ETP TBP-S131-150-13
Battery-Powered Nutrunner
Produktinformation
Allgemeine Informationen
Sicherheitsbezogene Signalwörter
Die sicherheitsbezogenen Signalworte Gefahr, Warnung, Vorsicht und Hinweis haben folgende Bedeutung:
GEFAHR | GEFAHR weist auf eine gefährliche Situation hin, die bei Nichtvermeidung zu schweren Verletzungen mit möglicher Todesfolge führen wird. |
WARNUNG | WARNUNG weist auf eine gefährliche Situation hin, die bei Nichtvermeidung zu schweren Verletzungen mit möglicher Todesfolge führen könnte. |
ACHTUNG | VORSICHT weist bei Verwendung mit dem Sicherheitswarnsymbol auf eine gefährliche Situation hin, die bei Nichtvermeidung zu leichten oder mittelschweren Verletzungen führen könnte. |
HINWEIS | Ein HINWEIS wird für Situationen verwendet, die sich nicht auf eine mögliche Verletzungsgefahr beziehen. |
Garantie
Die Produktgarantie verfällt 12+1 Monate nach dem Versand aus dem Distributionszentrum von Atlas Copco.
Normaler Verschleiß von Teilen wird nicht von der Garantie abgedeckt.
Unter normalem Verschleiß versteht man, dass während der für diesen Zeitraum typischen Standardwerkzeugwartung Teile ausgetauscht oder Einstellungen / Verbesserungsarbeiten durchgeführt werden müssen (ausgedrückt in Zeit, Betriebsstunden, oder anderweitig).
Die Produktgarantie stützt sich auf einen korrekten Einsatz, Wartung und Reparatur des Werkzeugs und seiner Bestandteile.
Schäden an Teilen, die als Folge einer unzureichenden Wartung oder eines falschen Einsatzes durch andere Parteien als Atlas Copco oder deren zertifizierten Service-Partner während der Garantiezeit verursacht werden, sind nicht durch die Garantie gedeckt.
Um eine Beschädigung oder Zerstörung von Werkzeugteilen zu vermeiden, warten Sie das Werkzeug entsprechend der empfohlenen Wartungspläne und befolgen Sie die richtigen Anweisungen.
Garantiereparaturen werden nur in Atlas Copco-Werkstätten oder von einem zertifizierten Service-Partner ausgeführt.
Atlas Copco bietet eine erweiterte Garantie und eine vorbeugende Wartung nach dem neuesten Stand der Technik durch seine ToolCover-Verträge. Weitere Informationen erhalten Sie von Ihrem lokalen Servicerepräsentanten.
Für Elektromotoren:
Die Garantie gilt nur dann, wenn der Elektromotor nicht geöffnet wurde.
Website
Informationen zu unseren Produkten, Zubehör, Ersatzteilen und Veröffentlichungen finden Sie auf der Internetseite von Atlas Copco.
Besuchen Sie: www.atlascopco.com.
ServAid
ServAid ist ein Portal, das ständig aktualisiert wird und technische Informationen bietet, wie z.B.:
Behörden- und Sicherheitsinformationen
Technische Daten
Installations-, Betriebs- und Wartungsanweisungen
Ersatzteillisten
Zubehör
Maßzeichnungen
Besuchen Sie: https://servaid.atlascopco.com.
Weitere technische Informationen erhalten Sie bei Ihrem Atlas Copco-Vertreter vor Ort.
Sicherheitsdatenblätter MSDS/SDS
In den Sicherheitsdatenblättern werden die von Atlas Copco vertriebenen chemischen Produkte beschrieben.
Weitere Informationen finden Sie auf der Internetseite von Atlas Copco unter www.atlascopco.com/sds.
Video Produktsicherheit für Drehschrauber
Erfahren Sie mehr zu den Sicherheitsmerkmalen der Drehschrauber von Atlas Copco und den Maßnahmen, die der Bediener für den sicheren Betrieb zu ergreifen hat. Klicken Sie auf den Link, oder scannen Sie den nachfolgenden QR-Code, um das Video anzusehen:
https://www.youtube.com/watch?v=FAh6yttvUpw
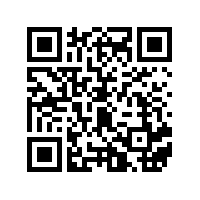
Herkunftsland
Informationen zum Herkunftsland sind auf dem Produktetikett angegeben.
Maßzeichnungen
Maßzeichnungen finden Sie entweder im Maßzeichnungsarchiv oder auf ServAid.
Besuchen Sie: http://webbox.atlascopco.com/webbox/dimdrw oder https://servaid.atlascopco.com.
Übersicht
Allgemeine Beschreibung
Der kabellose Impulsschrauber TBP ist eine echte Neuerung. Es handelt sich um ein akkubetriebenes Impulswerkzeug mit niedrigem Reaktionsmoment, bei gleichzeitig hoher Flexibilität und hohem Drehmoment. Die DuraPulse-Technologie erhöht die Werkzeugverfügbarkeit und sorgt damit für mehr effektive Einsatzzeit in der Produktion. Mit TorqueBoost, aktiver Kühlung und fortschrittlicher Motorsteuerung wird das Drehmoment schneller aufgebaut, der Zeitaufwand je montiertem Bauteil sinkt und das Werkzeug ermöglicht mehr Produktivität. Die vorbildlich niedrigen Schwingungswerte der TBPs wirken der Bediener-Ermüdung entgegen und minimieren das Risiko vibrationsbedingter Erkrankungen.
Eigenschaften
DuraPulse-Technologie mit neuer Dichtung und Luft-Öl-Separator an der Impulszelle
Hohes Drehmoment
Herausragende Ergonomie mit geringen Vibrationen und Reaktionskräften
Kühlsystem zum Schutz des Werkzeugs vor Überhitzen
Einfache Inbetriebnahme und Zuweisung einer Virtuellen Station mit dem Power Focus 6000
Pufferakku
Doppelte Antenne
Rapid Backup Unit (RBU)-Funktion
Vorteile
Verbesserte Verfügbarkeit – bis zu fünf mal höher
Verringert die Ermüdung des Bedieners und das Risiko vibrationsbedingter Erkrankungen
Ein-Hand-Betrieb
Hohe Werkzeugleistung
Weniger Ausfallzeiten in der Produktion
Systemfunktionen
Das POWER FOCUS-System sendet das Verschraubungsprogramm und die Stapelprogrammgröße an das Werkzeug, in dem diese gespeichert bzw. ausgeführt werden. Das Verschraubungsergebnis wird dann an POWER FOCUS zurückgegeben. Siehe schematische Abbildung unten.
Das Werkzeug verfügt über die gleichen Grundfunktionen wie andere Werkzeuge, aufgrund der drahtlosen Kommunikation, bei der die Verschraubungsdaten im Werkzeug gespeichert werde, stehen jedoch an diesem Werkzeug möglicherweise nicht alle Funktionen der POWER FOCUS-Software zur Verfügung.
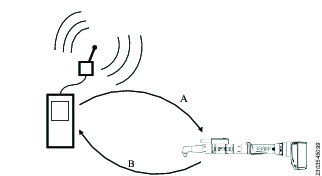
A | Verschraubungsprogramm |
B | Ergebnis |
LED-Anzeige (HMI)
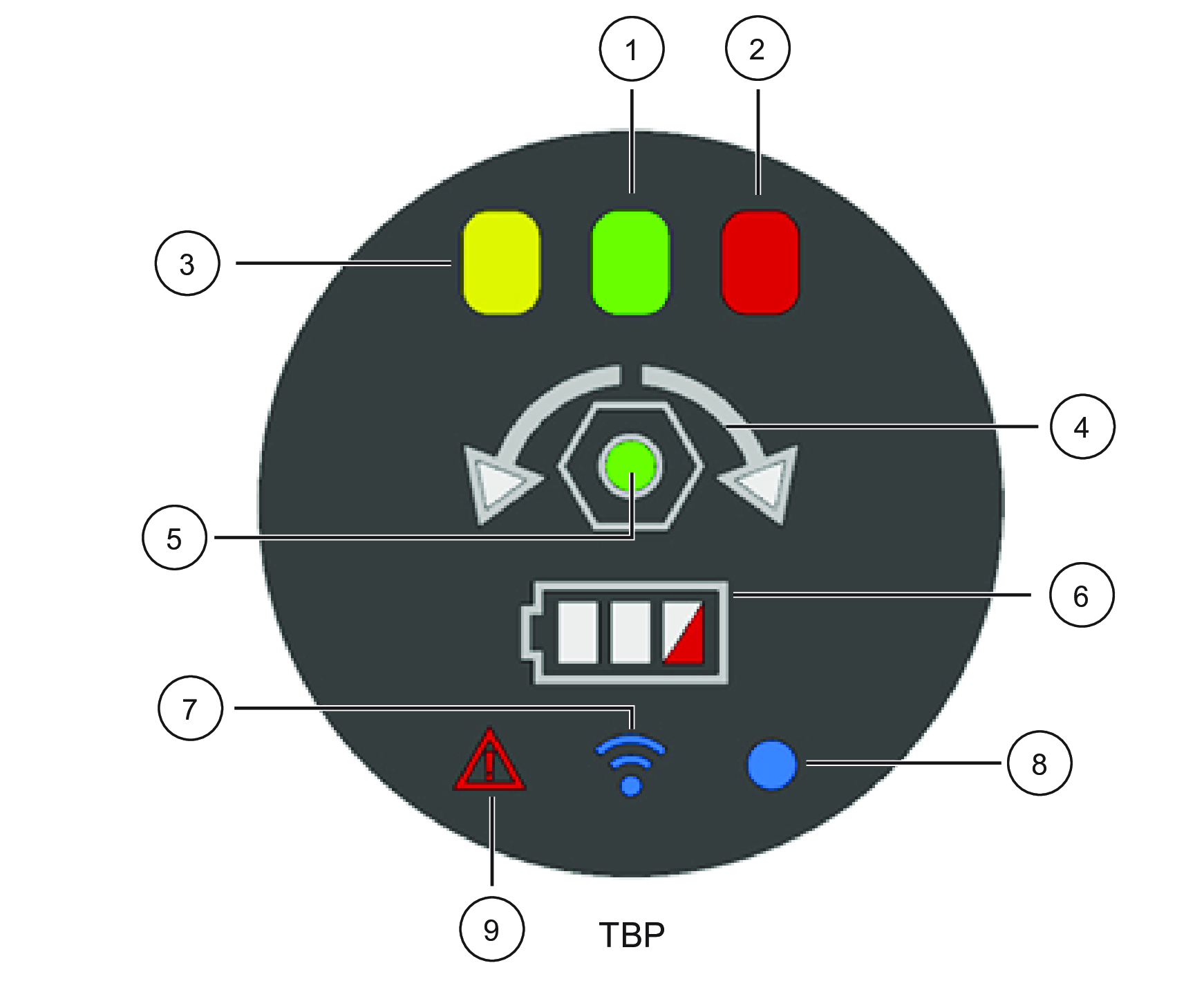
Anzeigeposition | LED-Anzeige | Hauptanzeige |
---|---|---|
1 | Grün | Verschraubungsergebnis OK |
2 | Rot | Verschraubungsergebnis NOK |
3 | Gelb | Warnung Verschraubungsergebnis |
4 | Weiß | Verschraubungsrichtung |
5 | Grün | Stapelprogramm fertig OK |
6 | Akku | Akkuladestatus |
7 | Blau | Funkverbindung mit POWER FOCUS 6000/ToolsTalk Service 2 hergestellt |
8 | Blau | Konfigurierbar - Kann in der Steuerung für die Anzeige verschiedener Ereignisse konfiguriert werden |
9 | Rot | Es ist ein Alarmfehler im Werkzeug aufgetreten |
Weitere Informationen hierzu finden Sie unter LED-Blinkmuster.
Werkzeugfunktionen
Das Werkzeug besitzt einen Summer sowie LED-Anzeigen (HMI), die für die Ausgabe von ereignisbezogenen Signalen konfiguriert werden können. Außerdem sind im Werkzeug bereits eine Reihe Standard-LED-Warnkonfigurationen programmiert.
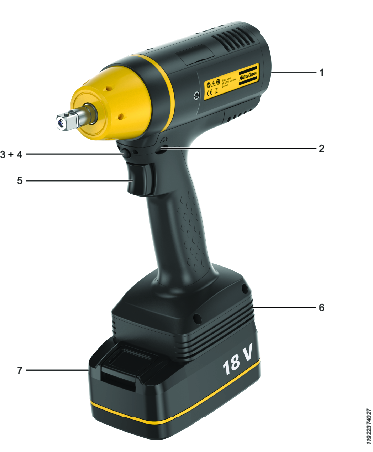
Nummer | Beschreibung |
---|---|
1 | LED-Anzeige (HMI) |
2 | Richtungsschalter |
3 | Front-LED |
4 | Funktionstaste |
5 | Startschalter |
6 | Rapid Backup Unit (RBU) und USB-Anschluss |
7 | Akku oder Adapter mit Netzkabel und Netzteil |
Produkt-Stromversorgung
Dieses Produkt kann entweder mit einem Akku oder mit einem Stromkabel in Kombination mit einem Netzteil verwendet werden.
Speicherkapazität
Im Werkzeug können bis zu 2000 Ergebnisse protokolliert werden.
Umgebungstemperatur
Halten Sie den Akku für optimale Leistung und Lebensdauer innerhalb der angegebenen Temperaturbereiche.
Betriebstemperatur, Laden | +5 bis +40 °C |
Betriebstemperatur, Entladen | 0 bis +40 °C |
Transporttemperatur | -20 bis +40 °C |
Lagertemperatur | +10 bis +25 °C |
Setzen Sie den Akku nicht direkter Sonneneinstrahlung aus.
Technische Produktdaten
Technische Produktdaten finden Sie entweder auf ServAid oder auf der Internetseite von Atlas Copco.
Besuchen Sie: https://servaid.atlascopco.com oder www.atlascopco.com.
Installation
Installationsanforderung
Installation
Eine Informationsrichtlinie finden Sie in der Power Focus 6000-Bedienungsanleitung.
Konfigurations-Kurzanleitung
Diese Kurzanleitung nutzt die Residualdrehmoment-Methode für die Parametereinstellungen. Es existieren auch andere Methoden, die hier jedoch nicht behandelt werden.
Während der Konfiguration der Parametereinstellungen kann das angelegte Drehmoment höher oder niedriger als auf dem POWER FOCUS-Anzeigebildschirm angegeben sein. Der Korrelationsfaktor Restmoment (RTCF) wirkt sich auf den angezeigten Wert aus, überprüfen Sie daher das Restmoment mit einem ST-Schlüssel oder einem ähnlichen Werkzeug, wenn die Verbindungseinstellungen mit Teilen in der laufenden Produktion vorgenommen werden.
Stellen Die den RTCF auf 100 % ein.
Verwenden Sie stets die vorgesehenen Steckschlüssel und Verlängerungen (bevorzugt geführte Steckschlüssel und Verlängerungen).
Führen Sie die Einstellungen jeweils an der vorgesehenen Verbindung durch.
Die Verwendung der gleichen Verbindung für mehrere Verschraubungen kann sich auf das Ergebnis auswirken.
Stellen Sie das Zielmoment auf das angegebene erforderliche Moment ein.
Ziehen Sie die Verbindung mit den POWER FOCUS-Standardeinstellungen fest.
Überprüfen Sie das Drehmoment.
Ändern Sie den RTCF, falls das Restmoment deutlich niedriger oder höher als auf dem POWER FOCUS angezeigt ist. Das Restmoment sollte dem POWER FOCUS entsprechen. Ist die Abweichung gering (+/-4 %), fahren Sie mit dem nächsten Schritt fort.
Der RTCF korreliert mit den im nächsten Schritt vorgenommenen Einstellungen, wenden Sie nicht zu viel Zeit für diesen Schritt auf.
Erhöhen oder verringern Sie die Leistung und die Einschraubdrehzahl, um 10-20 Impulse während der Verschraubung zu erreichen.
Ist ein Schraubfall sehr hart oder variiert er zwischen hart und mittelhart, passen Sie die Einstellungen für den härtesten Schraubfall an.
Erhöhen Sie die Leistung und/oder die Einschraubdrehzahl, falls die Zahl der Impulse zu hoch ist (>20), da dies den Verschleiß erhöht und die Produktivität verringert.
Verringern Sie die Leistung und/oder die Einschraubdrehzahl, falls die Zahl der Impulse zu niedrig ist, da dies zu einer niedrigen Genauigkeit führt.
Falls eine hohe Produktivität erforderlich ist, versuchen Sie mindestens 5-10 Impulse pro Verschraubung zu erhalten.
Eine Einschraubdrehzahl von 2000 U/min reicht aus. Falls die Anziehgeschwindigkeit verbessert werden muss, erhöhen Sie die Einschraubdrehzahl in kleinen Schritten und bewerten Sie die Ergebnisse vorsichtig. Eine hohe Einschraubdrehzahl reduziert die Verschraubungszeit, kann jedoch zu einer Drehmomentüberhöhung führen.
Wird die Winkelüberwachung verwendet, so muss die Einschraubdrehzahl möglicherweise gesenkt werden, um die Winkelstreuung zu verringern. Kontaktieren Sie für weitere Informationen das Kundendienstzentrum von Atlas Copco Industrial Technique AB für die öffentlichen Berichte zur Übertragungsgeschwindigkeit von Impulswerkzeugen.
Ziehen Sie die Verbindung mit den neuen Einstellungen an. Ändern Sie die Einstellungen nötigenfalls und führen Sie die Verschraubung erneut durch.
Führen Sie eine Reihe von Verschraubungen durch, um den RTCF zu überprüfen und zu verändern, siehe Power Focus 6000-Konfigurationshandbuch.
Verschrauben Sie eine Reihe von Verbindungen mit dem neuen RTCF, um zu überprüfen, ob die gewünschten Ergebnisse erzielt werden. Liegt die Werkzeugleistung nicht im gewünschten Bereich, führen Sie die Schritte 6 bis 9 erneut durch.
Verschrauben Sie so viele Verbindungen wie nötig, um die Werkzeugleistung an der gewünschten Verbindung zu überprüfen.
Installationsanleitung
Drehmomenteinstellung
Informationen zur Drehmomenteinstellung finden Sie im Power Focus 6000 -Konfigurationshandbuch.

Der Drehmomenteinstellfaktor wird im nichtflüchtigen Speicher des Werkzeugs gespeichert. Jede Änderung des Drehmomenteinstellfaktors in der POWER FOCUS 6000 aktualisiert den gespeicherten Wert im Werkzeug.
Rapid Backup Unit
Die Rapid Backup Unit (RBU) hat den Formfaktor einer SD-Karte. Die RBU enthält alle aktuellen Netzwerkkonfigurationen und -einstellungen. Einige der Parameter werden bei der Installation und Konfiguration auf der Karte gespeichert. Bei einem Ausfall kann die Karte schnell entnommen und in ein neues Werkzeug eingelegt werden. So bleiben alle Funktionen erhalten.

Wenn die RBU von einem Werkzeug auf ein anderes übertragen wird, wird das neue Werkzeug mit der Software auf der Karte aktualisiert. Während dieser Aktualisierung kann es zu Datenverlusten kommen. Um dieses Risiko zu minimieren, ist es zu empfehlen, dass auf dem neuen Werkzeug bereits dieselbe Softwareversion wie auf dem alten Werkzeug läuft.

Diese RBU kann ausschließlich zum Speichern der Werkzeugkonfigurationsdaten und der Software verwendet werden. Eine Neuformatierung der Karte sowie Änderungen an den Daten auf der Karte, die nicht mit ToolsTalk Service 2 vorgenommen werden, führen dazu, dass die Karte unbrauchbar wird.

Beachten Sie, dass die mit dem Werkzeug verknüpften gespeicherten Ergebnisse verlorengehen, wenn die RBU auf ein anderes Werkzeug übertragen wird.

Die MAC-Adresse ist nicht mit dem Werkzeug selbst, sondern mit der RBU verknüpft. Beim Übertragen einer Karte auf ein neues Werkzeug nimmt dieses Werkzeug daher die MAC-Adresse der RBU an.
Werkzeugkonvertierung
Beim Konvertieren eines Werkzeugs (z.B. durch Wechsel des Vorderteils) müssen die Werkzeuginformationen aktualisiert werden, um die Änderungen abzubilden. Weitere Informationen finden Sie im Benutzerhandbuch der ToolsTalk Service 2 User Edition
Beim Verbinden mit ToolsTalk 2 werden Sie zum Ändern der Werkzeuginformationen aufgefordert. Führen sie zur Anpassung der Werkzeugbezeichnung an die Werkzeugkonvertierung die gleichen Schritte aus wie bei einem Austausch von Ersatzteilen. Aktualisieren Sie das Werkzeug mit der Werkzeugbezeichnung des neuen Teils.

Da das Werkzeug konvertiert wurde, stimmen die im Werkzeug gespeicherten Werkzeuginformationen nicht mehr mit der Werkzeugbezeichnung auf dem Typenschild überein.
Anbringen und Abnehmen des Akkus
Bringen Sie den Akku am Werkzeug an und stellen Sie sicher, dass er korrekt sitzt. Der Akku kann so angebracht werden, dass er nach vorne oder nach hinten zeigt, um die bestmögliche Zugänglichkeit und Balance zu erreichen.
Um den Akku zu entfernen, drücken Sie die Taste am Akku und schieben Sie ihn heraus.
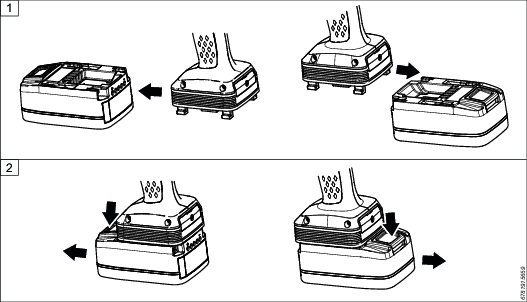
Anbringen des Netzkabels
Informationen zum Anbringen des Netzkabels finden Sie in den Produktanweisungen für das Netzteil 950.
Ausgangskonfiguration
Werkzeugkonfiguration
Informationen zur Werkzeugkonfiguration finden Sie im Power Focus 6000-Konfigurationshandbuch oder im Benutzerhandbuch der ToolsTalk Service 2 User Edition.
Werkzeugkalibrierung
Informationen zur Kalibrierung dieses Werkzeugs finden Sie im Power Focus 6000-Konfigurationshandbuch oder im Benutzerhandbuch der ToolsTalk Service 2 User Edition.
Bedienung
Ergonomie-Richtlinien
Betrachten Sie Ihren Arbeitsplatz, während Sie diese Liste mit allgemeinen Ergonomie-Richtlinien lesen, und versuchen Sie, Bereiche zu identifizieren, in denen Verbesserungen in Bezug auf Körperhaltung, Positionierung der Komponenten oder Arbeitsumgebung möglich sind.
Legen Sie regelmäßige Pausen ein und wechseln Sie regelmäßig die Arbeitshaltung.
Passen Sie den Bereich um Ihre Arbeitsstation Ihren Anforderungen und den auszuführenden Arbeiten an.
Positionieren Sie Teile und Werkzeuge so, dass statische Belastungen möglichst vermieden werden und sich sämtliche Arbeitsmittel bequem erreichen lassen.
Verwenden Sie an Ihrer Arbeitsstation für die Aufgabe geeignete Tische, Stühle oder andere Gegenstände.
Vermeiden Sie während der Ausführung von Montagearbeiten Körperhaltungen über Schulterhöhe oder mit statischer Halteposition.
Wenn Sie über Schulterhöhe arbeiten müssen, verringern Sie die auf die statischen Muskeln wirkende Belastung durch Verringerung des Werkzeuggewichts. Setzen Sie hierzu beispielsweise Drehmomentarme, Schlauchaufroller oder Gewichtsausgleicher ein. Sie können die auf die statischen Muskeln ausgeübte Belastung auch reduzieren, indem Sie das Werkzeug nah am Körper halten.
Legen Sie häufig Pausen ein.
Vermeiden Sie extreme Arm- oder Handgelenkhaltungen, insbesondere während Arbeiten, bei denen ein gewisser Kraftaufwand erforderlich ist.
Richten Sie Ihren Arbeitsplatz so in Ihrem Sichtfeld ein, dass nur minimale Augen- und Kopfbewegungen erforderlich sind.
Verwenden Sie zur Ausführung Ihrer Arbeit eine angemessene Beleuchtungen.
Wählen Sie ein zur Ausführung Ihrer Arbeit angemessenes Werkzeug aus.
Tragen Sie in lauten Umgebungen einen entsprechenden Gehörschutz.
Verwenden Sie hochwertige Einsätze und Kleinteile, um eine übermäßige Vibrationsbelastung möglichst zu vermeiden.
Minimieren Sie nach Möglichkeit durch Reaktionskräfte verursachte Belastungen.
Beim Schneiden:
Eine Trennscheibe kann stecken bleiben, wenn sie verbogen ist oder nicht korrekt geführt wird. Verwenden Sie einen für die Trennscheibe geeigneten Flansch und vermeiden Sie es, die Trennscheibe während des Betriebs zu biegen.
Beim Bohren:
Die Bohrmaschine kann beim Durchbrechen des Bohrers stehen bleiben. Verwenden Sie bei hohem Stillstandsmoment Stützgriffe. Gemäß Teil 3 der Sicherheitsnorm ISO11148 wird empfohlen, bei Pistolengriffmodellen eine Vorrichtung zur Aufnahme von Reaktionsmomenten von über 10 Nm und bei Stabmodellen zur Aufnahme von Reaktionsmomenten von über 4 Nm zu verwenden.
Bei Verwendung von Schraubendrehern und Schraubern mit Direktantrieb:
Reaktionskräfte sind von der Werkzeugeinstellung und den Eigenschaften der jeweiligen Verbindung abhängig. Die Höhe der Reaktionskraft, die eine Bediener tolerieren kann, hängt von dessen Körperkraft und Haltung ab. Passen Sie die Drehmomenteinstellung der Stärke und der Körperhaltung des Bedieners an und verwenden Sie bei zu hohem Drehmoment einen Drehmomentarm oder einen Gegenhalter.
Verwenden Sie in staubigen Umgebungen ein System zur Staubabsaugung oder tragen Sie einen Mundschutz.
Konfigurationsanleitung
Verschraubungsprogramme
Das Zuweisen von Verschraubungsprogrammen und die Änderung von Programmparametern erfolgen über eine Internet-Benutzeroberfläche oder über die Steuerung, mit der das Werkzeug gekoppelt ist.
Weitere Informationen finden Sie in der ETP TBP / ETP TBP-S Software-Bedienungsanleitung.
Betriebsanleitung
LED-Blinkmuster
Neben den von der Steuerung festgelegten LED-Blinkmustern gibt es eine Reihe von Standard-Blinkmustern für die Werkzeug-LEDs.
In der folgenden Tabelle sind diese Standard-Blinkmuster zusammengefasst.
LED-Anzeige | Lichtverhalten | Status |
---|---|---|
Alle Anzeigen | Alle blinken | Werkzeug wurde gestartet. |
Ladezustand Akku | Alle LED blinken weiß: schnelles Blinken | Werkzeug läuft mit Notstrombatterie. |
Ladezustand Akku | Eine LED blinkt rot | Akku ist leer. |
Alarm | Blinken: einmal pro Sekunde | Ungültige Konfiguration der WLAN-Einstellungen des Werkzeugs in ToolsTalk Service 2. |
Alarm | Blinken: schnelles Blinken | Akkusoftware veraltet. Der Betrieb des Werkzeugs mit veralteter Akkusoftware ist nicht zulässig. |
Funkverbindung | Blau | Funkverbindung hergestellt / ToolsTalk Service 2-Verbindung hergestellt. |
Funkverbindung | Blinken | Die Startanforderung wurde aufgrund einer schlechten Verbindung vom Werkzeug nicht rechtzeitig empfangen. |
Verschraubungsrichtung | Beide Richtungen blinken: schnelles Blinken, 3-mal pro Sekunde. | Softwareupdate läuft (kann bis zu 7 Minuten dauern). |
Verschraubungsrichtung | Beide Richtungen blinken: schnelles Blinken, danach Dauerlicht. | Zeigt eines der folgenden Probleme an:
|
Verschraubungsrichtung | Beide Richtungen blinken: langsames Blinken, 1-mal pro Sekunde. | Werkzeug ist über USB-Kabel angeschlossen und wartet auf Verbindung mit ToolsTalk Service 2. |
Verschraubung
Drehrichtung für die Verschraubung
Prüfen Sie, ob das Werkzeug in der richtigen Drehrichtung rotiert, indem Sie den Drehrichtungsumschalter oder den Umkehrring drehen.
Modelle mit Pistolengriff (mit Seitentasten)
Drücken Sie den Drehrichtungsumschalter auf der rechten Seite des Werkzeugs, um die Drehrichtung im Uhrzeigersinn (CW) festzulegen.
Drücken Sie den Drehrichtungsumschalter auf der linken Seite des Werkzeugs, um die Drehrichtung gegen den Uhrzeigersinn (CCW) festzulegen.
Modelle mit Pistolengriff (ohne Seitentasten)
Drücken Sie die Funktionstaste oben auf dem Startschalter doppelt, um die Drehrichtung zwischen im Uhrzeigersinn (CW) und gegen den Uhrzeigersinn (CCW) umzuschalten.
Winkelschrauber
Drehen Sie den Umsteuerring nach rechts, um die Drehrichtung im Uhrzeigersinn (CW) festzulegen.
Drehen Sie den Umsteuerring nach links, um die Drehrichtung gegen den Uhrzeigersinn (CCW) festzulegen.
Softstart
Die Softstart-Funktion unterstützt ein straffes Anliegen von Schraubenkopf und Gewinde. Die Dauer des Softstarts ist einstellbar.
Weitere Informationen zu Verschraubungen finden Sie im Power Focus 6000-Konfigurationshandbuch.
Optimieren der Leistung Ihres Impulswerkzeugs

Für eine optimale Leistung der TBP/TBP-S-Werkzeuge verwenden Sie immer STRB2-Batterien in gutem Zustand. Niedrige Ladestände der Batterie können die Leistung der Werkzeuge beeinträchtigen, insbesondere bei anspruchsvollen Anwendungen. Bei den TBP91/TBP-S91-Werkzeugen empfehlen wir dringend, die 36-V-Batterie für die meisten Anwendungen zu verwenden. Die Verwendung der 18-V-Batterie mit den TBP91/TBP-S91-Werkzeugen kann zu Leistungsbegrenzungen der Werkzeuge führen.
Empfohlene Impulsanzahl
Ein für Ihre Anwendung geeignetes Impulswerkzeug sollte das Zieldrehmoment (mit Abschaltung) innerhalb von 5-20 Impulsen erreichen. Die benötigte Anzahl der Impulse, um das Zieldrehmoment zu erreichen, kann mit einem Analysator gemessen werden. Die Anzugsdauer kann auch als Richtlinie verwendet werden, um zu bestimmen, ob das Werkzeug für Ihre Anwendung geeignet ist:
≤ 1 Sekunde für Werkzeuge bis 30 Nm
≈ 1 Sekunde für Werkzeuge bis 80 Nm
≈ 2 Sekunden für Werkzeuge bis 150 Nm
≈ 5 Sekunden für Werkzeuge bis 450 Nm
≤ 10 Sekunden für Werkzeuge bis 850 Nm
Wenn das Zieldrehmoment mit weniger als 5 Impulsen erreicht wird (= kurze Anzugszeit), nimmt die Drehmomentstreuung zu und es kann schwierig werden, das richtige Niveau einzustellen, insbesondere bei harten Gelenken.
Wenn das Zieldrehmoment mit mehr als 20 Impulsen erreicht wird (= zu lange Anzugszeit), nimmt der Verschleiß zu und Ölfüllungen und Wartungen werden häufiger nötig. Eine zu lange Anzugszeit in Kombination mit einer hohen Produktionsrate kann auch zu einer übermäßigen Erwärmung des Öls führen. In diesem Fall verringert sich die Leistung mit längerer Anzugszeit und manchmal ohne Abschaltung.
Wenn das Zieldrehmoment mit weniger als 5 Impulsen erreicht wird, kann dies behoben werden durch:
Verringerung der Leistungseinstellung während des Verschraubens.
Senkung der Einschraubdrehzahl.

Eine Veränderung der Leistungseinstellungen und/oder der Einschraubdrehzahl kann sich auf die Drehmomentgenauigkeit auswirken.
Wenn das Zieldrehmoment mit mehr als 20 Impulsen erreicht wird, kann dies behoben werden durch:
Erhöhung der Leistungseinstellung.
Erhöhung der Einschraubdrehzahl.

Eine Veränderung der Leistungseinstellungen und/oder der Einschraubdrehzahl kann sich auf die Drehmomentgenauigkeit auswirken.
Summer
Dieses Werkzeug verfügt über einen Summer, der für eine Signalausgabe bei bestimmten Ereignissen oder Warnungen konfiguriert werden kann.
Weitere Informationen zu Funktion und Konfiguration des Summers finden sie im Power Focus 6000-Konfigurationshandbuch.
Wartung
Allgemeine Serviceinformationen
Wenn das Werkzeug nicht ordnungsgemäß funktioniert, nehmen Sie es außer Betrieb und prüfen Sie es. Es wird empfohlen, eine vorbeugende Wartung regelmäßig durchzuführen. Beachten Sie die ausführlichen Informationen über vorbeugende Wartungen.
Achten Sie darauf, die von Atlas Copco empfohlenen Service-Werkzeuge, Service-Kits und Ersatzteile zu verwenden.
Stellen Sie sicher, dass Sie die Service-Anweisungen von Atlas Copco befolgen.

Stellen Sie sicher, dass Sie in einer sauberen Umgebung arbeiten und alle Teile vor dem Zusammenbau gereinigt werden. Fremdpartikel, auch kleine Papiergewebefasern, können die Lebensdauer der Pulseinheit beeinträchtigen.
ESD-Probleme vermeiden
Die Komponenten im Inneren des Produkts und der Steuerung sind empfindlich gegenüber elektrostatischen Entladungen. Stellen Sie zur Vermeidung zukünftiger Störungen sicher, dass Service und Wartung in einer ESD-genehmigten Arbeitsumgebung erfolgen. Die Abbildung unten zeigt ein Beispiel für eine entsprechende Service-Arbeitsstation.

Wartungsanweisungen
Wartungsempfehlungen
Es wird empfohlen, eine vorbeugende Wartung regelmäßig durchzuführen. Beachten Sie die ausführlichen Informationen über die vorbeugende Wartung. Wenn das Produkt nicht ordnungsgemäß funktioniert, bringen Sie es außer Betrieb und prüfen Sie es.
Wenn keine detaillierten Informationen über eine vorbeugende Wartung enthalten sind, befolgen Sie die folgenden allgemeinen Richtlinien:
Entsprechende Teile gründlich reinigen
Defekte und verschlissene Teile ersetzen
Service
Tägliche Überprüfung
Stellen Sie sicher, dass das Werkzeug in gutem Zustand ist und keine sichtbaren Schäden hat.
Stellen Sie sicher, dass die Steckdosen und Verlängerungen keinen sichtbaren Schaden aufweisen.
Achten Sie darauf, dass beim Verwenden des Werkzeugs keine unerwarteten Geräusche auftreten.
Vorbeugende Wartung
Für die Wartungsbedarf dieses Werkzeugs existieren mehrere Kriterien:
Art der Verbindung
Drehmomentniveau
Verschraubungsdauer
Produktionsrate
Die Service-Intervalle und -Lösungen basieren auf Erfahrungen und internen Tests.
Ölstand in der Pulseinheit
Der richtige Ölstand in der Pulseinheit ist wichtig, damit das Werkzeug korrekt arbeitet.
Die Notwendigkeit, der Pulseinheit Öl zuzuführen, hängt von der Anzahl der Anzugsdrehmomente, dem Drehmomentniveau und der Impulsanzahl (Anzugszeit) ab.

Wird das Werkzeug bei niedrigem Ölstand betrieben, führt dies zu einem schnelleren Verschleiß der Teile in der Pulseinheit. Dies wirkt sich auch auf Werkzeugleistung aus.
Niedriger Ölstand in der Pulseinheit erkannt
Längere Anzugsdauer
Ölmangel-Warnung
Sehr hohe Impulsfrequenz, besonders wenn das Werkzeug längere Zeit nicht benutzt wurde.
Drehmoment niedrig
Um die Pulsfrequenz zu messen, siehe Werkzeugzustandsprüfung.
Vorbeugende Wartung Stufe 2
Wartung Stufe 2
Führen Sie nach jeweils 12.000.000 Impulsen, wenn die POWER FOCUS-Steuerung die Meldung: „Ölstand der Pulseinheit niedrig“ anzeigt oder alle zwei Jahre eine Wartung durch, je nachdem, was zuerst eintritt.
Für maximale Werkzeugleistung befolgen Sie bitte die Anweisungen und verwenden Sie die empfohlenen Service-Tools und Service-Kits von Atlas Copco. Achten Sie darauf, alle in den Servicesätzen enthaltenen Teile zu verwenden. Verwenden Sie immer das Anzugsmoment und die Schmiermittel, die von Atlas Copco empfohlen werden.
Beginnen Sie mit der Wartung gemäß Vorbeugende Wartung Stufe 1 und fahren Sie anschließend wie folgt fort:

Pulseinheit: Verwenden Sie bei der Wartung der Pulseinheit immer ein fusselfreies Tuch.
Lassen Sie das Öl vollständig aus der Pulseinheit ab.
Bauen Sie die Pulseinheit auseinander (siehe Ersatzteilliste).
Reinigen und prüfen Sie alle Teile und Oberflächen gründlich auf Verschleiß oder Beschädigung.
Reinigen Sie die Magnete von Metallpartikeln.
Tauschen Sie die Rollen, Kolben, die Pulswelle und das Kugelrückschlagventil aus, wenn diese abgenutzt sind.
Tauschen Sie alle O-Ringe aus.
Ersetzen Sie die Ambossdichtung. Achten Sie darauf, dass das vordere Teil des Zylinders vor der Montage der neuen Dichtung auf der Innenseite sauber und trocken ist und keine Schmierung aufweist.
Stellen Sie sicher, dass die Ambossoberfläche glatt, sauber und mit Impulsöl geschmiert ist, um Beschädigungen der Ambossabdichtung während der Montage zu vermeiden.
Richten Sie die Nut am vorderen Teil des Zylinders an der Pulswelle und der Trennscheibe des Abscheiders aus. Sind diese nicht ausgerichtet, wird das Endstück des Zylinders nicht richtig festgezogen und die Pulseinheit kann nicht ordnungsgemäß funktionieren.
Füllen Sie die Pulseinheit mit der korrekten Ölmenge. Siehe Ölfüll-/wechselanweisung für Pulseinheit.
Vorbeugende Wartung Stufe 1
Wartung Stufe 1
Führen Sie nach jeweils 6.000.000 Impulsen, wenn die POWER FOCUS-Steuerung die Meldung: „Ölstand der Pulseinheit niedrig“ anzeigt oder einmal jährlich eine Wartung durch, je nachdem, was zuerst eintritt.
Für maximale Werkzeugleistung befolgen Sie bitte die Anweisungen und verwenden Sie die empfohlenen Service-Tools und Service-Kits von Atlas Copco. Verwenden Sie immer Anzugsmomente und Schmiermittel, wie von Atlas Copco empfohlen.
Werkzeughandgriff
Führen Sie eine Sichtprüfung auf Schäden durch.
Inspizieren Sie die Joch- und Aufhängepunkte.
Überprüfen Sie das Kugellager im Gehäuse der Pulseinheit und die Oberfläche des Ambosses.
Elektromotor
Achten Sie auf ungewöhnliche Geräusche.
Pulseinheit
Wechseln Sie das Öl entsprechend der Ölfüll-/wechselanweisung der Pulseinheit.
Stellen Sie sicher, dass die Taktfrequenz innerhalb der Grenzwerte liegt, siehe Abschnitt Werkzeugzustandstest.
Rotormutter komplett
Führen Sie eine Sichtprüfung auf Schäden durch.
Remontage der Impulseinheit am Motor

Bei der Remontage der Impulseinheit:
Das Lösemoment kann erheblich höher sein als das Anzugsmoment.
Es ist wichtig, die Impulseinheit entsprechend festzuziehen und die empfohlenen Schmierstoffe zu verwenden.
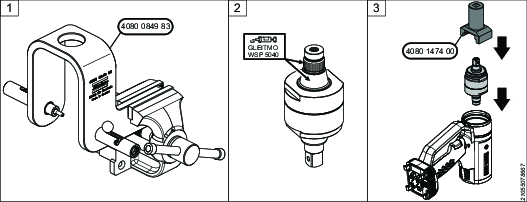
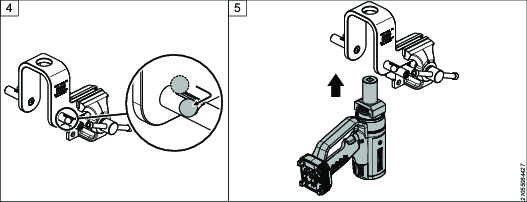

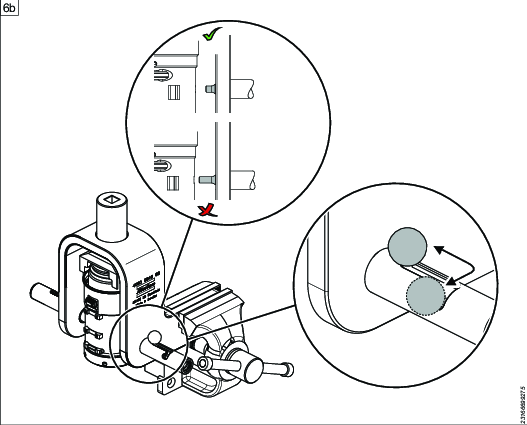
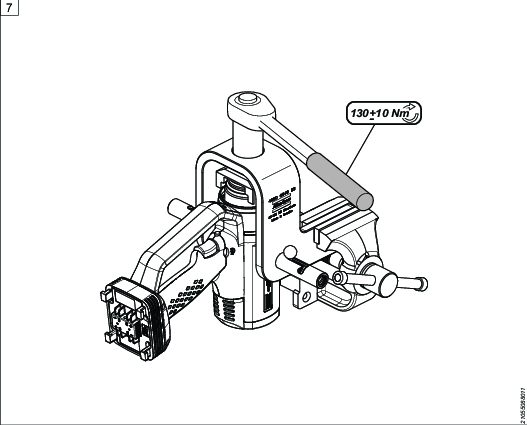
Montage der Pulseinheit

Stellen Sie sicher, dass Sie alle Teile der Pulseinheit in der richtigen Reihenfolge montieren.
Es ist wichtig, dass die Nockenwelle und die Trennscheibe an der Nut im vorderen Zylinderstück des Zylinders ausgerichtet sind. Andernfalls wird das Endstück des Zylinders nicht richtig festgezogen, und die Pulseinheit kann nicht vorschriftsmäßig funktionieren.
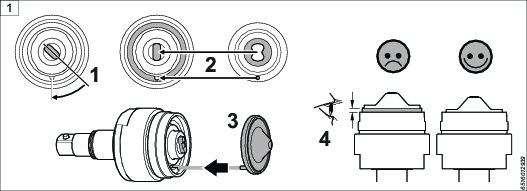
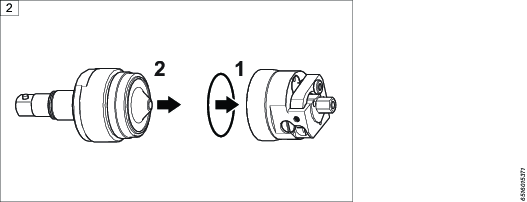
Pflege der Notstrombatterie
Das Werkzeug verfügt über eine interne Notstrombatterie. Die Notstrombatterie wird beispielsweise verwendet, um die Funkkommunikation bei einem Wechsel des Hauptakkus aufrechtzuerhalten. Die Notstrombatterie erlaubt etwa 20 Sekunden zum Wechsel des Hauptakkus, bevor das Werkzeug abgeschaltet wird.

Verbinden Sie neu hergestellte Werkzeuge immer mit einem Hauptakku und lassen Sie sie zwei Stunden lang eingeschaltet, um die Notstrombatterie zu laden.

Ersetzen Sie die Notstrombatterie bei Verwendung einer Softwareversion, die älter als die in der folgenden Tabelle aufgeführten ist, mindestens alle 12 Monate. Der Austausch muss durch einen qualifizierten Servicetechniker durchgeführt werden. Ausgetauschte Notstrombatterien müssen gemäß den Recycling-Anweisungen recycelt werden.

Tauschen Sie die Notstrombatterie für Softwareversionen gemäß der folgenden Tabelle alle drei Jahre aus. Das verlängerte Wartungsintervall gilt für neue Batterien, die mit den in der folgenden Tabelle enthaltenen Softwareversionen verwendet werden. Beträgt das Alter der Notstrombatterie bereits fast 12 Monate, wird empfohlen, die Notstrombatterie beim Update auf die neue Software auszutauschen.
TBP/TBP-S | SRB31 | SRB81 | IxB |
Version 2.1.3 oder höher | Version 1.3.15 oder höher | Version 1.4.0 oder höher | Version 3.10.4 oder höher |
Lagerbedingungen
Die Lebensdauer der Notstrombatterie wird durch extreme Temperaturen beeinträchtigt. Lagern Sie das Werkzeug bei einer Umgebungstemperatur von 0-30 °C. Halten Sie keine zusätzlichen Notstrombatterien auf Lager.
Wenn ein neu hergestelltes Werkzeug eingelagert werden soll, achten Sie darauf, dieses zuvor für mindestens zwei Stunden einzuschalten.
Schalten Sie das Werkzeug während der Lagerung mindestens alle fünf Monate ein, um die Notstrombatterie aufzuladen. Das Werkzeug muss jedes Mal für mindestens zwei Stunden eingeschaltet werden.
Überholung
Die Wartung Ihres Elektrowerkzeugs darf nur von qualifizierten Technikern unter Verwendung identischer Ersatzteile durchgeführt werden. Damit wird die fortwährende Sicherheit des Elektrowerkzeugs sichergestellt.
Die Wartung darf nur von erfahrenem Personal ausgeführt werden, das Zugang zu den Wartungsanleitungen hat und/oder für die Wartung dieser Werkzeuge ausgebildet ist.
Der Elektromotor ist eine geschlossene Einheit und darf unter keinen Umständen von anderen Personen als den Technikern von Atlas Copco Industrial Technique AB geöffnet werden.
Wenn der Elektromotor defekt ist oder gewartet werden muss, senden Sie die komplette Motoreinheit an Atlas Copco Industrial Technique AB zurück.
An Motoren, die von anderen Personen als Mitarbeitern von Atlas Copco Industrial Technique AB geöffnet wurden, führen wir keine Wartung durch.
Es wird empfohlen, regelmäßig – einmal jährlich, nach maximal 6.000.000 Impulsen (je nachdem, was zuerst eintritt) – eine Überholung und vorbeugende Wartung durchzuführen. Im Falle von Hochleistungseinsätzen ist u. U. eine häufigere Überholung vonnöten. Falls die Maschine nicht einwandfrei funktioniert, ist sie unverzüglich außer Betrieb zu nehmen und einer Inspektion zu unterziehen.
Verwenden Sie für die Demontage des Werkzeugs stets die speziell entwickelten, im Abschnitt Ersatzteile unter ServAid - https://servaid.atlascopco.com empfohlenen Wartungswerkzeuge.
Schmieranweisungen
Schmieranleitung
Fabrikat | Universal |
---|---|
Almagard | LE3752 |
Ölfüll-/wechselanweisung für Pulseinheit
Benötigte Ausrüstung für Ölfüllung und -wechsel:
Atlas Copco Pulseinheitsöl
Atlas Copco Pulseinheit-Ölfüllset.
Siehe https://servaid.atlascopco.com für Bestellnummern der Ersatzteile.
Ölfüllset
2 x Adapter M3
2 x Adapter M4
4 x Schlauchlänge 540 mm
2 x Schlauchlänge 50 mm
1 x Schlauchlänge 120 mm
1 x Spritze 50 ml
1 x Spritze 1 ml
4 x Verschluss
5 x Anschluss
2 x Anschluss
2 x Kanne
2 x Abdeckung
Platzieren Sie die Pulseinheit in einem Schraubstock in solch einem Winkel, dass der Auslass am höchsten Punkt ist.
Entfernen Sie die Schraube, die die Einlassöffnung abdeckt. Stellen Sie sicher, dass sich der O-Ring an der Schraube befindet und nicht in der Pulseinheit verbleibt. Befestigen Sie den Füllschlauch von Hand mit dem Schlauchanschlussende an der Pulseinheit.
Befüllen Sie die große Spritze mit Öl bis zur maximalen Kapazität aus der Ölkanne.
Verwenden Sie immer neues Atlas Copco Pulseinheitsöl.
Entfernen Sie den Stopfen vom Füllschlauch und befestigen Sie die Spritze am Schlauch.
Entfernen Sie die Schraube, die die Auslassöffnung der Pulseinheit abdeckt. Stellen Sie sicher, dass sich der O-Ring an der Schraube befindet und nicht in der Pulseinheit verbleibt. Befestigen Sie den Rücklaufschlauch an der Pulseinheit.
Entfernen Sie den Stopfen vom Rücklaufschlauch und befestigen Sie ihn dann an der Ölkanne.
Füllen Sie Öl aus der großen Spritze in die Pulseinheit. Beim Einfüllen von Öl in die Pulseinheit treten Luftblasen aus.
Drehen Sie den Amboss hin und her, während Sie das Öl einfüllen, bis keine Luftblasen mehr aus der Pulseinheit austreten.
Drehen Sie die gesamte Impulseinheit herum, während Sie das Öl einfüllen, um sicherzustellen, dass sich keine Luftblasen mehr in der Pulseinheit befinden.
Entfernen Sie den Rücklaufschlauch von der Ölkanne und befestigen Sie den Stopfen am Ende des Rücklaufschlauchs.
Entfernen Sie den Rücklaufschlauch von der Auslassöffnung der Pulseinheit. Setzen Sie die Schraube, die die Auslassöffnung abdeckt, zurück in ihre Position.
Positionieren Sie nun die Pulseinheit im Schraubstock mit der Einlassöffnung nach oben.
Entfernen Sie die Spritze vom Füllschlauch und befestigen Sie den Stopfen am Füllschlauch.
Entfernen Sie den Ölfüllschlauch von der Pulseinheit.
Verwenden Sie die kleine Spritze, um die korrekte Menge Öl zu entnehmen, siehe Tabelle Ölfüllung.
Setzen Sie die Schraube, die die Einlassöffnung abdeckt, zurück in ihre Position.
Modell | Ölreduzierung (X) von 100% voller Pulseinheit |
---|---|
ETP TBP/TBP-S 6 | 0,7 ± 0,05 ml |
ETP TBP/TBP-S 8 | 0,7 ± 0,05 ml |
ETP TBP/TBP-S 9 | 1,1 ± 0,05 ml |
ETP TBP/TBP-S 13 | 1,8 ± 0,05 ml |
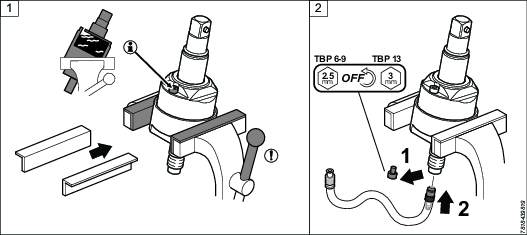
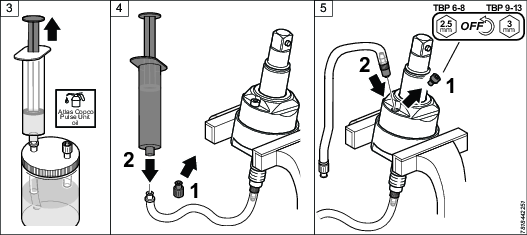
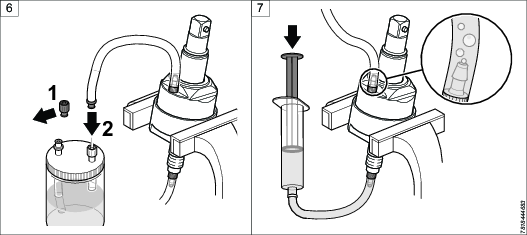
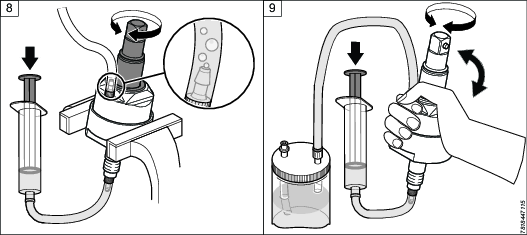
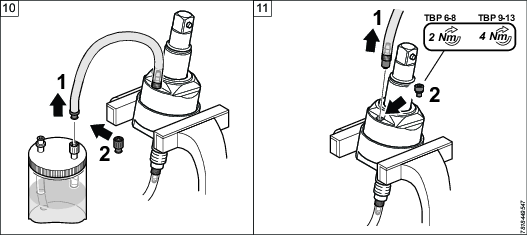
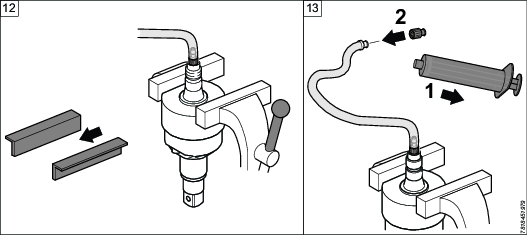
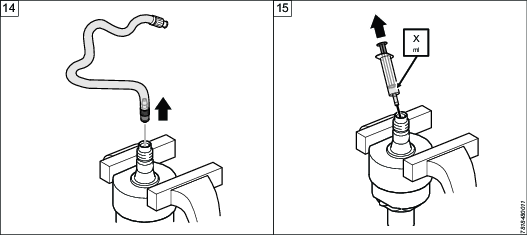
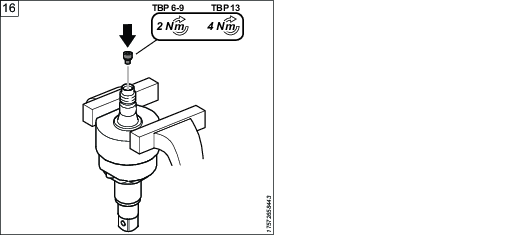
Reparaturanleitung
Austausch von Ersatzteilen
Beim Austausch bestimmter elektrischer Teile des Werkzeugs werden die Werkzeugbezeichnung und die Parameter von ToolsTalk Service 2 gelöscht und müssen erneut eingerichtet werden. Weitere Informationen finden Sie in der ToolsTalk Service 2 User Edition-Bedienungsanleitung.
Test nach Wartungseingriff
Werkzeugzustandstest
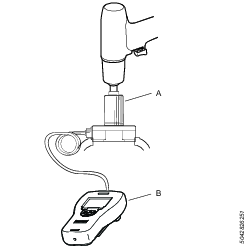
A | Statischer Momentgeber SRTT |
B | STa6000 |
Testen des maximale Drehmoments und der Impulsfrequenz
Stellen Sie die Filterfrequenz im STa6000 auf 850 Hz ein.
Testen Sie das maximale Drehmoment und die Impulsfrequenz mit einem statischen SRTT-Momentgeber. Verschraubungszeit max. 1 Sekunde.
Testbedingungen
Temperatur Pulseinheit: etwa 20° C.
Die folgende Änderung im POWER FOCUS 6000 verhindert das Abschalten des Werkzeugs: Werkzeug → Einstellung → Drehmoment-Einstellfaktor auf 50%. Messen Sie Drehmoment und Impulsfrequenz im Uhrzeigersinn im SRTT für ca. 1 Sekunde. Überprüfen Sie, ob die Werte die in der folgenden Tabelle angegebenen Grenzwerte einhalten.
Ein Werkzeug in gutem Zustand sollte folgende Werte erreichen:
Modell | Impulsfrequenz | Max. Drehmoment CW statisch (Minimum) (Nm) |
---|---|---|
ETP TBP/TBP-S 6 | 14-20 Hz | > 42 Nm |
ETP TBP/TBP-S 6 (42) | 10-20 Hz | >37 Nm |
ETP TBP/TBP-S 8 | 14-20 Hz | > 64 Nm |
ETP TBP/TBP-S 9 | 10-20 Hz | > 97 Nm |
ETP TBP/TBP-S 13 | 8-15 Hz | > 181 Nm |
Drehmomentkontrolle an Ist-Gelenk
Verwenden Sie die gleiche Ausrüstung und Einstellungen. Verwenden Sie zum Beispiel an der Testverbindung die gleichen Verlängerungen, Steckschlüssel und Verschraubungsprogramme, welche beim Ist-Gelenk verwendet werden.
Bei einer Drehmomentprüfung am Ist-Gelenk empfehlen wir die Verwendung eines STWrench mit Restmessung*.
* Drehmoment, das nötig ist, um das Gewinde des Befestigungselements (einschließlich des Kopfes), auf das das Drehmoment aufgebracht wird, relativ zum Gegengewinde zu bewegen.
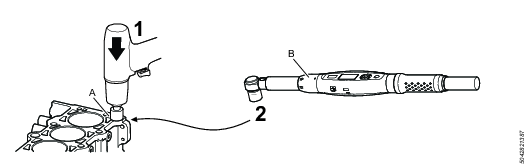
A | Das Ist-Gelenk |
B | Drehmomentschlüssel |
Führen Sie eine Verschraubung aus.
Messen Sie das Ergebnis mit dem Drehmomentschlüssel.
Wenn das Restdrehmoment nicht dem Solldrehmoment entspricht, die Festziehparameter einstellen.
Überprüfung der Werkzeuggenauigkeit
Dieses Testverfahren wird durchgeführt, um die Genauigkeit des Werkzeugs zu überprüfen. Die Prüfung erfolgt in drei verschiedenen Drehmomentstufen mit jeweils zehn (10) Festziehmomenten, die insgesamt 30 Festziehmomente ergeben. Das Ergebnis wird mit dem Referenzaufnehmer verglichen und wenn die Abweichung innerhalb der Grenzen liegt, besteht das Werkzeug den Test.
Prüfbedingungen und Aufbau
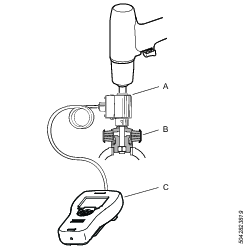
Die folgenden Prüfbedingungen müssen erfüllt sein:
● Verwenden Sie einen IRTT als Referenzgeber.
● Verwenden Sie eine Prüfverbindung mit einer echten Schraube, die beim Anziehen eine erhöhte Klemmkraft ergibt, d. h. verwenden Sie keine Bremse o. ä.. Der Schraubfall sollte weich sein (~100o, die Gesamtzahl der Impulse während des Anziehens >20 betragen).
● Verwenden Sie keine Erweiterungen, sondern nur den IRTT und die Buchse.
● Die Filterfrequenz des STa6000 muss auf 850 Hz eingestellt werden.
● Der Werkzeug-Drehmoment-Einstellfaktor muss auf 100% eingestellt werden.
● Das Werkzeug muss mit 3 verschiedenen Drehmomenten und 10 Zyklen pro Stufe geprüft werden, siehe Tabelle Werkzeugeinstellungen je Schraubsequenz.
POWER FOCUS 6000-Einstellungen
Stufe | Parameter | Einstellung |
---|---|---|
1. Startphase | Softstart | AUS |
Rehit-Erkennung | AUS | |
2. Einschraubphase | Einschraubdrehzahl | Siehe Tabelle1 |
Zeitlimits für Einschraubphase | AUS | |
Grenzwerte Einschraubpulse | AUS | |
Einschraubphase beendet | 5 Nm | |
3. Verschraubungsphase | Solldrehmoment | Siehe Tabelle1 |
Pulsenergie | Siehe Tabelle1 | |
Korrelationsfaktor Restmoment | 1 | |
Erkennungszeit vorzeitiger Drehmomentverlust | 200 ms | |
| Moment-Grenzwerte | Auto |
Winkel-Grenzwerte | AUS | |
Zeitbegrenzungen | AUS | |
Pulsbegrenzungen | AUS |
1 Tabelle: Werkzeugeinstellungen je Schraubsequenz
Werkzeugeinstellungen je Schraubsequenz
Werkzeugmodell | Schraubsequenz- | Anzahl Verschraubungen | Einschrauben (U/min) | Pulsenergie (%) | Solldrehmoment. (Nm) |
---|---|---|---|---|---|
ETP TBP/TBP-S 6 | 1 | 10 | 1500 | 50 | 12 |
2 | 10 | 2000 | 80 | 22 | |
3 | 10 | 3000 | 100 | 32 | |
ETP TBP/TBP-S 8 | 1 | 10 | 1500 | 40 | 20 |
2 | 10 | 2000 | 75 | 37 | |
3 | 10 | 3000 | 100 | 55 | |
ETP TBP/TBP-S 9 | 1 | 10 | 1500 | 50 | 35 |
2 | 10 | 2000 | 85 | 55 | |
3 | 10 | 3000 | 100 | 70 | |
ETP TBP/TBP-S 13 | 1 | 10 | 1600 | 60 | 50 |
2 | 10 | 1900 | 80 | 100 | |
3 | 10 | 2200 | 100 | 150 |
Berechnungen
Verwenden Sie die Ergebnisse aus den Werten für Anziehen, TBP und STa6000, um die folgenden Berechnungen und Auswertungen durchzuführen:
1. Mittelwerte berechnen
● Berechnen Sie den mittleren Drehmomentwert (TBP-Mittelwert) aller auf dem POWER FOCUS 6000 angezeigten Ergebnisse.
● Berechnen Sie den mittleren Drehmomentwert (STa6000-Mittelwert) aller vom STa6000 erfassten Ergebnisse.
2. Berechnen Sie die Abweichung der Drehmomentmessung zwischen TBP-Werkzeug und STa6000:
Abweichung des Drehmoment-Messfaktors = 100x [TBPmean-STa6000-Mittelwert ]÷STa6000-Mittelwert
Ergebnis für Durchgang ist ± 2.0%
3. Normalisieren Sie das Ergebnis aus dem TBP, um den gleichen Mittelwert wie beim STa6000 zu erreichen:
TBP normalisiert (1…30) = TBP value (1…30) x STa6000-Mittelwert÷TBP -Mittelwert
4. Berechnen Sie die Abweichung zwischen dem STa6000 und dem POWER FOCUS 6000 für jedes Festziehen:
Abweichung (1...30) = TBP normalisiert(1...30) - STa6000-Wert(1...30)
5. Berechnen Sie die Standardabweichung (Sigma) für die 30 berechneten Abweichungen:
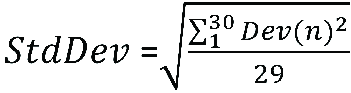
6. Überprüfung der Drehmomentmessgenauigkeit in Bezug auf das maximale Werkzeugmoment (ToolMax), angegeben pro Werkzeugmodell, z. B. 55 Nm für TBP8.
Drehmoment-Messgenauigkeit = 100 x 3 x StdDev)÷ToolMax
Ergebnis für den Durchlauf ist: maximal 4.0%
Aktualisieren der Werkzeug-Software
Informationen zum Aktualisieren der Werkzeug-Software finden Sie in der ToolsTalk Service 2 User Edition-Bedienungsanleitung unter Firmware kopieren.

So vermeiden Sie Werkzeugschäden:
Achten Sie darauf, dass der Akku vollständig aufgeladen ist, wenn Sie ein Softwareupdate durchführen.
Nehmen Sie bei laufendem Softwareupdate den Akku nicht aus dem Werkzeug heraus.
Nehmen Sie bei laufendem Softwareupdate die Speicherkarte nicht aus dem Werkzeug heraus.
Störungshilfe
Anleitung zur Fehlerbehebung
Problem | Ursache | Maßnahme |
---|---|---|
Das Werkzeug schaltet sich nicht ab oder die Festziehzeit ist zu lang. | Zielmoment nahe dem maximalen Drehmoment des Werkzeugs. | Wählen Sie ein größeres Werkzeug mit mehr Kraft. |
Abgenutzte Verlängerung oder Sockel/Bits. | Überprüfen Sie die Verlängerung und Sockel/Bits. | |
Falscher Ölstand in der Pulseinheit. | Lassen Sie Öl ab oder füllen Sie Öl nach. | |
Das Gelenk ist zu weich für das Werkzeug. | Wählen Sie ein größeres Werkzeug mit mehr Leistung oder erhöhen Sie die Pulsenergie. | |
Abgenutzte Teile in der Pulseinheit. | Untersuchen und ersetzen Sie verschlissene Teile. | |
Die Streckgrenze des Gelenks ist erreicht. | Überprüfen Sie die Gelenk-Spezifikationen. | |
Inkonsistente Abschaltung oder unzureichende Genauigkeit. | Das Zieldrehmoment liegt nicht innerhalb der Werkzeugspezifikation. | Wechseln Sie zu einer anderen Werkzeuggröße. |
Erweiterung ist zu lang. | Verwenden Sie eine kürzere Erweiterung. | |
Abgenutzte Verlängerung oder Sockel/Bits. | Ersetzen Sie die Erweiterung und Sockel/Bits. | |
Falscher Ölstand in der Pulseinheit. | Lassen Sie Öl ab oder füllen Sie Öl nach. | |
Das Gelenk ist zu steif. | Wählen Sie ein kleineres Werkzeug oder verringern Sie die Pulsenergie. | |
Wenn das Werkzeug sehr heiß wird. | Sehr hohes Reibmoment. | Wechseln Sie zu einer anderen Werkzeuggröße. |
Sehr weiche Verbindungen. | Wechseln Sie zu einer anderen Werkzeuggröße. | |
Hohe Zyklusrate. | Wechseln Sie zu einer anderen Werkzeuggröße. |
Ereignisse und Fehlercodes
Eine vollständige Liste der Werkzeugereignisse und Fehlercodes finden Sie im Power Focus 6000-Konfigurationshandbuch.
Recycling
Umweltschutzbestimmungen
Nachdem ein Produkt seinen Zweck erfüllt hat, muss es ordnungsgemäß recycelt werden. Zerlegen Sie das Produkt und recyceln Sie die Komponenten gemäß örtlicher Vorschriften.
Batterien sollten an Ihre öffentliche Batterieverwertungsstelle weitergegeben werden.
Recycling-Anweisung
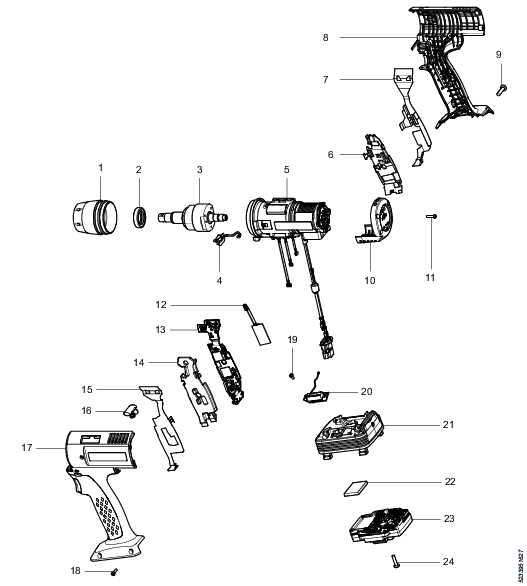
Pos. | Teil | Anmerkungen | Recyceln als |
---|---|---|---|
1 | Vordere Abdeckung | Metall, Aluminium | |
2 | Lager | Metall, Stahl | |
3 | Pulseinheit | Metall, Stahl | |
4 | Leuchte vorne | Elektronik | |
5 | Motorgehäuse, vollständig | Elektronik | |
6 | Hauptplatine Dichtungsgummi | Gummi, PUR | |
7 | GND-Streifen rechts | Metall, Messing | |
8 | Griff, rechts | Kunststoff, Sonstiges, PA | |
9 | Schrauben | 8 Stück | Metall, Stahl |
10 | Endabdeckung hinten | Kunststoff, Sonstige, PA | |
11 | Schrauben | 4 Stück | Metall, Stahl |
12 | Funkmodul | Elektronik | |
13 | Hauptplatinenmodul | Kunststoff, Sonstige, PA | |
14 | Hauptplatine Dichtungsgummi | Gummi, PUR | |
15 | GND-Streifen links | Metall, Messing | |
16 | Umschaltknopf | Metall, Neodym | |
17 | Griff, links | Kunststoff, Sonstiges, PA | |
18 | Schraube | Metall, Stahl | |
19 | Schraube | 4 Stück, zu den Antennen | Metall, Stahl |
20 | Antennen | Elektronik | |
21 | Akkuhalterung | Metall, Aluminium | |
22 | Notstrombatterie | Batterie, Lithium-Ionen | |
23 | Antriebsmodul | Elektronik | |
24 | Schrauben | 4 Stück zum Antriebsmodul | Metall, Stahl |

Wenn das TBP-Tool ein Netzteil und ein Stromkabel verwendet, finden Sie weitere Informationen in den Produktanweisungen für das Netzteil 950W - Recyclinganweisungen.