Product Information
General Information
Safety Signal Words
The safety signal words Danger, Warning, Caution, and Notice have the following meanings:
DANGER | DANGER indicates a hazardous situation which, if not avoided, will result in death or serious injury. |
WARNING | WARNING indicates a hazardous situation which, if not avoided, could result in death or serious injury. |
CAUTION | CAUTION, used with the safety alert symbol, indicates a hazardous situation which, if not avoided, could result in minor or moderate injury. |
NOTICE | NOTICE is used to address practices not related to personal injury. |
Warranty
Product warranty will expire 12 months after the product is first taken into use, but will in any case expire at the latest 13 months after delivery.
Normal wear and tear on parts is not included within the warranty.
Normal wear and tear is that which requires a part change or other adjustment/overhaul during standard tools maintenance typical for that period (expressed in time, operation hours or otherwise).
The product warranty relies on the correct use, maintenance, and repair of the tool and its component parts.
Damage to parts that occurs as a result of inadequate maintenance or performed by parties other than Atlas Copco or their Certified Service Partners during the warranty period is not covered by the warranty.
To avoid damage or destruction of tool parts, service the tool according to the recommended maintenance schedules and follow the correct instructions.
Warranty repairs are only performed in Atlas Copco workshops or by Certified Service Partners.
Atlas Copco offers extended warranty and state of the art preventive maintenance through its ToolCover contracts. For further information contact your local Service representative.
For electrical motors:
Warranty will only apply when the electric motor has not been opened.
ServAid
ServAid is a portal that is continuously updated and contains Technical Information, such as:
Regulatory and Safety Information
Technical Data
Installation, Operation and Service Instructions
Spare Parts Lists
Accessories
Dimensional Drawings
Please visit: https://servaid.atlascopco.com.
For further Technical Information, please contact your local Atlas Copco representative.
Safety Data Sheets MSDS/SDS
The Safety Data Sheets describe the chemical products sold by Atlas Copco.
Please consult the Atlas Copco website for more information www.atlascopco.com/sds.
Country of Origin
For the Country of Origin, please refer to the information on the product label.
Dimensional Drawings
Dimensional Drawings can be found either in the Dimensional Drawings Archive, or on ServAid.
Please visit: http://webbox.atlascopco.com/webbox/dimdrw or https://servaid.atlascopco.com.
Overview
Applications
The MicroTorque screw fastening systems are ultra low-torque applications.
Normal Environmental Conditions
This product is designed to be safe under the following conditions:
Indoor use
Altitude up to 2 000 m
Operating temperature +5 °C / +41 °F to +40 °C / +104 °F
Storage temperature -25 °C / -13 °F to +60 °C / +140 °F
Maximum relative humidity 80 % for temperatures up to 31 °C / 89 °F decreasing linearly to 50 % relative humidity at 40 °C / 104 °F
Mains supply voltage fluctuations up to ±10 % of the nominal voltage
Transient overvoltages up to the levels of overvoltage category II
Temporary overvoltages occurring on the mains supply
Pollution degree 2
Ingress protection rating: IP20
Technical Product Data
Technical Product Data can be found on either ServAid, or the Atlas Copco website.
Please visit: https://servaid.atlascopco.com or www.atlascopco.com.
Accessories
Optional accessories
Tool cable 2.0 m | 8432 0835 02 |
Tool cable 3.5 m | 8432 0835 03 |
Bit grounding test
Bit grounding is measured by the ground circuit stability and resistance with the tool running at no load with a rotation speed of 200 rpm. Resistance is measured between the special bit 4216 2194 00 and the outside of the tool connector and the resistance limit is 20 Ω.
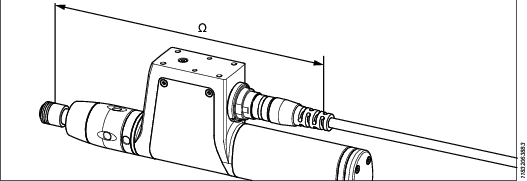
Bit run out test
Bit run out is measured with the tool securely fastened in a test rig and with the tool running at no load with a rotation speed of 200 rpm. Measuring point is at 44 mm (length of a standard bit) out on a special bit 4216 2194 00. Bit run out limit is 0.15 mm.
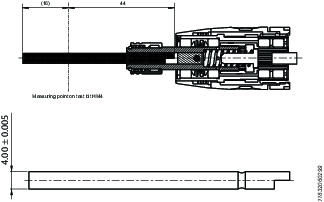
Service Overview
Service Recommendations
Preventive maintenance is recommended at regular intervals. See the detailed information on preventive maintenance. If the product is not working properly, take it out of service and inspect it.
If no detailed information about preventive maintenance is included, follow these general guidelines:
Clean appropriate parts accurately
Replace any defective or worn parts
Preventive maintenance
Recommended interval between actions:
Valid at normal usage of the tool at a load up to 70% of maximum torque.

Service should only be carried out by trained technician following provided service instructions and using original Atlas Copco spare parts.
Interval | Action |
---|---|
1.500.000 cycles or 1 year | Calibrate the tool |
1.500.000 cycles | Exchange bit grounding |
3.000.000 cycles | Exchange front part |
3.000.000 cycles | Exchange motor |
Installation
Installation Instructions
Installing the tool
For details, please refer to the dimensional drawings.
Mechanical installation
Attach the tool to the fixture in one of the following ways:
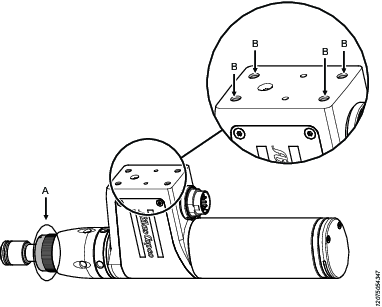
A: Using the threads at the front part, accessible under the thread protection ring.
B: Using the holes of the tool base.

Four holes are intended for screws and two holes are intended for guide pins.
Electrical installation
Connect the tool to the drive using the supplied cable.
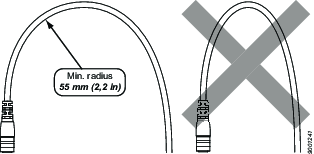
Operation
Ergonomic Guidelines
Consider your workstation as you read through this list of general ergonomic guidelines to identify areas for improvement in posture, component placement, or work environment.
Take frequent breaks and change work positions frequently.
Adapt the workstation area to your needs and the work task.
Adjust for a convenient reach range by determining where parts and tools need to be located to avoid static load.
Use workstation equipment such as tables and chairs appropriate for the work task.
Avoid work positions above shoulder level or with static holding during assembly operations.
When working above shoulder level, reduce the load on the static muscles by lowering the weight of the tool, using for example torque arms, hose reels or weight balancers. You can also reduce the load on the static muscles by holding the tool close to the body.
Take frequent breaks.
Avoid extreme arm or wrist postures, particularly during operations requiring a degree of force.
Adjust for a convenient field of vision that requires minimal eye and head movements.
Use appropriate lighting for the work task.
Select the appropriate tool for the work task.
In noisy environments, use ear protection equipment.
Use high-quality inserted tools and consumables to minimize exposure to excessive levels of vibration.
Minimize exposure to reaction forces.
When cutting:
A cut-off wheel can get stuck if the cut-off wheel is bent or not guided properly. Use the correct flange for the cut-off wheel and avoid bending the cut-off wheel during operation.
When drilling:
The drill might stall when the drill bit breaks through. Use support handles if the stall torque is high. The safety standard ISO11148 part 3 recommends using a device to absorb a reaction torque above 10 Nm for pistol grip tools and 4 Nm for straight tools.
When using direct-driven screwdrivers or nutrunners:
Reaction forces depend on the tool settings and joint characteristics. Strength and posture determine the amount of reaction force that an operator can tolerate. Adapt the torque setting to the operator's strength and posture and use a torque arm or reaction bar if the torque is too high.
In dusty environments, use a dust extraction system or wear a mouth protection mask.
Operating Instructions
Mount bit
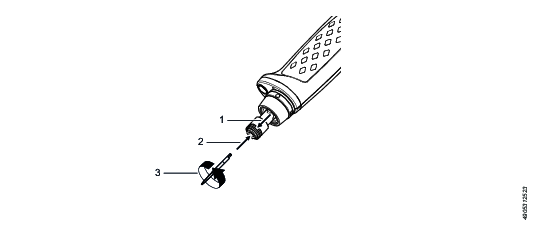
Pull the chuck ring outwards
Insert the bit
Turn the bit, if not seated properly
Service
Preventing ESD Problems
The components inside the product and controller are sensitive to electrostatic discharge. To avoid future malfunction, make sure that service and maintenance is carried out in an ESD approved work environment. The figure below shows an example of an appropriate service work station.
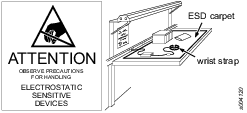
Maintenance Instructions
Service Recommendations
Preventive maintenance is recommended at regular intervals. See the detailed information on preventive maintenance. If the product is not working properly, take it out of service and inspect it.
If no detailed information about preventive maintenance is included, follow these general guidelines:
Clean appropriate parts accurately
Replace any defective or worn parts
Preventive maintenance
Recommended interval between actions:
Valid at normal usage of the tool at a load up to 70% of maximum torque.

Service should only be carried out by trained technician following provided service instructions and using original Atlas Copco spare parts.
Interval | Action |
---|---|
1.500.000 cycles or 1 year | Calibrate the tool |
1.500.000 cycles | Exchange bit grounding |
3.000.000 cycles | Exchange motor |
Instructions
Service equipment:
Normal workshop equipment.
Necessary special equipment as shown in the exploded views/tables.
For testing a calibration rig is recommended.
PC with internet connection to be able to download necessary keys.
Recycling
Environmental Regulations
When a product has served its purpose it has to be recycled properly. Dismantle the product and recycle the components in accordance with local legislation.
Batteries shall be taken care of by your national battery recovery organization.
Recycling information
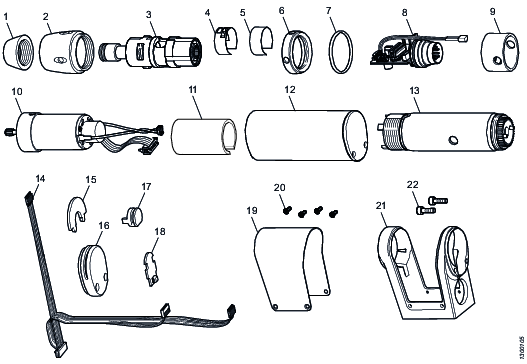
1 |
Front protection |
Recycle as PA6 GF30 |
2 |
Cap nut |
Recycle as steel |
3 |
Front part |
Recycle as steel |
4 |
Grounding ring |
Recycle as CuSn6 |
5 |
Spring ring |
Recycle as steel |
6 |
Cap nut |
Recycle as steel |
7 |
Cover ring |
Recycle as TPU GF30 |
8 |
Main board |
Recycle as WEEE |
9 |
Cap nut |
Recycle as steel |
10 |
Motor |
Recycle as WEEE |
11 |
Heatsink |
Recycle as aluminum |
12 |
Motor cover |
Recycle as aluminum |
13 |
Drive unit without motor |
Recycle as steel |
14 |
Light electronics |
Recycle as WEEE |
15 |
Lens |
Recycle as PC |
16 |
Light module housing |
Recycle as aluminum |
17 |
Reflector |
Recycle as POM |
18 |
Part of light electronics |
Recycle as WEEE |
19 |
Cover plate |
Recycle as stainless steel |
20 |
Screws |
Recycle as stainless steel |
21 |
Housing frame |
Recycle as aluminum |
22 |
Screws |
Recycle as steel |