MWR-300 TA
Product Information
General Information
Safety Signal Words
The safety signal words Danger, Warning, Caution, and Notice have the following meanings:
DANGER | DANGER indicates a hazardous situation which, if not avoided, will result in death or serious injury. |
WARNING | WARNING indicates a hazardous situation which, if not avoided, could result in death or serious injury. |
CAUTION | CAUTION, used with the safety alert symbol, indicates a hazardous situation which, if not avoided, could result in minor or moderate injury. |
NOTICE | NOTICE is used to address practices not related to personal injury. |
Warranty
Product warranty will expire 12 months after the product is first taken into use, but will in any case expire at the latest 13 months after delivery.
Normal wear and tear on parts is not included within the warranty.
Normal wear and tear is that which requires a part change or other adjustment/overhaul during standard tools maintenance typical for that period (expressed in time, operation hours or otherwise).
The product warranty relies on the correct use, maintenance, and repair of the tool and its component parts.
Damage to parts that occurs as a result of inadequate maintenance or performed by parties other than Atlas Copco or their Certified Service Partners during the warranty period is not covered by the warranty.
To avoid damage or destruction of tool parts, service the tool according to the recommended maintenance schedules and follow the correct instructions.
Warranty repairs are only performed in Atlas Copco workshops or by Certified Service Partners.
Atlas Copco offers extended warranty and state of the art preventive maintenance through its ToolCover contracts. For further information contact your local Service representative.
For electrical motors:
Warranty will only apply when the electric motor has not been opened.
ServAid
ServAid is a portal that is continuously updated and contains Technical Information, such as:
Regulatory and Safety Information
Technical Data
Installation, Operation and Service Instructions
Spare Parts Lists
Accessories
Dimensional Drawings
Please visit: https://servaid.atlascopco.com.
For further Technical Information, please contact your local Atlas Copco representative.
Country of Origin
For the Country of Origin, please refer to the information on the product label.
Dimensional Drawings
Dimensional Drawings can be found either in the Dimensional Drawings Archive, or on ServAid.
Please visit: http://webbox.atlascopco.com/webbox/dimdrw or https://servaid.atlascopco.com.
Overview
Applications
The MWR-300 TA is a mechanical click-wrench combined with an electronic torque transducer.
The MWR-300 TA are equipped with the ISM band radio interface (characterized by a frequency equal to 868 MHz / 915 MHz) for wireless connection with Focus 61.
The MWR-300 TA works with Focus 61, which defines the tightening programs for the MWR-300 TA.
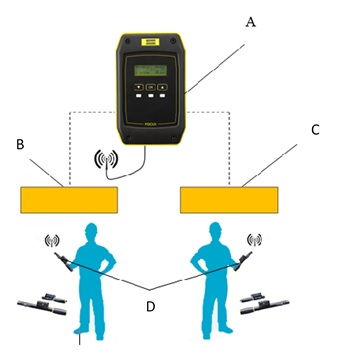
A | Focus 61 | B | Station 1 |
C | Station 2 | D | MWR-300 TA |

For more information about the configuration and the use of the MWR-300 TA, refer to the Focus 61 User Guide.
LEDs
The MWR-300 TA has three sets of LEDs and each set consists of red, green, yellow and blue LEDs.

A | LED | B | Right view |
C | Left view | D | Top view |
In the following, a description of the LEDs behavior.
If the MWR-300 TA is out from the MWR Charging cradle, the battery is charged and at least a job is available on the MWR-300 TA:
Yellow LED blinks every 3 s and blue LED blinks every 1 s: the MWR-300 TA is ready to use and any force is applied.
Green LED on for 3 s and blue LED blinks every 1 s: the last tightening is OK and any force is applied on the MWR-300 TA after click.
Red LED on for 3 s and blue LED blinks every 1 s: the last tightening is NOK and any force is applied on the MWR-300 TA after click.
Yellow LED blinks with an interval less than 1 s: the MWR-300 TA is measuring.
Green LED on for 3 s, yellow LED on during deadtime and blue LED on after deadtime: the last tightening is OK (TOK) and any force is applied on MWR-300 TA after click.
Red LED on for 3 s, yellow LED on during deadtime and blue LED on after deadtime: the last tightening is NOK (TNOK) and any force is applied on MWR-300 TA after click.
Red LED on for 3 s, yellow LED on during deadtime and blue LED bliks every 1 s: the last tightening is rehit or NOK and any force is applied on MWR-300 TA after click.
If the MWR-300 TA is out from the MWR Charging cradle, the battery is out of power and at least, a job is available on the MWR-300 TA:
Red LED blinks every 3 s and blue LED blinks every 1 s: the MWR-300 TA is ready to use.
Green LED on for 3 s and blue LED blinks every 1 s: the last tightening is OK and any force is applied on the MWR-300 TA after click.
Red LED on for 3 s and blue LED blinks every 1 s: the last tightening is NOK and any force is applied on the MWR-300 TA after click.
Red LED blinks every 1 s: the MWR-300 TA is measuring.
Green LED on for 3 s, yellow LED on during deadtime and blue LED on after deadtime: the last tightening is OK (TOK) and any force is applied on MWR-300 TA after click.
Red LED on for 3 s, yellow LED on during deadtime and blue LED on after deadtime: the last tightening is NOK (TNOK) and any force is applied on MWR after click.
Red LED on for 3 s, yellow LED on during deadtime and blue LED bliks every 1 s: the last tightening is rehit or NOK and any force is applied on MWR-300 TA after click.
If the MWR-300 TA is out from the Charging cradle, the battery is charged and no jobs are available on the MWR-300 TA:
Yellow LED blinks every 3 s: theMWR-300 TA is ready to use and any force is applied.
Red LED on for 3 s: the last tightening is OK and any force is applied on the MWR-300 TA after click.
Red LED on for 3 s and blue LED blinks every 1 s: the last tightening is NOK and any force is applied on the MWR-300 TA after click.
Yellow LED blinks with an interval less than 1 s: the MWR-300 TA is measuring.
If the MWR-300 TA is out from the MWR Charging cradle, the battery is out of power and no jobs are available on the MWR-300 TA:
Red LED blinks every 3 s: the MWR-300 TA is ready to use and any force is applied.
Red LED on for 3 s: the last tightening is OK and any force is applied on the MWR-300 TA after click.
Red LED on for 3 s and blue LED blinks every 1 s: the last tightening is NOK and any force is applied on the MWR-300 TA after click.
Red LED blinks every 1 s: the MWR-300 TA is measuring.
If the MWR-300 TA is in the MWR Charging cradle, the battery is charged and the MWR-300 TA is ready to use:
Yellow LED on permanently and the blue LED blinks every 1 s: active job available on the MWR-300 TA.
Yellow LED on permanently: no active job available on the MWR-300 TA.
If the MWR-300 TA is in the MWR Charging cradle, the battery is out of power and the MWR-300 TA is ready to use:
Yellow LED on permanently and the blue LED blinks every 1 s: active job available on the MWR-300 TA.
Yellow LED on permanently: no active job available on the MWR-300 TA.
If the MWR-300 TA is out the MWR Charging cradle and an error occurred: Red LED blinks every 300 ms
If the MWR-300 TA is in the MWR Charging cradle and an error occurred: Red LED blinks every 300 ms and yellow LED on permanently.
If the MWR-300 TA is out the MWR Charging cradle and it is out the radio range: Red LED, the green LED and the yellow LED blink every 3 s.
If the MWR-300 TA is in the Charging cradle and out of the radio range: Yellow LED blinks on permanently.
Radio module frequencies

Refer to the local Regulatory Domain for frequency selection.
Europe
Number | Channel | Frequency [MHz] | Data rate [bit/s] |
1 | 51 | 868.034 | 38400 |
2 | 56 | 868.297 | 38400 |
3 | 60 | 868.502 | 38400 |
4 | 64 | 868.706 | 38400 |
5 | 69 | 868.006 | 38400 |
7 | 82 | 869.573 | 38400 |
8 | 84 | 869.840 | 38400 |
9 | 51 | 868.034 | 19200 |
10 | 56 | 868.297 | 19200 |
11 | 60 | 868.502 | 19200 |
12 | 64 | 868.706 | 19200 |
13 | 69 | 869.006 | 19200 |
15 | 82 | 869.573 | 19200 |
16 | 84 | 869.840 | 19200 |
USA
Number | Channel | Frequency [MHz] | Data rate [bit/s] |
1 | 2 | 902.791 | 38400 |
2 | 9 | 906.478 | 38400 |
3 | 10 | 907.004 | 38400 |
4 | 17 | 910.691 | 38400 |
5 | 20 | 912.271 | 38400 |
6 | 31 | 918.064 | 38400 |
7 | 32 | 918.590 | 38400 |
8 | 46 | 925.963 | 38400 |
9 | 2 | 902.791 | 19200 |
10 | 9 | 906.478 | 19200 |
11 | 10 | 907.004 | 19200 |
12 | 17 | 910.691 | 19200 |
13 | 20 | 912.271 | 19200 |
14 | 31 | 918.064 | 19200 |
15 | 32 | 918.590 | 19200 |
16 | 46 | 925.963 | 19200 |
Korea
Number | Channel | Frequency [MHz] | Data rate [bit/s] |
1 | 85 | 917.300 | 38400 |
3 | 91 | 918.900 | 38400 |
4 | 94 | 919.900 | 38400 |
5 | 97 | 920.500 | 38400 |
6 | 100 | 921.100 | 38400 |
7 | 103 | 922.500 | 38400 |
8 | 106 | 923.100 | 38400 |
9 | 85 | 917.300 | 19200 |
11 | 91 | 918.900 | 19200 |
12 | 94 | 919.900 | 19200 |
13 | 97 | 920.500 | 19200 |
14 | 100 | 921.100 | 19200 |
15 | 103 | 922.500 | 19200 |
16 | 106 | 923.100 | 19200 |
Japan
Number | Channel | Frequency [MHz] | Data rate [bit/s] |
1 | 108 | 922.800 | 38400 |
2 | 109 | 923.400 | 38400 |
3 | 110 | 923.600 | 38400 |
4 | 111 | 924.200 | 38400 |
5 | 112 | 924.600 | 38400 |
6 | 113 | 924.800 | 38400 |
7 | 114 | 926.000 | 38400 |
8 | 115 | 926.200 | 38400 |
9 | 116 | 926.600 | 38400 |
10 | 117 | 926.800 | 38400 |
11 | 118 | 927.600 | 38400 |
12 | 108 | 922.800 | 19200 |
13 | 109 | 923.400 | 19200 |
14 | 110 | 923.600 | 19200 |
15 | 111 | 924.200 | 19200 |
16 | 112 | 924.600 | 19200 |
17 | 113 | 924.800 | 19200 |
18 | 114 | 926.000 | 19200 |
19 | 115 | 926.200 | 19200 |
20 | 116 | 926.600 | 19200 |
21 | 117 | 926.800 | 19200 |
22 | 118 | 927.600 | 19200 |

This device may not accept interference in the band 520 MHz - 720 MHz, including interference that may cause undesired operation.
ISM band radio interface
Frequency bands: 868 MHz / 915 MHz
RF output power: 3 mW
Receive input level (max): -112 dBm
Product data
Operating torque measuring range: 60 [N·m] - 300 [N·m] / 44.3 [lb·ft] - 221.3 [lb·ft]
Drive: 14x18 mm.
Overall length: 900 mm.
Operating torque range: from 20% to 100% of the capacity
Torque measurement accuracy (within the operating torque range): 2%
Mechanical repeatability click: ± 4%
Overload capacity: 120 % of nominal capacity
Maximum angular speed: 250 °/s
Angle measurement accuracy: ± 3.6 ° / 360 ° (at 6 ° per second)
Temperature stability of torque measurement: +10 °C to +40 °C (10 °F to 104 °F)
Tightening results memory capacity: 8100 Data sets (maximum)
MWR-300 TA Reference Firmware version: 3.0.0
Power supply: 1.2 V rechargeable battery
Environmental conditions
Comply with the following environmental conditions during the operation:
Indoor Use ONLY
Room temperature: 5 °C to 40 °C (41 °F to 104 °F)
Maximum relative humidity 80% for temperature up to 31 °C (88 °F) decreasing linearly to 50% relative humidity at 40 °C (104 °F)
Accessories
MWR Charging cradle
To recharge the battery of the MWR-300 TA with the MWR Charging Cradle:
Connect the MWR Charging Cradle to the AC power.
Insert the MWR-300 TA into the MWR Charging Cradle:
When the wrench is placed into the MWR Charging Cradle, the red, yellow and green LEDs (placed on three sides of the MWR-300 TA) flash alternately. This indicates that the wrench sets the internal offset (zero point) for the torque transducer and runs a quick self-test.
When the MWR-300 TA is in charging mode and the internal offset has been performed, the yellow LED of the MWR-300 TA is on and the Status LED of the MWR Charging Cradle is flashing (green colored).
When the charging process of the MWR-300 TA is complete, the Status LED of the MWR Charging Cradle is constantly on (green colored).

For more information on the MWR Charging Cradle functioning, refer to the MWR Charging Cradle Product Instructions.
Battery
A rechargeable NiMH AAA battery 1.2 V 1000 mAh provides power to the MWR-300 TA.

Use only rechargeable batteries. Do not use other battery types.
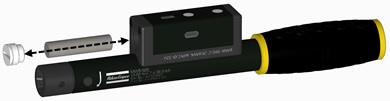
A | Front cap | B | + (positive pole) |
To power on the MWR-300 TA:
Remove the front cap of the MWR-300 TA by using a flat screwdriver.
Insert the battery (with the correct polarity) into the dedicated case.
Screw the front cap of the MWR-300 TA by using a flat screwdriver.
To power off the MWR-300 TA:
Remove the front cap of the MWR-300 TA by using a flat screwdriver.
Remove the battery from the case.
Screw the front cap of the MWR-300 TA by using a flat screwdriver.
End Fittings
At the front part, the wrench has a standard drive (14x18 mm) which allows to attach different types of end fittings.
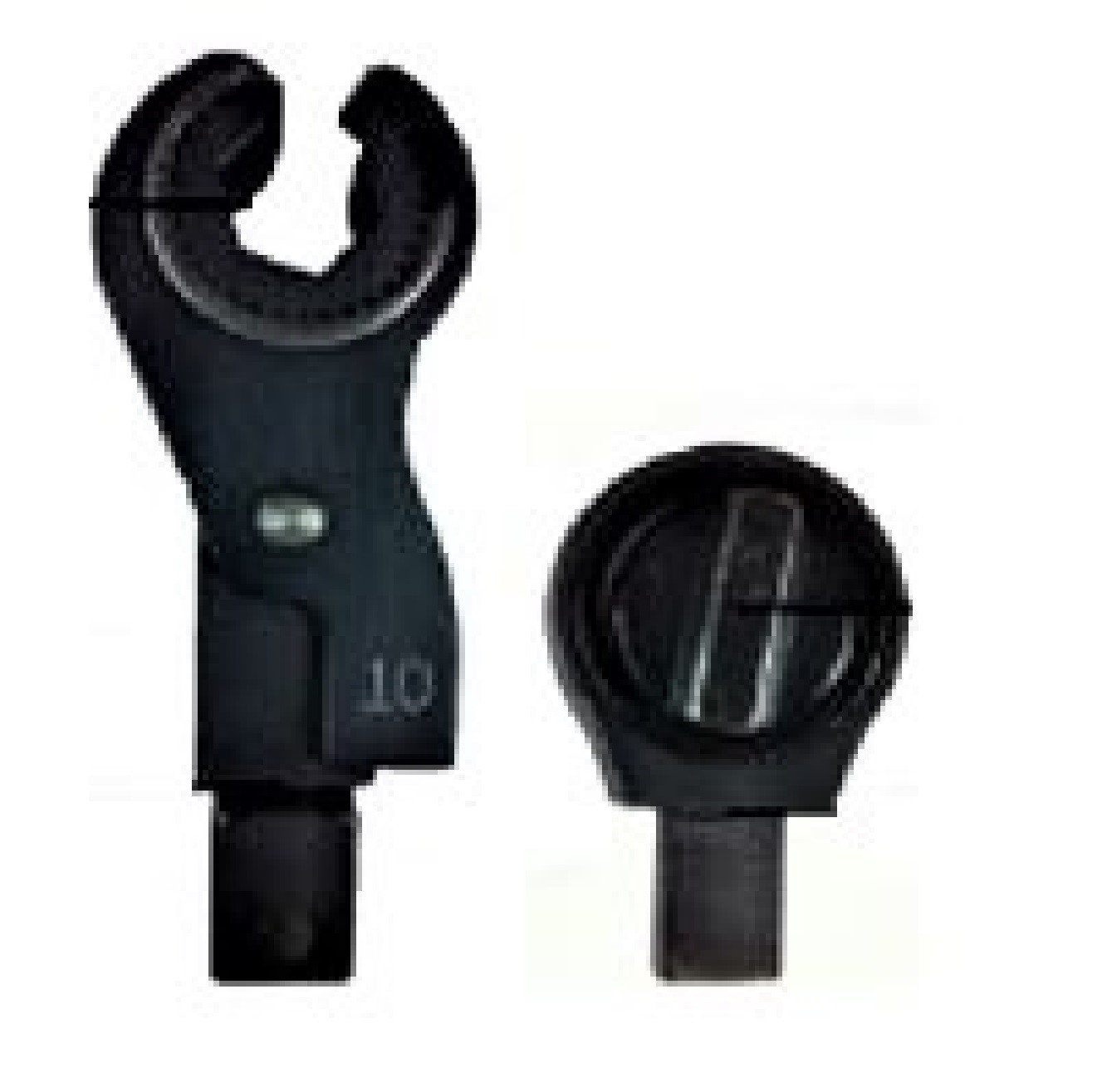

For information on the compensations, please refer to the Focus 61 User guide.
Protection cover
The protection cover protects the MWR-300 TA electronic housing from accidental light impacts in production.
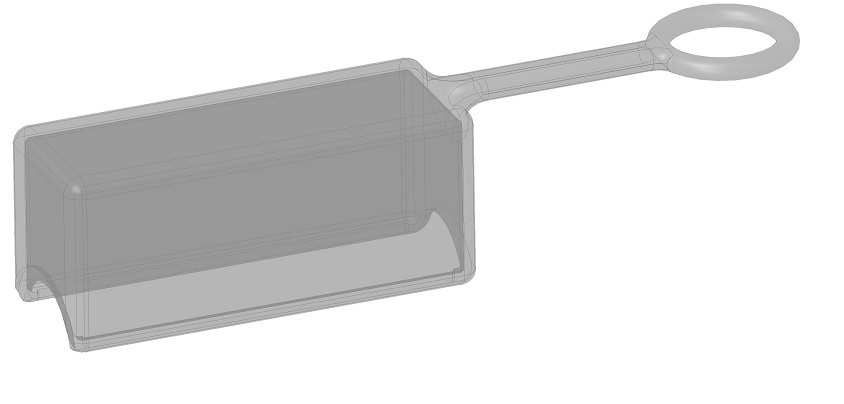
Insert the ring of the protection cover on the handle of the MWR-300 TA and slide it to the electronic housing.
Operation
Ergonomic Guidelines
Consider your workstation as you read through this list of general ergonomic guidelines to identify areas for improvement in posture, component placement, or work environment.
Take frequent breaks and change work positions frequently.
Adapt the workstation area to your needs and the work task.
Adjust for a convenient reach range by determining where parts and tools need to be located to avoid static load.
Use workstation equipment such as tables and chairs appropriate for the work task.
Avoid work positions above shoulder level or with static holding during assembly operations.
When working above shoulder level, reduce the load on the static muscles by lowering the weight of the tool, using for example torque arms, hose reels or weight balancers. You can also reduce the load on the static muscles by holding the tool close to the body.
Take frequent breaks.
Avoid extreme arm or wrist postures, particularly during operations requiring a degree of force.
Adjust for a convenient field of vision that requires minimal eye and head movements.
Use appropriate lighting for the work task.
Select the appropriate tool for the work task.
In noisy environments, use ear protection equipment.
Use high-quality inserted tools and consumables to minimize exposure to excessive levels of vibration.
Minimize exposure to reaction forces.
When cutting:
A cut-off wheel can get stuck if the cut-off wheel is bent or not guided properly. Use the correct flange for the cut-off wheel and avoid bending the cut-off wheel during operation.
When drilling:
The drill might stall when the drill bit breaks through. Use support handles if the stall torque is high. The safety standard ISO11148 part 3 recommends using a device to absorb a reaction torque above 10 Nm for pistol grip tools and 4 Nm for straight tools.
When using direct-driven screwdrivers or nutrunners:
Reaction forces depend on the tool settings and joint characteristics. Strength and posture determine the amount of reaction force that an operator can tolerate. Adapt the torque setting to the operator's strength and posture and use a torque arm or reaction bar if the torque is too high.
In dusty environments, use a dust extraction system or wear a mouth protection mask.
Wrong handling
The operation of the MWR-300 TA must be carried out by the middle of the handle.
Pull / Push only in the tightening direction.
Do not touch the body of the MWR-300 TA during tightening operations. Positioning the thumb on the tube alters the click value!
Do not hold the body of the MWR-300 TA during tightening operations. The operation of the MWR-300 TA must be carried out by the middle of the handle.
Correct handling and click tightening
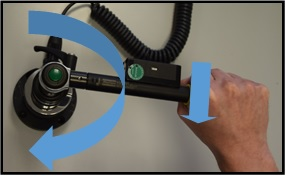
The screw should be tightened in even strokes.
The closing speed should allow an immediate interruption of the tightening operation as the MWR-300 TA clicks.
The operation of the MWR-300 TA must be carried out by the middle of the handle.
The force should be one-handed, uniform, parallel and applied with no interruptions until the tool clicks.

After the automatic release (click), the MWR-300 TA must not be moved further.
Operating Instructions
Adjusting the click-torque
Insert the Setting key in the MWR-300 TA.
Rotate A counterclockwise to unlock the Setting key.
Rotate B clockwise to increase the torque, or counterclockwise to decrease the torque.
Rotate A clockwise to lock the Setting key.
Make sure that the Setting key is locked properly after adjusting the mechanical click. After locking the Setting key, it is highly recommended to perform at least 25 clicks to verify the mechanical click suits.
The label printed on each MWR-300 TA indicates the torque range of the wrench.
Tightening Test
The Focus 61 sends the tightening program (Pset and Job) to the MWR-300 TA.

For more information on the configuration and the use of MWR-300 TA, refer to the Focus 61 User Guide.
When the MWR-300 TA receives the tightening program and the wrench is ready for use, the blue LED flashes.
Load the MWR-300 TA following the direction of the arrow as shown on the label on the MWR-300 TA body (see the figure below):
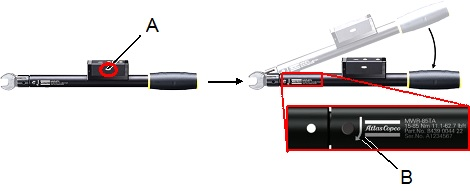
A | Blue LED | B | Tightening direction |
During the measurement (MWR-300 TA is loaded with torque), the yellow LED flashes.
At the end of each tightening, the LEDs are alight according to the test result:
Green LED: Tightening OK
Red LED: Tightening NOT OK
Service
Maintenance Instructions
Service Recommendations
Preventive maintenance is recommended at regular intervals. See the detailed information on preventive maintenance. If the product is not working properly, take it out of service and inspect it.
If no detailed information about preventive maintenance is included, follow these general guidelines:
Clean appropriate parts accurately
Replace any defective or worn parts
Cleaning
Keep the MWR-300 TA clean.
After use, remove any traces of oil and grease from the MWR-300 TA with a soft cloth and a soft surface cleaner for oil/grease. Do not use aggressive or abrasive cleaner.
Use an anti-static cleaning cloth in order to remove dust from the MWR-300 TA.
Avoid using harsh detergents to clean the MWR-300 TA.
Clean the contact of the MWR-300 TA by using an electrical contact cleaner solution.
Recycling
Environmental Regulations
When a product has served its purpose it has to be recycled properly. Dismantle the product and recycle the components in accordance with local legislation.
Batteries shall be taken care of by your national battery recovery organization.
Recycling information
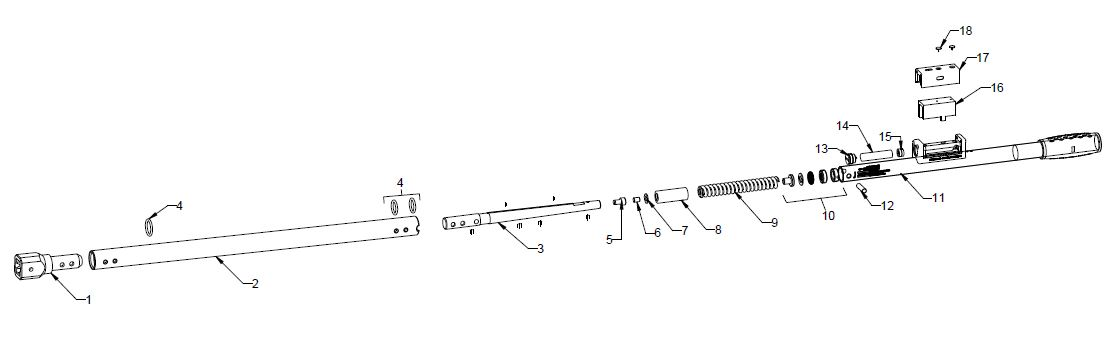
PART | RECYCLE AS | |
---|---|---|
1 | Square | Steel |
2 | Extension | Steel |
3 | Transducer | WEEE |
4 | O-ring | Plastic |
5 | Pin | Steel |
6 | Cylinder | Steel |
7 | Washer | Iron |
8 | Support | Mixed waste: not recyclable |
9 | Spring | Steel |
10 | Gear Washer & Nut | Steel |
11 | Tube | Mixed waste: not recyclable |
12 | Spine | Iron |
13 | Battery cup | Steel |
14 | Battery | Battery |
15 | Contact | Steel |
16 | Electronic board | WEEE |
17 | Electronic cover | Plastic |
18 | Contacts | Steel |
Screws | Steel |