Torcflex Low Profile Tool
Hydraulic Torque Wrench
Produktinformation
Allgemeine Informationen
Sicherheitsbezogene Signalwörter
Die sicherheitsbezogenen Signalworte Gefahr, Warnung, Vorsicht und Hinweis haben folgende Bedeutung:
GEFAHR | GEFAHR weist auf eine gefährliche Situation hin, die bei Nichtvermeidung zu schweren Verletzungen mit möglicher Todesfolge führen wird. |
WARNUNG | WARNUNG weist auf eine gefährliche Situation hin, die bei Nichtvermeidung zu schweren Verletzungen mit möglicher Todesfolge führen könnte. |
ACHTUNG | VORSICHT weist bei Verwendung mit dem Sicherheitswarnsymbol auf eine gefährliche Situation hin, die bei Nichtvermeidung zu leichten oder mittelschweren Verletzungen führen könnte. |
HINWEIS | Ein HINWEIS wird für Situationen verwendet, die sich nicht auf eine mögliche Verletzungsgefahr beziehen. |
Garantie
Die Produktgarantie verfällt 12+1 Monate nach dem Versand aus dem Distributionszentrum von Atlas Copco.
Normaler Verschleiß von Teilen wird nicht von der Garantie abgedeckt.
Unter normalem Verschleiß versteht man, dass während der für diesen Zeitraum typischen Standardwerkzeugwartung Teile ausgetauscht oder Einstellungen / Verbesserungsarbeiten durchgeführt werden müssen (ausgedrückt in Zeit, Betriebsstunden, oder anderweitig).
Die Produktgarantie stützt sich auf einen korrekten Einsatz, Wartung und Reparatur des Werkzeugs und seiner Bestandteile.
Schäden an Teilen, die als Folge einer unzureichenden Wartung oder eines falschen Einsatzes durch andere Parteien als Atlas Copco oder deren zertifizierten Service-Partner während der Garantiezeit verursacht werden, sind nicht durch die Garantie gedeckt.
Um eine Beschädigung oder Zerstörung von Werkzeugteilen zu vermeiden, warten Sie das Werkzeug entsprechend der empfohlenen Wartungspläne und befolgen Sie die richtigen Anweisungen.
Garantiereparaturen werden nur in Atlas Copco-Werkstätten oder von einem zertifizierten Service-Partner ausgeführt.
Atlas Copco bietet eine erweiterte Garantie und eine vorbeugende Wartung nach dem neuesten Stand der Technik durch seine ToolCover-Verträge. Weitere Informationen erhalten Sie von Ihrem lokalen Servicerepräsentanten.
Website
Informationen zu unseren Produkten, Zubehör, Ersatzteilen und Veröffentlichungen finden Sie auf der Internetseite von Atlas Copco.
Besuchen Sie: www.atlascopco.com.
ServAid
ServAid ist ein Portal, das ständig aktualisiert wird und technische Informationen bietet, wie z.B.:
Behörden- und Sicherheitsinformationen
Technische Daten
Installations-, Betriebs- und Wartungsanweisungen
Ersatzteillisten
Zubehör
Maßzeichnungen
Besuchen Sie: https://servaid.atlascopco.com.
Weitere technische Informationen erhalten Sie bei Ihrem Atlas Copco-Vertreter vor Ort.
Sicherheitsdatenblätter MSDS/SDS
In den Sicherheitsdatenblättern werden die von Atlas Copco vertriebenen chemischen Produkte beschrieben.
Weitere Informationen finden Sie auf der Internetseite von Atlas Copco unter www.atlascopco.com/sds.
Sicherheitshinweis
Keine Modifikationen an Geräten oder Zubehör vornehmen und Stoßeinwirkungen auf diese vermeiden - Kontaktieren Sie Atlas Copco für besondere Werkzeuganwendungen oder Modifikationen an Geräten. Nicht genehmigte Modifikationen können zu einem vorzeitigen Ausfall des Gerätes und somit zu Personenschäden führen.
Elektrische Pumpen nicht in explosionsgefährdeten oder feuchten Umgebungen einsetzen - Stellen Sie beim Einsatz einer elektrischen Pumpe sicher, dass die Verlängerungskabel, Netzteile und Erdung den elektrotechnischen Vorschriften entsprechen. Achten Sie auf elektrische Gefahr, z. B. Funkenbildung oder Stromschläge.
Gefahren bei hohem Hydraulikdruck -
Verwenden Sie geeignete Werkzeuge, Schläuche und Anschlussstücke. Stellen Sie sicher, dass alle Schlauchanschlüsse komplett verbunden, festsitzend und frei von Leckagen sind.
Frei von austretender Hydraulikflüssigkeit halten. Von austretenden Flüssigkeiten reinigen.
Überschreiten Sie niemals den maximalen Betriebsdruck der Pumpe. Stellen Sie sicher, dass Schlauch und Anschlussstücke für einen dynamischen Betriebsdruck von 10000 psi (700 bar) geeignet sind. Der maximale Betriebsdruck ist dauerhaft auf dem Werkzeug gekennzeichnet.
Hände und Finger von Einklemmstellen fernhalten - Einklemmstellen treten um den Einzugsbereich sowie beim Betrieb in beengten Räumen auf.
Gerät in gutem Betriebszustand halten - Auf Schäden am Werkzeug, Risse oder Abnutzung überprüfen und der Gerätenutzung entsprechend schmieren. Beschädigte Geräte außer Betrieb nehmen.
Betrieb durch eine Person empfohlen - Das Werkzeug sollte ausschließlich durch geschultes und qualifiziertes Personal betrieben werden. Kann ein Werkzeugbetrieb durch zwei Personen nicht vermieden werden, so muss eine Risikobewertung durchgeführt werden, welche die Umgebung, Anwendung, Koordination (zwischen den Bedienern) und Kommunikation vollständig abdeckt. Der Bediener, der den Drehmomentschlüssel hält, sollte den Betrieb kontrollieren, d. h. die kontrollierende Person ist nicht notwendigerweise im Besitz des Steuergeräts, gibt jedoch die Anweisungen zur Steuerung der Pumpe/des Werkzugs.
Werkzeugreaktion korrekt einstellen - Ein falscher oder instabiler Reaktionspunkt kann zu Bewegungen des Werkzeugs während des Betriebs und somit zu einem erhöhten Bedienerrisiko führen. Eine fehlerhafte Auswahl des Reaktionspunkts kann zudem zu einem vorzeitigen Werkzeugausfall führen.
Geeignete persönliche Schutzausrüstung tragen – Geeignet für die Arbeit mit oder in der Nähe von Hochdruck-Hydrauliksystemen, z.B. Schutzbrille (EN166), Handschuhe, Sicherheitsschuhe, usw. Tragen Sie keine weiten Handschuhe oder Handschuhe, bei denen die Fingerteile Risse aufweisen oder ausgefranst sind. Handschuhe können sich in der umlaufenden Antriebsspindel/im Aufsatz verfangen, was dazu führen kann, dass Finger abgetrennt oder gebrochen werden.
Schläuche nicht übermäßig verbiegen; Einklemmen oder Beschädigungen an Schläuchen vermeiden - Schäden an den Schläuchen können durch thermische, mechanische oder chemische Beanspruchung entstehen. Hierdurch kann Hochdruck-Hydraulikflüssigkeit austreten, was zu Schäden am Gerät sowie zu Personenschäden führen kann.
Werkzeugauswahl – Wählen Sie ein hinsichtlich der Drehmomentanforderungen und Platzverhältnisse für die Anwendung geeignetes Werkzeug.
Herkunftsland
Informationen zum Herkunftsland sind auf dem Produktetikett angegeben.
Maßzeichnungen
Maßzeichnungen finden Sie entweder im Maßzeichnungsarchiv oder auf ServAid.
Besuchen Sie: http://webbox.atlascopco.com/webbox/dimdrw oder https://servaid.atlascopco.com.
Übersicht
Überblick Flachschlüssel
Der Torcflex-Flachschlüssel (TFX) ist ein professionelles Hydraulikwerkzeug, das für die Ausübung von Drehmoment auf industrielle Befestigungselemente entwickelt wurde, um so das korrekte Anziehen oder Lösen von industriellen Schraubverbindungen sicherzustellen. Das Werkzeug setzt einen doppeltwirkenden Hydraulikzylinder ein, um lineare Kraft über einen Klinkenmechanismus in Drehmoment umzuwandeln. Das Drehmoment wird durch die Anpassung des auf den Hydraulikzylinder wirkenden Drucks geregelt.
Das Werkzeug besteht aus den folgenden Hauptkomponenten:

A | Schwenkbarer Verteiler | Ein schwenkbarer Verteiler mit Hydraulikkupplungen zum Anschluss an eine geeignete Druckluftversorgung. |
B | Sperrklinkenverbindung | Eine Sperrklinkenverbindung, welche den Sechskantantrieb antreibt. Atlas Copco bietet verschiedene optionale Sperrklinkenverbindungen für jedes Antriebskopfmodell an, sodass die Größe des Sechskants verändert werden kann. |
C | Sechskantantrieb | Der Sechskantantrieb ist ein Funktionsteil zur Anwendung von Drehmoment für die Sperrklinkenverbindung. |
D | Haltestift | Ein Haltestift zur Verbindung des Antriebskopfs mit der Sperrklinkenverbindung. |
E | Reaktionsarm | Ein fester Reaktionsarm, der die während des Betriebs des Werkzeugs entstehenden Reaktionskräfte absorbiert. |
F | Antriebskopf | Ein Antriebskopf, der das Hydraulikelement des Werkzeugs ist. |
Technische Daten
Stromversorgung Hydraulikdruck alle Modelle
Min. 104 bar – Max. 700 bar Min. 1500 psi – Max. 10000 psi |
Product No. | Min. Drehmomentbereich | Max. Drehmomentbereich | Gewicht | |||
---|---|---|---|---|---|---|
Nm | ft lb | Nm | ft lb | kg | lb | |
TFX02 (Co-Axial) 8434240668 | 348 | 257 | 2318 | 1710 | 1.12 | 2.47 |
TFX02 (Doppel) 8434241975 | 348 | 257 | 2318 | 1710 | 1.31 | 2.89 |
TFX04 (Co-Axial) 8434241147 | 784 | 579 | 5227 | 3855 | 1.96 | 4.32 |
TFX04 (Doppel) 8434241976 | 784 | 579 | 5227 | 3855 | 2.14 | 4.72 |
TFX08 (Co-Axial) 8434241787 | 1658 | 1223 | 11051 | 8151 | 3.29 | 7.25 |
TFX08 (Doppel) 8434242070 | 1658 | 1223 | 11051 | 8151 | 3.46 | 7.63 |
TFX14 (Co-Axial) 8434242402 | 2725 | 2010 | 18168 | 13400 | 5.1 | 11.24 |
TFX14 (Doppel) 8434242405 | 2725 | 2010 | 18168 | 13400 | 5.27 | 11.62 |
TFX18 (Co-Axial) 8434242713 | 3879 | 2861 | 25861 | 19074 | 6.92 | 15.26 |
TFX18 (Doppel) 8434242732 | 3879 | 2861 | 25861 | 19074 | 7.08 | 15.61 |
Abmessungen
Maßzeichnungen finden Sie entweder im Maßzeichnungsarchiv oder auf ServAid: http://webbox.atlascopco.com/webbox/dimdrw oder https://servaid.atlascopco.com.
Technische Produktdaten
Technische Produktdaten finden Sie entweder auf ServAid oder auf der Internetseite von Atlas Copco.
Besuchen Sie: https://servaid.atlascopco.com oder www.atlascopco.com.
Angaben zur ATEX-Zertifizierung
ATEX

In explosionsgefährdeten Bereichen sollten ausschließlich Werkzeuge und Geräte verwendet werden, die entsprechend zertifiziert und mit dem ATEX-Symbol gekennzeichnet sind.

Der Bediener muss vor der Verwendung sämtliche Betriebsanleitungen lesen und zur Kenntnis nehmen!
Diese (zusätzlichen) Informationen und Anleitungen müssen gemeinsam mit den standardmäßigen Produkt- und Sicherheitshinweisen verwendet werden, die allen hydraulischen Torcflex-Drehmomentschlüsseln beiliegen.

Betrieb in ATEX-Zonen: Bei Arbeiten innerhalb von explosionsgefährdeten Bereichen ist mit besonderer Vorsicht vorzugehen. Hinsichtlich der Verschraubungsanwendung und der Verwendung des Torcflex-Werkzeugsortiments ist besondere Sorgfalt geboten. Der Bediener muss vor dem Einsatz eines hydraulischen Torcflex-Drehmomentschlüssels innerhalb einer explosionsgefährdeten Umgebung (ATEX-Zone) eine Risikobewertung durchführen.
Es liegt in der Verantwortung des Bedieners, das Werkzeug zu warten und so einen sicheren Betrieb innerhalb von ATEX-Zonen sicherzustellen. Durch die Nichteinhaltung der Wartungsempfehlungen wird die Wahrscheinlichkeit eines mechanischen Versagens und somit das Risiko mechanischer Funkenbildung erhöht.
Falls der Schlüssel Anzeichen einer Fehlfunktion aufweist, entfernen Sie diesen aus der ATEX-Zone, bevor Sie nach ihrer Ursache suchen. Versuchen Sie NICHT, den Schlüssel in der ATEX-Zone zu reparieren.
Wenn der Schlüssel herunterfällt, entfernen Sie ihn zunächst aus der ATEX-Zone, bevor Sie ihn auf Schäden untersuchen. Führen Sie vor der erneuten Verwendung einen Druck- und einen Funktionstest durch.
Inspektion des Torcflex-Schlüssels
Überprüfen Sie den Allgemeinzustand des Torcflex-Schlüssels, bevor Sie das Werkzeug in einer ATEX-Zone einsetzen. Besondere Aufmerksamkeit sollte den Antriebskomponenten zukommen, also dem Vierkant- oder Sechskantantrieb, der Sperrklinke und den Antriebsklinken. Teile, die sich in schlechtem Zustand befinden oder deutlichen Verschleiß aufweisen, müssen ausgetauscht werden. Achten Sie während des Wiederzusammenbaus darauf, die Teile korrekt gemäß den Wartungsanweisungen zu schmieren.
Hinweise zu System und Betrieb
Verwenden Sie Torcflex-Drehmomentschlüssel nur dann in ATEX-Zonen, wenn sie mit anderen ATEX-konformen oder zertifizierten Komponenten verbunden sind, wie z. B. Schläuchen und Hydraulikpumpen.
Überprüfen Sie den elektrischen Durchgang innerhalb des Drehmomentschlüsselsystems. Um elektrostatische Aufladungen zu vermeiden, ist das System / die Pumpe entsprechend elektrisch zu erden.
Besondere Aufmerksamkeit ist bei der Auswahl von Reaktionspunkten sowie der Platzierung und dem Halten des hydraulischen Drehmomentschlüssels geboten.
Stellen Sie sicher, dass sich das Zubehör und die Steckschlüssel in einem guten Betriebszustand befinden und für den Einsatz in explosionsgefährdeten Bereichen geeignet sind.
ATEX-Codedefinition
Der ATEX-Code ist: | |
---|---|
![]() | II 2 G Ex h IIC T4 Gb II 2 D Ex h IIIC T135°C Db -20 °C ≤ Ta ≤ 40 °C |
Beschreibung | Wert | Definition |
---|---|---|
Gerätegruppe | II | Oberflächenindustrie |
Gerätekategorie Gruppe II | 2 | Hohes Schutzniveau
|
Umgebung
| G | Umgebung, in der Gas, Dämpfe oder Nebel vorhanden sind |
D | Umgebung, in der Staub vorhanden ist | |
Sicherheitsdesign | h | Mechanisches Produkt |
Gasgruppe | IIC | Wasserstoff / Acetylen |
IIB | Ethylen | |
Staubgruppe: | IIIC | Oberflächlicher brennbarer Staub |
Max. Oberflächentemperatur in einer Umgebung, in der Gas vorhanden ist |
| T1 = 450 °C T2 = 300°C T3 = 200°C T4 = 135°C T5 = 100°C T6 = 85°C |
Max. Oberflächentemperatur in einer Umgebung, in der Staub vorhanden ist |
| Beispieltemperaturen: T85 °C T100 °C T135 °C T200 °C T240 °C |
Installation
Installationsanforderung
Allgemeine Installationsanforderungen
Schließen Sie den Torcflex-Schlüssel zum Betrieb mit einem Hydraulikschlauch an ein Hydraulikaggregat an. Verwenden Sie für maximale Effizienz und Genauigkeit Pumpen und Schläuche für Drehmomentschlüssel von Atlas Copco. Werden keine Pumpen und Schläuche von Atlas Copco verwendet, stellen Sie Folgendes vor dem Anschluss von Torcflex-Schlüsseln sicher:
Systemvoraussetzungen:
Alle Systemkomponenten müssen für eine dynamische Druckbelastung von 700 bar (10.000 psi) ausgelegt sein.
Pumpenanforderungen:
Maximaler Vorschubdruck: 700 bar (10.000 psi).
Maximaler Einzugsdruck: 120 bar (1.740 psi).
Ferngesteuertes Wegeventil für den Betrieb des doppeltwirkenden Zylinders; der Druck muss beim Wechsel von Vorschub zu Einzug abgelassen werden.
Aus Sicherheitsgründen muss die Fernsteuerung so konfiguriert werden, dass das Werkzeug automatisch eingezogen wird, wenn der Knopf losgelassen wird.
Einstellbares Druckbegrenzungsventil.
Kalibriertes Manometer (Genauigkeitsklasse 1).
Achten Sie bei Systemen mit Schraubkupplung darauf, dass die Vorschubkupplung eine Steckverbindung und die Einzugskupplung eine Buchsenverbindung ist. Weitere Informationen finden Sie im Abschnitt Systemanschluss – Schraubkupplung.
Mit Schraubkupplungen ausgestattete Torcflex-Schlüssel verwenden CEJN 232-Kupplungen mit ¼-NPT-Gewinden. Überprüfen Sie vor der Verwendung von Kupplungen anderer Marken für das System deren Kompatibilität. Weitere Informationen finden Sie im Abschnitt Systemanschluss – Schraubkupplung.
Anforderungen an die Hydraulikschläuche:
Vorschubleitung − Verbindung Buchse zu Buchse.
Einzugsleitung − Nippel Stecker zu Stecker.
Führen Sie vor dem Systemanschluss folgende Maßnahmen durch:
Stellen Sie bei elektrischen Pumpen sicher, dass die Stromversorgung für die Pumpe geeignet ist, und minimieren Sie die Länge der Verlängerungskabel.
Stellen Sie bei Druckluftpumpen sicher, dass die Druckluftversorgung für die Pumpe geeignet ist, und minimieren Sie die Länge der Luftleitungen.
Überprüfen Sie die Netz- und Zuleitungskabel auf Schäden, bevor Sie die Kabel an die Stromversorgung anschließen.
Überprüfen Sie die Druckluftschläuche und -kupplungen auf Schäden, bevor Sie die Schläuche an das System anschließen.
Überprüfen Sie den Ölstand und füllen Sie gegebenenfalls Öl nach.
Stellen Sie sicher, dass das Manometer kalibriert ist.
Stellen Sie sicher, dass die Schlag-Steckschlüssel über die für die Anwendung geeignete Größe verfügen.
Stellen Sie sicher, dass die Schlag-Steckschlüssel frei von Beschädigungen sind.
Wählen Sie einen für das Solldrehmoment der Anwendung geeigneten Schlüssel aus.
Um die Lebensdauer des Schlüssels zu erhöhen, betreiben Sie das Werkzeug nicht für längere Zeiträume mit über 80 % seiner Leistung. Wie bei jeder Maschine wird durch den kontinuierlichen Betrieb bei voller Leistung die Lebensdauer reduziert. Zudem muss der Schlüssel öfter gewartet und öfter verschlissene Teil ausgetauscht werden.
Achten Sie bei Anwendungen, bei denen die hintere Mutter sich drehen kann, darauf, dass ein geeigneter Ersatzschrauber zur Verfügung steht.
Installationsanleitung
Installation der TL-Sperrklinkenverbindung

Achten Sie darauf, dass das Endstück der Kolbenstange und die Antriebsplatten vor der Installation korrekt geschmiert wurden.

Einsetzen der Sperrklinkenverbindung
Ziehen Sie den Verbindungsstift (1) heraus. Drücken Sie den Klinkenmechanismus (2) vollständig ein und haken Sie den Antriebskopf an der Verbindung ein.
Sichern Sie den Antriebskopf mit dem Verbindungsstift (3).

Installation der RL-Sperrklinkenverbindung

Achten Sie darauf, dass das Endstück der Kolbenstange und die Antriebsplatten vor der Installation korrekt geschmiert wurden.

Einsetzen der Sperrklinkenverbindung
Ziehen Sie den Verbindungsstift (1) heraus. Drücken Sie den Klinkenmechanismus (2) vollständig ein und haken Sie den Antriebskopf an der Verbindung ein.
Sichern Sie den Antriebskopf mit dem Verbindungsstift (3).

Installation des Stützgriffs
Achten Sie darauf, dass der Handgriff über die korrekte Schraubengröße verfügt, bevor Sie diesen am Schrauber installieren. Es sind zwei Schraubengrößen für den Stützgriff verfügbar; wählen Sie die korrekte Schraubengröße aus der Liste aus.
TF01 / TFX02 = M6
TF03/05/08/10 / TFX04/08 = M8
Der Schlüssel erlaubt die Installation des Stützgriffs an drei unterschiedlichen Positionen.
Seitliche Position, links oder rechts:

Vordere Position:

Seitliche Position am Antriebskopf, links oder rechts:

Vorbereitung des Handgriffs für die Installation
Schieben Sie die Schraube durch den Handgriff.
Ziehen Sie die Schraube mithilfe der Rändelschraube fest.
Stellen Sie sicher, dass die Schraube über Axialspiel verfügt, um die Installation zu erlauben.

Installation des Handgriffs am Schlüssel
Führen Sie die Passstifte an der Basis des Handgriffs in die Bohrungen am Schlüssel ein.
Halten Sie den Handgriff in Position und ziehen Sie die Schraube mithilfe der Rändelschraube am Schlüssel fest.

Anpassen der Handgriffposition

Die Schraube muss zum Anpassen der Handgriffposition nicht gelöst werden.
Sie können den Stützgriff in 30-Grad-Schritten in 12 Positionen drehen.
Ziehen Sie den Sicherungsstift heraus und halten Sie diesen.
Drehen Sie den Handgriff in die gewünschte Position und lassen Sie den Sicherungsstift los, um ihn zu verriegeln.

Ablassen des Drucks
Torcflex-Schlüssel können entweder mit Co-Axial-Kupplungen oder Schraubkupplungen geliefert werden. Beim Co-Axial-System werden sowohl die Vorschub- als auch die Einzugsleitung mit einem einzelnen Anschluss verbunden. Beim Schraubkupplungs-System müssen die Vorschub- und die Einzugsleitung einzeln angeschlossen werden. Achten Sie vor dem Anschluss darauf, dass die Kupplungen sauber und frei von Schäden sind.

Stellen Sie vor dem Anschluss oder dem Trennen von Hydraulikkupplungen sicher, dass kein Restdruck in der Pumpe besteht.
Elektropumpen
Drücken Sie den Knopf an der Oberseite des Magnetventils mehrmals, um den Druck abzulassen.
Druckluftpumpen
Drücken Sie die Stopp-Taste [0] an der Fernsteuerung, um die Pumpe anzuhalten.
Drücken und halten Sie die Stopp-Taste [0] und drücken Sie mehrmals die Vorlauf-Taste [1], um das Magnetventil mehrere Zyklen durchlaufen zu lassen.
1
Vorlauf-Taste
0
Stopp-Taste
Alle Kupplungen sollten sich einfach per Hand anschließen und trennen lassen. Überprüfen Sie sie anderenfalls auf Schäden oder Restdruck im System.
Systemanschluss – Co-Axial-Kupplung
Das Co-Axial-System verbindet sowohl die Vorschub- als auch Einzugsleitung des Druckluftkreislaufs mit einer einzelnen Kupplung.

Anschluss des Schlauchs an die Pumpe
Halten Sie den Pumpenrahmen (1), um Bewegungen der Pumpe während des Anschlusses zu vermeiden. Richten Sie den Schlauchnippel (2) an der Pumpenkupplung aus.
Drücken Sie den Schlauchnippel und die Pumpenkupplung kräftig zusammen (2). Wenn die Verbindung hergestellt wurde, ist ein Klickgeräusch zu hören.
Der Rändelbund an der Pumpenkupplung muss beim Anschluss nicht zurückgezogen werden.
Ziehen Sie am Schlauch (3), um sicherzustellen, dass die Verbindung korrekt hergestellt wurde.

Anschluss des Schlauchs an den Schlüssel
Halten Sie den schwenkbaren Verteiler an der der Kupplung (1) gegenüberliegenden Seite. Richten Sie die Schlauchkupplung am Schlüsselnippel (2) aus.
Drücken Sie den Schlüsselnippel und die Schlauchkupplung fest zusammen. Wenn die Verbindung hergestellt wurde, ist ein Klickgeräusch zu hören.
Der Rändelbund an der Schlauchkupplung muss beim Anschluss nicht zurückgezogen werden.
Ziehen Sie am Schlauch (3), um sicherzustellen, dass die Verbindung korrekt hergestellt wurde.

Trennen des Schlauchs von der Pumpe

Die Co-Axial-Kupplung verfügt über eine Sicherheitseinrichtung, um ein versehentliches Trennen während der Verwendung zu vermeiden. Machen Sie sich vor der Verwendung des Geräts mit dem Verfahren zum Trennen des Schlauchs vertraut.
Halten Sie den Pumpenrahmen, um Bewegungen der Pumpe während des Trennens zu vermeiden.
Drücken Sie den Schlauchnippel in Richtung der Pumpe (Abbildung 1), bis sich der Spalt zwischen dem Rändelbund und dem Nippel schließt (Abbildung 2).
Während Sie die oben beschriebene Position halten, schieben Sie den Rändelbund in Richtung der Pumpe (Abbildung 3).
Ziehen Sie den Schlauch von der Pumpe weg, sodass die Verbindung sich automatisch öffnet (Abbildung 4).

Werden die Verbindungen nicht zusammengedrückt und in dieser Position gehalten, kann sich der Rändelbund nicht bewegen und die Kupplungen können nicht getrennt werden. Dies ist eine Sicherheitseinrichtung, um ein versehentliches Trennen zu vermeiden.


Trennen des Schlauchs vom Schlüssel

Die Co-Axial-Kupplung verfügt über eine Sicherheitseinrichtung, um ein versehentliches Trennen während der Verwendung zu vermeiden. Machen Sie sich vor der Verwendung des Geräts mit dem Verfahren zum Trennen des Schlauchs vertraut.
Halten Sie den schwenkbaren Verteiler an der der Kupplung gegenüberliegenden Seite.
Drücken Sie den Schlauch in Richtung des Schlüssels (Abbildung 1), bis sich der Spalt zwischen dem Rändelbund und dem Nippel schließt, wie in (Abbildung 2) gezeigt.
Während Sie die oben beschriebene Position halten, ziehen Sie den Rändelbund vom Schlüssel weg (Abbildung 3).
Ziehen Sie den Schlauch vom Schlüssel weg, sodass die Verbindung sich automatisch öffnet (Abbildung 4).

Werden die Verbindungen nicht zusammengedrückt und in dieser Position gehalten, kann sich der Rändelbund nicht bewegen und die Kupplungen können nicht getrennt werden. Dies ist eine Sicherheitseinrichtung, um ein versehentliches Trennen zu vermeiden.


Systemanschluss – Schraubkupplung
Pumpen und Schläuche von Atlas Copco verfügen über für den Betrieb von Torcflex-Schlüsseln vorkonfigurierte Kupplungen, wie unten dargestellt.

Wenn Sie nicht von Atlas Copco stammende Ausrüstung zum Betrieb von Torcflex-Schlüsseln verwenden, stellen Sie sicher, dass die Kupplungen wie nachfolgend gezeigt konfiguriert sind.

1 | Schraubenschlüssel | 2 | Pumpe |
Achten Sie darauf, dass alle Kupplungen korrekt angeschlossen sind, ohne Spalte zwischen den Manschetten und den Anschlüssen. Verwenden Sie niemals Schraubenschlüssel oder andere Werkzeuge zum Anziehen oder Lösen von Kupplungen.


Achten Sie darauf, dass die Kupplungen eingerastet und fest verschraubt sind.
Verwenden Sie niemals zwei Doppel-Hydraulikschläuche zwischen der Pumpe und dem Werkzeug. Um eine Fehlfunktion des Werkzeugs zu vermeiden, vertauschen Sie die Kupplungen nicht. Versuchen Sie nicht, unter Druck stehende Kupplungen anzuziehen oder zu lösen.
Bedienung
Ergonomie-Richtlinien
Betrachten Sie Ihren Arbeitsplatz, während Sie diese Liste mit allgemeinen Ergonomie-Richtlinien lesen, und versuchen Sie, Bereiche zu identifizieren, in denen Verbesserungen in Bezug auf Körperhaltung, Positionierung der Komponenten oder Arbeitsumgebung möglich sind.
Legen Sie regelmäßige Pausen ein und wechseln Sie regelmäßig die Arbeitshaltung.
Passen Sie den Bereich um Ihre Arbeitsstation Ihren Anforderungen und den auszuführenden Arbeiten an.
Positionieren Sie Teile und Werkzeuge so, dass statische Belastungen möglichst vermieden werden und sich sämtliche Arbeitsmittel bequem erreichen lassen.
Verwenden Sie an Ihrer Arbeitsstation für die Aufgabe geeignete Tische, Stühle oder andere Gegenstände.
Vermeiden Sie während der Ausführung von Montagearbeiten Körperhaltungen über Schulterhöhe oder mit statischer Halteposition.
Wenn Sie über Schulterhöhe arbeiten müssen, verringern Sie die auf die statischen Muskeln wirkende Belastung durch Verringerung des Werkzeuggewichts. Setzen Sie hierzu beispielsweise Drehmomentarme, Schlauchaufroller oder Gewichtsausgleicher ein. Sie können die auf die statischen Muskeln ausgeübte Belastung auch reduzieren, indem Sie das Werkzeug nah am Körper halten.
Legen Sie häufig Pausen ein.
Vermeiden Sie extreme Arm- oder Handgelenkhaltungen, insbesondere während Arbeiten, bei denen ein gewisser Kraftaufwand erforderlich ist.
Richten Sie Ihren Arbeitsplatz so in Ihrem Sichtfeld ein, dass nur minimale Augen- und Kopfbewegungen erforderlich sind.
Verwenden Sie zur Ausführung Ihrer Arbeit eine angemessene Beleuchtungen.
Wählen Sie ein zur Ausführung Ihrer Arbeit angemessenes Werkzeug aus.
Tragen Sie in lauten Umgebungen einen entsprechenden Gehörschutz.
Verwenden Sie hochwertige Einsätze und Kleinteile, um eine übermäßige Vibrationsbelastung möglichst zu vermeiden.
Betriebsanleitung
Sicherheit während des Betriebs
Betriebsdruck
Alle Systemkomponenten müssen für eine dynamische Druckbelastung von 700 bar (10.000 psi) ausgelegt sein. Werden nicht von Atlas Copco stammende Pumpen und Schläuche verwendet, stellen Sie sicher, dass die Ausrüstung für den Betrieb mit Schraubenschlüsseln von Atlas Copco geeignet ist.
Pumpen-Betriebsdruck:
Maximaler Vorschubdruck: 700 bar (10.000 psi)
Maximaler Einzugsdruck: 120 bar (1.740 psi)
Einstellen des Solldrehmoments
Sobald der Schlüssel eingerichtet und mit einer Pumpe verbunden wurde, müssen Sie das Solldrehmoment einstellen. Um das Drehmoment festzulegen, müssen Sie das Ventil für den Ausgangsdruck der Pumpe einstellen.
Den Druck, mit dem das korrekte Drehmoment erreicht wird, können Sie dem Kalibrierdatenblatt oder der Drehmoment/Druck-Umrechnungstabelle entnehmen.
Lösen Sie die Sperrmutter am Druckregelventil und anschließend die Rändelschraube, bis diese sich frei drehen lässt. Entfernen Sie die Rändelschraube nicht.
Schließen Sie die Pumpe an eine geeignet Stromversorgung an.
Starten Sie bei frei beweglichem, also nicht an einem Befestigungselement anliegendem Schlüssel die Pumpe, indem Sie die Vorlauf-Taste [1] an der Fernsteuerung einmal drücken und loslassen.
Drücken und halten Sie die Vorlauf-Taste [1].
Der Kolben des Schlüssels wird bis zum vollen Hub ausgefahren und es baut sich Druck auf.
Achten Sie auf den am Manometer angezeigten Druck. Halten Sie die Vorlauf-Taste [1] weiterhin gedrückt und ziehen Sie die Rändelschraube fest oder lösen Sie diese, bis die Anzeige den Sollwert erreicht.
Lassen Sie die Vorlauf-Taste [1] los.
Der Kolben des Schlüssels wird eingezogen.
Drücken und halten Sie die Vorlauf-Taste [1] erneut. Stellen Sie sicher, dass der Sollwert erreicht wird, und lassen Sie die Vorlauf-Taste [1] anschließend wieder los.
Halten Sie die Rändelschraube in Position und verriegeln Sie das Ventil mit der Sperrmutter.
Nachdem das Ventil verriegelt wurde, drücken und halten Sie die Vorlauf-Taste [1] erneut und vergewissern Sie sich, dass auch weiterhin der Sollwert erreicht wird. Ggf. einstellen.
Das System ist nun einsatzbereit.
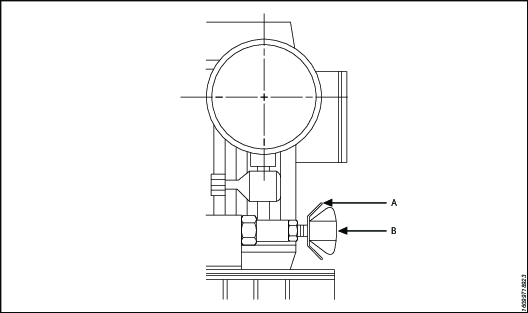
A | Rändel-Sicherungsmutter | B | T-Handgriff |

1 | Vorlauf-Taste | 0 | Stopp-Taste |
Betrieb des Flachschlüssels
Voraussetzungen
Tragen Sie persönliche Schutzausrüstung: Es muss korrekte und geeignete Schutzausrüstung getragen werden.
Führen Sie vor der Verwendung des Werkzeugs eine aufgabenbasierte Risikobewertung durch.
Kontrollieren Sie das Werkzeug, das Netzteil, die Schläuche, Anschlüsse, Stromkabel und Zubehör regelmäßig auf sichtbare Schäden. Befolgen Sie stets die Anweisungen zur Wartung von Werkzeug und Pumpe.
Wählen Sie die passende flach ausgeführte Sperrklinkenverbindung aus und setzen Sie sie in das Werkzeug ein. Werkzeugbetrieb sowie Festziehen und Lösen von Schrauben werden durch die Position des Werkzeugs relativ zur Mutter/Schraube bestimmt.
Schließen Sie die Schläuche an: Stellen Sie sicher, dass alle Schlauchverbindungen sicher und korrekt hergestellt wurden. Stellen Sie sicher, dass die Schläuche frei von Mängeln sind.
Inbetriebnahme
Starten Sie das Werkzeug: Legen Sie das Werkzeug auf einer ebenen Fläche ab und schalten Sie die Pumpe ein. Drücken und halten Sie die Vorlauf-Taste [1] an der Fernsteuerung der Pumpe, bis das Werkzeug ein Klickgeräusch von sich gibt. Lassen Sie die Taste los und warten Sie auf den Klick des Werkzeugs. Wiederholen Sie den Vorgang.
Druckeinstellung: Drücken und halten Sie die Vorlauf-Taste [1] und drehen Sie den Druckregler langsam im Uhrzeigersinn, bis der korrekte Druck erreicht wurde.
Setzen Sie das Werkzeug auf der Mutter auf, die angezogen oder gelöst werden soll.
Durch den Antriebshub des Antriebskopfs wird die Sechskant-Sperrklinke (und damit die Mutter) immer in Richtung des Futters an der Vorderseite des Werkzeugs, also vom Reaktionspunkt weg, gedreht. Die flach ausgeführten Sperrklinkenverbindungen werden komplett mit einem langen Reaktionsblock geliefert. Dieser Reaktionsblock ist für eine Reaktion gegen eine benachbarte Mutter ausgelegt.
Die Sperrklinkenverbindung ist so konstruiert, dass der Reaktionsblock das Moment an eine benachbarte Mutter oder einen anderen geeigneten, sicheren Reaktionspunkt abgibt. Wenn ein solcher Reaktionspunkt nicht verfügbar ist, können Standard-Reaktionszubehör oder spezielle Reaktionsarme eingesetzt werden.
Achten Sie darauf, dass die Mutter der Werkzeuggröße entspricht.
Achten Sie darauf, während des Betriebs stets einen widerstandsfähigen Reaktionspunkt zu verwenden.
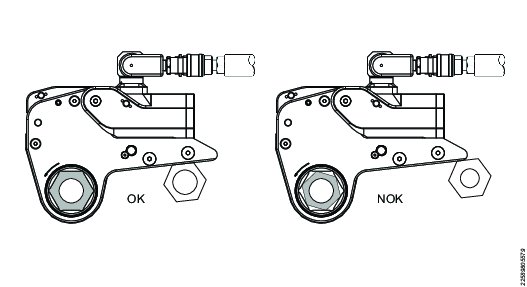
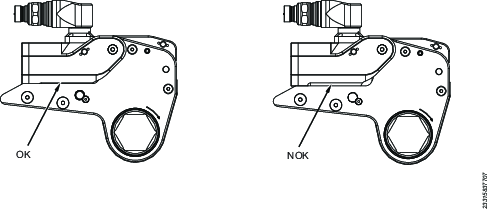
Knicken Sie Schläuche nicht ab und biegen Sie sie nicht übermäßig:
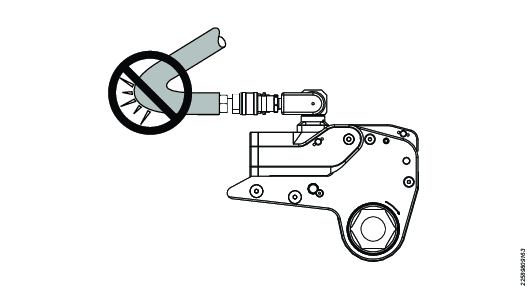
Schlagen Sie niemals auf den Schraubenschlüssel, um das Lösen zu unterstützen:

Überprüfen der Antriebsrichtung
Achten Sie vor der Verwendung des Schlüssels darauf, dass die Drehrichtung korrekt eingestellt ist. Die Richtung wird durch den Pfeil an der Oberseite des Werkzeugs angezeigt.

Der Reaktionsarm dreht sich in die dem Antrieb entgegengesetzte Richtung, bis er mit einem geeigneten Reaktionspunkt in Kontakt kommt.

1 | Lösen: gegen den Uhrzeigersinn Anziehen: im Uhrzeigersinn |
2 | Reaktionsarm |
3 | Richtungspfeil |
Wenn die Drehrichtung umgekehrt werden muss, muss der Antrieb abgenommen und auf der gegenüberliegenden Seite des Schraubers wieder installiert werden.
Festziehen
Setzen Sie das Werkzeug auf das zu verschraubende Befestigungselement auf. Drücken Sie das Werkzeug in Richtung der Wirkungsfläche, bis der Reaktionsarm mit einem geeigneten Reaktionspunkt in Kontakt kommt.
Die Gegenhaltestruktur muss widerstandsfähig genug sein, um der Reaktionskraft des Druckluftwerkzeugs widerstehen zu können.
Vermeiden Sie konische Oberflächen, da der Reaktionsarm abrutschen kann, was zu unerwünschten Belastungen und Instabilität des Werkzeugs führen kann.
Verwenden Sie keine losen Abstandsstücke, um eine Gegenhaltestruktur herzustellen. Ist der standardmäßige Reaktionsarm nicht geeignet, wenden Sie sich für Unterstützung an Atlas Copco.
Drücken Sie die Vorlauf-Taste [1] auf der Fernbedingung und lassen Sie diese wieder los, um die Pumpe zu starten.
Halten Sie das Werkzeug am Stützgriff und stellen Sie Folgendes sicher:
Die Sperrklinkenverbindung ist vollständig am zu verschraubenden Befestigungselement eingerastet.
Der Reaktionsarm liegt fest an der Gegenhaltestruktur an.
Der Schlauch und die Kupplungen lassen sich frei bewegen und haben genügend Abstand zu umgebenden Strukturen.
Beachten Sie, dass Sie das Werkzeuggewicht halten müssen, während dieses eingezogen wird, insbesondere bei Über-Kopf-Anwendungen. Wird das Werkzeug nicht gehalten, kann es aus der Anwendungsposition herunterfallen.
Drücken und halten Sie die Vorlauf-Taste [1], damit der Antrieb sich dreht.
Wenn der Kolben das Ende des Hubs erreicht, geschieht Folgendes:
Die Reaktionsklinke gibt ein Klickgeräusch von sich.
Die Sperrklinkenverbindung hört auf sich zu drehen.
Der Druck baut sich bis zum eingestellten Druckwert auf.
Dies bedeutet nicht, dass die Schraube korrekt angezogen wurde, sondern lediglich, dass das Werkzeug den vollen Hub erreicht hat.
Wenn das Werkzeug den vollen Hub erreicht, halten Sie das Werkzeug und lassen Sie die Vorlauf-Taste [1] an der Fernsteuerung los. Das Werkzeug wird automatisch eingezogen. Wenn das Werkzeug vollständig eingezogen ist, gibt die Antriebsklinke ein Klickgeräusch von sich.
Das Werkzeug ist nun bereit für den nächsten Vorschub. Wiederholen Sie die Schritte 3-5, bis der Druck sich sofort bis zum Sollwert aufbaut und keine Bewegung des Befestigungselements zu sehen ist. Der Schlüssel ist zum Stillstand gekommen und das Befestigungselement ist korrekt verschraubt.
Sobald das Werkzeug zum Stillstand kommt, drücken Sie die Vorlauf-Taste [1] erneut, um sicherzustellen, dass das Befestigungselement sich nicht bewegt. Tut es dies nicht, ist der Verschraubungsvorgang abgeschlossen.
Gelegentlich kann das Werkzeug bei der Anwendung blockieren. Führen Sie zum Entfernen des Werkzeugs die folgenden Schritte durch:
Drücken und halten Sie die Vorlauf-Taste [1].
Sobald der Druck den Sollwert erreicht, drücken Sie die Hebel der Klinke per Hand nach vorne, um diese von der Sperrklinke zu lösen.
Halten Sie das Werkzeug fest, bevor Sie die Vorlauf-Taste an der Fernsteuerung loslassen.
Entfernen Sie das Werkzeug von der Anwendung.
Bewegen Sie die Klinkenhebel per Hand. Verwenden Sie keine Werkzeuge zum Bewegen der Hebel.
Drücken Sie die Stopp-Taste [0] auf der Fernbedingung, um die Pumpe anzuhalten.
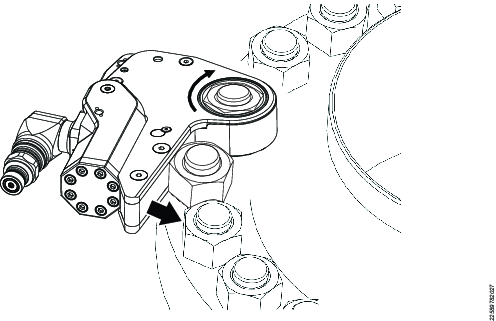
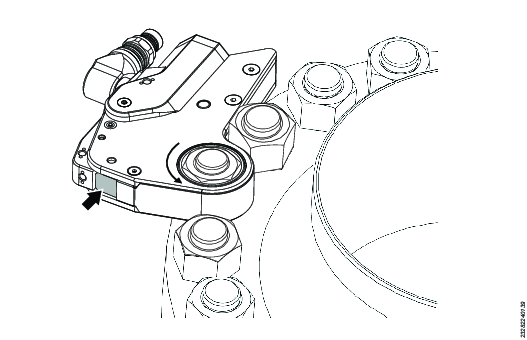
Lösen
Sind die Befestigungselemente stark verrostet oder wurden diese während des Betriebs hohen Temperaturen ausgesetzt, kann das Losbrechmoment mehr als das Doppelte des Anzugsdrehmoments betragen. Verwenden Sie zum Lösen ein größeres Werkzeug als zum Verschrauben. Um das Lösen zu erleichtern, entfernen Sie sämtlichen oberflächlichen Rost mit einer Drahtbürste und tragen Sie Schmieröl auf die Mutter, Schraube und Auflagefläche auf. Lassen Sie das Öl lange genug einwirken, bevor Sie versuchen, das Befestigungselement zu lösen.
Beim Lösen von Befestigungselementen kann es zu einer plötzlichen Freisetzung von Energie kommen, wenn das Befestigungselement losbricht. Hierbei kann es zu einer unerwarteten Stoßeinwirkung auf das Werkzeug kommen. Um die Antriebskomponenten zu schützen, überschreiten Sie beim Lösen 90 % des Maximaldrucks nicht. Wenn sich das Befestigungselement bei 90 % nicht lösen lässt, verwenden Sie nach Möglichkeit ein größeres Werkzeug.

Schlagen Sie niemals mit einem Hammer auf einen Schrauber oder einen Steckschlüssel, um den Lösevorgang zu unterstützen.

Stellen Sie den Drucksollwert auf 620 bar (9.000 psi) ein.
Setzen Sie das Werkzeug auf das zu lösende Befestigungselement auf. Drücken Sie das Werkzeug in Richtung der Wirkungsfläche, bis der Reaktionsarm mit einem geeigneten Reaktionspunkt in Kontakt kommt.
Die Gegenhaltestruktur muss widerstandsfähig genug sein, um der Reaktionskraft des Druckluftwerkzeugs widerstehen zu können.
Vermeiden Sie konische Oberflächen, da der Reaktionsarm abrutschen kann, was zu unerwünschten Belastungen und Instabilität des Werkzeugs führen kann.
Verwenden Sie keine losen Abstandsstücke, um eine Gegenhaltestruktur herzustellen. Ist der standardmäßige Reaktionsarm nicht geeignet, wenden Sie sich für Unterstützung an Atlas Copco.
Drücken Sie die Vorlauf-Taste [1] und lassen Sie diese wieder los, um die Pumpe zu starten.
Halten Sie das Werkzeug am Stützgriff und stellen Sie Folgendes sicher:
Die Sperrklinkenverbindung ist vollständig am zu lösenden Befestigungselement eingerastet.
Der Reaktionsarm liegt fest an der Gegenhaltestruktur an.
Der Schlauch und die Kupplungen haben genügend Abstand zu umgebenden Strukturen und lassen sich frei bewegen.
Beachten Sie, dass Sie das Werkzeuggewicht halten müssen, während dieses eingezogen wird, insbesondere bei Über-Kopf-Anwendungen. Wird das Werkzeug nicht gehalten, kann es aus der Anwendungsposition herunterfallen.
Drücken und halten Sie die Vorlauf-Taste [1], damit der Antrieb sich dreht.
Der Druck baut sich auf, bis das Losbrechmoment erreicht wird. Anschließend fällt der Druck ab, wenn der Antrieb sich dreht und das Befestigungselement gelöst wird.
Wenn der Kolben das Ende des Hubs erreicht, geschieht Folgendes:
Die Reaktionsklinke gibt ein Klickgeräusch von sich.
Die Sperrklinkenverbindung hört auf sich zu drehen.
Der Druck baut sich bis zum eingestellten Sollwert auf.
Dies bedeutet nicht, dass die Schraube vollständig gelöst wurde, sondern lediglich, dass das Werkzeug den vollen Hub erreicht hat.
Wenn das Werkzeug den vollen Hub erreicht, halten Sie das Werkzeug und lassen Sie die Vorlauf-Taste [1] an der Fernsteuerung los. Das Werkzeug wird automatisch eingezogen. Wenn das Werkzeug vollständig eingezogen ist, gibt die Antriebsklinke ein Klickgeräusch von sich.
Das Werkzeug ist nun bereit für den nächsten Vorschub. Wiederholen Sie die Schritte 4-6, bis das Befestigungselement vollständig gelöst wurde.
Drücken Sie die Stopp-Taste [0] auf der Fernbedingung, um die Pumpe anzuhalten.
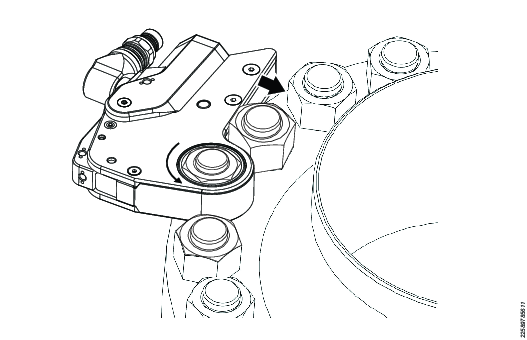
Wartung
Wartungsanweisungen
Empfehlungen für Instandhaltung und Wartung

Tragen Sie stets schlagfeste Schutzbrillen und Gesichtsschutz, wenn Sie mit dem Werkzeug arbeiten, es warten oder reparieren, Zubehör austauschen oder sich in der Nähe der Arbeiten am oder mit dem Werkzeug aufhalten.
Alle Untersuchungs-, Wartungs- oder Reparaturarbeiten sollten nur durchgeführt werden, wenn das komplette System druckfrei ist.
Kontrollieren Sie im Interesse einer optimalen Leistung Werkzeug, Netzteil, Schläuche, Anschlüsse, Stromkabel und Zubehör regelmäßig auf sichtbare Schäden. Befolgen Sie stets die Anweisungen zur Wartung von Werkzeug und Pumpe.
Hinweise zu den Wartungsintervallen
Regelmäßiges Schmieren und Überholungen werden empfohlen, um sicherzustellen, dass der Schlüssel in gutem Betriebszustand bleibt. Es können kürzere Wartungsintervalle notwendig sein, wenn das Werkzeug bei hohem Drehmoment, hoher Zyklusrate oder langen Verschraubungszeiten eingesetzt wird. Falls der Schlüssel nicht einwandfrei funktioniert, sollte er unverzüglich zur Inspektion gesendet werden.
Die folgenden Wartungsintervalle dienen lediglich als Orientierungshilfe. Jeder Anwendungsfall ist einzigartig, es liegt daher in der Verantwortung des Endnutzers, eine geeignete Wartung im Einklang mit den Arbeitsbedingungen und der Verwendung durchzuführen.
Leichte Anwendungen
Beispiel: Unregelmäßige Verwendung bei niedrigem Druck, <40 % Leistung.
Schmierung: alle 6 Monate
Überholung: alle 12 Monate
Normaler Betrieb
Beispiel: Regelmäßige Verwendung, <80 % Leistung.
Schmierung: alle 3 Monate
Überholung: alle 12 Monate, einschließlich Austausch des Antriebsstifts. Siehe Abschnitt Montage der Sperrklinkenverbindung.
Schwerlastbetrieb
Beispiel: Konstante Verwendung bei verschiedenen Drücken; Nutzung mit >80 % Leistung; regelmäßiger Einsatz zum Lösen korrodierter Schrauben.
Schmierung: monatlich
Überholung: alle 6 Monate, einschließlich Austausch des Antriebsstifts und der Antriebsklinke. Siehe Abschnitt Montage der Sperrklinkenverbindung.
Einsatz in ATEX-Zonen
Halten Sie ungeachtet der tatsächlichen Beanspruchung die Leitlinien für den Schwerlastbetrieb ein, um das Risiko eines Komponentenausfalls während der Verwendung deutlich zu senken. Falls der Schlüssel Anzeichen einer Fehlfunktion aufweist, entfernen Sie diesen aus der ATEX-Zone, bevor Sie nach ihrer Ursache suchen. Versuchen Sie NICHT, den Schlüssel in der ATEX-Zone zu reparieren. Durch die Nichteinhaltung der Wartungsempfehlungen wird die Wahrscheinlichkeit eines mechanischen Versagens und somit das Risiko mechanischer Funkenbildung erhöht.
Hochdruck-Schlauch
Schläuche sollten regelmäßig demontiert werden. Die Anschlüsse und Adapter müssen auf Verschleiß und Beschädigungen überprüft werden. Sollten während der Wartung Verschleiß oder Beschädigungen festgestellt werden, so muss das betroffene Teil entfernt und ausgetauscht werden.
Überprüfen Sie die Schläuche auf Ölspuren, die auf einen schleichenden Austritt am Schlauch durch ein kleines Leck hinweisen können. Achten Sie besonders auf die Stahlpressungen an beiden Enden des Schlauches, da diese am häufigsten von Öllecks betroffen sind. Wird ein Leck mit schleichendem Austritt entdeckt, tauschen Sie den Schlauch aus.
Säubern Sie den Schlauch nach jeder Verwendung und rollen Sie ihn auf. Wischen Sie die Schläuche mit einem sauberen Tuch ab und sprühen Sie sie mit einem geeigneten Rostschutzöl wie Shell Ensis oder Castrol Rustillo ein.
Biegen Sie den Schlauch nicht über Hindernisse und ziehen Sie nicht am Schlauch, um daran angeschlossene Gerätschaften zu bewegen.
Führen Sie alle zwei Jahre einen Drucktest der Schläuche durch und ersetzen Sie die Schlauchsätze nach sechs Jahren.
Vorbeugende Wartung
Um das hydraulische Drehmomentschlüsselsystem in einem guten Betriebszustand zu halten, führen Sie die folgenden Wartungsschritte nach jedem Nutzungszeitraum durch.
Wischen Sie alle äußeren Oberflächen ab und führen Sie eine Sichtprüfung des Werkzeugs auf Anzeichen von Beschädigungen durch. Untersuchen Sie solche gegebenenfalls.
Überprüfen Sie alle hydraulischen Anschlüsse und Verbindungen auf Anzeichen hydraulischer Lecks. Untersuchen Sie solche gegebenenfalls.
Stellen Sie sicher, dass alle Hydraulikkupplungen sauber und frei von Verunreinigungen sind.
Überprüfen Sie die gesamte Länge des Schlauchs; achten Sie auf Risse oder Verschleiß. Achten Sie besonders auf die Stahlpressungen an den Enden sowie auf Anzeichen von Leckagen.
Befindet sich das Gerät in einem guten Betriebszustand, sprühen Sie es mit einem geeigneten Rostschutzöl, wie etwa Shell Ensis oder Castrol Rustillo, ein und bewahren Sie es einsatzbereit für die nächste Verwendung auf.
Anweisungen zur Überholung
Schließen Sie den Schlüssel an eine Pumpe an.
Führen Sie eine Druckprüfung durch, um sicherzustellen, dass alle Mechanismen wie erwartet funktionieren.
Untersuchen Sie sämtliche Fehlfunktionen oder Hydrauliklecks.
Lassen Sie den Druck aus dem System ab und trennen Sie alle Kupplungen.
Demontieren Sie den Schlüssel. Siehe Abschnitt Demontage-/Montageanweisungen.
Tauschen Sie alle Dichtungen und Federn aus.
Tauschen Sie den Antriebsstift aus.
Tauschen Sie alle sonstigen Komponenten aus, die Anzeichen von Beschädigungen oder Verschleiß aufweisen.
Schmieren Sie den Schlüssel und montieren Sie diesen wieder. Siehe Abschnitt Demontage-/Montageanweisungen.
Führen Sie eine Druckprüfung durch und stellen Sie sicher, dass alle Mechanismen wie erwartet funktionieren.
Kalibrieren Sie den Schlüssel und stellen Sie sicher, dass die Drehmomentleistung im erwarteten Bereich liegt.
Schmieranweisungen
Schmieranleitung
Antriebskomponenten | Molykote 1000 |
Dichtungen | Rocol Sapphire Aqua-Sil |
Befestigungselemente | Loctite 243 |
Konische Hydraulikgewinde | Loctite 577 |
Schmierung
Um die Schlüssel in einem guten Betriebszustand zu halten, schmieren Sie die Antriebskomponenten regelmäßig zwischen den Wartungsintervallen.
Demontage vor dem Schmieren:
Entfernen Sie die Schrauben der Seitenplatte und die Seitenplatte [1].
Entfernen Sie die Antriebsbaugruppe [2].

Führen Sie die folgenden Maßnahmen während der Schmierung durch:
Überprüfen Sie den Antriebsstift und die Federn auf Anzeichen von Verschleiß oder Beschädigungen. Tauschen Sie den Antriebsstift und die Federn gegebenenfalls aus.
Überprüfen Sie die Kanten der Sperrklinkenzähne auf Anzeichen von Beschädigungen. Tauschen Sie die Sperrklinke gegebenenfalls aus.
Überprüfen Sie die Zähne der Antriebsklinke auf Anzeichen von Beschädigungen. Tauschen Sie die Antriebsklinke gegebenenfalls aus.
Überprüfen Sie die Federn der Antriebsklinke auf Anzeichen von Beschädigungen. Tauschen Sie die Federn gegebenenfalls aus.
Schmieren Sie die schattierten Bereiche mit Molykote 1000.
Der Montagevorgang entspricht dem für die Demontage, nur in umgekehrter Reihenfolge.
Demontage-/Montageanweisungen
Demontage des Antriebskopfs
Lösen Sie die Halteschrauben der Schwenktülle.
Entfernen Sie die Schwenktülle.
Positionieren Sie die Öl-Auslassöffnungen über einem geeigneten Behälter.
Ziehen Sie die Kolbenstange bis zum Anschlag heraus.
Drücken Sie die Kolbenstange zurück.
Das Öl des Werkzeugs läuft aus den Auslassöffnungen heraus.
Entfernen Sie die Schrauben des Endverschlusses sowie den Endverschluss.
Ziehen Sie die Kolbenstange bis zum Anschlag heraus. Spannen Sie das Endstück der Kolbenstange in einen Schraubstock ein.
Lösen Sie das Endstück der Kolbenstange mit einem Steckschlüssel und einer Verlängerung. Schrauben Sie das Endstück der Kolbenstange ab.
Ziehen Sie den Kolben aus der Bohrung im Gehäuse.


Demontage der Sperrklinkenverbindung
Der Demontagevorgang entspricht dem für die Montage, nur in umgekehrter Reihenfolge. Siehe Abschnitt Montage der Sperrklinkenverbindung.
Montage des Antriebskopfs
Schmieren Sie die Lippendichtung mit Aqua-Sil und setzen Sie sie in das Gehäuse ein [1].
Schmieren Sie den O-Ring und die Lippendichtung mit Aqua-Sil und installieren Sie diese am Kolben [2].
Schmieren Sie den O-Ring mit Aqua-Sil und installieren Sie diesen am Endverschluss [3].
Tragen Sie eine geringe Menge Hydrauliköl auf die Bohrung am Gehäuse auf.
Schieben Sie den Kolben in das Gehäuse und drücken Sie ihn bis zum Ende der Bohrung am Gehäuse.
Tragen Sie Loctite 277 auf alle Gewinde am Endstück der Kolbenstange auf und schrauben Sie dieses auf die Kolbenstange auf.
Spannen Sie das Endstück der Kolbenstange in einen Schraubstock ein und ziehen Sie die Kolbenstange mithilfe eines Steckschlüssels und einer Verlängerung an.
Modell
Installationsdrehmoment (Nm)
Steckschlüsselgröße
TFX02
12
9/16 Zoll
TFX04
40
19 mm
TFX08
45
24 mm
TFX14
80
1-1/8 Zoll
TFX18
90
1-1/8 Zoll
TFX30
100
38 mm
Setzen Sie den Endverschluss in das Gehäuse ein.
Tragen Sie Loctite 243 auf die Endverschlussschrauben auf; schrauben Sie diese in das Gehäuse ein und ziehen Sie sie mit dem korrekten Installationsdrehmoment fest.
Modell
Sechskantschlüssel (mm)
Drehmoment (Nm)
TFX02
4
11
TFX04
5
18
TFX08
6
40
TFX14
8
70
TFX18
8
80
TFX30
10
125
Installieren Sie den schwenkbaren Verteiler. Siehe Abschnitt Montage des schwenkbaren Verteilers.
Entfetten Sie die Gewinde am Befestigungsstift und tragen Sie Loctite 243 auf das Innengewinde auf. Schrauben Sie die beiden Teile des Befestigungsstifts zusammen und ziehen Sie sie mit dem korrekten Installationsdrehmoment fest.
Modell
Sechskantschlüssel (mm)
Drehmoment (mm)
TFX02
4
11
TFX04
5
18
TFX08
6
18
TFX14
6
18
TFX18
6
18
TFX30
6
18



Montage des schwenkbaren Verteilers
Der Torcflex-Schlüssel kann mit einem schwenkbaren Verteiler in zwei Ausführungen ausgestattet werden. Befolgen Sie die folgenden Anweisungen für den Austausch oder Wechsel des Verteilers, falls erforderlich.
Verwenden Sie Loctite 243 als Sicherungslack, um ein Lösen bei der Montage zu vermeiden.
Modell | Sechskantschlüssel (mm) | Drehmoment (Nm) |
---|---|---|
TFX02 | 4 | 11 |
TFX04–TFX30 | 5 | 18 |
Installation eines co-axialen schwenkbaren Verteilers

Installation eines schwenkbaren Verteilers mit doppelter Leitung

Nachfüllen von Öl
Schließen Sie den Schlüssel mithilfe eines Schlauchs an eine Pumpe an.
Drücken Sie die Vorlauf-Taste [1] und lassen Sie diese wieder los, um die Pumpe zu starten.
Die Einzugsseite des Hydraulikzylinders wird automatisch gefüllt und drückt den Kolben in die Ausgangsposition. Von der Vorschubseite des Kolbens aus wird Luft in den Schlauch gedrückt.
Drücken Sie die Stopp-Taste [0], um die Pumpe anzuhalten. Drücken Sie anschließend den Knopf am Wegeventil, um den Druck aus der Einzugsleitung abzulassen.
Trennen Sie den Schlauch und lassen Sie die Luft aus dem Schlauch ab, wie nachfolgend beschrieben:
Für Co-Axial-Schläuche: Starten Sie die Pumpe bei getrenntem Schlüssel und halten Sie sie nach zehn Sekunden wieder an. Hierdurch zirkuliert das Öl zwischen den Vorschub- und Einzugsleitungen, wodurch der Schlauch entlüftet wird.
Für Schraubkupplungs-Schläuche: Schrauben Sie die freien Enden des Schlauchs zusammen, um einen Kreislauf zu bilden. Starten Sie die Pumpe und halten Sie sie nach zehn Sekunden wieder an. Hierdurch zirkuliert das Öl zwischen den Vorschub- und Einzugsleitungen, wodurch der Schlauch entlüftet wird.
Schließen Sie den Schlauch wieder an den Schlüssel an.
Fahren Sie den Kolben zehnmal aus und ein.
Halten Sie die Pumpe an.
Trennen Sie den Schlauch und wiederholen Sie das Entlüftungsverfahren.
Druckprüfung
Schließen Sie den Schlüssel an die Pumpe an.
Drücken Sie die Vorlauf-Taste [1] und lassen Sie diese wieder los, um die Pumpe zu starten. Warten Sie zehn Sekunden und achten Sie auf Anzeichen von Öllecks.
Drücken und halten Sie die Vorlauf-Taste und beaufschlagen Sie das Werkzeug mit einem Druck von 690 bar (10.000 psi). Halten Sie den Kopf zehn Sekunden gedrückt und achten Sie auf Anzeichen von Öllecks.
Lassen Sie die Taste los und führen Sie die Druckbeaufschlagung drei weitere Male durch, wobei jedes Mal auf Anzeichen von Öllecks geachtet werden muss.
Montage der Sperrklinkenverbindung
Bringen Sie das obere Abstandsstück, das Gegenhalte-Abstandsstück und den Stift der Reaktionsklinke mithilfe der Schrauben an der Seitenplatte an. Tragen Sie Loctite 243 auf die Schrauben auf und ziehen Sie diese fest.
Modell
Kleine Schraube Sechskantantrieb
Große Schraube Sechskantantrieb
Größe
Drehmoment (Nm)
Größe
Drehmoment (Nm)
TL02
1/8 Zoll
6
5/32 Zoll
12
TL04
5/32 Zoll
12
3/16 Zoll
16
TL08
3/16 Zoll
16
7/32 Zoll
20
TL14
7/32 Zoll
25
5/16 Zoll
35
TL18
7/32 Zoll
40
5/16 Zoll
50
TL30
5/16 Zoll
45
3/8 Zoll
55
Schmieren Sie die Seitenplatte und den Stift der Reaktionsklinke mit Molykote 1000. Montieren Sie anschließend das Futter und die Reaktionsklinke mit den Abstandsstücken und der Feder.
Tragen Sie Loctite 243 auf die Futterschraube auf und ziehen Sie diese am Gegenhalte-Abstandsstück fest.
Schmieren Sie die Antriebsplatte und die Lagerdurchmesser der Sperrklinke mit Molykote 1000. Installieren Sie diese anschließend an der Seitenplatte.
Führen Sie die Sperrklinke durch die Antriebsplatte und in die Seitenplatte ein.
Legen Sie die Federstifte [2×] in die Antriebsplatte ein.
Montieren Sie die Antriebsklinken [2×], die Feder und die Federführung.
Installieren Sie den Antriebsstift und die Feder.
Schmieren Sie beide Seiten der zweiten Antriebsplatte mit Molykote 1000. Richten Sie die Bohrungen an den Federstiften aus und drücken Sie die Federstifte anschließend in ihre Position. Achten Sie darauf, dass die Bohrungen der Antriebsklinke ausgerichtet bleiben.
Achten Sie darauf, dass der Spalt zwischen den Antriebsplatten parallel ist und über einen gleichmäßigen Abstand verfügt und dass die Federn für eine korrekte Funktion der Antriebsklinken am Stift eingehakt sind.
Überprüfen Sie, ob die Antriebsklinken wie erwartet funktionieren: halten Sie die Sperrklinke und schieben Sie die Antriebsplatten an.
Beide Antriebsklinken sollten sich über den Sperrklinkenzahn bewegen und mit einem Klickgeräusch wieder einrasten. Wenn die Antriebsklinken steckenbleiben, überprüfen Sie, ob der Spalt zwischen den Antriebsplatten korrekt ist.
Schmieren Sie die Bohrung und die Innenfläche der Seitenplatte mit Molykote 1000. Ziehen Sie die Seitenplatte über die Sperrklinke und richten Sie die Schraubenlöcher in einer Linie aus. Tragen Sie Loctite 243 auf die Schrauben auf und ziehen Sie diese wie zuvor fest.
Führen Sie den Haltestift durch beide Seitenplatten ein. Richten Sie den Stiftausschnitt am Schraubenloch aus und installieren Sie anschließend die Reibscheibe und die Schraube. Stellen Sie das Drehmoment an der Schraube ein, um die korrekte Reibung gegen den Stift sicherzustellen.











Montageprüfung
Bringen Sie den Antriebskopf an der Sperrklinkenverbindung an. Siehe jeweils Abschnitt Installation der TL-Sperrklinkenverbindung oder Installation der RL-Sperrklinkenverbindung.
Drehen Sie die Sperrklinke und achten Sie darauf, dass die Antriebsklinke und die Reaktionsklinken sich wie erwartet bewegen.
Schließen Sie den Schlüssel an eine Pumpe und einen Schlauch an.
Fahren Sie den Schlüssel aus und ein; achten Sie darauf, dass die Sechskant-Sperrklinke sich mit jedem Zyklus nach vorne bewegt.
Kalibrieren Sie den Schlüssel als abschließende Prüfung, um sicherzustellen, dass die Drehmomentleistung im erwarteten Bereich liegt.
Störungshilfe
Störungshilfe
Symptom | Mögliche Ursache | Erforderliche Maßnahme |
---|---|---|
Der Schlüssel fährt nicht aus. |
|
|
Der Schrauber wird nicht eingezogen. |
|
|
Der Schlüssel fährt nicht aus, das Manometer zeigt jedoch Druck an. |
|
|
Der Schlüssel läuft im Rückwärtslauf (nur bei Schraubkupplungen). |
|
|
Im Schlüssel baut sich kein Druck auf. |
|
|
Der Schlüssel läuft nur langsam. |
|
|
Das Werkzeug ist in der Anwendung blockiert. |
|
|
Die Sperrklinke führt keine aufeinanderfolgenden Hübe aus. |
|
|
Die Sperrklinke springt während des Ausfahrhubs. |
|
|
Keine Anzeige am Manometer, der Schlüssel ist jedoch betriebsfähig. |
|
|
Der Schlauch lässt sich nur schwer am Schlüssel oder an der Pumpe anschließen. |
|
|
Am Futter tritt Öl aus. |
|
|
Die Schwenktülle oder die Co-Axial-Kupplung ist heiß. |
|
|
Nach dem Trennen der Kupplung tritt aus dieser Öl aus. |
|
|
Recycling
Umweltschutzbestimmungen
Nachdem ein Produkt seinen Zweck erfüllt hat, muss es ordnungsgemäß recycelt werden. Zerlegen Sie das Produkt und recyceln Sie die Komponenten gemäß örtlicher Vorschriften.