ETD STR31-05-10
Electric straight nutrunner
Produktinformation
Allgemeine Informationen
Symbole am Werkzeug
Die am Werkzeug befindlichen Symbole haben folgende Bedeutung:
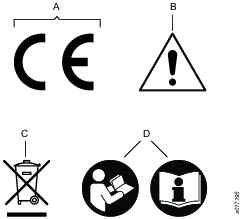
A | Die Maschinenrichtlinie 2006/42/EG legt die wesentlichen Sicherheits- und Gesundheitsschutzanforderungen fest, die das Produkt erfüllen muss, um vom Hersteller mit dem CE-Symbol gekennzeichnet werden zu können. |
B | Gehen Sie beim Betrieb des Geräts umsichtig vor. |
C | Dieses Symbol weist darauf hin, dass Produktkomponenten gemäß der WEEE-Richtlinie gehandhabt werden müssen. |
D | Lesen Sie vor dem Arbeitsbeginn oder vor der Inbetriebsetzung des Geräts oder der Maschine die Bedienungsanleitung durch. |
Sicherheitsbezogene Signalwörter
Die sicherheitsbezogenen Signalworte Gefahr, Warnung, Vorsicht und Hinweis haben folgende Bedeutung:
GEFAHR | GEFAHR weist auf eine gefährliche Situation hin, die bei Nichtvermeidung zu schweren Verletzungen mit möglicher Todesfolge führen wird. |
WARNUNG | WARNUNG weist auf eine gefährliche Situation hin, die bei Nichtvermeidung zu schweren Verletzungen mit möglicher Todesfolge führen könnte. |
ACHTUNG | VORSICHT weist bei Verwendung mit dem Sicherheitswarnsymbol auf eine gefährliche Situation hin, die bei Nichtvermeidung zu leichten oder mittelschweren Verletzungen führen könnte. |
HINWEIS | Ein HINWEIS wird für Situationen verwendet, die sich nicht auf eine mögliche Verletzungsgefahr beziehen. |
Garantie
Die Produktgarantie verfällt 12+1 Monate nach dem Versand aus dem Distributionszentrum von Atlas Copco.
Normaler Verschleiß von Teilen wird nicht von der Garantie abgedeckt.
Unter normalem Verschleiß versteht man, dass während der für diesen Zeitraum typischen Standardwerkzeugwartung Teile ausgetauscht oder Einstellungen / Verbesserungsarbeiten durchgeführt werden müssen (ausgedrückt in Zeit, Betriebsstunden, oder anderweitig).
Die Produktgarantie stützt sich auf einen korrekten Einsatz, Wartung und Reparatur des Werkzeugs und seiner Bestandteile.
Schäden an Teilen, die als Folge einer unzureichenden Wartung oder eines falschen Einsatzes durch andere Parteien als Atlas Copco oder deren zertifizierten Service-Partner während der Garantiezeit verursacht werden, sind nicht durch die Garantie gedeckt.
Um eine Beschädigung oder Zerstörung von Werkzeugteilen zu vermeiden, warten Sie das Werkzeug entsprechend der empfohlenen Wartungspläne und befolgen Sie die richtigen Anweisungen.
Garantiereparaturen werden nur in Atlas Copco-Werkstätten oder von einem zertifizierten Service-Partner ausgeführt.
Atlas Copco bietet eine erweiterte Garantie und eine vorbeugende Wartung nach dem neuesten Stand der Technik durch seine ToolCover-Verträge. Weitere Informationen erhalten Sie von Ihrem lokalen Servicerepräsentanten.
Für Elektromotoren:
Die Garantie gilt nur dann, wenn der Elektromotor nicht geöffnet wurde.
Website
Informationen zu unseren Produkten, Zubehör, Ersatzteilen und Veröffentlichungen finden Sie auf der Internetseite von Atlas Copco.
Besuchen Sie: www.atlascopco.com.
ServAid
ServAid ist ein Portal, das ständig aktualisiert wird und technische Informationen bietet, wie z.B.:
Behörden- und Sicherheitsinformationen
Technische Daten
Installations-, Betriebs- und Wartungsanweisungen
Ersatzteillisten
Zubehör
Maßzeichnungen
Besuchen Sie: https://servaid.atlascopco.com.
Weitere technische Informationen erhalten Sie bei Ihrem Atlas Copco-Vertreter vor Ort.
Sicherheitsdatenblätter MSDS/SDS
In den Sicherheitsdatenblättern werden die von Atlas Copco vertriebenen chemischen Produkte beschrieben.
Weitere Informationen finden Sie auf der Internetseite von Atlas Copco unter www.atlascopco.com/sds.
Video Produktsicherheit für Drehschrauber
Erfahren Sie mehr zu den Sicherheitsmerkmalen der Drehschrauber von Atlas Copco und den Maßnahmen, die der Bediener für den sicheren Betrieb zu ergreifen hat. Klicken Sie auf den Link, oder scannen Sie den nachfolgenden QR-Code, um das Video anzusehen:
https://www.youtube.com/watch?v=FAh6yttvUpw
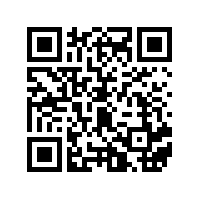
Herkunftsland
Informationen zum Herkunftsland sind auf dem Produktetikett angegeben.
Maßzeichnungen
Maßzeichnungen finden Sie entweder im Maßzeichnungsarchiv oder auf ServAid.
Besuchen Sie: http://webbox.atlascopco.com/webbox/dimdrw oder https://servaid.atlascopco.com.
Übersicht
Das Tensor-System
Das Tensor-System besteht aus einer Reihe von Schraubwerkzeugen, die über bürstenlose Elektromotoren und verschiedene Antriebseinheiten betrieben werden.
Die Motoren sind in verschiedenen Größen erhältlich. Alle Werkzeuge sind vor Überhitzung des Motors geschützt. Das elektrische Schutzsystem basiert auf einem Erdschlussschalter (EFP). Der EFP erkennt kleine Stromverluste (>30 mA) und führt in dem Fall zu einer Abschaltung des Antriebs (30 ms). Bei Änderungen oder Eingriffen in die Schutzsysteme verfällt die von Atlas Copco gewährleistete Garantie. Fehlersuche und Systemneustart dürfen nur von einer berechtigten Person ausgeführt werden. Überprüfen Sie regelmäßig die Funktion des EFP, indem Sie den Auslöseschalter drücken. Der EFP muss eine Ausschaltfunktion ausführen.
Technische Produktdaten
Technische Produktdaten finden Sie entweder auf ServAid oder auf der Internetseite von Atlas Copco.
Besuchen Sie: https://servaid.atlascopco.com oder www.atlascopco.com.
RFID-Chip
Das Werkzeug verfügt über einen integrierten RFID-Chip, auf dem Informationen über das Produkt gespeichert werden. Der Chip befindet sich am Motor des Werkzeugs. Mit einem RFID-Lesegerät können Informationen aus dem Chip ausgelesen und darauf geschrieben werden.
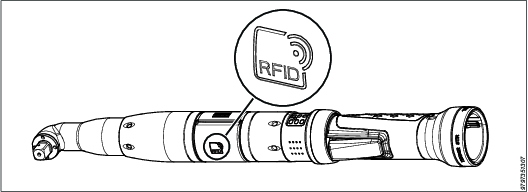
EPC-Speicher
Produktnummer, Generationsbuchstabe und Seriennummer des Werkzeugs sind im EPC-Speicher des RFID-Chips gespeichert. Die Informationen werden als Zeichenkette mit 20 Zeichen dargestellt.
Beispiel
Zeichenkette im EPC-Speicher: 84366130150670730145
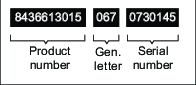
In der Zeichenkette sind drei Stellen für den Generationsbuchstaben reserviert, der im ASCII-Format dargestellt wird. Da die ASCII-Codes der Generationsbuchstaben nur aus zwei Zeichen bestehen, wird vor dem ASCII-Code stets eine „0“ eingefügt.
In der folgenden Tabelle sind die Generationsbuchstaben mit den entsprechenden ASCII-Codes aufgeführt.
Generations- | ASCII- | Generations- | ASCII- |
A | 65 | N | 78 |
B | 66 | O | 79 |
C | 67 | P | 80 |
D | 68 | Q | 81 |
E | 69 | R | 82 |
F | 70 | S | 83 |
G | 71 | D | 84 |
H | 72 | U | 85 |
I | 73 | V | 86 |
J | 74 | W | 87 |
K | 75 | X | 88 |
L | 76 | Y | 89 |
M | 77 | Z | 90 |
Der EPC-Speicher kann neu beschrieben und damit die Chipinformation neu programmiert werden, wenn der Motor eines Werkzeugs in einem anderen Werkzeug eingesetzt werden soll.
Benutzerspeicher
Neben den Werkzeuginformationen im EPC-Speicher enthält der RFID-Chip auch einen 512-Bit Benutzerspeicher, in dem der Kunde zusätzliche Informationen eintragen kann.

Benutzen Sie zum Auslesen und Beschreiben des RFID-Chips ein UHF RFID-Lesegerät.
Technische Daten
Leistungsmerkmale
Lesereichweite (handgeführt)* | Bis zu 1,5 m |
Lesereichweite (fixiert)* | Bis zu 2 m |

*Leistung basierend auf Standardtestmethoden, kann je nach Umgebungsfaktoren und Ausgangsleistung des Lesegeräts abweichen.
Funktionsmerkmale
RF Protokoll | EPC global Klasse 1 Gen2 |
Frequenz | 902-928 (US) ; 865-868 (EU) |
Speicher* | 96-EPC-Bits, 64-Bit eindeutige TID, 512-Bit Benutzerspeicher |

*EPC und Benutzerspeicher können umprogrammiert, durch Passwort geschützt oder dauerhaft gesperrt werden. TID wird zum Zeitpunkt der Herstellung festgelegt, ist eindeutig und gesperrt.
Industriestandards
RoHS | EU-Richtlinie 2011/65/EU |
CE | Ja |
Service-Übersicht
Wartungsempfehlungen
Es wird empfohlen, eine vorbeugende Wartung regelmäßig durchzuführen. Beachten Sie die ausführlichen Informationen über die vorbeugende Wartung. Wenn das Produkt nicht ordnungsgemäß funktioniert, bringen Sie es außer Betrieb und prüfen Sie es.
Wenn keine detaillierten Informationen über eine vorbeugende Wartung enthalten sind, befolgen Sie die folgenden allgemeinen Richtlinien:
Entsprechende Teile gründlich reinigen
Defekte und verschlissene Teile ersetzen
Installation
Installationsanforderung
Werkzeuganzeige
Die Werkzeuganzeige wird über die Steuerung eingeschaltet.
Bei Power Focus 4000:
Die Prog-Taste drücken.
Mit den Navigationstasten Werkzeug > Konfiguration > Zubehör-Bus > ST-Bus > Modus auswählen.
Funktion zur Stecknuss-Freigabe
Es wird empfohlen, die Funktion zur Stecknuss-Freigabe bei allen ETP ST101 Werkzeugen zu verwenden. Wenn die Funktion aktiviert ist, wird die Stecknuss nach Abschluss einer Verschraubung um 3° zurück gedreht. Dadurch soll die Spannung am Gegenhalter reduziert und eine einfachere Werkzeugentfernung ermöglicht werden.
Die Funktion zur Stecknuss-Freigabe wird über die Steuerung eingeschaltet.
Bei Power Focus 4000:
-
Die Prog-Taste drücken.
-
Mit den Navigationstasten PSatz > Programmierung+ > Optionen > Stecknuss-Freigabe > Modus Ein auswählen.
Anschluss des Werkzeugs
Das Werkzeug ist über die korrekte Power Focus Antriebseinheit mit 230 V/50 Hz (bzw. 115 V/60 Hz, einphasig) an das Netz anzuschließen. Siehe Anweisungen für Ihre Power Focus Antriebseinheit.
Erdung
Wenn das Werkzeug in eine handgehaltene oder handgeführte Halterung montiert ist, muss die Halterung unter Verwendung eines separaten 2,5 mm2 Massekabels an den Antrieb angeschlossen werden.
Installationsanleitung
Anschluss des Werkzeugkabels
-
Sicherstellen, dass das Werkzeugkabel für das Werkzeug geeignet ist.
-
Den Kabelstecker mit den beiden asymmetrisch angebrachten Köpfen am Stecker ausrichten und in die Schlitze des Werkzeughandgriffs einpassen.
-
Sicherungsmutter festziehen.
-
Sicherstellen, dass der Anschluss richtig ist. Dazu am Stecker ziehen, drücken und drehen (er darf sich nicht bewegen).

Das Werkzeug ist mit einem eingebauten elektronischen Speicherchip versehen, mit dem die Kalibrierwerte und Winkelimpulse des Drehmomentwandlers an die POWER FOCUS-/Antriebseinheit gesendet werden. Alle Änderungen der Werte in der POWER FOCUS-Einheit, die vorgenommen werden, wenn das Werkzeug angeschlossen ist, werden im Werkzeugspeicher gespeichert.
Montage des Schwenklagerjochs
Erforderliche Werkzeuge und Material
Montage-/Demontagewerkzeug 4080 1406 80
Schraubstock
Sicherungsringzange
Werkzeuge bis 50 Nm
Halten Sie das Werkzeug mit einem Schraubstock und dem Montage-/Demontagewerkzeug fest.
Bringen Sie die Gummiabdeckung an der Motorverkleidung neben dem Montage-/Demontagewerkzeug an.
Bringen Sie die Klemmringe an der Gummiverkleidung an.
Montieren Sie den Jochring am Werkzeug, indem Sie ihn auf die Klemmringe schieben.
Befestigen Sie den Jochring mit einem Sicherungsring in der Nut der Klemmringe.
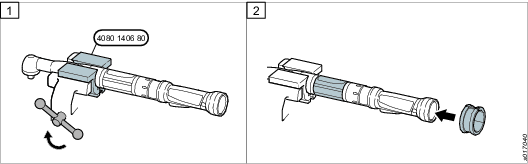
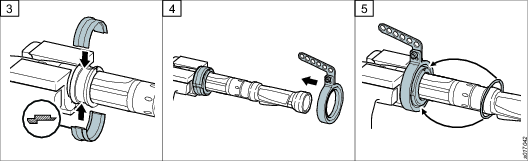
Werkzeuge ab 50 Nm
Schrauben Sie den Sicherungsring und den Jochring auf das Werkzeug.
Bringen Sie die Gummiabdeckung an der Motorverkleidung des Werkzeugs an.
Bringen Sie die Klemmringe an der Gummiverkleidung an.
Halten Sie das Werkzeug mit einem Schraubstock und dem Montage-/Demontagewerkzeug an der Gummiabdeckung fest.
Schieben Sie den Jochring auf die Klemmringe.
Befestigen Sie den Jochring mit einem Sicherungsring in der Nut der Klemmringe.
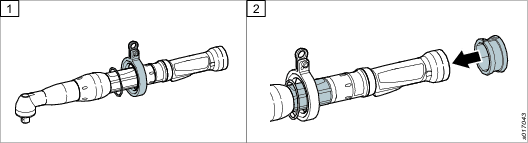
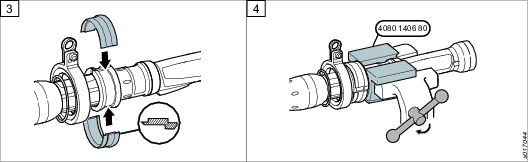
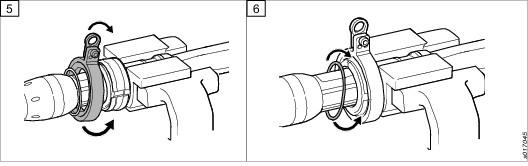
Werkzeuge mit Zubehör
Schrauben Sie den Sicherungsring und den Jochring auf das Werkzeug.
Bringen Sie die Gummiabdeckung an der Motorverkleidung an.
Bringen Sie die Klemmringe an der Gummiverkleidung an.
Halten Sie das Werkzeug mit einem Schraubstock und dem Montage-/Demontagewerkzeug an der Gummiabdeckung fest.
Schieben Sie den Jochring auf die Klemmringe.
Befestigen Sie den Jochring mit einem Sicherungsring in der Nut der Klemmringe.
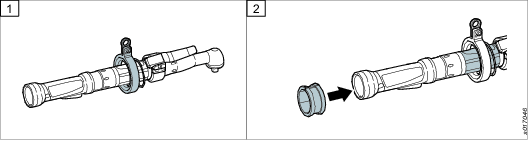
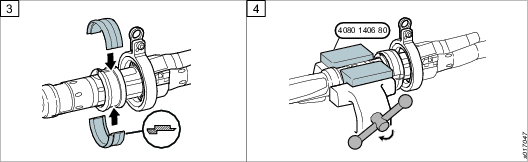
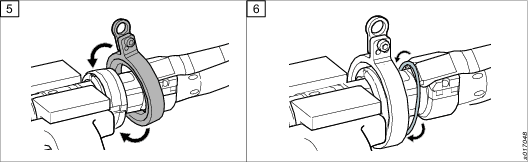
Werkzeuge mit Scannerzubehör
Bringen Sie die Gummiabdeckung an der Motorverkleidung des Werkzeugs an.
Bringen Sie die Klemmringe an der Gummiverkleidung an.
Montieren Sie den Jochring am Werkzeug, indem Sie ihn auf die Klemmringe schieben.
Befestigen Sie den Jochring mit einem Sicherungsring in der Nut der Klemmringe.
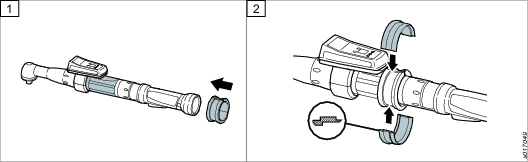
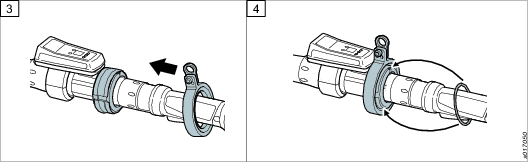
Bedienung
Ergonomie-Richtlinien
Betrachten Sie Ihren Arbeitsplatz, während Sie diese Liste mit allgemeinen Ergonomie-Richtlinien lesen, und versuchen Sie, Bereiche zu identifizieren, in denen Verbesserungen in Bezug auf Körperhaltung, Positionierung der Komponenten oder Arbeitsumgebung möglich sind.
Legen Sie regelmäßige Pausen ein und wechseln Sie regelmäßig die Arbeitshaltung.
Passen Sie den Bereich um Ihre Arbeitsstation Ihren Anforderungen und den auszuführenden Arbeiten an.
Positionieren Sie Teile und Werkzeuge so, dass statische Belastungen möglichst vermieden werden und sich sämtliche Arbeitsmittel bequem erreichen lassen.
Verwenden Sie an Ihrer Arbeitsstation für die Aufgabe geeignete Tische, Stühle oder andere Gegenstände.
Vermeiden Sie während der Ausführung von Montagearbeiten Körperhaltungen über Schulterhöhe oder mit statischer Halteposition.
Wenn Sie über Schulterhöhe arbeiten müssen, verringern Sie die auf die statischen Muskeln wirkende Belastung durch Verringerung des Werkzeuggewichts. Setzen Sie hierzu beispielsweise Drehmomentarme, Schlauchaufroller oder Gewichtsausgleicher ein. Sie können die auf die statischen Muskeln ausgeübte Belastung auch reduzieren, indem Sie das Werkzeug nah am Körper halten.
Legen Sie häufig Pausen ein.
Vermeiden Sie extreme Arm- oder Handgelenkhaltungen, insbesondere während Arbeiten, bei denen ein gewisser Kraftaufwand erforderlich ist.
Richten Sie Ihren Arbeitsplatz so in Ihrem Sichtfeld ein, dass nur minimale Augen- und Kopfbewegungen erforderlich sind.
Verwenden Sie zur Ausführung Ihrer Arbeit eine angemessene Beleuchtungen.
Wählen Sie ein zur Ausführung Ihrer Arbeit angemessenes Werkzeug aus.
Tragen Sie in lauten Umgebungen einen entsprechenden Gehörschutz.
Verwenden Sie hochwertige Einsätze und Kleinteile, um eine übermäßige Vibrationsbelastung möglichst zu vermeiden.
Minimieren Sie nach Möglichkeit durch Reaktionskräfte verursachte Belastungen.
Beim Schneiden:
Eine Trennscheibe kann stecken bleiben, wenn sie verbogen ist oder nicht korrekt geführt wird. Verwenden Sie einen für die Trennscheibe geeigneten Flansch und vermeiden Sie es, die Trennscheibe während des Betriebs zu biegen.
Beim Bohren:
Die Bohrmaschine kann beim Durchbrechen des Bohrers stehen bleiben. Verwenden Sie bei hohem Stillstandsmoment Stützgriffe. Gemäß Teil 3 der Sicherheitsnorm ISO11148 wird empfohlen, bei Pistolengriffmodellen eine Vorrichtung zur Aufnahme von Reaktionsmomenten von über 10 Nm und bei Stabmodellen zur Aufnahme von Reaktionsmomenten von über 4 Nm zu verwenden.
Bei Verwendung von Schraubendrehern und Schraubern mit Direktantrieb:
Reaktionskräfte sind von der Werkzeugeinstellung und den Eigenschaften der jeweiligen Verbindung abhängig. Die Höhe der Reaktionskraft, die eine Bediener tolerieren kann, hängt von dessen Körperkraft und Haltung ab. Passen Sie die Drehmomenteinstellung der Stärke und der Körperhaltung des Bedieners an und verwenden Sie bei zu hohem Drehmoment einen Drehmomentarm oder einen Gegenhalter.
Verwenden Sie in staubigen Umgebungen ein System zur Staubabsaugung oder tragen Sie einen Mundschutz.
Betriebsanleitung
Allgemeine Anweisungen
Das Werkzeug darf nur in Kombination mit dem zugehörigen Gegenhalter verwendet werden, der auf die entsprechende Schraubverbindungsanwendung angepasst wurde.
Doppel-Hebelstarter
Doppel-Hebelstarter (im Betrieb empfohlen)
Bedienung
Sicherzustellen, daß sich das Werkzeug in einem guten Zustand befindet und die Steuereinheit vor der Benutzung richtig programmiert ist, um eine unerwartete Bewegung des Werkzeugs zu vermeiden, die zu Verletzungen führen kann.
Überprüfen, ob das Werkzeug in der richtigen Drehrichtung rotiert, indem geprüft wird ob das Funktionslicht Angeschaltet oder Ausgeschaltet ist. Das Funktionslicht befindet sich über dem Handgriff.
Die Sanftstart-Funktion erleichtert das Aufsetzen der Maschine auf den Schraubenkopf und das Gewinde.
Die Dauer des Sanftstarts ist verstellbar, siehe Bedienungsanleitung für die Antriebseinheit.
Das Werkzeug ist mit Anzeigeleuchten versehen,
Grün = Festziehen OK
Gelb = Warnung – niedriges Drehmoment.
Rot = Warnung – hohes Drehmoment.
Orange = Funktionslicht
Blau = Funktionslicht
Wartung
ESD-Probleme vermeiden
Die Komponenten im Inneren des Produkts und der Steuerung sind empfindlich gegenüber elektrostatischen Entladungen. Stellen Sie zur Vermeidung zukünftiger Störungen sicher, dass Service und Wartung in einer ESD-genehmigten Arbeitsumgebung erfolgen. Die Abbildung unten zeigt ein Beispiel für eine entsprechende Service-Arbeitsstation.
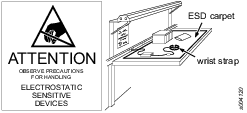
Wartungsanweisungen
Überholung
Die Wartung darf nur von erfahrenem Personal ausgeführt werden, das Zugang zu den Wartungsanleitungen hat und/oder für die Wartung von Tensor Werkzeugen ausgebildet ist.

Beim Elektromotor handelt es sich um eine abgedichtete Einheit, die grundsätzlich nur von Atlas Copco Industrial Technique AB geöffnet werden darf!
Sollte der Elektromotor defekt sein oder gewartet werden müssen, senden Sie die komplette Motoreinheit an Atlas Copco Industrial Technique zurück.
Motoren, die von jemand anderem als Atlas Copco Industrial Technique geöffnet wurden, werden nicht gewartet.
Es wird empfohlen, regelmäßig – zumindest einmal jährlich oder alle 250.000 Verschraubungen (je nachdem, was früher eintritt) – eine Überholung und vorbeugende Wartung durchzuführen. Im Falle von Hochleistungseinsätzen ist u. U. eine häufigere Überholung vonnöten. Falls die Maschine nicht einwandfrei funktioniert, ist sie unverzüglich außer Betrieb zu nehmen und einer Inspektion zu unterziehen.
Um das Werkzeug zu zerlegen, ist das spezielle Wartungswerkzeug 4080 0848 80 zu verwenden, (zwei Wartungswerkzeuge sind erforderlich).
Überholung für Modelle mit kleinem Werkzeugkopf (SH-Modelle): Es wird empfohlen, regelmäßig – ein Mal jährlich oder nach jeweils max. 100.000 Verschraubungen (je nachdem, was früher eintritt) – eine Überholung und vorbeugende Wartung durchzuführen. Eine häufigere Überholung kann notwendig werden, wenn das Werkzeug bei hohem Drehmoment, hoher Zyklusrate oder langen Verschraubungszeiten eingesetzt wurde. Falls die Maschine nicht einwandfrei funktioniert, ist sie unverzüglich außer Betrieb zu nehmen und einer Inspektion zu unterziehen.
Wartungsempfehlungen
Es wird empfohlen, eine vorbeugende Wartung regelmäßig durchzuführen. Beachten Sie die ausführlichen Informationen über die vorbeugende Wartung. Wenn das Produkt nicht ordnungsgemäß funktioniert, bringen Sie es außer Betrieb und prüfen Sie es.
Wenn keine detaillierten Informationen über eine vorbeugende Wartung enthalten sind, befolgen Sie die folgenden allgemeinen Richtlinien:
Entsprechende Teile gründlich reinigen
Defekte und verschlissene Teile ersetzen
Serviceanleitung
Es wird empfohlen, regelmäßig – zumindest ein Mal jährlich oder alle 250.000 Verschraubungen (je nachdem, was früher eintritt) – eine Überholung und vorbeugende Wartung durchzuführen. Eine häufigere Überholung kann notwendig werden, wenn das Werkzeug bei hohem Drehmoment, hoher Zyklusrate oder langen Verschraubungszeiten eingesetzt wurde. Falls die Maschine nicht einwandfrei funktioniert, ist sie unverzüglich außer Betrieb zu nehmen und einer Inspektion zu unterziehen.
Bei den Überholungen müssen alle Teile sorgfältig gereinigt und defekte oder verschlissene Teile (z.B. O-Ringe) müssen ausgetauscht werden.
Schmieranweisungen
Schmieranleitung
Teil | Schmiermittel |
---|---|
Planetengetriebe mit Lagern | Molycote BR2 Plus |
Winkelgetriebe mit Lagern | Atlas Gear Grease 270 |
Kabeldurchführung | CRC Lithium Grease No. 3020 |
Gewinde, O-Ringe, Sonstige | Almagard LE 3751 |
Schmierung
Bei jedem Servicefall gemäß dem Leitfaden zur Schmierung schmieren.
Weitere Informationen finden Sie im Abschnitt Ersatzteile unter ServAid - https://servaid.atlascopco.com.
Reparaturanleitung
Reparatur
Reparaturarbeiten dürfen nur von qualifiziertem und entsprechend autorisiertem Personal ausgeführt werden. Weitere Informationen erhalten Sie bei Ihrem zuständigen Atlas Copco Händler.
Störungshilfe
Überhitztes Werkzeug
Bei korrekter Einstellung kann das Werkzeug sämtlichen normalen Arbeitsbedingungen standhalten. Eine Überhitzung kann durch eine Verbindung verschiedener Faktoren verursacht werden: Drehmoment über dem Sollwert, zu niedrige Drehzahl, zu lange Rampendauer (Motor muss für lange Zeit ein hohes Drehmoment liefern), sehr hohes Sicherungsmoment, sehr weiche Verbindungen, kurze Zykluszeit. Zur Behebung Drehzahl, Rampendauer und Schraubstrategie überprüfen. Eine einstufige Schraubstrategie und Ergoramp konservieren am meisten Wärme. Weitere Informationen finden Sie im Benutzerhandbuch Ihres POWER FOCUS. Sollten die obigen Behebungsmaßnahmen nicht ausreichend sein, wählen Sie ein Werkzeug mit der nächsthöheren Kapazität aus.
Power Focus 3000/4000
Ist POWER FOCUS eingeschaltet und im LAUF-Modus? Prüfen, dass die korrekte POWER FOCUS Einheit verwendet wird (ST31/ST32/ST61/STR31/STR61-Tensor3-7, ST81-Tensor8-9). Die Sicherungen für das Antriebsteil prüfen. Antriebsparameter prüfen, siehe Benutzerhandbuch der POWER FOCUS-/Antriebseinheit. Den Erdschlussschalter hinten am Antrieb prüfen. Falls er ausgelöst wurde, muss sichergestellt werden, dass vor Fortsetzen der Arbeiten die Hauptursache für den Fehler festgestellt wurde. Prüfen, dass die Verdrahtung am Fernstartanschluss korrekt ist. Weitere Informationen entnehmen Sie 9836 4954/9836 2258.
Power Focus 600/6000
Ist das Gerät eingeschaltet? Den Erdschlussschalter hinter der Frontklappe prüfen. Falls er ausgelöst wurde, muss sichergestellt werden, dass vor Fortsetzen der Arbeiten die Hauptursache für den Fehler festgestellt wurde. Prüfen, dass die Verdrahtung am Fernstartanschluss korrekt ist. Weitere Informationen entnehmen Sie 9836 4954/9836 7446.
Recycling
Umweltschutzbestimmungen
Nachdem ein Produkt seinen Zweck erfüllt hat, muss es ordnungsgemäß recycelt werden. Zerlegen Sie das Produkt und recyceln Sie die Komponenten gemäß örtlicher Vorschriften.
Batterien sollten an Ihre öffentliche Batterieverwertungsstelle weitergegeben werden.
Recycling-Informationen
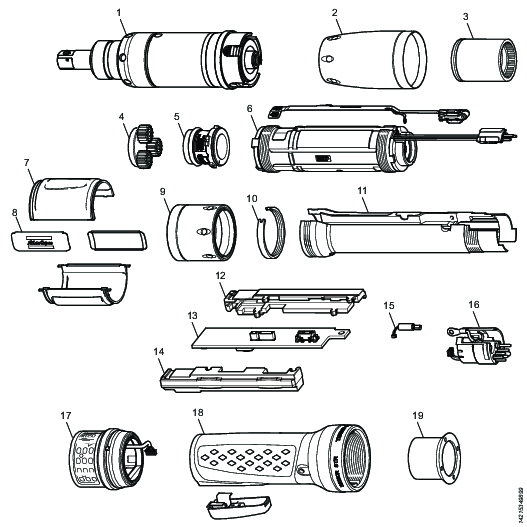
Teil | Anmerkungen | Recyceln als | |
1 | Vorderteil | Metall, Stahl | |
2 | Hutmutter | Metall, Stahl | |
3 | Getriebegehäuse | Metall, Stahl | |
4 | Planetengetriebe | Metall, Stahl | |
5 | Drehmomentgeber | Metall, Stahl | |
6 | Motor | WEEE | |
7 | Cover | Kunststoff, Sonstiges, PA | |
8 | Platten | Metall, Stahl | |
9 | Hutmutter |
| Metall, Stahl |
10 | Federring | Metall, Stahl | |
11 | Griffkörper |
| Metall, Aluminium |
12 | Hauptplatinenhalter | Achtung, nur bei neuer Version des Elektronikmoduls (Nr. 13) | Gummi, Thermoplastisches Elastomer |
13 | Elektronikmodul | WEEE | |
14 | Hauptplatinenhalter | Achtung, nur bei neuer Version des Elektronikmoduls (Nr. 13) | Gummi, Thermoplastisches Elastomer |
15 | Elektronikmodul | WEEE | |
16 | Elektronikmodul | WEEE | |
17 | MMS-Modul | WEEE | |
18 | Handgriff und Taster | Kunststoff, sonstige und Metall, Stahl | |
19 | Mutter | Metall, Stahl |