ETP SRB81-500-20-D
Battery-Powered Nutrunner
Produktinformation
Allgemeine Informationen
Informationen zum motorisch angetriebenen Werkzeug
Sicherheitsbezogene Signalwörter
Die sicherheitsbezogenen Signalworte Gefahr, Warnung, Vorsicht und Hinweis haben folgende Bedeutung:
GEFAHR | GEFAHR weist auf eine gefährliche Situation hin, die bei Nichtvermeidung zu schweren Verletzungen mit möglicher Todesfolge führen wird. |
WARNUNG | WARNUNG weist auf eine gefährliche Situation hin, die bei Nichtvermeidung zu schweren Verletzungen mit möglicher Todesfolge führen könnte. |
ACHTUNG | VORSICHT weist bei Verwendung mit dem Sicherheitswarnsymbol auf eine gefährliche Situation hin, die bei Nichtvermeidung zu leichten oder mittelschweren Verletzungen führen könnte. |
HINWEIS | Ein HINWEIS wird für Situationen verwendet, die sich nicht auf eine mögliche Verletzungsgefahr beziehen. |
Garantie
Die Produktgarantie verfällt 12+1 Monate nach dem Versand aus dem Distributionszentrum von Atlas Copco.
Normaler Verschleiß von Teilen wird nicht von der Garantie abgedeckt.
Unter normalem Verschleiß versteht man, dass während der für diesen Zeitraum typischen Standardwerkzeugwartung Teile ausgetauscht oder Einstellungen / Verbesserungsarbeiten durchgeführt werden müssen (ausgedrückt in Zeit, Betriebsstunden, oder anderweitig).
Die Produktgarantie stützt sich auf einen korrekten Einsatz, Wartung und Reparatur des Werkzeugs und seiner Bestandteile.
Schäden an Teilen, die als Folge einer unzureichenden Wartung oder eines falschen Einsatzes durch andere Parteien als Atlas Copco oder deren zertifizierten Service-Partner während der Garantiezeit verursacht werden, sind nicht durch die Garantie gedeckt.
Um eine Beschädigung oder Zerstörung von Werkzeugteilen zu vermeiden, warten Sie das Werkzeug entsprechend der empfohlenen Wartungspläne und befolgen Sie die richtigen Anweisungen.
Garantiereparaturen werden nur in Atlas Copco-Werkstätten oder von einem zertifizierten Service-Partner ausgeführt.
Atlas Copco bietet eine erweiterte Garantie und eine vorbeugende Wartung nach dem neuesten Stand der Technik durch seine ToolCover-Verträge. Weitere Informationen erhalten Sie von Ihrem lokalen Servicerepräsentanten.
Für Elektromotoren:
Die Garantie gilt nur dann, wenn der Elektromotor nicht geöffnet wurde.
Website
Informationen zu unseren Produkten, Zubehör, Ersatzteilen und Veröffentlichungen finden Sie auf der Internetseite von Atlas Copco.
Besuchen Sie: www.atlascopco.com.
ServAid
ServAid ist ein Portal, das ständig aktualisiert wird und technische Informationen bietet, wie z.B.:
Behörden- und Sicherheitsinformationen
Technische Daten
Installations-, Betriebs- und Wartungsanweisungen
Ersatzteillisten
Zubehör
Maßzeichnungen
Besuchen Sie: https://servaid.atlascopco.com.
Weitere technische Informationen erhalten Sie bei Ihrem Atlas Copco-Vertreter vor Ort.
Sicherheitsdatenblätter MSDS/SDS
In den Sicherheitsdatenblättern werden die von Atlas Copco vertriebenen chemischen Produkte beschrieben.
Weitere Informationen finden Sie auf der Internetseite von Atlas Copco unter www.atlascopco.com/sds.
Video Produktsicherheit für Drehschrauber
Erfahren Sie mehr zu den Sicherheitsmerkmalen der Drehschrauber von Atlas Copco und den Maßnahmen, die der Bediener für den sicheren Betrieb zu ergreifen hat. Klicken Sie auf den Link, oder scannen Sie den nachfolgenden QR-Code, um das Video anzusehen:
https://www.youtube.com/watch?v=FAh6yttvUpw
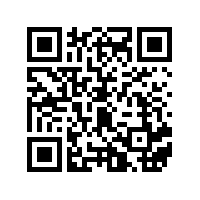
Herkunftsland
Informationen zum Herkunftsland sind auf dem Produktetikett angegeben.
Maßzeichnungen
Maßzeichnungen finden Sie entweder im Maßzeichnungsarchiv oder auf ServAid.
Besuchen Sie: http://webbox.atlascopco.com/webbox/dimdrw oder https://servaid.atlascopco.com.
Übersicht
Allgemeine Beschreibung
Der kabellose Elektroschrauber Tensor SRB wird von einer neuen Akkugeneration von Atlas Copco angetrieben und bietet Einhandbedienung mit Genauigkeit, Rückverfolgbarkeit und Flexibilität. Der SRB sendet Berichte drahtlos an das Power-Focus-6000-System und nutzt die kompletten Vorteile der Virtuellen Stationen. Er kann Verschraubungsstrategien für niedrige Reaktionskräfte – wie Turbo Tight und Tensor Pulse – genauso wie herkömmliche Strategien – wie zweistufiges Anziehen – ausführen. Der Tensor SRB ist ideal für Anwendungen mit niedrigem Drehmoment, bei denen die Reaktionskraft das Handgelenk des Bedieners belastet. Er ist leicht, hervorragend ausbalanciert und ergonomisch gestaltet, um Ermüdungen des Bedieners vorzubeugen.
Umgebungstemperatur
Halten Sie den Akku für optimale Leistung und Lebensdauer innerhalb der angegebenen Temperaturbereiche.
Betriebstemperatur, Laden | +5 bis +40 °C |
Betriebstemperatur, Entladen | 0 bis +40 °C |
Transporttemperatur | -20 bis +40 °C |
Lagertemperatur | +10 bis +25 °C |
Setzen Sie den Akku nicht direkter Sonneneinstrahlung aus.
Technische Produktdaten
Technische Produktdaten finden Sie entweder auf ServAid oder auf der Internetseite von Atlas Copco.
Besuchen Sie: https://servaid.atlascopco.com oder www.atlascopco.com.
Installation
Installationsanleitung
Rapid Backup Unit
Die Rapid Backup Unit (RBU) hat den Formfaktor einer SD-Karte. Die RBU enthält alle aktuellen Netzwerkkonfigurationen und -einstellungen. Einige der Parameter werden bei der Installation und Konfiguration auf der Karte gespeichert. Bei einem Ausfall kann die Karte schnell entnommen und in ein neues Werkzeug eingelegt werden. So bleiben alle Funktionen erhalten.

Wenn die RBU von einem Werkzeug auf ein anderes übertragen wird, wird das neue Werkzeug mit der Software auf der Karte aktualisiert. Während dieser Aktualisierung kann es zu Datenverlusten kommen. Um dieses Risiko zu minimieren, ist es zu empfehlen, dass auf dem neuen Werkzeug bereits dieselbe Softwareversion wie auf dem alten Werkzeug läuft.

Diese RBU kann ausschließlich zum Speichern der Werkzeugkonfigurationsdaten und der Software verwendet werden. Eine Neuformatierung der Karte sowie Änderungen an den Daten auf der Karte, die nicht mit ToolsTalk Service 2 vorgenommen werden, führen dazu, dass die Karte unbrauchbar wird.

Beachten Sie, dass die mit dem Werkzeug verknüpften gespeicherten Ergebnisse verlorengehen, wenn die RBU auf ein anderes Werkzeug übertragen wird.

Die MAC-Adresse ist nicht mit dem Werkzeug selbst, sondern mit der RBU verknüpft. Beim Übertragen einer Karte auf ein neues Werkzeug nimmt dieses Werkzeug daher die MAC-Adresse der RBU an.
Werkzeugkonvertierung
Beim Konvertieren eines Werkzeugs (z.B. durch Wechsel des Vorderteils) müssen die Werkzeuginformationen aktualisiert werden, um die Änderungen abzubilden. Weitere Informationen finden Sie im Benutzerhandbuch der ToolsTalk Service 2 User Edition
Beim Verbinden mit ToolsTalk 2 werden Sie zum Ändern der Werkzeuginformationen aufgefordert. Führen sie zur Anpassung der Werkzeugbezeichnung an die Werkzeugkonvertierung die gleichen Schritte aus wie bei einem Austausch von Ersatzteilen. Aktualisieren Sie das Werkzeug mit der Werkzeugbezeichnung des neuen Teils.

Da das Werkzeug konvertiert wurde, stimmen die im Werkzeug gespeicherten Werkzeuginformationen nicht mehr mit der Werkzeugbezeichnung auf dem Typenschild überein.
Anbringen und Abnehmen des Akkus
Bringen Sie den Akku am Werkzeug an und stellen Sie sicher, dass er korrekt sitzt. Der Akku kann so angebracht werden, dass er nach vorne oder nach hinten zeigt, um die bestmögliche Zugänglichkeit und Balance zu erreichen.
Um den Akku zu entfernen, drücken Sie die Taste am Akku und schieben Sie ihn heraus.
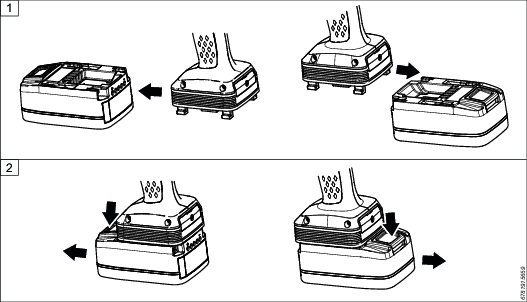
Ausgangskonfiguration
Werkzeugkonfiguration
Informationen zur Werkzeugkonfiguration finden Sie im Power Focus 6000-Konfigurationshandbuch oder im Benutzerhandbuch der ToolsTalk Service 2 User Edition.
Werkzeugkalibrierung
Informationen zur Kalibrierung dieses Werkzeugs finden Sie im Power Focus 6000-Konfigurationshandbuch oder im Benutzerhandbuch der ToolsTalk Service 2 User Edition.
Bedienung
Ergonomie-Richtlinien
Betrachten Sie Ihren Arbeitsplatz, während Sie diese Liste mit allgemeinen Ergonomie-Richtlinien lesen, und versuchen Sie, Bereiche zu identifizieren, in denen Verbesserungen in Bezug auf Körperhaltung, Positionierung der Komponenten oder Arbeitsumgebung möglich sind.
Legen Sie regelmäßige Pausen ein und wechseln Sie regelmäßig die Arbeitshaltung.
Passen Sie den Bereich um Ihre Arbeitsstation Ihren Anforderungen und den auszuführenden Arbeiten an.
Positionieren Sie Teile und Werkzeuge so, dass statische Belastungen möglichst vermieden werden und sich sämtliche Arbeitsmittel bequem erreichen lassen.
Verwenden Sie an Ihrer Arbeitsstation für die Aufgabe geeignete Tische, Stühle oder andere Gegenstände.
Vermeiden Sie während der Ausführung von Montagearbeiten Körperhaltungen über Schulterhöhe oder mit statischer Halteposition.
Wenn Sie über Schulterhöhe arbeiten müssen, verringern Sie die auf die statischen Muskeln wirkende Belastung durch Verringerung des Werkzeuggewichts. Setzen Sie hierzu beispielsweise Drehmomentarme, Schlauchaufroller oder Gewichtsausgleicher ein. Sie können die auf die statischen Muskeln ausgeübte Belastung auch reduzieren, indem Sie das Werkzeug nah am Körper halten.
Legen Sie häufig Pausen ein.
Vermeiden Sie extreme Arm- oder Handgelenkhaltungen, insbesondere während Arbeiten, bei denen ein gewisser Kraftaufwand erforderlich ist.
Richten Sie Ihren Arbeitsplatz so in Ihrem Sichtfeld ein, dass nur minimale Augen- und Kopfbewegungen erforderlich sind.
Verwenden Sie zur Ausführung Ihrer Arbeit eine angemessene Beleuchtungen.
Wählen Sie ein zur Ausführung Ihrer Arbeit angemessenes Werkzeug aus.
Tragen Sie in lauten Umgebungen einen entsprechenden Gehörschutz.
Verwenden Sie hochwertige Einsätze und Kleinteile, um eine übermäßige Vibrationsbelastung möglichst zu vermeiden.
Minimieren Sie nach Möglichkeit durch Reaktionskräfte verursachte Belastungen.
Beim Schneiden:
Eine Trennscheibe kann stecken bleiben, wenn sie verbogen ist oder nicht korrekt geführt wird. Verwenden Sie einen für die Trennscheibe geeigneten Flansch und vermeiden Sie es, die Trennscheibe während des Betriebs zu biegen.
Beim Bohren:
Die Bohrmaschine kann beim Durchbrechen des Bohrers stehen bleiben. Verwenden Sie bei hohem Stillstandsmoment Stützgriffe. Gemäß Teil 3 der Sicherheitsnorm ISO11148 wird empfohlen, bei Pistolengriffmodellen eine Vorrichtung zur Aufnahme von Reaktionsmomenten von über 10 Nm und bei Stabmodellen zur Aufnahme von Reaktionsmomenten von über 4 Nm zu verwenden.
Bei Verwendung von Schraubendrehern und Schraubern mit Direktantrieb:
Reaktionskräfte sind von der Werkzeugeinstellung und den Eigenschaften der jeweiligen Verbindung abhängig. Die Höhe der Reaktionskraft, die eine Bediener tolerieren kann, hängt von dessen Körperkraft und Haltung ab. Passen Sie die Drehmomenteinstellung der Stärke und der Körperhaltung des Bedieners an und verwenden Sie bei zu hohem Drehmoment einen Drehmomentarm oder einen Gegenhalter.
Verwenden Sie in staubigen Umgebungen ein System zur Staubabsaugung oder tragen Sie einen Mundschutz.
Betriebsanleitung
Verschraubung
Drehrichtung für die Verschraubung
Prüfen Sie, ob das Werkzeug in der richtigen Drehrichtung rotiert, indem Sie den Drehrichtungsumschalter oder den Umkehrring drehen.
Modelle mit Pistolengriff (mit Seitentasten)
Drücken Sie den Drehrichtungsumschalter auf der rechten Seite des Werkzeugs, um die Drehrichtung im Uhrzeigersinn (CW) festzulegen.
Drücken Sie den Drehrichtungsumschalter auf der linken Seite des Werkzeugs, um die Drehrichtung gegen den Uhrzeigersinn (CCW) festzulegen.
Modelle mit Pistolengriff (ohne Seitentasten)
Drücken Sie die Funktionstaste oben auf dem Startschalter doppelt, um die Drehrichtung zwischen im Uhrzeigersinn (CW) und gegen den Uhrzeigersinn (CCW) umzuschalten.
Winkelschrauber
Drehen Sie den Umsteuerring nach rechts, um die Drehrichtung im Uhrzeigersinn (CW) festzulegen.
Drehen Sie den Umsteuerring nach links, um die Drehrichtung gegen den Uhrzeigersinn (CCW) festzulegen.
Softstart
Die Softstart-Funktion unterstützt ein straffes Anliegen von Schraubenkopf und Gewinde. Die Dauer des Softstarts ist einstellbar.
Weitere Informationen zu Verschraubungen finden Sie im Power Focus 6000-Konfigurationshandbuch.
Allgemeine Anweisungen
Das Werkzeug darf nur in Kombination mit dem zugehörigen Gegenhalter verwendet werden, der auf die entsprechende Schraubverbindungsanwendung angepasst wurde.
Den Gegenhalter am Werkzeug anbringen und den Sicherungsring in die Nut einsetzen, um so den Gegenhalter ausreichend zu sichern.
Die Stecknuss am Abtriebsvierkant anbringen. Den Sicherungsstift wie in der Abbildung dargestellt durch die Stecknuss und den Abtriebsvierkant führen.
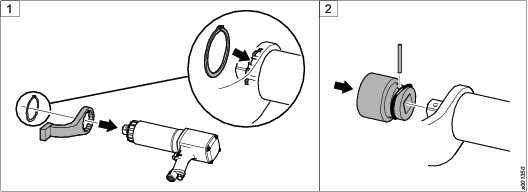
Besondere Vorsichtsmaßnahmen
RHMI
Übersicht
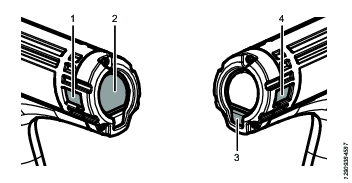
1 | Navigationstaste |
2 | Anzeigebildschirm |
3 | Bestätigungstaste
|
4 | Navigationstaste |
Menü
Resultat
Gehen Sie zum Hauptfenster zurück, um die Schraubergebnisse zu sehen.Verschraubung
Zeigen Sie eine Liste der vorinstallierten Programme vom Power Focus 6000 im Produktionsmodus an oder ermöglichen Sie es dem Benutzer, ein manuelles Programm im Feldmodus zu bearbeiten.Stapelprogramm
Konfigurieren Sie das Stapelprogramm. Gilt nicht für -HA-D- und SRB-D-Werkzeuge.Information
Aktivierung/Deaktivierung der Web-HMI (nur für -HA-, -HA-D-, und SRB-D-Werkzeuge im Smart Modus verfügbar), Anzeige von Akkuinformationen, Temperaturen, Softwareversion, usw.Konfiguration
Konfiguration der Werkzeugtaste und der Frontleuchteneinstellungen.Verschraubungsergebnis
Zeigen Sie eine Liste der letzten Verschraubungsergebnis an.
Wartung
ESD-Probleme vermeiden
Die Komponenten im Inneren des Produkts und der Steuerung sind empfindlich gegenüber elektrostatischen Entladungen. Stellen Sie zur Vermeidung zukünftiger Störungen sicher, dass Service und Wartung in einer ESD-genehmigten Arbeitsumgebung erfolgen. Die Abbildung unten zeigt ein Beispiel für eine entsprechende Service-Arbeitsstation.

Wartungsanweisungen
Serviceanleitung
Die Wartung darf nur von erfahrenem Personal ausgeführt werden, das Zugang zu den Wartungsanleitungen hat und/oder für die Wartung von Tensor Werkzeugen ausgebildet ist. Falls das Werkzeug nicht einwandfrei funktioniert, ist es unverzüglich einer Inspektion zu unterziehen.
Gesamtes Werkzeug
Es wird empfohlen, regelmäßig – zumindest einmal jährlich oder alle 250,000 Verschraubungen (je nachdem, was früher eintritt) – eine Überholung und vorbeugende Wartung des gesamten Werkzeugs durchzuführen.
Getriebe
Es wird empfohlen, regelmäßig – ein Mal jährlich oder nach jeweils max. 250,000 Verschraubungen (je nachdem, was früher eintritt) – eine Überholung und vorbeugende Wartung des Getriebes durchzuführen. Eine häufigere Überholung kann notwendig werden, wenn es bei hoher Zyklusrate oder langen Verschraubungszeiten eingesetzt wurde.
Entnehmen Sie Fett von jedem Gangsprung und schmieren Sie es auf ein weißes Papier.
Prüfen Sie das Fett. Wenn Metallspäne sichtbar sind, ist dies ein Zeichen für Abreibung in dem Gangsprung.
Säubern Sie alle Teile des Getriebes gründlich.
Kontrollieren Sie die Teile.
Kontrollieren Sie die Nadellager und ersetzen Sie sie, wenn Sie nicht bündig zur Oberfläche oder beschädigt sind.
Kontrollieren Sie die Zahnräder und ersetzen Sie Zahnräder oder den Zahnradsatz bei Beschädigung.
Kontrollieren Sie die O-Ringe und ersetzen Sie sie, wenn die O-Ringe rissig sind.
Geben Sie Fett hinzu und montieren Sie alle Teile.
Pflege der Notstrombatterie
Das Werkzeug verfügt über eine interne Notstrombatterie. Die Notstrombatterie wird beispielsweise verwendet, um die Funkkommunikation bei einem Wechsel des Hauptakkus aufrechtzuerhalten. Die Notstrombatterie erlaubt etwa 20 Sekunden zum Wechsel des Hauptakkus, bevor das Werkzeug abgeschaltet wird.

Verbinden Sie neu hergestellte Werkzeuge immer mit einem Hauptakku und lassen Sie sie zwei Stunden lang eingeschaltet, um die Notstrombatterie zu laden.

Ersetzen Sie die Notstrombatterie bei Verwendung einer Softwareversion, die älter als die in der folgenden Tabelle aufgeführten ist, mindestens alle 12 Monate. Der Austausch muss durch einen qualifizierten Servicetechniker durchgeführt werden. Ausgetauschte Notstrombatterien müssen gemäß den Recycling-Anweisungen recycelt werden.

Tauschen Sie die Notstrombatterie für Softwareversionen gemäß der folgenden Tabelle alle drei Jahre aus. Das verlängerte Wartungsintervall gilt für neue Batterien, die mit den in der folgenden Tabelle enthaltenen Softwareversionen verwendet werden. Beträgt das Alter der Notstrombatterie bereits fast 12 Monate, wird empfohlen, die Notstrombatterie beim Update auf die neue Software auszutauschen.
TBP/TBP-S | SRB31 | SRB81 | IxB |
Version 2.1.3 oder höher | Version 1.3.15 oder höher | Version 1.4.0 oder höher | Version 3.10.4 oder höher |
Lagerbedingungen
Die Lebensdauer der Notstrombatterie wird durch extreme Temperaturen beeinträchtigt. Lagern Sie das Werkzeug bei einer Umgebungstemperatur von 0-30 °C. Halten Sie keine zusätzlichen Notstrombatterien auf Lager.
Wenn ein neu hergestelltes Werkzeug eingelagert werden soll, achten Sie darauf, dieses zuvor für mindestens zwei Stunden einzuschalten.
Schalten Sie das Werkzeug während der Lagerung mindestens alle fünf Monate ein, um die Notstrombatterie aufzuladen. Das Werkzeug muss jedes Mal für mindestens zwei Stunden eingeschaltet werden.
Schmieranweisungen
Schmieranleitung
Fabrikat | Innenverzahnung | Universal | Frontgetriebe |
---|---|---|---|
Rhenus | LKR 03 | - | - |
Almagard | - | LE 3751 | - |
Molycote | - | - | BR2 Plus |
Schmierung
Bei jedem Servicefall gemäß dem Leitfaden zur Schmierung schmieren.
Weitere Informationen finden Sie im Abschnitt Ersatzteile unter ServAid - https://servaid.atlascopco.com.
Reparaturanleitung
Austausch von Ersatzteilen
Beim Austausch bestimmter elektrischer Teile des Werkzeugs werden die Werkzeugbezeichnung und die Parameter von ToolsTalk Service 2 gelöscht und müssen erneut eingerichtet werden. Weitere Informationen finden Sie in der ToolsTalk Service 2 User Edition-Bedienungsanleitung.
Demontage-/Montageanweisungen
Demontage
Frontgetriebe demontieren
Die Schraube ausbauen.
Drehen Sie den Verschlussring und ziehen Sie das Frontgetriebe heraus.
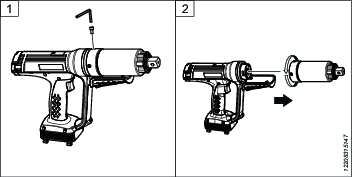
Doppel-Hebelstarter demontieren
Entfernen Sie die Sicherungsschraube.
Drehen Sie den Doppel-Hebelstarter etwas zur Seite um die Schraube am der Frontkappe sichtbar zu machen.
Die Schrauben entfernen.
Entfernen Sie die Kappe und die Kabel.
Ziehen Sie den Doppel-Hebelstarter heraus.
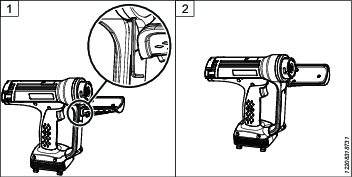
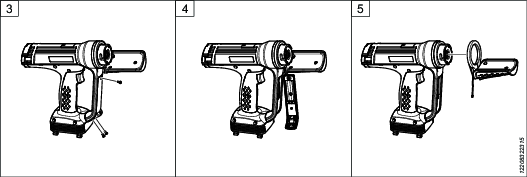
Antriebsmodul demontieren
Entfernen Sie die Schrauben und ziehen Sie das Antriebsmodul heraus.
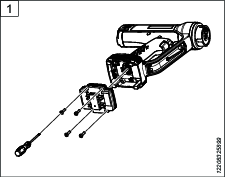
HMI demontieren
Entfernen Sie die Schrauben und die Rückabdeckung.
Ziehen Sie das HMI heraus und entfernen Sie das Kabel.
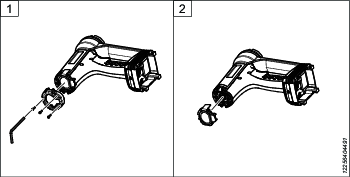
Griffs demontieren
Entfernen Sie die Schrauben, um den Griff auszubauen.
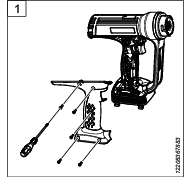
Startknopf demontieren
Drücken Sie den Startknopf (A) leicht und schieben Sie den Sicherungsstift (B) mit einer Pinzette heraus.
Entfernen Sie den Sicherungsstift mit einer Zange.
Entfernen Sie den Startknopf.
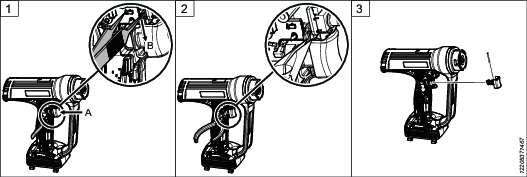
Funktionstaste und Konfigurationsplatine demontieren
Heben Sie die Funktionstaste zum Entfernen aus dem Schlitz.
Heben Sie die Konfigurationsplatine zum Entfernen.
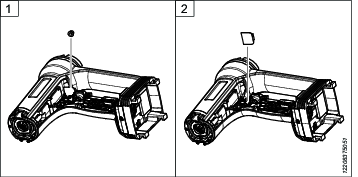
Hauptplatine demontieren
Entfernen Sie die Schrauben, um die Hauptplatine zu entfernen.
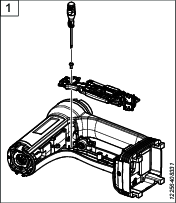
Innenverzahnung demontieren
Entfernen Sie zuerst die Schrauben, dann die Innenverzahnung und die Zwischenwelle.
Entfernen Sie die Schrauben, um die Getriebe-Identifikationstafel herausziehen zu können.
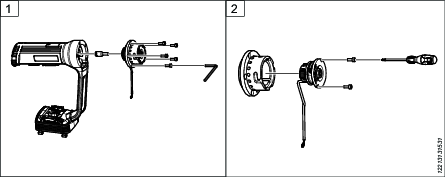
Vorderes Lagerschild demontieren
Entfernen Sie die Schrauben, um das Lagerschild auszubauen.
Entfernen Sie die Wellfeder mit einer Zange.
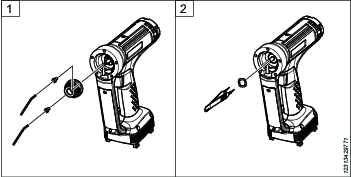
Kommutierungsplatine demontieren
Die Schrauben entfernen.
Entfernen Sie den Sicherungsring, um die Kommutierungsplatine auszubauen.
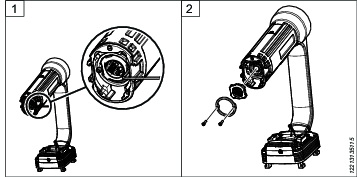
Magnetschalter demontieren
Verwenden Sie Zange 4080 1180 80, um dem Magnetschalter zu greifen und zu entfernen,
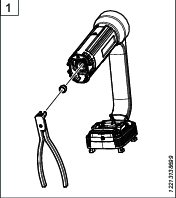
Hinteres Lagerschild demontieren
Entfernen Sie die Sicherungsschraube.
Entfernen Sie das Lagerschild.
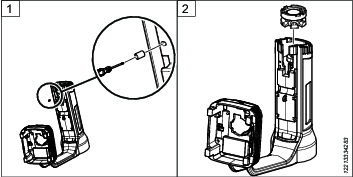
Zubehörplatine demontieren
Die Schraube ausbauen.
Entfernen Sie den Zubehördeckel.
Die Schraube ausbauen.
Ziehen Sie die Zubehörplatine heraus und entfernen Sie das Kabel.
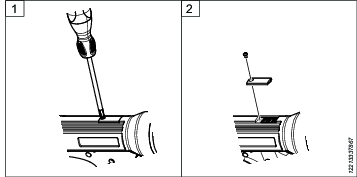
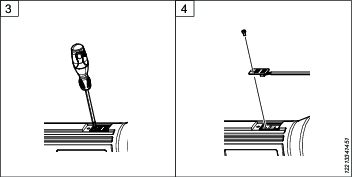
Montage
Zubehörplatine montieren
Schließen Sie das Kabel an und legen Sie die Zubehörplatine ein.
Ziehen Sie die Schraube in der Zubehörplatine an.
Ziehen Sie die Schraube am Deckel fest.
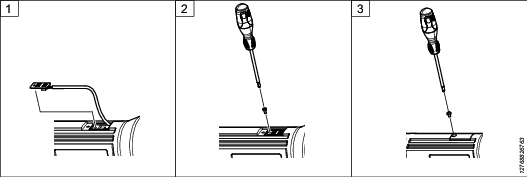
Hinteres Lager montieren
Fügen Sie das Lagerschild ein.
Ziehen Sie die Klemmschraube an.
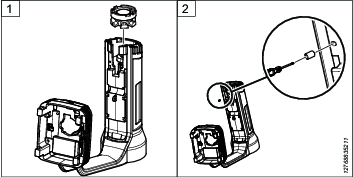
Magnetschalter montieren
Fügen Sie den Magnetschalter ein.
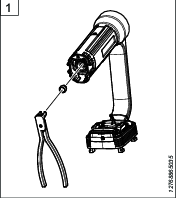
Kommutierungsplatine montieren
Fügen Sie die Kommutierungsplatine ein.
Ziehen Sie die Schrauben zur Befestigung des Verschlussring fest.
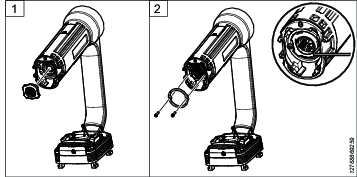
Vorderes Lagerschild montieren
Fügen Sie die Wellfeder ein.
Montieren Sie das Lagerschild. Führen Sie das Kabel durch den Kanal, um es zu befestigen.
Ziehen Sie die Schrauben fest.
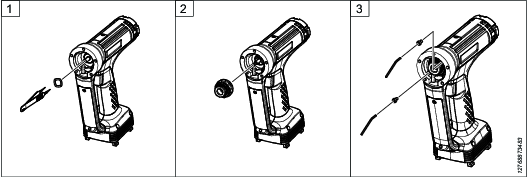
Innenverzahnung montieren
Fügen Sie die Getriebe-Identifikationstafel ein.
Setzen Sie die Innenverzahnung ein. Führen Sie das Kabel durch den Kanal.
Ziehen Sie die Schrauben zur Befestigung der Innenverzahnung fest.
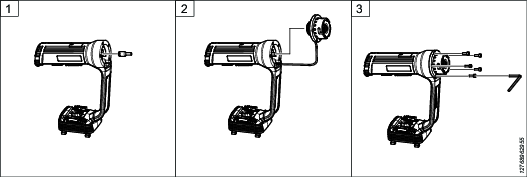
Hauptplatine montieren
Ziehen Sie die Schraube zur Befestigung der Hauptplatine an.
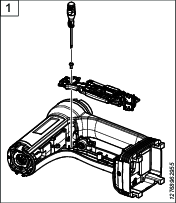
Funktionstaste und Konfigurationsplatine montieren
Fügen Sie die Konfigurationsplatine ein und schließen Sie das Kabel an.
Legen Sie die Funktionstaste in den Schlitz.
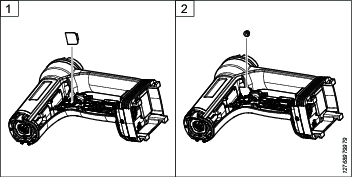
Startknopf montieren
Legen Sie den Startknopf in den Schlitz.
Drücken Sie den Startknopf (A) leicht und schieben Sie den Sicherungsstift (B) mit einer Zange ein.
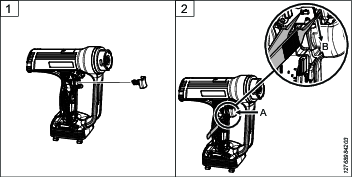
Griff montieren
Ziehen Sie die Schrauben zur Befestigung des Griffs fest.
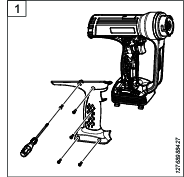
HMI montieren
Fügen Sie das HMI ein und schließen Sie das Kabel an.
Befestigen Sie die Rückabdeckung mit den Schrauben.
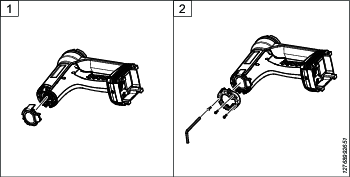
Antriebsmodul montieren
Befestigen Sie das Antriebsmodul mit den Schrauben.
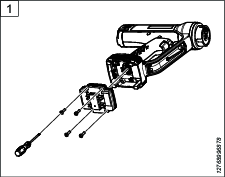
Doppel-Hebelstarter montieren
Montieren Sie den Doppel-Hebelstarter und führen Sie das Kabel durch den Kanal.
Befestigen Sie die Kabel am Frontdeckel.
Ziehen Sie die Schrauben zur Befestigung des Frontdeckels fest.
Drehen Sie den Doppel-Hebelstarter in die richtige Position.
Die Feststellschraube am Starter festziehen.
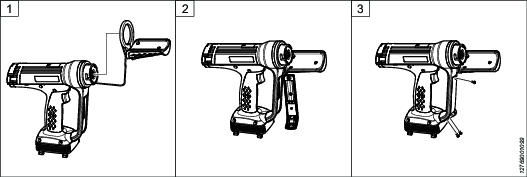
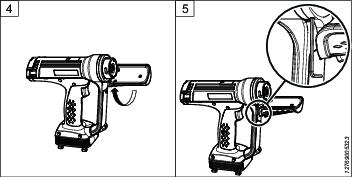
Frontgetriebe montieren
Montieren Sie das Frontgetriebe und drehen Sie den Verschlussring in die richtige Position.
Ziehen Sie die Schraube fest.
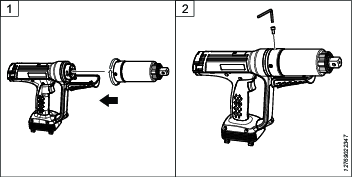
Aktualisieren der Werkzeug-Software
Informationen zum Aktualisieren der Werkzeug-Software finden Sie in der ToolsTalk Service 2 User Edition-Bedienungsanleitung unter Firmware kopieren.

So vermeiden Sie Werkzeugschäden:
Achten Sie darauf, dass der Akku vollständig aufgeladen ist, wenn Sie ein Softwareupdate durchführen.
Nehmen Sie bei laufendem Softwareupdate den Akku nicht aus dem Werkzeug heraus.
Nehmen Sie bei laufendem Softwareupdate die Speicherkarte nicht aus dem Werkzeug heraus.
Störungshilfe
Überhitztes Werkzeug
Bei korrekter Einstellung kann das Werkzeug sämtlichen normalen Arbeitsbedingungen standhalten.
Die Werkzeugtemperatur kann durch folgende Parameter beeinflusst werden:
kurze Zykluszeit
Drehmoment über Nennwert
Drehzahl zu niedrig
sehr hohes Reibmoment
sehr weiche Verbindungen
Umgebungstemperatur
Fehlercodes
Fehlerformat: E<Fehlergruppe>-<Fehlercode>

Der Fehlercode ist nur zur internen Verwendung vorgesehen.
Kann der Fehler nicht behoben werden, kontaktieren Sie Ihren Atlas Copco-Vertreter.
Fehlergruppe | Fehlerkategorie | Service-Tipps |
---|---|---|
none | item | none |
00 | Fehler bei der Aktualisierung der Werkzeug-SW | Problem mit der SW-Aktualisierung. Versuchen, das Werkzeug mit TTS2 zu verbinden. Dies kann weitere Informationen liefern. |
01 | Allgemeiner SW-Fehler | Allgemeines Softwareproblem. Aktualisierung auf neueste Software. |
02 | Allgemeiner SW-Fehler | Allgemeines Softwareproblem. Aktualisierung auf neueste Software. |
03 | Fehler der Frontleuchte | Problem mit der Frontleuchte. Kabel überprüfen bzw. Platine austauschen. |
04 | Werkzeug-HMI-Fehler | Werkzeug-HMI-Fehler. 1. Software mithilfe des FFU-Flags aktualisieren. 2. Das Kabel auf festen Sitz der Stecker überprüfen. |
05 | Allgemeiner SW-Fehler | Problem mit der Motorsteuerung. 1. Hauptplatine (MB) – Motorsteuerplatine (MCB) überprüfen. 2. Aktualisierung auf neueste Software. |
06 | Werkzeug-Speicherfehler | Problem mit dem Parameterspeicher. Versuchen Sie, das Werkzeug mit TTS2 zu verbinden, um es auf die Werksparameter zurückzusetzen. |
07 | Fehler der Motorabstimmung | Problem mit der Motorabstimmung. 1. Software auf neueste Version aktualisieren. 2. Versuchen, Tests in TTS2 auszuführen. 3. Sicherstellen, dass die Kommutierungsplatine im hinteren Teil des Werkzeugs korrekt montiert ist. Ein mögliches Problem ist, dass sie nicht korrekt in ihre Position gedrückt wurde. |
08 | Allgemeiner SW-Fehler | Parameterproblem. Versuchen Sie, das Werkzeug mit TTS2 zu verbinden, um es auf die Werksparameter zurückzusetzen. |
09 | Allgemeiner SW-Fehler | Funkproblem. 1. Das Kabel auf festen Sitz der Stecker überprüfen. 2. Werkzeug-Antennenkabel überprüfen. 3. Software mithilfe des FFU-Flags aktualisieren. |
10 | Fehler bei der Aktualisierung der Funk-SW | Problem mit der Funk-SW-Aktualisierung. 1. Das Kabel auf festen Sitz der Stecker überprüfen. 2. Werkzeug-Antennenkabel überprüfen. 3. Software mithilfe des FFU-Flags aktualisieren. |
11 | Allgemeiner SW-Fehler | Funkproblem. 1. Das Kabel auf festen Sitz der Stecker überprüfen. 2. Werkzeug-Antennenkabel überprüfen. 3. Software mithilfe des FFU-Flags aktualisieren. |
12 | Allgemeiner SW-Fehler | Funk-Bluetooth-Problem. 1. Kabel zum Funkmodul überprüfen. 2. Software mithilfe des FFU-Flags aktualisieren. |
13 | Allgemeiner SW-Fehler | Funk-WIFI-Problem. 1. Kabel des Funkmoduls überprüfen. 2. Software mithilfe des FFU-Flags aktualisieren. |
14 | Allgemeiner SW-Fehler | Problem mit der Smart Web-Konfiguration. 1. Kabel des Funkmoduls überprüfen. 2. Software mithilfe des FFU-Flags aktualisieren. |
15 | RBU-HW-Fehler | IAM-Problem. Versuchen, die SD-Karten-Prüfsumme in TTS2 zurückzusetzen. |
16 | RBU-HW-Fehler | IAM-Problem. Versuchen, die SD-Karten-Prüfsumme in TTS2 zurückzusetzen. |
17 | Allgemeiner SW-Fehler | Problem mit dem Parameterspeicher. Versuchen Sie, das Werkzeug mit TTS2 zu verbinden, um es auf die Werksparameter zurückzusetzen. |
18 | Allgemeiner HW-Fehler | Problem der Anzeigeplatine. |
19 | Allgemeiner SW-Fehler | Allgemeines Softwareproblem. Aktualisierung auf neueste Software. |
20 | Allgemeiner SW-Fehler | Internes Kommunikationsproblem. Hauptplatine – Motorsteuerplatine überprüfen. |
21 | Allgemeiner SW-Fehler | Internes Kommunikationsproblem. Hauptplatine – Motorsteuerplatine überprüfen. |
22 | Allgemeiner SW-Fehler | Allgemeines Softwareproblem. Aktualisierung auf neueste Software. |
23 | Fehler des Zusatzakkus | Problem mit dem Zusatzakku. Verbindung des Zusatzakkus überprüfen. |
24 | Allgemeiner SW-Fehler | Allgemeines Softwareproblem. Aktualisierung auf neueste Software. |
25 | Fehler bei der Aktualisierung der Motorsteuerplatine | Problem bei der Software-Aktualisierung der Motorsteuerplatine (MCB). 1. MCB-Verbindung überprüfen. 2. Aktualisierung auf neueste Software. |
26 | Allgemeiner SW-Fehler | Kommunikationsfehler der Motorsteuerplatine. 1. MCB-Verbindung überprüfen. 2. Aktualisierung auf neueste Software. |
27 | Allgemeiner SW-Fehler | Allgemeines Hardware- oder Softwareproblem. |
28 | Fehler der Stromversorgung | Allgemeines Problem mit der Stromversorgung. |
29 | Allgemeiner SW-Fehler | Problem mit der Werkzeug-Geräteerkennung. Verbindung mit TTS2 kann helfen, die Werkzeugkennung neu zu schreiben. |
30 | Allgemeiner SW-Fehler | Problem mit der Werkzeug-Geräteerkennung. Verbindung mit TTS2 kann helfen, die Werkzeugkennung neu zu schreiben. |
31 | Allgemeiner SW-Fehler | Problem mit dem Drehmomentgeber. Drehmomentgeber und Kabel überprüfen. |
32 | Allgemeiner Verschraubungsfehler | Allgemeiner Verschraubungsfehler. |
33 | Werkzeug-Auslöserfehler | Problem mit dem Werkzeugauslöser. 1. Auslöser in TTS2 testen. 2. Sicherstellen, dass der Auslöser nicht beschädigt ist. 3. Hauptplatine austauschen. |
34 | Allgemeiner SW-Fehler | Problem mit der Verschraubungskurve. |
35 | Allgemeiner SW-Fehler | Problem mit der Verschraubungskurve. |
36 | Allgemeiner HW-Fehler | Problem mit der Hardware oder der Verbindung zwischen den MB-/MCB-Platinen. 1. Mechanische Verbindung überprüfen. 2. MB und/oder MCB ersetzen. |
37 | Fehler der Funktionstaste | Problem mit dem Wechsel der Werkzeugrichtung. 1. Funktionstaste in TTS2 testen. 2. SW auf neueste Version aktualisieren. |
38 | Allgemeiner HW-Fehler | Problem mit dem Drehmomentgeber. Drehmomentgeber und Kabel überprüfen. |
39 | Allgemeiner HW-Fehler | Allgemeines HW-Problem. |
40 | Allgemeiner HW-Fehler | Allgemeines HW-Problem. Versuchen, die MB auszutauschen. |
41 | Fehler bei der Aktualisierung der Werkzeug-SW | Problem mit der SW-Aktualisierung. Verbindung des Werkzeugs mit TTS2 kann weitere Informationen liefern. |
42 | Fehler bei der Aktualisierung der Werkzeug-SW | Problem mit der SW-Aktualisierung. Verbindung des Werkzeugs mit TTS2 kann weitere Informationen liefern. |
43 | Allgemeiner HW-Fehler | Problem der Anzeigeplatine. <SRB HA verwendet diese Anzeigeplatine nicht> |
44 | Allgemeiner HW-Fehler | Problem mit dem zweiten Auslöser. 1. Kabel bzw. Platine des zweiten Auslösers überprüfen. 2. Getriebe-ID-Platine von der Frontleuchtenplatine trennen. 3. Frontleuchtenplatine austauschen. |
45 | Fehler beim Lesen der SRB HA-Werkzeugkonfiguration | Problem mit dem Parameterspeicher. Versuchen Sie, das Werkzeug mit TTS2 zu verbinden, um es auf die Werksparameter zurückzusetzen. |
46 | Allgemeiner SW-Fehler | SRB HA – Problem mit Smart-Ergebnis. 1. Versuchen, „RESULT.CSV“ aus dem IAM im Ordner HA zu entfernen. 2. Software aktualisieren. |
47 | Allgemeiner SW-Fehler | SRB HA – Problem mit Smart-Programm. 1. Auf neueste Werkzeug-Software aktualisieren. 2. Werkseinstellungen in TTS2 wiederherstellen. |
48 | Allgemeiner SW-Fehler | SRB HA – Problem mit Smart-Programm oder Set&Go. 1. Auf neueste Werkzeug-Software aktualisieren. 2. Werkseinstellungen in TTS2 wiederherstellen. |
49 | Allgemeiner SW-Fehler | Allgemeines Softwareproblem. Aktualisierung auf neueste Software. |
50 | Allgemeiner HW-Fehler | Problem mit IAM SD-Karte. |
51 | Allgemeiner SW-Fehler | Allgemeines Softwareproblem. Aktualisierung auf neueste Software. |
52 | Allgemeiner SW-Fehler | Problem mit dem Parameterspeicher. Versuchen Sie, das Werkzeug mit TTS2 zu verbinden, um es auf die Werksparameter zurückzusetzen. |
53 | Fehler mit Offenmaul-Konfiguration | Problem mit der Offenmaul-Konfiguration. <SRB HA unterstützt diese Funktion nicht> |
54 | Allgemeiner SW-Fehler | Allgemeines HW-Problem. |
55 | HW-Fehler der Frontleuchte | Problem mit der Frontleuchte. 1. Kabel überprüfen bzw. Platine austauschen. 2. Aktualisierung auf neueste Software. |
56 | Drucktasten-Fehler | Fehler der Funktionstaste. Test der Funktionstaste in TTS2 ausführen. Tastenplatine oder Kabel austauschen. |
57 | Allgemeiner SW-Fehler | HW-Eingangsfehler. Versuchen, Hauptplatine auszutauschen. |
58 | Allgemeiner SW-Fehler | HW-Eingangsfehler. Versuchen, Hauptplatine auszutauschen. |
59 | Allgemeiner SW-Fehler | Probleme bei der Einrichtung des Funkmoduls im Zugangspunktmodus. |
60 | Fehler beim Aktualisieren der SW der Anzeigeplatine. | Problem der Anzeigeplatine. <SRB HA verwendet diese Anzeigeplatine nicht> |
61 | Allgemeiner SW-Fehler | Kommunikationsproblem der Frontleuchte. Kabel bzw. Platine der Frontleuchte überprüfen. |
62 | RBU-HW-Fehler | Problem mit IAM SD-Karte. |
63 | Allgemeiner HW-Fehler | FPGA-Fehler der Hauptplatine. 1. Versuchen, mit neuester Software zu aktualisieren. 2. Hauptplatine austauschen. |
64 | Allgemeiner HW-Fehler | FPGA-Aktualisierungsfehler der Hauptplatine. 1. Versuchen, mithilfe des FFU-Flags mit der neuesten Software zu aktualisieren. 2. Hauptplatine austauschen. |
65 | Allgemeiner HW-Fehler | Problem mit dem Parameterspeicher. Versuchen Sie, das Werkzeug mit TTS2 zu verbinden, um es auf die Werksparameter zurückzusetzen. |
66 | Allgemeiner SW-Fehler | Internes Kommunikationsproblem. Im Zusammenhang mit Funk- oder TTS2-Kommunikation. |
67 | Allgemeiner SW-Fehler | Internes Kommunikationsproblem. Im Zusammenhang mit Funk- oder TTS2-Kommunikation. |
68 | Allgemeiner SW-Fehler | Internes Kommunikationsproblem. Im Zusammenhang mit Funk- oder TTS2-Kommunikation. |
69 | Allgemeiner SW-Fehler | Allgemeines SW-Problem. |
70 | Allgemeiner SW-Fehler | Allgemeines SW/HW-Problem. |
71 | Allgemeiner SW-Fehler | Allgemeines SW/HW-Problem. |
72 | Allgemeiner SW-Fehler | Allgemeines SW-Problem. |
73 | Fehler bei der Softwareaktualisierung | Allgemeines Problem bei der SW-Aktualisierung. |
74 | FH_ECG_ToolsTalkServices2Test | Problem mit TTS2-gestützten Tests. |
Recycling
Umweltschutzbestimmungen
Nachdem ein Produkt seinen Zweck erfüllt hat, muss es ordnungsgemäß recycelt werden. Zerlegen Sie das Produkt und recyceln Sie die Komponenten gemäß örtlicher Vorschriften.
Batterien sollten an Ihre öffentliche Batterieverwertungsstelle weitergegeben werden.
Recycling-Informationen
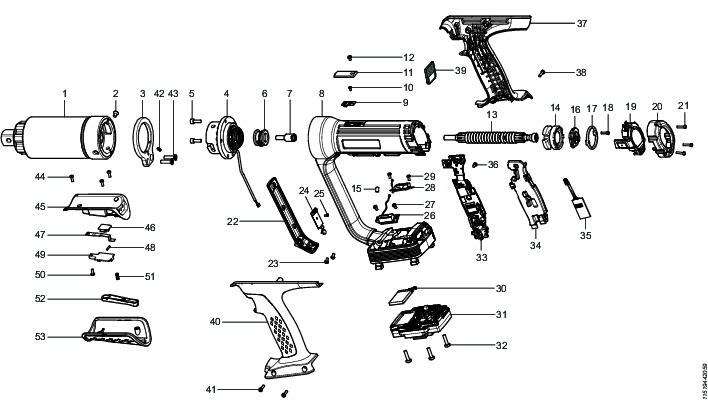
Pos. | Teil | Anmerkungen | Recyceln als |
---|---|---|---|
1 | Frontgetriebe |
| Metall, Stahl |
2 | Schraube | Metall, Stahl | |
3 | Befestigungsplatte | Metall, Aluminium | |
4 | Innenverzahnung | Metall, Stahl | |
5 | Schraube | 5 Stück | Metall, Stahl |
6 | Messwertgeber | Elektronik | |
7 | Zwischenwelle | Metall, Stahl | |
8 | Motorrahmen und Stator | Metall, Aluminium und Stahl | |
9 | Zubehörplatine | Elektronik | |
10 | Schraube | Metall, Stahl | |
11 | Zubehördeckel | Metall, Aluminium | |
12 | Schraube | Metall, Stahl | |
13 | Läufer | Metall, Neodym | |
14 | Hinteres Lagerschild | Metall, Aluminium | |
15 | Schraube | Metall, Stahl | |
16 | Kommutierungsplatine | Elektronik | |
17 | Verschlussring | Metall, Aluminium | |
18 | Schraube | 2 Stück | Metall, Stahl |
19 | HMI komplett | Elektronik | |
20 | Rückseite | Metall, Aluminium | |
21 | Schraube | 3 Stück | Metall, Stahl |
22 | Frontdeckel | Metall, Aluminium | |
23 | Schraube | 3 Stück | Metall, Stahl |
24 | Lichtplatine vorne | Elektronik | |
25 | Schraube | Metall, Stahl | |
26 | Antenne | Elektronik | |
27 | Schraube | 2 Stück | Metall, Stahl |
28 | Antenne | Elektronik | |
29 | Schraube | 2 Stück | Metall, Stahl |
30 | Notstrombatterie | Akku, Lithium-Ionen | |
31 | Antriebsmodul | Elektronik | |
32 | Schraube | 4 Stück | Metall, Stahl |
33 | Hauptplatinenmodul | Elektronik | |
34 | Hauptplatine Dichtungsgummi | Gummi, PUR | |
35 | Funkmodul | Elektronik | |
36 | Schraube | Metall, Stahl | |
37 | Handgriff rechts | Kunststoff, Sonstiges, PA | |
38 | Schraube | 5 Stück | Metall, Stahl |
39 | Konfigurationsplatine | Elektronik | |
40 | Handriff links | Kunststoff, Sonstiges, PA | |
41 | Schraube | 2 Stück | Metall, Stahl |
42 | Schraube | Metall, Stahl | |
43 | Schraube | 2 Stück | Metall, Stahl |
44 | Schraube | 3 Stück | Metall, Stahl |
45 | Basis Doppel-Hebelstarter | Metall, Zink | |
46 | Schalter | Elektronik | |
47 | Feder | Metall, Stahl | |
48 | Pin | Metall, Stahl | |
49 | Drückerhalter | Metall, Stahl | |
50 | Schraube | Metall, Stahl | |
51 | Feder | Metall, Stahl | |
52 | Startknopf | Metall, Stahl | |
53 | Griff Doppel-Hebelstarter | Kunststoff, Sonstiges, PA |