FlexCarrier 6 slot
Control and drive unit
Product Information
General Information
Safety Signal Words
The safety signal words Danger, Warning, Caution, and Notice have the following meanings:
DANGER | DANGER indicates a hazardous situation which, if not avoided, will result in death or serious injury. |
WARNING | WARNING indicates a hazardous situation which, if not avoided, could result in death or serious injury. |
CAUTION | CAUTION, used with the safety alert symbol, indicates a hazardous situation which, if not avoided, could result in minor or moderate injury. |
NOTICE | NOTICE is used to address practices not related to personal injury. |
Warranty
Product warranty will expire 12+1 months after dispatch from Atlas Copco's Distribution Center.
Normal wear and tear on parts is not included within the warranty.
Normal wear and tear is that which requires a part change or other adjustment/overhaul during standard tools maintenance typical for that period (expressed in time, operation hours or otherwise).
The product warranty relies on the correct use, maintenance, and repair of the tool and its component parts.
Damage to parts that occurs as a result of inadequate maintenance or performed by parties other than Atlas Copco or their Certified Service Partners during the warranty period is not covered by the warranty.
To avoid damage or destruction of tool parts, service the tool according to the recommended maintenance schedules and follow the correct instructions.
Warranty repairs are only performed in Atlas Copco workshops or by Certified Service Partners.
Atlas Copco offers extended warranty and state of the art preventive maintenance through its ToolCover contracts. For further information contact your local Service representative.
For electrical motors:
Warranty will only apply when the electric motor has not been opened.
Website
Information concerning our Products, Accessories, Spare Parts and Published Matters can be found on the Atlas Copco website.
Please visit: www.atlascopco.com.
ServAid
ServAid is a portal that is continuously updated and contains Technical Information, such as:
Regulatory and Safety Information
Technical Data
Installation, Operation and Service Instructions
Spare Parts Lists
Accessories
Dimensional Drawings
Please visit: https://servaid.atlascopco.com.
For further Technical Information, please contact your local Atlas Copco representative.
Safety Data Sheets MSDS/SDS
The Safety Data Sheets describe the chemical products sold by Atlas Copco.
Please consult the Atlas Copco website for more information www.atlascopco.com/sds.
Signs and Stickers
The product is fitted with signs and stickers containing important information about personal safety and product maintenance. The signs and stickers shall always be easy to read. New signs and stickers can be ordered by using the spare parts list.

Country of Origin
For the Country of Origin, please refer to the information on the product label.
Dimensional Drawings
Dimensional Drawings can be found either in the Dimensional Drawings Archive, or on ServAid.
Please visit: http://webbox.atlascopco.com/webbox/dimdrw or https://servaid.atlascopco.com.
Overview
Overview
The FlexCarrier is available in two versions: 3 slot and 6 slot. The FlexController and the FlexDrives connect into slots on the FlexCarrier.
The FlexCarrier distributes power, interconnection, emergency stop (e-stop) and cooling. The FlexCarrier also connects to accessories.
It is possible to connect one FlexCarrier to other FlexCarriers in a daisy chain.
Average power consumption
Average power consumption (only FlexCarrier) |
20 W |
Normal Environmental Conditions
This product is designed to be safe under the following conditions:
Indoor use
Altitude up to 2 000 m
Operating temperature +5 °C / +41 °F to +50 °C / +122 °F
Storage temperature +5 °C / +41 °F to +50 °C / +122 °F
Maximum relative humidity 80 % for temperatures up to 31 °C / 89 °F decreasing linearly to 50 % relative humidity at 40 °C / 104 °F
Mains supply voltage fluctuations up to ±10 % of the nominal voltage
Transient overvoltages up to the levels of overvoltage category II
Temporary overvoltages occurring on the mains supply
Pollution degree 2
Ingress protection rating: IP54
Technical Product Data
Technical Product Data can be found on either ServAid, or the Atlas Copco website.
Please visit: https://servaid.atlascopco.com or www.atlascopco.com.
Accessories
Optional Accessories
Power cable, left entry (LE)

Left entry (LE) power cables are used when the FlexCarriers are mounted horizontally.
Length | Name | Article number | Remark | FlexCarrier size |
---|---|---|---|---|
0.22 m | Power Cable | 4222 2082 11 | DaisyCh Power Cable LE 0.22m | 3 slot |
0.365 m | Power Cable | 4222 2082 12 | DaisyCh Power Cable LE 0.365m | 6 slot |
Power cable, straight entry (SE)
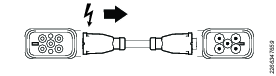
Length | Name | Article number | Remark |
---|---|---|---|
1 m | Power Cable | 4222 1948 01 | DaisyCh Power Cable SE 1m |
2 m | Power Cable | 4222 1948 02 | DaisyCh Power Cable SE 2m |
3 m | Power Cable | 4222 1948 03 | DaisyCh Power Cable SE 3m |
5 m | Power Cable | 4222 1948 05 | DaisyCh Power Cable SE 5m |
10 m | Power Cable | 4222 1948 10 | DaisyCh Power Cable SE 10m |
Power cable, straight to right entry (SRE)
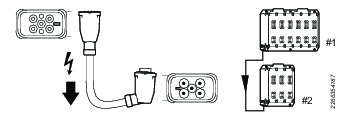
Use straight to entry (SRE) power cables when the FlexCarriers are mounted vertically top down, that is, the first FlexCarrier mounted above second the FlexCarrier.
Length | Name | Article number | Remark |
---|---|---|---|
0.65 m | Power cable | 4222 2083 11 | DaisyCh Power Cable SRE 0.65m |
Power cable, right entry to straight (RES)
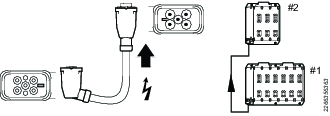
Use straight to entry (RES) power cables when the FlexCarriers are mounted vertically bottom up, that is, the first FlexCarrier mounted below second the FlexCarrier.
Length | Name | Article number | Remark |
---|---|---|---|
0.65 m | Power Cable | 4222 2084 11 | DaisyCh Power Cable RES 0.65m |
Power cable, open end (OE)
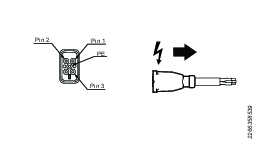
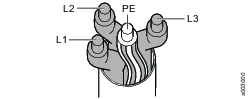
Length | Name | Article number | Remark |
---|---|---|---|
3 m | Power Cable | 4222 1887 03 (EU) 4222 3147 03 (US) 4222 3189 03 (orange) | Flex PowerCable(EU)OE 3m Flex PowerCable(US)OE 3m Flex PowerCable(orange)OE 3m |
10 m | Power Cable | 4222 1887 10 (EU) 4222 3147 10 (US) 4222 3189 10 (orange) | Flex PowerCable(EU)OE 10m Flex PowerCable(US)OE 10m Flex PowerCable(orange)OE 10m |
30 m | Power Cable | 4222 1887 30 (EU) 4222 3147 30 (US) 4222 3189 30 (orange) | Flex PowerCable(EU)OE 30m Flex PowerCable(US)OE 30m Flex PowerCable(orange)OE 30m |
Use 4222 1887 xx for fixed installations in EU.
Use 4222 3147 xx for fixed installations in the USA and Canada.
Use 4222 3189 xx for non-fixed installations.
All installations must follow local laws and regulations.
Control cable

System orientation | Name | Article number |
---|---|---|
Horizontal 3 slot | Flex Daisy Control Cable 0.46 m | 4222 2062 01 |
Horizontal 6 slot | Flex Daisy Control Cable 0.61 m | 4222 2062 04 |
Vertical system | Flex Daisy Control Cable 0.84 m | 4222 2062 03 |
The following cables are provided when the FlexCarriers are mounted far from each other:
Length | Name | Article number |
---|---|---|
1 m | Flex Daisy Control Cable 1m | 4222 2062 11 |
2 m | Flex Daisy Control Cable 2m | 4222 2062 12 |
3 m | Flex Daisy Control Cable 3m | 4222 2062 13 |
5 m | Flex Daisy Control Cable 5m | 4222 2062 15 |
10 m | Flex Daisy Control Cable 10m | 4222 2062 20 |
Power cable, right entry (RE)
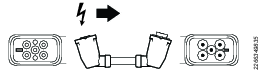
Right entry (RE) power cables are used when the FlexCarriers are mounted horizontally.
Length | Name | Article number | Remark | FlexCarrier size |
---|---|---|---|---|
0.22 m | Power Cable | 4222 1946 11 | DaisyCh Power Cable RE 0.22m | 3 slot |
0.365 m | Power Cable | 4222 1946 12 | DaisyCh Power Cable RE 0.365m | 6 slot |
FlexFan module
As an option there is a possibility to use one fan module per three slots. The fan modules will increase the amount of power dissipation the system can tolerate without being overheated
The fan module consists of two redundant fans:
3 slot: One fan module.
6 slot: Two fan modules.
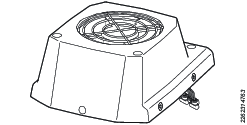
Weight | 0.45 kg |
Dimensions | 180x75x144 mm (W x H x D) |
Total height of FlexSystem with FlexFan | 306 mm |
IP rating | IP54 |
Supply voltage | 24 VDC |
Power | 4.8 W |
Temperature | 20…+70 °C |
Rotational speed | 500-3000 rpm |
Air flow rate | 18.2 l/s |
Sound pressure | 3 slot: 39.9 dB(A) @ 70% speed 48.1 dB(A) @ 100% speed 6 slot: 42.4 dB(A) @ 70% speed 50.4 dB(A) @ 100% speed 9 slot system (One 3 slot + one 6 slot): 43.9 dB(A) @ 70% speed 52.0 dB(A) @ 100% speed |
Service Life | 100 000 h 40 °C / 50 000 h 70 °C |
Bypass plug
The bypass plug is used in the second FlexCarrier and each of the following FlexCarriers in an e-stop chain. The bypass plug does not have any connections and the plug covers the 24 VDC IN.
E-stop entry plug
The e-stop entry plug is used in the first FlexCarrier in an e-stop chain. It has four connectors for the e-stop button and two connectors for the reset button
The reset button circuit is normally closed, when the e-stop button is pressed the reset circuit opens.
Wiring
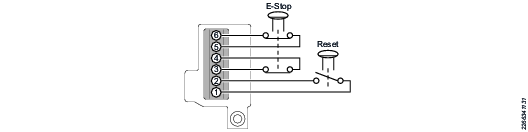
Terminal | Function |
6 | +24V |
5 | E-stop + |
4 | E-stop - |
3 | GND |
2 | E-stop reset |
1 | NC (Normally closed) |
24 VDC connector
The 24 VDC connector is ordered separately and must be the following:
Plug component, screw connection with tension sleeve, 2 connections
Type: MC 1,5/ 2-ST-3,5
Order No.: 1840366 from PHOENIX CONTACT.
ASM plug
If an external safety PLC will control the e-stop, an ASM plug is used in the first FlexCarrier in the e-stop chain. The safety PLC is connected to a PROFINET fieldbus module on the FlexController
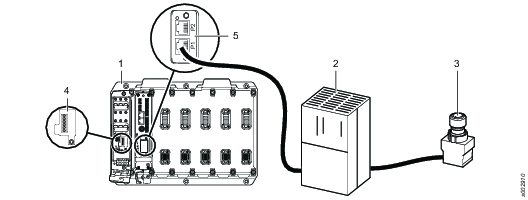
Pos | |
1 |
First FlexCarrier |
2 |
Safety PLC |
3 |
E-stop |
4 |
ASM plug |
5 |
PROFINET fieldbus |
E-stop configuration plug
Select a plug to connect in the e-stop configuration connector. Each plug will have a pre-configuration. The following plugs are available:
-
E-stop entry plug
-
Bypass plug
-
ASM plug.
Installation
Installation Requirements
Mounting FlexSystem
For minimal footprint select power cables and mount the FlexSystem according to the specified distances.
The FlexCarrier should be mounted vertically for optimal system functionality. This will allow for best air flow and heat transfer. Mounting FlexCarrier horizontally can affect the lifetime of the system.
The FlexSystem and the main switch box can be mounted in any normal industrial environment without any extra enclosure, if local regulations do not require otherwise.
The FlexSystem should not be exposed to excessive amount of vibrations. The vibration should be less than 10 g (98 m/s2) and between 1000 to 2000 Hz.
Screw: M6, Torque: 9.8 Nm
Distances between FlexSystem parts for minimal footprint (with FlexFan)
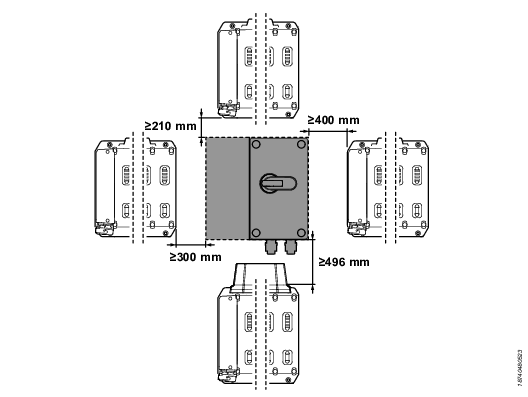

Distances between FlexSystem parts for minimal footprint (without FlexFan)
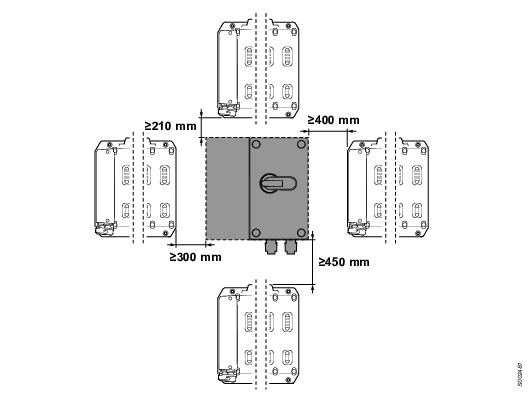
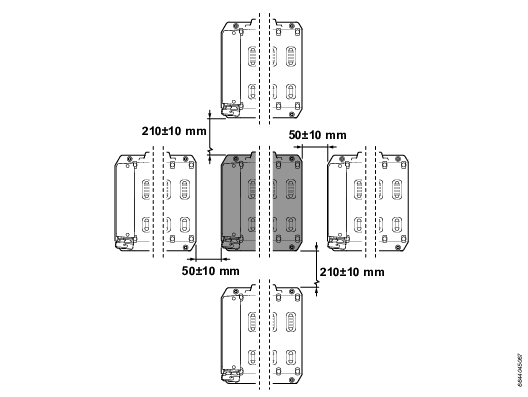
Cable planning
Recommended cables for minimum footprint
For information of dimensions for minimal footprint installation, see Mounting FlexSystem.
Power cables
To connect a FlexCarrier to mains switch board, use the power cable:
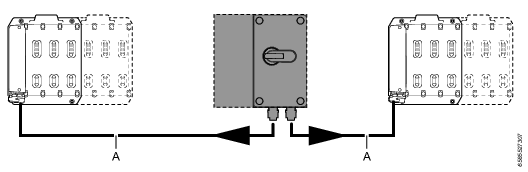
Name | Article number | |
---|---|---|
A | DaisyCh Power Cable SE 1m | 4222 1948 01 |
To connect a FlexCarrier to a 3 slot FlexCarrier, use these power cables:
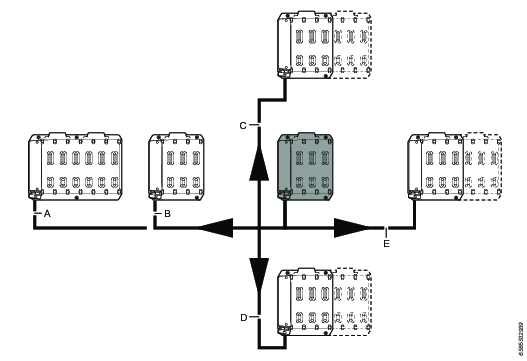
To connect a FlexCarrier to a 6 slot FlexCarrier, use these power cables:
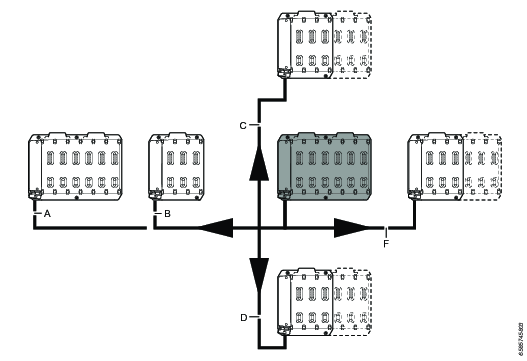
Name | Article number | |
---|---|---|
A | DaisyCh Power Cable LE 0.365m | 4222 2082 12 |
B | DaisyCh Power Cable LE 0.22m | 4222 2082 11 |
C | DaisyCh Power Cable RES 0.65m | 4222 2084 11 |
D | DaisyCh Power Cable SRE 0.65m | 4222 2083 11 |
E | DaisyCh Power Cable RE 0.22m | 4222 1946 11 |
F | DaisyCh Power Cable RE 0.365m | 4222 1946 12 |
Control cables
Use these control cables:
System orientation | Name | Article number |
---|---|---|
Horizontal 3 slot | Daisy Control Cable 0.44m | 4222 2062 01 |
Horizontal 6 slot | Flex Daisy Control Cable 0.61m | 4222 2062 04 |
Vertical system | Flex Daisy Control Cable 0.84m | 4222 2062 03 |
Recommended cables for general positioning
FlexCarriers can be positioned freely, with more spacing or with FlexCarriers not placed in the same plane.
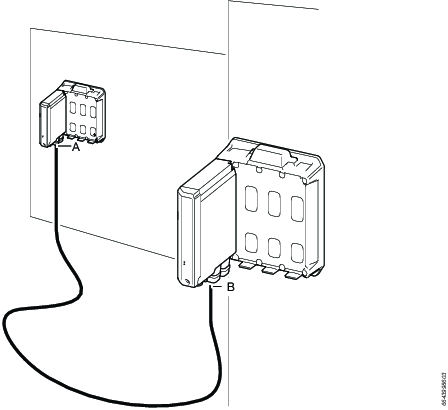
Power cables
The selection is based on the routed length between cable ends from A to B. Select a FlexPower cable with the closest longer length to the measurement.

The minimum bending radius (0.12 m) must be followed.
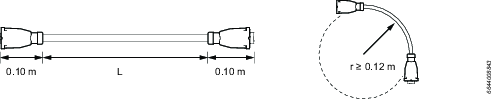
Length (L) | Name | Article number | Remark |
---|---|---|---|
1 m | Power Cable | 4222 1948 01 | DaisyCh Power Cable SE 1m |
2 m | Power Cable | 4222 1948 02 | DaisyCh Power Cable SE 2m |
3 m | Power Cable | 4222 1948 03 | DaisyCh Power Cable SE 3m |
5 m | Power Cable | 4222 1948 05 | DaisyCh Power Cable SE 5m |
10 m | Power Cable | 4222 1948 10 | DaisyCh Power Cable SE 10m |
Control cables
The selection is based on the routed length between cable ends from A to B. Select a FlexControl cable with the closest longer length to the measurement.

The minimum bending radius (0.1 m) must be followed.
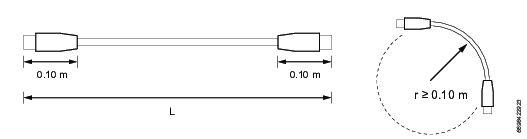
Length (L) | Name | Article number | Remark |
---|---|---|---|
1 m | Control Cable | 4222 2062 11 | Flex Daisy Control Cable 1m |
2 m | Control Cable | 4222 2062 12 | Flex Daisy Control Cable 2m |
3 m | Control Cable | 4222 2062 13 | Flex Daisy Control Cable 3m |
5 m | Control Cable | 4222 2062 15 | Flex Daisy Control Cable 5m |
10 m | Control Cable | 4222 2062 20 | Flex Daisy Control Cable 10m |
Installation Instructions
Connection interfaces
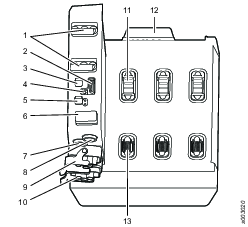
Pos | |
1. | Circuit breakers (16 A). |
2. | Emergency stop (e-stop) configuration plug:
|
3. | 24 VDC IN (Max 8 A) For (CPU) backup supply. |
4. | Hex switch to set the FlexCarrier address. |
5. | 24 VDC OUT (1.8 A) For external devices |
6. | Gasket for cable routing. |
7. | Inter-Com Port, In (for daisy chain) (24VDC, ethernet, e-stop). |
8. | Inter-Com Port, Out (24VDC, ethernet, e-stop). |
9. | High voltage 400/480 VAC, Out (for daisy chain). |
10 | High voltage 400/480 VAC, In. |
11. | Device slot, 400/480 VAC. |
12 | FlexFan connector. |
13 | Device slot, 24 VDC, ethernet, e-stop. |
Install first FlexCarrier
Make sure the circuit breakers are off (down).
Fasten the FlexCarrier. Use M6 screws. Tighten at 9.8 Nm.
Use 4 screws for a 3 slot FlexCarrier.
Use 6 screws for a 6 slot FlexCarrier.
Set the FlexCarrier address.
The first FlexCarrier must be set to 1, the second to 2 etc. The default factory setting is 0. It is not allowed to have 0 as an address in an installed application. For more information on system planning, see FlexSystem System Overview Manual.
Select e-stop plug:
E-stop entry plug.
Advanced Security Module (ASM) plug.
Fasten the e-stop cables to the e-stop entry plug according to schematics. This step is not applicable for the ASM plug.
This is most easily done on a working bench.
Plug in the e-stop plug.
If the 24 VDC OUT and 24 VDC IN will be used, prepare the connectors.
This is most easily done on a working bench.
Install the 24 VDC IN/OUT connectors. Make sure you use the correct connector.
Do not connect the cables to the connector when the connector is fastened to the FlexCarrier.
If using an external 8 A power supply it shall be current limited to 8 A, double insulation. It shall be certified according to EN 61010-1 or according to another standard compatible with the requirements in EN 61010-1 (for example EN 60950 or EN 60601).
Route the cables through the gasket.
Make sure the cables are not pinched or damaged when the cover is put back on.
Do not route the cables so they block the LED light guide in the cover.
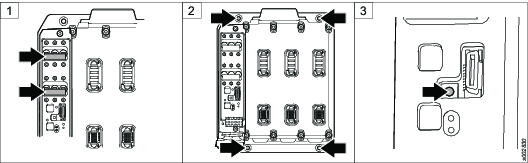
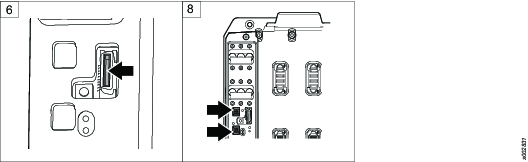
Route and install power- and control cables to FlexCarrier
Make sure that the cables are in good condition before connecting them to the system. Check that
Cables are not damaged
Connectors are not damaged.

If these conditions are not fulfilled the system must not be connected to mains or switched on.
Systems where damages to connections or cables are found must be disconnected and repaired immediately.
Install power cables.
Install control cables.
Operation
Ergonomic Guidelines
Consider your workstation as you read through this list of general ergonomic guidelines to identify areas for improvement in posture, component placement, or work environment.
Take frequent breaks and change work positions frequently.
Adapt the workstation area to your needs and the work task.
Adjust for a convenient reach range by determining where parts and tools need to be located to avoid static load.
Use workstation equipment such as tables and chairs appropriate for the work task.
Avoid work positions above shoulder level or with static holding during assembly operations.
When working above shoulder level, reduce the load on the static muscles by lowering the weight of the tool, using for example torque arms, hose reels or weight balancers. You can also reduce the load on the static muscles by holding the tool close to the body.
Take frequent breaks.
Avoid extreme arm or wrist postures, particularly during operations requiring a degree of force.
Adjust for a convenient field of vision that requires minimal eye and head movements.
Use appropriate lighting for the work task.
Select the appropriate tool for the work task.
In noisy environments, use ear protection equipment.
Use high-quality inserted tools and consumables to minimize exposure to excessive levels of vibration.
Minimize exposure to reaction forces.
When cutting:
A cut-off wheel can get stuck if the cut-off wheel is bent or not guided properly. Use the correct flange for the cut-off wheel and avoid bending the cut-off wheel during operation.
When drilling:
The drill might stall when the drill bit breaks through. Use support handles if the stall torque is high. The safety standard ISO11148 part 3 recommends using a device to absorb a reaction torque above 10 Nm for pistol grip tools and 4 Nm for straight tools.
When using direct-driven screwdrivers or nutrunners:
Reaction forces depend on the tool settings and joint characteristics. Strength and posture determine the amount of reaction force that an operator can tolerate. Adapt the torque setting to the operator's strength and posture and use a torque arm or reaction bar if the torque is too high.
In dusty environments, use a dust extraction system or wear a mouth protection mask.
Service
Preventing ESD Problems
The components inside the product and controller are sensitive to electrostatic discharge. To avoid future malfunction, make sure that service and maintenance is carried out in an ESD approved work environment. The figure below shows an example of an appropriate service work station.

Maintenance Instructions
Service Recommendations
Preventive maintenance is recommended at regular intervals. See the detailed information on preventive maintenance. If the product is not working properly, take it out of service and inspect it.
If no detailed information about preventive maintenance is included, follow these general guidelines:
Replace any defective or worn parts
Recycling
Environmental Regulations
When a product has served its purpose it has to be recycled properly. Dismantle the product and recycle the components in accordance with local legislation.
Batteries shall be taken care of by your national battery recovery organization.
Recycling information
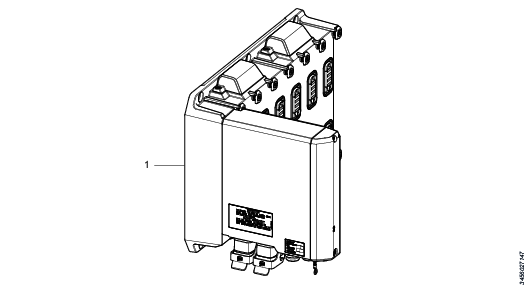
| Part | Recycle as |
---|---|---|
1 | FlexCarrier 6 slot | WEEE |