niedrigsten Maximaldruck seiner angeschlossenen Geräte. Falls eines der angeschlossenen Geräte über einen niedrigeren Maximaldruck verfügt, wird die Druckbeaufschlagung bei diesem Druckwert angehalten. |
Spannprogramm
Wählen Sie auf dem Startbildschirm die Registerkarte Spannen aus. Multistep-Programmbibliothek wird automatisch ausgewählt.
Um ein Spannprogramm hinzuzufügen, klicken Sie auf das Plus-Symbol oberhalb der Programmliste, um die Registerkarte Programm zu öffnen, und klicken Sie anschließend auf Stufen.
Falls bereits ein Spannprogramm verfügbar ist, wählen Sie dieses aus, um es zu bearbeiten.
Verschieben Sie die Spannstufen in den Spannbereich.

Stufen können nur zwischen dem Start- und Endpunkt des Programms platziert werden.
Die Schaltflächen Verschraubungsprogramm löschen und Verschraubungsprogramm kopieren zum Löschen und Kopieren des Programms finden Sie in der unteren rechten Ecke.

Ein Spannsystem verwendet lediglich eine Stufe pro Konfiguration.
Änderungen an den Verschraubungsprogrammen in einem der Abschnitte müssen aktiv übernommen werden, indem die Schaltfläche „Anwenden“ rechts unten in der Benutzeroberfläche angeklickt wird. Alternativ können Änderungen rückgängig gemacht werden, indem Sie auf die Schaltfläche „Rückgängig“ an der gleichen Stelle klicken.
Wenn der Abschnitt, in dem Änderungen vorgenommen wurden, verlassen wird (mit der Schaltfläche Zurück, Startseite oder Ergebnis), wird dem Benutzer ein Warnfenster angezeigt, in dem die Änderungen auch übernommen oder rückgängig gemacht werden können. Der Benutzer kann nicht fortfahren, ohne die Änderungen zu übernehmen oder rückgängig zu machen.
Funktion | Beschreibung | |
---|---|---|
Start- und Endpunkte | ![]() | Start- und Endpunkte des mehrstufigen Programms. Alle Stufen müssen zwischen diesen beiden Punkten platziert werden. |
Anzeigen der Stufeneigenschaften | ![]() | Klicken Sie auf die Stufe, damit deren Eigenschaften angezeigt werden. |
Schließen der Stufeneigenschaften | ![]() | Klicken Sie auf einen beliebigen Punkt im Verschraubungsbereich, um das Einstellungsmenü zu schließen. |
Einen Schritt löschen | ![]() | Klicken Sie auf die Stufeneigenschaften und anschließend am Ende des Menüs auf Löschen. |
Stufenfehler | ![]() | Wenn es bei einer Stufe zu einem Validierungsfehler kommt, wird diese Stufe gekennzeichnet. Beachten Sie, dass der Parameter, der den Fehler verursacht, bei geöffneten Stufeneigenschaften ebenfalls gekennzeichnet wird. Klicken Sie auf die rote Kennzeichnung, um weitere Informationen zum Fehler zu erhalten. |
Verbotene Platzierung | ![]() | Wenn eine bestimmte Platzierung einer Stufe nicht zulässig ist, wird das Platzhaltersymbol nicht angezeigt. |
Spannparameter
Klicken Sie auf der Registerkarte Programm auf ein Spannelement, um dieses zu öffnen und die Parameter zu bearbeiten. Die Spannparameter sind in der folgenden Tabelle aufgeführt. Siehe auch Abbildung des Spannvorgangs im Abschnitt Spannvorgang.
Parameter | Standardwert | Einheit | Beschreibung | Kommentar | |
---|---|---|---|---|---|
a Alle Standardwerte sind auf das Einschrauben einer M36-Schraube mit einem Minimalwinkel von 40 Grad und ohne Maximalwinkel abgestimmt. b Die Parameter für die Rotationserkennung legen das erwartete Spiel innerhalb der Kette Schlüssel-Steckschlüssel-Getriebe fest. Erfahrungsgemäß kann dieses hauptsächlich aufgrund der Schraubengeometrie stark abweichen – selbst wenn das Werkzeug an derselben Schraube aufgesetzt wird, der Steckschlüssel sich jedoch an anderen Seiten der Mutter ausrichtet. c Die Parameter für die Rotationserkennung legen das erwartete Spiel innerhalb der Kette Schlüssel-Steckschlüssel-Getriebe fest. Erfahrungsgemäß kann dieses hauptsächlich aufgrund der Schraubengeometrie stark abweichen – selbst wenn das Werkzeug an derselben Schraube aufgesetzt wird, der Steckschlüssel sich jedoch an anderen Seiten der Mutter ausrichtet. | |||||
Bezeichnung |
| Benutzername der Stufenkonfiguration, in der XML-Berichtsdatei hinterlegt und in den Stufenergebnissen angegeben. | |||
Schraubengröße | M36 a | mm | Die Größe der Schraube für die vorgesehene Konfiguration. Die Schraubengröße wird mit dem angeschlossenen Werkzeug verglichen und, falls diese nicht übereinstimmt, das Ereignis Ungültige Konfiguration ausgegeben. | Die Steuerungs-GUI filtert die Konfigurationen heraus, die zu den angeschlossenen Werkzeugen passen. Für andere Werkzeuggrößen erstellte Konfigurationen werden in der Liste unter Aufgaben > Montage oder Aufgaben > Gruppenmontage nicht angezeigt. | |
Spannertyp | Flanschschraube | Der Spannertyp muss dem angeschlossenen Spanner entsprechen. Der String wird mit dem String zur Identifikation der Art des Spanners verglichen, welcher dem Spanner bei seiner Herstellung einprogrammiert wird. Beim Vergleich des Strings mit demjenigen im Spanner wird die Groß- und Kleinschreibung berücksichtigt. | Die Steuerungs-GUI filtert die Konfigurationen heraus, die zu den angeschlossenen Werkzeugen passen. Für andere Spannertypen erstellte Konfigurationen werden in der Liste unter Aufgaben > Montage oder Aufgaben > Gruppenmontage nicht angezeigt. | ||
Min. Muttern-Rotationswinkel | 40 | Grad | Der minimale Muttern-Rotationswinkel für einen IO-Spannvorgang. | Das Feld kann leer gelassen werden, wenn für den Spannvorgang kein minimaler Anzugswinkel benötigt wird. | |
Max. Muttern-Rotationswinkel | Grad | Der maximale Muttern-Rotationswinkel für einen IO-Spannvorgang. | Das Feld kann leer gelassen werden, wenn der maximale Anzugswinkel für den Spannvorgang nicht entscheidend ist. | ||
Winkelbestätigung | Letzten Winkel bestätigen | Steuert das Verhalten der Winkelmessung beim erneuten Spannen nach einem NIO-Ergebnis. Die Auswahloptionen sind:
| Bei Konfigurationen, die einen Maximalwinkel erfordern, wird nur die Verwendung des letzten Winkels empfohlen. Verwenden Sie bei Konfigurationen, die einen Minimalwinkel erfordern, die Winkelzusammenfassung, um die Summe aller Versuche für IO/NIO-Ergebnisse zu berücksichtigen. Überprüfen Sie bei Konfigurationen, die einen Winkelbereich festlegen, welches Verhalten zur Aufgabe passt, für welche die Konfiguration ausgelegt ist. | ||
Klemmkraftschätzung verwenden | Ein | Regelt, welche Klemmkraftschätzung für das Ergebnis verwendet wird. Ein -> Klemmkraftschätzung wird verwendet: Spannkraft – Geschätzte durchschnittliche anfängliche Senkung Aus -> Klemmkraft wird gemäß der Gleichung für den Lastübertragungsfaktor berechnet: Spannkraft / (1,01 + (Schraubendurchmesser / Klemmlänge)) | Die Gleichung für den Lastübertragungsfaktor (LTF) von Atlas Copco (AC), die für das STS eingesetzt wird, ist nur zur Verwendung bei „Flansch“-Verbindungen vorgesehen. NICHT für Fundamentverbindungen verwenden. | ||
Klemmlänge | mm | Die Höhe des Flanschs, also der Abstand zwischen den Muttern auf beiden Seiten des Flanschs. Aktiv, wenn: Klemmkraftschätzung verwenden „Aus“ ist. | Sichtbar, wenn Klemmkraftschätzung verwenden „Aus“ ist. | ||
Geschätzte durchschnittliche anfängliche Senkung | 99 | kN | Ein Schätzwert des durchschnittlichen Kraftverlusts, wenn der Druck abgelassen wird. Aktiv, wenn: Klemmkraftschätzung verwenden „An“ ist. | Sichtbar, wenn Klemmkraftschätzung verwenden „An“ ist. Wird bei der Erstellung von XML-Berichten verwendet. Der Wert hängt von der Größe des Spanners und der Art des Flanschs ab. | |
Geschätzte maximale anfängliche Senkung | 155 | kN | Ein Schätzwert des maximalen Kraftverlusts, wenn der Druck abgelassen wird. Aktiv, wenn: Klemmkraftschätzung verwenden „An“ ist. | Sichtbar, wenn Klemmkraftschätzung verwenden „An“ ist. Wird bei der Erstellung von XML-Berichten verwendet. Der Wert hängt von der Größe des Spanners und der Art des Flanschs ab. | |
Mindestens erforderliche durchschnittliche Klemmkraft | 510 | kN | Die minimale durchschnittliche Klemmkraft für alle Schrauben am Flansch, die im Abschnitt Flanschüberblick des XML-Berichts enthalten sind. Aktiv, wenn: Klemmkraftschätzung verwenden „An“ ist. | Sichtbar, wenn Klemmkraftschätzung verwenden „An“ ist. Wird bei der Erstellung von XML-Berichten verwendet. Der Wert hängt von der Größe des Spanners und der Art des Flanschs ab. | |
Berichtstyp Gruppenaufgabe | Allgemein | Regelt die Erstellung des Flanschüberblicks in XML-Berichten:
| Angepasst für Vestas‘ Anforderungen an XML-Berichte: Erste Runde, Zweite Runde, Benutzer Allgemein für Wartungsarbeiten. | ||
Kraft für Winkelsensor-Reset | 100 | kN | Die Kraft, bei der die Winkelmessreferenz für 0 Grad festgelegt wird. | Die erwarteten Winkel werden in Abhängigkeit vom Kraftanstieg von der Kraft für den Winkelsensor-Reset bis zum Minimalen Schraubenspanndruck berechnet. Dies entspricht je nach Größe des Spanners verschiedenen Drücken, siehe Tabelle im Abschnitt Drücke für verschiedene Spannergrößen. Je größer der Spanner ist, desto höher muss die Kraft für den Winkelreset aufgrund von Problemen bei der Kontrolle niedriger Drücke beim Schritt Installationsprüfung eingestellt werden. Dies ist notwendig, um eine Überschreitung des Installationsprüfungs-Hydraulikdrucks um mehr als das Druckäquivalent der Kraft für den Winkelsensor-Reset zu vermeiden. | |
Minimaler Schraubenspanndruck | 1900 | Bar | Der Mindestdruck für ein IO-Spannergebnis. | Die Druckregelung im System legt einen Sollwert fest, der höher als der Minimale Schraubenspanndruck ist, um Druckabfälle zu vermeiden, die zu einem NIO-Ergebnis führen. Siehe Abbildung im Abschnitt Hydraulikdruck-Zielfenster. | |
Max. System-Hydraulikdruck | 1980 | Bar | Der höchste Druck, den die Druckregelung in der Handsteuerung für diese Konfiguration zulässt. | Der tatsächliche Maximaldruck ist der niedrigste der Maximaldrücke an der Pumpe und dem Spanner und zudem der Max. System-Hydraulikdruck der Konfiguration. | |
Minimale Schraubenspannkraft | 698 | kN | Kraftäquivalent des Parameters Minimaler Schraubenspanndruck. | Der Wert wird manuell aus dem Schraubendruck berechnet. Dieser Wert wird in die XML-Berichtsdateien aufgenommen, jedoch nicht von der Software der Handsteuerung verwendet. | |
Installationsprüfungs-Drehmoment | 20 | Nm | Das für eine bestätigte Installationsprüfung benötigte Drehmoment. | ||
Installationsprüfungs-Drehmomentdauer | 1,0 | S | Die Dauer, für welche das Installationsprüfungs-Drehmoment für eine bestätigte Installationsprüfung anliegen muss. | ||
Verschraubungs-Solldrehmoment | 100 | Nm | Das für eine bestätigte Verschraubung der Mutter benötigte Drehmoment. | ||
Verschraubungs-Drehmomentdauer | 1,0 | S | Die Dauer, für welche das Verschraubungs-Solldrehmoment für eine bestätigte Verschraubung der Mutter anliegen muss. | ||
Erkennungswinkel für unerwartete Drehung im Uhrzeigersinn bei der Verschraubung | 5 | Grad | Die maximal zulässige Veränderung des Muttern-Rotationswinkels im Uhrzeigersinn, während der Prozess auf den Druckablass wartet. | Um die Gefahr einer Rotation der Mutter während des Wartens auf den Druckablass zu vermeiden, aktivieren Sie den automatischen Druckablass (siehe Abschnitt Werkzeugkonfiguration). b | |
Erkennungswinkel für unerwartete Drehung gegen den Uhrzeigersinn bei der Verschraubung | 5 | Grad | Die maximal zulässige Veränderung des Muttern-Rotationswinkels gegen den Uhrzeigersinn, während der Prozess auf den Druckablass wartet. | Um die Gefahr einer Rotation der Mutter während des Wartens auf den Druckablass zu vermeiden, aktivieren Sie den automatischen Druckablass (siehe Abschnitt Werkzeugkonfiguration). c | |
Installationsprüfungs-Hydraulikdruck | 20 | Bar | Der Drucksollwert für die Installationsprüfung. | Der Installationsprüfungsdruck fixiert den Spanner während der Installationsprüfung am Flansch. Der Installationsprüfungsdruck darf einschließlich der Überschreitung nicht das Druckäquivalent der Kraft für den Winkelreset übersteigen. | |
Hydraulikdruck-Sollwertfaktor | 1,025 | Der tatsächliche Sollwert für die Druckregelung wird wie folgt berechnet: Minimaler Schraubenspanndruck mal Hydraulikdruck-Sollwertfaktor. Siehe Abbildung im Abschnitt Hydraulikdruck-Zielfenster. | Wenn die Taste für die Druckbeaufschlagung gedrückt gehalten wird, wird im System Druck aufgebaut und dieser innerhalb eines Druckfensters oberhalb des Minimalen Schraubenspanndrucks gehalten. |
Spannvorgang
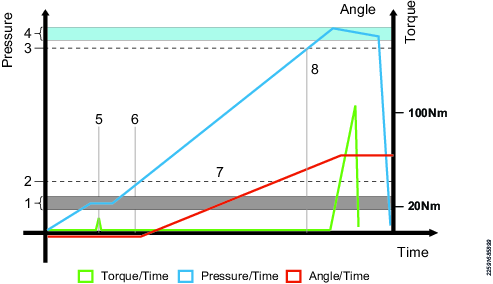
1 | Hydraulikdruck für die Installationsprüfung |
2 | Winkel-Rückstellkraft |
3 | Minimaler Schraubenspanndruck |
4 | Druck-Zielfenster. Bei gedrückter Taste für die Druckbeaufschlagung wird der Druck innerhalb dieses Fensters gehalten |
5 | Installationsprüfung. Legt die Mechanismen in einer bekannten Position fest. Die Mutter dreht sich nicht. Das Spiel für die Ratsche und das Getriebe wird in Verschraubungsrichtung festgelegt. |
6 | Der Winkel-Referenzpunkt wird abgelesen. Die Verschraubungs-Winkelmessung beginnt an diesem Punkt. |
7 | Der Druck wird aufgebaut, die Drehung der Mutter ist IO, es muss jedoch kein hohes Drehmoment angewendet werden. Lassen Sie die Hydraulik die Arbeit übernehmen. |
8 | Minimaler Schraubendruck erreicht. Abschließende Fixierung der Mutter. |

Falls der Druck der Installationsprüfung beim Abschluss über dem der Winkel-Rückstellkraft entsprechenden Druck liegt, kann der Spannvorgang keinen Winkel-Referenzpunkt (6) festlegen.
Daher muss der Parameter Winkel-Rückstellkraft möglicherweise je nach Spannergröße angepasst werden, um einen gewissen Spielraum für Drucküberschreitungen bei der Installationsprüfung sicherzustellen. Der tatsächliche Installationsprüfdruck hängt beispielsweise vom Öltyp und der Öltemperatur ab. Siehe Tabelle im Abschnitt Drücke für verschiedene Spannergrößen.
Drücke für verschiedene Spannergrößen
Die Winkel-Rückstellkraft von 100 kN mit den berechneten Äquivalentdrücken für verschiedene Spannergrößen ist in Tabelle 1 aufgeführt.
Spanner | Winkel-Rückstellkraft (kN) | Winkel-Rückstelldruck (in bar) |
---|---|---|
M36 | 100 | 272 |
M42 | 100 | 198 |
M48 | 100 | 151 |
M56 | 100 | 109 |
M64 | 100 | 83 |
M72 | 100 | 64 |
Die Einstellungen für die Winkel-Rückstellkraft für verschiedene Spanner mit Spielraum für den Installationsprüfdruck sind in Tabelle 2 aufgeführt.
Spanner | Winkel-Rückstellkraft (kN) | Winkel-Rückstelldruck (in bar) |
---|---|---|
M36 | 100 | 272 |
M42 | 100 | 198 |
M48 | 150 | 226 |
M56 | 200 | 219 |
M64 | 200 | 166 |
M72 | 250 | 161 |
Hydraulikdruck-Zielfenster
Die nachfolgende Abbildung zeigt, wie das System den Druck innerhalb des Druck-Zielfensters hält, während die Taste zur Druckbeaufschlagung gedrückt gehalten wird.
Siehe auch die Darstellung des Spannvorgangs im Abschnitt Spannvorgang.
1 | Minimaler Schraubenspanndruck (y) |
2 | Hydraulikdruck-Sollwert (x) |
3 | Hydraulikdruck-Hysterese-Schwellenwert (x-y)/3 |
Berechnung
Hydraulikdruck-Sollwert (x) = Minimaler Schraubenspanndruck (y) × Hydraulikdruck-Sollwertfaktor (k)
Hydraulikdruck-Hysterese-Schwellenwert = 1/3 des Abstands zwischen dem Hydraulikdruck-Sollwert (x) und dem Minimalen Schraubenspanndruck (y).
Die Druckbeaufschlagung beginnt auf diesem Niveau, um den Druck über dem minimalen Stand zu halten.
Schraubendienst-Parameter
Parameter | Standardwert | Einheit | Beschreibung | Kommentar | |
---|---|---|---|---|---|
a Alle Standardwerte sind auf das Einschrauben einer M36-Schraube mit einem Minimalwinkel von 40 Grad und ohne Maximalwinkel abgestimmt. b Die Parameter für die Rotationserkennung legen das erwartete Spiel innerhalb der Kette Schlüssel-Steckschlüssel-Getriebe fest. Erfahrungsgemäß kann dieses hauptsächlich aufgrund der Schraubengeometrie stark abweichen – selbst wenn das Werkzeug an derselben Schraube aufgesetzt wird, der Steckschlüssel sich jedoch an anderen Seiten der Mutter ausrichtet. c Die Parameter für die Rotationserkennung legen das erwartete Spiel innerhalb der Kette Schlüssel-Steckschlüssel-Getriebe fest. Erfahrungsgemäß kann dieses hauptsächlich aufgrund der Schraubengeometrie stark abweichen – selbst wenn das Werkzeug an derselben Schraube aufgesetzt wird, der Steckschlüssel sich jedoch an anderen Seiten der Mutter ausrichtet. | |||||
Bezeichnung | Benutzername der Stufenkonfiguration, in der XML-Berichtsdatei hinterlegt und in den Stufenergebnissen angegeben. | ||||
Schraubengröße | M36 a | mm | Die Größe der Schraube für die für diese vorgesehene Konfiguration. Die Schraubengröße wird mit dem angeschlossenen Werkzeug verglichen und, falls diese nicht übereinstimmt, das Ereignis Ungültige Konfiguration ausgegeben. | Die Steuerungs-GUI filtert die Konfigurationen heraus, die zu den angeschlossenen Werkzeugen passen. Für andere Werkzeuggrößen erstellte Konfigurationen werden in der Liste unter Aufgaben > Schraubenwartung oder Aufgaben > Gruppen-Schraubenwartung nicht angezeigt. | |
Spannertyp | Flanschschraube | Der Spannertyp muss dem angeschlossenen Spanner entsprechen. Der String wird mit dem String zur Identifikation der Art des Spanners verglichen, welcher dem Spanner bei seiner Herstellung einprogrammiert wird. Beim Vergleich des Strings mit demjenigen im Spanner wird die Groß- und Kleinschreibung berücksichtigt. | Die Steuerungs-GUI filtert die Konfigurationen heraus, die zu den angeschlossenen Werkzeugen passen. Für andere Spannertypen erstellte Konfigurationen werden in der Liste unter Aufgaben > Schraubenwartung oder Aufgaben > Gruppen-Schraubenwartung nicht angezeigt. | ||
Max. Delta-Mutternrotation | 13 | Grad | Die maximal zulässige Gesamtrotation der Mutter für den Schraubenwartungsprozess, also die maximale Mutternrotation in Verschraubungsrichtung im Vergleich zum Startpunkt. | Siehe auch Abschnitt Schraubenwartungsprozess. | |
Min. Delta-Mutternrotation | 0 | Grad | Die minimale tatsächliche Mutternrotation, die für den Schraubenwartungsprozess zulässig ist. | Die min. Delta-Mutternrotation und die max. Delta-Mutternrotation bilden einen Bereich akzeptabler Ergebnisse des Schraubvorgangs, z. B. 0,13 – die Mutter muss in ihre ursprüngliche Position zurückkehren (Min. Delta-Mutternrotation = 0), darf jedoch nicht um mehr als 13 Grad in Verschraubungsrichtung rotieren (Max. Delta-Mutternrotation = 13). Ein Wert von < 0 für die Min. Delta-Mutternrotation lässt zu, dass die Schraube nicht vollständig in ihre Ausgangsposition zurückkehrt. | |
Klemmkraftschätzung verwenden | Ein | Regelt, welche Klemmkraftschätzung für das Ergebnis verwendet wird. Ein -> Klemmkraftschätzung wird verwendet: Spannkraft – Geschätzte durchschnittliche anfängliche Senkung Aus -> Klemmkraft wird gemäß der Gleichung für den Lastübertragungsfaktor berechnet: Spannkraft / (1,01 + (Schraubendurchmesser / Klemmlänge)) | Die Gleichung für den Lastübertragungsfaktor (LTF) von Atlas Copco (AC), die für das STS eingesetzt wird, ist nur zur Verwendung bei „Flansch“-Verbindungen vorgesehen. NICHT für Fundamentverbindungen verwenden. | ||
Klemmlänge | mm | Die Höhe des Flanschs, also der Abstand zwischen den Muttern auf beiden Seiten des Flanschs. | |||
Geschätzte durchschnittliche anfängliche Senkung | 99 | kN | Ein Schätzwert des durchschnittlichen Kraftverlusts, wenn der Druck abgelassen wird. Aktiv, wenn: Klemmkraftschätzung verwenden „An“ ist. | Sichtbar, wenn Klemmkraftschätzung verwenden „An“ ist. Wird bei der Erstellung von XML-Berichten verwendet. Der Wert hängt von der Größe des Spanners und der Art des Flanschs ab. | |
Geschätzte maximale anfängliche Senkung | 155 | kN | Ein Schätzwert des maximalen Kraftverlusts, wenn der Druck abgelassen wird. Aktiv, wenn: Klemmkraftschätzung verwenden „An“ ist. | Sichtbar, wenn Klemmkraftschätzung verwenden „An“ ist. Wird bei der Erstellung von XML-Berichten verwendet. Der Wert hängt von der Größe des Spanners und der Art des Flanschs ab. | |
Mindestens erforderliche durchschnittliche Klemmkraft | 510 | kN | Die minimale durchschnittliche Klemmkraft für alle Schrauben am Flansch, die im Abschnitt Flanschüberblick des XML-Berichts enthalten sind. | Wird bei der Erstellung von XML-Berichten verwendet. Der Wert hängt von der Größe des Spanners und der Art des Flanschs ab. | |
Berichtstyp Gruppenaufgabe | Allgemein | Regelt die Erstellung des Flanschüberblicks in XML-Berichten:
| |||
Drehmoment für den Muttern-Löseversuchszähler | 75 | Nm | Der Drehmomentgrenzwert für einen Löseversuch. Wenn die Anzahl der Versuche die Versuchsanzahl für das Lösen einer Mutter übersteigt, fordert der Schraubenwartungsprozess den Benutzer zum erneuten Anziehen der Schraube auf, da diese nicht gelöst werden konnte. | ||
Versuchsanzahl für das Lösen einer Mutter | 3 | Die Anzahl von Versuchen mit einem Drehmoment, das höher als das Drehmoment für den Muttern-Löseversuchszähler ist, bevor der Benutzer zum erneuten Anziehen der Mutter aufgefordert wird, da diese nicht gelöst werden konnte. | |||
Minimaler Lösewinkel für das Lösen einer Mutter | 10 | Grad | Der für einen bestätigten Schraubenwartungsvorgang benötigte Lösewinkel. | ||
Kraft für Winkelsensor-Reset | 100 | kN | Die Kraft, bei der die Winkelmessreferenz für 0 Grad festgelegt wird. | Die erwarteten Winkel werden in Abhängigkeit vom Kraftanstieg von der Kraft für den Winkelsensor-Reset bis zum Minimalen Schraubenspanndruck berechnet. Dies entspricht je nach Größe des Spanners verschiedenen Drücken, siehe Tabelle im Abschnitt Drücke für verschiedene Spannergrößen. Je größer der Spanner ist, desto höher muss die Kraft für den Winkelreset aufgrund von Problemen bei der Kontrolle niedriger Drücke beim Schritt Installationsprüfung eingestellt werden. Dies ist notwendig, um eine Überschreitung des Installationsprüfungs-Hydraulikdrucks um mehr als das Druckäquivalent der Kraft für den Winkelsensor-Reset zu vermeiden. | |
Minimaler Schraubenspanndruck | 1900 | Bar | Der Mindestdruck für ein IO-Spannergebnis. | Die Druckregelung im System legt einen Sollwert fest, der höher als der Minimale Schraubenspanndruck ist, um Druckabfälle zu vermeiden, die zu einem NIO-Ergebnis führen. Siehe Abbildung im Kapitel Hydraulikdruck-Zielfenster. | |
Max. System-Hydraulikdruck | 1980 | Bar | Der höchste Druck, den die Druckregelung in der Handsteuerung für diese Konfiguration zulässt. | Der tatsächliche Maximaldruck ist der niedrigste der Maximaldrücke an der Pumpe und dem Spanner und zudem der Max. System-Hydraulikdruck der Konfiguration. | |
Minimale Schraubenspannkraft | 698 | kN | Kraftäquivalent des Parameters Minimaler Schraubenspanndruck. | Der Wert wird manuell aus dem Schraubendruck berechnet. Dieser Wert wird in die XML-Berichtsdateien aufgenommen, jedoch nicht von der Software der Handsteuerung verwendet. | |
Installationsprüfungs-Drehmoment | 20 | Nm | Das für eine bestätigte Installationsprüfung benötigte Drehmoment. | ||
Installationsprüfungs-Drehmomentdauer | 1,0 | S | Die Dauer, für welche das Installationsprüfungs-Drehmoment für eine bestätigte Installationsprüfung anliegen muss. | ||
Verschraubungs-Solldrehmoment | 100 | Nm | Das für eine bestätigte Verschraubung der Mutter benötigte Drehmoment. | ||
Verschraubungs-Drehmomentdauer | 1,0 | S | Das für eine bestätigte Verschraubung der Mutter benötigte Drehmoment. | ||
Erkennungswinkel für unerwartete Drehung im Uhrzeigersinn bei der Verschraubung | 5 | Grad | Die maximal zulässige Veränderung des Muttern-Rotationswinkels im Uhrzeigersinn, während der Prozess auf den Druckablass wartet. | Um die Gefahr einer Rotation der Mutter während des Wartens auf den Druckablass zu vermeiden, aktivieren Sie den automatischen Druckablass (siehe Abschnitt Werkzeugkonfiguration). b | |
Erkennungswinkel für unerwartete Drehung gegen den Uhrzeigersinn bei der Verschraubung | 5 | Grad | Die maximal zulässige Veränderung des Muttern-Rotationswinkels gegen den Uhrzeigersinn, während der Prozess auf den Druckablass wartet. | Um die Gefahr einer Rotation der Mutter während des Wartens auf den Druckablass zu vermeiden, aktivieren Sie den automatischen Druckablass (siehe Abschnitt Werkzeugkonfiguration). c | |
Installationsprüfungs-Hydraulikdruck | 20 | Bar | Der Drucksollwert für die Installationsprüfung. | Der Installationsprüfungsdruck fixiert den Spanner während der Installationsprüfung am Flansch. Der Installationsprüfungsdruck darf einschließlich der Überschreitung nicht das Druckäquivalent der Kraft für den Winkelsensor-Reset übersteigen. | |
Hydraulikdruck-Sollwertfaktor | 1,025 | 1,025 | Der tatsächliche Sollwert für die Druckregelung wird wie folgt berechnet: Minimaler Schraubenspanndruck mal Hydraulikdruck-Sollwertfaktor. Siehe Abbildung im Abschnitt Hydraulikdruck-Zielfenster. | Wenn die Taste für die Druckbeaufschlagung gedrückt gehalten wird, wird im System Druck aufgebaut und dieser innerhalb eines Druckfensters oberhalb des Minimalen Schraubenspanndrucks gehalten. |
Schraubendienstvorgang
Halten Sie für garantierte Ergebnisse für den Löse- und Anzugswinkel den Schraubenwartungsprozess ein:
Positionieren Sie das Werkzeug auf der Schraube.
Erhöhen Sie den Druck bis zum Installationsprüfungs-Hydraulikdruck.
Führen Sie vor der Schraubenwartung eine Installationsprüfung durch:
Wenden Sie ein Drehmoment von >20 Nm in Verschraubungsrichtung an. Die Handsteuerung erfasst einen Winkelreferenzpunkt in Verschraubungsrichtung.
Wenden Sie ein Drehmoment von >20 Nm in Löserichtung an. Die Handsteuerung erfasst einen Winkelreferenzpunkt in Löserichtung.
Die Handsteuerung speichert den Winkel des mechanischen Spiels.
Während sich der Schlüssel und das Getriebe in Löseposition befinden, drücken und halten Sie die Taste zur Druckbeaufschlagung, bis der Druck den Minimalen Schraubenspanndruck erreicht.
Lösen Sie die Mutter bis zu einem Winkel, der größer oder gleich dem Schraubenwartungsparameter Minimaler Lösewinkel für das Lösen einer Mutter ist.
Die Steuerungs-UI zeigt den Lösewinkel als negativen Messwert vom Lösewinkel-Referenzpunkt aus an.
Ziehen Sie die Schraube bis zum Parameter Verschraubungs-Solldrehmoment an. Der Anzugswinkel wird aufgezeichnet.
Löse- und Verschraubungswinkel beziehen sich auf die tatsächliche Mutternrotation. Die Handsteuerung gleicht das mechanische Spiel aus. Die Steuerungs-GUI beginnt mit der Aktualisierung des Winkels, sobald die Mutter sich dreht, das mechanische Spiel wird somit nicht berücksichtigt. Der angezeigte Winkel bildet somit die Bewegung der Mutter ab; wenn die Winkelmessung 0 beträgt, befindet die Mutter sich wieder in ihrer Ausgangsposition.
Die Delta-Mutternrotation in Verschraubungsrichtung darf nicht größer als der Parameter Max. Delta-Mutternrotation sein, der standardmäßig auf 13 Grad eingestellt ist. In der Praxis bedeutet das, dass die Mutter sich nicht um einen Winkel größer als 13 Grad zu ihrer Ausgangsposition drehen darf.
Lassen Sie den Druck ab und speichern Sie das Ergebnis. Zum Erhalt von IO-Ergebnissen müssen die folgenden Bedingungen erfüllt sein:
Der aufgezeichnete Lösewinkel ist größer oder gleich dem Minimalen Lösewinkel für das Lösen einer Mutter.
Der aufgezeichnete Delta-Winkel nach der Verschraubung muss im Bereich zwischen der Min. Delta-Mutternrotation und der Max. Delta-Mutternrotation liegen.
Die Min. Delta-Mutternrotation entspricht dem Buchstaben D in der Abbildung zum Schraubenwartungsprozess.
1 | Schlüsseltransport zur Verschraubungsausrichtung |
2 | Mutternrotation beginnt hier |
3 | Bis zur Ausgangsposition angezogen |
A | Lösewinkel |
B | Fixpunkt Lösen |
C | Wiedergabe |
D | Fixpunkt Verschraubung |
E | Der zulässige Verschraubungsbereich nach dem Lösen liegt zwischen den Parametern minimale und maximale Delta-Mutternrotation |
F | Max. Mutternrotation |
Arbeiten mit der Registerkarte Konfigurationen
Die Konfiguration der Werkzeuge wird im Menü Konfigurationen vorgenommen.
Werkzeugkonfiguration
Wählen Sie auf der Startseite Konfigurationen > Werkzeugkonfiguration aus, um die im System verfügbaren Funktionen zu konfigurieren.
Geben Sie einen Namen im Feld Name ein.
Bearbeiten Sie eine Konfiguration, indem Sie auf die Schaltfläche Bearbeiten klicken. Siehe nachfolgende Tabelle.
Um eine zusätzliche Konfiguration mit anderen Einstellungen zu erstellen, klicken Sie auf das Plus-Symbol im oberen Bereich der Seite.
Erstellen Sie beispielsweise eine Konfiguration mit Automatischer Druckablass = EIN oder einem Pumpenmotor-Timeout mit einer anderen Dauer.Um eine Konfiguration zur Verwendung auszuwählen, öffnen Sie auf der Startseite Spanner-Steuerung > Werkzeug.
Parameter | Standardwert | Einheit | Beschreibung | Kommentar |
---|---|---|---|---|
Pumpenmotor-Timeout | 30 | s | Timer für den Abkühlvorgang des Pumpenmotors, der zudem das Hydrauliköl-Rückschlagventil steuert. Der Pumpenmotor wird angehalten, wenn der Timer abläuft, und das Hydrauliköl-Rückschlagventil geschlossen. Wenn der Druck abgelassen wird, wird das Hydrauliköl-Rückschlagventil geöffnet und der Motor läuft 6 Sekunden lang. Anschließend beginnt der Pumpenmotor-Timeout und nach dessen Ablauf wird das Ventil wieder geschlossen und der Motor angehalten. | Wird das System unter warmen Bedingungen eingesetzt, kann das Hydrauliköl beim Stopp des Motors überhitzen. Für längere Spanner kann der Transport des Hydrauliköls zurück zum Ölbehälter der Pumpe länger als die Mindestdauer von 6 Sekunden benötigen. |
Automatischer Druckablass | AUS | Wenn der automatische Druckablass auf EIN geschaltet ist, wird der Druck automatisch abgelassen, wenn die Mutter gemäß den Einstellungen angezogen wurde – die Verschraubung ist abgeschlossen. | Der Druck wird abgelassen, wenn das Drehmoment nachlässt, nachdem das erforderliche Drehmoment für die erforderliche Dauer anlag. Siehe Darstellung des Spannvorgangs im Abschnitt Spannvorgang. Die empfohlene Einstellung für diesen Parameter ist EIN, aus den folgenden Gründen:
|
Arbeiten mit der Registerkarte Spanner-Steuerung
Virtuelle Station
Eine virtuelle Station ist eine softwareseitige Nachbildung einer Handsteuerung. Die Handsteuerung verfügt über eine integrierte Steuerung mit einer verbundenen virtuellen Station. Der virtuellen Station können verschiedene Konfigurationen je nach Bedarf zugewiesen werden.
Werkzeug
In den Werkzeuginformationen werden die Daten des Spanners angezeigt.
Modell: Steckschlüsselgröße und Spannertyp. Damit eine Konfiguration mit dem angeschlossenen Spanner kompatibel ist, müssen die Felder Schraubengröße und Spannertyp dem String unter Modell entsprechen (unter Berücksichtigung der Groß- und Kleinschreibung). Wird eine Konfiguration nicht unter Handsteuerungs-GUI -> Aufgaben -> Montage-Schraubenwartung angezeigt, ist der Grund hierfür mit hoher Wahrscheinlichkeit bei diesen beiden Eigenschaften zu finden.
Getriebeübersetzung: Die Übersetzung des Getriebes im Spanner.
Seriennummer: Die Seriennummer des Spanners.
Max. Drehmoment: Das höchste Drehmoment, das den Drehmomentwandler nicht beschädigt.
Softwareversion.
Produktnummer: Die Artikelnummer des Spanners.
Intelligentes Applikationsmodul
Das Intelligente Applikations-Modul (IAM) ist ein nichtflüchtiger Speicher in der Handsteuerung. Das Speichermodul enthält alle Werkzeugprogramme, Konfigurationen und Ergebnisse.
Öffnen Sie im Hauptmenü die Registerkarte Spanner-Steuerung und wählen Sie IAM aus.
Wenden Sie das Eingabefeld Name für die Handsteuerung an.
Der Name wird in der Web-Benutzeroberfläche und der Oberfläche der Handsteuerung verwendet.
Softwareversionen
Es können zwei Softwareversionen gleichzeitig auf dem Werkzeug installiert werden. Die Installation einer zweiten Softwareversion kann hilfreich zur Vorbereitung der Aktualisierung mehrerer Handsteuerungen für eine synchronisierte Aktivierung sein.

Bei einer Änderung der Softwareversion werden die Werkzeugkonfigurationen sowie die Spannprogramme nicht übertragen.
Software-Aktivierung
Die Handsteuerung kann zwei installierte Softwareversionen speichern. Über die Funktion Software-Aktivierung ist es möglich, die zu verwendende Softwareversion auszuwählen.
Wechseln Sie im Hauptmenü zu Spanner-Steuerung und wählen Sie Software im linken Fenster aus.
Wählen Sie Aktuell oder Gespeichert im Fenster Software-Aktivierung aus.

Die Handsteuerung wird automatisch neu gestartet, damit die Aktivierung wirksam wird.
Aktualisierung der Softwareversion

Falls das installierte Softwarepaket nicht mit der Hardware der Handsteuerung kompatibel ist, wird das Software-Update abgebrochen. Es wird eine Warnmeldung angezeigt, welche angibt, welche Teile der Hardware den Abbruch verursacht haben.
Informationen zur aktuellen Werkzeug-Hardware finden Sie unter Handsteuerung > Hardware.
Wechseln Sie zum Menü Handsteuerung und wählen Sie Software im linken Fenster aus.
Wechseln Sie zum Feld Softwareupdate und wählen Sie DURCHSUCHEN aus.
Suchen Sie nach der zip-Datei mit der entsprechenden Software und wählen Sie diese aus. Folgenden Sie den Anweisungen, um die Installation abzuschließen.
Hardware
Die Registerkarte Hardware enthält Informationen zur Steuerung, wie etwa die Modellbezeichnung und die Seriennummer.
Im Fenster Steuerung neu starten kann ein Neustart der Handsteuerung ausgeführt werden. Klicken Sie auf die Schaltfläche NEU STARTEN.
Exportieren und Importieren von Konfigurationen
Die Export- und Importfunktionen werden zum Export von Ereignissen und Spannergebnissen zur Analyse in externen Programmen sowie zur Übertragung von Spannprogrammen und Werkzeugkonfigurationen zwischen Werkzeugen verwendet.
Die Exportfunktion dient zum:
Export von Spannergebnissen und Aktionen für die weitere Verarbeitung.
Export von Protokolldateien zur Fehlerbehebungsunterstützung für einen Servicetechniker von Atlas Copco.
Export von Werkzeugkonfigurationen, die zum Kopieren von Einstellungen auf ein anderes Werkzeug verwendet werden können.
Wechseln Sie im Hauptmenü zu Spanner-Steuerung. Wählen Sie im linken Fenster Export/Import aus.
Wählen Sie aus, was vom Werkzeug exportiert werden soll:
Alle Informationen
Einstellungen und Konfigurationen
Systemprotokolle und -informationen
Ergebnisse
Wählen Sie für den Export von Parametern, welche in andere Steuerungen importiert werden sollen, Einstellungen und Konfigurationen aus.
Bei der Auswahl von Einstellungen und Konfigurationen werden keine Dateien mit Ergebnissen oder Ereignissen in das Archiv exportiert. Mit dieser Einstellung nimmt der Export weniger Zeit in Anspruch.
Wählen Sie EXPORT. Es wird eine Aufforderung zur Auswahl des Speicher- oder Abrufpfads der exportierten Datei angezeigt.
Wechseln Sie im Hauptmenü zu Spanner-Steuerung. Wählen Sie im linken Fenster Export/Import aus.
Wählen Sie IMPORT. Bei Verwendung der Importfunktion werden alle Einstellungen für Spannprogramme und Konfigurationen durch die Einstellungen in der Importdatei ersetzt. Einstellungen für Netzwerk, PIN sowie Ergebnisse und Ereignisse werden jedoch nicht importiert.
Wählen Sie im Dialogfeld FORTFAHREN aus, um mit dem Import zu beginnen.
Exportierte Informationen und Dateiformat
Die exportierte Datei ist ein komprimiertes Dateiarchiv, das die folgenden Dateien enthält:
Alle Informationen
PFExport_<datetime>_Results.csv
PFExport_<datetime>_Events.csv
ExportInfo.txt
settings/settings.zip
atlas_tool_i.zip
atlas_sys_i.zip
atlas_subsystems_info.zip
atlas_plc.zip
jsonConfigurations.zip
Einstellungen und Konfigurationen
ExportInfo.txt
settings/settings.zip
jsonConfigurations.zip
Datei | Beschreibung |
---|---|
PFExport__<Tool name>_<Time stamp>_Events.csv | Eine CSV-Datei mit folgenden Informationen:
|
PFExport__<Tool name>_<Time stamp>_Results.csv | Eine CSV-Datei mit folgenden Informationen:
|
ExportInfo.txt | Angaben zur Werkzeugeinrichtung und der Werkzeugsoftware. |
settings/settings.zip | Eine Binärdatei, die alle Verschraubungsprogramme, Gruppeneinstellungen, Zubehörkonfigurationen und Werkzeugeinstellungen enthält, wie beispielsweise: Sprache, Drehmomenteinheiten, Datum und Uhrzeit und Erscheinungsbild der Ergebnisansicht. |
atlas_tool_i.zip | Werkzeugprotokolle (zur Fehlerbehebung) |
atlas_sys_i.zip | Protokolldateien von IT-Anwendung |
atlas_subsystems_info.zip | Informationen zur Subsystem-Software |
atlas_plc.zip | PLC-Konfiguration |
jsonConfigurations.zip | Mehrstufige Verschraubungs- und Löseprogramme |
Export von „Systemprotokollen und -informationen“
Mit diesem Export kann ein Servicetechniker die Systemprotokolle und -informationen zur Unterstützung bei der Fehlersuche mit den Servicetechnikern von Atlas Copco teilen.

Der Export von Systemprotokollen und -informationen schließt keine Protokolle von angeschlossenen Werkzeugen mit ein.
Alle im Export der Systemprotokolle und -informationen enthaltenen Daten werden in einer Datei mit dem Namen PFExport_<IAM-Name>_<DatumUhrzeit>.tar.gz gespeichert, welche die folgenden Dateien und Verzeichnisse umfasst:
atlas_sys_i.zip – Protokolldateien von IT-Anwendungen
atlas_protocol_log.zip – Protokolldateien von externen Protokoll-Adaptern
ExportInfo.txt – Textdokument mit Informationen zum IAM und zur Steuerung
licenseInformation.zip – Lizenzinformationen und Systemfunktionalitäten
atlas_systeminformation.zip – Informationen zum aktuellen Systemzustand und zur Einrichtung für die F&E-Abteilung von Atlas Copco
Exportieren von „Systemprotokollen und -informationen“
Wechseln Sie im Hauptmenü zu Spanner-Steuerung und wählen Sie im linken Fenster Export/Import aus.
Öffnen Sie im Fenster Export das Dropdown-Menü und wählen Sie Systemprotokolle und -informationen aus.
Wählen Sie im Export-Fenster EXPORT aus.
Am Ende des Exportvorgangs bestätigt ein Popup-Fenster, dass der Export abgeschlossen ist.
Es wird automatisch eine Datei PFExport_<IAM Name>_<DatumZeit>.tar.gz heruntergeladen.
Arbeiten mit der Registerkarte Berichte
Anzeige von Ergebnissen
In diesem Abschnitt wird beschrieben, wie auf Spannergebnisse auf der Handsteuerung zugegriffen werden kann und wie die in den verschiedenen Ergebnisansichten bereitgestellten Informationen zu lesen sind.
Bei Ausführung eines Spannvorgangs wird das Ergebnis auf der Handsteuerung gespeichert. Ergebnisse können auch an ein externes System, wie beispielsweise ToolsNet, gesendet oder mittels der Export-Funktion zur Analyse exportiert werden. Weitere Informationen zur statistischen Analyse, Filterung von Ergebnissen und Spannungsanalyse mittels ToolsNet finden Sie im ToolsNet 8-Benutzerhandbuch.
Gespeicherte Ergebnisse
Jede Aufgabe wird als ein Ergebnis angezeigt. Zu einem einzelnen Spannvorgang können Ergebnisse in einer Tabelle mit den wichtigsten Parametern dargestellt werden.
Ansicht gespeicherter Ergebnisse
In der Handsteuerung wird das Ergebnis für jeden ausgeführten Verschraubungs- oder Lösevorgang gespeichert.
Öffnen Sie Berichte im Hauptmenü und wählen Sie im linken Fenster Ergebnisse aus.
Wählen Sie Alle Ergebnisse anzeigen aus. In der Ergebnisliste werden folgende Informationen angezeigt:
Datum: Datum und Uhrzeit des ausgeführten Spannvorgangs.
Verschraubungsprogramm: In der Spalte Verschraubungsprogramm wird der Name des mehrstufigen Spannprogramms angezeigt.
Kraft: Während des Spannvorgangs gemessene Kraft.
Druck: Während des Spannvorgangs gemessener Druck.
Ergebnis: Drehmoment- / Winkel-Ergebnis.
Grenzwerte: Drehmomentbereich, Winkelbereich und Druckbereich für ein IO-Ergebnis. Bei NIO-Ergebnissen werden die überschrittenen Bereichsgrenzwerte mit rotem Text hervorgehoben.
Mit einem roten Balken markierte Ergebnisse haben den Status NIO.
Ereignisse anzeigen
Aktionen werden dazu genutzt, um den Bediener über bestimmte Zustandsänderungen oder Vorkommnisse im System zu benachrichtigen. Diese werden in drei Gruppen unterteilt, Informationen, Warnungen und Fehler, und erfordern verschiedene Arten von Maßnahmen.
Jedes Ereignis umfasst eine Standardeinstellung, mit der bestimmt wird, ob es bestätigt (Ack), aufgezeichnet (Log) oder angezeigt (Disp) werden soll. Diese Einstellungen können im Menü Einstellungen unter Ereignisse konfiguriert werden.
Öffnen Sie Berichte im Hauptmenü und wählen Sie im linken Fenster Ereignisse aus.
Wählen Sie Alle Ereignisse anzeigen aus.
Wählen Sie ein Ereignis aus der Liste aus, um das Ereignis-Dialogfenster zu öffnen.
Das Ereignis-Dialogfenster
Das Ereignis-Dialogfenster enthält Informationen zum eingetretenen Ereignis und beschreibt was wo und wann passiert ist.

Position | Beschreibung |
---|---|
1 | Kopfzeile – Beschreibt, in welchem Systembereich das Ereignis auftrat. |
2 | Ereignisname – Eine kurze Beschreibung des Ereignisses. |
3 | Code – Eine spezifische vierstellige Zahl, mit der das Ereignis identifiziert wird. |
4 | Modul – Beschreibt, in welchem Systembereich das Ereignis auftrat. |
5 | Typ – Information, Warnung oder Fehler. |
6 | Zeit – Datum und Uhrzeit des Ereignisses. |
Ereigniscodes
Es werden verschiedene Arten von Ereignissen genutzt, um den Bediener über bestimmte Zustandsänderungen oder Vorkommnisse im System zu benachrichtigen. Jedes Ereignis erfordert eine andere Aktion.

Es ist zu beachten, dass bestimmte Vorgänge nur von Servicemitarbeitern von Atlas Copco ausgeführt werden dürfen.
Verwenden Sie für weitere Informationen zu bestimmten Ereigniscodes die nachfolgenden Filter oder geben Sie die Suchkriterien für den Ereigniscode in das Suchfeld ein.
Protokoll / Anzeige / Bestätigung / Konfiguration | |||||||
---|---|---|---|---|---|---|---|
none | item | none | none | none | column | list | list |
1000 | Info | Steuerung gestartet | Die Steuerung wird gestartet. | Flex IxB Power Focus 6000 Power Focus 8 StepSync Power Focus XC PFHC | Steuerung und Werkzeug | ||
1001 | Warnung | Controller-Seriennummer aktualisiert | Sie wird beim Hochfahren generiert, wenn die Seriennummer der IT-Platinenbox (Controller-Seriennummer) von der Seriennummer der AUX-Platinenbox abweicht. Die AUX-Platine lässt sich nicht vor Ort austauschen. Der Controller wird neu gestartet, wenn die Seriennummer aktualisiert wird. | IT-Platine oder Box austauschen. | Protokoll Konfiguration | Power Focus 6000 Power Focus 8 StepSync Power Focus XC | Steuerung und Werkzeug |
1010 | Info | Werkzeug angeschlossen | Ein Werkzeug wird angeschlossen. | Protokoll Display Konfiguration | Flex Power Focus 6000 Power Focus 8 StepSync Power Focus XC PFHC | Steuerung und Werkzeug | |
1011 | Info | Werkzeug nicht angeschlossen | Ein Werkzeug wird vom Anschluss getrennt. | Protokoll Display Konfiguration | Flex Power Focus 6000 Power Focus 8 StepSync Power Focus XC PFHC | Steuerung und Werkzeug | |
1012 | Info | Werkzeug hat die Verbindung zum Controller abgelehnt | Dieses Ereignis kann auftreten, wenn sich das Werkzeug in einer Skip-Zone befindet. | Überprüfen Sie, ob ein anderer Controller mit dem Werkzeug verbunden ist. Stellen Sie sicher, dass die Werkzeugeinstellungen korrekt eingerichtet wurden. | Protokoll Display Konfiguration | Power Focus 6000 Power Focus 8 Power Focus XC | Steuerung und Werkzeug |
2000 | Warnung | Akkuspannung niedrig | Den Akku austauschen. | Protokoll Display Konfiguration | IxB Power Focus 6000 Power Focus 8 Power Focus XC | Werkzeug | |
2001 | Warnung | Akku leer | Den Akku austauschen. | Protokoll Display Konfiguration | IxB Power Focus 6000 Power Focus 8 Power Focus XC | Werkzeug | |
2002 | Warnung | Werkzeug-Akkuzustand niedrig | Werkzeug-Akkuhaltbarkeitsproblem wurde erkannt. | Den Akku austauschen. | Protokoll Display Konfiguration | IxB Power Focus 6000 Power Focus 8 Power Focus XC | Werkzeug |
2004 | Warnung | Werkzeug ist keine bevorzugte Art | Das Werkzeug wurde durch ein Werkzeug mit einem anderen maximalen Werkzeugdrehmoment ersetzt. | Werkzeug wechseln. | Konfiguration | IxB Power Focus 6000 Power Focus 8 Power Focus XC | Werkzeug |
2006 | Warnung | Zustand des Werkzeugzusatzakkus niedrig | Die Backup-Batterie im Werkzeug zeigt schlechte Leistungsdaten. | Die Backup-Batterie muss ausgetauscht werden. | Protokoll Display Bestät. Konfiguration | IxB Power Focus 6000 Power Focus 8 Power Focus XC | Werkzeug |
2007 | Warnung | Werkzeugzusatzakku fehlt | Der Werkzeugzusatzakku fehlt. | Akku einlegen | Protokoll Display Konfiguration | IxB Power Focus 6000 Power Focus 8 Power Focus XC | Werkzeug |
2008 | Warnung | Fehler des Werkzeugzusatzakkus | Fehler am Werkzeugzusatzakku erkannt. | Den Akku austauschen. | Protokoll Display Konfiguration | IxB Power Focus 6000 Power Focus 8 Power Focus XC | Werkzeug |
2009 | Warnung | Zusatzakkuspannung niedrig | Der Reserveakku der Steuerung ist fast leer. | Den Akku austauschen. | Protokoll Display Konfiguration | IxB Power Focus 6000 Power Focus 8 Power Focus XC | Werkzeug |
2010 | Fehler | Falsche Werkzeugsoftware-Version | Die Softwareversionen des Werkzeugs und der Steuerung sind nicht kompatibel. | Werkzeug warten - Werkzeugsoftware aktualisieren. | Protokoll Display Bestät. Konfiguration | Flex IxB Power Focus 6000 Power Focus 8 StepSync Power Focus XC | Werkzeug |
2012 | Warnung | Störung Werkzeugkommunikation | Die Kommunikation zwischen Werkzeug und Steuerung wurde unterbrochen. | Antenne neu positionieren. | Konfiguration | Flex Power Focus 6000 Power Focus 8 StepSync Power Focus XC PFHC | Werkzeug |
2013 | Warnung | Ungültige Umschaltringposition | Der Richtungsschalter am Werkzeug befindet sich in einer falschen Stellung. | Bei häufigem Auftreten - Werkzeug warten. | Protokoll Display Konfiguration | Flex Power Focus 6000 Power Focus 8 Power Focus XC | Werkzeug |
2014 | Warnung | Werkzeug überhitzt | Werkzeug überhitzt. | Werkzeug abkühlen lassen. | Protokoll Display Konfiguration | Flex IxB Power Focus 6000 Power Focus 8 StepSync Power Focus XC | Werkzeug |
2015 | Fehler | Fehler Werkzeugtemperatursensor | Nur für SRB-, TBP- und IxB-Werkzeuge. | Führen Sie eine Werkzeugwartung durch. | Protokoll Display Konfiguration | Flex IxB Power Focus 6000 Power Focus 8 StepSync Power Focus XC | Werkzeug |
2016 | Warnung | Impulseinheit des Werkzeugs überhitzt | Impulseinheit überhitzt. Werkzeug ist nicht gesperrt, aber die Warnung wird immer dann angezeigt, wenn das Werkzeug gestartet wird, solange die Pulseinheitstemperatur über dem Schwellenwert liegt. | Werkzeug abkühlen lassen. | Protokoll Display Konfiguration | Power Focus 6000 Power Focus 8 Power Focus XC | Werkzeug |
2019 | Warnung | Werkzeug konnte Motor nicht starten | Fehler Werkzeugmotor | Protokoll Display Konfiguration | IxB Power Focus 6000 Power Focus 8 Power Focus XC | Werkzeug | |
2020 | Warnung | Motortuning des Werkzeugs erforderlich | Motortuning des Werkzeugs erforderlich. | Führen Sie ein Motortuning durch. | Protokoll Display Konfiguration | Flex IxB Power Focus 6000 Power Focus 8 StepSync Power Focus XC | Werkzeug |
2021 | Warnung | Motortuning fehlgeschlagen | Motortuning fehlgeschlagen. | Motortuning vollständig ausführen oder das Werkzeug warten. | Protokoll | Flex IxB Power Focus 6000 Power Focus 8 StepSync Power Focus XC | Werkzeug |
2022 | Info | Motortuning vollständig ausgeführt | Motortuning vollständig ausgeführt. | Protokoll Konfiguration | Flex IxB Power Focus 6000 Power Focus 8 StepSync Power Focus XC | Werkzeug | |
2023 | Warnung | Offenmaul-Tuning des Werkzeugs erforderlich | Offenmaul-Tuning des Werkzeugs erforderlich. | Offenmaul-Tuning ausführen. | Protokoll Display Konfiguration | IxB Power Focus 6000 Power Focus 8 Power Focus XC | Werkzeug |
2024 | Warnung | Offenmaul-Tuning fehlgeschlagen | Offenmaul-Tuning fehlgeschlagen. | Versuchen Sie noch einmal, ein Offenmaul-Tuning auszuführen. Bei erneutem Fehler das Werkzeug warten. | Protokoll Konfiguration | IxB Power Focus 6000 Power Focus 8 Power Focus XC | Werkzeug |
2025 | Info | Offenmaul-Tuning erfolgreich | Offenmaul Tuning erfolgreich. | Protokoll Konfiguration | IxB Power Focus 6000 Power Focus 8 Power Focus XC | Werkzeug | |
2026 | Warnung | Offenmaul-Positionierung fehlgeschlagen | Offenmaul-Positionierung fehlgeschlagen. | Den Werkzugstartknopf erneut drücken und warten, bis die Positionierung abgeschlossen ist. Bei erneutem Fehler das Werkzeug warten. | Protokoll Display Konfiguration | IxB Power Focus 6000 Power Focus 8 Power Focus XC | Werkzeug |
2027 | Warnung | Nutzung aufgrund hoher Werkzeugtemperatur eingeschränkt | Der Temperaturgrenzwert wurde erreicht. Die Verschraubung wurde gesperrt, um die Gefahr eines Herunterfahrens des Werkzeugs aufgrund von Überhitzung zu verringern. | Warten Sie, bis das Werkzeug abgekühlt ist. | Protokoll Display Konfiguration | Flex IxB Power Focus 6000 Power Focus 8 StepSync Power Focus XC | Werkzeug |
2030 | Fehler | Fehler des Werkzeugspeichers: Werkzeug wechseln | Werkzeugspeicher-Fehler. | Führen Sie eine Werkzeugwartung durch. | Protokoll Display Bestät. Konfiguration | Flex IxB Power Focus 6000 Power Focus 8 StepSync Power Focus XC | Werkzeug |
2031 | Fehler | Werkzeugzubehörspeicher fehlerhaft | Werkzeugzubehörspeicher fehlerhaft. | Eine Werkzeugzubehörwartung durchführen. | Protokoll Display Bestät. Konfiguration | Flex IxB Power Focus 6000 Power Focus 8 StepSync Power Focus XC | Werkzeug |
2040 | Fehler | Systemprüfung fehlgeschlagen | Protokoll Display Bestät. Konfiguration | Flex IxB Power Focus 6000 Power Focus 8 StepSync Power Focus XC | Werkzeug | ||
2041 | Fehler | Fehler des Drehmomentgebers | Wird entweder bei einem Kalibrierfehler oder wenn das Werkzeug einen Messwertgeberfehler meldet, erzeugt. | Führen Sie eine Werkzeugwartung durch. | Protokoll Display Konfiguration | Flex IxB Power Focus 6000 Power Focus 8 StepSync Power Focus XC | Werkzeug |
2042 | Fehler | Fehler des Winkelgebers | Führen Sie eine Werkzeugwartung durch. | Protokoll Display Bestät. Konfiguration | Flex IxB Power Focus 6000 Power Focus 8 StepSync Power Focus XC | Werkzeug | |
2043 | Fehler | Werkzeugerdungsfehler | Führen Sie eine Werkzeugwartung durch. | Protokoll Display Bestät. Konfiguration | Flex IxB Power Focus 6000 Power Focus 8 StepSync Power Focus XC | Werkzeug | |
2044 | Info | Werkzeugwartungsintervall abgelaufen | Gibt an, dass das Werkzeug gewartet werden muss. Wird ausgelöst, wenn die festgelegte Anzahl von Verschraubungen überschritten wurde. | Das Werkzeug warten. | Protokoll Display Konfiguration | Flex IxB Power Focus 6000 Power Focus 8 StepSync Power Focus XC | Werkzeug |
2045 | Warnung | Werkzeugkalibrierdaten ungültig | Wenn die Validierung der Kalibrierdaten fehlschlägt. | Führen Sie eine Werkzeugwartung durch. | Protokoll Display Konfiguration | Flex IxB Power Focus 6000 Power Focus 8 StepSync Power Focus XC | Werkzeug |
2046 | Info | Werkzeug: Nächstes Kalibrierdatum wurde überschritten | Gibt an, dass das Werkzeug kalibriert werden muss. Wird ausgelöst, wenn der Kalibrierungsalarm in den Einstellungen aktiviert ist und die gegenwärtige Zeit über dem nächstem Kalibrierdatum liegt. | Führen Sie eine Werkzeugwartung durch. | Protokoll Display Konfiguration | Flex IxB Power Focus 6000 Power Focus 8 StepSync Power Focus XC | Werkzeug |
2048 | Info | Wert für Werkzeugkalibrierung durch QS-Gerät aktualisiert | Eine Aktualisierung der Werkzeugkalibrierung erfolgte, als eine Kalibrierung mit einem QS-Gerät durchgeführt wurde. | Protokoll Display Konfiguration | IxB Power Focus 6000 Power Focus 8 Power Focus XC | Werkzeug | |
2050 | Fehler | Werkzeug-Parameterdatei wird nicht unterstützt | Erforderliche Werkzeugparameter fehlen. | Werkzeugparameter aktualisieren. | Protokoll Display Konfiguration | Flex IxB Power Focus 6000 Power Focus 8 StepSync Power Focus XC | Werkzeug |
2060 | Info | Unerwartetes Startknopfverhalten | Wird zur Verhinderung eines Starts des Werkzeugs bei Anschluss eines Zubehörs verwendet. | Protokoll Display Konfiguration | IxB Power Focus 6000 Power Focus 8 StepSync Power Focus XC | Werkzeug | |
2071 | Fehler | Werkzeugspeicher fehlerhaft | Werkzeugbeschreiber ist fehlerhaft. | Führen Sie eine Werkzeugwartung durch. | Protokoll Display Konfiguration | Flex Power Focus 6000 Power Focus 8 StepSync Power Focus XC | Werkzeug |
2072 | Info | Unbekanntes Gerät verbunden | Protokoll Display Konfiguration | Flex IxB Power Focus 6000 Power Focus 8 StepSync Power Focus XC | Werkzeug | ||
2073 | Warnung | Startknopf-Überwachungsfehler | HW-Kanal-Fehler. Hardware und Software des Werkzeugstartknopfs passen nicht zusammen. | Protokoll Display Konfiguration | IxB Power Focus 6000 Power Focus 8 Power Focus XC | Werkzeug | |
2074 | Warnung | Fehler der Werkzeug-Anzeigeplatine | Fehler, Werkzeug-Anzeigeplatine. | Führen Sie eine Werkzeugwartung durch. | Protokoll Display Konfiguration | Flex IxB Power Focus 6000 Power Focus 8 StepSync Power Focus XC | Werkzeug |
2075 | Warnung | Werkzeuglüfter-Spannungsfehler | Werkzeuglüfter-Spannungsfehler. | Führen Sie eine Werkzeugwartung durch. | Protokoll Display Konfiguration | Power Focus 6000 Power Focus 8 StepSync Power Focus XC | Werkzeug |
2076 | Warnung | Busspannungsfehler des Werkzeugzubehörs | Busspannungsfehler, Werkzeugzubehör. | Führen Sie eine Werkzeugwartung durch. | Protokoll Display Konfiguration | Flex IxB Power Focus 6000 Power Focus 8 StepSync Power Focus XC | Werkzeug |
2077 | Warnung | Werkzeugstartknopf-Sensorfehler | Startknopf-Sensorfehler. | Führen Sie eine Werkzeugwartung durch. | Protokoll Display Konfiguration | IxB Power Focus 6000 Power Focus 8 StepSync Power Focus XC | Werkzeug |
2078 | Info | Verschraubungsprogramm des Werkzeugs aktualisiert | Werkzeug aufgrund von Verschraubungsprogramm-Aktualisierung gesperrt. | Protokoll Display Konfiguration | IxB Power Focus 6000 Power Focus 8 Power Focus XC | Werkzeug | |
2079 | Fehler | Werkzeugkabel nicht unterstützt | Werkzeugkabel ist fehlerhaft. Der im Kabel befindliche Chip reagiert nicht oder ist beschädigt. | Kabel austauschen. | Protokoll Display Konfiguration | Flex Power Focus 6000 Power Focus 8 StepSync Power Focus XC | Werkzeug |
2080 | Fehler | Fehler Werkzeugakku | Gleichspannung zu hoch oder zu niedrig. Akkufehler. | Wenden Sie sich an einen Atlas Copco-Kundendienstvertreter und schicken Sie den Akku an Atlas Copco zurück (verwenden Sie ihn nicht wieder!). | Protokoll Display Konfiguration | IxB Power Focus 6000 Power Focus 8 Power Focus XC | Werkzeug |
2081 | Fehler | Werkzeug-Stromgrenze erreicht | Der Stromgrenzwert wurde erreicht und der Antrieb ist abgeschaltet. | Führen Sie eine Werkzeugwartung durch. | Protokoll Display Konfiguration | IxB Power Focus 6000 Power Focus 8 Power Focus XC | Werkzeug |
2082 | Fehler | Werkzeug-Strommessfehler | Strommessfehler. Bei der Strommessung kann kein zuverlässiges Ergebnis erhalten werden. | Führen Sie eine Werkzeugwartung durch. | Protokoll Display Konfiguration | IxB Power Focus 6000 Power Focus 8 Power Focus XC | Werkzeug |
2083 | Fehler | Interner Werkzeugfehler | Diverse interne Hardwarefehler. | Führen Sie eine Werkzeugwartung durch. | Protokoll Display Konfiguration | IxB Power Focus 6000 Power Focus 8 Power Focus XC | Werkzeug |
2084 | Fehler | Interner Werkzeug-Softwarefehler | Diverse interne Softwarefehler. | Führen Sie eine Werkzeugwartung durch. | Protokoll Display Konfiguration | IxB Power Focus 6000 Power Focus 8 Power Focus XC | Werkzeug |
2085 | Fehler | Werkzeug-RBU-Fehler | Von der Werkzeugsoftware wurde ein RBU-Fehler festgestellt. | Überprüfen Sie, dass die RBU ordnungsgemäß installiert ist. Wenn der Fehler weiterhin vorhanden ist, das Werkzeug warten. | Protokoll Display Konfiguration | IxB Power Focus 6000 Power Focus 8 Power Focus XC | Werkzeug |
2086 | Fehler | Werkzeugstillstand | Werkzeugmotor bleibt stehen. | Führen Sie eine Werkzeugwartung durch. | Protokoll Display Konfiguration | IxB Power Focus 6000 Power Focus 8 Power Focus XC | Werkzeug |
2087 | Warnung | Werkzeugmotor-Strom zu hoch | Der Stromgrenzwert des Werkzeugmotors wurde überschritten und das Werkzeug ist gesperrt. Das Werkzeug wechselt in den Modus Ausfallsicher. | Protokoll Display Konfiguration | IxB Power Focus 6000 Power Focus 8 Power Focus XC | Werkzeug | |
2088 | Warnung | Werkzeugakku-Strom zu hoch | Der Strom des Werkzeugakkus ist zu hoch. | Protokoll Display Konfiguration | IxB Power Focus 6000 Power Focus 8 Power Focus XC | Werkzeug | |
2089 | Warnung | Werkzeugantriebsspannung zu niedrig | Die Werkzeug-Antriebsspannung liegt unter dem überwachten unteren Spannungsgrenzwert. | Protokoll Display Konfiguration | IxB Power Focus 6000 Power Focus 8 Power Focus XC | Werkzeug | |
2090 | Warnung | Werkzeugantriebsspannung zu hoch | Die Werkzeug-Antriebsspannung liegt über dem überwachten oberen Spannungsgrenzwert. | Protokoll Display Konfiguration | IxB Power Focus 6000 Power Focus 8 Power Focus XC | Werkzeug | |
2091 | Warnung | Fehler der Werkzeug-Hauptplatine | Interner Fehler der Werkzeug-Hauptplatine. | Protokoll Display Konfiguration | IxB Power Focus 6000 Power Focus 8 Power Focus XC | Werkzeug | |
2092 | Warnung | Fehler des Werkzeug-Stromversorgungsmoduls | Interner Fehler des Werkzeug-Stromversorgungsmoduls. | Protokoll Display Konfiguration | IxB Power Focus 6000 Power Focus 8 Power Focus XC | Werkzeug | |
2093 | Warnung | Ölstand der Impulseinheit niedrig | Der Ölstand des angeschlossenen Impulsschraubers ist niedrig. | Führen Sie eine Werkzeugwartung durch. | Protokoll Display Konfiguration | Power Focus 6000 Power Focus 8 Power Focus XC | Werkzeug |
2094 | Warnung | Ölstand der Impulseinheit leer | Der Ölstand des angeschlossenen Impulsschraubers liegt unter dem für den Betrieb erforderlichen Pegel. | Führen Sie eine Werkzeugwartung durch. | Protokoll Display Bestät. Konfiguration | Power Focus 6000 Power Focus 8 Power Focus XC | Werkzeug |
2095 | Warnung | Kommunikation mit Werkzeugakku ausgefallen | Kommunikation zwischen Werkzeug und Akku wurde unterbrochen. | Stellen Sie sicher, dass der Akku richtig eingelegt ist. Andernfalls Akku wechseln. | Protokoll Display Konfiguration | IxB Power Focus 6000 Power Focus 8 Power Focus XC | Werkzeug |
2096 | Fehler | Falsche Version der Werkzeugakku-Software | Software des Werkzeugakkus ist nicht mit der Werkzeugsoftware kompatibel. | Software aktualisieren. | Protokoll Display Konfiguration | IxB Power Focus 6000 Power Focus 8 Power Focus XC | Werkzeug |
2100 | Info | STwrench smartHEAD entfernt | STwrench smartHEAD wurde entfernt. | smartHead wieder anschließen und den Schlüssel neu starten. | Protokoll Display Konfiguration | IxB Power Focus 6000 Power Focus 8 Power Focus XC | Werkzeug |
2101 | Warnung | Schlüssel-Verschraubung wenn gesperrt | Eine Schraubenschlüssel-Verschraubung wurde durchgeführt, als der Werkzeugstatus im Controller auf gesperrt gesetzt war. | Warten Sie, bis der Werkzeugstatus im Controller entsperrt ist. | Protokoll Display Konfiguration | Power Focus 6000 Power Focus 8 | Werkzeug |
2120 | Warnung | Kann nicht gestartet werden: Werkzeug verfügt über keinen aktiven Momentgeber | Protokoll Display | Flex | Werkzeug | ||
2121 | Warnung | Geber sind für angeschlossenes Werkzeug deaktiviert | Protokoll Display | Flex | Werkzeug | ||
2122 | Warnung | Kann nicht gestartet werden: Werkzeug verfügt nicht über den erforderlichen Momentgeber | Protokoll Display | Flex IxB | Werkzeug | ||
2123 | Warnung | Kann nicht gestartet werden: Werkzeug verfügt nicht über den erforderlichen Winkelgeber | Protokoll Display | Flex | Werkzeug | ||
2124 | Fehler | Momentgeber-Fehler am Hauptwandler | Zeigt an, dass bei einem Werkzeug mit zwei Gebern ein Fehler am primären Momentgeber vorliegt. | Protokoll Display | Flex | Werkzeug | |
2125 | Fehler | Momentgeber-Fehler am sekundären Wandler | Zeigt an, dass bei einem Werkzeug mit zwei Gebern ein Fehler am sekundären Momentgeber vorliegt. | Protokoll Display | Flex | Werkzeug | |
2126 | Fehler | Werkzeug-Momentgeber, Kalibrierungsfehler im Hauptwandler | Protokoll Display | Flex | Werkzeug | ||
2127 | Fehler | Werkzeug-Momentgeber, Kalibrierungsfehler | Protokoll Display | Flex StepSync | Werkzeug | ||
2128 | Fehler | Werkzeug-Momentgeber: Shunt-Test für Hauptwandler fehlgeschlagen | Protokoll Display | Flex | Werkzeug | ||
2129 | Fehler | Werkzeug-Momentgeber: Shunt-Test fehlgeschlagen | Protokoll Display | Flex StepSync | Werkzeug | ||
2130 | Fehler | Werkzeug-Momentgeber: Nullpunktabgleich-Kompensierung am Hauptwandler fehlgeschlagen | Protokoll Display | Flex | Werkzeug | ||
2131 | Fehler | Werkzeug-Momentgeber: Nullpunktabgleich-Kompensierung fehlgeschlagen | Protokoll Display | Flex StepSync | Werkzeug | ||
2132 | Fehler | Werkzeug-Momentgeber, Gerätefehler im Hauptwandler | Protokoll Display | Flex | Werkzeug | ||
2133 | Fehler | Werkzeug-Momentgeber, Gerätefehler | Protokoll Display | Flex StepSync | Werkzeug | ||
2134 | Fehler | Fehler des Werkzeug-Momentgebers: Überlauf in A/D-Wandler des Hauptwandlers | Protokoll Display | Flex | Werkzeug | ||
2135 | Fehler | Fehler des Werkzeug-Momentgebers: Überlauf in A/D-Wandler | Protokoll Display | Flex StepSync | Werkzeug | ||
2136 | Fehler | Werkzeug-Momentgeber, Kalibrierungsfehler im Sekundärwandler | Protokoll Display | Flex | Werkzeug | ||
2137 | Fehler | Fehler des Werkzeug-Momentgebers: Shunt-Test für Sekundärwandler fehlgeschlagen | Protokoll Display | Flex | Werkzeug | ||
2138 | Fehler | Fehler des Werkzeug-Momentgebers: Nullpunktabgleich-Kompensierung am Sekundärwandler fehlgeschlagen | Protokoll Display | Flex | Werkzeug | ||
2139 | Fehler | Werkzeug-Momentgeber, Gerätefehler im Sekundärwandler | Protokoll Display | Flex | Werkzeug | ||
2140 | Fehler | Fehler des Werkzeug-Momentgebers: Überlauf in A/D-Wandler des Sekundärwandlers | Protokoll Display | Flex | Werkzeug | ||
2202 | Fehler | Überstrom an der Werkzeug-MMS aufgetreten | An der Werkzeug-MMS wurde ein Überstrom erkannt. | Führen Sie eine Werkzeugwartung durch. Werkzeug-MMS austauschen. | Protokoll Display Bestät. Konfiguration | IxB | Werkzeug |
2203 | Fehler | Überstrom an der Frontleuchte aufgetreten | An der Frontleuchte wurde ein Überstrom erkannt. | Führen Sie eine Werkzeugwartung durch. Die Frontleuchte austauschen. | Protokoll Display Bestät. Konfiguration | IxB | Werkzeug |
2204 | Fehler | Überstrom am Zubehörbus aufgetreten | Am Zubehörbus wurde ein Überstrom erkannt. | Führen Sie eine Werkzeugwartung durch. Den Zubehörbus austauschen. | Protokoll Display Bestät. Konfiguration | IxB | Werkzeug |
2207 | Fehler | Überstrom am Vibrationsgerät aufgetreten | Am Vibrationsgerät wurde ein Überstrom erkannt. | Führen Sie eine Werkzeugwartung durch. Das Vibrationsgerät austauschen. | Protokoll Display Bestät. Konfiguration | IxB | Werkzeug |
2208 | Warnung | Temperatur der System-CPU hoch | Temperatur der System-CPU hoch. | Warten Sie, bis das Werkzeug abgekühlt ist. | Protokoll Display Konfiguration | IxB | Werkzeug |
2209 | Fehler | Temperatur der System-CPU kritisch | Temperatur der System-CPU kritisch. | Warten Sie, bis das Werkzeug abgekühlt ist. | Protokoll Display Konfiguration | IxB | Werkzeug |
2210 | Fehler | Nicht unterstützte Stromquelle: Verschraubung nicht zulässig | Akku mit zu geringer Spannung am Werkzeug angebracht. | Bringen Sie einen Akku mit höherer Spannung am Werkzeug an. | Protokoll Display Bestät. Konfiguration | IxB | Werkzeug |
2500 | Fehler | Max. Anzahl Spanner-Zugstange | Spanner-Zugstange muss ausgetauscht werden. Das System ist für die Nutzung gesperrt. Es kann nur Druck abgelassen werden. | Senden Sie den Spanner zum Austausch der Zugstange an das Serviceunternehmen. | Protokoll Display Bestät. | PFHC | Werkzeug |
2501 | Fehler | Alarm Pumpenmotorschutz | Der Pumpenmotorschutz hat den Motor angehalten. Das System muss angehalten werden. Falls das System unter Druck steht, muss der Druck manuell abgelassen werden. | Schalten Sie das System ab. Falls dieses unter Druck steht, lassen Sie den Druck manuell ab und senden Sie die Pumpe zur Wartung ein. | Protokoll Display Bestät. | PFHC | Werkzeug |
2502 | Fehler | Alarm niedriger Ölstand Pumpenmotor | Der Ölstand des Pumpenmotors ist niedrig, daher wurde der Motor abgeschaltet. Falls das System unter Druck steht, muss der Druck manuell abgelassen werden. | Schalten Sie das System ab. Falls dieses unter Druck steht, lassen Sie den Druck manuell ab und füllen Sie Öl nach. | Protokoll Display Bestät. | PFHC | Werkzeug |
2503 | Fehler | Alarm Pumpenmotor-Öltemperatur hoch | Die Öltemperatur des Pumpenmotors ist hoch. | Schalten Sie das System ab und warten Sie, bis das Öl abgekühlt ist. | Protokoll Display Bestät. | PFHC | Werkzeug |
2504 | Fehler | Alarm Spanner-Drucksensor | Fehler der Drucksensorelektronik des Spanners. Es kann kein Druck abgelesen oder an das System gemeldet werden. | Schalten Sie das System ab. Falls dieses unter Druck steht, lassen Sie den Druck manuell ab und senden Sie den Spanner zur Wartung ein. | Protokoll Display Bestät. | PFHC | Werkzeug |
2505 | Fehler | Alarm Pumpen-Drucksensor | Fehler der Drucksensorelektronik der Pumpe. Es kann kein Druck abgelesen oder an das System gemeldet werden. | Schalten Sie das System ab. Falls dieses unter Druck steht, lassen Sie den Druck manuell ab und senden Sie die Pumpe zur Wartung ein. | Protokoll Display Bestät. | PFHC | Werkzeug |
2506 | Fehler | Unerwartete Rotation im Uhrzeigersinn erkannt | Rotation der Mutter im Uhrzeigersinn während nach einem abgeschlossenen Spannvorgang auf den Druckablass gewartet wurde. Das Ergebnis wird ungültig. | Lassen Sie den Druck ab und spannen Sie die Mutter erneut. | Protokoll Display Konfiguration | PFHC | Werkzeug |
2507 | Fehler | Unerwartete Rotation gegen den Uhrzeigersinn erkannt | Rotation der Mutter gegen den Uhrzeigersinn während nach einem abgeschlossenen Spannvorgang auf den Druckablass gewartet wurde. Das Ergebnis wird ungültig. | Lassen Sie den Druck ab und spannen Sie die Mutter erneut. | Protokoll Display Konfiguration | PFHC | Werkzeug |
2508 | Fehler | Fehler des Pumpen- oder Spanner-Drucksensors | Zu große Differenz zwischen den Messwerten des Drucksensors in der Pumpe und dem Spanner. Die Druckbeaufschlagung wird angehalten. | Problem der Hydraulik oder mit der Kalibrierung der Drucksensoren. Starten Sie das System neu und versuchen Sie es erneut. Falls das Problem weiterhin besteht, wenden Sie sich an Ihren örtlichen Vertriebsmitarbeiter von Atlas Copco. | Protokoll Display Bestät. | PFHC | Werkzeug |
2509 | Fehler | Ausfall des Spanner-Drucksensors oder des Hydraulikschlauchs | Der Drucksensor des Spanners zeigt keinen Druck an, der Pumpensensor jedoch einen Druckanstieg. Die Druckbeaufschlagung wird angehalten. | Problem der Hydraulik oder mit der Kalibrierung der Drucksensoren. Starten Sie das System neu und versuchen Sie es erneut. Falls das Problem weiterhin besteht, wenden Sie sich an Ihren örtlichen Vertriebsmitarbeiter von Atlas Copco. | Protokoll Display Bestät. | PFHC | Werkzeug |
2510 | Fehler | Festlegen der benutzerdefinierten ID fehlgeschlagen | Das Festlegen der benutzerdefinierten ID ist fehlgeschlagen. | Starten Sie das System neu und überprüfen Sie die angeschlossenen Geräte. Wenn die benutzerdefinierte ID für das Gerät falsch ist, nehmen Sie die Einstellung erneut vor. | Protokoll Display Bestät. | PFHC | Werkzeug |
2511 | Info | Benutzerdefinierte ID wurde festgelegt | Das Festlegen der benutzerdefinierten ID war erfolgreich. | Protokoll Display Bestät. | PFHC | Werkzeug | |
2512 | Warnung | Falsch formatierter Barcode-String, ignoriert | Der gescannte String konnte nicht als Turmdaten-Barcode geparst werden. | Scannen Sie einen korrekten Turmdaten-QR-Code oder eine Turmbereichs-ID. | Protokoll Display Bestät. | PFHC | Werkzeug |
2513 | Fehler | Kein Pumpendruck erkannt | Das System versucht, Druck aufzubauen, es wird jedoch kein Druckanstieg an der Pumpe erkannt. Mögliche Ursache ist eine falsche Phasenfolge am dreiphasigen Stecker. | Schalten Sie das System ab und kehren Sie die Phasen des Stromanschlusses um. | Protokoll Display Bestät. | PFHC | Werkzeug |
2514 | Warnung | Alarm Spanner-Überdrehmoment | Am Knickschlüssel liegt ein zu hohes Drehmoment an. Dies kann zu Schäden am Drehmomentwandler führen. | Senken Sie das Drehmoment. | Protokoll | PFHC | Werkzeug |
2515 | Warnung | Alarm Spanner-Überdruck | Der Druck am Spanner ist zu hoch. | Senken Sie den Druck oder lassen Sie diesen ab. Überprüfen Sie die Hydraulikdruckparameter. | Protokoll | PFHC | Werkzeug |
2516 | Warnung | Unerwartete Pumpen- oder Spanner-Firmware | Unerwartete Pumpen- oder Spanner-Firmwareversion erkannt, System neu starten. Falls das Problem weiterhin besteht, kann das System eventuell trotzdem betrieben werden, achten Sie jedoch sorgfältig auf unerwartetes Verhalten. | Netzschalter des Systems aus- und einschalten | Protokoll Display Bestät. | PFHC | Werkzeug |
2517 | Fehler | Inkompatible Pumpen- oder Spanner-Firmwareversion, System neu starten. Das System kann nicht betrieben werden. | Inkompatible Pumpen- oder Spanner-Firmwareversion, System neu starten. Das System kann nicht betrieben werden. | Starten Sie das System neu, falls dies nicht hilft, tauschen Sie das fehlerhafte Gerät aus. Überprüfen Sie die angeschlossenen Geräte, um herauszufinden, welches sich nicht verbunden hat. | Protokoll Display Bestät. | PFHC | Werkzeug |
3000 | Fehler | Interner Software-Fehler der Steuerung | Softwarefehler in der Steuerung. | Den Kundendienst kontaktieren. | Protokoll Display Bestät. Konfiguration | IxB Power Focus 6000 Power Focus 8 Power Focus XC | Steuerung, Antrieb und StepSync |
3001 | Fehler | Akku der Controller-Uhr leer | Interne Batterie nähert sich dem Ende ihrer Lebensdauer. | Den Akku austauschen. | Protokoll Display Bestät. Konfiguration | Flex Power Focus 6000 Power Focus 8 StepSync Power Focus XC | Steuerung, Antrieb und StepSync |
3010 | Warnung | System überhitzt | Die Steuerung wurde überhitzt. | Abkühlen lassen. | Protokoll Display Konfiguration | Power Focus 6000 Power Focus 8 Power Focus XC | Steuerung, Antrieb und StepSync |
3011 | Warnung | Laufwerk hat zur Überhitzung der Controller-Hardware geführt | Abkühlen lassen. | Protokoll Display Konfiguration | Flex | Steuerung, Antrieb und StepSync | |
3013 | Warnung | Nutzung aufgrund hoher Controller-Temperatur eingeschränkt | Der Temperaturgrenzwert wurde erreicht. Die Verschraubung wurde gesperrt, um die Gefahr eines Herunterfahrens des Controllers aufgrund von Überhitzung zu verringern. | Warten Sie, bis der Controller abgekühlt ist. | Protokoll Display Konfiguration | Power Focus 6000 Power Focus 8 StepSync Power Focus XC | Steuerung, Antrieb und StepSync |
3020 | Warnung | Hardwarefehler der Steuerung | Protokoll Display Konfiguration | Flex IxB Power Focus 6000 Power Focus 8 StepSync Power Focus XC | Steuerung, Antrieb und StepSync | ||
3021 | Warnung | Systemspannungsproblem | Gleichspannung zu hoch oder zu niedrig. | Protokoll Display Konfiguration | Flex IxB Power Focus 6000 Power Focus 8 StepSync Power Focus XC | Steuerung, Antrieb und StepSync | |
3022 | Warnung | Steuerungsspannungsproblem Wechselstromeingangsspannung zu hoch | Gleichspannung zu hoch oder zu niedrig. | Eingangsspannung korrigieren | Protokoll Display | Power Focus 6000 Power Focus 8 StepSync Power Focus XC | Steuerung, Antrieb und StepSync |
3023 | Warnung | Steuerungsspannungsproblem Wechselstromeingangsspannung zu niedrig | Gleichspannung zu hoch oder zu niedrig. | Eingangsspannung korrigieren | Protokoll Display | Power Focus 6000 Power Focus 8 StepSync Power Focus XC | Steuerung, Antrieb und StepSync |
3024 | Warnung | Antriebsspannungsproblem: Wechselstromeingangsspannung zu hoch | Gleichspannung zu hoch oder zu niedrig. | Eingangsspannung korrigieren | Protokoll Display | Flex | Steuerung, Antrieb und StepSync |
3025 | Warnung | Antriebsspannungsproblem: Wechselstromeingangsspannung zu niedrig | Gleichspannung zu hoch oder zu niedrig. | Eingangsspannung korrigieren | Protokoll Display | Flex | Steuerung, Antrieb und StepSync |
3030 | Fehler | IP-Adressenkonflikt mit einem anderen Knoten im Netzwerk | Die eingestellte IP-Adresse wird von einem anderen Gerät im selben Netzwerk verwendet. | Die IP-Adresse an einem der Geräte ändern. | Protokoll Display Konfiguration | Flex Power Focus 6000 Power Focus 8 StepSync Power Focus XC PFHC | Steuerung, Antrieb und StepSync |
3031 | Info | Netzwerkkabel wurde entfernt | Der Träger der firmeneigenen Schnittstelle ist verloren gegangen (Kabel nicht angeschlossen). | Den Kabelanschluss prüfen. | Protokoll Display Konfiguration | Flex Power Focus 6000 Power Focus 8 StepSync Power Focus XC | Steuerung, Antrieb und StepSync |
3032 | Info | Pairing wurde gestartet | Werkzeugkopplung gestartet. | Protokoll Display Konfiguration | Power Focus 6000 Power Focus 8 Power Focus XC | Steuerung, Antrieb und StepSync | |
3033 | Info | Pairing erfolgreich | Werkzeugkopplung erfolgreich. | Protokoll Display Konfiguration | Power Focus 6000 Power Focus 8 Power Focus XC | Steuerung, Antrieb und StepSync | |
3034 | Info | Pairing fehlgeschlagen: Kein Werkzeug gefunden | Von der Steuerung wurde bei der Suche nach Geräten für das Funk-Pairing kein Werkzeug für das Pairing-Verfahren gefunden. | Das Werkzeug in den Pairing-Modus schalten und erneut versuchen. | Protokoll Display Konfiguration | Power Focus 6000 Power Focus 8 Power Focus XC | Steuerung, Antrieb und StepSync |
3035 | Fehler | Pairing fehlgeschlagen: Es wurde mehr als ein Werkzeug gefunden | Von der Steuerung wurde bei der Suche nach Geräten für das Funk-Pairing mehr als ein Werkzeug gefunden. | Wenn der Pairing-Modus an der Steuerung gestartet wird sicherstellen, dass nur ein Werkzeug sich im Pairing-Modus befindet. | Protokoll Display Konfiguration | Power Focus 6000 Power Focus 8 Power Focus XC | Steuerung, Antrieb und StepSync |
3036 | Fehler | Pairing fehlgeschlagen: Kommunikationsfehler | Während des Pairing-Verfahrens trat bei der Steuerung ein Verbindungsabbruch, eine unerwartete Antwort oder eine Zeitabschaltung auf. | Versuchen Sie noch einmal, ein Pairing-Verfahren auszuführen. Bei erneutem Fehler das Werkzeug warten. | Protokoll Display Konfiguration | Power Focus 6000 Power Focus 8 Power Focus XC | Steuerung, Antrieb und StepSync |
3037 | Info | Pairing fehlgeschlagen: Werkzeugplatz ist voll | Einen Werkzeugplatz freimachen. | Protokoll Display Konfiguration | Power Focus 6000 Power Focus 8 Power Focus XC | Steuerung, Antrieb und StepSync | |
3040 | Warnung | Not-Aus | Antrieb aufgrund eines Notstopps deaktiviert. | Not-Aus rückstellen. | Protokoll Display Konfiguration | Flex Power Focus 6000 Power Focus 8 StepSync Power Focus XC | Steuerung, Antrieb und StepSync |
3050 | Info | Systemuhr aktualisiert | Systemuhr wurde aktualisiert. | Protokoll Konfiguration | Flex IxB Power Focus 6000 Power Focus 8 StepSync Power Focus XC PFHC | Steuerung, Antrieb und StepSync | |
3051 | Fehler | Systemuhr-Fehler | Von der Echtzeituhr (RTC) der Hardware wurde die falsche Zeit abgelesen. | Den RTC-Akku austauschen. | Protokoll Display Bestät. Konfiguration | Flex IxB Power Focus 6000 Power Focus 8 StepSync Power Focus XC PFHC | Steuerung, Antrieb und StepSync |
3052 | Warnung | Fernstartkonfigurationsfehler | HW und SW für die Fernstartkonfiguration passen nicht zusammen. | Sicherstellen, dass der HW-DIP-Schalter zur ausgewählten Startquelle passt. | Protokoll Display Konfiguration | Power Focus 6000 Power Focus 8 StepSync Power Focus XC | Steuerung, Antrieb und StepSync |
3053 | Info | Laufwerk verbunden | StepSync-Laufwerk wurde verbunden. | Protokoll Display | Flex Power Focus 6000 Power Focus 8 StepSync Power Focus XC | Steuerung, Antrieb und StepSync | |
3054 | Info | Laufwerk getrennt | StepSync-Laufwerk getrennt. | Protokoll Display | Flex Power Focus 6000 Power Focus 8 StepSync Power Focus XC | Steuerung, Antrieb und StepSync | |
3055 | Warnung | Fehler bei Moduskonfiguration | Wird erzeugt, wenn der ausgewählte Modus falsch konfiguriert wird. Beispielsweise Konfiguration von zwei Bolzen mit der gleichen Bolzennummer oder dem gleichen Kanal, unvollständige Moduskonfiguration. | Überprüfen Sie ToolsTalk 2 auf Fehler bei der Moduskonfiguration. | Protokoll Display | Flex StepSync | Steuerung, Antrieb und StepSync |
3056 | Warnung | Kann nicht gestartet werden: Werkzeug oder Laufwerk fehlt | Wird erzeugt, wenn einem verwendeten Kanal ein Laufwerk oder Werkzeug fehlt. | Überprüfen Sie das Kanalmenü auf der MMS. Verbinden Sie das fehlende Laufwerk oder Werkzeug. | Protokoll Display | Flex StepSync | Steuerung, Antrieb und StepSync |
3057 | Info | Kann nicht gestartet werden: Der Kanal wird bereits verwendet | Erzeugt, wenn ein benötigter Kanal einer anderen virtuellen Station zugewiesen wurde. | Protokoll Display | Flex | Steuerung, Antrieb und StepSync | |
3058 | Info | Kein Modus ausgewählt | Modus auswählen. | Protokoll Display | Flex StepSync | Steuerung, Antrieb und StepSync | |
3059 | Warnung | Verbindung mit Lizenzmanager von Atlas Copco fehlgeschlagen | Zeigt an, dass der Controller keine Verbindung mit dem lokalen Lizenzmanager zum Erhalt von Lizenzen aufbauen konnte. | Lokales Netzwerk prüfen Wenn die Verbindung erneut fehlschlägt, warten Sie den Controller. | Protokoll Display Konfiguration | IxB Power Focus 6000 Power Focus 8 StepSync Power Focus XC | Steuerung, Antrieb und StepSync |
3061 | Warnung | Kann nicht gestartet werden: Freigabesignal ist niedrig | Protokoll Display | Flex StepSync | Steuerung, Antrieb und StepSync | ||
3062 | Warnung | Kann nicht gestartet werden: Stoppsignal ist hoch | Protokoll Display | Flex StepSync | Steuerung, Antrieb und StepSync | ||
3063 | Warnung | Kann nicht gestartet werden: Alle Kanäle gesperrt | Alle Kanäle wurden auf gesperrt gesetzt, daher kann keine Verschraubung gestartet werden. | Mindestens ein Kanal muss auf nicht gesperrt gesetzt sein. | Protokoll Display | Flex StepSync | Steuerung, Antrieb und StepSync |
3064 | Warnung | Fehlerhafte Trägernummer | Der Hex-Schalter eines FlexCarriers wurde auf Null gesetzt. | Setzen Sie den Schalter auf einen von Null verschiedenen Wert. | Protokoll Display | Flex | Steuerung, Antrieb und StepSync |
3065 | Warnung | Notaus-Konfigurationsstecker des Trägers vom falschen Typ oder fehlt | Der Notaus-Konfigurationsstecker eines Trägers fehlt oder der Stecker ist vom falschen Typ. | Setzen Sie einen Stecker des korrekten Typs ein. | Protokoll Display | Flex | Steuerung, Antrieb und StepSync |
3066 | Warnung | Trägerspannung Einlass Kein 3-phasiger Wechselstrom | Protokoll Display | Flex | Steuerung, Antrieb und StepSync | ||
3067 | Warnung | Trägerspannung Einlass Eine Wechselstromphase fehlt | Protokoll Display | Flex | Steuerung, Antrieb und StepSync | ||
3068 | Warnung | Träger: Interne 24-VDC-Stromversorgungseinheit defekt | Protokoll Display | Flex | Steuerung, Antrieb und StepSync | ||
3069 | Warnung | Träger 24-V-Ausgangsanschluss wegen Überstrom deaktiviert | Führen Sie einen System-Reset durch. | Protokoll Display | Flex | Steuerung, Antrieb und StepSync | |
3070 | Warnung | Träger, Hardware-Fehler PF6 FlexControl-Kabel OUT | Führen Sie einen System-Reset durch. | Protokoll Display | Flex | Steuerung, Antrieb und StepSync | |
3071 | Warnung | Träger, Hardware-Fehler PF6 FlexControl-Kabel IN | Führen Sie einen System-Reset durch. | Protokoll Display | Flex | Steuerung, Antrieb und StepSync | |
3072 | Warnung | Not-Halt Fehler 24-VDC-Stromversorgung durch Kurzschluss | Protokoll Display | Flex | Steuerung, Antrieb und StepSync | ||
3073 | Warnung | Kann nicht gestartet werden: Notstopp für System wurde ausgelöst | Dieses Ereignis wird beim Zuweisen von mehreren Spindeln durch „preStartCheckFailed“ aufgrund eines Notaus ausgelöst. | Setzen Sie den Notaus zurück. | Protokoll Display | Flex StepSync | Steuerung, Antrieb und StepSync |
3074 | Warnung | Träger überhitzt | Protokoll Display | Flex | Steuerung, Antrieb und StepSync | ||
3075 | Warnung | Trägertemperatur IO | Protokoll Display | Flex | Steuerung, Antrieb und StepSync | ||
3076 | Warnung | Träger: Überlast der internen 24-VDC-Stromversorgung | Der Stromausgang vom internen Netzteil ist zu hoch. | Trennen Sie andere Träger, die vom Netzteil mit Strom versorgt werden. Trennen Sie alle externen Geräte, die die 24-VDC-Stromversorgung nutzen. | Protokoll Display | Flex | Steuerung, Antrieb und StepSync |
3077 | Warnung | Träger: Interne 24-VDC-Stromversorgung Überspannung | Der Spannungsausgang vom internen Netzteil ist zu hoch. | Tauschen Sie den Träger aus. | Protokoll Display | Flex | Steuerung, Antrieb und StepSync |
3078 | Warnung | Träger: Interne 24-VDC-Stromversorgung Unterspannung | Der Spannungsausgang vom internen Netzteil ist zu niedrig. | Tauschen Sie den Träger aus. | Protokoll Display | Flex | Steuerung, Antrieb und StepSync |
3079 | Warnung | Externe Versorgung für Träger: 24-VDC-Überspannung | Die Sicherungs-Eingangsspannung ist größer als 27 VDC. | Passen Sie die Sicherungs-Eingangsspannung an. | Protokoll Display | Flex | Steuerung, Antrieb und StepSync |
3080 | Warnung | Externe Versorgung für Träger: 24-VDC-Unterspannung | Die Sicherungs-Eingangsspannung ist kleiner als 19 VDC. | Passen Sie die Sicherungs-Eingangsspannung an. | Protokoll Display | Flex | Steuerung, Antrieb und StepSync |
3081 | Warnung | Trägerspannung Einlass 3-Phasen-Wechselstrom-Überspannung | Die Eingangsspannung ist zu hoch. | Senken Sie die Eingangsspannung auf 400 VAC oder 480 VAC. | Protokoll Display | Flex | Steuerung, Antrieb und StepSync |
3082 | Warnung | Trägerspannung Einlass 3-Phasen-Wechselstrom-Unterspannung | Die Eingangsspannung ist zu niedrig. | Erhöhen Sie die Eingangsspannung auf 400 VAC oder 480 VAC. | Protokoll Display | Flex | Steuerung, Antrieb und StepSync |
3083 | Fehler | Falsche Anybus/Profisafe-Modul-Firmware | Protokoll Display | Flex Power Focus 6000 Power Focus 8 StepSync | Steuerung, Antrieb und StepSync | ||
3084 | Fehler | Laufzeitfehler Soft-PLC | eCLR wurde unkontrolliert beendet. | Protokoll Display Konfiguration | Flex Power Focus 6000 Power Focus 8 StepSync | Steuerung, Antrieb und StepSync | |
3085 | Warnung | Träger: Gebläsemodul außer Betrieb | Protokoll Display | Flex | Steuerung, Antrieb und StepSync | ||
3086 | Warnung | Träger: Gebläsemodul teilweise außer Betrieb | Protokoll Display | Flex | Steuerung, Antrieb und StepSync | ||
3087 | Warnung | Träger: Linkes Gebläsemodul außer Betrieb | Protokoll Display | Flex | Steuerung, Antrieb und StepSync | ||
3088 | Warnung | Träger: Linkes Gebläsemodul teilweise außer Betrieb | Protokoll Display | Flex | Steuerung, Antrieb und StepSync | ||
3089 | Warnung | Träger: Rechtes Gebläsemodul außer Betrieb | Protokoll Display | Flex | Steuerung, Antrieb und StepSync | ||
3090 | Warnung | Träger: Rechtes Gebläsemodul teilweise außer Betrieb | Protokoll Display | Flex | Steuerung, Antrieb und StepSync | ||
3096 | Warnung | Stärke des Mobilfunksignals niedrig | Der RSSI-Wert für die Mobilfunkverbindung liegt unterhalb des festgelegten Grenzwerts von -98 dBm. | Bewegen Sie das Werkzeug für eine bessere Verbindung sowie zur Vermeidung von Datenverlusten näher an die Mobilfunkantennen heran. | Konfiguration | IxB | Steuerung, Antrieb und StepSync |
3097 | Warnung | Mobilfunkverbindung unterbrochen | Das System hat die Verbindung zum Mobilfunknetzwerk verloren. |
| Protokoll Display Konfiguration | IxB | Steuerung, Antrieb und StepSync |
3100 | Warnung | Moduskonfiguration existiert nicht | Protokoll Display | Flex StepSync | Steuerung, Antrieb und StepSync | ||
3150 | Fehler | Software nicht IAM-kompatibel | IAM ist nicht mit der auf dem Controller installierten Software kompatibel. | IAM ersetzen. | Protokoll Display Bestät. | Flex IxB Power Focus 6000 Power Focus 8 StepSync Power Focus XC | Steuerung, Antrieb und StepSync |
3160 | Fehler | Neu installierte Software konnte nicht aktiviert werden | Bei der Aktivierung ist ein Problem aufgetreten. Wenn die neu installierte Software startet, dann erfolgt ein Rückfall zur vorherigen Betriebssoftware. Dieser Fehler tritt ausschließlich während der Softwareinstallation auf, wenn die neue Software nach drei Versuchen nicht gestartet werden konnte. | Nehmen Sie einen Export vor und wenden Sie sich für weitere Unterstützung an Atlas Copco. Notieren Sie die zu installierende Softwareversion sowie die funktionierende Softwareversion. | Protokoll Display Bestät. | Flex IxB Power Focus 6000 Power Focus 8 StepSync Power Focus XC | Steuerung, Antrieb und StepSync |
3161 | Fehler | Start in unerwarteter Softwarepartition | Die Steuerung wurde bei der inaktiven Softwareseite und nicht bei der erwarteten Softwareseite gestartet. | Notieren Sie die Softwareversion (wählen Sie auf der Startseite der Steuerung „Steuerung > Software“ aus). Versuchen Sie, die Steuerung neu zu starten und vergewissern Sie sich, dass sie beim Neustart mit der richtigen Software läuft. Wenn der Fehler bestehen bleibt, nehmen Sie einen Export vor und wenden Sie sich an Atlas Copco. | Protokoll Display Bestät. | Flex IxB Power Focus 6000 Power Focus 8 StepSync Power Focus XC | Steuerung, Antrieb und StepSync |
3500 | Fehler | Generischer Lizenzmanager-Fehler | Inkonsistenzen im verwendeten Eigenschaftsverwaltungssystem erkannt. | Wenden Sie sich an einen Atlas Copco-Vertreter. | Protokoll Display Bestät. | IxB Power Focus 6000 Power Focus 8 StepSync Power Focus XC | Steuerung, Antrieb und StepSync |
3501 | Fehler | Synchronisationsfehler Lizenzmanager | Protokoll Display Bestät. | IxB Power Focus 6000 Power Focus 8 StepSync Power Focus XC | Steuerung, Antrieb und StepSync | ||
3502 | Info | Lizenzmanager-Synchronisierung ausgeführt | IxB Power Focus 6000 Power Focus 8 StepSync Power Focus XC | Steuerung, Antrieb und StepSync | |||
3503 | Warnung | Lizenz-Manager: Andere Quelle wird verwendet | Die Lizenz wird von einer anderen Quelle genutzt. | Lizenzzuordnung prüfen. | Protokoll Display | IxB Power Focus 6000 Power Focus 8 StepSync Power Focus XC | Steuerung, Antrieb und StepSync |
3504 | Warnung | Neustart des Lizenzmanagers notwendig | Lizenzmanager erneut starten. | Protokoll Display | IxB Power Focus 6000 Power Focus 8 StepSync Power Focus XC | Steuerung, Antrieb und StepSync | |
3505 | Info | USB-Lizenzsynchronisierung gestartet | Protokoll | Power Focus 6000 Power Focus 8 Power Focus XC | Steuerung, Antrieb und StepSync | ||
3506 | Fehler | Fehler bei der USB-Lizenzsynchronisierung | Protokoll | Power Focus 6000 Power Focus 8 Power Focus XC | Steuerung, Antrieb und StepSync | ||
3507 | Info | USB-Lizenzsynchronisierung abgeschlossen | Protokoll | Power Focus 6000 Power Focus 8 | Steuerung, Antrieb und StepSync | ||
3508 | Info | Eine oder mehrere Lizenzen laufen bald ab. Bitte stellen Sie sicher, dass ein Lizenzserver konfiguriert wurde | Lizenzen aktualisieren. | Protokoll Display Konfiguration | IxB Power Focus 6000 Power Focus 8 StepSync Power Focus XC | Steuerung, Antrieb und StepSync | |
3511 | Warnung | Eine Ihrer Lizenzen besitzt eine abweichende Lizenzdefinition | Inkonsistenzen in einer zu verwendenden Lizenz erkannt. | Wenden Sie sich an einen Atlas Copco-Vertreter. | Protokoll Display Konfiguration | IxB Power Focus 6000 Power Focus 8 StepSync Power Focus XC | Steuerung, Antrieb und StepSync |
3550 | Warnung | Lizenz fehlt | Korrekte Lizenz installieren. | Protokoll Display Konfiguration | IxB Power Focus 6000 Power Focus 8 StepSync Power Focus XC | Steuerung, Antrieb und StepSync | |
3551 | Warnung | Drahtlose Kommunikation durch Lizenzierung deaktiviert | Zuweisung der Standalone-Lizenz zur virtuellen Station aufheben. | Protokoll Display Konfiguration | IxB Power Focus 6000 Power Focus 8 StepSync Power Focus XC | Steuerung, Antrieb und StepSync | |
4010 | Info | Werkzeug durch digitalen Eingang gesperrt | Das Werkzeug ist über ein Digitaleingangssignal gesperrt. | Protokoll Display Konfiguration | Flex IxB Power Focus 6000 Power Focus 8 StepSync Power Focus XC | Verschraubungsvorgang | |
4011 | Info | Werkzeug gesperrt durch Open Protocol | Das Werkzeug ist durch Open Protocol gesperrt. | Protokoll Display Konfiguration | Flex IxB Power Focus 6000 Power Focus 8 StepSync Power Focus XC | Verschraubungsvorgang | |
4012 | Info | Werkzeug durch Feldbus gesperrt | Das Werkzeug ist durch den Feldbus gesperrt. | Protokoll Display Konfiguration | Flex Power Focus 6000 Power Focus 8 StepSync Power Focus XC | Verschraubungsvorgang | |
4013 | Info | Werkzeug durch Stecknuss-Selektor gesperrt | Das Tool ist gesperrt, wenn der Aufsatz-Selektor von der virtuellen Station getrennt wird. | Entsperren durch Master-Freigabe. | Protokoll Display Konfiguration | IxB Power Focus 6000 Power Focus 8 Power Focus XC | Verschraubungsvorgang |
4014 | Info | Werkzeug durch Soft-PLC gesperrt | Soft-PLC-Signal hat das Werkzeug gesperrt. | Entsperren durch Master-Freigabe. | Protokoll Display Konfiguration | Flex Power Focus 6000 Power Focus 8 StepSync Power Focus XC | Verschraubungsvorgang |
4015 | Info | Lösen deaktiviert | Die Lösefunktion ist im Verschraubungsprogramm deaktiviert. | Protokoll Display Konfiguration | Flex IxB Power Focus 6000 Power Focus 8 StepSync Power Focus XC | Verschraubungsvorgang | |
4016 | Info | Verschraubung deaktiviert | Protokoll Display Konfiguration | Flex IxB Power Focus 6000 Power Focus 8 StepSync Power Focus XC | Verschraubungsvorgang | ||
4017 | Info | Lösen nicht konfiguriert | Die Lösefunktion ist im gewählten Verschraubungsprogramm nicht konfiguriert | Auswahl eines anderen Verschraubungsprogramms. | Protokoll Display Konfiguration | Flex IxB Power Focus 6000 Power Focus 8 StepSync Power Focus XC | Verschraubungsvorgang |
4020 | Info | Zu viele NIO-Verschraubungen | In der Gruppe wurde der Wert für max. aufeinanderfolgende NIO-Verschraubungen überschritten | Protokoll Display Konfiguration | Flex IxB Power Focus 6000 Power Focus 8 StepSync Power Focus XC | Verschraubungsvorgang | |
4025 | Info | Kein Verschraubungsprogramm ausgewählt | Kein Verschraubungsprogramm ausgewählt. | Verschraubungsprogramm oder Gruppensequenz auswählen. | Display Konfiguration | IxB Power Focus 6000 Power Focus 8 Power Focus XC | Verschraubungsvorgang |
4030 | Info | Gruppensequenz abgebrochen | Die Gruppensequenz wurde abgebrochen. | Protokoll Konfiguration | Flex IxB Power Focus 6000 Power Focus 8 StepSync Power Focus XC PFHC | Verschraubungsvorgang | |
4031 | Info | Max. Zeit bis zum Abschluss der Gruppensequenz erreicht | Protokoll Display Konfiguration | Flex IxB Power Focus 6000 Power Focus 8 StepSync Power Focus XC | Verschraubungsvorgang | ||
4032 | Info | Max. Zeit bis zum Abschluss der ersten Verschraubung erreicht | Protokoll Display Konfiguration | Flex IxB Power Focus 6000 Power Focus 8 StepSync Power Focus XC | Verschraubungsvorgang | ||
4035 | Info | Gesperrt durch Liniensteuerung | Protokoll Display Konfiguration | IxB Power Focus 6000 Power Focus 8 Power Focus XC | Verschraubungsvorgang | ||
4040 | Info | Durch alternativen Identifikator gesperrt | Werkzeug durch alternativen Identifikator arretiert. | Protokoll Display Konfiguration | IxB Power Focus 6000 Power Focus 8 Power Focus XC | Verschraubungsvorgang | |
4050 | Ungültige Stecknusskonfiguration | Verschraubungsprogramm mehreren Stecknüssen zugewiesen. | Verschraubungsprogramm mehreren Stecknüssen zugewiesen. | Protokoll Display Konfiguration | IxB Power Focus 6000 Power Focus 8 Power Focus XC | Verschraubungsvorgang | |
4060 | Info | Werkzeug nach abgeschlossener Charge gesperrt | Wenn Sie eine Charge mit der Kennzeichnung \"Werkzeugarretierung\" auf einer abgeschlossenen Chargensequenz laufen lassen, wird dieses Ereignis erstellt, wenn der Auslöser gedrückt wird. | Entriegeln Sie es mithilfe des Signals \"Werkzeugentriegelung\" nach Abschluss des Vorgangs. | Protokoll Display Konfiguration | Flex IxB Power Focus 6000 Power Focus 8 StepSync Power Focus XC | Verschraubungsvorgang |
4070 | Info | Prozess tritt in manuellen Modus ein | Gibt an, dass der manuelle Modus für eine virtuelle Station aktiviert wurde. | Konfiguration | IxB Power Focus 6000 Power Focus 8 Power Focus XC | Verschraubungsvorgang | |
4071 | Info | Prozess tritt in den automatischen Modus ein | Gibt an, dass der automatische Modus für eine virtuelle Station gewählt wurde. | Konfiguration | IxB Power Focus 6000 Power Focus 8 Power Focus XC | Verschraubungsvorgang | |
4072 | Info | Schraubenprüfung | Konfiguration | Flex StepSync | Verschraubungsvorgang | ||
4073 | Info | Werkzeug-Nullposition aktualisiert | Zeigt an, dass die Werkzeug-Nullposition mithilfe von Signalen festgelegt wurde. | Konfiguration | Flex IxB Power Focus 6000 Power Focus 8 StepSync Power Focus XC | Verschraubungsvorgang | |
4100 | Warnung | Bezeichner nicht akzeptiert: Ungültige Zeichenkettenlänge | Display Konfiguration | Flex IxB Power Focus 6000 Power Focus 8 StepSync Power Focus XC | Verschraubungsvorgang | ||
4101 | Warnung | Zeichenkettenauswahl nicht erfolgreich: Mehrere Übereinstimmungen | Display Konfiguration | Flex IxB Power Focus 6000 Power Focus 8 StepSync Power Focus XC | Verschraubungsvorgang | ||
4102 | Warnung | Zeichenkettenauswahl nicht erfolgreich: Keine Übereinstimmung gefunden | Display Konfiguration | Flex IxB Power Focus 6000 Power Focus 8 StepSync Power Focus XC | Verschraubungsvorgang | ||
4103 | Warnung | Bezeichner nicht akzeptiert: Identische Zeichenkette bereits erhalten | Display Konfiguration | Flex IxB Power Focus 6000 Power Focus 8 StepSync Power Focus XC | Verschraubungsvorgang | ||
4104 | Warnung | Bezeichner nicht akzeptiert: Keine Übereinstimmung gefunden | Display Konfiguration | Flex IxB Power Focus 6000 Power Focus 8 StepSync Power Focus XC | Verschraubungsvorgang | ||
4500 | Info | Ergebnis Antriebsfehler | Interner Antriebsfehler oder Antriebsverlust erkannt. | Konfiguration | Power Focus 6000 Power Focus 8 Power Focus XC | Verschraubungsvorgang | |
4501 | Info | Ergebnis Rehit | Versuch, eine schon festgezogene Schraube anzuziehen, während die Rehit-Erkennung aktiviert ist. | Konfiguration | IxB Power Focus 6000 Power Focus 8 Power Focus XC | Verschraubungsvorgang | |
4502 | Info | Ergebnis Soft-Start-Drehmoment zu niedrig | Softstart-Drehmoment unter der Mindestgrenze. | Konfiguration | IxB Power Focus 6000 Power Focus 8 Power Focus XC | Verschraubungsvorgang | |
4503 | Info | Ergebnis Soft-Start-Drehmoment zu hoch | Softstart-Drehmoment über der Höchstgrenze. | Konfiguration | IxB Power Focus 6000 Power Focus 8 Power Focus XC | Verschraubungsvorgang | |
4504 | Info | Ergebnis Self-Tap-Drehmoment zu hoch | Self-Tap-Drehmoment über der Höchstgrenze. | Konfiguration | IxB Power Focus 6000 Power Focus 8 Power Focus XC | Verschraubungsvorgang | |
4505 | Info | Ergebnis Self-Tap-Drehmoment zu niedrig | Self-Tap-Drehmoment unter der Mindestgrenze. | Konfiguration | IxB Power Focus 6000 Power Focus 8 Power Focus XC | Verschraubungsvorgang | |
4506 | Info | Ergebnis Sicherheitsdrehmoment zu niedrig | Automatisch berechneter Drehmomentwert zur Sicherstellung eines korrekt montierten Drehmomentsensors. | Konfiguration | IxB Power Focus 6000 Power Focus 8 Power Focus XC | Verschraubungsvorgang | |
4507 | Info | Ergebnis Einschraubdrehmoment zu hoch | Einschraubdrehmoment über der Höchstgrenze. | Konfiguration | IxB Power Focus 6000 Power Focus 8 Power Focus XC | Verschraubungsvorgang | |
4508 | Info | Ergebnis Einschraubwinkel zu hoch | Einschraubwinkel über der Höchstgrenze. | Konfiguration | IxB Power Focus 6000 Power Focus 8 Power Focus XC | Verschraubungsvorgang | |
4509 | Info | Ergebnis Einschraubdauer zu hoch | Einschraubzeit über der Höchstgrenze. | Konfiguration | IxB Power Focus 6000 Power Focus 8 Power Focus XC | Verschraubungsvorgang | |
4510 | Info | Ergebnis Einschraubdauer zu niedrig | Einschraubzeit unter der Mindestgrenze. | Konfiguration | IxB Power Focus 6000 Power Focus 8 Power Focus XC | Verschraubungsvorgang | |
4511 | Info | Ergebnis Einschraubdrehmoment zu niedrig | Einschraubdrehmoment unter der Mindestgrenze. | Konfiguration | IxB Power Focus 6000 Power Focus 8 Power Focus XC | Verschraubungsvorgang | |
4512 | Info | Ergebnis Einschraubwinkel zu niedrig | Einschraubwinkel unter der Mindestgrenze. | Konfiguration | IxB Power Focus 6000 Power Focus 8 Power Focus XC | Verschraubungsvorgang | |
4513 | Info | Ergebnis Istwert-Drehmoment zu hoch | Drehmoment für letzte Stufe über der Höchstgrenze. | Konfiguration | IxB Power Focus 6000 Power Focus 8 Power Focus XC | Verschraubungsvorgang | |
4514 | Info | Ergebnis Istwert-Winkel zu hoch | Winkel für letzte Stufe über der Höchstgrenze. | Konfiguration | IxB Power Focus 6000 Power Focus 8 Power Focus XC | Verschraubungsvorgang | |
4515 | Info | Ergebnis Istwert-Drehmoment zu niedrig | Drehmoment für letzte Stufe unter der Mindestgrenze. | Konfiguration | IxB Power Focus 6000 Power Focus 8 Power Focus XC | Verschraubungsvorgang | |
4516 | Info | Ergebnis Istwert-Winkel zu niedrig | Winkel für letzte Stufe unter der Mindestgrenze. | Konfiguration | IxB Power Focus 6000 Power Focus 8 Power Focus XC | Verschraubungsvorgang | |
4517 | Info | Ergebnis Zeitüberschreitung Verschraubung | Zeitlimit für Verschraubung überschritten. Für allgemeine Verschraubungsstrategien beträgt die maximale Verschraubungszeit 30 Sekunden. Für eine mehrstufige maximale Verschraubungszeit hängt die maximale Zeitbegrenzung von der Stufenbeschränkung ab. Der Fehlercode ist abhängig von der Verschraubungsphase. | Verschraubung wiederholen: | Konfiguration | IxB Power Focus 6000 Power Focus 8 Power Focus XC | Verschraubungsvorgang |
4518 | Info | Ergebnis Start verloren | Der Startknopf am Werkzeug wurde losgelassen, bevor der Sollwert erreicht wurde. Bei allgemeinen Verschraubungsstrategien darf der Startknopf nicht losgelassen werden, bevor die Verschraubungsphase abgeschlossen ist. Bei Multistep wird der Fehler angezeigt, wenn der Startknopf losgelassen wird, bevor der Sollwert in einer bestimmten Stufe erreicht wurde. | Konfiguration | IxB Power Focus 6000 Power Focus 8 Power Focus XC | Verschraubungsvorgang | |
4519 | Info | Vorzeitiger Drehmomentverlust | Die Stecknuss rutschte von der Mutter. | Konfiguration | IxB Power Focus 6000 Power Focus 8 Power Focus XC | Verschraubungsvorgang | |
4520 | Info | Ergebnis Ziel vor letztem Schritt erreicht | Das Sollmoment wurde vor der letzten Stufe des Verschraubungsprogramms erreicht. | Konfiguration | IxB Power Focus 6000 Power Focus 8 Power Focus XC | Verschraubungsvorgang | |
4521 | Info | Ergebnis Post-View-Drehmoment zu niedrig | Drehmoment nach Anzeige unter der Mindestgrenze. | Konfiguration | IxB Power Focus 6000 Power Focus 8 Power Focus XC | Verschraubungsvorgang | |
4522 | Info | Ergebnis Post-View-Drehmoment zu hoch | Drehmoment nach Anzeige über der Höchstgrenze. | Konfiguration | IxB Power Focus 6000 Power Focus 8 Power Focus XC | Verschraubungsvorgang | |
4523 | Info | Ergebnis Post-View-Drehmoment Intervall nicht erreicht | Intervall Drehmoment nach Anzeige nicht erreicht. | Konfiguration | IxB Power Focus 6000 Power Focus 8 Power Focus XC | Verschraubungsvorgang | |
4524 | Info | Ergebnis Drehmomentausgleich Intervall nicht erreicht | Momentkompensationsintervall-Winkel vor Einschraubende nicht erreicht. | Konfiguration | IxB Power Focus 6000 Power Focus 8 Power Focus XC | Verschraubungsvorgang | |
4525 | Info | Ergebnis der Werkzeugbewegung überschritten | Von einem detaillierten NOK-Verschraubungsstatus. | Konfiguration | IxB Power Focus 6000 Power Focus 8 Power Focus XC | Verschraubungsvorgang | |
4526 | Info | Ergebnis SafetyCurrMon-Sensor Fehlzuordnung | Stromüberwachungsfehler. | IxB Power Focus 6000 Power Focus 8 Power Focus XC | Verschraubungsvorgang | ||
4527 | Info | Ergebnis der Werkzeugbewegung überschritten | IxB Power Focus 6000 Power Focus 8 Power Focus XC | Verschraubungsvorgang | |||
4538 | Info | Ergebnis Istwert-Überwachungs-Drehmoment zu niedrig | Endgültiges Überwachungsdrehmoment wurde nicht erreicht. | Konfiguration | IxB Power Focus 6000 Power Focus 8 Power Focus XC | Verschraubungsvorgang | |
4543 | Info | Ergebnisüberwachung hoch | Nur Schraubenschlüssel. Entdeckten überschrittenen Festziehwert überwachen. | Konfiguration | IxB Power Focus 6000 Power Focus 8 Power Focus XC | Verschraubungsvorgang | |
4545 | Info | Ergebnis Kein Rest-Drehmoment | Nur Schraubenschlüssel. Restdrehmoment lag unter der Schwelle. | Konfiguration | IxB Power Focus 6000 Power Focus 8 Power Focus XC | Verschraubungsvorgang | |
4546 | Info | Ergebnis Überdrehzahl | Nur Schraubenschlüssel. Schraubschlüssel-Gyro konnte Winkel aufgrund der hohen Geschwindigkeit nicht messen. | Konfiguration | IxB Power Focus 6000 Power Focus 8 Power Focus XC | Verschraubungsvorgang | |
4547 | Info | Ergebnis Effektives Lösen | Nur Schraubenschlüssel. Schlüssel hat eine unerwartete Lockerung festgestellt. | Konfiguration | IxB Power Focus 6000 Power Focus 8 Power Focus XC | Verschraubungsvorgang | |
4548 | Info | Ergebnis Final Unter Soll | Enddrehmoment liegt unter dem im Verschraubungsprogramm eingestellten Sollmoment. | Konfiguration | IxB Power Focus 6000 Power Focus 8 Power Focus XC | Verschraubungsvorgang | |
4549 | Info | TurboTight-Zeitlimit überschritten | Konfiguration | IxB Power Focus 6000 Power Focus 8 Power Focus XC | Verschraubungsvorgang | ||
4550 | Info | Ergebnis Einschraubimpulse hoch | Maximale Anzahl von Eindrehungs-Impulsen ist überschritten. | Konfiguration | IxB Power Focus 6000 Power Focus 8 Power Focus XC | Verschraubungsvorgang | |
4551 | Info | Ergebnis Einschraubimpulse niedrig | Die Eindrehung ist abgeschlossen, bevor die Mindestanzahl von Eindrehungs-Impulsen erreicht ist. | Konfiguration | IxB Power Focus 6000 Power Focus 8 Power Focus XC | Verschraubungsvorgang | |
4552 | Info | Ergebnis letzte Impulse hoch | Maximale Anzahl von Impulsen überschritten. | Konfiguration | IxB Power Focus 6000 Power Focus 8 Power Focus XC | Verschraubungsvorgang | |
4553 | Info | Ergebnis letzte Impulse niedrig | Die Anziehung ist abgeschlossen, bevor die Mindestanzahl von Impulsen erreicht ist. | Konfiguration | IxB Power Focus 6000 Power Focus 8 Power Focus XC | Verschraubungsvorgang | |
4554 | Info | Strom bei Abschaltung zu hoch | Strom bei Abschaltung überschritt Stromgrenze Hoch. | Konfiguration | IxB Power Focus 6000 Power Focus 8 Power Focus XC | Verschraubungsvorgang | |
4555 | Info | Strom bei Abschaltung zu niedrig | Gemessener Strom bei Abschaltung lag unter Stromgrenze Niedrig. | Konfiguration | IxB Power Focus 6000 Power Focus 8 Power Focus XC | Verschraubungsvorgang | |
4556 | Info | Nicht kategorisierter Multistep-Fehler | Ein Fehler in der mehrstufigen Konfiguration, oft bei der Werkzeugvalidierung. | Konfiguration | IxB Power Focus 6000 Power Focus 8 Power Focus XC | Verschraubungsvorgang | |
4557 | Info | Ergebnis Überlast | Konfiguration | IxB Power Focus 6000 Power Focus 8 Power Focus XC | Verschraubungsvorgang | ||
4600 | Warnung | Daten verwerfen oder Daten zurückhalten verwendet in Kombination mit Gruppenverschraubung. Die Signale haben keinen Effekt | Daten verwerfen oder Daten zurückhalten werden nur für Arbeitsaufgaben ohne Gruppensteuerung unterstützt. Wählen Sie eine andere Arbeitsaufgabe aus, wenn die Signale verwendet werden müssen. | Flex StepSync | Verschraubungsvorgang | ||
4601 | Info | Daten zurückhalten aktiv: Verschraubungsergebnis wird gesendet, sobald das Signal niedrig ist. | Flex StepSync | Verschraubungsvorgang | |||
4602 | Info | Daten verwerfen aktiv: Verschraubungsergebnis verworfen. | Flex StepSync | Verschraubungsvorgang | |||
5010 | Warnung | Ungültige Parameterwerte für Verschraubungsprogramm | Die Parameter im ausgewählten Verschraubungsprogramm sind ungültig | Überprüfen Sie die Konfiguration des ausgewählten Verschraubungsprogramms, um den Wert des Parameters zu finden und zu ändern. | Protokoll Display Konfiguration | Flex IxB Power Focus 6000 Power Focus 8 StepSync Power Focus XC PFHC | Programmkonfiguration |
5011 | Warnung | Programmspeicher im Werkzeug konnte nicht vorbereitet werden | Es ist nicht möglich, die aktuelle Speichergröße des Programms im STB-Werkzeug auszulesen oder den Programmspeicher für das Herunterladen des aktualisierten - oder neu ausgewählten - Verschraubungsprogramms auf das STB-Tool vorzubereiten. |
| Protokoll Display Konfiguration | Power Focus 6000 Power Focus 8 Power Focus XC | Programmkonfiguration |
5020 | Info | Hauptstarter ist nicht die aktive Startquelle | Wird ausgelöst, wenn nur der Schubstarter konfiguriert wurde und der Benutzer den Hauptstartknopf drückt. Wird so lange ausgelöst, bis der Schubstarter gedrückt wird. | Den Schubstarter zum Starten des Werkzeugs drücken. | Protokoll Display Konfiguration | IxB Power Focus 6000 Power Focus 8 Power Focus XC | Programmkonfiguration |
5030 | Info | Die Komplexität des Verschraubungsprogramms überschreitet die Werkzeugkapazität | Das gewählte Verschraubungsprogramm ist für das verwendete STB-Werkzeug zu komplex. Das Werkzeug wird gesperrt. | Reduzieren Sie die Komplexität des Verschraubungsprogramms oder wählen Sie ein anderes Programm. | Protokoll Display Konfiguration | Power Focus 6000 Power Focus 8 Power Focus XC | Programmkonfiguration |
6010 | Info | Zubehör angeschlossen | Zubehör an Steuerung angeschlossen. | Protokoll Display Bestät. Konfiguration | Flex IxB Power Focus 6000 Power Focus 8 StepSync Power Focus XC | Zubehör | |
6020 | Info | Zubehör getrennt | Zubehör von Steuerung getrennt. | Protokoll Display Bestät. Konfiguration | Flex IxB Power Focus 6000 Power Focus 8 StepSync Power Focus XC | Zubehör | |
6021 | Warnung | Feldbus offline | Keine Kommunikation mit dem Feldbus. | Protokoll Display Bestät. Konfiguration | Flex Power Focus 6000 Power Focus 8 StepSync Power Focus XC | Zubehör | |
6030 | Warnung | Zubehör-Adressenkonflikt | Es sind zwei oder mehr Zubehörgeräte mit derselben Adresse angeschlossen. | Ändern Sie die Adresse am Zubehör. | Protokoll Display Bestät. Konfiguration | Flex IxB Power Focus 6000 Power Focus 8 StepSync Power Focus XC | Zubehör |
6040 | Warnung | Zubehör-Kommunikationsfehler | Zeitweise auftretender Kommunikationsfehler mit dem Zubehör. | Kabel und Anschlüsse prüfen. | Protokoll Display Konfiguration | Flex IxB Power Focus 6000 Power Focus 8 StepSync Power Focus XC | Zubehör |
6041 | Warnung | Feldbusfehler | Kommunikationsfehler mit dem Feldbus. |
| Protokoll Display Bestät. Konfiguration | Flex Power Focus 6000 Power Focus 8 StepSync | Zubehör |
6042 | Warnung | Abweichung bei Feldbusmodul | Das installierte Feldbusmodul passt nicht zum konfigurierten Modul. | Ändern Sie die Konfiguration, sodass diese zum installierten Modul passt, oder tauschen Sie das installierte Modul gegen das korrekte aus. | Protokoll Display Bestät. Konfiguration | Flex Power Focus 6000 Power Focus 8 StepSync | Zubehör |
6043 | Warnung | Überlauf des Feldbus-Ausgangspuffers | Der für die Feldbuskommunikation verwendete Ausgangspuffer ist ausgeschöpft und ein Überlauf des Puffers ist eingetreten. Eine oder mehrere Signalaktualisierungen wurden verworfen. | Halten Sie die Feldbuskommunikation und die Feldbusdiagnose (falls verwendet) an, um den Puffer wiederherzustellen. Falls dieses Ereignis regelmäßig eintritt, überprüfen Sie die Einrichtung der Feldbuskommunikation einschließlich des SPS-Programms: Zu häufige Aktualisierungen im Verhältnis zu Ihrem Aktualisierungsintervall können zu diesem Szenario führen. | Protokoll Display Bestät. Konfiguration | Flex Power Focus 6000 Power Focus 8 StepSync | Zubehör |
6044 | Warnung | Falsche ID des Feldbus-Providers | Das installierte Feldbusmodul wird nicht unterstützt. | Verbinden Sie ein unterstütztes Feldbusmodul von Atlas Copco. | Protokoll Display Bestät. | Power Focus 8 | Zubehör |
6050 | Info | Falsche Stecknuss ausgewählt | Wird ausgelöst, wenn keine oder die falsche Stecknuss ausgewählt wurde. | Protokoll Display Konfiguration | IxB Power Focus 6000 Power Focus 8 Power Focus XC | Zubehör | |
6090 | Warnung | Barcode-Lesegerät konnte nicht identifiziert werden | Wenn keine spezifische Seriennummer gefunden wird. | Das Barcode-Lesegerät konfigurieren. | Protokoll Display Bestät. Konfiguration | Flex Power Focus 6000 Power Focus 8 StepSync Power Focus XC PFHC | Zubehör |
7010 | Info | Anzuzeigender Meldungstext | Allgemeines Ereignis für die Anzeige von Meldungen. | Display Bestät. Konfiguration | Flex IxB Power Focus 6000 Power Focus 8 StepSync Power Focus XC PFHC | Nachricht | |
8200 | Info | Fehler beim Öffnen des Seriellen Ports | Der zur Nutzung vorgesehene Serielle Port konnte nicht geöffnet werden. | Prüfen Sie die Anschlüsse des Seriellen Ports. | Display Konfiguration | IxB Power Focus 6000 Power Focus 8 Power Focus XC | Verschiedenes |
8300 | Warnung | Zeitüberschreitung bei Kommunikation mit Open Protocol Client | Zeitüberschreitung bei der Kommunikation mit einem Open Protocol Client. Es wurde keine Keep-Alive-Nachricht oder kein Keep-Alive-Befehl innerhalb der erwarteten Zeit gesendet. |
| Protokoll Display Konfiguration | Flex IxB Power Focus 6000 Power Focus 8 StepSync Power Focus XC | Verschiedenes |
8214 | Fehler | Falsche Version der EHMI-Software | Die EHMI-Softwareversion ist mit dem Controller nicht kompatibel. | Aktualisieren Sie die EHMI-Softwareversion. | Protokoll Display Bestät. Konfiguration | IxB Power Focus 6000 Power Focus 8 Power Focus XC | Verschiedenes |
Listet Produkte auf, für die der Ereigniscode verfügbar ist.
Gruppe, zu der die Ereigniscodes gehören.
Eine kurze Beschreibung des Ereignisses und des Grundes für dessen Eintritt.
Gegebenenfalls werden Anweisungen zum Löschen des Ereignisses angegeben.
Teilt dem Benutzer mit, ob das Ereignis im Ereignisprotokoll gespeichert werden soll. Beim in dieser Liste angegebenen Wert handelt es sich um die Standardeinstellung.
Teilt dem Benutzer mit, ob das Ereignis auf dem Bildschirm angezeigt werden soll. Beim in dieser Liste angegebenen Wert handelt es sich um die Standardeinstellung.
Teilt dem Benutzer mit, ob das Ereignis vor dem Fortfahren bestätigt werden muss. Beim in dieser Liste angegebenen Wert handelt es sich um die Standardeinstellung.
Die spezifische Ereignisnummer
Art des Ereignisses: Info, Warnung und Fehler.
Ein beschreibender Name des Ereignisses
Arbeiten mit der Registerkarte Einstellungen
Netzwerkkonfigurationen
Das Werkzeug kann für drahtlosen Zugriff über einen Webbrowser in einem lokalen Netzwerk (LAN) mittels des IPv4-Protokolls konfiguriert werden.
Optional kann das Werkzeug als Client oder als Zugangspunkt für andere Geräte verwendet werden.
Öffnen Sie die Abdeckung am USB-Anschluss der Handsteuerung.
Verbinden Sie einen PC mit dem USB-C-Anschluss an der Handsteuerung. Um sicherzustellen, dass der PC genügend Leistung an die Handsteuerung abgibt, verwenden Sie die USB-3.0-Anschlüsse.
Um auf die Konfigurations-GUI zuzugreifen, geben Sie die folgende Adresse in Ihren Browser ein: 164.254.1.1/config.html.
Weitere Informationen finden Sie im Abschnitt Webbrowser-Anforderungen.
Konfiguration von Kanälen
Öffnen Sie Einstellungen im Hauptmenü und wählen Sie im linken Fenster Netzwerk aus.
Wählen Sie im Feld Kanäle die Frequenz (2,4 GHz oder 5 G Hz) und dann Bearbeiten.
Aktivieren oder deaktivieren Sie Kanäle.
Konfiguration eines Drahtlos-Client
Öffnen Sie Einstellungen im Hauptmenü und wählen Sie im linken Fenster Netzwerk aus.
Wählen Sie im Feld Drahtloser Client Bearbeiten aus.
Setzen Sie Aktiviert auf Ein.
Setzen Sie DHCP je nach Konfiguration auf Ein oder Aus. Wenn es auf Aus gesetzt wurde, geben Sie die erforderlichen Informationen ein, die vom lokalen Systemadministrator bereitgestellt wurden.
IP-Adresse
Subnetzmaske
Gateway
Geben Sie einen Netzwerknamen (SSID) ein.
Wählen Sie im Feld Sicherheit Modus aus und wählen Sie einen Sicherheitsmodus aus der Liste. Wenn WPA2 Privat ausgewählt ist, geben Sie einen Sicherheitsschlüssel ein.
Geben Sie die Sicherheitsparameter ein und importieren Sie Zertifizierungsdateien und Schlüssel, falls erforderlich.
Bearbeiten Sie gegebenenfalls die Option Optionale Einstellungen.
Wählen Sie Übernehmen.
Das Werkzeug stellt eine Drahtlosverbindung zum Netzwerk her, was durch dauerhaftes Leuchten der blauen Verbindungs-LED am Werkzeug angezeigt wird.
Um drahtlos auf die Benutzeroberfläche zuzugreifen, geben Sie die IP-Adresse in einen Webbrowser ein.
Konfiguration des Werkzeugs als Drahtloser Zugangspunkt

Wenn zuvor mehrere Kanäle unter Drahtlos-Client-Modus konfiguriert wurden, dann wird durch Aktivieren von Drahtlos-AP-Modus die Kanalliste aktualisiert, sodass diese nur den aktuellen/standardmäßigen Kanal für den Drahtlos-AP-Modus enthält.
Öffnen Sie Einstellungen im Hauptmenü und wählen Sie im linken Fenster Netzwerk aus.
Wählen Sie im Feld Drahtloser ZP Bearbeiten aus.
Setzen Sie Aktiviert auf Ein.
Geben Sie die erforderlichen Informationen ein, die vom lokalen Systemadministrator bereitgestellt werden.
IP-Adresse
Subnetzmaske
Gateway
Setzen Sie für die Vergabe von IP-Adressen DHCP-Server auf Ein und geben Sie den IP-Bereichsanfang und das IP-Bereichsende ein.
Geben Sie einen Netzwerknamen (SSID) ein.
Wählen Sie im Feld Sicherheit Modus aus und wählen Sie einen Sicherheitsmodus aus der Liste. Wenn WPA2 Privat ausgewählt ist, geben Sie einen Sicherheitsschlüssel ein.
Wählen Sie Übernehmen.
Serververbindungen
Die Handsteuerung kann zur Kommunikation mit Servern eingerichtet werden, welche das folgende Atlas Copco-Softwareprodukt ausführen:
ToolsNet − zur Verwaltung von Ergebnisberichten.
Konfiguration der ToolsNet-Verbindung
Öffnen Sie Einstellungen im Hauptmenü und wählen Sie im linken Fenster Serververbindungen aus.
Legen Sie im Feld ToolsNet die folgenden Parameter fest:
Feld
Beschreibung
Ein/Aus
Aktivierung/Deaktivierung des Datenaustauschs mit dem ToolsNet Server
Server-Port
ToolsNet Server-Port
Server-Host
IP-Adresse ToolsNet Server
Wählen Sie Übernehmen.

Um den ToolsNet-Verbindungsstatus anzuzeigen, öffnen Sie Berichte > Ergebnisse und wählen Sie die Schaltfläche . Wählen Sie im angezeigten Dialogfeld die Registerkarte Serververbindungen.
Weitere Informationen zur Konfiguration von ToolsNet finden Sie im ToolsNet 8-Benutzerhandbuch.
Konfigurieren der Remote-Protokollierungsverbindung
Um eine Steuerung mit einem Remote-Protokollierungsserver zu verbinden, müssen Sie die Remote-Protokollierungseinstellungen in der Steuerung konfigurieren und aktivieren.
Rufen Sie in der Startansicht die Registerkarte Einstellungen auf und wählen Sie auf der linken Seite Serververbindungen aus.
Konfigurieren Sie im Fenster Remote-Protokollierung die folgenden Parameter:
Feld | Beschreibung |
---|---|
Ein/Aus | Aktivierung/Deaktivierung des Datenaustauschs mit dem Remote-Protokollierungsserver |
TCP/UDP | Auswahl des TCP- oder UDP-Protokolls |
Server-Host | IP-Adresse des Remote-Protokollierungsservers |
Server-Port | Port des Remote-Protokollierungsservers |
Konfiguration von Protokollebenen
Die auf dem Remote-Protokollierungsserver gespeicherten Protokolle werden folgendermaßen konfiguriert:
Rufen Sie in der Startansicht die Registerkarte Einstellungen auf und wählen Sie auf der linken Seite Serververbindungen aus.
Wählen Sie im Remote-Protokollierung-Fenster Konfigurieren aus.
Wählen Sie im Fenster Funktionen konfigurieren die entsprechenden Kontrollkästchen aus.
Kategorie
SysLog-Klassifizierung
Fehler
Warnung, Kritisch, Notfall, Fehler
Warnung
Warnung
Info
Informativ, Hinweis
Um die Auswahl auf die vorherige Konfiguration zurückzusetzen, wählen Sie RÜCKGÄNGIG.
Wählen Sie Übernehmen.
Präferenzen
Datum und Uhrzeit
Datum und Uhrzeit müssen eingestellt werden, damit für Ereignisse und Ergebnisse der korrekte Zeitstempel verwendet wird. Die Zeit wird von einer der drei verfügbaren Quellen eingelesen:
Manuell − Datum, Uhrzeit und Zeitzone werden manuell eingestellt.
NTP − Datum und Uhrzeit werden von einem in der Benutzeroberfläche definierten NTP (Network Time Protocol)-Server bezogen.
ToolsNet − Datum und Uhrzeit und werden vom ToolsNet-Server bezogen.
Für die Zeitquellen NTP und ToolsNet wird eine funktionsfähige Netzwerkverbindung benötigt.
Öffnen Sie Einstellungen im Hauptmenü und wählen Sie im linken Fenster Voreinstellungen aus.
Legen Sie im Feld Datum und Uhrzeit die folgenden Parameter fest:
Parameter
Beschreibung
Quelle
Quelle zum Abrufen der Uhrzeit.
NTP Server 1
IP-Adresse eines NTP-Servers, der Datum und Uhrzeit für das Werkzeug bereitstellt.
Server 1 Status
OK/Kein Status
NTP Server 2
IP-Adresse eines NTP-Servers, der Datum und Uhrzeit für das Werkzeug bereitstellt.
Server 2 Status
OK/Kein Status
Datum
Das Datum wird manuell eingegeben, wenn die Quelle auf „manuell“ eingestellt ist.
Zeit
Die Uhrzeit wird manuell eingegeben, wenn die Quelle auf „manuell“ eingestellt ist.
Zeitzone
Die Zeitzone – entweder der Standort oder eine Standardzeitzone wie beispielsweise UTC (koordinierte Weltzeit)
Wählen Sie ANWENDEN aus.
Sprache einstellen
Die Benutzeroberfläche ist in den folgenden zwölf Sprachen verfügbar:
Englisch
Tschechisch
Deutsch
Spanisch
Französisch
Koreanisch
Italienisch
Japanisch
Portugiesisch
Russisch
Schwedisch
Chinesisch
Öffnen Sie Einstellungen im Hauptmenü und wählen Sie im linken Fenster Voreinstellungen aus.
Wählen Sie im Feld Sprache die aktuell verwendete Sprache und wählen Sie eine Sprache aus der Liste aus.
Die Sprachänderung wird sofort wirksam.
Einstellung der Drehmomenteinheit
Drehmomentergebnisse werden in der ausgewählten Einheit sowohl nach Ausführung einer Verschraubung als auch bei der Speicherung in der Ergebnisliste angezeigt.
Einheit | Beschreibung |
---|---|
cNm | Zentinewtonmeter |
dNm | Dezinewtonmeter |
Nm | Newtonmeter |
kNm | Kilonewtonmeter |
in·lbf | Pfundkraft-Zoll |
ft·lbf | Pfundkraft-Fuß |
in·ozf | Unzekraft-Zoll |
ft·ozf | Unzekraft-Fuß |
gf·cm | Grammkraft-Zentimeter |
kgf·cm | Kilogrammkraft-Zentimeter |
kgf·m | Kilogrammkraft-Meter |
Druckeinheiten
Öffnen Sie Einstellungen im Hauptmenü und wählen Sie im linken Fenster Voreinstellungen aus.
Wählen Sie im Feld Druckeinheiten die Einheit Bar oder Pa aus der Liste aus.
Konfiguration der PIN-Einstellungen
Der PIN-Code verhindert einen nicht autorisierten Gebrauch der Web-Benutzeroberfläche oder versehentliche Änderungen.
Wenn aktiviert, ist ein PIN-Code erforderlich, wenn Änderungen der Konfiguration über die Web-GUI vorgenommen werden.
PIN-Konfiguration
In der Web-Benutzeroberfläche können einer oder mehrere verschiedene PIN-Codes konfiguriert werden. Sie als Nutzer können entscheiden, ob keine, eine oder mehrere PIN-Konfigurationen gleichzeitig aktiviert werden sollen.
Jede PIN-Konfiguration besteht aus einem PIN-Code, einem Benutzernamen, einem Schalter zum Aktivieren oder Deaktivieren des Benutzers/der PIN und einer Liste von verfügbaren Konfigurationen, auf die der Benutzer zugreifen kann.
Wenn die PIN aktiviert und der Bildschirm gesperrt ist, wird in der oberen rechten Ecke der Benutzeroberfläche das Symbol eines geschlossenen Schlosses angezeigt. Der Benutzer kann ohne Eingabe des PIN-Codes nur auf die ausgewählte(n) Konfiguration(en) zugreifen und diese ändern, die nicht ausgewählten Konfigurationen kann er lediglich im schreibgeschützten Modus anzeigen. Die nicht ausgewählten Konfigurationen sind ausgegraut oder deaktiviert.
Die Bildschirmsperre wird nach einer vom Benutzer konfigurierbaren Inaktivitätszeit automatisch aktiviert.
Der Einstellwert für die Inaktivitätszeit liegt zwischen 20 und 600 Sekunden. Die Inaktivitätszeit ist konfigurierbar und gilt für alle PIN-Konfigurationen.
Wenn die PIN aktiviert ist, wird die Steuerung, unabhängig von der eingestellten Inaktivitätszeit, bei einem Systemstart gesperrt.

Die konfigurierten Benutzer und PIN gelten auch für den Wartungsanschluss (169.254.1.1).
Aktivieren des PIN-Schutzes am Wartungsanschluss: Setzen Sie im Fenster PIN die Option PIN für Wartungsanschluss verwenden auf Ein.
In jeder Steuerung können bis zu 10 Benutzer konfiguriert werden.
Die PIN jeder Konfiguration muss eindeutig sein. Zum Aktivieren der PIN-Funktionen in der Steuerung ist mindestens eine Konfiguration erforderlich.
Die PIN kann über die Web-GUI konfiguriert werden.
Hinzufügen neuer Benutzer
Wählen Sie im Startbildschirm die Registerkarte Einstellungen. Wählen Sie dann links PIN.
Wählen Sie im PIN-Fenster Konfigurieren aus.
Wählen Sie das Plus-Symbol in der oberen rechten Ecke der Benutzeroberfläche aus.
Das Fenster PIN-Benutzer zeigt den neuen Benutzer. Wenn keine Benutzer innerhalb der Web-Benutzeroberfläche gespeichert sind, dann ist der neue Benutzer der erste und einzige Benutzer in der Liste; wenn in der Web-Benutzeroberfläche bereits andere Benutzer gespeichert sind, dann ist der neue Benutzer der letzte Benutzer in der Liste.Wählen Sie den neuen Benutzer aus.
Daraufhin wird das Fenster Benutzer eingeblendet.
Geben Sie den Namen und die PIN des neuen Benutzers ein und bestätigen Sie die PIN.Der Benutzername muss eindeutig sein.
Der Text im Textfeld Name muss 1 bis 32 Zeichen lang sein.Der PIN-Code muss 4 Stellen lang sein (Zahlen 1 bis 9).
Das Feld PIN eingeben und das Feld PIN bestätigen müssen übereinstimmen, damit die Änderungen übernommen werden. Standardmäßig werden in beiden Textfeldern Punkte angezeigt. Hierbei handelt es sich jedoch lediglich um Platzhalter, die durch die tatsächlichen PIN-Codes ersetzt werden müssen.Wählen Sie Berechtigungen aus. Die Liste der verfügbaren Konfigurationen wird angezeigt.
Wählen Sie das Kontrollkästchen links der gewünschten Konfiguration(en) aus, auf welche der Benutzer Zugriff erhält und an der/denen er Änderungen vornehmen kann.
Wählen Sie nach der Auswahl der gewünschten Konfiguration(en) OK aus.
Daraufhin wird das Fenster Benutzer eingeblendet.Alle auswählen wählt alle verfügbaren Konfigurationen gleichzeitig aus.
Wählen SieAlle abwählen, um die Kontrollkästchen zu deaktivieren und die Optionen abzuwählen.Der Benutzer kann nur auf die im Fenster Berechtigungen ausgewählte(n) Konfiguration(en) zugreifen und diese verändern. Die nicht ausgewählten Konfigurationen können nur im schreibgeschützten Modus angesehen werden. Für nicht ausgewählte Konfigurationen können keine Änderungen vorgenommen werden.
Wählen Sie im Benutzer-Fenster Übernehmen aus.
Aktivieren von Benutzern
Wählen Sie im Startbildschirm die Registerkarte Einstellungen. Wählen Sie dann links PIN.
Wählen Sie im PIN-Fenster Konfigurieren aus.
Markieren Sie im Fenster PIN-Benutzer das Kontrollkästchen links neben dem Benutzernamen, der aktiviert werden soll.
Die PIN kann auch aktiviert werden, indem Sie auf den Benutzernamen klicken und den Schalter Aktiviert auf Ein setzen (im Fenster Benutzer).
Aktivieren der PIN-Konfiguration
Wählen Sie im Startbildschirm die Registerkarte Einstellungen. Wählen Sie dann links PIN.
Wählen Sie im PIN-Fenster Konfigurieren aus.
Setzen Sie im Fenster PIN-Aktivierung den Schalter PIN-Code auf Ein.
Die PIN kann nur aktiviert werden, wenn mindestens ein Benutzer/eine PIN freigegeben ist. Wenn kein Benutzer/keine PIN freigegeben ist, wird eine Warnung angezeigt.
Geben Sie das Inaktivitätszeitlimit (in Sekunden) ein, nach dem der Bildschirm automatisch gesperrt werden soll.
Der Standardwert für das Inaktivitätszeitlimit beträgt 120 Sekunden. Dies ist eine globale Einstellung, die nicht für jeden Benutzer einzeln festgelegt werden kann.
Entsperren der Web-GUI
Wählen Sie im Startbildschirm das Schloss-Symbol oben rechts aus. Ein Popup-Fenster mit einem Ziffernblock wird angezeigt.
Geben Sie den konfigurierten PIN-Code ein und wählen Sie OK.
Wenn die PIN aktiviert ist und der Bildschirm entsperrt wurde, wird in der oberen rechten Ecke der Benutzeroberfläche ein offenes Schloss-Symbol angezeigt. Die Web-GUI kann durch Auswahl des offenen Schloss-Symbols erneut manuell gesperrt werden.
Deaktivieren von Benutzern
Wählen Sie im Startbildschirm die Registerkarte Einstellungen. Wählen Sie dann links PIN.
Wählen Sie im PIN-Fenster Konfigurieren aus.
Deaktivieren Sie im Fenster PIN-Benutzer das Kontrollkästchen links neben dem Benutzernamen, der deaktiviert werden soll.
Die PIN kann auch deaktiviert werden, indem Sie auf den Benutzernamen klicken und den Schalter Aktiviert auf Aus setzen (im Fenster Benutzer).
Löschen von Benutzern
Wählen Sie im Startbildschirm die Registerkarte Einstellungen. Wählen Sie dann links PIN.
Wählen Sie im PIN-Fenster Konfigurieren aus.
Wählen Sie im Fenster PIN-Benutzer das Symbol Löschen rechts neben dem Benutzernamen, der gelöscht werden soll.
Wenn der Benutzer entfernt wird, wird ebenso die PIN gelöscht. Über die gelöschte PIN kann dann auf keinerlei Konfigurationen zugegriffen werden.
Konfiguration der Ereigniseinstellungen
Es ist möglich, die im Controller verfügbaren Aktionen als folgende Eigenschaften zu konfigurieren:
Bestätigt
Aufgezeichnet
Angezeigt
Konfiguration der erweiterten Protokollierung
Die PFHC erstellt automatisch Protokolle und speichert diese. Diese Protokolle können so konfiguriert werden, dass sie eine erweiterte Protokollierung mit Protokollgruppen umfassen.
Konfigurieren der Protokollgruppen
Die Standardeinstellung für eine Protokollgruppe ist ‚Aus‘. Die Einstellung einer Protokollgruppe wird folgendermaßen zu ‚Ein‘ geändert:
Rufen Sie in der Startansicht die Registerkarte Einstellungen auf und wählen Sie auf der linken Seite Erweiterte Protokollierung aus.
Setzen Sie im Fenster Protokollgruppen die Gruppe auf EIN.
Zurücksetzen der Protokollgruppen
Alle Protokollgruppen können auf ihre Standardeinstellungen zurückgesetzt werden.
Rufen Sie in der Startansicht die Registerkarte Einstellungen auf und wählen Sie auf der linken Seite Erweiterte Protokollierung aus.
Wählen Sie im Fenster Protokollgruppen zurücksetzen die Option Zurücksetzen.
Es wird ein Pop-up-Fenster angezeigt, in dem Sie gefragt werden, ob Sie alle Protokollgruppen zurücksetzen möchten. Wählen Sie YES.
Dauerhafte Protokollgruppen
Die Protokollgruppen werden bei jedem Neustart auf ihre Standardeinstellungen zurückgesetzt. Verwenden Sie dauerhafte Protokollgruppen, um das Zurücksetzen zu verhindern.
Rufen Sie in der Startansicht die Registerkarte Einstellungen auf und wählen Sie auf der linken Seite Erweiterte Protokollierung aus.
Setzen Sie im Fenster Auswahl nach Neustart beibehalten die Option Dauerhaft auf EIN.
Zurücksetzen
Zurücksetzung der Steuerung auf Werkseinstellungen
Die Steuerung kann auf ihre ursprünglichen Werkseinstellungen zurückgesetzt werden.

Alle Einstellungen, Ereignisse, Konfigurationen und Verlaufsdaten werden beim Zurücksetzen der Steuerung gelöscht. Nehmen Sie nur dann eine Zurücksetzung auf die Werkseinstellungen vor, wenn Sie vollkommen sicher sind, dass dies erforderlich ist.
Zurücksetzen auf die Werkseinstellungen
Wählen Sie im Startbildschirm die Registerkarte Einstellungen. Wählen Sie dann links Zurücksetzen.
Wählen Sie im Fenster Steuerung auf Werkseinstellungen zurücksetzen die Option Zurücksetzen.
Es wird ein Popup-Fenster angezeigt, das davor warnt, dass alle Daten gelöscht werden. Wählen Sie dann Ja.
Die Steuerung wird neu gestartet, um die neuen Einstellungen zu aktivieren.
Ergebnisse löschen
Es ist möglich, auf der Steuerung gespeicherte Ergebnisse und Ereignisse zu löschen.
Löschen von Ergebnissen und Ereignissen
Wählen Sie im Startbildschirm die Registerkarte Einstellungen. Wählen Sie dann links Zurücksetzen.
Wählen Sie im Fenster Ergebnisse löschen die Option Löschen.
Es wird ein Popup-Fenster angezeigt, das davor warnt, dass alle Ergebnisse und Ereignisse gelöscht werden. Wählen Sie dann Ja.
Schalten Sie die Steuerung aus und warten Sie 30 Sekunden lang, bevor Sie sie wieder einschalten.
Arbeiten mit der Registerkarte Hilfe
Dieser Abschnitt unterstützt Sie beim Arbeiten mit der Web-GUI. Das Benutzerhandbuch der Power Focus HC ist in diese Registerkarte eingebettet. Die Kapitel finden Sie im linken Bereich.
Bedienung
In diesem Abschnitt finden Sie Schritt-für-Schritt-Anleitungen zur Bedienung des Produkts.
Steuerungsoberfläche
Systemstart
Des Menü Aufgaben an der Handsteuerung ist während des Starts grau hinterlegt, was bedeutet, dass es erst verfügbar ist, wenn der Systemstart abgeschlossen ist.
Während des Systemstarts geschieht das Folgende:
Die Pumpe und der Spanner starten und stellen die Kommunikation mit der Handsteuerung her.
Wenn die Firmwareversion der Pumpe oder des Spanners nicht mit der Softwareversion der Handsteuerung kompatibel ist, wird die Firmwareversion auf eine kompatible Version aktualisiert. Dieser Prozess kann an der LED des Spanners beobachtet werden, die während der Kompatibilitätsprüfung der Firmware und dem eventuellen Aktualisierungsvorgang blau leuchtet. Wenn die Status-LED des Spanners aufhört zu blinken und dauerhaft weiß leuchtet, hat der Spanner die Verbindung mit der Handsteuerung hergestellt.
Entspricht die Firmware der Pumpe oder des Spanners nicht der von der Handsteuerung erwarteten, wird das Ereignis 2516 „Unerwartete Pumpen- oder Spanner-Firmwareversion erkannt, System neu starten. Falls das Problem weiterhin besteht, kann das System eventuell trotzdem betrieben werden, achten Sie jedoch sorgfältig auf unerwartetes Verhalten“, ausgelöst. Falls eine Firmware sich auf der Liste der inkompatiblen Firmwareversionen der Handsteuerung befindet, gibt diese das Ereignis 2617 „Inkompatible Pumpen- oder Spanner-Firmwareversion, System neu starten. Das System kann nicht betrieben werden“ aus. Im Falle einer inkompatiblen Firmware aktiviert die Handsteuerung Start->Aufgaben nicht. In beiden Fällen startet das System neu und lässt einen erneuten Versuch durch das Gerät zu, dessen Aktualisierung fehlgeschlagen ist.
Der Name der Handsteuerung kann im IAM ersetzt werden, siehe Abschnitt Intelligentes Anwendungs-Modul.
Verbindungsstatus
Die Symbole für den Drahtlosverbindungsstatus und den ToolsNet-Verbindungsstatus zeigen eine Live-Aktualisierung des Zustands der Verbindung an. Die Handsteuerung verbindet sich mit dem WLAN, wenn sie unter Einstellungen -> Netzwerk entsprechend konfiguriert wurde.
Wenn die Drahtlosverbindung hergestellt wurde und die Handsteuerung über eine aktive Verbindung mit dem WLAN-Netzwerk verfügt, erscheint das WLAN-Verbindungssymbol ohne die diagonale Linie.
Wenn die Handsteuerung für die Verbindung mit ToolsNet konfiguriert wurde, entspricht der Zustand des Symbols dem Zustand der Verbindung. Die diagonale Linie bedeutet, dass keine offene Verbindung zu ToolsNet besteht.
Hauptbildschirm
Wenn alle drei Komponenten den Startvorgang abgeschlossen haben und die Systemkommunikation hergestellt wurde, ist das Menü Aufgaben verfügbar.
Warnungen und Erinnerungen
Wenn im System eine Warnung oder eine Benachrichtigung hinsichtlich des Pumpen- oder Spannerstatus vorliegt, wird das Symbol für angeschlossene Geräte mit einem blauen Rahmen hervorgehoben und die Anzahl der Meldungen angezeigt. Beim Zugriff auf die Registerkarte Angeschlossene Geräte zeigt das Informations- oder Warnsymbol dem Benutzer, wo zusätzliche Informationen zur Verfügung stehen. Einige Zustände werden auch als Warnungsbanner auf der Startseite angezeigt.
Erinnerung für den Ölwechsel
Wenn der nächste Ölwechsel in weniger als vier Wochen ansteht oder die Motorlaufzeit die letzten 50 Stunden erreicht hat, wird eine Erinnerung für den Ölwechsel angezeigt.

In den letzten 28 Tagen vor dem nächsten Ölwechseldatum und in den letzten 50 Stunden der Motorlaufzeit wird das Infosymbol angezeigt.
Das Infosymbol wird zu einer Warnung, wenn das Ölwechseldatum überschritten wurde oder die Motorlaufzeit den Grenzwert erreicht hat.
Arbeiten mit der Registerkarte Aufgaben
Das Menü Aufgaben ist verfügbar, wenn sowohl die Pumpe als auch der Spanner mit der Handsteuerung verbunden sind.
Auf der Benutzeroberfläche der Handsteuerung werden nur Aufgaben angezeigt, die über gültige Konfigurationen verfügen.
Liegen beispielsweise keine Konfigurationen für Montage vor, dann ist weder Montage noch Gruppenmontage verfügbar.
Der Manuelle Modus ist immer vorhanden.
Montage und Schraubendienst erlauben eine Ausführung pro Schraube, zum Beispiel für Schulungs- oder Testzwecke.
Die folgenden Aufgaben sind auf der Handsteuerung verfügbar:
Montage: Eine einfache Ausführung einer Stufen-Spannkonfiguration.
Gruppenmontage: Führt eine Gruppenaufgabe einer Stufen-Spannkonfiguration aus. Der Bediener muss vor dem Start dieser Aufgabe zusätzliche Informationen eingeben.
Manueller Modus: Erlaubt die manuelle Steuerung des Spannvorgangs. Dieser Vorgang kann durch einen beliebigen Spanner ausgeführt werden.
Schraubendienst: Eine einfache Ausführung einer Schraubendienst-Konfiguration.
Gruppen-Schraubendienst: Führt eine Gruppenaufgabe einer Spann-Dienst-Konfiguration aus. Der Bediener muss vor dem Start dieser Aufgabe zusätzliche Informationen eingeben.
Verwenden Sie den Manuellen Modus für das erneute Spannen oder Lösen von Schrauben. Es wird die Verwendung einer entsprechenden Lösestrategie empfohlen. Weitere Informationen zum Lösen finden Sie im Abschnitt Entspannen der Mutter.
Vereinfachte GUI für Spannvorgänge
Für Spannvorgänge sind zwei Bildschirme innerhalb der Benutzeroberfläche der Handsteuerung verfügbar, eine vollständige GUI und eine vereinfachte GUI.
Die vollständige GUI zeigt die Messwerte für Druck, Drehmoment, Winkel sowie die auf den Flansch einwirkende Kraft an.
Die vereinfachte GUI ist eine optimierte Bediener-GUI, ähnlich den LEDs am Spanner, wobei die LEDs an der Handsteuerung den gleichen Status wie die LEDs am Spanner anzeigen.
Mithilfe der Hoch- und Runter-Tasten an der Handsteuerung kann zwischen diesen beiden GUI-Bildschirmen gewechselt werden.
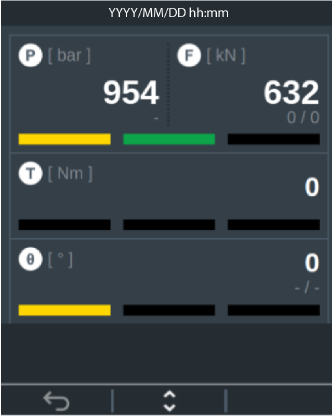
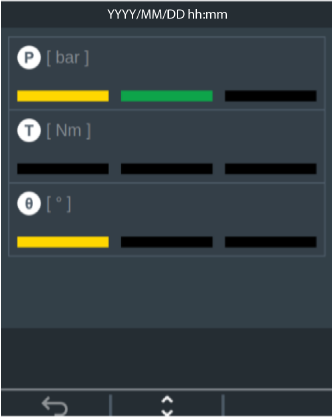
Baugruppe
Die Registerkarte Montage enthält eine Liste der vorkonfigurierten Spannprogramme, welche mit dem verbundenen Spanner kompatibel sind. Sind keine kompatiblen Programme vorhanden, erscheint die folgende Meldung im unteren Bereich des Bildschirms: Kein kompatibles Programm.
Öffnen Sie auf dem Startbildschirm Aufgaben > Montage.
Wählen Sie ein Programm aus, das ausgeführt werden soll, indem Sie mithilfe der Hoch- und Runter-Tasten durch die Liste navigieren und anschließend die Eingabe-Taste in der Mitte drücken, um Ihre Auswahl zu bestätigen.
Der in der Liste angezeigte Name wird dem Feld Name auf der Registerkarte Allgemeine Einstellungen > Eigenschaften entnommen.
Sobald die Meldung Werkzeug auf Schraube positionieren auf dem Bildschirm erscheint, fahren Sie den Spanner direkt auf die Oberseite der Schraube herunter.
Stellen Sie sicher, dass der Aufsatz an der Mutter ausgerichtet ist.
Drücken Sie die Taste Vorwärts auf der Tastatur, um den Spannvorgang zu starten.
Spannvorgang
Der Spannvorgang setzt sich aus den folgenden Phasen zusammen:
Installationsprüfung
Phase der Druckbeaufschlagung
Anziehen der Mutter
Der Spannvorgang kann jederzeit abgebrochen werden.
Wann das System auf eine Handlung des Benutzer wartet, erscheint nach einigen Sekunden ein Hilfetext, der verschwindet, sobald die erwartete Aktion erkannt wurde.
Installationsprüfung
Der Zweck der Installationsprüfung ist, einen Referenzpunkt für die Winkelmessung zu erstellen.
Drücken Sie die Taste für die Druckbeaufschlagung, um ein Drehen des Spanners während der Installationsprüfung zu verhindern.
Der Druck kann zunächst unterhalb des erwarteten Niveaus liegen, insbesondere beim ersten Durchlauf nach einer längeren Pause. Betätigen Sie in diesem Fall erneut die Taste zur Druckbeaufschlagung.
Es kann zu einer Druck-Überschreitung kommen – das System fordert den Benutzer auf, Druck abzulassen und es erneut zu versuchen.
Eine Überschreitung kann aufgrund des Parameters Winkel-Rückstellkraft eintreten, siehe Abschnitt Spannparameter.
Drehen Sie die Mutter im Uhrzeigersinn, um das im Parameter Installationsprüfungs-Drehmoment festgelegte Drehmomentniveau zu erreichen (Standardeinstellung 20 Nm). Erhalten Sie das Drehmoment mindestens für die Dauer des Installationsprüfungs-Drehmoments aufrecht (Standardeinstellung 1 Sekunde).
Alle 3 LEDs färben sich grün.
Lassen Sie die Kraft am Knickschlüssel ab.
Phase der Druckbeaufschlagung
Drücken und halten Sie die Taste für die Druckbeaufschlagung.
Wenn eine LED in der Zeile Winkel am Spanner und ihr Äquivalent an der Handsteuerung leuchtet, ziehen Sie die Mutter entlang der Länge der Schraube an.
Wenden Sie kein Drehmoment auf die Mutter an, bevor der Solldruck erreicht wurde. Der Druck erledigt die Arbeit.
Anziehen der Mutter
Halten Sie die Taste zur Druckbeaufschlagung gedrückt, um den Druck oberhalb des Parameters Minimaler Schraubenspanndruck zu halten.
Der Druck fällt langsam ab und das System führt einen Druckablass durch, bevor der Druck unter den Mindestwert fällt.
Ziehen Sie die Mutter mit dem Anzugs-Solldrehmoment fest und halten Sie das Drehmoment für die Dauer des Anzugsdrehmoments.
Alle LEDs leuchten, wenn diese Bedingung erfüllt ist.
Lassen Sie das Drehmoment ab.
Wenn der Parameter Automatischer Druckablass auf EIN gesetzt ist, lässt das System den Druck ab, sobald das Drehmoment auf unter 10 Nm gesenkt wird.
Wenn der Parameter Automatischer Druckablass auf AUS gesetzt ist, lassen Sie den Druck mithilfe der entsprechenden Taste ab.
Nach dem Druckablass wird das Ergebnis IO oder NIO an der Handsteuerung angezeigt. In beiden Fällen werden in der Detailansicht die aufgezeichneten Werte für Druck/Kraftwinkel und Drehmoment angezeigt.
Abbruch

Eine laufende Aufgabe kann jederzeit abgebrochen werden, jedoch muss zuvor der Systemdruck abgelassen werden.
Betätigen Sie die Taste für den Druckablass, um den Druck abzulassen.
Drücken Sie die Taste Zurück, um den Spannvorgang zu verlassen.
Wird ein Spannvorgang während einer Gruppenaufgabe abgebrochen, hat der Benutzer zwei Auswahlmöglichkeiten:
Schraube abbrechen: wenn die Schraubennummer falsch ist. Die GUI der Handsteuerung kehrt zum Bildschirm Werkzeug auf Schraube positionieren zurück.
Gruppe abbrechen: wenn die Spannaufgabe pausiert oder angehalten werden muss.
Bei der Ausführung einer Montage-Aufgabe kehrt die GUI der Handsteuerung zum Menü Aufgaben zurück.
Gruppenmontage
Es wird eine Gruppe eingerichtet, um eine festgelegte Anzahl von aufeinanderfolgenden Spannvorgängen mit denselben Spannkonfigurationen durchzuführen.
Öffnen Sie auf den Startbildschirm Aufgaben > Gruppenmontage.
Wählen Sie ein Programm aus, das ausgeführt werden soll, indem Sie mithilfe der Hoch- und Runter-Tasten durch die Liste navigieren und anschließend die Eingabe-Taste in der Mitte drücken, um Ihre Auswahl zu bestätigen.
Der in der Liste angezeigte Name wird dem Feld Name auf der Registerkarte Allgemeine Einstellungen > Eigenschaften entnommen.
Wählen Sie eine der folgenden beiden Optionen aus: Turm-Bereichs-ID oder Turmdaten.
Scannen Sie die Flanschkennung.
Scannen Sie die Turm-Bereichs-ID, welche die Referenz für den jeweiligen Flansch ist, oder geben Sie diese manuell ein. Diese Kennung wird für die Erstellung des Ergebnisberichts benötigt, da sie zur Gruppierung der Ergebnisse für einen bestimmten Flansch verwendet wird. Weitere Informationen zur Verwendung der Tastatur an der Handsteuerung finden Sie im Abschnitt Schaltflächen und Symbole auf der GUI.
Scannen Sie gegebenenfalls den QR-Code für die Turmdaten oder geben Sie diese manuell ein. Dieser String ist eine per Semikolon separierte Liste, welche die Turm-Bereichs-ID und einige zusätzliche Daten umfasst, die den Ergebnissen hinzugefügt werden. Die Handsteuerung verifiziert das Format dieses Strings und gibt eine Fehlermeldung aus, wenn dieses nicht bestätigt wird.
Scannen Sie die optionalen Aufgaben-Metadaten, die Teil der Ergebnisse sind:
Bediener-Daten scannen
Bediener-Unternehmen scannen
Schraubendaten
Flanschposition
Werker-ID
Bediener-Daten
Bediener-Unternehmen
Drücken Sie zum Fortfahren die Taste Vorwärts.
Geben Sie die Gesamtzahl von Schrauben am Flansch ein, selbst wenn nur ein Teil der Schrauben bearbeitet werden soll.
Geben Sie mithilfe der Hoch- und Runter-Tasten eine Ziffer ein und drücken Sie zur Bestätigung die Eingabe-Taste. Drücken Sie die Taste Weiter, um die nächste Ziffer mithilfe der Hoch- und Runter-Tasten einzugeben, und Eingabe, um die Auswahl zu bestätigen.
Weitere Informationen zur Verwendung der Tastatur an der Handsteuerung finden Sie im Abschnitt Schaltflächen und Symbole auf der GUI.
Wenn die Gesamtzahl von Schrauben am Flansch korrekt eingegeben wurde, drücken Sie die Taste Vorwärts, um den Übersichtsbildschirm aufzurufen.
Der Übersichtsbildschirm zeigt den Namen des auszuführenden Programms sowie die Anzahl der Schrauben an.
Drücken Sie die Taste Vorwärts, um mit dem ersten Spannvorgang zu beginnen.
Wenn eine zuvor gestartete Gruppenaufgabe fortgesetzt wird, erscheinen die Ergebnisse der einzelnen Spannvorgänge in Grün (IO) oder Rot (NIO) auf dem Bildschirm Werkzeug auf Schraube positionieren.
Ist die Schraubennummer nicht korrekt, bearbeiten Sie sie mithilfe der Schaltfläche Mehr.
Es liegt in der Verantwortung des Benutzers, sicherzustellen, dass die Schraubennummer korrekt ist.
Drücken Sie die Taste Vorwärts, um den Spannvorgang zu starten, siehe Abschnitt Spannvorgang.
Betriebsmodus Manuell
Im Manuellen Modus werden keine Prozesse durch das System überwacht, mit Ausnahme der Regelung des Solldrucks, und es werden keine Ergebnisse aufgezeichnet.
Um den Prozess manuell überwachen zu können, zeigt die Steuerungs-GUI Informationen zum Druck, Drehmoment und Winkel an.
Wenn der Manuelle Modus nach dem Systemstart erstmalig ausgeführt wird, muss der Benutzer den Solldruck durch Eingabe des vorgesehenen Solldrucks festlegen. Bei darauffolgenden Ausführungen des manuellen Modus wird der zuletzt verwendete Solldruck beibehalten, solange das System eingeschaltet bleibt.
Der Bildschirm Solldruck festlegen wird mit dem Konfigurationsparameter für den Spannvorgang im manuellen Modus Standardmäßiger manueller Hydraulikdruck befüllt.
Der Solldruck wird durch den jeweils niedrigsten der folgenden Werte begrenzt:
Maximaldruck der Pumpe
Maximaldruck des Spanners
Maximaler System-Hydraulikdruck – der Konfigurationsparameter für den manuellen Modus
Betrieb im manuellen Modus
Öffnen Sie auf dem Startbildschirm Aufgaben > Manueller Modus.
Legen Sie den Solldruck fest.
Wenn Werkzeug auf Schraube positionieren erscheint, kann der Solldruck durch Druck auf die Schaltfläche Mehr geändert werden.
Drücken Sie die Taste Vorwärts, um den Manuellen Modus zu starten.
Führen Sie die Druckbeaufschlagung mithilfe der entsprechenden Taste durch.
Die Druckbeaufschlagung wird beim Solldruck angehalten oder wenn die Taste losgelassen wird.
Das am Schlüssel anliegende Drehmoment wird sowohl als weißer Balken als auch Ziffern visualisiert.
Der registrierte Winkel wird in Ziffern dargestellt.
Sobald das Drehmoment zu sinken beginnt, wird das Spitzenmoment als schwarzer und das aktuelle Drehmoment als weißer Balken dargestellt. Die Spitzenwertmessung wird mit Ziffern dargestellt.
Verwenden Sie die Schaltfläche Mehr für die folgenden Aktionen:
Neuen Solldruck festlegen – wählen Sie im Popup-Fenster Solldruck festlegen aus.
Löschen des registrierten Spitzenmoments und -winkels.
Eine Bewegung des Schlüssels gegen den Uhrzeigersinn wird als negatives Drehmoment und negativer Winkel registriert.
Verwenden Sie die Taste Zurück, um den manuellen Modus zu verlassen.
Das Verlassen des manuellen Modus ist nur möglich, wenn der Druck vom System abgelassen wird.
Die Steuerungsoberfläche kehrt zum Menü Aufgaben zurück.
Entspannen der Mutter
Drehen Sie den Spanner um 3 mm vom Kontaktpunkt mit der Fläche des Flanschs aus zurück.
Wählen Sie an der Handsteuerung den Manuellen Modus aus, legen Sie anschließend den Druck fest, mit dem die Schraube ursprünglich gespannt wurde, und beginnen Sie mit dem Druckaufbau, während Sie den Knickschlüssel mit positiver Kraft gegen den Uhrzeigersinn halten.
Wenn die anliegende Kraft den Lösepunkt erreicht, lässt sich der Knickschlüssel frei zum Öffnen der Mutter bewegen. Drehen Sie den Knickschlüssel um das 6- bis 7-fache seines begrenzten Fensterzyklus.
Lassen Sie den Druck ab und überprüfen Sie, ob die Schraube gelöst wurde.

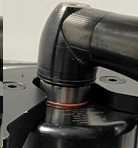

Die Maximalhub-Anzeige auf der Zugstange sollte nicht leuchten, während der Spanner unter Druck gesetzt wird. Wenn diese Anzeige leuchtet, stoppen Sie und stellen die Position der Zugstange auf dem Bolzen so ein, dass die maximale Position nicht erreicht wird, bis der erforderliche Druck erreicht ist. Andernfalls können, bei wiederholter Durchführung, die internen Komponenten des Spanners beschädigt werden.
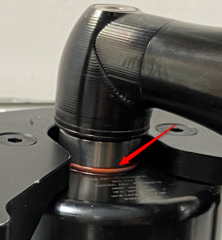
Schraubendienst
Der Schraubendienstvorgang stellt sicher, dass die Muttern und Schrauben in gutem Zustand sind. Die Mutter wird bis zum Minimalen Lösewinkel für das Lösen einer Mutter (Standardeinstellung 10 Grad) gelöst und anschließend wieder angezogen.
Der Winkel und das Drehmoment in Verschraubungsrichtung werden als positive Werte angezeigt, wohingegen der Winkel und das Drehmoment in Löserichtung als negative Werte angezeigt werden.
Öffnen Sie auf dem Startbildschirm Aufgaben > Schraubendienst.
Wählen Sie ein Programm aus, das ausgeführt werden soll, indem Sie mithilfe der Hoch- und Runter-Tasten durch die Liste navigieren und anschließend die Eingabe-Taste in der Mitte drücken, um Ihre Auswahl zu bestätigen.
Der in der Liste angezeigte Name wird dem Feld Name auf der Registerkarte Allgemeine Einstellungen > Eigenschaften entnommen.
Sobald die Meldung Werkzeug auf Schraube positionieren auf dem Bildschirm erscheint, fahren Sie den Spanner direkt auf die Oberseite der Schraube herunter.
Stellen Sie sicher, dass der Aufsatz an der Mutter ausgerichtet ist.
Drücken Sie die Taste Vorwärts auf der Tastatur, um den Schraubendienstvorgang zu starten.
Schraubendienstvorgang
Der Schraubenwartungsvorgang besteht aus den folgenden Phasen:
Installationsprüfung
Phase der Druckbeaufschlagung
Lösen der Mutter
Anziehen der Mutter
Der Schraubenwartungsvorgang kann jederzeit abgebrochen werden.
Wenn das System auf eine Aktion seitens des Benutzers wartet, erscheint nach einigen Sekunden ein Hilfetext, der verschwindet, sobald die erwartete Aktion erkannt wurde.

Die Delta-Mutternrotation ist als die Summe der Mutternrotationen definiert: Löserotation + Verschraubungsrotation. Beträgt die Löserotation beispielsweise -13 Grad und die Verschraubungsrotation 15 Grad, so beträgt die Gesamt-Mutternrotation 2. (-13 + 15 = 2)
Installationsprüfung
Zweck der Installationsprüfung ist es, einen Referenzpunkt für die Winkelmessung zu erstellen.
Drücken Sie die Taste zur Druckbeaufschlagung, um eine Rotation des Spanners während der Installationsprüfung zu vermeiden.
Es kann zur Druckunterschreitung kommen, insbesondere bei den ersten Durchläufen nach einer längeren Pause. Drücken Sie die Taste zur Druckbeaufschlagung in diesem Fall erneut.
Es kann zu Drucküberschreitungen kommen – das System fordert den Benutzer auf, den Druck abzulassen und es noch einmal zu versuchen.
Überschreitungen können aufgrund des Parameters Kraft für den Winkelreset auftreten, siehe Abschnitt Spannparameter.
Drehen Sie die Mutter im Uhrzeigersinn, um das im Parameter Installationsprüfungs-Drehmoment festgelegte Drehmomentniveau zu erreichen (Standardwert 20 Nm). Halten Sie das Drehmoment mindestens für die Installationsprüfungs-Drehmomentdauer (Standardwert 1 Sekunde).
Alle 3 LEDs leuchten grün.
Lassen Sie die Kraft am Knickschlüssel ab.
Drehen Sie die Mutter gegen den Uhrzeigersinn, um das im Parameter Installationsprüfungs-Drehmoment festgelegte Drehmomentniveau zu erreichen (Standardwert 20 Nm). Halten Sie das Drehmoment mindestens für die Installationsprüfungs-Drehmomentdauer (Standardwert 1 Sekunde).
Alle 3 LEDs leuchten grün.
Lassen Sie die Kraft am Knickschlüssel ab.
Phase der Druckbeaufschlagung
Drücken und halten Sie den Knopf für die Druckbeaufschlagung.
Versuchen Sie nicht, die Mutter zu drehen, bevor der Solldruckwert erreicht wurde, da die Mutter mit hoher Kraft am Flansch angebracht ist.
Lösen der Mutter
Halten Sie die Taste für die Druckbeaufschlagung gedrückt, damit das System den Druck oberhalb des Parameters Minimaler Schraubenspanndruck halten kann.
Der Druck fällt langsam ab und das System erhöht diesen wieder, bevor er unter den Mindestdruck fällt.
Lösen Sie die Mutter bis zum Minimalen Lösewinkel für das Lösen einer Mutter.
Bleibt die Mutter beispielsweise aufgrund von Korrosion stecken, erlaubt das System die Versuchsanzahl für das Lösen einer Mutter (Standardwert 3), anschließend wird der Benutzer zum erneuten Anziehen der Mutter aufgefordert. Dies führt zu einem NIO-Ergebnis.
Ein Versuch ist als die Anwendung eines Drehmoments höher als das Drehmoment für den Muttern-Löseversuchszähler definiert.
Alle drei LEDs in der Winkelreihe leuchten auf, wenn diese Bedingung erfüllt ist.
Ist der Lösewinkel größer als der Minimale Lösewinkel für das Lösen einer Mutter und liegt die Gesamtbewegung der Mutter innerhalb des Bereichs der Min. Delta-Mutternrotation und der Max. Delta-Mutternrotation, ist das Ergebnis IO.
Anziehen der Mutter
Ziehen Sie die Mutter bis zum Verschraubungs-Solldrehmoment fest und halten Sie das Drehmoment für die Verschraubungs-Drehmomentdauer in Sekunden.
Alle LEDs leuchten auf, wenn diese Bedingung erfüllt ist.
Lassen Sie die Kraft am Knickschlüssel ab.
Ist der Parameter Automatischer Druckablass auf EIN gestellt, lässt das System den Druck ab, wenn das Drehmoment auf unter 10 Nm gesenkt wird.
Ist der Parameter Automatischer Druckablass auf AUS gestellt, lassen Sie den Druck mithilfe der Taste für den Druckablass ab.
Wenn der Druck abgelassen wurde, wird auf der Handsteuerung ein IO- oder NIO-Ergebnis angezeigt. In beiden Fällen zeigt die Detailansicht den aufgezeichneten Druck/Kraftwinkel sowie die Drehmomentwerte an.
Ist der Lösewinkel größer als der Minimale Lösewinkel für das Lösen einer Mutter und liegt die Gesamtbewegung der Mutter innerhalb des Bereichs der Min. Delta-Mutternrotation und der Max. Delta-Mutternrotation, ist das Ergebnis IO.
Abbruch

Eine laufende Aufgabe kann jederzeit abgebrochen werden, zuvor muss jedoch der Systemdruck abgelassen werden.
Drücken Sie auf die Taste zum Druckablass, um den Druck abzulassen.
Drücken Sie auf die Taste Zurück, um den Schraubenwartungsvorgang zu verlassen.
Wird der Schraubenwartungsvorgang während einer Gruppenaufgabe abgebrochen, hat der Benutzer zwei Auswahlmöglichkeiten:
Schraube abbrechen: wenn die Schraubennummer falsch ist. Die Handsteuerungs-GUI kehrt zum Bildschirm Werkzeug auf Schraube positionieren zurück.
Gruppe abbrechen: wenn die Spannaufgabe pausiert oder gestoppt werden muss.
Bei der Ausführung der Aufgabe Schraubenwartung kehrt die GUI der Handsteuerung zum Menü Aufgaben zurück.
Gruppen-Schraubendienst
Öffnen Sie auf den Startbildschirm Aufgaben > Gruppen-Schraubendienst.
Wählen Sie ein Programm aus, das ausgeführt werden soll, indem Sie mithilfe der Hoch- und Runter-Tasten durch die Liste navigieren und anschließend die Eingabe-Taste in der Mitte drücken, um Ihre Auswahl zu bestätigen.
Der in der Liste angezeigte Name wird dem Feld Name auf der Registerkarte Allgemeine Einstellungen > Eigenschaften entnommen.
Wählen Sie eine der beiden Optionen aus: Turm-Bereichs-ID oder Turmdaten.
Scannen Sie die Flanschkennung.
Scannen Sie die Turm-Bereichs-ID, welche die Referenz für den jeweiligen Flansch ist, oder geben Sie diese manuell ein. Diese Kennung wird für die Erstellung des Ergebnisberichts benötigt, da sie zur Gruppierung der Ergebnisse für einen bestimmten Flansch verwendet wird.
Weitere Informationen zur Verwendung der Tastatur an der Handsteuerung finden Sie im Abschnitt Schaltflächen und Symbole auf der GUI.
Scannen Sie gegebenenfalls den QR-Code für die Turmdaten oder geben Sie diese manuell ein. Dieser String ist eine per Semikolon separierte Liste, welche die Turm-Bereichs-ID und einige zusätzliche Daten umfasst, die den Ergebnissen hinzugefügt werden. Die Handsteuerung verifiziert das Format dieses Strings und gibt eine Fehlermeldung aus, wenn dieses nicht bestätigt wird.
Scannen Sie die optionalen Aufgaben-Metadaten, die Teil der Ergebnisse sind:
Bediener-Daten scannen
Bediener-Unternehmen scannen
Schraubendaten
Flanschposition
Werker-ID
Bediener-Daten
Bediener-Unternehmen
Drücken Sie zum Fortfahren die Taste Vorwärts.
Geben Sie die Gesamtzahl von Schrauben am Flansch ein, selbst wenn nur ein Teil der Schrauben bearbeitet werden soll.
Weitere Informationen zur Verwendung der Tastatur an der Handsteuerung finden Sie im Abschnitt Schaltflächen und Symbole auf der GUI.
Drücken Sie die Taste Vorwärts, um den Übersichtsbildschirm zu öffnen.
Der Übersichtsbildschirm zeigt den Namen des auszuführenden Programms sowie die Anzahl der Schrauben an.
Drücken Sie die Taste Vorwärts, um den Schraubendienstvorgang zu starten.
Wenn eine zuvor gestartete Gruppenaufgabe fortgesetzt wird, erscheinen die Ergebnisse der einzelnen Schraubendienste in Grün (IO) oder Rot (NIO) auf dem Bildschirm Werkzeug auf Schraube positionieren.
Ist die Schraubennummer nicht korrekt, bearbeiten Sie sie mithilfe der Schaltfläche Mehr.
Es liegt in der Verantwortung des Benutzers, sicherzustellen, dass die Schraubennummer korrekt ist.
Drücken Sie die Taste Vorwärts, um den Schraubendienstvorgang zu starten, siehe Abschnitt Schraubendienstvorgang unter Schraubendienst.
Arbeiten mit der Registerkarte Berichte
Berichte ausgeben
Die Berichte werden auf einen mit dem USB-A-Anschluss an der Handsteuerung verbundenen USB-Stick ausgegeben.
Wählen Sie auf dem Startbildschirm die Registerkarte Berichte und anschließend Berichte ausgeben durch Druck auf die Eingabe-Taste aus.
Um den Datumsbereich für die Berichterstellung festzulegen, bearbeiten Sie das Startdatum und das Enddatum mittels der Tastatur an der Handsteuerung. Werden die Felder leer gelassen, beinhaltet der Bericht sämtliche in der Handsteuerung gespeicherten Ergebnisse.
Drücken Sie die Taste Vorwärts und wählen Sie anschließend Ausgabe starten durch Druck auf die Eingabe-Taste aus oder brechen Sie den Vorgang mithilfe der Taste Zurück ab.
Es erscheint die Warnmeldung Stellen Sie vor dem Start der Berichtsausgabe sicher, dass ein USB-Stick verbunden ist.
Wenn die Meldung Bericht ausgegeben auf dem Bildschirm erscheint, drücken Sie die Taste Weiter.
Entfernen Sie den USB-Stick.
Ergebnisse
Ergebnisse von Gruppen-Wartungsaufgaben können auf der Registerkarte Berichte angesehen werden. Die gespeicherten Ergebnisse können über die Turmbereichs-ID für alle Gruppenaufgaben angezeigt werden.
Das vollständige Ergebnis des Flanschs wird als Kreis dargestellt.
Grüne Segmente für IO-Ergebnisse.
Rote Segmente für NIO-Ergebnisse.
Aktive Segmente sind weiß.
Fehlende Ergebnisse sind grau.
Wählen Sie auf der Registerkarte Berichte Ergebnisse aus.
Um den Datenbereich für die Ergebnisse festzulegen, bearbeiten Sie das Startdatum und das Enddatum mithilfe der Tastaturtasten an der Handsteuerung. Werden diese Felder leer gelassen, werden alle Ergebnisse in der Handsteuerung angezeigt.
Navigieren Sie durch die Ergebnisse, indem Sie die Oben- und Unten-Tasten auf der Tastatur drücken.
Wählen Sie das anzuzeigende Ergebnis durch Druck auf die Taste Eingabe aus.
Es erscheint ein Kreisdiagramm des ausgewählten Ergebnisses. Jedes Segment steht für eine Schraube in der Gruppenaufgabe.
Navigieren Sie durch die Schraubenergebnisse, indem Sie die Oben- und Unten-Tasten an der Tastatur drücken, um sich zum nächsten oder vorherigen Ergebnis zu bewegen.
Über die Taste Mehr kann zu einer bestimmten Schraubennummer navigiert werden, indem die Schraubennummer eingegeben und die Taste Vorwärts gedrückt wird.
Klicken Sie auf die Schaltfläche Weiter, um Details zur gewählten Schraube anzuzeigen.
Arbeiten mit der Registerkarte Steuerungsinformationen
Das Menü Steuerungsinformationen enthält die folgenden Informationen:
Gerätedaten der Handsteuerung – Seriennummer
Artikelnummer
Ethernet-Adresse
Softwareversion
Software-Build-Datum
Arbeiten mit der Registerkarte Einstellungen
Wählen Sie auf dem Startbildschirm die Registerkarte Einstellungen aus, um Folgendes zu tun:
Zeit einstellen
Datum einstellen
Ergebnisse löschen
Sprache
Zeit einstellen
Legen Sie die Zeit mithilfe der Oben- und Unten-Tasten im 24-Stunden-Format fest und drücken Sie anschließend auf die Schaltfläche Weiter.
Weitere Informationen zur Verwendung der Tastaturtasten an der Handsteuerung finden Sie im Abschnitt Schaltflächen und Symbole auf der GUI.
Bestätigen Sie die Zeit mit der Taste Vorwärts, wenn das Minutenfeld aktiv ist.
Drücken Sie zum Abbrechen die Taste Zurück, wenn das Stundenfeld aktiv ist.
Datum einstellen
Legen Sie das Datum mithilfe der Oben- und Unten-Tasten im Format JJJJ/MM/TT fest und drücken Sie anschließend auf die Schaltfläche Weiter.
Weitere Informationen zur Verwendung der Tastaturtasten an der Handsteuerung finden Sie im Abschnitt Schaltflächen und Symbole auf der GUI.
Bestätigen Sie das Datum mit der Taste Vorwärts, wenn das Tagefeld aktiv ist.
Drücken Sie zum Abbrechen die Taste Zurück, wenn das Jahresfeld aktiv ist.
Ergebnisse löschen
Zum Löschen aller in der Handsteuerung gespeicherten Ergebnisse:
Öffnen Sie die Registerkarte Einstellungen und wählen Sie Ergebnisse löschen aus.
Drücken Sie zur Bestätigung die Eingabe-Taste und wählen Sie anschließend im Popup-Fenster Ja oder Nein zum Abbrechen aus.
Um Probleme zu vermeiden, wird empfohlen, die Ergebnisse nach abgeschlossenen Gruppenaufgaben und Exporten regelmäßig zu löschen. Der Festplattenspeicher der Handsteuerung ist nicht unbegrenzt.
Sprache
Zum Ändern der Spracheinstellung:
Öffnen Sie die Registerkarte Einstellungen und wählen Sie Sprache aus. Drücken Sie zur Bestätigung die Eingabe-Taste.
Das Sprachenmenü ist immer an letzter Stelle unter Start -> Einstellungen zu finden, um die Navigation zur Sprache auch dann zu erlauben, wenn die Handsteuerung eine dem Bediener unbekannte Sprache verwendet.
Wählen Sie die gewünschte Sprache aus der Liste aus. Drücken Sie zur Bestätigung die Eingabe-Taste.
Arbeiten mit angeschlossenen Geräten
Wählen Sie auf der Startseite die Registerkarte Angeschlossene Geräte aus, um Daten zu den verbundenen Geräten anzuzeigen.
Auf dem Startbildschirm werden zusätzlich die folgenden Informationen angezeigt:
Firmwareversionen
Spannergröße
Zugstangenzähler
Maximale Anzahl von Druckbeaufschlagungen der Zugstange
Pumpe
Wählen Sie auf der Startseite die Registerkarte Angeschlossene Geräte aus.
Wählen Sie Pumpe aus und drücken Sie anschließend die Eingabe-Taste, um das Folgende anzuzeigen:
Pumpendetails
Benutzerdefinierte Pumpenkennung
Ölwechsel – Verbleibende Laufzeit
Drücken Sie die Eingabe-Taste, um weitere Details anzuzeigen.
Pumpendetails
Wählen Sie Pumpendetails aus, um Informationen zum angeschlossenen Gerät anzuzeigen, z. B. Artikelnummer, Seriennummer, Hardwareversion sowie das Folgende:
Einschaltzeit des Pumpenmotors zählt die Anzahl von Sekunden, für die der Motor betrieben wurde.
Einschaltzeit des Pumpen-Druckübersetzers zählt die Anzahl von Sekunden, für die der Druckübersetzer betrieben wurde.
Zähler Pumpenöl-Druckbeaufschlagung zählt die Anzahl der Druckbeaufschlagungen mit > 75 % des Maximums (=>1400 bar) seit dem letzten aufgezeichneten Ölwechsel.
Benutzerdefinierte Pumpenkennung
Benutzerdefinierte Pumpenkennung ist ein Feld, das vom Kunden zur Identifikation des Geräts mithilfe einer beliebigen Kennung verwendet werden kann. Die benutzerdefinierte ID wird in der Pumpe gespeichert und von der Handsteuerung beim Systemstart ausgelesen.
Wählen Sie zum Bearbeiten der benutzerdefinierten ID den Bildschirm Benutzerdefinierte Pumpenkennung aus, indem Sie die Eingabe-Taste drücken.
Drücken Sie auf die Taste Mehr, um die benutzerdefinierte ID zu scannen oder manuell einzugeben.
Wählen Sie im Popup-Fenster zur Eingabe der neuen benutzerdefinierten ID Scannen oder Manuelle Eingabe aus.
Für die Manuelle Eingabe:
Wählen Sie im Popup-Fenster Speichern und Verlassen oder Zurücksetzen und Verlassen aus, um diesen Schritt abzubrechen.
Es wird ein Ereignis ausgegeben, um den Erfolg des Vorgangs anzuzeigen (Benutzerdefinierte ID wurde festgelegt erscheint).

Die Buchstaben der benutzerdefinierten Kennung müssen ASCII-Zeichen mit Werten < 128 sein, ziehen Sie bitte eine ASCII-Tabelle heran.

Die neue benutzerdefinierte ID wird erst mit dem nächsten Start des Systems gültig.
Ölwechsel – Verbleibende Laufzeit
Wenn der Öl- und Filterwechsel durchgeführt wurde, bestätigen Sie den Wechsel, indem Sie Pumpe -> Ölwechsel – Verbleibende Laufzeit -> Öl und Filter wurden gewechselt -> Ja auswählen.
Das Datum für den nächsten Ölwechsel wird für ein Jahr in der Zukunft festgelegt und die Einschaltzeit des Pumpenmotors auf 0 zurückgesetzt.
Das neue Datum wird an die Pumpe übermittelt und gespeichert. Das neue Datum für den Öl- und Filterwechsel folgt der Pumpe und wird auf jeder mit ihr verbundenen Handsteuerung angezeigt.
Spanner
Wählen Sie auf der Startseite die Registerkarte Angeschlossene Geräte aus.
Wählen Sie Spanner aus und drücken Sie anschließend die Eingabe-Taste, um das Folgende anzuzeigen:
Spanner
Zugstange
Wägezelle
Kolben
Benutzerdefinierte Spannerkennung
Drücken Sie die Eingabe-Taste, um weitere Details anzuzeigen.
Wenn die Liste länger als der Bildschirm ist, verwenden Sie die Oben- und Unten-Tasten, um die gesamte Liste anzusehen.
Spanner
Steckschlüsselgröße
Maximaldruck
Artikelnummer
Name – dieses Feld wird bei der Produktion festgelegt
Revision
Seriennummer
GUID
Zugstange
Die Zugstange ist ein internes Verschleißteil, das regelmäßig gewechselt werden muss.
Aktueller Zugstangenzählstand zeigt die Anzahl der Druckbeaufschlagungen der Zugstange an, welche jeweils >70 % des Maximaldrucks (1400 bar) entsprechen.
Max. Zugstangenzählstand zeigt die maximal zulässigen Druckbeaufschlagungen an, welche jeweils >70 % des Maximaldrucks (1400 bar) entsprechen.
Verbleibender Zugstangenzählstand
Artikelnummer
Seriennummer
Montagedatum
Herstelldatum
Wägezelle
Maximaldruck
Aktueller Wägezellenzählstand zeigt die Anzahl von Druckbeaufschlagungen mit > 75 % des Maximums (=> 1400 bar) an.
Artikelnummer
Seriennummer
Montagedatum
Herstelldatum
Kolben
Kolbenbereich
Artikelnummer
Seriennummer
Montagedatum
Herstelldatum
Benutzerdefinierte Spannerkennung
Benutzerdefinierte Spannerkennung ist ein Feld, das vom Kunden zur Identifikation des Geräts mithilfe einer beliebigen Kennung verwendet werden kann. Die benutzerdefinierte ID wird im Spanner gespeichert und von der Handsteuerung beim Systemstart ausgelesen.
Wählen Sie zum Bearbeiten der benutzerdefinierten ID den Bildschirm Benutzerdefinierte Spannerkennung aus, indem Sie die Eingabe-Taste drücken.
Drücken Sie auf die Taste Mehr, um die benutzerdefinierte ID zu scannen oder manuell einzugeben.
Wählen Sie im Popup-Fenster zur Eingabe der neuen benutzerdefinierten ID Scannen oder Manuelle Eingabe aus.
Für die Manuelle Eingabe:
Wählen Sie im Popup-Fenster Speichern und Verlassen oder Zurücksetzen und Verlassen aus, um diesen Schritt abzubrechen.
Es wird ein Ereignis ausgegeben, um den Erfolg (Benutzerdefinierte ID wurde festgelegt erscheint) oder den Fehlschlag des Vorgangs anzuzeigen.

Die Buchstaben der benutzerdefinierten Kennung müssen ASCII-Zeichen mit Werten < 128 sein, ziehen Sie bitte eine ASCII-Tabelle heran.

Die neue benutzerdefinierte ID wird erst mit dem nächsten Start des Systems gültig.
Warnung maximaler Zugstangenzählerstand
Wenn der Zugstangenzählstand sich dem Maximum der Zugstange nähert, erscheint die Warnmeldung Verbleibender Zugstangenzählstand, die ebenfalls beim Start einer Spannaufgabe erscheint, auf der Registerkarte Angeschlossene Geräte.
Wenn die Anzahl der verbleibenden Spannaufgaben 500 beträgt, erscheint die Warnmeldung Verbleibender Zugstangenzählstand: 500. Die Warnmeldungen erscheinen anschließend immer häufiger, je mehr die Anzahl sich 0 annähert. Wenn die Anzahl der verbleibenden Spannaufgaben 0 beträgt, sind keine weiteren Spannvorgänge mehr zulässig. Tauschen Sie den Spanner aus, um mit der Aufgabe fortzufahren.
Wählen Sie auf der Steuerungs-GUI Angeschlossene Geräte, danach Spanner aus und klicken Sie auf Zugstange, um die folgenden Informationen anzuzeigen:
Aktueller Zugstangenzählstand
Max. Zugstangenzählstand
Verbleibender Zugstangenzählstand
Artikelnummer
Seriennummer
Fehlersuche und Wartung
Dieser Abschnitt soll den Benutzer bei der Behebung eventuell auftretender Fehler unterstützen und enthält Informationen zur Wartung und Instandhaltung des Produkts.
Fehlersuche und Alarme
Die nachfolgenden Tabellen beschreiben verschiedene Situationen, Probleme und Alarme mit ihren jeweiligen möglichen Ursachen und Lösungen. Die Alarme zeigen eine Warnmeldung mit einem Code auf der Handsteuerung an, sodass Korrekturmaßnahmen getroffen werden können.
Alarm | Mögliche Ursachen | Lösung |
---|---|---|
Alarm Pumpenmotor-Öltemperatur hoch | Die Öltemperatur innerhalb der Pumpe liegt aus verschiedenen Gründen über der zulässigen Temperatur: Kontinuierlicher Betrieb | Lassen Sie die Pumpe für einige Minuten ruhen, damit sie abkühlen kann. |
Ölqualität | Auf Verschmutzungen überprüfen. Wechseln Sie das Öl. | |
Externe Temperatur | Wechseln Sie das Öl zu einer geeigneten Sorte. | |
Alarm niedriger Ölstand Pumpenmotor | Wenn der Ölstand innerhalb der Pumpe unter dem Mindeststand liegt, hält das System an. | Füllen Sie Öl an der Pumpe nach, um die Arbeit fortsetzen zu können. |
Leckage innerhalb des Systems | Überprüfen Sie das System auf Leckagen und reparieren Sie diese oder tauschen Sie das entsprechende Teil aus. | |
Alarm Pumpenmotorschutz | Hochstrom oder ungewöhnliche Stromaktivität im Motor. Dieser Alarm wird zum Schutz der Elektronik und elektrischen Komponenten ausgelöst, die mit dem Motor verbunden sind. | Öffnen Sie das kleine Fenster an der Vorderseite der Pumpe. Stellen Sie den schwarzen Knopf wieder auf die I-Position, um die Stromversorgung des Motors wiederherzustellen. Falls der Fehler wieder auftritt, überprüfen Sie die Hauptstromversorgung. |
Störung Werkzeugkommunikation | Ein für eine übermäßige Dauer fließender Überstrom ist die häufigste Ursache. Dieser Alarm wird zum Schutz der Elektronik und elektrischen Komponenten innerhalb des Schaltschranks ausgelöst. | Öffnen Sie das kleine Fenster an der Vorderseite der Pumpe. Reaktivieren Sie den Schutzschalter, um die Arbeit fortzusetzen. Falls der Schalter innerhalb von Sekunden nach dem erneuten Arbeitsbeginn wieder auslöst, stellen Sie die Arbeiten ein und ergreifen Sie Korrekturmaßnahmen.
|
Ein elektrischer Kurzschluss. | ||
Ein elektrischer Erdschluss. | ||
Kein Pumpendruck erkannt | Motorausfall Falsche Phasenfolge am dreiphasigen Stecker. | Schalten Sie das System ab und kehren Sie die Phasen des Stromanschlusses um. |
Warnung | Mögliche Ursachen | Lösung |
---|---|---|
Ölwechsel | Es ist ein Ölwechsel erforderlich. Es wird eine Hinweismeldung angezeigt:
Es wird eine Warnmeldung angezeigt:
| Wechseln Sie das Öl. Bestätigen Sie, dass das Öl gewechselt wurde, siehe Ölwechsel – Verbleibende Laufzeit, Pumpe. |
Überdrehmoment | Die Anzugskraft ist zu hoch. | Lassen Sie die Kraft am Schlüssel ab. |
Überdruck | Ein zu hoher Druck, der zu Schäden an der Maschine führen kann. | Senken Sie den Druck. |
Problem | Mögliche Ursachen | Lösung |
---|---|---|
Der Spanner bleibt nach dem Spannvorgang an der Schrauber stecken | Niedriger Ladezustand des Akkuschraubers. | Tauschen Sie den Akku des Schraubers gegen einen geladenen aus. |
Kein Spalt zwischen der Wand und dem Spanner. | Überprüfen Sie den Abstand zur Wand an der Rückseite des Spanners. Besteht kein Spalt, lösen Sie die Schraube mithilfe des manuellen Modus. | |
Bohrungsausrichtung, Schmierung und Schraubgewinde. | Überprüfen Sie zusätzlich die Bohrungsausrichtung, Schmierung und Schraubgewinde. Wechseln Sie im Zweifelsfall die Schraube und versuchen Sie es erneut. | |
Der Spanner senkt sich nicht auf die Schraube ab | Die Schraubgewinde sind beschädigt. | Tauschen Sie die Schraube aus. |
Die Schraubgewinde sind nicht geschmiert. | Schmieren Sie die Schraubgewinde. | |
Verschmutzungen in den Schraubgewinden. | Entfernen Sie die Verschmutzungen mit einer Drahtbürste aus den Gewinden. | |
Der Schraubenüberstand übersteigt den maximalen Grenzwert. | Passen Sie den Überstand an, indem Sie die Schraube soweit lösen, dass sie nicht den maximalen Grenzwert übersteigt. | |
Der Druck in der Pumpe baut sich nicht über 200 bar auf | Leckage an der Pumpe. | Überprüfen Sie, ob Leckagen an der Pumpe oder der Hydraulikleitung des Systems vorliegen. Überprüfen Sie den Ölstand. Füllen Sie Öl nach, falls dieser zu niedrig ist. Senden Sie die Pumpe zur Wartung oder Reparatur, wenn das Problem bestehen bleibt. |
Falsche Ölsorte. | Stellen Sie sicher, dass Sie die richtige Ölsorte verwenden. | |
Der Anschluss der Hydraulikleitung lässt sich nur schwer von der Pumpe trennen | Der Nippel des Schlauchs ist abgenutzt. | Wechseln Sie die Nippel am Schlauch und am Spanner, sobald diese klebrig werden oder sich schwer trennen lassen. |
Referenz
In diesem Abschnitt finden Sie verschiedene nützliche Informationen.
Begriffe und Definitionen
Begriff | Synonym | Definition | Hinweis |
---|---|---|---|
Gruppe | Mehrere Spannvorgänge, für die dasselbe Spannprogramm und die gleiche Stecknuss verwendet werden | ||
Controller-GUI | Grafische Benutzeroberfläche | Benutzeroberfläche der Handsteuerung, die zum Betrieb des Systems verwendet wird | |
Ereignis | Statussignale von der Handsteuerung oder angeschlossenen Geräten | ||
Endwinkel | Tatsächlicher gemessener Winkelwert am Ende des Spannvorgangs | ||
Enddrehmoment | Tatsächlicher gemessener Drehmomentwert am Ende des Spannvorgangs | ||
Enddruck | Tatsächlicher gemessener Druckwert am Ende des Spannvorgangs | ||
GUI | Grafische Benutzeroberfläche | Die grafische Benutzeroberfläche besteht aus interaktiven grafischen Elementen wie Fenstern, Icons und Symbolen auf einem Display | |
IAM | Intelligentes Applikationsmodul | Modul der Handsteuerung, das Produktionsdaten enthält | |
Spannprogramm | Parametersatz | Konfiguration der Parameter und Werte zur Steuerung und Überwachung eines einzelnen Spannvorgangs und zur Speicherung des Spannergebnisses | Der Sollwert wird als Druck, Drehmoment oder Winkel angegeben. |
Sollwert | Erwünschtes Spannergebnis | Der Sollwert wird als Drehmoment oder Drehwinkel angegeben. | |
Sollwinkel | Erwünschter Winkelwert am Ende eines Spannvorgangs; wird von einem Bezugspunkt aus gemessen | ||
Sollmoment | Erwünschter Drehmomentwert am Ende des Spannvorgangs | ||
Web-GUI | Benutzerschnittstelle zur Steuerung über das Webbrowser-Fenster von einem Ferncomputer | ||
virtuelle Station | virtuelle Steuerung | Software-Abstraktion einer physischen Steuerung | Eine Steuerung kann nur Teil eines Spannsystems sein. |
Drittanbieterlizenzen
Liste von Drittanbieterlizenzen
Power Focus-Steuerungen enthalten Komponenten von Drittanbietern, deren Lizenzen die Veröffentlichung von Kopien der Lizenzsprache und/oder Copyright-Hinweise erfordern. Entsprechend dieser Anforderungen finden Sie hier Kopien der Lizenzen. Klicken Sie bitte auf eine der nachfolgend aufgeführten Lizenzen, um eine Kopie des Lizenztextes anzuzeigen.
Software | Version | Licenses |
---|---|---|
acl | 2.2.52 | |
alsa-lib | 1.1.2 | |
alsa-state | 0.2.0 | |
alsa-tools | 1.1.0 | |
alsa-utils | 1.1.2 | |
anybus | 1.1 |
|
atftp | 0.7.1 + gitAUTOINC + be3291a18c | |
attr | 2.4.47 | |
barebox | 2018.06.0 | |
base-files | 3.0.14 | |
base-files-px2-base | 1.0 | |
base-passwd | 3.5.29 | |
bash | 4.3.30 | |
bash-completion | 2.4 | |
bluez5 | 5.41 | |
boost | 1.61.0 | |
busybox-px2base | 1.24.1 | |
bzip2 | 1.0.6 | |
ca-certificates | 20160104 | |
cppunit | 1.13.1 | |
cryptodev-linux | 1.8 | |
curl | 7.50.1 | |
db | 3.0.35 | |
dbus | 1.10.10 | |
dhcp | 4.3.4 | |
dosfstools | 4.0 | |
dt-utils | 2017.03.0 | |
e2fsprogs | 1.43 | |
ecryptfs-tools | 1.0 | |
elfutils | 0.166 | |
eudev | 3.2.2 | |
expat | 2.2.0 | |
fbset | 2.1 | |
fb-test | 1.1.0 | |
fcgi | 2.4.0 | |
finit | 3.1 | |
firmware-imx | 5.4 |
|
flac | 1.3.1 | |
flatbuffers | 1.9.0 | |
fruit | 3.4.0 + gitAUTOINC + ece0f7218c | |
fuse | 2.9.4 | |
gcc-runtime | 6.2.0 | |
gdb | 8.0.1 | |
gdbm | 1.12 | |
glib-2.0 | 2.48.2 | |
glibc | 2.24 | |
gmp | 6.1.1 | |
gnutls | 3.5.3 | |
grep | 2.25 | |
gstreamer1.0 | 1.8.3 | |
gstreamer1.0-plugins-base | 1.8.3 | |
hostpad | 2.6 | |
htop | 1.0.3 | |
icu | 57.1 | |
init-ifupdown | 1.0 | |
initscripts | 1.0 | |
iproute2 | 4.7.0 | |
iptables | 1.6.0 | |
ipwatchd | 1.2 | |
iw | 4.7 | |
json-spirit | 4.08 | |
keyutils | 1.5.9 | |
kmod | 23 + gitAUTOINC + 65a885df5f | |
kmsfbwrap-px2base | 12.0 | |
libarchive | 3.2.2 | |
libbsd | 0.8.3 |
|
libcap | 2.25 | |
libdrm | 2.4.70 | |
libestr | 0.1.10 | |
libevent | 2.0.22 | |
libfastjson | 0.99.4 | |
libffi | 3.2.1 | |
libgcc | 6.2.0 | |
libgcrypt | 1.7.3 | |
libgpg-error | 1.24 | |
libidn | 1.33 | |
libite | 2.0.2 | |
libjpeg-turbo | 1.5.0 | |
liblogging | 1.0.5 | |
libnet | 1.2-rc3 | |
libnfsidmap | 0.25 | |
libnl | 3.2.28 | |
libogg | 1.3.2 | |
libpcap | 1.8.1 | |
libpcre | 8.39 | |
libpng | 1.6.24 | |
librcf | 2.2.0.0 | |
libsamplerate0 | 0.1.8 | |
libsndfile1 | 1.0.27 | |
libtinyxml | 2.6.2 | |
libtirpc | 1.0.1 | |
libuev | 2.2.0 | |
libusb1 | 1.0.20 | |
libvorbis | 1.3.5 | |
libxml2 | 2.9.4 | |
libxslt | 1.1.29 | |
lighttpd | 1.4.51 | |
linux-atlas | 4.14 | |
linux-libc-headers | 4.14.13 | |
logrotate | 3.9.1 | |
lua | 5.1.5 | |
luabind | git | |
lzo | 2.09 | |
lzop | 1.03 | |
memlog | 2.0 | |
mesa | 12.0.1 | |
mg | 20161005 |
|
minizip | 1.2.8 | |
mmc-utils | 0.1 | |
mtd-utils | 1.5.2 | |
nano | 2.2.5 | |
ncurses | 6.0 + 20160625 | |
netbase | 5.3 | |
netcat-openbsd | 1.105 | |
nettle | 3.2 | |
nfs-utils | 2.1.1 | |
ntp | 4.2.8p8 | |
openssh | 7.6p1 | |
openssl | 1.0.2n | |
opkg | 0.3.3 | |
opkg-arch-config | 1.0 | |
opkg-utils | 0.3.2 + gitAUTOINC + 3ffece9bf1 | |
orc | 0.4.25 | |
os-release | 1.0 | |
packagegroup-atlas-qt5 | 1.0 | |
packagegroup-atlas-sxb | 1.0 | |
packagegroup-base | 1.0 | |
packagegroup-core-boot | 1.0 | |
packagegroup-core-eclipse-debug | 1.0 | |
packagegroup-core-nfs | 1.0 | |
packagegroup-core-ssh-openssh | 1.0 | |
packagegroup-px2it | 1.0 | |
parted | 3.2 | |
perl | 5.22.1 | |
pm-utils | 1.4.1 | |
poco | 1.9.0 | |
pointercal | 0.0 | |
popt | 1.16 | |
procps | 3.3.12 | |
protobuf | 2.6.1 + gitAUTOINC + bba83652e1 | |
python | 2.7.12 | |
qtbase | 5.7.1 + gitAUTOINC + a55f36211e | |
qtdeclarative | 5.7.1 + gitAUTOINC + 2a992040e2 | |
qtlocation | 5.7.1 + gitAUTOINC + de5be121d8 | |
qtsensors | 5.7.1 + gitAUTOINC + 5a57beaaa5 | |
qtwebkit | 5.7.1 + gitAUTOINC + 76e2732f01 | |
qtwebsockets | 5.7.1 + gitAUTOINC + 60cede232a | |
qtxmlpatterns | 5.7.1 + gitAUTOINC + 89dbcc4f80 | |
rauc | 0.4 | |
readline | 6.3 | |
rpcbind | 0.2.3 | |
rsync | 3.1.2 | |
rsyslog | 8.22.0 | |
run-postinsts | 1.0 | |
shadow | 4.2.1 | |
shadow-security | 4.2.1 | |
sqlite3 | 3.14.1 |
|
squashfs-tools | 5.7.1 + gitrAUTOINC + 9c1db6d13a |
|
st-load | 1.0 |
|
stm32flash | git | |
strace | 4.13 | |
sysfsutils | 2.1.0 | |
sysvinit-bootlogd | 2.88dsf | |
tcf-agent | 1.4.0 + gitAUTOINC + 2dddd5f440 | |
tcpdump | 4.7.4 | |
tcp-wrappers | 7.6 | |
tslib | 1.1 | |
tzdata | 2016i |
|
u-boot-atlas | 2017.09 | |
u-boot-fw-utils | 2017.09 | |
unzip | 6.0 | |
usbutils | 008 | |
util-linux | 2.28.1 | |
wireless-tools | 30.pre9 | |
wpa-supplicant | 2.5 | |
xerces-c | 2.7.0 | |
xz | 5.2.2 |
|
yaml-cpp | 0.6.2 | |
zip | 3.0 | |
zlib | 1.2.8 |