Product Information
General Information
Safety Signal Words
The safety signal words Danger, Warning, Caution, and Notice have the following meanings:
DANGER | DANGER indicates a hazardous situation which, if not avoided, will result in death or serious injury. |
WARNING | WARNING indicates a hazardous situation which, if not avoided, could result in death or serious injury. |
CAUTION | CAUTION, used with the safety alert symbol, indicates a hazardous situation which, if not avoided, could result in minor or moderate injury. |
NOTICE | NOTICE is used to address practices not related to personal injury. |
Warranty
Product warranty will expire 12+1 months after dispatch from Atlas Copco's Distribution Center.
Normal wear and tear on parts is not included within the warranty.
Normal wear and tear is that which requires a part change or other adjustment/overhaul during standard tools maintenance typical for that period (expressed in time, operation hours or otherwise).
The product warranty relies on the correct use, maintenance, and repair of the tool and its component parts.
Damage to parts that occurs as a result of inadequate maintenance or performed by parties other than Atlas Copco or their Certified Service Partners during the warranty period is not covered by the warranty.
To avoid damage or destruction of tool parts, service the tool according to the recommended maintenance schedules and follow the correct instructions.
Warranty repairs are only performed in Atlas Copco workshops or by Certified Service Partners.
Atlas Copco offers extended warranty and state of the art preventive maintenance through its ToolCover contracts. For further information contact your local Service representative.
For electrical motors:
Warranty will only apply when the electric motor has not been opened.
Website
Information concerning our Products, Accessories, Spare Parts and Published Matters can be found on the Atlas Copco website.
Please visit: www.atlascopco.com.
ServAid
ServAid is a portal that is continuously updated and contains Technical Information, such as:
Regulatory and Safety Information
Technical Data
Installation, Operation and Service Instructions
Spare Parts Lists
Accessories
Dimensional Drawings
Please visit: https://servaid.atlascopco.com.
For further Technical Information, please contact your local Atlas Copco representative.
Safety Data Sheets MSDS/SDS
The Safety Data Sheets describe the chemical products sold by Atlas Copco.
Please consult the Atlas Copco website for more information www.atlascopco.com/sds.
Product Safety Video for Nutrunners
Learn more about safety features on Atlas Copco nutrunners and what measures the operator has to take for a safe operation. Click the link or scan the QR code below to view the video:
https://www.youtube.com/watch?v=FAh6yttvUpw
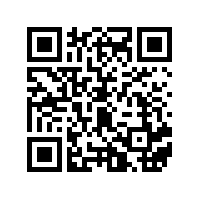
Country of Origin
For the Country of Origin, please refer to the information on the product label.
Dimensional Drawings
Dimensional Drawings can be found either in the Dimensional Drawings Archive, or on ServAid.
Please visit: http://webbox.atlascopco.com/webbox/dimdrw or https://servaid.atlascopco.com.
Overview
Technical Product Data
Technical Product Data can be found on either ServAid, or the Atlas Copco website.
Please visit: https://servaid.atlascopco.com or www.atlascopco.com.
Service Overview
Service Recommendations
Preventive maintenance is recommended at regular intervals. See the detailed information on preventive maintenance. If the product is not working properly, take it out of service and inspect it.
If no detailed information about preventive maintenance is included, follow these general guidelines:
Clean appropriate parts accurately
Replace any defective or worn parts
Installation
Installation Requirements
Installation
For installation guideline, see Power Focus 6000 user guide.
Installation Instructions
Attaching and Removing the Battery
Attach the battery to the tool and make sure that it is fastened correctly. The battery can be attached pointing forward or backward, to get the best accessibility and balance.
To remove the battery, press the button on the battery and push it out.
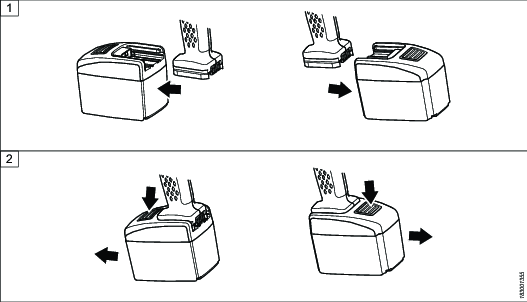
Operation
Ergonomic Guidelines
Consider your workstation as you read through this list of general ergonomic guidelines to identify areas for improvement in posture, component placement, or work environment.
Take frequent breaks and change work positions frequently.
Adapt the workstation area to your needs and the work task.
Adjust for a convenient reach range by determining where parts and tools need to be located to avoid static load.
Use workstation equipment such as tables and chairs appropriate for the work task.
Avoid work positions above shoulder level or with static holding during assembly operations.
When working above shoulder level, reduce the load on the static muscles by lowering the weight of the tool, using for example torque arms, hose reels or weight balancers. You can also reduce the load on the static muscles by holding the tool close to the body.
Take frequent breaks.
Avoid extreme arm or wrist postures, particularly during operations requiring a degree of force.
Adjust for a convenient field of vision that requires minimal eye and head movements.
Use appropriate lighting for the work task.
Select the appropriate tool for the work task.
In noisy environments, use ear protection equipment.
Use high-quality inserted tools and consumables to minimize exposure to excessive levels of vibration.
Minimize exposure to reaction forces.
When cutting:
A cut-off wheel can get stuck if the cut-off wheel is bent or not guided properly. Use the correct flange for the cut-off wheel and avoid bending the cut-off wheel during operation.
When drilling:
The drill might stall when the drill bit breaks through. Use support handles if the stall torque is high. The safety standard ISO11148 part 3 recommends using a device to absorb a reaction torque above 10 Nm for pistol grip tools and 4 Nm for straight tools.
When using direct-driven screwdrivers or nutrunners:
Reaction forces depend on the tool settings and joint characteristics. Strength and posture determine the amount of reaction force that an operator can tolerate. Adapt the torque setting to the operator's strength and posture and use a torque arm or reaction bar if the torque is too high.
In dusty environments, use a dust extraction system or wear a mouth protection mask.
Operating Instructions
LED Indicator (HMI)
LED Indicator | Description |
---|---|
Connection | Indicates the connection to the paired controller or software system. |
Batch | Indicates when Batch done. |
Battery | Indicates battery status (flashing light = low battery, constant light = empty battery). |
Alarm | A failure or event is detected. |
Tightening
As tightening torque increase the reaction force build up equally. Make sure that the tool is in correct working order and that the controller is correctly programmed. By doing this you avoid unexpected behavior from the tool, which may result in operator injury.
Rotation Direction for the Tightening
Check that the tool is in the correct running direction by turning the reverse button or reverse ring :
Pistol Grip Models (with side buttons)
Press in the reverse switch on the right hand side of the tool, to set the direction clockwise (CW).
Press in the reverse switch on the left hand side of the tool, to set the direction counter clockwise (CCW).
Pistol Grip Models (without side buttons)
Double press the function button on the top of the start trigger to shift the direction between clockwise (CW) and counter clockwise (CCW).
Angle Models
Turn the reverse ring to the right, to set the direction clockwise (CW).
Turn the reverse ring to the left, to set the direction counter clockwise (CCW).
Soft Start
The soft start function facilitates the screwhead and thread to reach the snug level. The duration of the soft start is adjustable.
For further information about tightening, see Power Focus 6000 Configuration manual.
Scanner
Specification
Scanner |
|
---|---|
Classification | Class 2 laser |
Wave lengh | 630 - 665 nm |
Maximum power output | 1.7 mW |
Beam divergence | 47º horizontally, 30º vertically |
Service
Preventing ESD Problems
The components inside the product and controller are sensitive to electrostatic discharge. To avoid future malfunction, make sure that service and maintenance is carried out in an ESD approved work environment. The figure below shows an example of an appropriate service work station.
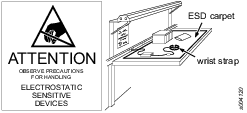
Maintenance Instructions
Service Recommendations
Preventive maintenance is recommended at regular intervals. See the detailed information on preventive maintenance. If the product is not working properly, take it out of service and inspect it.
If no detailed information about preventive maintenance is included, follow these general guidelines:
Clean appropriate parts accurately
Replace any defective or worn parts
Preventive Maintenance
Maximizing Battery Life
Do not leave the battery connected to the tool if you do not use the tool for several days. The battery can discharge and go into “sleep mode” which will require a special wake-up charge procedure. For further information, see instructions for multicharger, 4211542485.
Overhaul
Have your power tool serviced by a qualified repair person using only identical replacement parts. This will ensure that the safety of the power tool is maintained.
Service must only be carried out by qualified personnel who have access to the Service instruction and/or have been trained for service on this tool.
The electric motor is a sealed unit and may under no circumstances be opened by anyone else than Atlas Copco Industrial Technique AB.
If it is judged that the electric motor is defect or in need of service, the complete motor unit should be returned to Atlas Copco Industrial Technique AB for exchange.
Motors which have been opened by anyone else than Atlas Copco Industrial Technique AB will not be serviced.
Overhaul and preventive maintenance is recommended at regular intervals once per year or after maximum 250.000 tightening depending on which occurs sooner. More frequent overhaul may be needed if the machine is used in heavy-duty operations. If the machine not is working properly, it should immediately be taken away for inspection.
The backup battery must be replaced within 24 months from the tool's production date, or last battery backup replacement. Shorter interval if tool has been used in the higher accepted temperature range. A replaced backup battery should be recycled according to the Recycling Instruction. Spare backup batteries must not be stored in ambient temperatures above 300C and should due to self-discharge not be stored more than 6 months before powering it up for 4 hours. Spare backup batteries can be stored in a fridge (non-condensing environment).
When dismantling the tool always use the specially designed service tool 4080 0848 80, (two service tools are required).
Lubrication Instructions
Lubricating Guide
Brand | Cable nut | Gears |
---|---|---|
Molycote |
| BR2 Plus |
CRC | Litium grease No. 3020 |
|
Brand | Angle gears | General purpose |
---|---|---|
Molycote | Longterm 2 plus |
|
Almagard |
| LE 3751 |
Lubrication
Lubricate gears and clutch with grease containing molybdenum disulphide (e.g. Molykote BR2 Plus). Lubricate o-rings and threaded connections with grease before assembling.
For more information, see Spare Parts section in ServAid - https://servaid.atlascopco.com.
Troubleshooting
Overheated Tool
The tool can handle any normal line jobs that an operator sustains with the proper adjustments.
The tool temperature can be influenced by the following parameters:
short cycle time
torque above rated
too low speed
very high prevailing torque
very soft joints
ambient temperature
Recycling
Environmental Regulations
When a product has served its purpose it has to be recycled properly. Dismantle the product and recycle the components in accordance with local legislation.
Batteries shall be taken care of by your national battery recovery organization.
Recycling Instruction
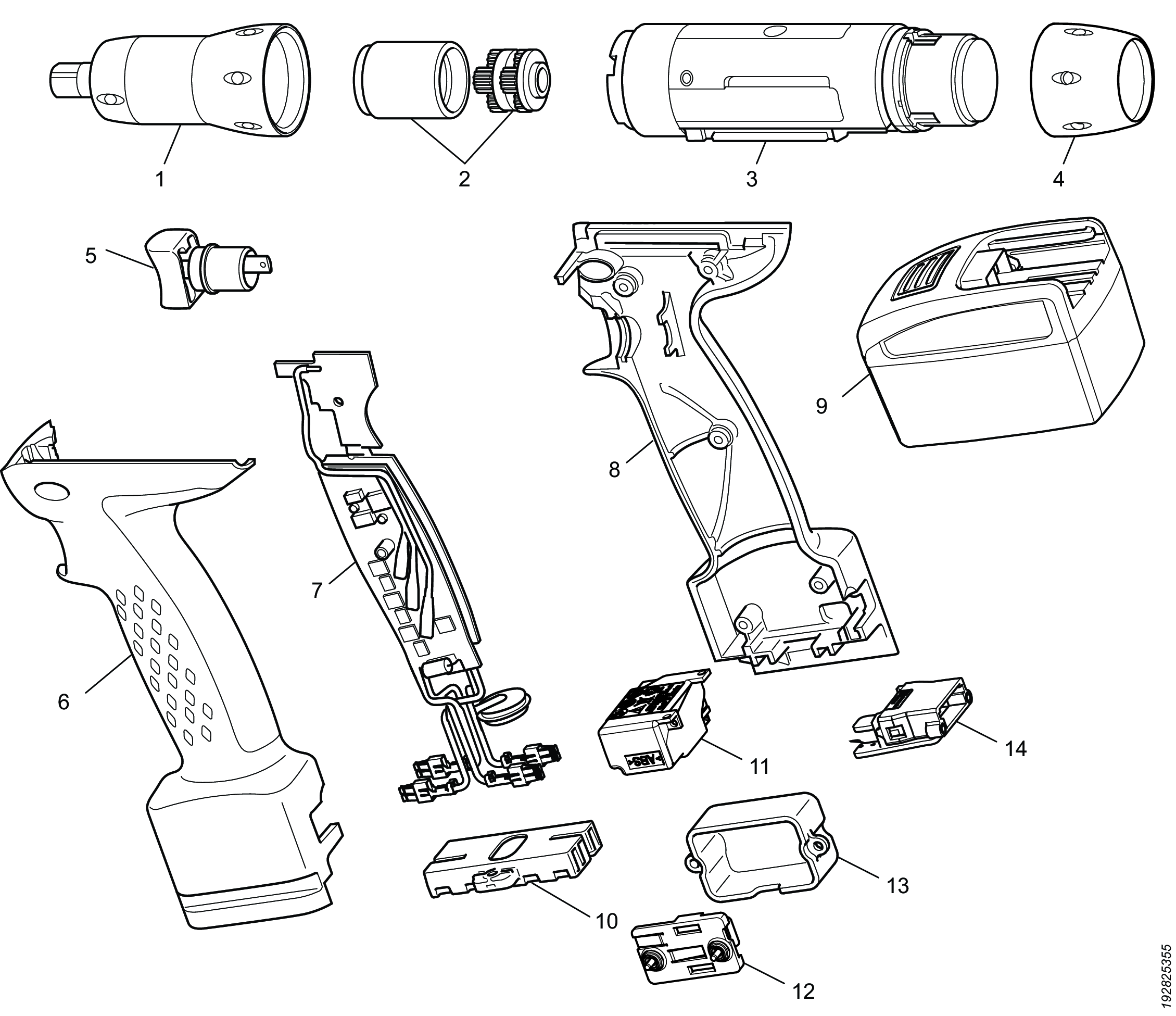
Pos. | Part | Remarks | Recycle as |
---|---|---|---|
1 | Front part |
| Metal, steel |
2 | Planetary gear | Metal, steel | |
3 | Motor module (with transducer, speaker module and led flex card) | Electronic | |
4 | Nut | Metal, steel | |
5 | Trigger button | Metal, steel | |
6 | Handle body | PA6 GF30 | |
7 | Electronics module | Electronic | |
8 | Handle body | Plastics, other, PA | |
9 | Battery | Battery, Li-Ion | |
10 | Battery connector | Plastics, other, PA | |
11 | Back up battery | Battery, Li-Ion | |
12 | Radio module | Electronic | |
13 | Lid | Plastics, other, PA | |
14 | RBU board assembly | Electronic |