EP6PTX18 SR42-AT
Nutrunner
Product Information
General Information
Safety Signal Words
The safety signal words Danger, Warning, Caution, and Notice have the following meanings:
DANGER | DANGER indicates a hazardous situation which, if not avoided, will result in death or serious injury. |
WARNING | WARNING indicates a hazardous situation which, if not avoided, could result in death or serious injury. |
CAUTION | CAUTION, used with the safety alert symbol, indicates a hazardous situation which, if not avoided, could result in minor or moderate injury. |
NOTICE | NOTICE is used to address practices not related to personal injury. |
Warranty
Product warranty will expire in 12+1 months after dispatch from Atlas Copco's Distribution Center.
Normal wear and tear on parts is not included within the warranty.
Normal wear and tear is that which requires a part change or other adjustment/overhaul during standard tool maintenance typical for that period (expressed in time, operation hours or otherwise).
The product warranty relies on the correct use, maintenance, and repair of the tool and its component parts.
Damage to parts that occurs as a result of inadequate maintenance or performed by parties other than Atlas Copco or their Certified Service Partners during the warranty period is not covered by the warranty.
To avoid damage or destruction of tool parts, service the tool according to the recommended maintenance schedules and follow the correct instructions.
Warranty repairs are performed only in Atlas Copco workshops or by Certified Service Partners.
Atlas Copco offers extended warranty and state-of-the-art preventive maintenance through its ToolCover contracts. For further information, contact your local Service representative.
For electrical motors:
Warranty will apply, only when the electric motor has not been opened.
Website
Information concerning our Products, Accessories, Spare Parts and Published Matters can be found on the Atlas Copco website.
Please visit: www.atlascopco.com.
ServAid
ServAid is a portal that is continuously updated and contains Technical Information, such as:
Regulatory and Safety Information
Technical Data
Installation, Operation and Service Instructions
Spare Parts Lists
Accessories
Dimensional Drawings
Please visit: https://servaid.atlascopco.com.
For further Technical Information, please contact your local Atlas Copco representative.
Safety Data Sheets MSDS/SDS
The Safety Data Sheets describe the chemical products sold by Atlas Copco.
Please consult the Atlas Copco website for more information www.atlascopco.com/sds.
Special Precaution
Check that the power socket is properly fastened.
Replace the square drive retainer or socket if worn.
Avoid unnecessary idling.
When using a suspension yoke, make sure that it is in good condition and correctly fastened.
PTFE
Country of Origin
For the Country of Origin, please refer to the information on the product label.
Dimensional Drawings
Dimensional Drawings can be found either in the Dimensional Drawings Archive, or on ServAid.
Please visit: https://webbox.atlascopco.com/webbox/dimdrw or https://servaid.atlascopco.com.
Overview
AutoTrim Valve Overview
This tool is equipped with an AutoTrim valve, which gives the tool optimal performance on mixed hard and soft joints. (For applications where the tool is used for tightening joints with similar characteristics, Trim Valve can be used.)
The AutoTrim valve is factory preset to suit a majority of applications. It gives a reduced speed during rundown. After 1-2 pulses it shifts automatically to full speed/power for the rest of the tightening. Regularly check the correct operation of the AutoTrim valve. Non-switching (from restricted to open operation) will cause longer tightening time with risk of over-tightening of the joint. Premature switching to open position (i.e. when tool is running free) might cause erratic shut-off due to too few pulses.
The AutoTrim valve gives a reduced speed during rundown. After 1-2 pulses on a joint it shifts automatically to full speed/power for the rest of the tightening, as shown in illustration below.
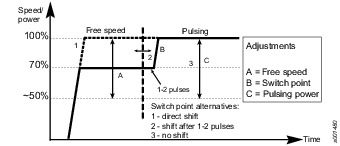
Possible adjustments:
Free speed (factory set to approx 70% of full speed). See Adjusting the Free Speed.
Switch point from reduced to full power (factory set to 1-2 pulses) for standard, non reporting (RE) applications. See Adjusting the Switch Point for the Auto Trim valve.
Power during pulsing (factory set to full power). See Adjusting the Pulsing Power.

In most cases the factory settings give the best performance.
Technical Product Data
Technical Product Data can be found on either ServAid, or the Atlas Copco website.
Please visit: https://servaid.atlascopco.com or www.atlascopco.com.
Installation
Installation Requirements
Air Quality
For optimum performance and maximum product life we recommend the use of compressed air with a maximum dew point of +10°C (50°F). We also recommend to install an Atlas Copco refrigeration type air dryer.
Use a separate air filter which removes solid particles larger than 30 microns and more than 90% of liquid water. Install the filter as close as possible to the product and prior to any other air preparation units to avoid pressure drop.

For impulse/impact tools make sure to use lubricators adjusted for these tools. Regular lubricators will add too much oil and therefore decrease the tool performance due to too much oil in the motor.

Make sure that the hose and couplings are clean and free from dust before connecting to the tool.

Both lubricated and lubrication free products will benefit from a small quantity of oil supplied from a lubricator.
Air Lubrication Guide
Recommended air lubricators:
Atlas Copco Optimizer (1 liter) 9090 0000 04
Q8 Chopin 46
Q8 Chopin 32
Shell Air Tool Oil S2 A 320
Mobil SHC Cibus 32
Compressed Air Connection
For correct air pressure and hose size, see the Technical Product Data on - https://servaid.atlascopco.com or www.atlascopco.com.

Make sure that the hose and couplings are clean and free from dust before connecting to the tool.
Air Pressure Regulation
Make sure to adjust the regulator to the lowest expected pressure on the line.
Adjusting the air pressure will have the following consequences:
Decreasing the air pressure will result in a slower but more accurate tool.
Increasing the air pressure will result in a faster but less accurate tool.

If the pressure from the airline is below five bar, a tool from the EP L-series (designed for low pressure installations) is recommended.
Installation Instructions
Recommended hose sizes
Make sure that all connections, adapters and couplings exceed the recommended minimum inner diameter, corresponding to the recommended hose size of the tool. Refer to the examples in the table. Recommended hose size for a specific tool is found in "Technical specifications" in https://servaid.atlascopco.com

Recommended hose size | Minimum inner diameter for |
---|---|
8 mm | 7 mm |
10 mm | 7 mm |
13 mm | 9.4 mm |
Installation of Flexible Hose
To prevent tool vibrations use a flexible hose for compressed air with a minimum length of 300 mm (12") between the tool and the quick coupling.
Operation
Ergonomic Guidelines
Consider your workstation as you read through this list of general ergonomic guidelines and see if you can identify areas for improvement in posture, component placement, or work environment.
Take frequent breaks and change work positions frequently.
Adapt the work area to your needs and the work task.
Adjust for convenient reach range by determining where parts or tools should be located to avoid static load.
Use workstation equipment such as tables and chairs appropriate for the work task.
Avoid work positions above shoulder level or with static holding during assembly operations.
When working above shoulder level, reduce the load on the static muscles by reducing the weight of the load. You can also reduce the load on the static muscles by holding the load close to the body.
Make sure to take frequent breaks.
Avoid extreme arm or wrist postures, particularly for operations requiring a degree of force.
Adjust for convenient field of vision by minimizing movement of the eyes and head during the work task.
Use the appropriate lighting for the work task.
Use ear protection equipment in noisy environments.
Use dust extraction system or mouth protection mask in dusty environments.
Operating Instructions
Length of "L" and "N" for different tool sizes
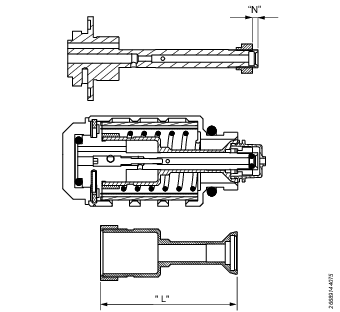
Auto trim valve | Length of “L” (mm) | Length of “N” (mm) |
---|---|---|
4250 1878 43 | 39.2 +/-0.1 | 1.5 |
4250 1878 90 | 39.2 +/-0.1 | 1.5 |
4250 1878 91 | 39.7 +/-0.1 | 1.0 |
4250 1878 92 | 40.2 +/-0.1 | 0.5 |
4250 1878 93 | 40.7 +/-0.1 | 0 |
4250 1878 94 | 40.3 +/-0.1 | 0 |
4250 1878 95 | 40.5 +/-0.1 | 0 |
4250 1878 97 | 39.2 +/-0.1 | 1.5 |
4250 1878 98 | 39.7 +/-0.1 | 1.0 |
4250 2675 91 | 40.5 +/-0.1 | 0 |
4250 2675 92 | 40.3 +/-0.1 | 0 |
4250 1878 50 | 38.7 +/-0.1 | 2.0 |
4250 1878 51 | 38.7 +/-0.1 | 2.0 |
Optimizing the Tool Performance

It is not recommended to use extensions with pulse tools. Extensions cause vibrations, which in turn may cause wear on the tool, longer tightening time, limited accuracy and difficulty reaching maximum torque. If an extension is necessary due to accessibility constraints, it should be as short as possible. Guided sockets or extensions are strongly recommended.
Recommended number of pulses
The pulse tool shall reach the target torque, with shut off, within 5-20 pulses. Measure the number of pulses to reach the target torque with an analyzer. The tightening time can also be used as a guide, to know if the tool is set correctly:
≤ 1 second for tools up to 30 Nm
≈ 1 second for tools up to 80 Nm
≈ 2 seconds for tools up to 150 Nm
≈ 5 seconds for tools up to 450 Nm
≤ 10 seconds for tools up to 850 Nm
If the target torque is reached within less than 5 pulses (= short tightening time), the torque scatter will increase and it can be difficult to adjust to the right level, especially on hard joints.
If the target torque is reached after more than 20 pulses (= too long tightening time) the wear will increase and more frequent oil filling and service will be required. Too long tightening time, in combination with high production rate, may also result in excessive heating of the oil. In that case the power will decrease with longer tightening time and sometimes no shut off.
If the target torque is reached within less than 5 pulses, adjust it by:
Decreasing the air pressure.
Reducing the speed with the AutoTrim or Trim valve.
If the above is not possible or does not give the wanted results, a smaller tool may be a better choice.
If the target torque is reached with more than 20 pulses, adjust it by:
Increasing the dynamic air pressure to 6-7 bar for standard EP tools, or up to 5 bar for low pressure EP L-tools.
Adjusting the AutoTrim or Trim valve to give maximum power/speed.
If the above is not possible or does not give the wanted results, a bigger tool may be a better choice.

When changing the air pressure, measure the target torque again and adjust it if needed.
Adjusting the Pulsing Power of the Auto Trim valve
The Auto Trim valve is factory set to full pulsing power, that is, the length of N is set according to the table, refer to Length of "L" and "N" for different tool sizes
To improve accuracy (more pulses before shut off) on hard or medium hard joints, reduce the power. The power is reduced by turning the nut (1) clockwise (increased length of N).
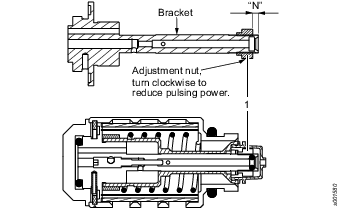
Checking the Auto Trim valve speed

Make sure that any socket is firmly attached. The tool should run at reduced speed.
Set the reversing knob in the reverse direction.
Push the trigger and keep it pressed as you run the tool in the air (A).
Quickly push the reversing knob to the forward direction (B).
The Auto Trim valve shall switch from reduced to full speed.If the tool is runs with full speed at step 1 (A) or runs at reduced speed at step 3 (B), adjust or service the AutoTrim valve, refer to Adjusting the Switch Point for the Auto Trim valve


Adjusting the reduced speed of the Auto Trim valve
The Auto Trim valve is factory set to approximately 70% of full speed. To decrease the speed, decrease the length of L. To increase the speed, increase the length of L.
Turn the support ring (1)to adjust the length of L.
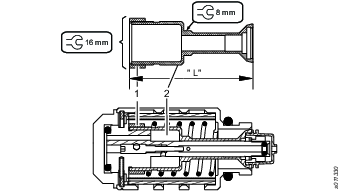

On very hard joints (<30°) at low torque levels, further speed reduction might be necessary. When the tool is used only on soft joints, less or no speed reduction is needed.
The factory set length of L is depending on the tool size, refer to Length of "L" and "N" for different tool sizes
Setting of the tightening torque with the AutoTrim Valve (AT)
The factory setting of the AutoTrim valve usually gives the correct performance. To set the tightening torque for the actual joint with the auto trim valve do the following:
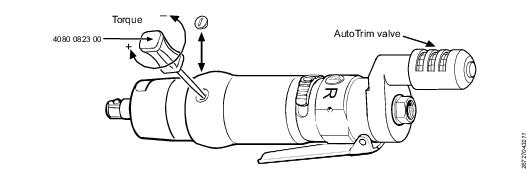
Remove the slotted cover plug at the front of the tool.
Turn the pulse unit until you see the adjusting screw in the hole.
Use a flat screwdriver and turn the set screw to set the tightening torque.
Do a control of the tightening torque on your actual joint.
If the tightening torque is Not OK, adjust the speed on the auto trim valve, refer to Adjusting the reduced speed of the Auto Trim valve.
If the tightening torque is OK, do a control of the tightening time, measure the number of pulses, to reach the target torque.
If the tightening time is Not OK, refer to Optimizing the Tool Performance
If the tightening torque and time is OK, the tool is ready for operation.
Adjusting the Switch Point for the Auto Trim valve
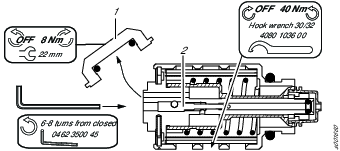
Hold the valve casing with a hook wrench and remove the cover (1) with a 22 mm wrench.
Adjust the valve (2) with a 1.5 mm Allen key. From closed (+) position to normal operation the needle valve is opened between 6 to 8 turns (-) depending on tool size.
Put the cover (1) back in position and fasten it.
Do a control of the Auto Trim valve speed.
If the valve is too much closed, the Auto Trim valve will not shift to open position when pulsing starts. If the valve is too much open, the Auto Trim will directly open to full speed and power.
Clockwise (+) rotation delays the switch point (closes the needle valve) and vice versa.

If the tool is used for reporting applications (RE) the needle valve has to be turned more open (-) to compensate for the air volume in the signal hose.
Checking the AT Valve function with Sight Glass
For a better understanding of the AutoTrim valve behaviour, a sight glass is recommended. Find a sight glass suitable for the tool on ServAid.
Assemble the sight glass with the tube adapter between the AutoTrim valve and the tool.
Make sure that the valve stays closed when running the tool in the air.
Run the tool on a joint and make sure that the valve goes from closed to open position when the pulsing starts.
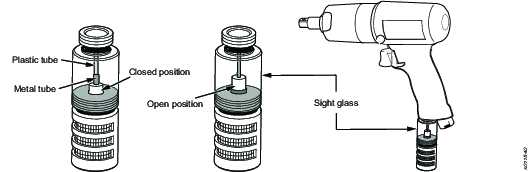
If the behavior in step 2 or 3 is not correct, the valve need to be adjusted or serviced, see Adjusting the Switch Point for the Auto Trim valve.
Operating Instructions
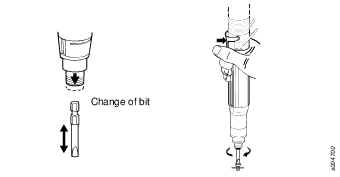
Setting of the Tightening Torque

To use the tool at a higher torque than recommended maximum torque may result in incorrect function and faster wear.

Always do a control of the tightening torque on the actual joint.
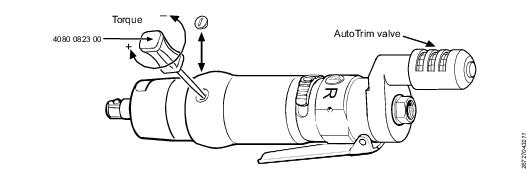
Remove the slotted cover plug at the front of the tool.
Turn the pulse unit until you see the adjusting screw in the hole.
Start at a low torque and increase it until you reach the wanted torque level.
Service
Maintenance Instructions
Servicing the AutoTrim Valve
Make sure all parts are clean. O-rings should be lightly greased. Valve and bracket should be sparsely oiled with light oil. Make sure that the valve moves easily on the bracket. When adjusting the throttle valve, start from fully closed position (clockwise) and open between 6-8 turns. Check and adjust again if needed.
Check and adjust the lengths of L and N corresponding to the ordering number of the AutoTrim valve (as of 2008 the ordering number is engraved on the AutoTrim casing). See Adjusting the reduced speed of the Auto Trim valveand Adjusting the Pulsing Power of the Auto Trim valve.
Test the valve function on the corresponding EP tool. Change the filter regularly to prevent clogging, decreased power, and incorrect function.
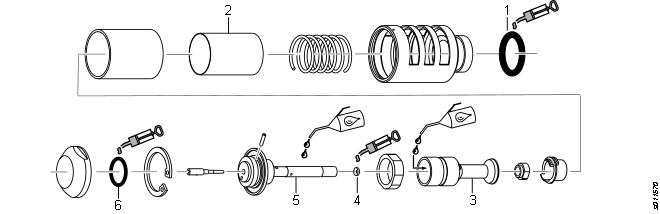
Ref.No | Description | Remark |
---|---|---|
1 | O-ring | Lightly greased |
2 | Filter | Change regularly |
3 | Valve | Lightly oiled. Valve should slide easily onto bracket. |
4 | O-ring | Lightly greased |
5 | Bracket | Lightly oiled. Valve should slide easily onto bracket. |
6 | O-ring | Lightly greased |
Service tools
Atlas Copco Service tools are designed to make assembly and disassembly fast and easy with less risk of damaging parts in the process.
When assembling the tool after service it is important to tighten the parts correctly to:
Optimize performance of the tool.
Minimize the risk of parts coming loose during operation.
You can find information about service tools and tightening data in the Spare part list on ServAid.
Preventive Maintenance
Preventive maintenance is recommended once per year or after a maximum of 250.000 tightenings. A complete overhaul includes:
Clean the following parts: pulse unit, air motor, silencer and strainer of the inlet adapter, trigger and reversing valve.
Replace worn or damaged parts and filter.

Only replace the o-rings in the pulse unit at the complete overhaul.
Lubrication Instructions
Rust Protection and Cleaning
Water in the compressed air can cause rust. To prevent rust we strongly recommend to install an air dryer.
Water and particles can cause sticking of vanes and valves. This can be prevented by installing an air filter close to the product to avoid pressure drop.
Before longer stand stills always protect your tool by adding a few drops of air motor oil into the air inlet. Run the tool for 5–10 seconds and absorb any excess oil at the air outlet in a cloth.
Grease Guide ErgoPulse
Brand | General purpose Bearings | Motor shaft | Air Lubrication |
---|---|---|---|
BP | Energrease LS-EP2 |
| Energol E46 |
Castrol | Spheerol EP L2 |
|
|
Esso | Beacon EP2 |
| Arox EP46 |
Q8 | Rembrandt EP2 |
| Chopin 46 |
Mobil | Mobilegrease XHP 222 |
| Almo oil 525 |
Shell | Alvania EP2 |
| Tonna R32 |
Texaco | Multifak EP2 |
| Aries 32 |
Molycote |
| BR2 Plus |
|
Lubrication Guide
Brand | General purpose, Bearings and Gears |
---|---|
BP | Energrease LS-EP2 |
Castrol | Optileb GR UF 1 |
Esso | Beacon EP2 |
Q8 | Rembrandt EP2 |
Mobil | Mobilegrease XHP 222 NLGI2 |
Klüber Lub. | Klübersynth UH 1 14-151 |
Texaco | Multifak EP2 |
Molykote | BR2 Plus |
Shell | Gadus S2 |
Brand | Pulse unit hexagon |
---|---|
Klüber Lub. | Microlube GL 261 |
Filling the Pulse Unit with Oil
There are different methods to fill the pulse unit with oil, depending on available equipment:
Using an ST Analyzer and a Transducer. Follow the instructions in Method 1.
This method is the fastest. It will give an optimized tool performance and result in the longest filling intervals.Without an ST Analyzer and a Transducer. Follow the instructions in Method 2.
This method is not as fast and accurate as using Method 1.
Method 1 (using an ST Analyzer and a Transducer)
Position the pulse unit in a vice. Remove the oil plug positioned on either the front (A) or the back (B) of the pulse unit. Add a small amount of oil to the pulse unit.
Assemble the tool and measure the pulse frequency.
If the pulse unit frequency is in the specified range the amount of oil is correct.
If the pulse unit frequency is too low reduce some oil and measure the pulse frequency again.
If the pulse frequency is to high add some oil and measure the pulse frequency again.
Model
Minimum free speed (r.p.m)
Pulse frequency (Hz)
Max Torque (minimum) (Nm)
EP 6 PTX SR42
6800
23-26
24
Method 2 (without ST Analyzer and Transducer)
Position the pulse unit in a vice. Remove the oil plug positioned on either the front (A) or the back (B) of the pulse unit. Fill the pulse unit to 100% full. Assemble the oil plug.
Assemble the tool and run in reverse for 3-5 seconds.
Position the pulse unit in a vice. Remove the oil plug. Wait for all air bubbles to disappear (approximately 15 minutes) and the temperature to drop down to 20 degrees.
Fill the pulse unit to 100% full.
Reduce the oil in the pulse unit with a specified volume according to table using a 1 ml syringe. Assemble the oil plug.
Oil volume to be
reduced from 100%
Approx. oil volume
in pulse-unit
0.40 ± 0.05 ml
5 ml
Check torque and shut off function, for procedure see Testing/Measuring.
If everything is in order the amount of oil is right.
If everything is not in order repeat from step one.
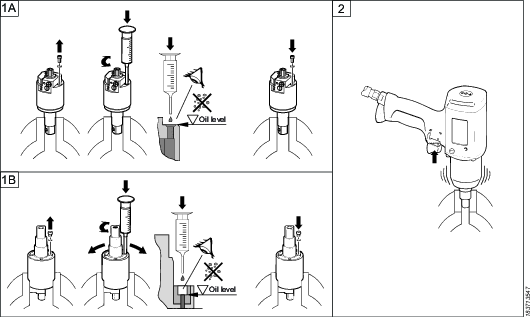

Inspection and Lubrication of the Pulse Unit
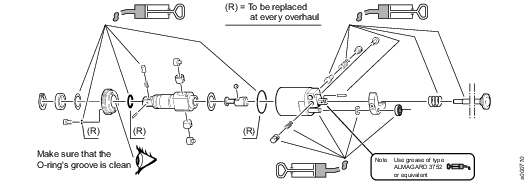
Recommended Oil for the Pulse Unit
The recommended oil for the pulse unit is Atlas Copco Pulse Unit Oil.
A bottle of Atlas Copco Pulse Unit Oil and the required syringe or syringes are orderable as kits. Please see Service Kits for ordering numbers.
Refill the Pulse-Unit with Oil
For optimum machine performance the pulse unit must be correctly filled with oil. Due to a possible microleakage of oil from the pulse unit, it could be necessary to refill the unit between the regular overhaul intervals. The frequency of this procedure depends on the type of application, number of cycles, tightening time etc. An accurate refill of the pulse unit gives long service intervals.
Too much oil in the pulse unit implies a low pulse frequency and slow tightening.
Too little oil in the pulse unit implies a high pulse frequency and there will be a risk of a decreasing tightening torque. In particular at the first tightening after a break the machine might race.
Use Atlas Copco Pulse Unit Oil Bio.
Running the machine with too little oil may damage the pulse unit.
After the refill – Check the tightening torque.
Steps
Fill the pulse unit with oil according to steps No. 1-3 seen in the picture, after the disassembly of the pulse unit. Run the machine in a vice for 10 seconds according to step No. 4. Complete the rest of the steps. For best performance use Atlas Copco Pulse Unit Oil Bio.
A bottle of Atlas Copco Pulse Unit Oil Bio and the required syringe or syringes are orderable as a kit. See Service Kits for ordering numbers.
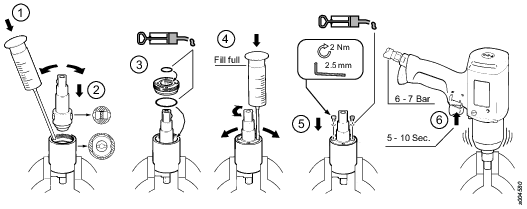
Low oil level
How to detect a low oil level in the pulse unit:
Longer tightening time
Very high pulse frequency, especially when the tool has not been used for a while.
Low torque or abnormal torque changes (increased scatter).
No shut off
To measure the pulse frequency use a static torque transducer or an inline transducer connected to torque testing equipment, se Testing/Measuring section.
Dismantling/Assembling Instructions
Tightening of Threaded Connections
The tightening torque indicated in the exploded views (see Spare parts section in https://servaid.atlascopco.com) will give the right clamping force and prevent parts from loosening. It is important not to exceed the clamping force, these parts must be able to open up without being damaged at service. After some time of operation and in special circumstances, depending on application and usage, the parts may however loosen somewhat. The tightening torque can then be increased by 10-20% and some type of low or medium thread locking fluid can be applied.
Static measuring with fixed transducers
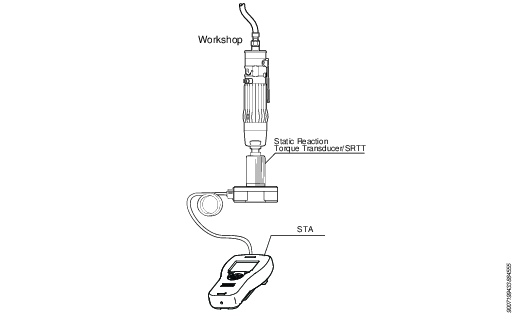
Test equipment and performance
Equipment:
Tachometer.
STanalyser.
SRTT transducer (secure the transducer firmly).
Test the free speed in the forward direction with the tachometer.
For AutoTrim versions make sure that the unreduced speed is measured (refer to section Function control - AutoTrim in the Trouble shooting schedule chapter of the service instruction for details).
Test the AutoTrim function.
Test the max torque and pulse frequency.
Set the filter frequency in STanalyser to 850 Hz.
Measure the torque and pulse frequency in the reverse direction. Use a tightening time of approximately 1 second.
Check of shut-off mechanism.
Run the tool in the forward direction. If the shut-off mechanism is working properly the tool shuts off.
Test conditions
Temperature pulse unit: approx. 20° C.
Air pressure: 6,3 bar (90psi) dynamic
Hose size: 8 mm Hose length: 3 m
The tool should achieve the following values after maintenance:
Model | Free speed (r.p.m) | Pulse frequency (Hz) | Max Torque (minimum)(Nm) |
---|---|---|---|
EP 6 PTX SR42 | 6800 | 23-26 | 24 |
Correct pulse frequency indicates that the air motor and the pulse unit are in good condition. If the pulse pulse frequency is to high - fill oil. If the pulse frequency is too low - reduce oil.
Static measurement (Recommended)
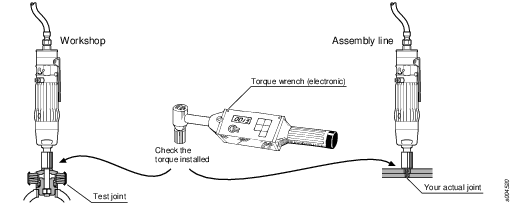
Test Method - Static or Dynamic
A static torque measurement is recommended for the ErgoPulse machines.
If dynamic torque measurement with an electronic inline torque transducer is used, always verify your measurement result by a static check with a torque wrench (electronic).
For more information, refer to Atlas Copco "Pocket Guide to Pulse Tools". Ordering No. 9833 1225 01.
Dynamic measurement
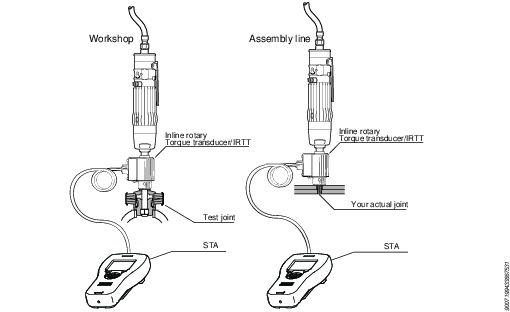

Always verify the setting on your actual joint.
Always verify the dynamic measurement on your actual joint by a static check with a torque wrench (electronic).
Recycling
Environmental Regulations
When a product has served its purpose it has to be recycled properly. Dismantle the product and recycle the components in accordance with local legislation.
Batteries shall be taken care of by your national battery recovery organization.
Recycling Instructions

Pos | Part | Recycle as |
---|---|---|
1 | Pulse unit casing | Metal, Aluminium |
2 | Ball bearing | Metal, Steel |
3 | Pulse unit | Metal, Steel |
4 | Screw ring | Metal, Steel |
5 | Sleeve | Metal, Steel |
6 | Ball bearing | Metal, Steel |
7 | End plate | Cast Iron |
8 | Cylinder | Cast Iron |
9 | Rotor | Metal, Steel |
10 | Vanes | POM |
11 | Plugs | POM |
12 | End plate | Cast Iron |
13 | Ball bearing | Metal, Steel |
14 | Reverse valve | Plastics, other, PES |
15 | Spring | Metal, Steel |
16 | Shut-off valve | Metal, Steel, Plastics |
17 | Plug | Metal, Steel |
18 | Revering knob | Plastics, other, PA66 |
19 | Tapping screw | Metal, Steel |
20 | Valve | Metal, Steel |
21 | Motor housing | Metal, Aluminium |
22 | Spiral pin | Metal, Steel |
23 | Lever | Metal, Steel |
24 | Signal tube | Metal, Steel |
25 | Exhaust casing | Metal, Aluminium |
26 | Silencer | Metal, Steel |
27 | Adapter | Metal, Steel |
28 | Restriction washer | Metal, Steel |